内容.docx
《内容.docx》由会员分享,可在线阅读,更多相关《内容.docx(25页珍藏版)》请在冰豆网上搜索。
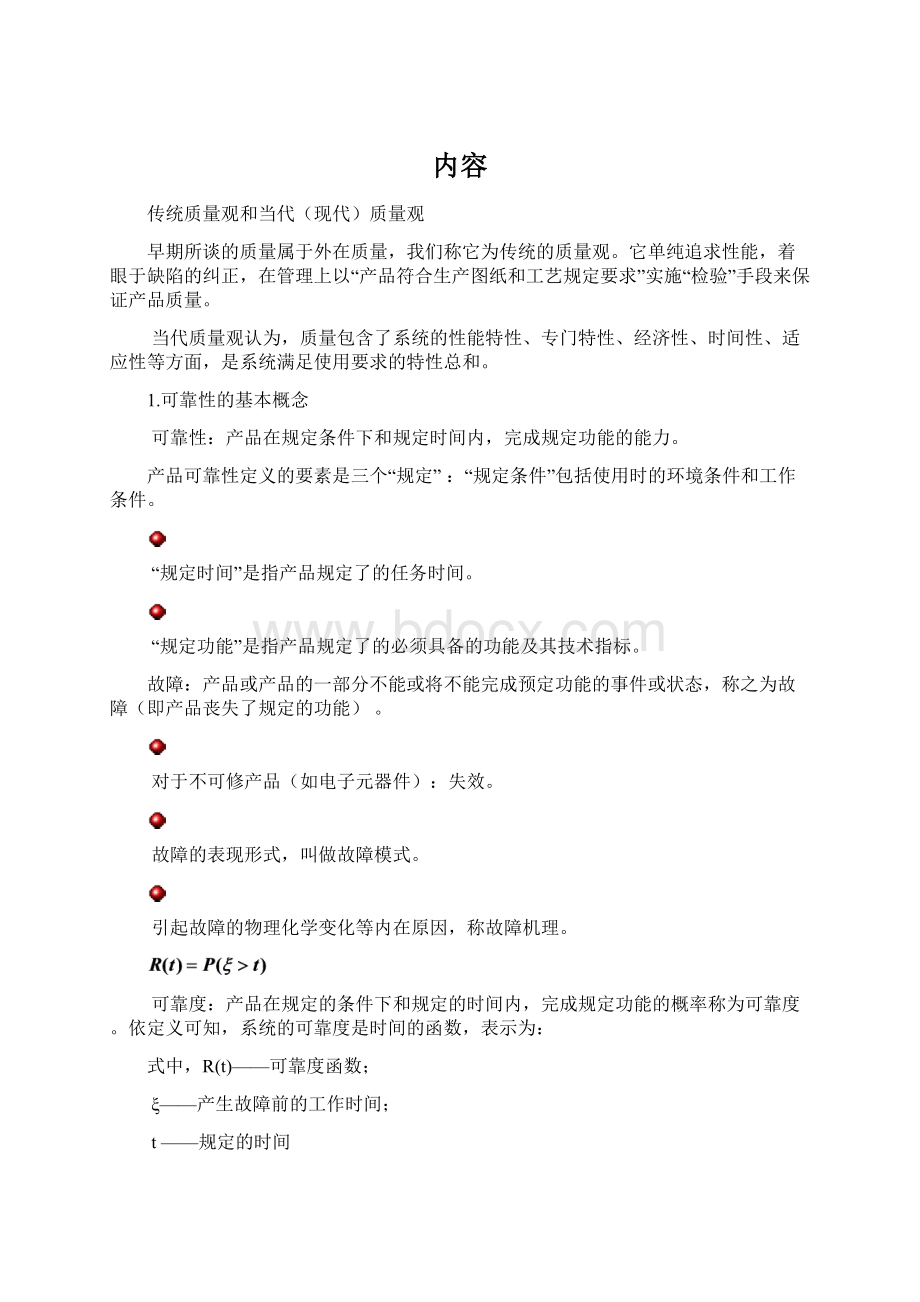
内容
传统质量观和当代(现代)质量观
早期所谈的质量属于外在质量,我们称它为传统的质量观。
它单纯追求性能,着眼于缺陷的纠正,在管理上以“产品符合生产图纸和工艺规定要求”实施“检验”手段来保证产品质量。
当代质量观认为,质量包含了系统的性能特性、专门特性、经济性、时间性、适应性等方面,是系统满足使用要求的特性总和。
1.可靠性的基本概念
可靠性:
产品在规定条件下和规定时间内,完成规定功能的能力。
产品可靠性定义的要素是三个“规定”:
“规定条件”包括使用时的环境条件和工作条件。
“规定时间”是指产品规定了的任务时间。
“规定功能”是指产品规定了的必须具备的功能及其技术指标。
故障:
产品或产品的一部分不能或将不能完成预定功能的事件或状态,称之为故障(即产品丧失了规定的功能)。
对于不可修产品(如电子元器件):
失效。
故障的表现形式,叫做故障模式。
引起故障的物理化学变化等内在原因,称故障机理。
可靠度:
产品在规定的条件下和规定的时间内,完成规定功能的概率称为可靠度。
依定义可知,系统的可靠度是时间的函数,表示为:
式中,R(t)——可靠度函数;
ξ——产生故障前的工作时间;
t——规定的时间
产品在规定的条件下和规定的时间内,丧失规定功能的概率称为累积故障概率(又叫不可靠度)。
故障率:
工作到某时刻尚未发生故障的产品,在该时刻后单位时间内发生故障的概率,称之为产品的故障率。
浴盆曲线
大多数产品的故障率随时间的变化曲线形似浴盆,称之为浴盆曲线。
由于产品故障机理的不同,产品的故障率随时间的变化大致可以分为三个阶段:
早期故障;偶然故障;耗损故障
某微型计算机的MTBF=10000小时,是否意味着该计算机每工作10000小时才出一次故障?
有一计算机系统的MTBF为2000h,试求失效(故障)率和可靠性。
越小、MTBF越长的机器就是好机器。
可靠性已经成为衡量系统或产品(计算机)性能的主要指标之一,并且通常用MTBF或MTTF来直接表示其可靠性的大小。
寿命特征
可靠寿命:
指给定的可靠度所对应的产品工作时间。
使用寿命:
指产品在规定的使用条件下,具有可接受的故障率的工作时间区间。
首次翻修期限(首翻期):
指在规定条件下,产品从开始使用到首次翻修的工作时间和(或)日历持续时间。
翻修是指把产品分解成零部件,清洗、检查,并通过修复或替换故障零部件,恢复产品寿命,等于或接近其首翻期的修理。
翻修间隔期限:
指在规定条件下,产品两次相继翻修间的工作时间、循环次数和(或)日历持续时间。
总寿命:
指在规定条件下,产品从开始使用到规定报废的工作时间、循环次数和(或)日历持续时间。
贮存期限:
在规定条件下,产品能够贮存的日历持续时间,在此时间内,产品启封使用能满足规定要求。
2.可靠性参数体系
可靠性参数是描述系统可靠性的度量。
它直接与战备完好、任务成功、维修人力费用和保障资源费用有关。
可靠性指标是可靠性参数要求的量值。
TMFHBF——平均故障间隔飞行小时(MFHBF)
TBM——平均维修间隔时间 (MTBM):
在规定的条件下和规定的时间内,产品寿命单位总数与该产品计划和非计划维修时间总数之比。
PMC——完成任务的成功概率(MCSP):
在规定的条件下和规定的时间内,系统能完成规定任务的概率。
TBCF——致命故障间的任务时间(MTBCF):
在规定的一系列任务剖面中,产品任务总时间与致命性故障数之比。
TTR——平均修复时间(MTTR):
在规定的条件下和规定的时间内,产品在任一规定的维修级别上,修复性维修总时间与该级别上被修复产品的故障总数之比。
TBR——平均拆卸间隔时间(MTBR):
在规定的时间内,系统寿命单位总数与从该系统上拆下的产品总次数之比。
可靠性设计需要综合权衡完成规定功能和减少用户费用两方面的需求,可靠性参数分为基本可靠性参数和任务可靠性参数
基本可靠性反映了产品对维修人力费用和后勤保障资源的需求。
确定基本可靠性指标时应统计产品的所有寿命单位和所有的故障。
常见参数有TBF、TBM、TMFHBF、TBR。
任务可靠性是产品在规定的任务剖面中完成规定功能的能力。
确定任务可靠性指标时仅考虑在任务期间那些影响任务完成的故障(即致命性故障)。
常见参数有任务可靠度、PMC、TBCF。
可靠性参数指标特性
综合性某些可靠性参数是其它可靠性、维修性参数的综合表示。
如固有可用度表示为:
即产品的平均故障间隔时间与平均故障间隔时间、平均修复时间的和之比。
相关性使用参数与合同参数之间相互关联,可以按照一定的规律进行转换。
阶段性产品可靠性,在研制阶段具有增长性。
描述系统的模型
原理图反映了系统及其组成单元之间的物理上的连接与组合关系。
功能框图、功能流程图反映了系统及其组成单元之间的功能关系。
系统的原理图、功能框图和功能流程图是建立系统可靠性模型的基础。
可靠性模型描述了系统及其组成单元之间的故障逻辑关系。
建立系统可靠性模型的目的和用途在于定量分配、估算和评估系统的可靠性。
可靠性模型建立于系统可靠性(方)框图,即为预计或估算产品的可靠性所建立的可靠性方框图和数学模型,也称可靠性逻辑框图及其数学模型。
了解系统中各个部分(或单元)的功能和它们相互之间的联系以及对整个系统的作用和影响对建立系统的可靠性数学模型、完成系统的可靠性设计、分配和预测都具有重要意义。
借助于可靠性框图可以精确地表示出各个功能单元在系统中的作用和相互之间的关系。
系统可靠性(方)框图(ReliabilityBlockDiagrams,简写RBD)
方框:
产品或功能
逻辑关系:
功能布局
连线:
系统功能流程的方向
无向的连线意味着是双向的。
节点(节点可以在需要时才加以标注)
输入节点:
系统功能流程的起点
输出节点:
系统功能流程的终点
中间节点
RBD和原理图的关系
原理图表示系统中各部分之间的物理关系,而RBD表示系统中各部分之间的功能关系,即用简明扼要的直观方法表现能使系统完成任务的各种串—并—旁联方框的组合。
虽然根据原理图也可以绘制出可靠性逻辑图,但并不能将它们二者等同起来。
功能框图与功能流程图
用以描述在系统功能分解过程中的较低层次功能间的接口与关联关系。
功能框图与功能流程图的逐级细化过程是与系统的功能分解相协调的。
功能框图——静态(不随时间而变)
系统级的功能以及它们的子功能具有唯一的时间基准(所有功能的执行时间一样长)
复杂系统一般具有两方面的特点:
系统具有多功能,各功能的执行时机是有时序的,各功能的执行时间长短不一。
在系统工作的过程中,系统的结构是可以随时间而变化的。
系统的功能随时间而变的系统——功能流程图
可以描述这类系统的功能关系,为建立系统可靠性框图模型奠定基础。
它的一个缺陷:
没有对系统功能的持续时间及功能间的时间进行描述,缺少一个时间坐标。
时间特性是可靠性分析中不可缺少的一个要素。
需要进行时间分析
确定时间基准
通过与该时间基准对应,可以得到系统功能流程图中各功能的执行时间及功能间的时间。
3.典型的可靠性模型
典型的可靠性模型分为有贮备与无贮备两种,有贮备可靠性模型按贮备单元是否与工作单元同时工作而分为工作贮备模型与非工作贮备模型。
串联模型
组成系统的所有单元中任一单元的故障都会导致整个系统故障的称为串联系统。
并联模型
组成系统的所有单元都发生故障时,系统才发生故障的称为并联系统,是最简单的冗余系统(有贮备模型)。
数学模型
对于最常用的两单元并联系统,有
旁联模型
组成系统的各单元只有一个单元工作,当工作单元故障时,通过转换装置接到另一个单元继续工作,直到所有单元都故障时系统才故障,称为非工作储备系统,又称旁联系统。
数学模型
1.假设转换装置可靠度为1,则系统的MTBFS等于各单元MTBFi之和。
当系统各单元的寿命服从指数分布时,有
[例]某2台发电机构成旁联模型,发电机故障率λ=0.001/h,切换开关成功概率0.98,求运行100小时的可靠度。
解:
R(t)=e-0.001×100(1+0.98×0.001×100)=0.9934
若两台发动机并联,系统可靠度
R(t)=2e-λt-e-2λt=2e-0.001×100-e-2×0.001×100=0.9909
若希望旁联可靠度大于并联,则
e-λt(1+RDλt)≥2e-λt-e-2λt
因此,要求切换开关成功概率
RD≥(1-e-0.001×100)/(0.001×100)=0.95
1.可靠性要求制定
可靠性要求产品使用方向承制方(或生产方)从可靠性角度提出的研制目标,是进行可靠性设计、分析、制造、试验和验收的依据。
研制人员只有在透彻地了解这些要求后,才能将可靠性正确地设计、生产到产品中去,并按要求有计划地实施有关的组织、监督、控制及验证工作。
可靠性要求分类
定性要求
用一种非量化的形式来设计、评价和保证产品的可靠性。
定量要求
规定产品的可靠性参数、指标和相应的验证方法。
用定量方法进行设计分析,进行可靠性验证,从而保证产品的可靠性。
可靠性定性要求概念
用一种非量化的形式来设计、评价和保证产品的可靠性,对数值无确切要求。
在定量化设计分析缺乏大量数据支持的情况下,提出定性设计分析要求并加以实现更为重要。
定性设计要求概念
定性设计要求一般是在产品研制过程中要求采取的可靠性设计措施,以保证与提高产品可靠性。
这些要求都是概要性的设计措施,在具体实施时,需要根据产品的实际情况而细化。
可靠性定量要求
概念
确定产品的可靠性参数、指标以及验证时机和验证方法,以便在设计、生产、试验验证、使用过程中用量化方法评价或验证装备的可靠性水平。
可靠性参数要反映战备完好性,任务成功性,维修人力费用及保障资源费用等四个方面的要求。
MTBF
MFHBF
MCSP
常用可靠性参数
平均故障间隔时间MTBF
在规定的条件下和规定的时间内,产品的寿命单位总数与故障总次数之比。
任务可靠度MR
产品在规定的任务剖面内完成规定功能的概率。
工作寿命
产品从开始工作到报废为止的全部工作时间。
首次翻修期限
在规定条件下,产品从交付(或开始使用)到首次经基地或工厂大修(或翻修)的工作时间和(或)日历持续时间。
贮存期限
即储存寿命,指产品在规定的条件下储存时,仍能满足规定质量要求的时间长度。
可靠性分配概念
可靠性分配的概念
系统可靠性分配就是将使用方提出的,在系统设计任务书(或合同)中规定的可靠性指标,自上而下,由大到小,从整体到局部,逐步分解,分配到各分系统,设备和元器件。
可靠性分配的原理
系统可靠性分配是求解下面的基本不等式
对于简单串联系统而言,上式就转换为
如果对分配没有任何约束条件,则上两式可以有无数个解;有约束条件,也可能有多个解。
因此,可靠性分配的关键在于要确定一个方法,通过它能得到合理的可靠性分配值的唯一解或有限数量解。
可靠性分配方法
无约束分配法
等分配法
评分分配法
比例组合法
等分配法的原理
在设计初期,即方案论证阶段,当产品没有继承性,而且产品定义并不十分清楚时所采用的最简单的分配方法,可用于基本可靠性和任务可靠性的分配。
其原理是:
对于简单的串联系统,认为其各组成单元的可靠性水平均相同。
系统可靠度为
分配给各单元的可靠度指标为
分配给第i个单元的故障率为
等分配法举例
某型抗荷服是由衣面、胶囊、拉链三个部分串联组成。
若要求该抗荷服的可靠度指标为0.9987,试用等分配法确定衣面、胶囊、拉链的可靠度指标。
这种分配法虽简单,但不太合理。
因为在实际系统中,一般不可能存在各单元可靠性水平均等的情况,但对一个新系统,在方案论证阶段进行初步分配是可取的。
评分分配法含义
在可靠性数据非常缺乏的情况下,通过有经验的设计人员或专家对影响可靠性的几种因素评分,并对评分值进行综合分析以获得各单元产品之间的可靠性相对比值,再根据该比值给每个分系统或设备分配可靠性指标。
应用该方法时,时间一般应以系统工作时间为基准。
主要用于分配系统的基本可靠性,也可用于分配串联系统的任务可靠性,一般假设产品服从指数分布。
适于方案论证和初步设计阶段。
评分因素
复杂度,技术水平,工作时间,环境条件
评分原则——分值越高说明可靠性越差
复杂度(组成的元部件数量及组装的难易程度)
最复杂的评10分,最简单的评1分。
技术水平(单元目前的技术水平和成熟程度)
水平最低的评10分,水平最高的评1分。
工作时间
单元工作时间最长的评10分,最短的评1分。
环境条件
单元工作过程中会经受极其恶劣而严酷的环境条件的评10分,环境条件最好的评1分。
分配步骤
①确定系统的基本可靠性指标,对系统进行分析,确定评分因素。
②确定该系统中“货架”产品或已单独给定可靠性指标的产品。
③聘请评分专家,专家人数不宜过少(至少5人)。
产品设计人员向评分专家介绍产品及其组成部分的构成、工作原理、功能流程、任务时间、工作环境条件、研制生产水平等情况;或专家通过查阅相关技术文件获得相关信息。
④评分。
首先由专家按照评分原则给各单元打分,填写评分表格。
再由负责可靠性分配的人员,将各专家对产品的各项评分总和,即每个单元的4个因素评分为各专家评分的平均值,填写表格。
⑤按公式分配各单元可靠性指标。
评分分配法原理
s*——系统可靠性指标;i*——各单元的故障率
Ci——第i个单元的评分系数
ωi——第i个单元的评分数
ω——系统的评分数
rij——第i个单元,第j个因素的评分数
评分分配法举例
某飞机共由18个分系统组成,其中5个分系统是已使用过的成件并已知其MFHBF,见下表。
规定飞机的可靠性指标MFHBF=2.9(飞行小时)。
试用评分分配法对其余13个分系统进行分配。
评分分配法举例
比例组合法原理
一个新设计的系统与老的系统非常相似,也就是组成系统的各单元类型相同,对这个新系统只是提出新的可靠性要求,那么就可以采用比例组合法。
根据老系统中各单元的故障率,按新系统可靠性的要求,给新系统的各单元分配故障率。
如果有老系统中各分系统故障数占系统故障数百分比的统计资料,可以按下式进行分配。
比例组合法举例一
一个液压动力系统,原故障率为256.0×10-6/h,改进设计要求故障率为200.0×10-6/h,试把这指标分配给各分系统。
比例组合法举例二
要求设计一种飞机,在5h的飞行任务时间内可靠度为0.9。
根据这种类型飞机各分系统故障百分比的统计资料,将指标分配给各分系统。
可靠性预计的概念
可靠性预计是在设计阶段对系统可靠性进行定量的估计,是根据历史的产品可靠性数据、系统的构成和结构特点、系统的工作环境等因素估计组成系统的部件及系统的可靠性。
系统的可靠性预计是根据组成系统的元件、部件的可靠性来估计的,是一个自下而上,从局部到整体、由小到大的一种系统综合过程。
根据战术技术中可靠性的定量要求分为
基本可靠性预计
任务可靠性预计(任务剖面、工作时间及功能特性等)
不可修产品
可修产品
从产品构成角度分析,可分为:
单元可靠性预计
系统可靠性预计
可靠性分配与可靠性预计的关系
两者都是可靠性设计分析的重要环节。
分配结果是可靠性预计的依据和目标,预计的相对结果是可靠性分配与指标调整的基础。
设计各阶段均相互交替,反复进行。
单元可靠性预计
说明
系统可靠性是各单元可靠性的概率综合
单元可靠性预计是系统可靠性预计的基础
直接预计系统各单元的故障率或可靠度
常用的单元可靠性预计方法:
相似产品法
评分预计法
应力分析法
故障率预计法
机械产品可靠性预计法
1.FMECA
FMECA的定义
故障模式影响及危害性分析(FailureMode,EffectsandCriticalityAnalysis,记为FMECA)是分析系统中每一产品所有可能产生的故障模式及其对系统造成的所有可能影响,并按每一个故障模式的严重程度及其发生概率予以分类的一种归纳分析方法。
FMECA是一种自下而上的归纳分析方法;
FMEA和CA。
FMECA的目的
从产品设计(功能设计、硬件设计、软件设计)、生产(生产可行性分析、工艺设计、生产设备设计与使用)和产品使用角度发现各种影响产品可靠性的缺陷和薄弱环节,为提高产品的质量和可靠性水平提供改进依据。
FMECA的作用
保证有组织地定性找出系统的所有可能的故障模式及其影响,进而采取相应的措施。
为制定关键项目和单点故障等清单或可靠性控制计划提供定性依据;为制定试验大纲提供定性信息;为确定更换有寿件、元器件清单提供使用可靠性设计的定性信息;为确定需要重点控制质量及工艺的薄弱环节清单提供定性信息。
可及早发现设计、工艺中的各种缺陷。
为可靠性(R)、维修性(M)、安全性(S)、测试性(T)和保障性(S)工作提供一种定性依据
FMECA的步骤
③危害性分析(CA)
目的是按每一故障模式的严重程度及该故障模式发生的概率所产生的综合影响对系统中的产品划等分类,以便全面评价系统中可能出现的产品故障的影响。
CA是FMEA的补充或扩展,只有在进行FMEA的基础上才能进行CA。
常用方法
风险优先数(RiskPriorityNumber,RPN)法
主要用于汽车等民用工业领域
危害性矩阵法
主要用于航空、航天等军用领域
系统可靠性设计的内容
一般包括:
元器件的选择和降额设计
元器件的容差和漂移设计
对高可靠性系统进行冗余设计
环境保护设计、热设计和三防设计
抗振动、冲击设计
电磁兼容设计和防电磁泄漏设计
可维性和可用性设计
软件可靠性设计
系统可测试性设计
容错技术
系统可靠性设计准则
系统可靠性设计准则是把已有的、相似的设备或系统的工程经验和教训总结起来,使其条理化、科学化、系统化,成为设计人员进行可靠性设计所遵循的原则和应满足的要求。
一般都是针对某个设备或系统的,也可以把各种型号的产品的可靠性设计准则的共性内容综合成某种类型的设备的可靠性设计准则。
如军用飞机控制系统和高可靠性计算机系统的准则,继承了多年设备和系统的可靠性设计经验,贯彻规范化设计,将其综合起来作为计算机应用系统可靠性准则,具有重要意义。
可靠性设计准则,不仅可指导工程技术人员进行系统可靠性设计,而且在项目评审时可用于审查设计的合理性。
如果设备或系统的设计方案与可靠性设计准则相符,说明该设备或系统的可靠性定性要求已经满足;如果因种种原因不能满足可靠性设计准则,则需要对该设计方案提出疑问,并做进一步的研究和改进设计。
制定可靠性设计准则是进行可靠性设计的重要依据;
贯彻可靠性设计准则可以提高系统的固有可靠性;
是使可靠性设计和性能设计相结合的有效方法;
贯彻可靠性设计准则,其工程实用价值高,费用低;
可靠性设计准则是各种工程经验、教训的总结。
系统可靠性设计准则的内容
简化设计准则
冗余设计准则
耐环境设计准则
热设计准则
降额设计准则
元器件选择与控制准则
电磁兼容设计准则
安全性设计准则
人机工程设计准则
采用新技术准则
稳定性设计准则
耐环境设计的内容
抗气候环境设计。
即进行热设计和三防设计。
抗机械环境设计,即抗振动、冲击设计。
抗辐射环境设计,即针对核辐射进行的防护设计。
抗电磁干扰设计,即电磁兼容性设计。
热设计产生
温度是影响电子产品可靠性的一个重要环境因素。
一般地,电子产品的故障率随着环境温度的增长呈指数增长。
半导体元器件、尤其是集成电路对温度最为敏感。
除了故障率随温度的增加呈指数增长,耐压值、漏电流、放大倍数等参数均是温度的函数。
热设计的必要性与目的
在航空航天等高科技产品中热设计技术日益得到重视。
对电子产品热设计分析的目的是基于对系统热交换过程的分析和热场的计算或测量,从热源、热流、散热等方面对电子产品进行热控制,以达到减少参数漂移,保持电气性能稳定,提高产品可靠性的目的。
系统三防设计
“三防”是指对潮湿、盐雾和霉菌的防护。
“三防”设计就是防潮湿、防盐雾和防霉菌的设计,也包含防尘及其它腐蚀气体。
潮湿、盐雾、霉菌和灰尘对系统可靠性的影响主要表现在使系统设备的绝缘性能降低、霉烂腐蚀和其他性能恶化或断路失效。
一般是:
绝缘材料被水汽所湿润,缝隙中侵入水汽后结露;
高温、高湿时霉菌容易生长,使器件变质失效;
金属表面产生电化腐蚀和使氧化作用加剧;
尘埃的堆积和水汽的湿润会造成各种材料的腐蚀。
对潮湿、盐雾、霉菌和灰尘的防护采用结构性防护、材料防护、隔离防护和工艺防护,即设计或选择良好的预防结构,选用良好的防护材料和装置,采用优良的制造工艺和可靠的涂覆层或镀层。
具体有:
采用元件密封、组件密封、零件涂覆等措施,防止腐蚀性气体介质与材料接触,如用气体、液体填充,实现全密封、硅覆盖陶瓷等气密性结构。
通过排湿气、冷却方法消除潮湿、霉菌、盐雾等影响,改善工作环境。
采用不受潮湿、盐雾、霉菌腐蚀的材料,如聚氨树脂漆、有机硅漆等,以及采用对金属可起防护作用的油漆、有机薄膜、电镀构成防护层。
对整机或系统采用加固式防护外壳。
印制板电路和组件涂覆防潮材料。
采用表面不易被破坏和防尘的结构,密封或灌封是有效的三防措施。
系统抗振动、冲击设计
振动、冲击对系统可靠性的影响
机械振动冲击对系统的可靠性也会产生影响,该类振动包括变频振动、线性加速等冲击。
在系统设备中,振动、冲击会造成元器件变形,接触不良,严重的还会造成元器件损坏。
因此,进行抗振动冲击设计,就是在设计上采用各种有效措施,减轻机械环境对系统设备可靠性的影响。
抗振动、冲击的措施
消除相关振源
消除设备内外的相关振源是设备振动与冲击防护的主要措施。
提高结构刚度,防止低频激振
设备的振动特性由其质量、刚度和阻尼特性确定。
当激振频率较低