无损检测细则.docx
《无损检测细则.docx》由会员分享,可在线阅读,更多相关《无损检测细则.docx(12页珍藏版)》请在冰豆网上搜索。
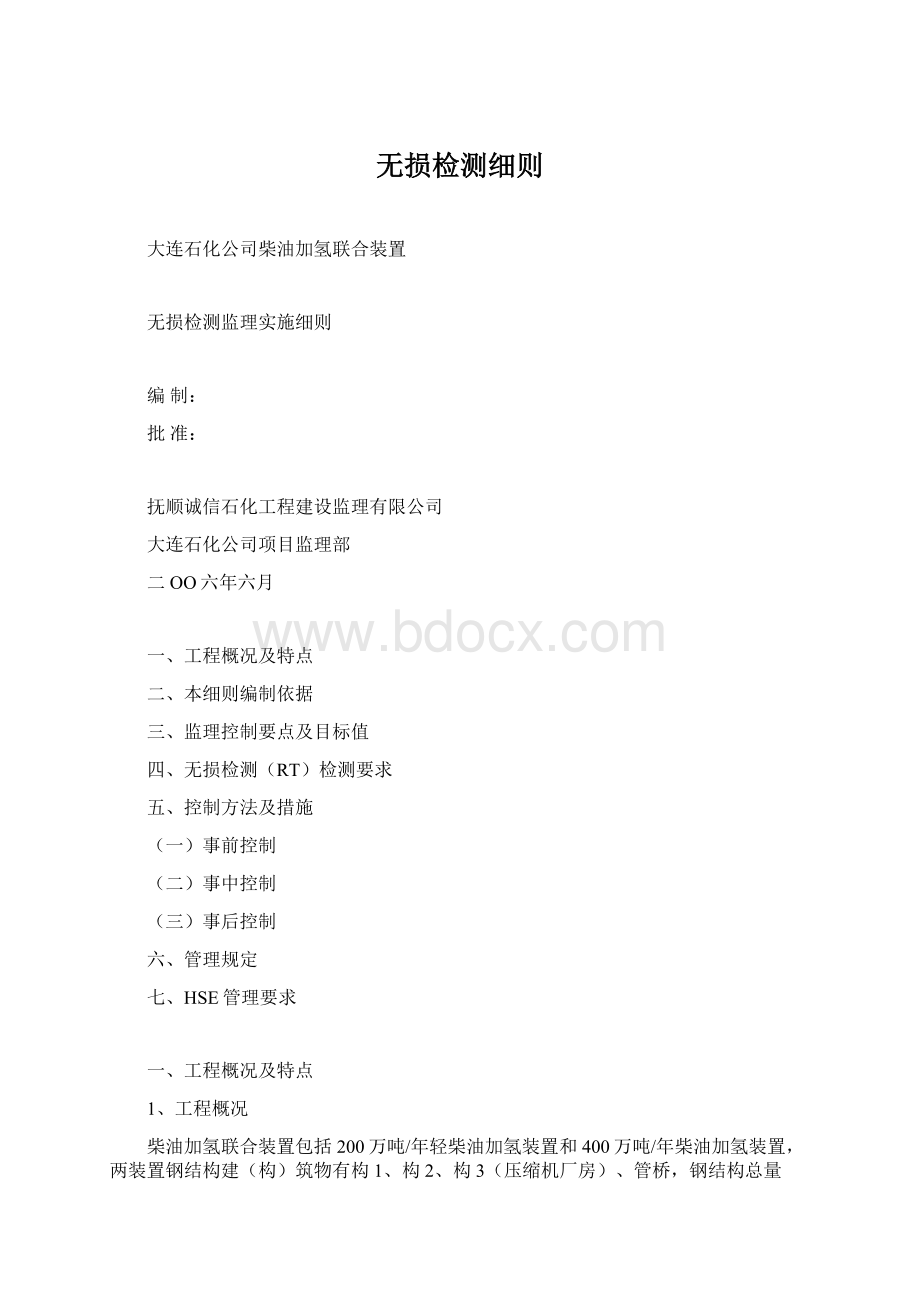
无损检测细则
大连石化公司柴油加氢联合装置
无损检测监理实施细则
编制:
批准:
抚顺诚信石化工程建设监理有限公司
大连石化公司项目监理部
二OO六年六月
一、工程概况及特点
二、本细则编制依据
三、监理控制要点及目标值
四、无损检测(RT)检测要求
五、控制方法及措施
(一)事前控制
(二)事中控制
(三)事后控制
六、管理规定
七、HSE管理要求
一、工程概况及特点
1、工程概况
柴油加氢联合装置包括200万吨/年轻柴油加氢装置和400万吨/年柴油加氢装置,两装置钢结构建(构)筑物有构1、构2、构3(压缩机厂房)、管桥,钢结构总量3000吨,材质均为Q235A,大都为热轧和焊接型材组成;两台工业炉,钢结构总量1100吨,加热炉炉管为进口TP321管材;各种工艺管道56000米,根据GB50235、SH3501及40B119的要求并结合所输送介质的危险程度和设计条件将管道分为A、B1、B2、B3、B4、C1、C2、E1、E2、E3十类;本装置两台产品汽提塔、高压换热器及柴油加氢冷高压分离器等设备因运输等条件的限制,需分段运输到现场组焊。
2、无损检测部位、检测方法、验收级别及工程量
根据设计及规范要求,本装置钢结构采用超声波检测,执行SH3507-1999《石油化工钢结构工程施工及验收规范》,按规范和图纸要求对梁、柱的对接焊缝进行超声波检测,Ⅱ级合格,具体检查部位和工程量见无损检测委托;加热炉炉管和工艺管线组对焊缝,采用X射线检测,执行JB/T4730.2-2005《承压设备无损检测》第2部分射线检测,Ⅱ级合格。
工艺管线检测比例及合格等级见表-3。
原材料复验光谱执行SH3501-2002。
具体见:
表-1,表-2
3、工程特点
1、无损检测种类多,数量大:
根据设计及规范的要求,本装置无损检测项目包括射线、超声、磁粉、着色等项目,检测数量(以RT为参考)为;
2、需要使用γ源:
因存在高压换热器、冷高压分离器等厚壁设备现场组焊,以及管道中有大口径厚壁管道的存在,在检测过程中需使用γ源进行检测;
3、装置和老生产装置区间隔小,装置西侧和南侧均为老生产区,和生产装置最近距离为20米,为检测过程中的协调工作带来了一定的困难。
二本细则编制依据
1、本工程监理规划
2、建设工程监理规范GB50319—2000
3、本工程项目的设计施工图及相关设计文件
4、大石化及联合项目管理部的相关管理规定
5、GB3323-87《钢熔化焊对接接头射线照相和质量分级》
6、JB/T4730.1~4730.6-2005《承压设备无损检测》
7、GB4792-94《放射卫生保护基本标准》
8、GB50235-97《工业金属管道工程施工及验收规范》
9、SH3501-2002《石油化工剧毒、可燃介质管道工程施工及验收规范》
10、GB50236-98《现场设备、工业管道焊接工程施工及验收规范》
11、JB/T7902-1999《线形像质计》
12、JB/T7903-1999《工业射线照相底片观片灯》
13、SH3507-1999《石油化工钢结构工程施工及验收规范》
三、监理控制要点、目标值
四、无损检测(RT)工艺控制
1、射线检测时机及要求
(1)焊道热处理结束,经质检员外观检查确认合格后方可进行检测,检测合格后再进行焊道热处理;对有延迟裂纹倾向的材料,应先进行焊后热处理,合格后在焊接完成24小时后再进行射线检测。
(2)表面要求:
焊缝的表面(包括焊缝余高)不规则状态在底片上的图像应不掩盖焊缝中的缺陷或与之相混淆,否则应作适当处理。
2、胶片选用及黑度要求
(1)采用AGFA(C7)工业胶片。
胶片规格为:
80×18080×24080×300
()增感屏的选用:
前屏0.03mm后屏0.1mm。
4.2.3X射线检测底片黑度范围为D=2.0~4.0。
3、焊缝、布片编排
焊缝编号与施工单线图焊口号编号统一,使用标记带确定片位,在焊缝侧用可长时间留存的白色标示画出片位。
4、像质计及放置位置
(1)线形像质计的型号和规格应符合JB/T4730.1~4730.6-2005的规定。
(2)像质计型号按下列表规定选择,见下表
透照厚度mm
2-12
12-50
像质计型号
III(Fe10/16)
II(Fe6/12)
(3)分段透照,每张底片上必须有一个像质计,中间一根钢丝位于底片一端1/4处,且细丝朝外,像质计放在射线源工件表面上,且垂直横跨焊缝。
当射线源一侧无法放置像质计时,也可放在胶片一侧的工件表面上,但像质计指数应提高一级或通过对比试验,使实际像质计指数达到规定的要求,像质计放在胶片一侧工件表面上时,应附加“F”标记以示区别。
(4)采用射线源置于圆心位置的周向曝光时,像质计应每隔90°放置一个。
(5)返工片、抽查片必须每张底片上有标准搭接,如必要应加中心标示。
(6)外径>89mm的钢管,焊缝透照应采用JB/T4730.1~4730.6-2005规定的Ⅱ、Ⅲ像质计,一般放置于胶片侧管子表面被检出长度的1/4处,壁厚大于20mm时需做对比试验。
(7)外径≤89mm的钢管,其焊缝透照应采用JB/T4730.1~4730.6-2005附录中的规定I型专用像质计,一般放在射源侧焊缝余高中心处,也可放在胶片一侧工件表面上。
(8)如数根管接头在一张底片上同时显示时,应至少在最外侧的管子上各放一个像质计。
5、透照布置
(1)依照现场条件,选择环缝内照法、环缝外照法、双壁单影法和双壁双影法四种透照方式。
(2)环缝透照时,尽量选用中心内照法。
(3)焦距必须同时满足几何不清晰度及透照厚度比k值的要求
(4)对于环缝透照应按不同的透照方式先求出100%透照整圈焊缝满足K=1.1要求的最少曝光次数N,然后再确定环缝的一次透照长度L3。
6、定位和识别标记
(1)定位标记:
透照时焊缝透照部位应有搭接标记(),和中心标(),搭接标记起确定有效评定长度的作用。
中心曝光时,定位标记置于被检工件内外均可。
单壁单影单张透照时,定位标记应置于射线源侧。
(2)识别标记:
为了使每张射线底片与工件被检部位始终可以对照,在透照过程中应将铅质识别标记和定位标记与被检区域同时透照在底片上。
识别标记必须有工程(产品)编号、焊缝编号、焊工号、底片号、厚度、搭接标记和中心标记、年月日等标记,铅字距离焊缝边缘至少5mm。
7、射线能量的选择
透照前,根据所检工件规格,严格按曲线选择曝光参数、操作。
8、暗室处理
严格按《暗室操作规程》进行。
9、焊接接头返工及复探
(1)不合格的底片由评片人员下达“焊接接头返工通知单”,一式二份,连同返工底片复制件交焊接技术员,可由探伤人员协助焊接技术员确定返工部位(壁厚大于25mm时可使用超声波探伤仪进行缺陷定位)。
(2)焊接接头返工后由焊接技术员回置返工通知单,进行复探。
(3)返工片按返工次数分别在焊缝编号后加R,R1,以示区别。
10、返修程序
当发现超标缺陷时,按以下程序返修。
11、底片的质量要求
(1)底片黑度控制在4.2.3条规定的范围内,这些黑度的数值包括不大于0.3的本底灰雾度。
(2)像质指数达到标准要求,摆放位置正确,在焊缝影像上如能清晰地看到长度不小于10mm的像质计金属丝影像,就认为是可识别的。
(3)各种标记齐全,摆放整齐,位置正确,且不掩盖被检焊缝影象。
(4)在较黑背影下无“B”的较淡影象。
(5)底片有效评定区域内不得有因胶片处理不当引起的缺陷或其它妨碍底片评定的缺陷。
(6)凡不符合上述要求之一的底片均应重照。
12底片观察
(1)评片室内光线应暗淡,室内照明不应在底片上产生反射。
(2)观片灯应能观察最高黑度为4.5以上,且亮度可调。
13底片的初评与审核
(1)按JB/T4730.1-JB/T4730.6-2005标准Ⅱ级合格进行评定。
(2)评片过程中应具备该产品单线图,现场透照记录,评片记录,暗室记录和射线检测委托单,布片图等。
(3)在评片过程中,发现异议应及时去现场了解被检件情况,与复评员、无损检测责任工程师汇评。
五、控制方法及措施
(一)事前控制
1、审查无损检测单位的资质是否符合规定要求
(1)从事射线检测工作的无损检测单位必须具有建筑施工企业无损检测承包资质、国家技监局颁发的《锅炉压力容器压力管道及特种设备检验许可证》,国家或地方环卫部门颁布发的《射线装置工作许可证》,(放射性同位素工作许可证),并具有承担国内重大工程无损检测工作的经验。
(2)从事无损检测人员必须持有国家质量技术监督部门颁发的无损检测资格证书,从事与资格证书级别、类别相应的无损检测工作,并承担相应责任。
合同中确认的高级无损检测人员应按规定到工程现场工作。
(3)无损检测机构必须建立符合ISO9001-2000标准的质量体系,并保持体系有效运转。
2、审查从事无损检测的人员是否符合规定要求
(1)无损检测人员须持有国家质量技术监督部门核发的资格证书,且从事的工作应与资格证相符,Ⅱ级及以上人员进行评片、审核、编制报告;无损检测责任师对报告进行审核,签发,盖章后有效。
从事射线检测的人员还应持有卫生防疫部门核发的放射工作人员上岗许可证。
(2)检测人员校正视力不得低于1.0,评片人员校正视力能读出距离400mm高为0.5mm、间距为0.5mm的一组印刷体英文字母;从事表面检测的人员不得有色盲。
(3)所有检测人员必须身体健康,责任心强,不弄虚作假,玩忽职守。
3、审查无损检测设施、设备是否满足要求
工程检测使用的无损检测设备、仪器应按有关规定定期检验并合格,暗室、评片室的环境条件满足相关技术要求时方能投用。
4、审查无损检测实施方案是否切实可行。
5、审查无损检测实施计划。
(二)事中控制
1、对检测比例不是百分之百的管道或部位,监理人员进行现场指口,指口比例不少于检测数量的20%。
所指的口数及部位要符合GB50237及SH3501的要求。
2、检查专用检测工艺卡,抽查技术交底情况
3、审核无损检测报告
4、专业监理人员对底片进行复评。
对于设计要求,100%射线检测的管道和现场组焊设备,射线底片复评率为100%;对天低温钢、使合金钢材料的管道和组焊设备,射线底片复评率为100%;对天其它材料,如设计要求执行《石油化工有毒、可燃介质管道工程施工及验收规范》(SH3501-2002),则射线底片复评率为50%,如设计要求执行《工业金属管道工程施工及验收规范》(GB50235-97),则射线底片复评率为20%。
(三)事后控制(第三方检测)
1、现场随机抽拍、检测复位和其它检测方法的抽检比例为原检测总量的5%,且不少于3处。
如抽检中发现不合格焊口,应加倍抽检,检查如再发现不合格焊口,则全数检测。
2、设计文件规定的100%射线检测的,用同样的检测方法进行抽检,检查比例为焊口数的1%,且不少于1道。
六、管理规定
1、容器、管道的《无损检测通知单》应附容器排版图、管道单线图以标识抽人部位。
抽检前,抽检人员应核对实物标记,确认无误后,方可实施检测。
2、无损检测单位应认真做好检测记录,及时出具检测报告。
检测报告填写应规范,各项签证、盖章手续齐备。
3、监理机构应及时核对检测结果,汇总各项检测记录或报告,按装置、区域、施工单位申报平行检验(报验)一次合格率,按时编报质量月报。
4、对于发现的问题,如需退货、返工、返修、复检或扩检时,由专业监理工程师将其列入不符合项,并跟踪封闭管理。
5、对于检测发现问题而采取的退货、拒收、返工、返修、复检、扩检等处理措施所发生的费用,由问题责任单位承担。
6、检测和测试作业的安全技术、劳动保护、环境保护等,执行国家、中国石油天然气集团及大连石化公司联合项目管理部HSE部的有关规定。
7、对于出现检测质量无法追踪的问题,应查明原因,分清责任,酌情处理。
若发现有作假行为进行通报并按合同约定严肃处理。
七、HSE管理规定
1、射线作业前,一般由探伤单位负责人要提前24小时提出申请,办理《射线作业许可证》,监理部进行施工协调,经IPMT-HSE管理部批准后,方可进行射线作业;对受影响的相关方,在施工调度会议上进行通报。
探伤单位要以《射线作业通告》的形式通知到相关方,并经他们签字确认。
特殊情况下,经IPMT-HSE管理部发布射线作业信息,提前通知现场的相关单位,经确认不会对相关方产生影响、落实安全措施,办理《射线作业许可证》后方可进行射线作业;严禁未经批准,擅自进行射线作业。
2、为使射线作业可能产生的危害降至最小,同时又不影响正常的施工,《射线作业许可证》的允许作业时间一般应为夜间23:
00点至次日凌晨6:
00点;必须在批准的区域内进行作业,严禁越出批准的作业区外作业。
3、批准的《射线作业许可证》和受影响的相关方签字的《射线作业通告》要进行张贴公示;《射线作业通告》要复印发送至受影响的所有相关方。
4、射线作业前,监理人要进行清场,确保周围无关人员安全撤离,正确设置好警戒线,根据放射源强度确定安全防护范围;至少在作业区的四个角设置警戒灯(频闪灯),对重要路口和人员经常出入的道口要派专人看守。
5、射线作业人员作业时,必须穿戴防护服并佩带个人计量仪。
6、操作过程中,一旦出现射线源失控事故,必须立即通知相关人员迅速撤离污染现场,设置安全警戒线、警戒岗,严禁其它人员进入,并立即向上级领导、HSE管理和治安保卫等有关部门汇报。
表-1
炉管
检测比例
检测部位
检测方法
每焊口(件)
检测量
验收级别
固定口
100%
焊缝
RT-X
6张
Ⅱ
活口
100%
焊缝
RT-X
6张
Ⅱ
对接焊口
100%
打底层
PT
延长米
Ⅰ
光谱
10%
母材/管件
直读
2点点元素
/
表-2
工艺管线
检测比例
检测部位
检测方法
每焊口(件)
检测量
验收级别
DN≤50
见无损检测委托
焊缝
PT
延长米
Ⅰ
50≤DN≤80
见无损检测委托
焊缝
RT-X
2
Ⅱ
DN100
见无损检测委托
焊缝
RT-X
6
Ⅱ
DN125
见无损检测委托
焊缝
RT-X
6
Ⅱ
DN150
见无损检测委托
焊缝
RT-X
6
Ⅱ
DN200
见无损检测委托
焊缝
RT-X
6
Ⅱ
DN250
见无损检测委托
焊缝
RT-X
6
Ⅱ
DN300
见无损检测委托
焊缝
RT-X
6
Ⅱ
DN400
见无损检测委托
焊缝
RT-X
8
Ⅱ
DN500
见无损检测委托
焊缝
RT-X
8
Ⅱ
DN600
见无损检测委托
焊缝
RT-X
10
Ⅱ
DN700
见无损检测委托
焊缝
RT-X
12
Ⅱ
DN800
见无损检测委托
焊缝
RT-X
12
Ⅱ
DN900
见无损检测委托
焊缝
RT-X
12
Ⅱ
DN1000
见无损检测委托
焊缝
RT-X
14
Ⅱ
光谱
见无损检测委托
母材/管件联接件
直读
合金钢
2点点元素
/
不锈钢
3点点元素
/
硬度
见无损检测委托
焊缝热影响区母材
直读
5点
/
表-3
管道对接焊缝检验比例、合格等级
管道等级
输送介质
设计压力P
MPa(表压)
设计温度t
℃
检测百分率
%
合格等级
SHA
毒性程度为极度危害介质(苯除外)和毒性程度为高度危害介质的丙烯腈、光气、二硫化碳和氟化氢
任意
任意
100
Ⅱ
有毒、可燃介质
P≥10.0
任意
100
Ⅱ
SHB
有毒、可燃介质
4.0≤P≤10.0
t≥400
100
Ⅱ
毒性程度为极度危害介质的苯、甲A类液化烃
P<10.0
-29≤t<400
40
Ⅱ
毒性程度为高度危害介质(丙烯腈、光气、二硫化碳和氟化氢除外)
P<10.0
-29≤t<400
20
Ⅱ
甲类可燃气体和甲B类可燃液体
乙类可燃气体和乙A类可燃液体
P<10.0
-29≤t<400
10
Ⅱ
P<4.0
t≥400
Ⅱ
SHC
毒性程度为中度、轻度危害介质和乙B类、丙类可燃介质
4.0≤P≤10.0
t≥400
100
Ⅱ
P<10.0
-29≤t<400
5
Ⅲ
P<4.0
t≥400
Ⅲ
SHD
有毒、可燃介质
任意
t<-29
100
Ⅱ
SHE
——
4.0≤P<10.0
t≥400
40
Ⅱ
——
4.0≤P<10.0
t<400
10
Ⅲ
1.0≤P<4.0
t≥400
——
1.0<P<4.0
t<400
5
Ⅲ
P≤1.0
t≥400
注:
(1)在被检测的焊接接头中,固定焊接接头不得少于检测数量的40%,且不少于一个焊接接头;
(2)上表所列检测比例为每名焊工焊接的同材料级别、同规格管道的焊接接头;
(3)消防水、仪表风管道的焊接接头检验比例为5%;
(4)对于角焊缝用磁粉或着色检验,检验比例同上表,合格等级均为Ⅰ级。