原作业指导书doc.docx
《原作业指导书doc.docx》由会员分享,可在线阅读,更多相关《原作业指导书doc.docx(21页珍藏版)》请在冰豆网上搜索。
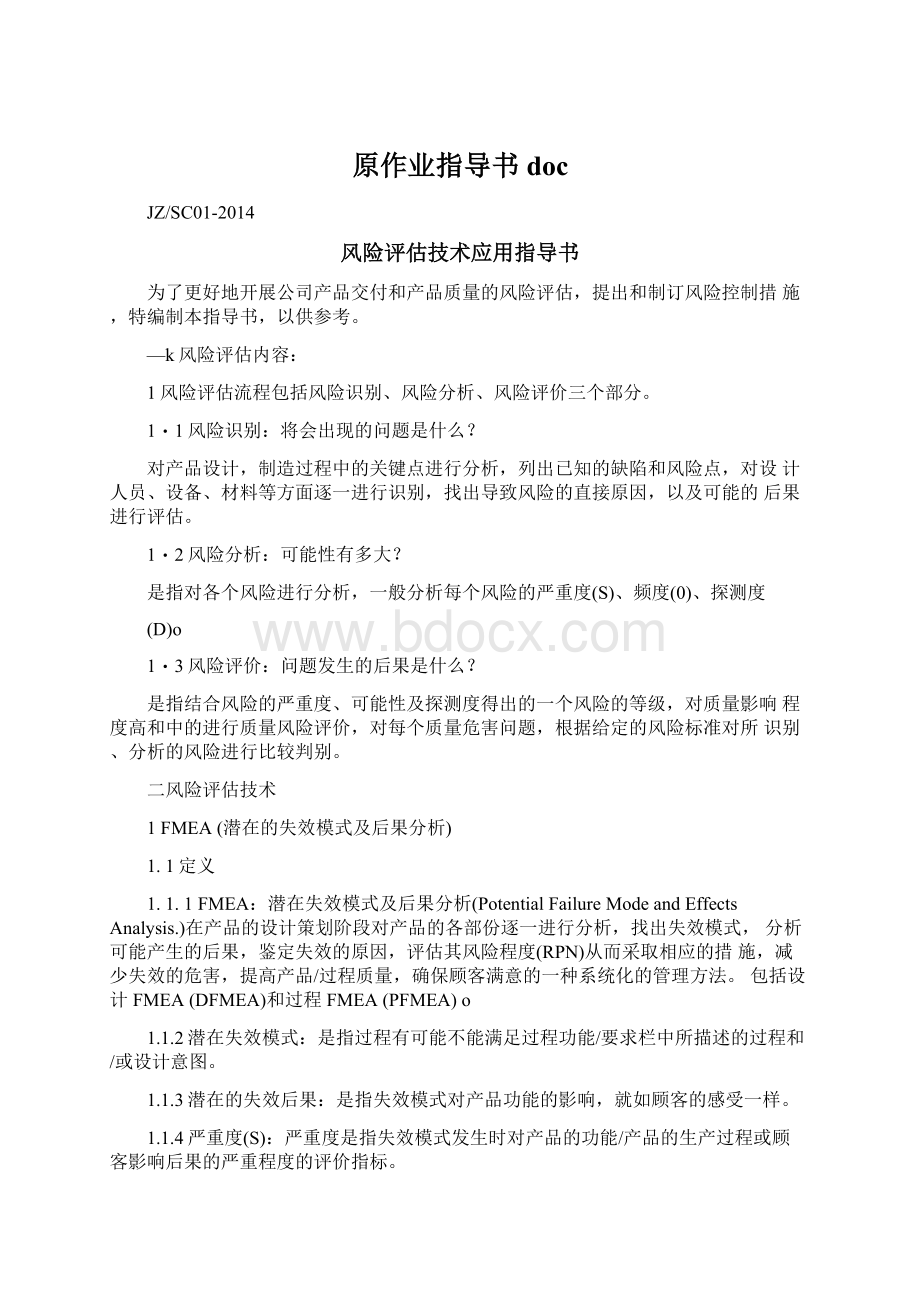
原作业指导书doc
JZ/SC01-2014
风险评估技术应用指导书
为了更好地开展公司产品交付和产品质量的风险评估,提出和制订风险控制措施,特编制本指导书,以供参考。
—k风险评估内容:
1风险评估流程包括风险识别、风险分析、风险评价三个部分。
1・1风险识别:
将会出现的问题是什么?
对产品设计,制造过程中的关键点进行分析,列出已知的缺陷和风险点,对设计人员、设备、材料等方面逐一进行识别,找出导致风险的直接原因,以及可能的后果进行评估。
1・2风险分析:
可能性有多大?
是指对各个风险进行分析,一般分析每个风险的严重度(S)、频度(0)、探测度
(D)o
1・3风险评价:
问题发生的后果是什么?
是指结合风险的严重度、可能性及探测度得出的一个风险的等级,对质量影响程度高和中的进行质量风险评价,对每个质量危害问题,根据给定的风险标准对所识别、分析的风险进行比较判别。
二风险评估技术
1FMEA(潜在的失效模式及后果分析)
1.1定义
1.1.1FMEA:
潜在失效模式及后果分析(PotentialFailureModeandEffectsAnalysis.)在产品的设计策划阶段对产品的各部份逐一进行分析,找出失效模式,分析可能产生的后果,鉴定失效的原因,评估其风险程度(RPN)从而采取相应的措施,减少失效的危害,提高产品/过程质量,确保顾客满意的一种系统化的管理方法。
包括设计FMEA(DFMEA)和过程FMEA(PFMEA)o
1.1.2潜在失效模式:
是指过程有可能不能满足过程功能/要求栏中所描述的过程和/或设计意图。
1.1.3潜在的失效后果:
是指失效模式对产品功能的影响,就如顾客的感受一样。
1.1.4严重度(S):
严重度是指失效模式发生时对产品的功能/产品的生产过程或顾客影响后果的严重程度的评价指标。
1.1.5潜在的失效起因:
是指失效是怎样发生的,并应依据可以纠正或可以控制的原则予以描述。
1.1.6频度(0):
指某一特定的起因/机理发生的可能性。
1.1.7探测度(D):
是指产品在投产之前,利用现行控制方法来探测失效的潜在起因/机理的能力评价指标。
1.2职责
1.2.1DFMEA小组:
负责组织编制设计FMEAo
1.2.2PFMEA小组:
负责组织编制过程FMEAo
1.3编制设计FMEA(DFMEA)
1.3.1编制DFMEA的时机:
在产品的设计阶段或之前进行;
1.3.2编制DFMEA的基本要求:
负责的工程师要有一定的FMEA和团队工作推进经验。
1.3.3编制过程
1.3.3.1根据产品要求的设计输入编写DFMEA
1.3.3.2FMEA编号:
•填入DFMEA文件的编号,以便查询。
1.3.3.3项目:
•注明正在进行设计分析的产品或部件的名称和编号。
1.3.3.4过程责任:
•填入部门和小组。
1.3.3.5编制者:
•填入负责编制DFMEA的工程师的姓名、电话和所在公司的名称。
1.3.3.6产品/项目:
•填入所分析的设计(如已知)。
1.3.3.7关键日期:
•填入初次DFMEA应完成的时间。
1.3.3.8FMEA日期:
•填入编制DFMEA原始稿的日期及最新修订的日期。
1.3.3.9核心小组:
•列出有权确定和/或执行任务的责任部门的名称和负责人的姓名。
1.3.3.10设计功能/要求
•根据设计输入的要求确定每一参数的要求或功能,并填入被分析的产品
部件简要说明。
1.3.3.11潜在失效模式:
•按照部件的设计参数列出特定参数的每一件潜在的失效模式,前提是这种失效可能发生,但不一定发生的;且应以规范化或技术术语来描述。
1.3.3.12潜在失效后果:
•要根据顾客可能发生或经历的情况来描述失效后果,顾客既可能是内部的顾客也可能是最终用户。
如果失效模式可能影响安全性或对法规的符合性,要清楚地予以说明。
•对于最终使用考来说,失效的后果应一律采用产品或系统的性能来描述。
1.3.3.13严重度(S)
•是单一的DFMEA范围内的相对定级结果。
•严重度数值的降低只有通过设计更改或重新设计才能实现。
•相同的失效后果,严重度分值是相同的。
•推荐的设计FMEA严重度评价准则见附件。
1.3.3.14级别:
•可用于对那些可能需要附加的过程控制的部件、子系统或系统的特殊产品或设计特性的分级;
•也可用于突出高优先度的失效模式以进行工程评定。
1.3.3.15失效的潜在起因/机理:
•尽可能地列出可归结到每一失效模式的每一件潜在起因。
•起因列出的方式应有利于有针对性对起因采取补救的努力。
1.3.3.16频度:
•描述出现的可能性的级别数具有相对意义,而不是绝对的。
•通过设计更改或过程更改来预防或控制失效模式的起因/机理是可能导致发生频度数降低的唯一的途径。
•为保证连续性,应采用一致的发生频度定级方法。
•推荐的评价准则见附件。
1.3.3.17现行过程控制:
•是对尽可能地防止失效模式或其起因/机理的发生或者探测将发生的失效模式或其起因/机理的控制的说明。
•有两类设计控制可以考虑:
◊预防:
防止失效的起因/机理或失效模式出现,或者降低其出现的几率。
◊探测:
探测岀失效的起因/机理或者失效模式,导致采用纠正措施。
1.3.3.18探测度
•是一个在某一DFMEA范围内的相对级别。
•为了获得一个较低的定级,通常计划的设计控制必须予以改进。
1.3.3.19风险顺序数:
•风险顺序数(RPN)是严重度(S),频度(0)和探测度(D)的乘积,也就是(S)X(0)X(D)二RPN,(1WRPNW1000)。
•根据实际需要,现规定当RPN>120吋,就一定有采取纠正/预防措施。
1.3.3.20建议的措施
•针对高严重度,高RP7值和小组指定的其它项目进行预防/纠正措施的工程评价。
•如果工程评价认为无需建议措施,则应在本栏内注明“无”。
1.3.3.21建议措施的责任
•填入每一项建议措施的责任者以及预计完成的目标口期。
1.3.3.22采取的措施
•在实施了措施之后,填入实际措施的简要说明以及生效日期
1.3.3.23措施结果
•在确定了预防/纠正措施以后,估算并记录严重度、频度和探测度值的结果。
计算并记录RPN的结果。
•如果没有采取任何措施,将相关栏空白即可。
1.3.3.24跟踪措施
负责设计的工程师应负责保证所有的建议措施已被实施或已妥善落实。
1.4编制过程FMEA(PFMEA)
1.4.1编制过程FMEA的时机
1.4.1.1在可行性阶段或之前进行;
1.4.1.2在生产用工装到位之前;
1.4.1.3建立或修改PMP(质量管理计划)之前应进行。
1.4.2编制过程FMEA的基本要求
1.4.2.1负责的工程师要有一定的FMEA和团队工作推进经验。
1.4.2.2过程FMEA假定所设计的产品能够满足设计要求。
1.4.2.3过程FMEA不依靠改变产品设计来克服过程中的薄弱环节,但是它要考虑与计划的制造或装配过程有关的产品设计特性,以最大限度的保证产品能够满足顾客的要求和期望。
1.4.2.4应考虑从单件部件到总成的所有的制造工序。
1.4.3编制过程FMEA
1.4.3.1根据产品要求或工序做岀产品流程图,这件流程图应明确与每一工序相关的产品/过程特性。
1.4.3.2FMEA编号:
•填入FMEA文件的编号,以便查询。
1.4.3.3项目:
•注明正在进行过程分析的产品或部件的名称和编号。
1.4.3.4过程责任:
•填入部门和小组。
1.4.3.5编制者:
•填入负责编制FMEA的工程师的姓名。
1.4.3.6产品/项目:
•填入所分析的设计/过程将要应用和/或影响的产品/项目(如已知)。
1.4.3.7关键日期:
•填入初次FMEA应完成的时间,该日期不应超过计划的投入生产日期;对于组织,初始的FMEA日期不应超过顾客要求的生产件批准过程(PPAP)的提交日期。
1.4.3.8FMEA日期:
•填入编制FMEA原始稿的日期及最新修订的日期。
1.4.3.9核心小组:
•列出有权确定和/或执行任务的责任部门的名称和件人的姓名。
1.4.3.10过程功能/要求
•根据产品流程图确定每件工序的要求或功能,并填入被分析过程或工序简要说明。
1.4.3.11潜在失效模式:
•按照产品、部件、工序或过程特性,列出特定工序的每一件潜在的失效模式,前提是这种失效可能发生,但不一定发生的;且应以规范化或技术术语来描述。
1.4.3.12潜在失效后果:
•要根据顾客可能发生或经历的情况来描述失效后果,顾客既可能是内部的顾客也可能是最终用户。
如果失效模式可能影响安全性或对法规的符合性,要清楚地予以说明。
•对于最终使用者来说,失效的后果应一律采用产品或系统的性能来描述。
•如果顾客是下一道工序或后续序/工位,失效的后果应用过程/工序性能来描述。
1.4.3.13严重度(S)
•是单一的FMEA范圉内的相对定级结果。
•严重度数值的降低只有通过设计更改或重新设计才能实现。
•相同的失效后果,严重度分值是相同的。
•推荐的过程FMEA严重度评价准则见附件。
1.4.3.14级别:
•可用于对那些可能需要附加的过程控制的部件、子系统或系统的特殊产品或过程特性的分级;
•也可用于突出高优先度的失效模式以进行工程评定。
•如果过程FMEA中确定了分级,应通告负责设计的工程师,因为这可能影响涉及控制项目辨别的工程文件。
1.4.3.15失效的潜在起因/机理:
•尽可能地列出可归结到每一失效模式的每一件潜在起因。
•起因列出的方式应有利于有针对性对起因采取补救的努力。
1.4.3.16频度:
•描述出现的可能性的级别数具有相对意义,而不是绝对的。
•通过设计更改或过程更改来预防或控制失效模式的起因/机理是可能导致发生频度数降低的唯一的途径。
•为保证连续性,应采用一致的发生频度定级方法。
•推荐的评价准则见附件。
1.4.3.17现行过程控制:
•是对尽可能地防止失效模式或其起因/机理的发生或者探测将发生的失效模式或其起因/机理的控制的说明。
•有两类过程控制可以考虑:
◊预防:
防止失效的起因/机理或失效模式出现,或者降低其出现的几率。
◊探测:
探测出失效的起因/机理或者失效模式,导致采用纠正措施
1.4.3.18探测度
•是一个在某一FMEA范围内的相对级别。
•为了获得一个较低的定级,通常计划的过程控制必须予以改进。
1.4.3.19风险顺序数:
•风险顺序数(RPN)是严重度(S),频度(0)和探测度(D)的乘积,也就是(S)X(0)X(D)二RPN,(1WRPNW1000)。
•根据实际需要,现规定当RPN>120吋,或S〉8吋,就一定有采取纠正/预防措施。
1.4.3.20建议措施
•针对高严重度,高RP7值和小组指定的其它项目进行预防/纠正措施的工程评价
•如果评价认为无需建议措施,则应在本栏内注明“无”。
1.4.3.21责任及目标完成口期
•填入每一项建议措施的责任者以及预计完成的目标日期。
1.4.3.22采取的措施
•在实施了措施之后,填入实际措施的简要说明以及生效日期
1.4.3.23措施结果
•在确定了预防/纠正措施以后,估算并记录严重度、频度和探测度值的结
果。
计算并记录RPN的结果。
•如果没有采取任何措施,将相关栏空白即可。
1.4.4跟踪措施
1.4.4.1负责过程的工程师应负责保证所有的建议措施已被实施或已妥善落实。
2风险矩阵分析法
2・1定义风险的严重性(S)、可能性(频度0)、不可检测性(D)的级别(模板)。
2.1.1可以按高、中、低定义(模板一):
风险的严重性(S)
类别
严重性系数
标准
严重
3高
一般
2中
轻微
1低
风险的可能性或频度(0)
类别
严重性系数
标准
几乎肯定发生
3高
可能发生
2中
儿乎不可能发生
1低
风险的不可检测性(D)
类别
严重性系数
标准
可检测性小
3高
中等可检测性
2中
可检测性高
1低
2.1.2可以按1至5的级别定义(模板二)
风险的严重性(S)
类别
严重性系数
标准
5
4
3
2
1
风险的可能性或频度(0)
类别
严重性系数
标准
5
4
3
2
1
风险的不可检测性(D)
类别
严重性系数
标准
5
4
3
2
1
2.2风险评价
2.2.1通过评价风险的严重性(S)和可能性(0)和/或不可检测性(D)从而确认风险的等级叩风险水平。
根据风险的严重性(S)和可能性(0)确定风险优先排序RPR(RiskPriorityRanking);根据风险的严重性(S)和可能性(0)及不可检测性(D)确定风险优先值RPN(RiskPriorityNumber)o
2.2.2风险优先排序(RPR)二风险的严重性(S)X可能性(频度0)
2.2.3根据RPR制定风险评估矩阵:
风险评估矩阵
3高
3中
6高
9高
2中
2低
4中
6高
1低
1低
2低
3中
1低
2屮
3高
可能性
A
严重性
2.2.4风险优先值(RPN)二风险严重性(S)X可能性(频度0)X不可检测性(D)
2.3风险控制
2.3.1风险控制就是将风险降低到一个可以接受的水平。
2.3.2第一步,确定风险可接受水平;按上式计算所有的RPN值,并列出所有RPN值,以根据中位数的95%可信限,确定风险接受水平。
2.3.3第二步,根据风险分析结果,比较现有风险水平与可接受风险水平;
2.3.4第三步,对超出可接受水平,或严重性较高的风险,进行汇总,分析,按《变更控制管理标准规程》(SMP)、《预防和纠正措施管理规程》(SMP),采取措施降低、控制或消除风险。
2.3.5第四步,风险水平和定义
2.3.5.1对于风险优先排序法,风险级别按“高、中、低”定义。
2.3.5.2对于风险因子按1、2、3定义时其风险水平及定义按下表:
风险水平
定义(RPN)
高
10—27
此风险必须降低
中
3〜9
此风险尽可能降低
低
1〜3
通常此类风险可以接受
2.3.5.3对于风险因子按1、2、3、4、5定义时,其风险水平按下表定义:
风险水平
定义(RPN)
高
25〜125
此风险必须降低
中
15〜24
此风险尽可能降低
低
<15
通常此类风险可以接受
2.3.5.4同时应考虑严重度(S),如严重度级别很高,应优先考虑降低其风险。
此时可根据SOD值的大小决定风险降低的优先排序。
在风险评估过程中,一般严重度的级别不会改变,主要考虑降低风险发生的可能性和增加可检测性。
附件1相关推荐评价准则
表1・推荐的DFMEA严重度评价准则
后果
评定准则:
后果的严重度
严重度
无警告的严重危害
这是一种非常的失效形式,它是在没有任何失效预兆的情况下影响到总成安全、严重的环境污染或不符合政府的法规
10
有警告的严重危害
这是一种非常的失效形式,是在具有失效预兆的前提下所发生的,影响到总成安全、严重的环境污染和/或违返不符合政府的法规
9
很高
总成/项ri不能运行(丧失基木功能)
8
高
/项H可运行,但性能下降,顾客非常不满意
7
中等
总成/项H可运行,但操作性或方便性项忖不能运行,顾客不满意
6
低
总成/项目可运行,但操作性或方便性项目的性能下降,顾客冇些不满意
5
很低
配合和外观等项目不舒服,大多数顾客(75%以上)能感觉到有缺陷
4
轻微
配合和外观等项目不舒服,50%的顾客能感觉到有缺陷
3
很轻微
配合和外观等项H不舒服,有辨识能力的顾客(25%—下)能感觉到有缺陷
2
无
无可辨别的后果
1
表2推荐的DFMEA频度评价准则
失效发生可能性
可能的失效率*
频度
很高:
持续发生失效
M100个每1000产品/项目
10
50个每1000产品/项H
9
高:
经常发生失效
20个每1000产品/项目
8
10个每1000产品/项目
7
中等:
偶然性失效
5个每1000产品/项目
6
2个每1000产品/项目
5
低:
相对很少发生失效
1个每100()产品/项目
4
0.5个每1000产品/项目
3
极低:
失效不太可能发生
0」个每1000产品/项目
2
wo.oi个每looo产品/项n
1
表3•推荐的DFMEA探测度评价准则
探测度
评价准则:
设计控制可能探测出来的可能性
定级
绝对不肯定
设计控制不能和/或不可能找出潜在失效的原因/机理和后续的失效模式,或根木没有设计控制
K)
很极少
设计控制只有极少的机会能找出潜在失效的原因/机理及后续的失效模式
9
极少
设计控制只冇极少的机会能找出潜在失效的原因/机理及后续的失效模式
8
很少
设计控制有很少的机会能找出潜在失效的原因/机理及后续的失效模式
7
少
设计控制有较少的机会能找出潜在失效的原因/机理及后续的失效模式
6
中等
设计控制有屮等的机会能找出潜在失效的原因/机理及后续的失效模式
5
中上
设计控制冇屮上多的机会能找出潜在失效的原因/机理及后续的失效模式
4
多
设计控制有较多的机会能找出潜在失效的原因/机理及后续的失效模式
3
很多
设计控制有很多的机会能找出潜在失效的原因/机理及后续的失效模式
2
儿乎肯定
设计控制儿乎肯定可以查出潜在失效的原因/机理及后续的失效模式
1
表4推荐的PFMEA严重度评价准则
后果
评定准则:
后果的严重度
当潜在失效模式模式导致最终顾客和/或一个制造/装配厂产生缺陷时便得出相应的定级结果。
最终顾客永远是首先考虑的。
如果两种可能都存在的,采用两个严重度值中的校高者。
(顾客的后果)
评定准则:
后果的严重度
当潜在失效模式模式导致至最终顾客和/或i个制造/装配厂产生缺陷时便得出相应的定级结果。
最终顾客永远是首先考虑的。
如果两种可能都存在的,采用两个严重度值中的校高者。
(制造/装配后果)
严重度级别
无警告的危害
当潜在的失效模式在无警告的情况下影响到产品安全运行和/或涉及不符合政府法规的情况时,严重度定级非常高
或可能在五警告的情况下对(机械或总成)操作员造成危害
10
有警
告的
危害
当潜在的失效模式在冇警告的情况下影响到产品安全运行和/或涉及不符合政府法规的情况时,严重度定级非常高
或可能在冇警告的情况下对(机械或总成)操作员造成危害
9
很高
产品/项H不能工作(丧失基本功能)
或100%的产品可能需要报废:
或者总成/项目在返修部门返修1个小时以上
8
高
产品/项目可能运行但性能水平下降顾客非常不满意
或产品需进行挑选,一部分(小于100%)报废,或者总成/项冃在返修部门进行返修的时间在0.5—1小吋
7
中筹
产品/项H可运行但操作性/便利性项H不能运行。
顾客不满意
或--部分(小于100%)产品可能需要报废,不需挑选或总成/项H需在返修部门返修少于0.5小吋
6
低
产品/项H可运行但操作性/便利性项H性能水平有所下降
或100%的产品可能需要返工或者总成/项H在线下返修,不需要送返修部门处理
5
很
低
配合和外观等项H不舒服。
大多数顾客(75%以上)能发现缺陷
或产品可能需要挑选,不需要报废,但部分产品(小于100%)需返工
4
轻
微
配合和外观等项目不舒服。
50%顾客能发现缺陷
或部分(小于100%)产品可能需要返工,无需报废,在生产线上英它工位返工
3
很轻微
配合和外观等项目不舒服。
有辨识能力的顾客(25%以下)能发现缺陷
或部分(小于100%)产品可能需要返工,无报废,在生产线上原工位返工
2
无
无可辨别的后果
或对操作或操作者而言有轻微的不方便或无影响
1
表5推荐的PFMEA频度评价准则
失效发生可能性
可能的失效率*
频度
很高:
持续发生失效
2100个每1000件
10
50个每1000件
9
高:
经常发生失效
20个每1000件
8
10个每1000件
7
中等:
偶然性失效
5个每1000件
6
2个每1000件
5
低:
相对很少发生失效
1个每1000件
4
0.5个每1000件
3
极低:
失效不太可能发生
0」个每1000件
2
<0.01个每100()件
1
表6•推荐的PFMEA探测度评价准则
探测到
准则
检查类别
探测方法的推荐范围
探测度
A
B
C
儿乎不可能
绝/肯定不可能探测
X
不能探测或没有检査
10
很微小
控制方法可能探测不出来
X
只能通过间接或随机检验来实现控制
9
微小
控制有很少的机会能探测出
X
只能过目测检查来实现控制
8
很小
控制有很少的机会能探测出
X
只有通过双重冃测检査来实现控制
7
小
控制可能能探测出
X
用制图的方法,如SPC来实现控制
6
中等
控制可能能探测出
X
当零件离开工位后的计量测量的控制,
或者零件离开工位后100%的G/NG量
具测量
5
中上
控制有较多机会可探测出
X
X
在后续工位上的谋差探测,或在作业准
备时进行测最和首件检查(仅适用于作
业准备的原因
4
高
控制有较多机会可探测出
X
X
在工位上的误差探测,或利用多层验收在后序上进行误差探测:
供应、选择、安装、确认。
不能接受有差异零件
3
很高
控制儿乎确定能探测出
X
X
在工位上的误差探测(自动测量并自动
停机)。
不能通过有差异的零件
2
很高
肯定能探测出
X
由于有关项目己通过过程/产品设计采用了防错措施,有差异的零件不可能产出
1
附件2
1.DFMEA填写参考内容
设计DFMEA:
项目/功能:
填入被分析项目的名称和其他相关信息(如编号、零件级别等)
典型的失效模式可包括,但不限于:
裂纹、变形、松动、泄露、粘接、氧化、断裂、不传输扭矩、打滑(不能承受全部扭矩)、无支撑(结构的)、支撑不足(结构的)、刚性啮合、脱离太快、信号不足、信号间断、无信号。
注:
潜在失效模式应以规范化或技术术语来描述,不必与顾客察觉的现象相