钢水流动性差分析研究与改进.doc
《钢水流动性差分析研究与改进.doc》由会员分享,可在线阅读,更多相关《钢水流动性差分析研究与改进.doc(4页珍藏版)》请在冰豆网上搜索。
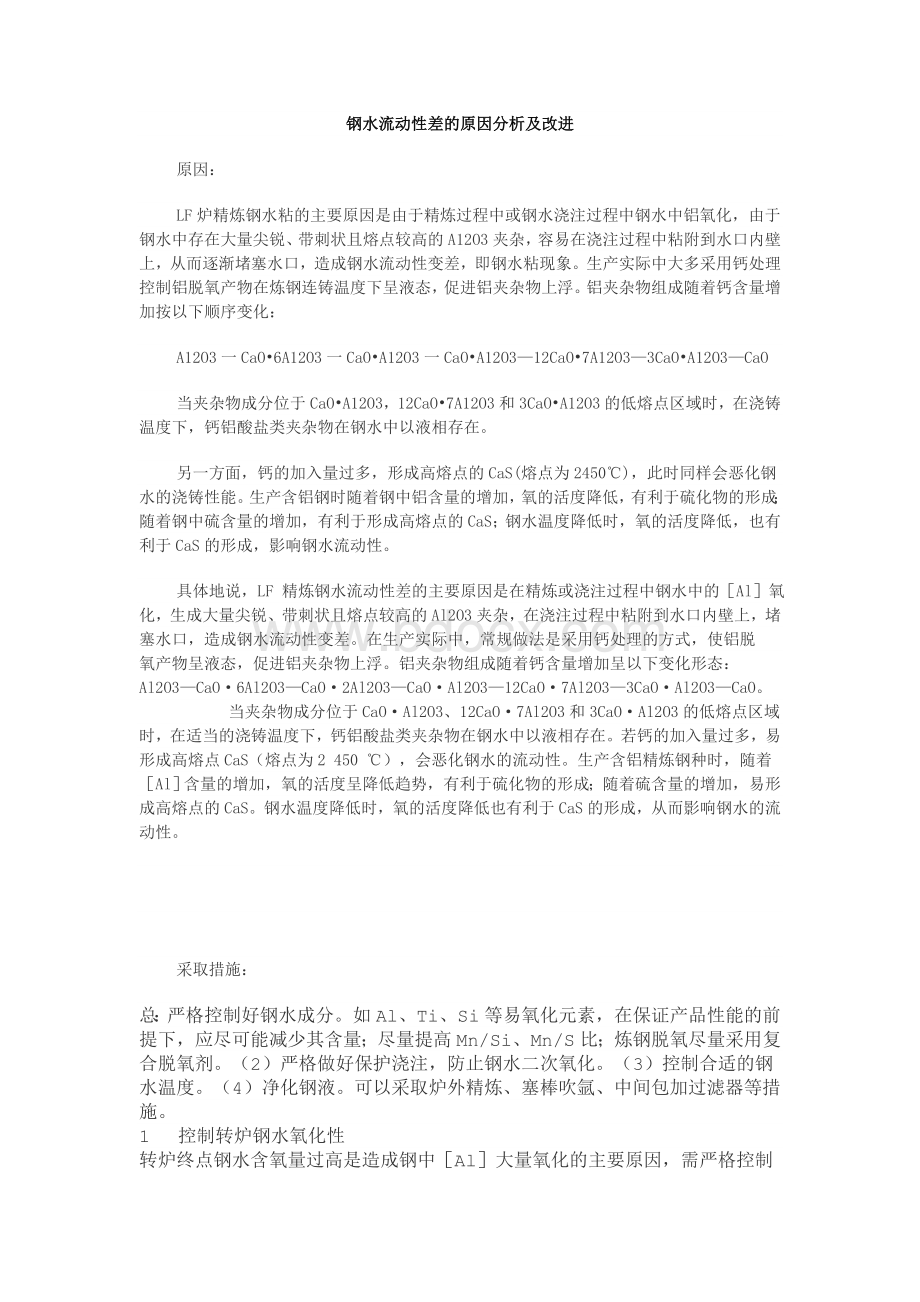
钢水流动性差的原因分析及改进
原因:
LF炉精炼钢水粘的主要原因是由于精炼过程中或钢水浇注过程中钢水中铝氧化,由于钢水中存在大量尖锐、带刺状且熔点较高的A12O3夹杂,容易在浇注过程中粘附到水口内壁上,从而逐渐堵塞水口,造成钢水流动性变差,即钢水粘现象。
生产实际中大多采用钙处理控制铝脱氧产物在炼钢连铸温度下呈液态,促进铝夹杂物上浮。
铝夹杂物组成随着钙含量增加按以下顺序变化:
A12O3一CaO•6A12O3一CaO•A12O3一CaO•A12O3—12CaO•7A12O3—3CaO•A12O3—CaO
当夹杂物成分位于CaO•A12O3,12CaO•7A12O3和3CaO•A12O3的低熔点区域时,在浇铸温度下,钙铝酸盐类夹杂物在钢水中以液相存在。
另一方面,钙的加入量过多,形成高熔点的CaS(熔点为2450℃),此时同样会恶化钢水的浇铸性能。
生产含铝钢时随着钢中铝含量的增加,氧的活度降低,有利于硫化物的形成;随着钢中硫含量的增加,有利于形成高熔点的CaS;钢水温度降低时,氧的活度降低,也有利于CaS的形成,影响钢水流动性。
具体地说,LF精炼钢水流动性差的主要原因是在精炼或浇注过程中钢水中的[Al]氧化,生成大量尖锐、带刺状且熔点较高的Al2O3夹杂,在浇注过程中粘附到水口内壁上,堵塞水口,造成钢水流动性变差。
在生产实际中,常规做法是采用钙处理的方式,使铝脱
氧产物呈液态,促进铝夹杂物上浮。
铝夹杂物组成随着钙含量增加呈以下变化形态:
Al2O3—CaO·6Al2O3—CaO·2Al2O3—CaO·Al2O3—12CaO·7Al2O3—3CaO·Al2O3—CaO。
当夹杂物成分位于CaO·Al2O3、12CaO·7Al2O3和3CaO·Al2O3的低熔点区域时,在适当的浇铸温度下,钙铝酸盐类夹杂物在钢水中以液相存在。
若钙的加入量过多,易形成高熔点CaS(熔点为2450℃),会恶化钢水的流动性。
生产含铝精炼钢种时,随着[Al]含量的增加,氧的活度呈降低趋势,有利于硫化物的形成;随着硫含量的增加,易形成高熔点的CaS。
钢水温度降低时,氧的活度降低也有利于CaS的形成,从而影响钢水的流动性。
采取措施:
总:
严格控制好钢水成分。
如Al、Ti、Si等易氧化元素,在保证产品性能的前提下,应尽可能减少其含量;尽量提高Mn/Si、Mn/S比;炼钢脱氧尽量采用复合脱氧剂。
(2)严格做好保护浇注,防止钢水二次氧化。
(3)控制合适的钢水温度。
(4)净化钢液。
可以采取炉外精炼、塞棒吹氩、中间包加过滤器等措施。
1控制转炉钢水氧化性
转炉终点钢水含氧量过高是造成钢中[Al]大量氧化的主要原因,需严格控制终点钢水的氧化性。
1)吹炼过程控制:
吹炼后期造渣剂的加入、终点温度和C含量等因素直接影响钢水氧化性,因此要根据不同钢种的要求,最大限度地提高出钢C含量和控制出钢温度,降低钢水氧化性。
2)出钢过程控制:
转炉渣为强氧化性炉渣,应严格控制出钢时的下渣量。
3)脱氧合金化过程控制:
脱氧合金化过程对钢水中氧含量起着决定性作用,应强化精炼钢种终脱氧,适当增加终脱氧剂用量,同时脱氧合金化过程严格按规程操作。
2出钢顶渣加入工艺的改进
提高钢水流动性,促进精炼钢水夹杂物上浮吸收的前提是造好低氧化性、碱度适合的精炼渣,精炼渣要求有良好的流动性和发泡能力及适宜的渣量。
在原转炉造渣料称量加料系统基础上,新增了部分管路和料仓,利用转炉造渣料加入系统来完成精炼顶渣剂的加入,解决了原顶渣加入工艺加入时间集中、且不宜熔融的弊端。
具体操作是:
生产精炼钢种时,在吹炼过程中按照钢种成分和质量要求,提前设定好顶渣剂(石灰等)加入量,并将称量好的顶渣剂放至石灰下料仓,出钢过程中操作炉后放料插板阀将顶渣剂放入钢包,同时加入部分萤石以保证化渣质量。
由于实现了提前称量、储运并自动加料,保证了出钢过程中顶渣剂及时加入,并能够在钢水搅拌作用下促进顶渣及时熔化,促进钢水脱氧合金化过程夹杂物的及时上浮。
3出钢挡渣工艺改进
依靠人工投掷挡渣球,极易造成挡渣球定位不准,挡渣效果不理想,钢包下渣量大。
氧化性炉渣对钢水中合金成分氧化严重,导致钢水成
分不稳定,合金收得率低,钢水中夹杂物含量高,影响到钢水纯净度和钢水流动性。
为此,经过反复试验,设计出转炉出钢简易定位投掷挡渣装置。
在出钢后期利用由支架和推杆组成的定位投掷挡渣装置将挡渣球加入,使挡渣球定位于出钢口上方。
从实际应用情况看,采用挡渣球定位投掷挡渣工艺后,钢包下渣量平均降低约100kg左右,减少了钢水中铝的氧化,提高了钢水流动性。
同时挡渣成功率提高至98%,避免了因出钢下渣量过大造成的钢包回磷现象,确保了钢水成分的稳定。
4出钢吹氩工艺改进
采取出钢过程顶渣加入工艺,一方面是为缩短钢水的精炼周期,使之与铸机浇铸时间相匹配,另一方面是为缩短造渣剂熔融时间。
为避免在出钢过程中加入顶渣剂易造成结块及包裹合金现象,顶渣剂的加入时间需在合金加完之后。
由于整个出钢过程时间较短,加入顶渣剂后时间所剩不多,造成顶渣剂熔融效果不好而堆积在钢包表面,起不到提前化渣的效果。
另外,由于顶渣堆积后结壳,在精炼过程进行吹氩操作时钢水无法正常翻动,加之提温操作时电极下探时极易折断,达不到顶渣剂预先加入的效果。
为解决这些问题,对钢水出钢吹氩工艺进行进,吹氩控制由静态变为动态,即根据钢包内钢水量及渣量的多少,在出钢及钢水转运过程中采用变氩气流量控制操作,通过提高吹氩效果来控制LF顶渣化渣效果,间接提高钢水流动性及精炼效果。
5精炼造渣工艺改进
提高精炼钢水流动性的根本是降低钢水中夹杂物特别是Al2O3夹杂物的含量,包括减少精炼过程夹杂物的生成和促进钢水中夹杂物的上浮吸收。
LF钢水精炼过程主要是钢水和还原性顶渣反应的过程,因此要求精炼渣具有高碱度、低氧化性、低熔点的特点,具有进一步脱硫和脱氧吸附夹杂的能力;而转炉炉渣FeO含量一般在15%~20%,氧化性较强,必须采取快速还原造渣工艺,减少钢水和炉渣中氧含量。
为此,改进精炼造渣工艺,一方面根据钢种成分要求,采用碳粉、铝粒和SiC进行前期快速脱氧操作,控制渣中FeO<0.5%,形成流动性良好的白渣;另一方面采用新型预熔精炼渣来促进炉渣熔化和调整炉渣成分,改进精炼渣吸附夹杂能力,促进钢中的[O]、[N]含量降低。
由于采用高碱度预熔精炼渣生产工艺,精炼渣化渣速度较快,缩短了精炼时间,提高了LF精炼炉生产率。
6精炼吹氩过程工艺改进
氩气的精炼去夹杂效果与耗氩量、吹氩压力、氩流量、处理时间及气泡大小等因素有关。
当吹氩量偏低时,相应限制了氩气的精炼作用,大部分只起到搅拌作用,从而使氩气的脱氧、去气、去夹杂和保护钢水等作用得不到充分发挥。
当氩气压力大时,搅动力也大,气泡上升速度快,但氩气流涉及到的范围趋于减少,甚至出现破裂致使氩气泡与钢液的接触面积减小,精炼效果反而降低。
理想的状况是氩气流(泡)遍布整个钢包,增大与钢水接触面积,延长氩气(流)泡上升的流程和时间。
因此,为提高氩气的精炼效果,在保持一定氩气压力的同时,保持相应的氩气流量。
底吹氩对钢水实施搅拌作用,搅拌强度不同,精炼效果也不同。
钢包吹氩时,钢液中夹杂物的去除量由夹杂物与气体的有效碰撞来决定,而小气泡与夹杂物发生碰撞的概率大于大气泡与夹杂物发生碰撞的概率,即从钢液中去除夹杂物的数量取决于吹入钢液的气泡数量及气泡尺寸。
根据实际情况,采用了分阶段氩气控制操作:
精炼前期控制氩气压力约0.3MPa,促进精炼剂的熔融;精炼中期氩气压力约0.5MPa,促进脱硫去夹杂;精炼后期氩气压力约0.2MPa,促进小型夹杂物上浮,并要求钢水不裸露,有效促进了精炼过程夹杂物的去除,提高了钢水的流动性。
7精炼喂铝线工艺改进
LF开始投用的初期,由于考虑到精炼前期钢水氧含量较高,此时喂铝线易形成Al2O3夹杂,因而采用了精炼后期喂铝线工艺。
经过一段时间的应用发现,大部分精炼钢水以低碳钢为主,钢水中氧含量相对较高,即使经过精炼前期的脱氧操作,钢水中氧含量仍然较高。
同时,由于铝的还原性极强,采取后期喂入铝线的工艺不可避免地造成Al与钢水及炉渣中氧化物夹杂反应形成大量Al2O3夹杂,又因为精炼后期吹氩时间较短,夹杂物上浮慢,造成钢水中Al2O3较多,从而影响了钢水纯净度和钢水的流动性。
由于采取精炼后期喂铝线,铝的收得率不稳定,为保证钢水含铝量,通常喂入大量铝线,造成钢水中铝含量偏高,有进一步使钢水流动性变差的趋势。
为合理控制钢水中铝含量和酸溶铝比例,需要对铝线喂入操作进行调整。
经试验,采取了分段铝线喂入法:
首先在精炼钢水进入LF工位时立即喂铝线,进行强化脱氧和初期铝含量控制。
根据氧含量水平,将酸溶铝目标值按0.02%~0.03%控制,然后用碳粉或以SiC进行顶渣还原操作。
其次在精炼后期根据钢水化验酸溶铝含量,采取在精炼终点前补喂Al线的方式,加强前期钢水快速深度脱氧,保证了夹杂物有充分上浮的时间。
同时,钢水容易保持合适的酸溶铝含量和比例,脱氧效果稳定。
据统计,精炼结束后平均[O]含量(喂Ca线前)由原来的0.003%~0.005%下降到0.002%以下,酸溶铝比例提高了10%,钢水铝含量达到目标铝含量值,铝收得率提高20%。
8精炼喂钙线工艺改进
采用精炼后期钢水喂钙线,目的是对Al2O3进行变性处理,改善钢水流动性。
在工艺改进之前,主要是控制精炼钢种的钙线喂入量,对改善钢水流动性未提出相应要求。
通过对水口结瘤的残留物成分分析,发现其主要组成物为CaS和2CaSiO3。
结合相关理论得出:
造成上述现象的主要因素为钙线喂入量不当。
当钙线喂入量少时,不能对钢水中的Al2O3进行充分的变性处理;钙线喂入量大时,又容易产生高熔点的CaS和2CaSiO3。
此2种情况均会造成钢水流动性变差。
钢水中Al2O3变性成为12CaO·7Al2O3夹杂的前提条件为[Ca]与[Al]的比值在0.13~0.20。
因此,需要根据钢水中[Al]含量的多少喂入相应的钙线数量,而不是一味按钢种控制钙线喂入量。
在实际生产中,一方面通过改变转炉终脱氧工艺,适当增加SiAlBa用量,避免因SiAlBa加入不足形成大量硅酸盐夹杂;另一方面控制钙线喂入速度在1.5~2m/min,保证钙的收得率。
为了防止生成CaS夹杂物,需降低钢水中S含量。
经验表明,部分钢种的硫含量应控制在0.015%以下。
9强化钢水温度控制及铸机操作
钢水温度对钢水流动性有双重影响,一方面温度高可以提高钢水流动性,另一方面温度高迫使铸机低速浇铸,Al2O3易粘附到水口内壁上,导致水口内径缩小,降低钢水流动性。
因此需严格控制中间包钢水温度,以高于液相线温度10~15℃为宜。
铸机浇铸过程是钢水流动性控制的最后阶段,其核心是保证连铸大包-中间包、中间包液面、中间包-结晶器保护浇注密封性,结晶器保护渣覆盖的良好性,避免钢水与空气接触造成二次氧化。