储罐制作施工方案.docx
《储罐制作施工方案.docx》由会员分享,可在线阅读,更多相关《储罐制作施工方案.docx(15页珍藏版)》请在冰豆网上搜索。
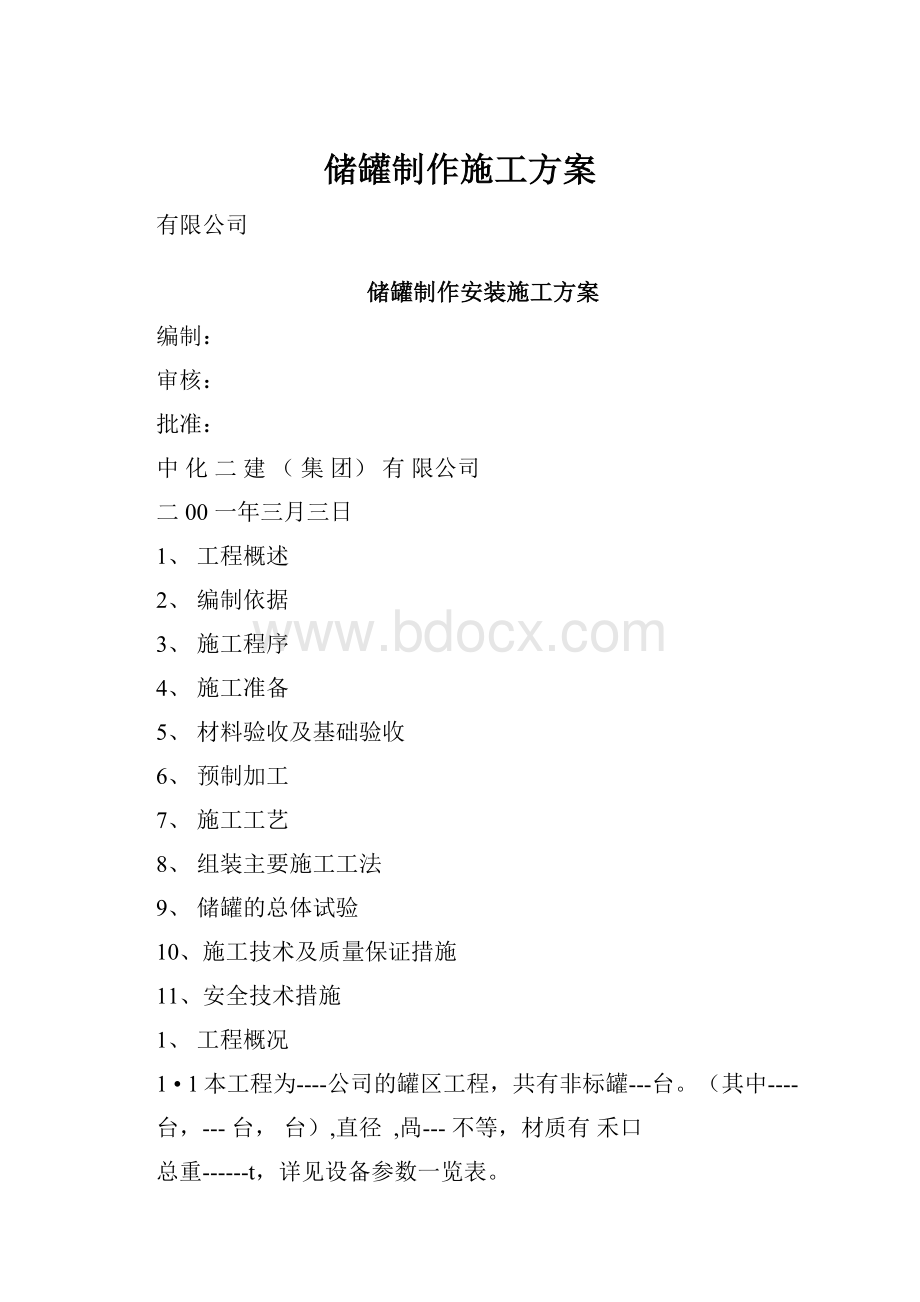
储罐制作施工方案
有限公司
储罐制作安装施工方案
编制:
审核:
批准:
中化二建(集团)有限公司
二00一年三月三日
1、工程概述
2、编制依据
3、施工程序
4、施工准备
5、材料验收及基础验收
6、预制加工
7、施工工艺
8、组装主要施工工法
9、储罐的总体试验
10、施工技术及质量保证措施
11、安全技术措施
1、工程概况
1•1本工程为----公司的罐区工程,共有非标罐---台。
(其中----
台,---台,台),直径,咼---不等,材质有禾口
总重------t,详见设备参数一览表。
设备参数一览表
名称
容积
规格(mm
材质
单重(kg)
数量
附件
1•2本方案为草案,待正式施工时,将详细编制施工方案以指导施
工。
2、编制依据
2•1招标文件、图纸及说明
2•2HGJ128-90《立式圆筒形钢制焊接油罐施工及验收规范》
2•3HG5020A95《钢结构工程施工及验收规范》
2•4HG2058;—1998《钢制化工容器结构设计规定》
2•5GB50151-92《低倍数泡沫灭火系统设计规范》
2•6HGJ229-83《化工设备、管道防腐蚀施工及验收规范》
2•770B107—1997《储罐用组装式铝制内浮顶安装验收技术条件》
2•8JB4730—94《钢制压力容器无损检测》
2•9GB/T13148—91《不锈钢复合钢板焊接技术条件》
3、施工程序
4、施工准备
4•1施工前现场应具备三通一平,即水通、路通、电通、施工场地平整的条件;
4•2施工所用的机具索具及手段用料已备齐;
4•3图纸已会审施工方案已审批并向全体施工人员作了技术交底;
4•4施工所用的计量器具齐全并已检验合格;
4•5焊工及无损检验人员的资格符合要求;
4•6开工报告已审批;
5、材料验收及基础验收
5•1贮罐用材应具有合格证书,焊材也应有合格证书,包括熔敷金属的化学成份和机械性能。
5•2贮罐所用钢板必须逐张进行外观检查,其表面不得有气孔、裂纹、拉裂、夹渣、夹层、重皮等现象,不合格严禁进厂。
5•3复合钢板的焊接材料应根据施工图的要求选用。
5•4贮罐基础竣工后,应按要求对基础进行验收,并办理中交手续。
应符合下列要求:
(1)中心坐标的允许偏差为±20mm。
(2)中心标高的允许偏差为±10mm。
5•5支承贮罐的环梁基础表面,每10m弧长内任意两点的高差不得大于6mm整个园周长度内任意两点的高差不得大于12mm
6、预制加工
6•1罐体板下料前应根据到货钢板规格,绘制出排版图,排版下料时应考虑焊接收缩量和坡口加工量。
6•2贮罐施工前,应在预制场地对底板、壁板和拱顶下料及坡口加工,壁板的滚园,包边角钢和施工用胀圈拱顶组装爪瓣均在预制场地加工。
6•3罐底底板任意相邻焊缝之间的距离不小于200mm中幅板的宽度不得小于1000mm长度不得小于2000mm边缘板沿罐底半径方向的最小尺寸不得小于700mm
6•4壁板下料后,应在预制场地将坡口加工后到卷板机上滚圆,拱顶下料后,将坡口加工好,并在胎具上煨制成形。
6•5罐体下料和坡口加工,碳钢采用半自动气割,不锈钢采用等离子切割机,坡口加工后将渣溶瘤、氧化皮等清除干净,特别是内衬不锈钢,必须把罐壁碳钢壁板焊缝打磨平整。
6・6罐体预制完成后,应检查所用样板是否符合GBJ128-90中的规定,弧形样板弦长不得小于1.5m,直线样板不得小于1m
(1)罐底弓形边缘板
测量部位
长度AB、C、D
宽度ACBDEF
对角线之差丨AD-BC|
允许偏差(mr)i
±2
±2
<3
(2)壁板
测量部位
板长AB(CD>10m
板长AB(CD)v10m
长度ABCD
±2
±1.5
宽度ACBDEF
±1.5
±1
对角线之差
<3
<2
直线度ACBD
<1
<2
直线度ABCD
<2
<2
6•壁板卷制后,垂直方向上用直线样板检查,其间隙不得大于1mm
水平方向弧形样板检查,其间隙不得大于4mm
6-8拱顶的顶板及加强肋,应进行成型加工,并用样板检查,其间隙不得大于10mm
6-9加强肋的拼接采用对接接头时,应加垫板,且应全焊透,采用搭接接头时,其搭接长不得小于加强肋宽度的2倍。
6-10加强肋不得与包边角钢相焊,径向肋和纬向肋之间T型接头采用满角焊。
6-11罐底用复合钢板焊接应符合GB/T13148-91《不锈钢复合钢板焊接技术条件》的规定。
6-12焊条选用:
碳钢之间用J422,碳钢与不锈钢之间用A302,不锈钢之间A132o
6-13预制完毕的顶板、壁板、包边角钢,在堆放、运输和起吊过程中应采取有效措施以防变形。
6•14贮罐预制件完成后,应进行除锈、防腐处理,防腐时,焊缝坡口边缘应预留50mn不涂刷,待组装完毕后补刷。
7、施工工艺
本贮罐区储罐采用液压提升倒装工艺进行施工,我公
司已有成熟的施工工法在不同地区得以应用,确保工程高效、优质、节省成本。
7•1最大提升载荷
以T5001乙二醇储罐为例,其余类推。
Gmax=F(G1+G2)
=1.2X(97591+5000)
=123109.2(Kg)
F——摩擦系数经验取1.2
G1————储罐最后提升重量
G2————施工附加载荷
7•2提升装置数量
千斤顶设计载荷P=10000Kg,因此提升装置组数n按下式计算:
Gmax123109.2
n=——————=——————=12.3
P10000
n取14套
7•3提升顺序
7•3•1铺设底板并组焊。
7•3•2组装最上一带壁板。
7•3•3安装罐顶板及顶部平台栏杆。
7•3•4安装胀圈
7•3•5安装液压提升装置,装配液压系统管道。
7•3•6液压系统启动供油,并予紧提升钩头。
7•3•7围下一带板,并焊接外侧立缝。
7•3•8供油提升100mn左右,停升检查。
7•3•9供油提升,并随时调平。
7•3•10提升到位,调整对接间隙及错边量,点焊及组焊环焊缝。
7•3•11落下提升钩头和胀圈,并安装在下一带板上。
7•3•12重复7•3•7—7•3•11直至下一带板与上一带板焊接完毕。
7•3•13焊接底板与最下一带板角缝。
7•4液压提升装置布置液压提升装置是由立拄、提升钩头、提升杆。
液压千斤顶、液压
油管及控制柜等组成(见图1)立拄沿罐壁内侧等距离分布,立拄和支撑秆应点焊固定在底板上。
叩一立空
民升杆
.迁JT壬.•〒呃
图1液压装置布置图
7•5提升装置操作7•5•1提升前的检查
7•5•1•1严格检查立柱、钩头、提升杆是否完好,提升杆的直径偏差和椭圆度均不超过0.5mm杆的不直度不超过2mm
7•5•1•2液压控制柜要全面检查电源,电缆及接地是否可靠,液压操作阀要动作灵活,进、回油接管正确。
7-5^1-3液压系统必须进行吹除干净,打开针形阀进行充油排气,最后进行1.5倍工作压力的试压,千斤顶动作3—5次,系统不得有漏油现象。
7•5•2提升操作
7•5•2•1首先使上、下卡块处于工作状态,启动油泵,调节油压到标定油压,按下提升按钮,千斤顶向上运动,到钩头钩紧胀圈时,
停下来检查各钩头应出力均匀。
继续提升到千斤顶完成一个行程后,按下回油按钮,千斤顶退回,如此反复,至一带板提升完毕。
7•5•2•2在提升中应多次检查,不得任意提高油压,千斤顶进出油的行程必须到位,确保千斤顶提升高度的同步性,罐体提升高度允许偏差小于等于30mm。
7•5•2•3罐体提升高度接近下带板高度时,应严格控制提升速度和同步性,提升高度达到要求,千斤顶最后一个行程不得回油,待环缝点焊完毕,方可回油。
7•5•2•4松卡放下提升杆和提升钩头,放下胀圈,准备下带板的提升。
7•5•2•5罐壁内衬不锈钢板贮罐,在起升完最上两带板后,开始衬8=2的最上一带不锈钢板。
7•5•2•6重复7•5•2•1〜7•5•2•5工序。
用同样的方法起吊各带壁板。
8、组装主要施工工法(倒装法)
8•1底板铺设
8•1•1底板铺设前,其下表面应按图纸要求涂刷防腐涂料。
8•1•2底板的角焊缝应两遍成型,不允许一遍成型。
8•1•3边缘板对接焊缝应完全焊透,表面应平整,垫板应与对接
的两块板贴紧,其间隙不得大于1mm对接焊缝间隙应符合图纸要求。
8•1•4中幅板搭接长度允许偏差为士5mm
8•1•5搭接接头三层钢板重叠部分,应将上层底板切角,切角长度应为搭接长度的2倍,其宽度应为搭接长度的2/3。
在上层底板铺设前,应先焊上层底板覆盖部分的角焊缝。
8•1•6底板铺设时,应预留安装孔,便于施工。
8•1•7罐底焊接完毕后,应将垫板伸出底板的部分切除。
8•2罐顶安装
8•2•1铺设完底板后,在底板上划出壁板的内外园周位置并点焊上限位块,然后安装第一带板。
8•2・2焊接顶部包边角钢。
8•2・3拱顶顶板搭接宽度允许偏差为士5mm内浮顶顶板搭接宽度允许偏差为±5mm。
8•2・4浮顶应与底圈壁板同心,浮顶外边缘板与底圈罐壁间隙允许偏差为士15mm。
8•2・5浮顶内外边缘板对接接头的错边量不得大于板厚的3/20,
且不应大于1.5mm。
8•2・6组焊拱顶上的附属构件。
8罐壁组装(倒装法)
8•3•15000用、4500卅罐壁组装采用液压提升倒装法。
每台采用
14套液压顶升均匀分布。
两台同时提升。
8•3・23000m3及以下储罐组装采用倒链倒装。
8•3•2•l装预制好的槽钢圈,放在最上一带壁板的底部,然后拧紧胀圈螺栓,使胀圈紧贴于壁板并胀紧。
同时在胀圈上部的壁板上均匀焊接角钢挡块。
8•3•2・2在罐底内靠近壁板400mm的位置上沿圆周均匀分布立
柱,立柱底座与罐底板点焊固定,立柱上部用四根角钢与底板斜拉点焊固定,立柱顶部焊吊耳,拉倒链,倒链下部挂在槽钢胀圈的吊耳上。
8•3•2・3同时拉紧倒链起吊到达起升高度后,将焊好的待组装壁
板收紧,点焊环缝,最后焊接活口纵缝和环缝。
8・3・2・4环缝焊完后,可慢慢松开倒链和胀圈螺栓,使胀圈落在
下一带板上顶部空出的边板即可进行封闭安装。
8•3•2・5用同样的方法起吊各带壁板。
8•3・3内衬不锈钢板的贮罐,应在吊完最上两带板后,同时衬里
且不锈钢板滚圆时应绘制准确的排版图,以减少不必要的工作。
8•3・4梯子及附件可与罐壁组装同时进行,以减少高空作业。
8•3・5内浮顶罐的铝浮盘需在罐体总试验合格后安装。
9、贮罐的总体试验
贮罐的组装完毕后,质量检测合格后方可进行总体试验。
9•1罐底的严密性试验及强度试验罐底焊缝应在外观检查合格后采用真空箱法进行严密性试验,试验负压值不得小于0.053MPQ无渗漏为合格。
9•2罐壁的严密性试验
9•2•1贮罐内充水,充水时逐节壁板和焊缝检查,充水到最高设计液位,并保持48小时后,罐壁无渗漏、无变形为合格。
9•2•2对于罐顶采用全不锈钢、罐壁不锈钢衬里、罐底采用不锈钢复合钢板。
试验用水的氯离子含量应控制在25ppm以下,试验合格后对罐体内表面清除污垢后作酸洗钝化处理
9•2•3固定顶的强度及严密性试验,罐内水位应在最高设计液位
下1m进行,缓慢充水升压,当升至试验压力时,应以罐顶无异常变形、焊缝无渗漏为合格。
试验后,应立即使罐内部与大气相通,恢复到常压。
9•2•4固定顶的稳定性试验应充水到设计最高液位,用放水方法进行,试验时应缓慢降压,达到试验负压时,罐顶无异常变形为合格,试验后,应立即使罐内部与大气相通,恢复到常压。
9•2•5内浮顶罐铝浮盘升降、试验应以升降平稳,导向机构、密封装置及自动通气阀支柱等无卡涩现象,内浮顶及其附件与罐体上的其它附件无干扰,内浮顶与液面接触部分无渗漏为合格。
9•2•6内衬不锈钢储罐必须在气密性试验合格后方可进行整体水压试验。
9•2•7基础沉降观测
9・2・7・1充水试验时,应按设计文件的要求对基础进行沉降观测。
9•2•7•2在罐壁下部每隔10m左右,设一个观测点,点数宜为4的整数倍且不少于4点。
9•3贮罐总体试验合格后,即可进行防腐保温,具体要求见施工图及规范要求进行。
10、施工技术及质量保证措施
10•1焊接及防止焊接变形措施
10•1•1焊工有相应的资格证书
10•1•2焊条使用前烘干,烘干后的焊条放在保温筒内使用。
10•1•3焊接前应将坡口及坡口两侧10mm范围内的油污、铁锈、毛刺等清除。
10•2焊接顺序
10•2•1焊中幅板时,应先焊短焊缝,后焊长焊缝。
10•2•2焊边缘板时,首先施焊靠外缘300mn部位的焊缝,在罐底与罐壁连接的角焊缝焊完后且边缘板与中幅板之间的收缩缝施焊前,应完成剩余的边缘板对接焊缝的焊接。
10•2•3弓形边缘板对接焊缝的初层焊,宜采用焊工均匀分布,对称施焊方法。
收缩缝的第一层焊接,应采用分段退焊或跳焊法。
10・2・4罐底与罐壁连接的角焊缝焊接,应在底圈壁板纵焊缝焊完后施焊,并由数对焊工从罐内外沿同一方向进行分段焊接。
双层的焊道,应采用分段退焊或跳焊法。
10・2・5罐壁的焊接,应先焊纵向焊缝,后焊环向焊缝。
当焊完相邻两圈壁板的纵向焊缝后,再焊其间的环向焊缝。
焊工应均匀分布,并沿同一方向施焊。
10・2・6罐壁环向的搭接焊缝,应先焊罐壁内侧焊缝,后焊罐壁外侧焊缝。
10・2・7顶板与包边角钢焊接时,焊工应对称均匀分布,并沿同一方向分段退焊。
10・2・8浮顶的焊接,应采用收缩变形最小的焊接工艺和焊接顺序。
浮顶的焊接顺序与罐底中幅板的焊接顺序相同。
10•2•9不锈钢塞焊衬里:
10•2•9•1在每张衬里层与壳体联结焊缝圭寸闭区的壳体相应位置
上应开①10小孔作气密性检查时用。
10•2•9•2采用氨气时开2个①10小孔。
检漏后,不得将检查孔焊死。
10•2•9•3塞焊与拼焊时,第一层与壳体联结的焊缝采用J422焊
条,第二层盖面焊缝用A132焊条。
10•2•9•4塞焊点与拼焊焊缝的加强度不得高出衬里层2mm
10•2•9•5塞焊点与拼焊焊缝均应无渗漏现象,检查方法:
氨渗漏法一一往衬里层与壳体夹层通入0.05—0.1MPa的氨气,在塞焊点和拼焊焊缝上涂以酚酞试剂,检查有无渗漏。
10•2•9•6整体水压试验必须在气密性试验合格后方可进行。
10•2•9•7塞焊点与拼焊焊缝发现漏后,允许进行补焊,但补焊次数不得多于2次。
10•2•9•8塞焊孔离衬里层焊缝间距不得小于30mm
10•2•9•9塞焊与拼焊前,必须将衬里压紧在筒壁上,塞焊孔或拼焊边缘与筒体间的间隙不超过0.3mm。
10•2•9•10边缘与筒体间的间隙不超过0.3mm
10•2•10复合钢板焊接时,基层和复层应分别选用焊材,基层与复层过渡处的焊接,应选用过渡层焊材。
10•2•11复合钢板组对时,应以复层表面为基准,错边量不应超过钢板厚度的50%,且不应大于1mm。
10•3质量保证措施10•3•1质量目标:
单位工程合格率100%确保优质工程。
10•3•2严格执行“三检一评”及“材料验收”制度,接受监理、甲方监督。
10•3•3严格执行ABC检查制度,严格执行规范、图纸要求并遵照施工。
10•3•4做好方案编制及技术交底工作。
10•3•5焊工必须持证上岗,严禁无证操作。
10•3•6建立行之有效的质保体系。
10•3•7项目负责人应组织人员进行雨季施工宣传教育,提高对雨季施工质量与安全的重视。
10•3•8供应科应提前做好雨季施工的物资及护品的供应。
10•3•9随时针对气象变化,对施工中不可受雨水冲刷的设备、机械等加以覆盖保护。
10•3•10电动工具要保持绝缘良好,并安装漏电保护器,电焊工、电工不得雨中作业。
10•3•11做好防暑、降温和安全施工,米取有效措施达到九防,既防触电、防雷击、防塌方、防坠落、防中毒、防传染病、防火、防盗、防自然灾害。
10•3•12焊接时应保证焊道始端和终端质量,始端应采用后退引弧法,必要时可米用引弧板,多层焊的层间接头要错开。
10•3•13罐体上的任何部位,都应采取有效的防变形措施,严禁
强力组对
10•3•14点焊环缝的动作要迅速,且应对称沿同一方向施焊。
10•4焊缝的无损检验
10•4•1每位焊工的每种板厚,在最初3m内取300mn射线检查,纵焊缝每30m焊缝及其尾数内任取300mn射线检查,环焊缝每60m内任取300mr射线检查。
10・4・2罐底边缘板的径向焊缝外端300mn范围内应进行射线探伤检查,检查数量为边缘板数量50%,且不少于4条。
10•4•3壁厚大于10mn的罐壁板,全部丁字焊应进行射线检查。
10•4•4罐壁衬里施工完毕后,应对20%勺焊缝作着色检查。
10•4•5无损探伤应符合JB4730-94《压力容器无损检测》中的第二篇《焊缝射线透照检测》的规定,皿级为合格。
11、安全技术措施
11•1教育全体施工人员严格遵守甲方及厂区的有关安全规定。
11•2坚持每周一次安全活动,做好安全交底,搞好现场文明施工。
11•3严格执行各工种安全操作规程,现场设专职安全员。
11•4现场的机电设备必须由有资格的专人管理和操作,电机设备必须可靠接地,接好漏电保护器,并有防风、防雨措施。
11•5进入现场要戴安全帽,高空作业需配带安全带,现场搭设的脚手架有防滑措施。
11•6罐内作业照明所用安全电压不得大于12V,并保持通风良好。
11•7进入罐内电线,电机设备必须检查绝缘良好,罐体接地应良
好。
11•8严格执行各种安全操作规程