开合螺母加工工艺流程及车削夹具设计论文.docx
《开合螺母加工工艺流程及车削夹具设计论文.docx》由会员分享,可在线阅读,更多相关《开合螺母加工工艺流程及车削夹具设计论文.docx(25页珍藏版)》请在冰豆网上搜索。
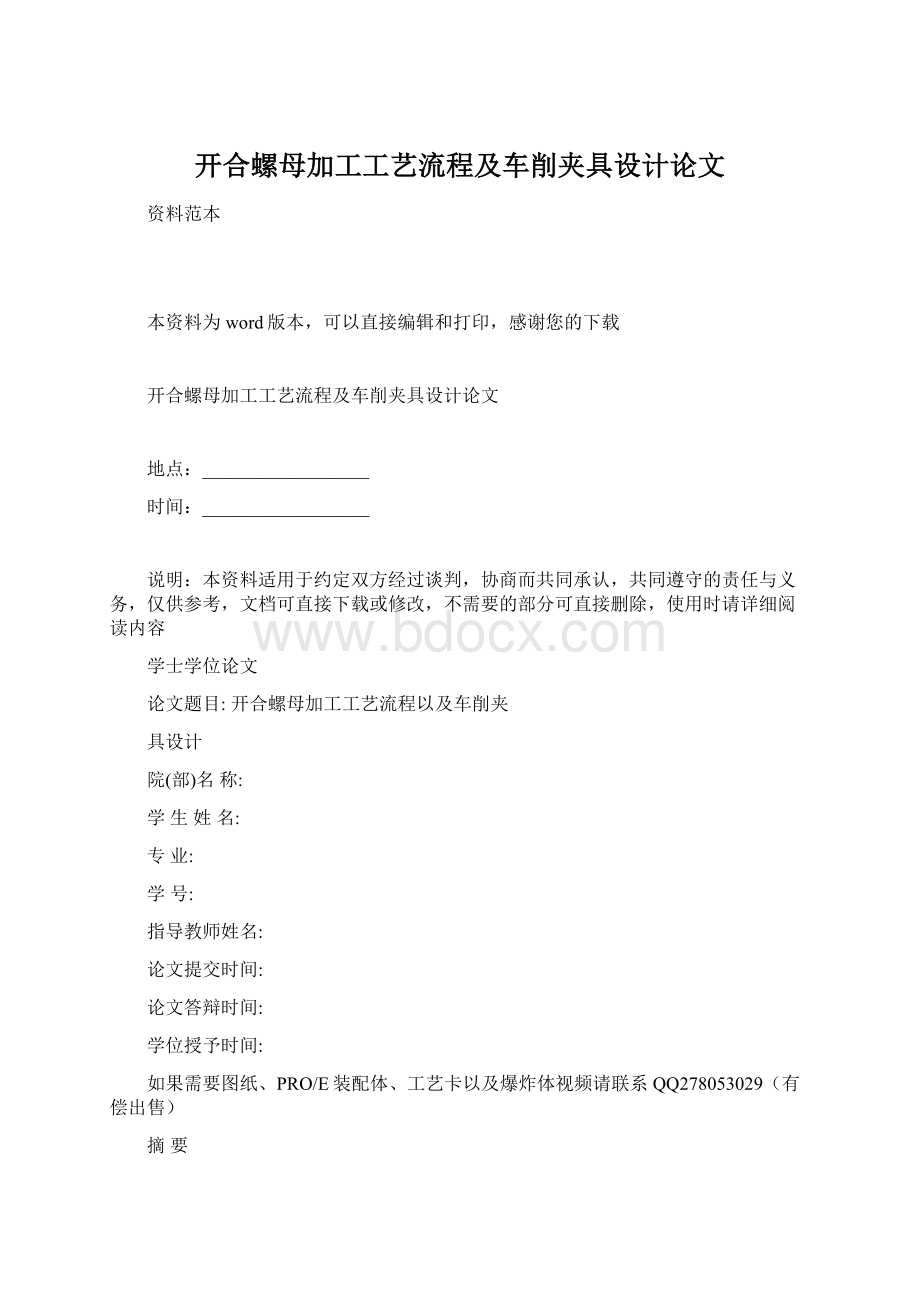
开合螺母加工工艺流程及车削夹具设计论文
资料范本
本资料为word版本,可以直接编辑和打印,感谢您的下载
开合螺母加工工艺流程及车削夹具设计论文
地点:
__________________
时间:
__________________
说明:
本资料适用于约定双方经过谈判,协商而共同承认,共同遵守的责任与义务,仅供参考,文档可直接下载或修改,不需要的部分可直接删除,使用时请详细阅读内容
学士学位论文
论文题目:
开合螺母加工工艺流程以及车削夹
具设计
院(部)名称:
学生姓名:
专业:
学号:
指导教师姓名:
论文提交时间:
论文答辩时间:
学位授予时间:
如果需要图纸、PRO/E装配体、工艺卡以及爆炸体视频请联系QQ278053029(有偿出售)
摘要
本次毕业设计主要介绍了开合螺母的加工工艺流程以及车削专用夹具的设计。
工作内容包括主要分为工艺过程设计以及夹具设计两个部分
加工工艺过程设计中主要工作包括:
对开合螺母结构进行了分析,对生产工艺进行了分析,制定了加工工艺路线,确定了重要工序尺寸、加工余量、切削用量、车床以及刀具,最后完成了加工工艺过程卡和加工工序卡。
夹具设计中主要工作包括:
分析任务要求,确定夹具体型式,分析定位原理与定位误差,确定加紧方案,计算加工过程中切削力、夹紧力并对其进行了校核,设计了夹具的主要零件。
关键字:
加工工艺,工艺流程,工艺卡片,夹具
ABSTRACT
Thisgraduateddesignintroducedthemanufacturingprocessofsplitnutsandthedesignofspecialfixtureonsplitnutstwoparts
Inthepartofprocessingmanufacturingprocess,Ianalyzedthestructureofsplitnutsandmanufacturingprocess,establishedmanufacturingroute,proceduredimension,machiningallowance,cuttingconditions,machinerytoolsandcuttingtools,atlastIfinishedmanufacturingflowcraftcardsandmanufacturingprocesscards
Inthepartofspecialfixture,Ianalyzedtherequirementsoftaskandpositioningprinciple,establishedthestructureoffixtureandprojectofclamping,countedclampingforceandcuttingforce,atlastIdesignedtheimportantpartsofthisfixture.
Keywords:
manufacturingprocesses,HYPERLINK"flow,engineeringflowsheer,fixture
TOC\o"1-3"\h\uHYPERLINK\l_Toc8823第1章绪论PAGEREF_Toc88231
HYPERLINK\l_Toc4021.1设计任务PAGEREF_Toc4021
HYPERLINK\l_Toc294991.2任务分析PAGEREF_Toc294991
HYPERLINK\l_Toc195231.3与论文有关的部分背景资料调研PAGEREF_Toc195231
HYPERLINK\l_Toc261961.3.1开合螺母的用途PAGEREF_Toc261961
HYPERLINK\l_Toc233151.3.2工艺流程PAGEREF_Toc233151
HYPERLINK\l_Toc237291.3.3夹具PAGEREF_Toc237292
HYPERLINK\l_Toc32317第2章工艺部分PAGEREF_Toc323173
HYPERLINK\l_Toc52712.1引言PAGEREF_Toc52713
HYPERLINK\l_Toc220122.2开合螺母的结构分析PAGEREF_Toc220123
HYPERLINK\l_Toc256322.3工艺分析PAGEREF_Toc256324
HYPERLINK\l_Toc255142.4制定工艺规程PAGEREF_Toc255144
HYPERLINK\l_Toc175012.4.2基准面的选择PAGEREF_Toc175015
HYPERLINK\l_Toc114622.4.3工艺路线的制定PAGEREF_Toc114625
HYPERLINK\l_Toc68372.4.4加工方法的选择PAGEREF_Toc68375
HYPERLINK\l_Toc182642.4.5加工的顺序安排PAGEREF_Toc182646
HYPERLINK\l_Toc231152.4.7制定加工工艺路线PAGEREF_Toc231156
HYPERLINK\l_Toc87812.5重要工序尺寸、加工余量、精度的确定PAGEREF_Toc87817
HYPERLINK\l_Toc95732.5.1Φ52孔PAGEREF_Toc95737
HYPERLINK\l_Toc127272.5.22XΦ12孔PAGEREF_Toc127277
HYPERLINK\l_Toc59252.5.3B1B2C面、底面的加工PAGEREF_Toc59258
HYPERLINK\l_Toc97562.6机床以及刀具的选择PAGEREF_Toc97568
HYPERLINK\l_Toc246112.6.1机床的选择PAGEREF_Toc246118
HYPERLINK\l_Toc202832.6.2刀具的选择PAGEREF_Toc202839
HYPERLINK\l_Toc298522.7主要切削用量的确定PAGEREF_Toc298529
HYPERLINK\l_Toc35632.9加工工序卡片PAGEREF_Toc356312
HYPERLINK\l_Toc16726第3章夹具设计部分PAGEREF_Toc1672613
HYPERLINK\l_Toc56343.1夹具的任务要求以及夹具体型式的确定PAGEREF_Toc563413
HYPERLINK\l_Toc175123.2定位原理分析以及确定PAGEREF_Toc1751213
HYPERLINK\l_Toc21503.3定位销尺寸以及定位误差分析PAGEREF_Toc215014
HYPERLINK\l_Toc44903.3.1确定两销中心距PAGEREF_Toc449014
HYPERLINK\l_Toc283433.3.2确定圆柱销尺寸PAGEREF_Toc2834314
HYPERLINK\l_Toc178153.3.3确定削边尺寸b以及BPAGEREF_Toc1781514
HYPERLINK\l_Toc115683.3.3菱形销的公差以及尺寸PAGEREF_Toc1156814
HYPERLINK\l_Toc193013.3.4定位误差的分析与计算PAGEREF_Toc1930115
HYPERLINK\l_Toc257823.4加紧方案的确定PAGEREF_Toc2578215
HYPERLINK\l_Toc92533.4.1总体结构的确定PAGEREF_Toc925316
HYPERLINK\l_Toc200083.4.2夹具体和机床的连接与固定PAGEREF_Toc2000816
HYPERLINK\l_Toc143013.4.3整体的安装及尺寸公差的分析PAGEREF_Toc1430117
HYPERLINK\l_Toc85603.4.4夹具体的要求PAGEREF_Toc856017
HYPERLINK\l_Toc58363.5切削力的计算PAGEREF_Toc583617
HYPERLINK\l_Toc281393.6夹紧力的计算以及校核PAGEREF_Toc2813919
HYPERLINK\l_Toc68253.7夹具体主要零件的选择与设计PAGEREF_Toc682520
HYPERLINK\l_Toc140973.7.1过渡盘PAGEREF_Toc1409720
HYPERLINK\l_Toc38693.7.2配重块PAGEREF_Toc386920
HYPERLINK\l_Toc326663.7.3压板PAGEREF_Toc3266621
HYPERLINK\l_Toc7573.7.4V型块PAGEREF_Toc75722
HYPERLINK\l_Toc323533.7.5定位板PAGEREF_Toc3235322
HYPERLINK\l_Toc122403.8夹具体中销轴的校核PAGEREF_Toc1224023
HYPERLINK\l_Toc21469第4章结论PAGEREF_Toc2146924
HYPERLINK\l_Toc5210致谢PAGEREF_Toc521025
HYPERLINK\l_Toc3048参考文献PAGEREF_Toc304826
HYPERLINK\l_Toc32089附录外语文献译文PAGEREF_Toc3208927
HYPERLINK\l_Toc22311英文原文PAGEREF_Toc2231127
HYPERLINK\l_Toc23565译文PAGEREF_Toc2356533
HYPERLINK\l_Toc86附录开合螺母加工工艺过程卡PAGEREF_Toc8637
HYPERLINK\l_Toc31932附录开合螺母加工工序卡PAGEREF_Toc3193237
绪论
1.1设计任务
本次毕业设计的任务分为两个部分,一是开合螺母的加工工艺流程,主要包括分析任务给定工件尺寸要求,形位要求,表面粗糙度的要求,以及制定一套工艺流程使工件达到任务要求。
二是设计在车床上精镗Φ52孔的夹具。
1.2任务分析
工艺部分先要考虑加工工件的结构特点以及生产批量,并按照其结构特点考虑在加工的过程中用何种手段能实现工件各个面、孔的加工,在提高效率的同时还要保证保证加工精度。
夹具部分重点考虑的两个部分一个是定位,另一个则是加紧,定位部分的设计需要保证工件在夹具上处于完全定位,即6个方向上的自由度完全被限定,加紧则需要保证工件在切削力的作用下依然能在正确位置不发生偏移,并且夹紧力的施加需要保证不能破坏工件。
1.3与论文有关的部分背景资料调研
1.3.1开合螺母的用途
开合螺母又称为“对合螺母”,主要由上下两个半螺母构成,装在机床溜板箱体后壁的导轨中。
开合螺母的底部各有一个圆孔,圆孔与槽盘的滑槽相连接。
扳动机床手柄,经轴带动槽盘顺时针或逆时针转动,通过销钉的作用与上下两个开合螺母使其分离或者闭合,从而与开合螺母中的丝杠啮合或脱开,从而起到一个相当于“离合器”的作用,完成机床从手动到机动的转换
1.3.2工艺流程
工艺流程指的是劳动者通过生产工具将各类原料、半成品,按照一定的顺序进行连续加工,最终使其成为成品的过程
工艺流程的设计应当遵循以下基本要求:
1、能满足产品的质量以及数量的指标。
2、符合经济性。
3、具有合理性。
4、环保。
5、生产过程具有可操作性。
6、生产过程具有可控制性。
我国近年更加注重以下几个方面:
1、尽量采用先进成熟的生产设备与生产技术。
2、尽量采取机械化自动化。
3、减少三废的排放。
4、保障安全生产。
1.3.3夹具
夹具是指机械加工中用来固定加工工件使之具有正确的位置,以便于接受施工或者检测设备。
本次设计的是一种用于车床上的加工工件内回转面的夹具,安装于车窗主轴上。
第2章工艺部分
2.1引言
本章主要任务是分析任务给定图样的技术要求,加工零件的各尺寸精度、形状精度、位置精度和表面粗糙度达到图纸要求。
并编制零件加工工艺流程、填写零件加工工艺卡片以及说明书。
2.2开合螺母的结构分析
图1
本次任务给定的开合螺母由左右两个结构对称的半螺母组成,底部有55°的燕尾,燕尾凸台地面有2XΦ12,孔深20的光孔,开合螺母中间开Φ52的螺孔,根部留有空刀槽。
燕尾凸台B1B2以及C面表面质量要求2.6,燕尾凸台底面2个Φ12光孔要求达到7级精度内表面质量要求2.6,孔间距±0.05,Φ52孔要求达到7级精度。
根据任务给定的二维图尺寸约束通过PRO/E拉伸建模出三维造型如下图2所示
图2
2.3工艺分析
将开合螺母的加工分为两类:
1.轴类(外表面)的加工
主要加工面有长度尺寸为75.2mm的底面,两个倒角,B1,B2,C面,开合螺母圆筒部左右两个端面,Φ52中心线到燕尾凸台底面330.05mm,中线到左边端面距离49,上表面总长96,下表面总长105
燕尾凸台底面到C面距离18。
2.孔类(内表面)的加工
主要有Φ52以及两个Φ12的孔,Φ12孔间距要求达到±0.05
2.4制定工艺规程
2.4.1确定毛坯的型式
任务给定工件轮廓不大,大批量生产,加工条件较高,选择离心铸造毛胚。
离心铸造得来的铸件具有紧密与微细的颗粒结构及较好的机械性能。
材料选用灰口铸铁HT150其铸造性能良好,减摩性好;减震性强;切削加工性良好;缺口敏感性较低;价格便宜,制造方便。
2.4.2基准面的选择
基准面是用来作为基准以确定其他点、线、面尺寸之间尺寸的平面,所以选择正确的基准面可以提高生产效率,保证加工质量。
开合螺母的加工当以底面以及两个直径12的光孔为精基准,而为精基准的表面应该提前加工完。
粗基准选择的重点应当是如何确保加工面有足够的余量,使得不加工面的位置尺寸符合任务给定的要求。
因此依据粗基准选择原则,选取R34的大外圆为粗基准来加工燕尾槽导轨面,然后以燕尾槽为面为基准加工Φ52的螺孔。
2.4.3工艺路线的制定
开合螺母的形状比较复杂,需要加工的表面不便于集中加工,为保障大批量生产的效率,需要在各个工序中选用高效率的专用机床,采取工序分散的原则拟定路线。
2.4.4加工方法的选择
依据《机械制造工艺学》表A-5、A-6以及零件图精度要求查询经济加工精度,选择主要加工面的加工方法
加工面表面质量要求精度加工方法
孔Φ522.6IT7粗镗-半精镗-精镗
孔Φ122.6I77钻-扩-粗绞-精绞
CB1B22.6无粗刨-半精刨-精刨
圆筒端面2.6无粗铣-半精铣
底平面6.3无粗铣-半精铣
2.4.5加工的顺序安排
依据零件图,质量要求比较高,一道工序显然不可以满足质量要求,所以需要多道工序逐步达到质量要求,依照加工性质的不同,将加工顺序分为,粗加工、半精加工、精加工三个阶段。
粗加工:
切除毛坯大部分加工余量。
使毛坯大体上接近于成品
半精加工:
留出精加工的加工余量为精加工做好准备。
精加工:
保证各个主要加工面达到图纸要求。
2.4.6加工过程中应当遵循的原则:
a.先粗后精先安排粗加工工序,再安排精加工工序。
b.基面先行先将底平面加工,然后以底平面和R34大圆弧为基准加工孔12
c.加工过程中应该先加工平面,后加工孔,这样利用加工后的平面定位稳定可靠,而且容易加工,提高孔的加工精度。
2.4.7制定加工工艺路线
工序1铸造
工序5退火
工序10以R34大外圆以及B1B2面定位粗铣下底面
工序15对要加工的两个Φ12孔划线以底平面以及侧端面定位
钻孔2xΦ12.5深20
扩孔至Φ12.85
工序20以底平面以及工序20中加工出的两个Φ12.85的孔定位粗铣半圆筒两侧端面、空刀槽、侧导轨面。
工序25以底平面和侧端面定位粗刨B1B2C面
工序30以底平面以及底面两个Φ12.85的孔定位打倒角2.5x45°
粗镗孔Φ50
工序35以孔Φ50以及B1B2面为定位半精铣下底面
工序40以侧端面以及底平面定位粗绞孔Φ12.85至Φ12.95
精绞孔Φ12.95至Φ12
工序45以底平面以及工序40中加工出的两个Φ12孔为定位半精铣半圆筒两侧端面
工序50以底平面和侧端面定位半精刨B1B2C面
精刨B1B2C面
工序55以底平面以及两个Φ12孔定位半精镗孔Φ50至Φ52.5
精镗孔Φ52.5至Φ52
镗螺纹
工序60以底平面以及两个Φ12孔定位切开
2.5重要工序尺寸、加工余量、精度的确定
2.5.1Φ52孔
最终需要加工至尺寸Φ52,查《互换性测量技术》可得7级精度
查《机械制造工艺学》需要经过一次粗镗,二次粗镗,半精镗,精镗,可以达到要求
查表《金属机械加工》表4-17查出镗孔各工序尺寸以及工序间余量
粗镗阶段,第一次粗镗至47(IT13)
第二次粗镗至50(IT12)
半精镗阶段,半精镗至52.5(IT10)
精镗阶段,精镗至52(IT7)
工序间加工余量:
粗加工阶段5mm
半精加工阶段2.5mm
精加工阶段0.5mm则镗Φ52孔总加工余量为6mm
2.5.22XΦ12孔
最终需要加工尺寸至Φ12,查《互换性测量技术》可得7级精度
查《机械制造工艺学》需要经过钻孔扩孔粗绞精绞可以达到要求
其中可以将钻孔、扩孔视为粗加工阶段
查表《金属机械加工》表4-15查出绞孔各工序尺寸以及工序间余量
粗绞、精绞视为半精加工、精加工阶段
钻孔阶段钻孔至11(IT11)
扩孔阶段扩孔至12.85(IT11)
粗绞阶段粗铰至12.95(IT9)
精绞阶段精铰至12(IT7)
工序间加工余量(排除钻孔)扩孔0.85mm
粗绞0.1mm
精绞0.05mm则加工Φ12孔总余量为1mm
2.5.3B1B2C面、底面的加工
查表《金属机械加工》表4-28查出平面加工工序尺寸以及工序间余量
精刨B1B2C面后,下底面到C面尺寸达到18.0mm,加工余量0.5mm,故此,半精刨加工时下底面到C面尺寸为17.5(IT8)。
半精刨B1B2C面后,由之前推出的尺寸下底面到C面尺寸为17.5(IT8),半精刨加工余量2.5mm,则在半精铣底面之后,下底面到C面的尺寸为16(IT10)。
半精铣底面,加工余量1mm则之前总高度应达到(粗刨CB1B2面之后)高度82(IT8)。
粗刨B1B2C面,加工余量2mm,则之前底平面到C面距离为14mm(IT10)
粗铣底平面,加工余量2.5mm则粗铣前,总高度应为84.5(IT11)(毛坯尺寸)
2.6机床以及刀具的选择
2.6.1机床的选择
工序10、25、45为铣削加工,工步少,依据工件尺寸选择X6132立式铣床
工序20、40为钻孔、扩孔、绞孔加工,依据工件尺寸选择Z5125A立式钻床
工序35、55为粗镗、精镗、半精镗加工,依据工件尺寸选择C620车床
工序30、50为粗刨、半精刨、精刨加工,依据工件尺寸选择B6025刨床
2.6.2刀具的选择
底面铣削选择硬质合金刀端面铣刀。
钻孔Φ12.5mm时,选用直柄麻花钻。
扩孔φ12.85时,选用高速钢锥柄。
绞孔φ12H7时,选用直柄机用铰刀。
铣削端面时选择硬质合金端面铣刀。
镗孔时选用硬质合金60°内孔车刀
刨削,粗刨时选用平面刨刀,精刨时选用圆头精刨刀
2.7主要切削用量的确定
查询《机械制造技术基础课程设计》表5.1~5.30选择进给量、切削速度并计算出主轴转速。
[工序10]粗铣下底面
在粗铣工序时,取加工余量为背吃刀量以提高铣削效率,所以a=2.5mm
取每齿进给量f=0.3mm/z
取切削速度V=34.6m/min
铣床主轴转速n=1000v/πd=1000*34.6/3.14*80=137r/min
[工序40]半精铣下底面
半精铣时,背吃刀量取0.5mm至2mm,故背吃刀量a等于半精铣工序时的加工余量=1mm
取每齿进给量f=0.2mm/z
取切削速度V=40m/min
铣床主轴转速n=1000*40/(3.14*80)=159r/min
[工序25]粗铣左右两侧端面
在粗铣工序时,取加工余量为背吃刀量以提高铣削效率,所以a等于粗铣工序时的加工余量=3mm
查手册取每齿进给量f=0.3mm/z
取切削速度V=34.6m/min
铣床主轴转速n=1000*34.6/(3.14*65)=170r/min
[工序50]半精铣左右两端面
半精铣时,背吃刀量取0.5mm至2mm,背吃刀量a等于半精铣工序时的加工余量=1mm
取每齿进给量f=0.2mm/z
取切削速度V=40m/min
铣床主轴转速n=1000*40/(3.14*65)=196r/min
[工序20]钻孔、扩孔
[工步1]钻孔至Φ11
第一次钻孔加工余量为11mm,一次行程钻完,故选择背吃刀量a等于钻孔工步时的加工余量=11mm
工件材料HT150,布氏硬度180HBS,选择进给量f=0.45mm/r
选择切削速度V=0.45mm/r
钻床主轴转速n=60000V/(πd)=60000*0.45/(3.14*11)=782.7r/min
[工步2]扩孔至Φ12.85
扩孔时加工余量0.85mm,一次行程扩完,故选择背吃刀量a等于扩孔工步时的加工余量=0.85mm
工件材料HT150,布氏硬度180HBS,选择进给量f=0.8mm/r
选择切削速度V=0.18m/s
钻床主轴转速n=60000V/(πd)=60000*0.18/(3.14*12.85)=290.2r/min
[工序45]绞孔
[工步1]粗绞孔至12.95
粗绞孔的加工余量为0.1mm,一次行程绞完。
背吃刀量a等于粗绞孔工步时的加工余量=0.1mm
选择进给量f=2.5mm/r
切削速度V=10m/min
主轴转速n=1000V/(πd)=1000*10/(3.14*12.95)=267r/min
[工步2]精绞孔至12
精绞孔的加工余量为0.05mm,一次行程绞完。
背吃刀量a等于精绞孔工步时的加