电器按钮注塑模具设计.docx
《电器按钮注塑模具设计.docx》由会员分享,可在线阅读,更多相关《电器按钮注塑模具设计.docx(24页珍藏版)》请在冰豆网上搜索。
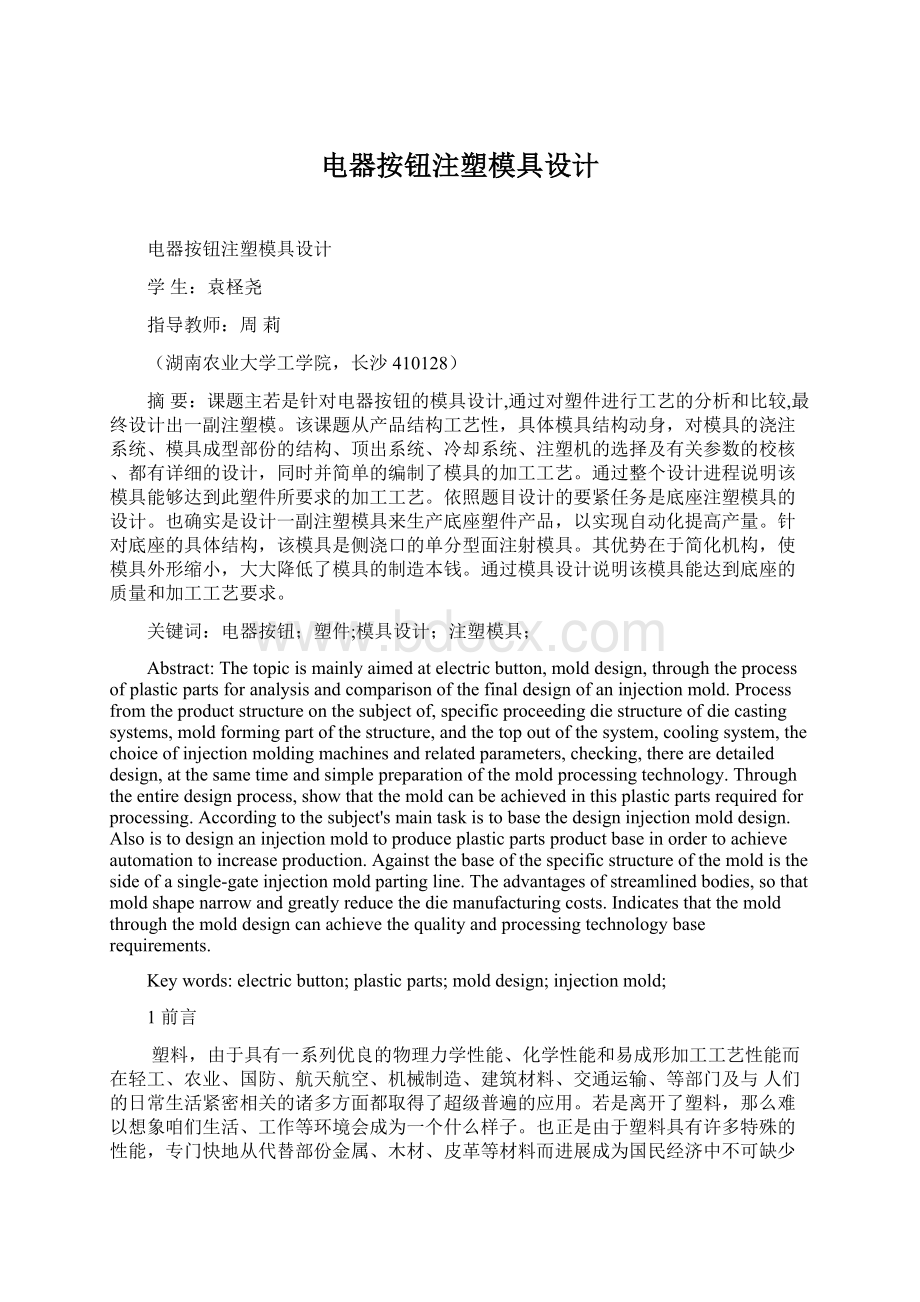
电器按钮注塑模具设计
电器按钮注塑模具设计
学生:
袁柽尧
指导教师:
周莉
(湖南农业大学工学院,长沙410128)
摘要:
课题主若是针对电器按钮的模具设计,通过对塑件进行工艺的分析和比较,最终设计出一副注塑模。
该课题从产品结构工艺性,具体模具结构动身,对模具的浇注系统、模具成型部份的结构、顶出系统、冷却系统、注塑机的选择及有关参数的校核、都有详细的设计,同时并简单的编制了模具的加工工艺。
通过整个设计进程说明该模具能够达到此塑件所要求的加工工艺。
依照题目设计的要紧任务是底座注塑模具的设计。
也确实是设计一副注塑模具来生产底座塑件产品,以实现自动化提高产量。
针对底座的具体结构,该模具是侧浇口的单分型面注射模具。
其优势在于简化机构,使模具外形缩小,大大降低了模具的制造本钱。
通过模具设计说明该模具能达到底座的质量和加工工艺要求。
关键词:
电器按钮;塑件;模具设计;注塑模具;
Abstract:
Thetopicismainlyaimedatelectricbutton,molddesign,throughtheprocessofplasticpartsforanalysisandcomparisonofthefinaldesignofaninjectionmold.Processfromtheproductstructureonthesubjectof,specificproceedingdiestructureofdiecastingsystems,moldformingpartofthestructure,andthetopoutofthesystem,coolingsystem,thechoiceofinjectionmoldingmachinesandrelatedparameters,checking,therearedetaileddesign,atthesametimeandsimplepreparationofthemoldprocessingtechnology.Throughtheentiredesignprocess,showthatthemoldcanbeachievedinthisplasticpartsrequiredforprocessing.Accordingtothesubject'smaintaskistobasethedesigninjectionmolddesign.Alsoistodesignaninjectionmoldtoproduceplasticpartsproductbaseinordertoachieveautomationtoincreaseproduction.Againstthebaseofthespecificstructureofthemoldisthesideofasingle-gateinjectionmoldpartingline.Theadvantagesofstreamlinedbodies,sothatmoldshapenarrowandgreatlyreducethediemanufacturingcosts.Indicatesthatthemoldthroughthemolddesigncanachievethequalityandprocessingtechnologybaserequirements.
Keywords:
electricbutton;plasticparts;molddesign;injectionmold;
1前言
塑料,由于具有一系列优良的物理力学性能、化学性能和易成形加工工艺性能而在轻工、农业、国防、航天航空、机械制造、建筑材料、交通运输、等部门及与人们的日常生活紧密相关的诸多方面都取得了超级普遍的应用。
若是离开了塑料,那么难以想象咱们生活、工作等环境会成为一个什么样子。
也正是由于塑料具有许多特殊的性能,专门快地从代替部份金属、木材、皮革等材料而进展成为国民经济中不可缺少的一类化工材料,并跻身与金属、纤维、硅酸盐三大传统材料之行列,成为现代工业四大基础材料之一,应用于人类活动于生产活动的各个领域
据最近数据统计,在工业发达国家,日本生产塑料模和生产冲压模的企业各占40%;韩国模具专业厂中,生产塑料模的占43.9%,生产冲压模的占44.8%;新加坡全国有460家模具企业,60%生产塑料模,35%生产冲模和夹具。
作为最有效的塑料成型方式之一的注射成型技术能够一次成型各类结构复杂和尺寸周密的塑件,它具有成型周期短、生产率高、大量生产时本钱低廉、易于实现自动化或自动化生产等优势。
因此,世界塑料成型模具产量中约半数以上是注射模具。
目前,塑料塑件在国民经济和日常生活中的应用日趋普遍,发挥着举足轻重的作用,塑料塑件的加工大体上是通过模具一次成型。
在众多的成型方式中,注射成型占主导地位,塑料塑件的质量、生产效率、本钱和模具的结构、利用性能紧密相关。
因此,设计制造出结构合理,利用性能优良的注射成型模具已成为塑料生产厂家关注的核心。
本次毕业设计题目是“塑料配件”,设计中重点注意侧抽芯的分型,其他系统结构具体按塑件结构要求设计。
本设计说明书要紧介绍了本人这次模具题目设计的整个思想进程,从开始构思到整套模具设计完毕,包括工程图,制造工艺,每一个环节都必需面面俱到,不能轻忽,专门是在尺寸与精度方面,更应该细心地测量与琢磨,不然就会直接阻碍塑料件的质量。
该设计聚集了本人在大学三年的专业知识,是模具设计与制造方面的一个积存功效。
通过这次设计,使我对塑料工业有了进一步的了解,也真正地感受到了塑料工业为推动国民经济和人们的日常生活带来了极大的便利的地方。
在设计中,由于时刻紧迫,不免产生错误,错误的地方请读者指正。
2塑件分析
2.1.材料的选择
该产品既是日经常使用品,也是工艺品,因此,外观要求比较高,尺寸要求较低。
因为是电器按钮,因此对力学要求较高。
因此从塑件的利用性能上分析,其必需具有有必然的综合机械性能,包括良好的机械强度,必然的弹性和耐油性,耐水性,化学稳固性和电气性能。
而符合以上性能的有多种塑料材料,从材料的来源和材料的本钱和调配颜色来看,ABS比较适合。
ABS是目前世界上应用最普遍的材料,它来源广,本钱底,符合该塑件成型的特性。
因此制作该塑件选用ABS塑料。
表一:
ABS的要紧技术指标
密度
比溶
吸水率
收缩率
0.2%-0.4%
130-160
抗拉强度
拉伸弹性
模量
弯曲强度
50Mpa
80Mpa
11HB
密度
比溶
吸水率
收缩率
0.2%-0.4%
130-160
表二:
ABS的注射工艺参数
注射机类型
螺杆转数
喷嘴形式
喷嘴温度
螺杆式
30
直通式
170-180
料筒的温度
模具温度
注射压力
保压力
150-170165-180180-200
50-80
60-100Mpa
30-60Mpa
注射时间
保压时间
冷却时间
成型周期
0-5S
20-90S
20-120S
50-220
ABS无毒,无味,呈微黄色,成型的塑料件有较好的光泽。
密度为/cm3。
ABS有极好的抗冲击强度,且在低温下也不迅速下降。
有良好的机械强度和必然的耐磨性,耐寒性,耐油性,耐水性,化学稳固性和电气性能。
ABS有必然的硬度和尺寸稳固性,易于成型加工。
通过调色可配成任何颜色。
其缺点是耐热性不高,持续工作温度为70度左右,热变形温度约为90度左右。
耐气候差,在紫外线作用下易变硬发脆。
其成型特点:
ABS在升温时黏度增高,因此成型压力较高,塑料上的脱模斜度稍大,ABS易吸水,成型前加工要进行干燥处置;易产生熔接痕,模具设计时应注意尽可能减小浇注系统对料流的阻力;在正常的成型条件下,壁厚,溶料温度及收缩率阻碍极小。
2.2明确制品批量
该产品精度要求效高,又是大量量生产,考虑到模具制造、模具运转费用尽可能低的原那么,因此模具采纳一模二腔结构。
2.3塑件结构工艺性分析
图1:
塑件
3初选注射机型号
3.1计算制品的体积和质量
-3),收缩率为0.4-0.7(%)。
计算平均密度为1(g/mm3),平均收缩率为0.5(%)。
通过计算,塑件质量m1为,塑件体积V1=m13流道凝料的质量m2按塑件的0.6倍计算,因此注射量为:
m2=0.6x2.5x2=3g.
塑件和流道凝料在分型面上的投影面积及所需锁模力的计算:
流道凝料在分型面上的投影面积A2,可按其在分型面上的投影面积A11来估算,因此:
A=nA1+11=2
式中A1=405.82mm2
Fm=AP型
式中型腔压力P型取30MPa(因是薄壁塑件,浇口又式暗藏式浇口,压力损失大,取大一些)
3.2注射机型参数
依照塑料制品的体积,本塑件初选用型号为XS-ZY-250
的注射机,其技术参数如下:
(查注射机表)。
注射量/cm3
250
注射时间/t
2
螺杆直径/mm
50
注射方式
螺杆式
注射压力/MPa
130
合模力/KN
1800
注射行程/mm
160
最大成型面积/cm2
500
螺杆转速r/min
移模行程/mm
500
模板最大厚度/mm
350
喷嘴孔直径/mm
模板最小厚度/mm
200
定位圈/mm
150
拉杆空间/mm
448X370
推出形式,中心距
两测推出
合模方式
液压-机械
喷嘴球直径/mm
14
4分型面位置的确信和型腔徘布
如何确信分型面,需要考虑的因素比较复杂。
由于分型面受到塑件在模具中的成型位置、浇注系统设计、塑件的结构工艺性及精度、嵌件位置形状和推出方式、模具的制造、排气、操作工艺等多种因素的阻碍,因此在选择分型面时应综合分析比较,从几种方案中优选出较为合理的方案。
选择分型面时一样应遵循以下几项原那么:
(1)分型面应选在塑件外形最大轮廓处。
(2)便于塑件顺利脱模,尽可能使塑件开模时留在动模一边。
(3)保证塑件的精度要求。
(4)知足塑件的外观质量要求。
(5)便于模具加工制造。
(6)对成型面积的阻碍。
(7)对排气成效的阻碍。
依照塑件的结构形式,分型面选在仪表盖的底平面。
如图2:
分型面
图2分型面
图3:
型腔排列图
5成型零件的设计
如图001所示,塑件结构尺寸和相应的模具型腔结构,塑件材料为ABS,计算收缩率为0.4%~0.6%。
求凸凹模组成型腔的尺寸。
塑件的平均收缩率为:
Scp=(Smin+Smix)/2=(0.4+0.6)/2%=0.5%
5.2凹模工作尺寸尺寸的计算
外形尺寸:
L1=[L塑1(1+K)-(3/4)△]+δ
=[38×(1+0.5%)-3/4×0.4]×1/6
L2=[L塑2(1+K)-(3/4)△]+δ
=[19×(1+0.5%)-3/4×0.3]×1/6
注:
1.未标注公差按公差表MT5查取;
2.小型芯(C2)为四个圆周均匀散布;
3.由于图幅受限等一些缘故零件其它尺寸就不在此一一计算,这些尺寸可按上述步骤计算出来;
凸模工作尺寸的计算
内形无精度要求,凸模直接按收缩率计算
6模架尺寸和类型的确信
6.1A板尺寸
A板是定模型腔板,型腔最高高度为19,在模板上还要开设冷却水道,冷却水道离型腔应有必然的距离,因此A板厚度取75mm。
6.2B板尺寸
B板是凸模固定板,型芯的最高高度为,因此B板厚度取65mm。
6.3垫块的厚度
推板与推杆固定板加推出行程,可得出垫块厚度为90mm。
7浇注系统设计
浇注系统设计是不是合理不仅对塑件性能、结构、尺寸、内外在质量等阻碍专门大,而且还对塑件所用的塑料的利用率、成型生产效率等相关,因此这是一个重要环节。
浇注系统设计要紧包括主流道,分流道,浇口和冷料穴四部份。
它的要紧作用是以后自注射机喷嘴的塑料熔体均匀而平稳地输送到型腔,同时使型腔内的气体能及时顺利排出,将注射压力有效地传递到型腔的各个部位,以取得形状完整、内外在质量优良的塑料制件。
7.1主流道设计
7.1.1主流道尺寸
为了便于凝料从主流道中拔出,主流道设计成圆锥形(如图4)。
其锥角取30,内壁表面粗糙度值Ra取0.7um。
为了补偿对中误差并解决凝料的脱模问题,主流道进料口端直径D1应比注射机喷嘴直径d大0.5~1mm。
主流道轴线位于模具中心线上,与注射机喷嘴轴线重合,型腔也以此轴线为中心对称布置。
主流道形式
主流道不直接开在模板上,将它单独设在一个主流道衬套中,即能够使易损坏的主流道部份单独选用优质钢材,延长模具利用寿命和损坏后便于改换或修磨,也能够幸免在模板上直接开住流道且需穿过量个模板时,拼按缝处产生钻料,主流道凝料无法拔出。
通常主流道入口端凹下的球面半径R比喷嘴球面半径r大1~2mm,凹下深度约2-5mm.R=r+1=14+1=15mm,凹下深度为2m。
主流道衬套的形式
主流道小端入口处与注射机喷嘴反复接触,属易损件,对材料要求较严,因此模具主流道部份常设计成可拆卸改换的主流道衬套形式(俗称浇口套,这边称唧咀),以便有效的选用优质钢材单独进行加工和热处置。
浇口套都是标准件,只需去买就好了。
浇口套与定位圈设计成一个零件的形式,以螺钉的形式固定在定模座板上。
本设中型模具,但为了便于加工和缩短主流到长度,衬套和定位圈也是设计成份体式,主流道长度取85,材料采纳T10A钢,热处置淬火后表面硬度为53HRC-57HRC.与模板间的配合采纳H7/m6的过度配合。
浇口套的具体参数如图4所示:
图4浇口套
7.2分流道设计
在多型腔或单型腔多浇口(塑件尺寸大)时应设置分流道,分流道是指主流道结尾与浇口之间这一段塑料熔体的流动通道。
它是浇注系统中熔融状态的塑料由主流道流入型腔前,通过截面积的转变及流向变换以取得平稳流态的过渡段。
因此分流道设计应知足良好的压力传递和维持理想的充填状态,并在流动进程中压力损失尽可能小,能将塑料熔体均衡地分派到各个型腔。
分流道的形式
截面形状为圆形,如此效率比较高。
分流道的截面尺寸
关于圆形截面分流道,直径一样在3~10mm的范围内变更,查《各类塑料的分流道直径表》,得ABS的分流道直径为3.8~,因本塑件比较简单,因此那个地址取5mm。
分流道的长度
分流道的长度应尽可能短,且少弯曲,便于注射成型进程中最经济地利用原料和降低注射机的能耗,减少压力损失和热量损失。
知足良好的压力传递和维持理想的填充状态,使塑件溶体尽快地分派到各个型腔,因此采纳平稳式分流道。
分流道长L1=28mm。
分流道的表面粗糙度
由于分流道中与模具接触的外层塑料迅速冷却,只有中心部位的塑料熔体的流动状态较为理想,因面分流道的内表面粗糙度Ra并非要求很低,一样取μm左右既可,如此表面稍不滑腻,有助于塑料熔体的外层冷却皮层固定,从而与中心部位的熔体之间产生必然的速度差,以保证熔体流动时具有适宜的剪切速度和剪切热。
分流道的布置形式
分流道在分型面上的布置与前面所述型腔排列紧密相关,有多种不同的布置形式,但应遵循两方面原那么:
即一方面排列紧凑、缩小模具板面尺寸;另一方面流程尽可能短、锁模力力求平稳。
本模具的分流道采纳平稳试。
(如图5)
图5分流道
7.3浇口的设计
浇口亦称进料口,是连接分流道与型腔的通道,除直接浇口外,它是浇注系统中截面最小的部份,但却是浇注系统的关键部份,浇口的位置、形状及尺寸对塑件性能和质量的阻碍专门大。
浇口的选用
浇口可分为限制性和非限制性浇口两种。
咱们将采纳限制性浇口。
限制性浇口一方面通过截面积的突然转变,使分流道输送来的塑料熔体的流速产生加速度,提高剪切速度,使其成为理想的流动状态,迅速面均衡地充满型腔,另一方面改善塑料熔体进入型腔时的流动特性,调剂浇口尺寸,可使多型腔同时充满,可操纵填充时刻、冷却时刻及塑件表面质量,同时还起着封锁型腔避免塑料熔体倒流,并便于浇口凝料与塑件分离的作用。
咱们采纳的是侧浇口。
侧浇口又称边缘浇口,国外称之为标准浇口。
侧浇口一样开设在分型面上,塑料熔体于型腔的侧面充模,其截面形状多为矩形狭缝,调整其截面的厚度和宽度能够调剂熔体充模时的剪切速度及浇口封锁时刻。
这种浇口加工容易,修整方便,而且能够依照塑件的形状特点灵活地选择进料位置,因此它是普遍利用的一种浇口形式,普遍利用于中小型塑件的多型腔模具,且对各类塑料的成型适应性均较强;但有浇口痕迹存在,会形成熔接痕、缩孔、气孔等塑件缺点,且注射压力损失大,对深型腔塑件排气不便。
浇口各部份尺寸都是取的体会值。
实际加工中,是先用圆形铣刀铣出直径为Φ5分流道,再将材料进行热处置,然后做一个铜公(电极)去放电加工,用电火花打出那个浇口来的。
浇口位置的选择
模具设计时,浇口的位置及尺寸要求比较严格,初步试模后还需进一步修改浇口尺寸,不管采纳何种浇口,其开设位置对塑件成型性能及质量阻碍专门大,因此合理选择浇口的开设位置是提高质量的重要环节,同时浇口位置的不同还阻碍模具结构。
总之要使塑件具有良好的性能与外表,必然要认真考虑浇口位置的选择,通常要考虑以下几项原那么:
(1)尽可能缩短流动距离。
(2)浇口应开设在塑件壁厚最大处。
(3)必需尽可能减少熔接痕。
(4)应有利于型腔中气体排出。
(5)考虑分子定向阻碍。
(6)幸免产生喷射和蠕动。
(7)浇口处幸免弯曲和受冲击载荷。
(8)注意对外观质量的阻碍。
本模具浇口的位置选在分流道延长线上,直接与型腔相连,如此便于塑料流动。
7.4冷料穴和拉料杆的设计
冷料穴
在完成一次注射循环的距离,考虑到注射机喷嘴和主流道入口这一小段熔体因辐射散热而低于所要求的塑料熔体的温度,从喷嘴端部到注射机料筒之内约10-25mm的深度有个温度慢慢升高的区域,这时才达到正常的塑料熔体温度。
位于这一区域内的塑料的流动性能及成型性能不佳,若是那个地址温度相对较低的冷料进入型腔,便会产生次品。
为克服这一现象的阻碍,用一个井穴将主流道延长以接收冷料,避免冷料进入浇注系统的流道和型腔,把这一用来容纳注射距离所产生的冷料的井穴称为冷料穴。
冷料穴一样开设在主流道对面的动模板上(也即塑料流动的转向处),其标称直径与主流道大端直径相同或略大一些,深度约为直径的1-1.5倍,最终要保证冷料的体积小于冷料穴的体积,冷料穴有六种形式,经常使用的是端部为Z字形的拉料杆的形式,具体要依照塑料性能合理选用。
本模具中的冷料穴的具体位置和形状如图5中所示。
事实上是将主流道顺向延长一段距离就好了。
拉料杆
在冷料穴后面设置一个推杆,那个地址设置一个Z字形的拉料杆,工作时依托Z字形拉钩将主流道凝料拉出浇口套,推出后人工掏出。
(如图6)
图6拉料杆
7.5浇注系统的平稳
关于中小型塑件的注射模具己普遍利用一模多腔的形式,设计应尽可能保证所有的型腔同时取得均一的充填和成型。
一样在塑件形状及模具结构许诺的情形下,应将从主流道到各个型腔的分流道设计成长度相等、形状及截面尺寸相同(型腔布局为平稳式)的形式,不然就需要通过调剂浇口尺寸使各浇口的流量及成型工艺条件达到一致,这确实是浇注系统的平稳。
显然,咱们设计的模具是平稳式的,即从主流道到各个型腔的分流道的长度相等,形状及截面尺寸都相同。
7.6浇注系统的连接
主流道与分流道的连接
主流道采纳半径为2mm的圆角过度,以减少料流阻力。
分流道与浇口的连接
分流道与浇口结合采纳圆弧过度,有利于溶体的流动及填充。
浇口与型腔的连接
浇口与型腔直接连接,以减少阻力。
8推出机构的设计
8.1推杆的固定形式
推杆与模板间采纳凸台紧压固定(如图7)。
图7顶杆
8.2推杆的布置
因本塑件较大、较厚,在每一个塑件上作用四根推杆,确保制品在推出进程中不变形不损坏的要求,每四根平均作用在塑件上(如图8)。
图8顶杆散布图
制件推出(顶出)是注射成型进程中的最后一个环节,推出质量的好坏将最后决定制品的质量,因此,制品的推出是不可轻忽的。
在设计推出脱模机构时应遵循以下原那么。
(1).推出机构应尽可能设置在动模一侧由于推出机构的动作是通过装在注射机合模机构上的顶杆来驱动的,因此一样情形下,推出机构设在动模一侧。
正因如此,在分型面设计时应尽可能注意,开模后使塑件能留在动模一侧。
(2).保证塑件不因推出而变形损坏为了保证塑件在推出进程中不变形、不损坏,设计时应认真分析塑件对模具的包紧力和粘附力的大小,合理的选择推出方式及推出位置。
推力点应作用在制品刚性好的部位,如筋部、凸缘、壳体形制品的壁缘处,尽可能幸免推力点作用在制品的薄平面上,避免制件破裂、穿孔,如壳体形制件及筒形制件多采纳推板推出。
从而使塑件受力均匀、不变形、不损坏。
(3).机构简单动作靠得住推出机构应使推出动作靠得住、灵活,制造方便,机构本身要有足够的强度、刚度和硬度,以经受推出进程中的各类力的作用,确保塑件顺利脱模。
(4).良好的塑件外观推出塑件的位置应尽可能设在塑件内部,或隐蔽面和非装饰面,关于透明塑件尤其要注意顶出位置和顶出形式的选择,以避免推出痕迹阻碍塑件的外观质量。
(5)合模时的正确复位设计推出机构时,还必需考虑合模机会构的正确复位,并保证不与其他模具零件相干与。
推出机构的种类按动力来源可分为手动推出,机动推出,液压气动推出机构。
那个地址采纳一次推出机构的推杆推出机构,它是注射模中利用最广的一种脱模机构,制造简便,滑动阻力小,可在塑件上任意位置配置,改换方便,脱模成效好。
本塑件采纳8根直径为等截面的标准推杆,由于采纳圆形推杆容易达到推杆与孔的加工和配合精度,因此采纳圆形推杆,利用圆形推杆还能够减少滑动阻力,推杆损坏后容易改换。
9侧抽芯机构的设计
之前在的塑件图不难看出,该侧孔直径比较小,且抽芯距也不是很长,因此有效斜导柱抽芯机构即能知足要求,斜导柱机侧向抽芯机构要紧由与开模方向成必然角度的斜导柱,侧型腔或型芯滑块,导滑槽,楔紧块和侧滑块定距限位等装置组成,一样用于抽芯力不大及抽芯距小于80mm的场合。
9.1斜导柱的设计
斜导柱的截面形状
经常使用的截面形状有圆形和矩形,圆形截面装配容易,加工方便,应用较广,矩形截面在相同截面条件下,具有较大的抗变截面系,能经受较大的变矩,强度,刚度好,但加工装配较难,适用于抽拔力较大的场合,但在此处,抽拔力比较小,因此采纳圆形截面即能知足利用要求。
斜导柱斜角的确信
斜导柱斜角是斜导柱抽芯的一个要紧参数,它的大小小涉及到开模力,斜导柱所受的弯曲力,滑块抽芯力和开模行程的大小。
当导柱的斜度越大,那么斜导柱所受的弯曲力要增大,同时所受的开模力也增大,因此,从希望斜导柱受力小的情形下,斜度愈小愈好,可是当抽芯距一按时,斜导柱的斜度越小必然致使斜导柱工作部份长度及开模行程的加大,因为开模行程受到注射机开模行程的限制,而且斜导柱工作长度的加长,会降低斜导柱的刚度,因此斜导柱应综合考虑本身的强度,刚度和注射机开模行程,从理论上推导,斜