铣工教案钻孔键槽要点.docx
《铣工教案钻孔键槽要点.docx》由会员分享,可在线阅读,更多相关《铣工教案钻孔键槽要点.docx(17页珍藏版)》请在冰豆网上搜索。
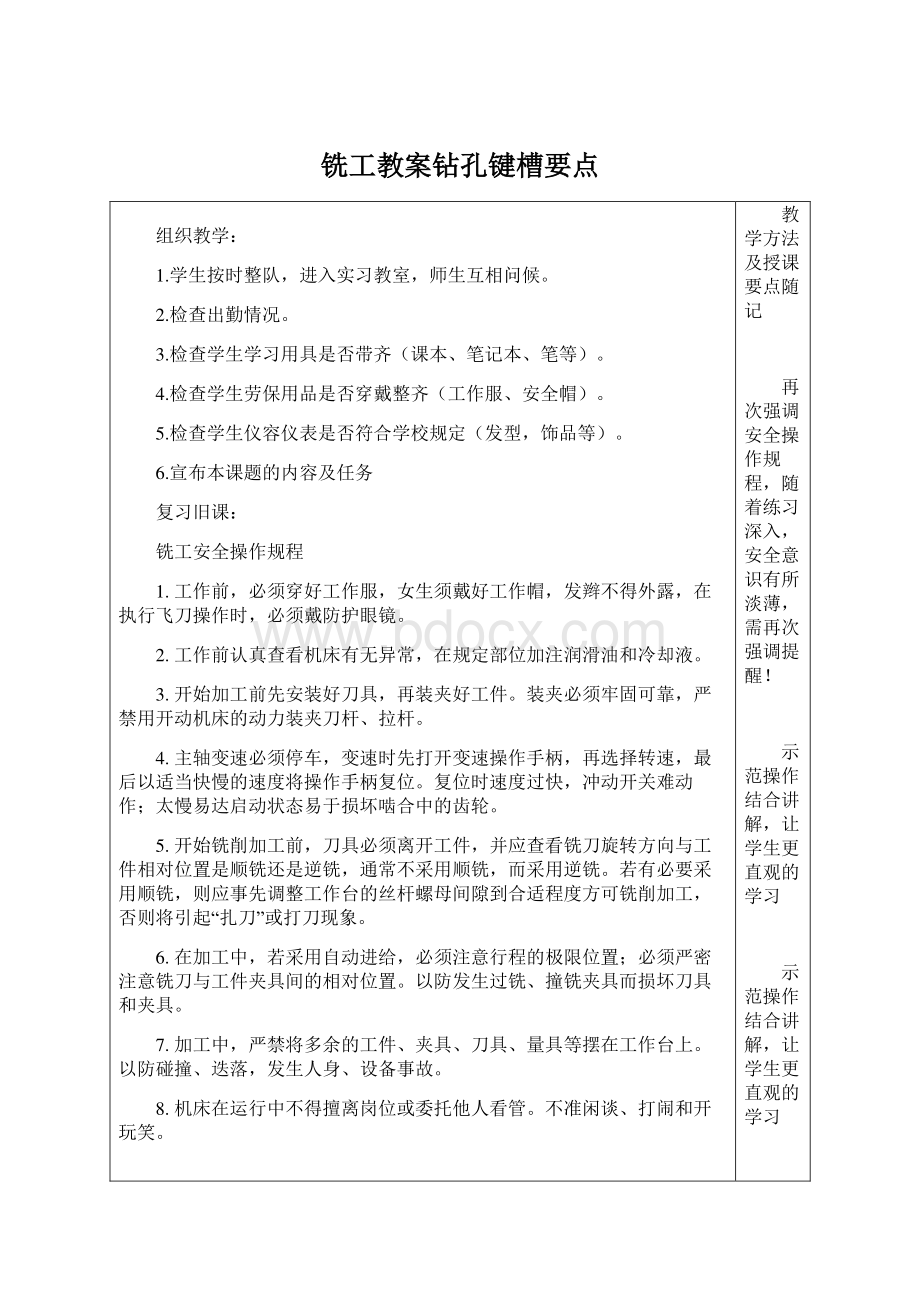
铣工教案钻孔键槽要点铣工教案钻孔键槽要点组织教学:
1.学生按时整队,进入实习教室,师生互相问候。
2.检查出勤情况。
3.检查学生学习用具是否带齐(课本、笔记本、笔等)。
4.检查学生劳保用品是否穿戴整齐(工作服、安全帽)。
5.检查学生仪容仪表是否符合学校规定(发型,饰品等)。
6.宣布本课题的内容及任务复习旧课:
铣工安全操作规程1.工作前,必须穿好工作服,女生须戴好工作帽,发辫不得外露,在执行飞刀操作时,必须戴防护眼镜。
2.工作前认真查看机床有无异常,在规定部位加注润滑油和冷却液。
3.开始加工前先安装好刀具,再装夹好工件。
装夹必须牢固可靠,严禁用开动机床的动力装夹刀杆、拉杆。
4.主轴变速必须停车,变速时先打开变速操作手柄,再选择转速,最后以适当快慢的速度将操作手柄复位。
复位时速度过快,冲动开关难动作;太慢易达启动状态易于损坏啮合中的齿轮。
5.开始铣削加工前,刀具必须离开工件,并应查看铣刀旋转方向与工件相对位置是顺铣还是逆铣,通常不采用顺铣,而采用逆铣。
若有必要采用顺铣,则应事先调整工作台的丝杆螺母间隙到合适程度方可铣削加工,否则将引起“扎刀”或打刀现象。
6.在加工中,若采用自动进给,必须注意行程的极限位置;必须严密注意铣刀与工件夹具间的相对位置。
以防发生过铣、撞铣夹具而损坏刀具和夹具。
7.加工中,严禁将多余的工件、夹具、刀具、量具等摆在工作台上。
以防碰撞、迭落,发生人身、设备事故。
8.机床在运行中不得擅离岗位或委托他人看管。
不准闲谈、打闹和开玩笑。
教学方法及授课要点随记再次强调安全操作规程,随着练习深入,安全意识有所淡薄,需再次强调提醒!
示范操作结合讲解,让学生更直观的学习示范操作结合讲解,让学生更直观的学习9.两人或多人共同操作一台机床时,必须严格分工分段操作,严禁同时操作一台机床。
10.中途停车测量工件,不得用手强行刹住惯性转动着的铣刀主轴。
11.铣后的工件取出后,应及时去毛刺,防止拉伤手指或划伤堆放的其它工件。
12.发生事故时,应立即切断电源,保护现场,参加事故分析,承担事故应负的责任。
13.工作结束应认真清扫机床、加油,并将工作台移向立柱附近。
14.打扫工作场地,将切屑倒入规定地点。
15.收拾好所用的工、夹、量具,摆放于工具箱中,工件交检。
讲授新课:
钻孔在铣床上进行钻孔、铰孔和镗孔的加工特点是:
主运动是通过刀具做旋转运动来完成,而辅助运动由刀具的上下移动或工作台的上下移动来完成,并且可以通过工作台的三个方向移动,较方便地调整切削刀具与工件的相对位置。
孔的主要工艺要求包括孔的尺寸精度、孔的形状精度、孔的表面粗糙度和孔的位置精度。
其中,孔的尺寸精度包括孔的直径及深度;孔的形状精度主要有圆度、圆柱度以及轴线的直线度;孔的表面粗糙度主要对铰孔、镗孔有较高的要求;孔的位置精度主要包括孔与孔、孔与外圆之间的同轴度要求,孔与孔的轴线平行度要求,孔的轴线与端面的垂直度要求,孔的轴线对基准的偏移量的位置度要求。
一、钻孔方法1.孔加工刀具1、麻花钻麻花钻是一种形状复杂的孔加工刀具,如图1-1所示。
它的应用十分广泛,常用来钻削精度较低和表面粗糙度要求不高的孔。
用高速钢钻头加工的孔精度可达IT13IT11,表面粗糙度可达Ra2.56.3m;用硬质合金钻头加工的孔精度可达IT11IT10,表面粗糙度可达Ra12.53.2m。
标准麻花钻主要由切削部分、导向部分和刀柄三部分组成。
钻头切削部分由它的切削刃和横刃作为刀具在起切削作用。
导向部分在切削过程中能保持钻头正直的钻削方向,同时具有修光孔壁的作用,并且是切削的后备部分。
刀柄用来夹持和传递钻孔时所需的扭矩和轴向力。
麻花钻上的沟槽起排屑的作用。
图1-1麻花钻头的结构2、中心钻中心钻用于孔加工的预制精确定位,引导麻花钻进行孔加工,可以减小误差。
中心钻有A型和B型两种型式。
A型是不带护锥的中心钻,B型是带护锥的中心钻。
加工直径d=110mm的中心孔时,通常采用不带护锥的中心钻,即A型。
A型中心孔只有60锥孔;工序较长、精度要求较高的工件,一般采用带护锥的中心钻,即B型。
B型中心孔外端有120锥面,又称保护锥面,用以保护60锥孔的外缘不被碰坏。
3、深孔钻一般情况下,孔深与孔径的比值为510的孔称为深孔。
加工深孔可用深孔钻。
常用的深孔钻主要有外排屑深孔钻(如枪钻)和内排屑深孔钻(如喷吸钻等等)。
2.钻削用量钻销用量与切削层各物理量的关系如图1-2所示。
选择钻削用量的顺序依次为背吃刀量进给量钻削速度。
1、背吃刀量ap的选择背吃刀量ap应根据加工孔直径dm来选择:
当dm35mm时,分两次钻削,第一次选择ap=0.35dm,第二选择ap=0.15dm,即需要进行扩孔时,钻头直径d0(2ap)取孔径的0.30.7倍。
2、进给量f的选择当加工孔的直径在5mm以下时,一般采用手动进给,选用35mm的小钻头。
普通麻花钻的进给量可按经验公式f=(0.010.02d0)计算获得。
当加工铸铁和有色金属材料时,进给量f可取0.150.50mm/r;当加工钢件时,进给量f可取0.100.35mm/r。
如采用先进钻型与修磨方法,则能有效降低轴向力,提高进给量。
3、钻削速度Vc的选择钻削速度是指钻头切削刃的线速度,表达式为:
式中,Vc为钻削速度,m/min;d0为钻头直径,mm;n为钻头转速,r/min。
图1-2钻削用量与切削层在铣床上钻孔,一般情况下都是主轴(刀具)做进给运动,所以要选择尽量低的钻削速度。
即使加工较大直径的孔,也要在规定范围内选择较低的钻削速度。
同时,还要考虑被钻孔工件的材料和表面粗糙度要求及麻花钻的耐用度。
钻削速度的选择见表1-1。
3.钻孔的对刀方法1、按划线钻孔如图1-3所示,首先根据加工孔的材料和刀具,合理选择主轴转速。
然后移动工件,使钻头对准划线的圆心样冲眼,即试钻。
如发现有偏心现象,需重新进行校准。
但由于钻头在工件上已定心,即使移动工件再钻,钻头还会落到原来位置上,所以,应在浅孔坑与划线距离较大处錾数条浅槽,使试钻孔底变平不再起导向作用,落钻再试,等对准后即可开始钻孔。
当钻头快要钻通时应减慢进给量,钻通后方可退刀。
图1-3按划线法钻孔2、按靠刀法钻孔如图1-4所示,工件上的孔对基准的孔距尺寸精度要求较高时,如果还采用划线法钻孔就不容易控制了,这时应利用铣床纵、横手轮有刻度的特点,采用靠刀法来对刀实现孔的钻削加工。
具体加工方法如下:
1)先将中心钻夹在夹头内,使中心钻外圆与工件基准刚好靠到后,再向X轴负方向摇进,使中心钻离开工件,再向Y轴正方向摇进s1距离。
2)在此位置上,靠近另一基准后,就可摇过s距离,即对好左起第一个孔的中心位置。
3)用中心钻钻出锥坑,作为导向定位,然后再用钻头钻孔以免产生偏移。
假如直接采用钻头钻削,会由于刀具横刃较长或顶角略不对称,造成定心不准而钻偏,使尺寸公差难以保证。
4)中心钻的钻削速度不宜太低,如3mm的中心钻,主轴可采用950r/min左右的转速,否则刀具容易受损。
一个孔钻削完成后,工作台移动一个孔距,再以相同的方法钻削另一个孔,这样加工的孔距容易得到保证。
图1-4用靠刀法移动距离确定孔的中心位置4.钻孔时工件的装夹在铣床上钻孔常采用机用虎钳和压板、螺栓装夹工件的方法。
如图1-5所示。
(a)用平口钳装夹工件钻孔(b)用压板、螺栓装夹工件钻孔图1-5铣床上钻孔的工件装夹方法二、钻孔的质量分析1.孔位置不准造成孔位置不准的主要原因如下:
1、划线不准或样冲眼未打准。
2、钻头横刃太长使定心不稳。
3、调整孔距时移动尺寸不准。
避免孔位置不准的预防措施如下:
1、提高划线、打样冲眼和钻孔时的对中精度。
2、合理修磨钻头横刃。
3、正确调整铣床移距的坐标尺寸。
2.孔偏斜在铣床上钻出的孔产生偏斜的主要原因如下:
1、钻头两主切削刃不对称。
2、进给量太大而使钻头弯曲。
3、工件端面与钻头轴线不垂直。
4、在圆柱端面上钻孔时,钻头中心未通过工件轴线避免孔产生偏斜的预防措施如下:
1、正确修磨钻头。
2、合理选择进给量。
3、若工件端面不平整,应在钻孔前加工平整或在端面预钻一个引导凹坑。
4、在圆柱端面上钻孔时,应仔细调整,使钻头中心通过工件轴线,并用中心钻预钻引导凹坑。
3.孔呈多角形在铣床上钻出的孔呈多角形的主要原因如下:
1、钻头后角太大。
2、钻头角度不对称,即两主切削刃长短不一致。
避免孔呈多角形的预防措施如下:
1、用砂轮打磨钻头,使其后角小一些。
2、保证两主切削刃的长度一致。
4.孔壁粗糙在铣床上钻出的孔孔壁粗糙的主要原因如下:
1、选用切削液不合理或进给量小。
2、背吃刀量ap过大。
3、钻头被磨损,不够锋利。
4、钻头过短,排屑槽堵塞。
避免钻出的孔孔壁粗糙的预防措施如下:
1、合理选择切削液和切削用量。
2、在加工前合理选择钻头,检查刀具磨损程度,正确修磨钻头。
3、选择工作部分长度大于孔深的钻头或及时退刀排屑。
键槽的铣削一、轴上键槽的技术要求轴上键槽的结构主要有敞开式、半封闭式和封闭式。
槽是要与键相互配合的,主要用于传递扭矩,防止机构打滑。
键槽宽度的尺寸精度要求较高,两侧面的表面粗糙度值要小,键槽与轴线的对称度也有较高的要求,键槽深度的尺寸一般要求不高。
具体要求如下:
1.键槽必须对称于轴的中心线。
在机械行业中,一般键槽的不对称度应该小于或等于0.05mm,侧面和底面须与轴心线平行,其平行度误差应小于或等于0.05mm(在100mm范围内)。
2.键槽宽度、长度和深度需达到图纸要求。
键槽宽的公差见表1-1。
3.键槽在零件上的定位尺寸需根据国标或者图纸要求进行严格控制。
4.表面粗糙度要求一般应不大于Ra6.3。
表5-1键槽宽的公差单位:
m二、轴上键槽的铣削工艺1.工件的装夹及校正装夹工件时,不但要保证工件的稳定性和可靠性,还要保证工件在夹紧后的中心位置不变,即保证键槽中心线与轴心线重合。
铣键槽的装夹方法一般有以下几种。
1、用机用虎钳安装如图1-1(a)所示,用机用虎钳安装适用于在中小短轴上铣键槽。
如图1-1(b)所示,当工件直径有变化时,工件中心在钳口内也随之变动,影响键槽的对称度和深度尺寸。
但装夹简便、稳固,适用于单件生产。
若轴的外圆已精加工过,也可用此装夹方法进行批量生产。
图1-1机用虎钳装夹轴类零件2、用V形铁装夹如图1-2所示为V形铁的装夹情况。
V形铁装夹适用于长粗轴上的键槽铣削,采用V形铁定位支撑的优点为夹持刚度好,操作方便,铣刀容易对中。
其特点是工件中心只在V形铁的角平分线上,随直径的变化而上下变动。
因此,当铣刀的中心对准V形铁的角平分线时,能保证键槽的对称度。
如图1-2(b)所示,在铣削一批直径有偏差的工件时,虽对铣削深度有影响,但变化量一般不会超过槽深的尺寸公差。
如图1-3(c)所示,在卧式铣床上用键槽铣刀加工,当工件的直径变化时,键槽的对称度会受影响。
图1-2V形铁装夹零件3、工作台上T形槽装夹如图1-3所示为将轴件直接安装在铣床工作台T形槽上并使用压板将轴件夹紧的情况,T形槽槽口处的倒角相当于V形铁上的V形槽,能起到定位作用。
当加工直径在2060mm范围内的长轴时,可直接装夹在工作台的T形槽口上,而阶梯轴件和大直径轴件不适合采用这种方法。
(a)铣削轴端键槽(b)铣削轴件上通键槽图1-3在T形槽上装夹轴件4、用分度头装夹如图1-4所示,如果是对称键与多槽工件的安装,为了使轴上的键槽位置分布准确,大都采用分度头或者是带有分度装置的夹具装夹。
利用分度头的三爪自动定心卡盘和后顶尖装夹工件时,工件轴线必定在三爪自定心卡盘和顶尖的轴心线上,工件轴线位置不会因直径变化而变化,因此,轴上键槽的对称性不会受工件直径变化的影响。
图1-4分度头装夹工件5、轴专用虎钳装夹如图1-5所示,使用轴专用虎钳装夹轴类零件时,具有用机用虎钳装夹和V形铁装夹的优点,装夹简便又迅速。
图1-5轴专用虎钳夹工件6、工件的校正如图1-6所示,要保证键槽两侧面和底面都平行于工件轴线,就必须使工件轴线既平行于工作台的纵向进给方向,又平行于工作台台面。
用机用虎钳装夹工件时,用百分表校正固定钳口与纵向进给方向平行,再校正工件上母线与工作台台面平行;用V形铁和分度头装夹工件时,要校正工件母线与纵向进给方向平行,又要校正工件上母线与工作台台面平行。
在装夹长轴时,最好用一对尺寸相等且底面有键的V形铁,以节省校正时间。
图1-6工件的校正2.铣削键槽的铣刀选择铣削键槽的过程中,对铣刀的要求是较为严格的,它直接影响到键槽的精度和表面粗糙度。
通常,铣削敞开式键槽是用三面刃盘铣刀或切口盘铣刀;铣削封闭式键槽是用立铣刀和键槽铣刀。
用立铣刀铣削时,应在槽底位置的一端预钻一个与铣刀直径相等的孔,其深度为槽深。
在安装条件等同的情况下,如果铣刀选择的不同,其铣削后的效果就不同,不论是表面粗糙度还是生产率都有差异,下面具体分析这个问题。
1、让刀现象由于立铣刀齿数较键槽铣刀多,刃带较键槽铣刀长,因此,在立铣刀铣削过程中,当受到一个较大的切削抗力作用时,铣刀就向槽的一侧偏让,在偏让的同时多铣去槽壁一部分,使铣出的槽宽增大,这就是铣工常说的“让刀”现象。
铣刀直径越小,铣削深度越大时让刀越显著。
键槽铣刀之所以能克服立铣刀铣削时产生的缺陷,是因为它齿数少,容屑空间大,排屑流畅,刃短,刚度强。
2、表面粗糙度由于键槽铣刀齿数较立铣刀少,螺旋角小,因此,在铣削时振动大,表面粗糙度大。
3.调整铣刀切削位置铣键槽时,调整铣刀与工件相对位置(对中心),使铣刀旋转轴线对准工件轴线,是保证键槽对称性的关键。
常用的对中心方法如下。
1、擦边对中心如图1-7所示,先在工件侧面贴张薄纸,用干净的液体作为黏液,开动铣床,当铣刀擦到薄纸后,向下退出工件,再横向移动铣刀。
用三面刃盘形铣刀时移动距离A为用键槽铣刀或者立铣刀时移动距离A为式中,A为工作台移动距离(mm);L为铣刀宽度(mm);D为工件直径(mm);d为铣刀直径(mm);为纸厚(mm)。
图1-7擦边对中心法2、切痕对中心切痕对中心的方法使用简便,但对中心精度不高,是最常用的对中心方法。
1)盘形铣刀切痕对中心法。
如图1-8(a)所示,先把工件大致调整到铣刀的中心位置上,开动铣床,在工件表面上切出一个接近铣刀宽度的椭圆形切痕,然后移动横向工作台,使铣刀落在椭圆的中间位置。
2)键槽铣刀切痕对中心法。
如图1-8(b)所示,其原理和盘形铣刀的切痕对中心法相同,只是键槽铣刀的切痕是个边长等于铣刀直径的四方形小平面。
对中心时,使铣刀在旋转时落在小平面的中间位置。
(a)盘形铣刀切痕对中心法(b)键槽铣刀切痕对中心法图1-8切痕对中心法3、百分表对中心如图1-9(a)所示为工件装夹在机用虎钳内加工键槽。
此时,可将杠杆百分表装在铣床主轴上,用手转动主轴,观察百分表在钳口两侧a、b两点的读数,若读数相等,则铣床主轴轴线对准了工件轴线。
这种对中心法较精确。
如图1-9(b)所示为工件装在V形铁或分度头上铣削键槽。
移动工作台,使百分表在a、b两点的数值相等,即对准中心。
(a)(b)图1-9百分表对中心法4.键槽的铣削1、分层铣削法如图1-10所示为分层铣削法。
用这种方法加工,每次铣削深度只有0.51mm,以较大的进给速度往返进行铣削,直至达到深度尺寸要求。
使用此加工方法的优点是铣刀用钝后,只需刃磨端面,磨短不到1mm,铣刀直径不受影响;铣削时不会产生“让刀”现象;但在普通铣床上进行加工时,操作的灵活性不好,生产效率反而比正常切削更低。
图1-10分层铣削法2、扩刀铣削法如图1-11所示为扩刀铣削法。
将选择好的键槽铣刀外径磨小0.30.5mm(磨出的圆柱度要好)。
铣削时,在键槽的两端各留0.5mm余量,分层往复走刀铣至深度尺寸,然后测量槽宽,确定宽度余量,用符合键槽尺寸的铣刀由键槽的中心对称扩铣槽的两侧至尺寸,并同时铣至键槽的长度,如图1-11所示。
铣削时注意保证键槽两端圆弧的圆度。
这种铣削方法容易产生“让刀”现象,使槽侧产生斜度。
图1-11分层铣削至深度尺再扩铣两侧三、轴上键槽的检测和铣削质量分析1.轴上键槽的检测方法1、键槽宽度检测根据键槽的具体精度要求,可选用游标卡尺、内径百分尺、内径千分尺和塞规测量键槽宽度。
键槽的宽度一般要求较高。
2、键槽深度检测键槽深度检测可用各类游标卡尺、外径百分尺、外径千分尺进行测量,如图1-12所示。
键槽的深度精度要求一般都不高。
(a)千分尺测量槽深(b)块规配合游标卡尺测量槽深图1-12轴上键槽深度检测3、键槽中心平面与轴心线的对称度检测如图1-13所示,将工件置入V形铁内,选择一块与键槽宽度尺寸紧密配合的塞块塞入槽内,并使塞块的平面大致处于水平位置,用百分表检测塞块A面与平板(钳工高精度检验和划线专用工具)平面平行并读数,然后将工件转180,用百分表检测塞块B面与平板平面平行并读数,两次读数差值的一半,就是键槽对称度误差。
图1-13轴上键槽对称度检测4、键槽的长度和轴向位置检测测量键槽的长度和轴向位置可用钢直尺或游标卡尺测量。
5、表面粗糙度的检测表面粗糙度的检测应注意选择相对应的对比样板,也可用粗糙度仪进行检验。
如果知道具体的数值,则用粗糙度检测仪;如果只是大概地评判,就可以用粗糙度样板来对比;也可以用探针检测,也就是在金属表面取一定长度的距离(10mm),用探针沿直线测其表面的凹凸深度,最后取平均值。
2.质量分析1、铣削半封闭键槽常见质量问题及其原因铣削半封闭键槽常见质量问题及其原因如下:
1)键槽宽度尺寸超差的主要原因可能是铣刀宽度尺寸人为测量误差、铣刀安装后端面跳动过大、铣刀刀尖刃磨质量不高或是早期磨损等情况。
2)键槽槽底与轴线不平行度超差的原因可能是工件圆柱面上素线与工作台面不平行、V形特殊钳口安装误差过大等。
3)键槽对称度超差的原因可能是目测切痕对刀法导致人为误差过大、铣削时产生“让刀”现象、铣削时工作台横向未锁紧等。
2、铣削封闭键槽常见的质量问题及其原因铣削封闭键槽常见的质量问题及其原因如下:
1)键槽宽度尺寸超差的主要原因可能是键槽铣刀直径尺寸的测量误差。
键槽铣刀安装后径向跳动过大、铣刀端部周刃刃磨质量不高或是早期磨损等情况。
2)键槽对称度超差的原因可能是目测切痕对中心法导致人为误差过大、铣削时因进给量较大产生了“让刀”现象、铣削时工作台横向未锁紧等。
3)键槽端部出现较大圆弧的原因可能是铣刀的转速过低、垂向手动进给速度过快、铣刀端齿中心部位刃磨质量不好(刀心没有过刃,即各切削刃间无连接),使端面齿切削受阻。
4)键槽深度超差的原因可能是铣刀夹持不够牢固,铣削时,沿螺旋线方向被拉下;垂向调整尺寸出现计算或操作失误。
巡回指导:
1.注意检查学生的操作是否正确,对于个别的差生,要单独进行指导,随时纠正其错误的操作。
2.对普遍存在的问题采取集中指导的方法,即把部分同学或全体同学集合起来,先根据出现的问题加以纠正,后再把正确结果进行反复演示,这样可使学生进一步加深理解。
3.注意帮助学生提高分析问题和解决问题的能力,充分发挥学生的主观能动性,引导学生自主学习和探究,激发学生的学习热情。
课后总结:
1.本课题实习操作训练总结:
1、教师全面总结。
2、学生自我总结。
2.总结课堂纪律情况。
3.做好机床及车间卫生