连杆加工工艺规程及夹具设计.docx
《连杆加工工艺规程及夹具设计.docx》由会员分享,可在线阅读,更多相关《连杆加工工艺规程及夹具设计.docx(15页珍藏版)》请在冰豆网上搜索。
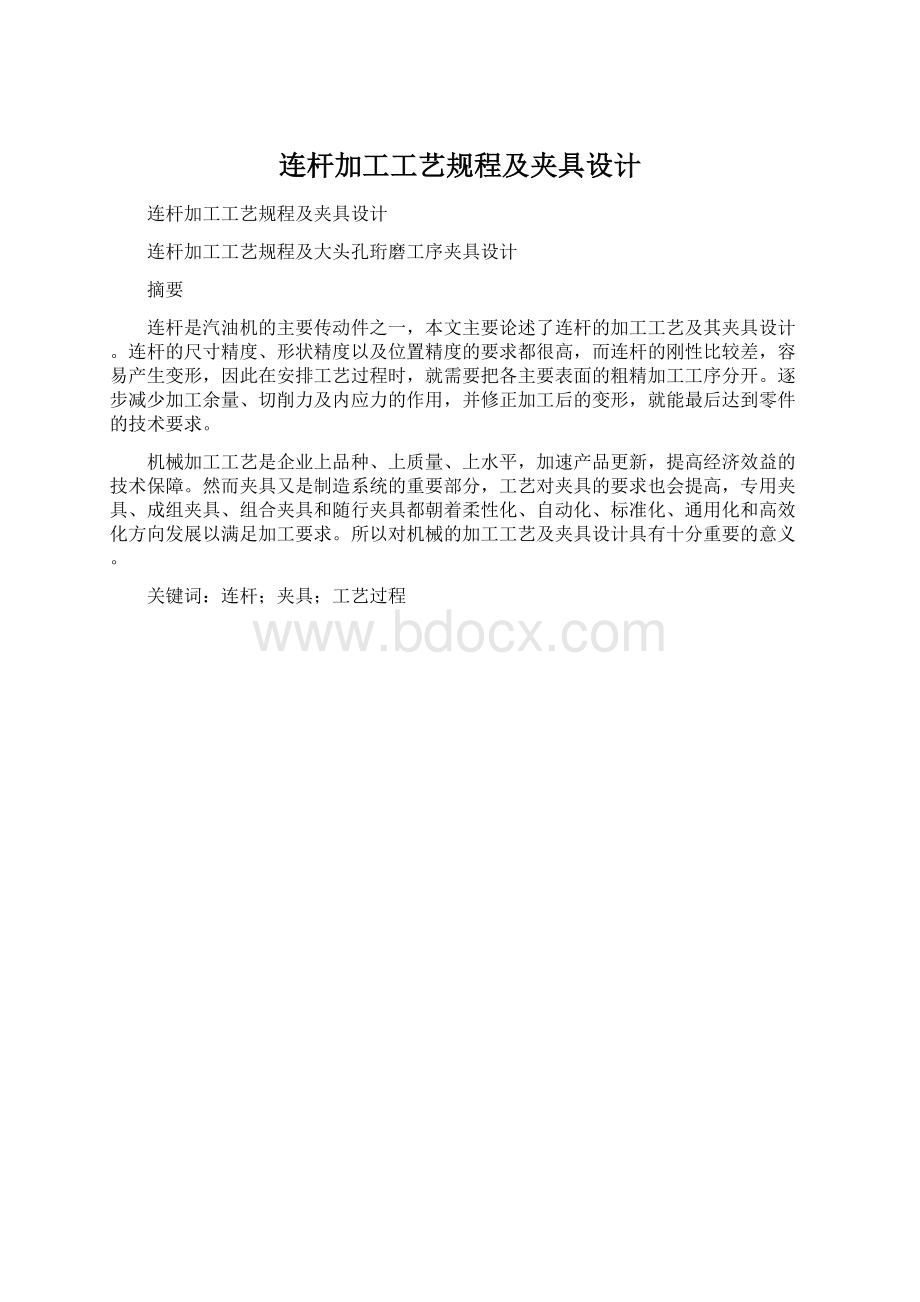
连杆加工工艺规程及夹具设计
连杆加工工艺规程及夹具设计
连杆加工工艺规程及大头孔珩磨工序夹具设计
摘要
连杆是汽油机的主要传动件之一,本文主要论述了连杆的加工工艺及其夹具设计。
连杆的尺寸精度、形状精度以及位置精度的要求都很高,而连杆的刚性比较差,容易产生变形,因此在安排工艺过程时,就需要把各主要表面的粗精加工工序分开。
逐步减少加工余量、切削力及内应力的作用,并修正加工后的变形,就能最后达到零件的技术要求。
机械加工工艺是企业上品种、上质量、上水平,加速产品更新,提高经济效益的技术保障。
然而夹具又是制造系统的重要部分,工艺对夹具的要求也会提高,专用夹具、成组夹具、组合夹具和随行夹具都朝着柔性化、自动化、标准化、通用化和高效化方向发展以满足加工要求。
所以对机械的加工工艺及夹具设计具有十分重要的意义。
关键词:
连杆;夹具;工艺过程
1连杆的结构特点
连杆是汽车发动机中的主要传动部件之一,它在汽油机中,把作用于活塞顶面的膨胀的压力传递给曲轴,又受曲轴的驱动而带动活塞压缩气缸中的气体。
连杆在工作中承受着急剧变化的动载荷。
连杆由连杆体及连杆盖两部分组成。
连杆体及连杆盖上的大头孔用螺栓和螺母与曲轴装在一起。
为了减少磨损和便于维修,连杆的大头孔内装有薄壁金属轴瓦。
轴瓦有钢质的底,底的内表面浇有一层耐磨巴氏合金轴瓦金属。
在连杆体大头和连杆盖之间有一组垫片,可以用来补偿轴瓦的磨损。
连杆小头用活塞销与活塞连接。
小头孔内压入青铜衬套,以减少小头孔与活塞销的磨损,同时便于在磨损后进行修理和更换。
在发动机工作过程中,连杆受膨胀气体交变压力的作用和惯性力的作用,连杆除应具有足够的强度和刚度外,还应尽量减小连杆自身的质量,以减小惯性力的作用。
连杆杆身一般都采用从大头到小头逐步变小的工字型截面形状。
为了保证发动机运转均衡,同一发动机中各连杆的质量不能相差太大,因此,在连杆部件的大、小头两端设置了去不平衡质量的凸块,以便在称量后切除不平衡质量。
连杆大、小头两端对称分布在连杆中截面的两侧。
考虑到装夹、安放、搬运等要求,连杆大、小头的厚度相等(基本尺寸相同)。
在连杆小头的顶端设有油孔(或油槽),发动机工作时,依靠曲轴的高速转动,把气缸体下部的润滑油飞溅到小头顶端的油孔内,以润滑连杆小头衬套与活塞销之间的摆动运动副。
连杆的作用是把活塞和曲轴联接起来,使活塞的往复直线运动变为曲柄的回转运动,以输出动力。
因此,连杆的加工精度将直接影响柴油机的性能,而工艺的选择又是直接影响精度的主要因素。
反映连杆精度的参数主要有5个:
(1)连杆大端中心面和小端中心面相对连杆杆身中心面的对称度;
(2)连杆大、小头孔中心距尺寸精度;(3)连杆大、小头孔平行度;(4)连杆大、小头孔尺寸精度、形状精度;(5)连杆大头螺栓孔与接合面的垂直度。
2毛坯选择
2.1毛坯的材料
连杆在工作中承受多向交变载荷的作用,要求具有很高的强度。
因此,连杆材料一般采用高强度碳钢和合金钢;如45钢、55钢、40Cr、40CrMnB等。
2.2毛坯制造方法的选择
连杆毛坯制造方法的选择,主要根据生产类型、材料的工艺性(可塑性,可锻性)及零件对材料的组织性能要求,零件的形状及其外形尺寸,毛坯车间现有生产条件及采用先进的毛坯制造方法的可能性来确定毛坯的制造方法。
根据生产纲领为大量生产,连杆多用模锻制造毛坯。
连杆模锻形式有两种,一种是体和盖分开锻造,另一种是将体和盖锻成—体。
整体锻造的毛坯,需要在以后的机械加工过程中将其切开,为保证切开后粗镗孔余量的均匀,最好将整体连杆大头孔锻成椭圆形。
相对于分体锻造而言,整体锻造存在所需锻造设备动力大和金属纤维被切断等问题,但由于整体锻造的连杆毛坯具有材料损耗少、锻造工时少、模具少等优点,故用得越来越多,成为连杆毛坯的一种主要形式。
总之,毛坯的种类和制造方法的选择应使零件总的生产成本降低,性能提高。
连杆的锻造工艺,将棒料在炉中加热至1140~1200C0,先在辊锻机上通过四个型槽进行辊锻制坯,然后在锻压机上进行预锻和终锻,再在压床上冲连杆大头孔并切除飞边见图2.1。
锻好后的连杆毛坯需经调质处理,使之得到细致均匀的回火索氏体组织,以改善性能,减少毛坯内应力。
为了提高毛坯精度,连杆的毛坯尚需进行热校正。
图2.1连杆毛坯图
3连杆的主要技术要求
连杆上需进行机械加工的主要表面为:
大、小头孔及其两端面,连杆体与连杆盖的结合面及连杆螺栓定位孔等。
连杆总成的主要技术要求如下。
3.1大、小头孔的尺寸精度、形状精度
为了使大头孔与轴瓦及曲轴、小头孔与活塞销能密切配合,减少冲击的不良影响和便于传热。
大头孔公差等级为IT6,表面粗糙度Ra应不大于0.4μm;大头孔的圆柱度公差为0.004~0.006mm,小头孔公差等级为IT7,表面粗糙度Ra应不大于3.2μm。
3.2大、小头孔轴心线在两个互相垂直方向的平行度
两孔轴心线在连杆轴线方向的平行度误差会使活塞在汽缸中倾斜,从而造成汽缸壁磨损不均匀,同时使曲轴的连杆轴颈产生边缘磨损,所以两孔轴心线在连杆轴线方向的平行度公差较小;而两孔轴心线在垂直于连杆轴线方向的平行度误差对不均匀磨损影响较小,因而其公差值较大。
两孔轴心线在连杆的轴线方向的平行度在100mm长度上公差为0.04mm;在垂直与连杆轴心线方向的平行度在100mm长度上公差为0.06mm。
3.3大、小头孔中心距
大小头孔的中心距影响到汽缸的压缩比,即影响到发动机的效率,所以规定了比较高的要求:
mm。
3.4连杆大头孔两端面对大头孔中心线的垂直度
连杆大头孔两端面对大头孔中心线的垂直度,影响到轴瓦的安装和磨损,甚至引起烧伤;所以对它也提出了一定的要求:
规定其垂直度公差等级应不低于IT7(大头孔两端面对大头孔的轴心线的垂直度在100mm长度上公差为0.06mm)。
3.5大、小头孔两端面的技术要求
连杆大、小头孔两端面间距离的基本尺寸相同,但从技术要求是不同的,大头两端面的尺寸公差等级为IT7,表面粗糙度Ra不大于0.8μm,小头两端面的尺寸公差等级为IT12,表面粗糙度Ra不大于6.3μm。
这是因为连杆大头两端面与曲轴连杆轴颈两轴肩端面间有配合要求,而连杆小头两端面与活塞销孔座内档之间没有配合要求。
连杆大头端面间距离尺寸的公差带正好落在连杆小头端面间距离尺寸的公差带中,这给连杆的加工带来许多方便。
3.6螺栓孔的技术要求
在前面已经说过,连杆在工作过程中受到急剧的动载荷的作用。
这一动载荷又传递到连杆体和连杆盖的两个螺栓及螺母上。
因此除了对螺栓及螺母要提出高的技术要求外,对于安装这两个动力螺栓孔及端面也提出了一定的要求。
规定:
螺栓孔按IT8级公差等级和表面粗糙度Ra应不大于6.3μm加工;两螺栓孔在大头孔剖分面的对称度公差为0.25mm。
4连杆机械加工工艺过程分析
连杆的主要加工表面为大、小头孔和两端面,较重要的加工表面为连杆体和盖的结合面及连杆螺栓孔定位面,次要加工表面为轴瓦锁口槽、油孔、大头两侧面及体和盖上的螺栓座面等。
连杆的机械加工路线是围绕着主要表面的加工来安排的。
连杆的加工路线按连杆的分合可分为三个阶段:
第一阶段为连杆体和盖切开之前的加工;第二阶段为连杆体和盖切开后的加工;第三阶段为连杆体和盖合装后的加工。
第一阶段的加工主要是为其后续加工准备精基准(端面、小头孔和大头外侧面);第二阶段主要是加工除精基准以外的其它表面,包括大头孔的粗加工,为合装做准备的螺栓孔和结合面的粗加工,以及轴瓦锁口槽的加工等;第三阶段则主要是最终保证连杆各项技术要求的加工,包括连杆合装后大头孔的半精加工和端面的精加工及大、小头孔的精加工。
如果按连杆合装前后来分,合装之前的工艺路线属主要表面的粗加工阶段,合装之后的工艺路线则为主要表面的半精加工、精加工阶段。
4.1工艺过程的安排
在连杆加工中有两个主要因素影响加工精度:
(1)连杆本身的刚度比较低,在外力(切削力、夹紧力)的作用下容易变形。
(2)连杆是模锻件,孔的加工余量大,切削时将产生较大的残余内应力,并引起内应力重新分布。
因此,在安排工艺进程时,就要把各主要表面的粗、精加工工序分开,即把粗加工安排在前,半精加工安排在中间,精加工安排在后面。
这是由于粗加工工序的切削余量大,因此切削力、夹紧力必然大,加工后容易产生变形。
粗、精加工分开后,粗加工产生的变形可以在半精加工中修正;半精加工中产生的变形可以在精加工中修正。
这样逐步减少加工余量,切削力及内应力的作用,逐步修正加工后的变形,就能最后达到零件的技术条件。
各主要表面的工序安排如下:
(1)两端面:
粗铣、精铣、粗磨、精磨
(2)小头孔:
钻孔、扩孔、铰孔、精镗
(3)大头孔:
扩孔、粗镗、半精镗、精镗、珩磨
一些次要表面的加工,则视需要和可能安排在工艺过程的中间或后面。
4.2定位基准的选择
在连杆机械加工工艺过程中,大部分工序选用连杆的一个指定的端面和小头孔作为主要基面,并用大头处指定一侧的外表面作为另一基面。
这是由于:
端面的面积大,定位比较稳定,用小头孔定位可直接控制大、小头孔的中心距。
这样就使各工序中的定位基准统一起来,减少了定位误差。
为了不断改善基面的精度,基面的加工与主要表面的加工要适当配合:
即在粗加工大、小头孔前,粗磨端面,在精镗大、小头孔前,精磨端面。
由于用小头孔和大头孔外侧面作基面,所以这些表面的加工安排得比较早。
在小头孔作为定位基面前的加工工序是钻孔、扩孔和铰孔,这些工序对于铰后的孔与端面的垂直度不易保证,有时会影响到后续工序的加工精度。
4.3连杆体与连杆盖的铣开工序
剖分面(亦称结合面)的尺寸精度和位置精度由夹具本身的制造精度及对刀精度来保证。
为了保证铣开后的剖分面的平面度不超过规定的公差0.03mm,并且剖分面与大头孔端面保证一定的垂直度,除夹具本身要保证精度外,锯片的安装精度的影响也很大。
如果锯片的端面圆跳动不超过0.02mm,则铣开的剖分面能达到图纸的要求,否则可能超差。
但剖分面本身的平面度、粗糙度对连杆盖、连杆体装配后的结合强度有较大的影响。
因此,在剖分面铣开以后再经过磨削加工。
4.4大头侧面的加工
以基面及小头孔定位,它用一个圆销(小头孔)。
装夹工件铣两侧面至尺寸,保证对称(此对称平面为工艺用基准面)。
5切削用量的选择原则
正确地选择切削用量,对提高切削效率,保证必要的刀具耐用度和经济性,保证加工质量,具有重要的作用。
5.1粗加工时切削用量的选择原则
粗加工时加工精度与表面粗糙度要求不高,毛坯余量较大。
因此,选择粗加工的切削用量时,要尽可能保证较高的单位时间金属切削量(金属切除率)和必要的刀具耐用度,以提高生产效率和降低加工成本。
金属切除率可以用下式计算:
Zw≈V.f.ap.1000
式中:
Zw单位时间内的金属切除量(mm3/s);
V切削速度(m/s);
f进给量(mm/r);
ap切削深度(mm)。
提高切削速度、增大进给量和切削深度,都能提高金属切除率。
但是,在这三个因素中,影响刀具耐用度最大的是切削速度,其次是进给量,影响最小的是切削深度。
所以粗加工切削用量的选择原则是:
首先考虑选择一个尽可能大的吃刀深度ap,其次选择一个较大的进给量度f,最后确定一个合适的切削速度V.
选用较大的ap和f以后,刀具耐用度t显然也会下降,但要比V对t的影响小得多,只要稍微降低一下V便可以使t回升到规定的合理数值,因此,能使V、f、ap的乘积较大,从而保证较高的金属切除率。
此外,增大ap可使走刀次数减少,增大f又有利于断屑。
因此,根据以上原则选择粗加工切削用量对提高生产效率,减少刀具消耗,降低加工成本是比较有利的。
5.1.1切削深度的选择
粗加工时切削深度应根据工件的加工余量和由机床、夹具、刀具和工件组成的工艺系统的刚性来确定。
在保留半精加工、精加工必要余量的前提下,应当尽量将粗加工余量一次切除。
只有当总加工余量太大,一次切不完时,才考虑分几次走刀。
5.1.