电石炉开车方案.docx
《电石炉开车方案.docx》由会员分享,可在线阅读,更多相关《电石炉开车方案.docx(10页珍藏版)》请在冰豆网上搜索。
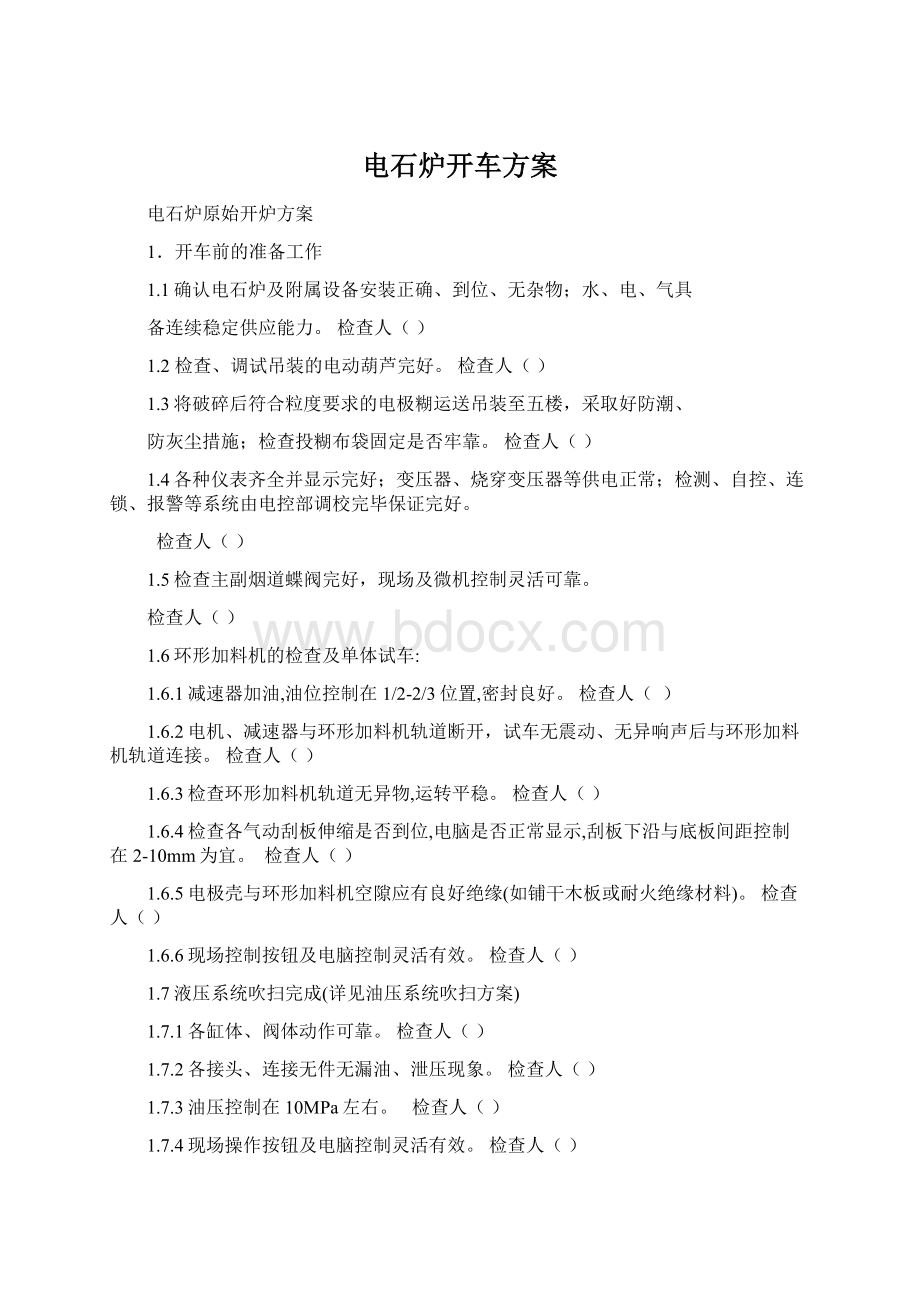
电石炉开车方案
电石炉原始开炉方案
1.开车前的准备工作
1.1确认电石炉及附属设备安装正确、到位、无杂物;水、电、气具
备连续稳定供应能力。
检查人()
1.2检查、调试吊装的电动葫芦完好。
检查人()
1.3将破碎后符合粒度要求的电极糊运送吊装至五楼,采取好防潮、
防灰尘措施;检查投糊布袋固定是否牢靠。
检查人()
1.4各种仪表齐全并显示完好;变压器、烧穿变压器等供电正常;检测、自控、连锁、报警等系统由电控部调校完毕保证完好。
检查人()
1.5检查主副烟道蝶阀完好,现场及微机控制灵活可靠。
检查人()
1.6环形加料机的检查及单体试车:
1.6.1减速器加油,油位控制在1/2-2/3位置,密封良好。
检查人()
1.6.2电机、减速器与环形加料机轨道断开,试车无震动、无异响声后与环形加料机轨道连接。
检查人()
1.6.3检查环形加料机轨道无异物,运转平稳。
检查人()
1.6.4检查各气动刮板伸缩是否到位,电脑是否正常显示,刮板下沿与底板间距控制在2-10mm为宜。
检查人()
1.6.5电极壳与环形加料机空隙应有良好绝缘(如铺干木板或耐火绝缘材料)。
检查人()
1.6.6现场控制按钮及电脑控制灵活有效。
检查人()
1.7液压系统吹扫完成(详见油压系统吹扫方案)
1.7.1各缸体、阀体动作可靠。
检查人()
1.7.2各接头、连接无件无漏油、泄压现象。
检查人()
1.7.3油压控制在10MPa左右。
检查人()
1.7.4现场操作按钮及电脑控制灵活有效。
检查人()
1.8电极升降、压放、夹紧装置、电加热元件、风机现场及电脑操作灵活可靠。
检查人()
1.9各料仓料位计、把持器位置、电极压放量、测量装置校验与电脑显示一致。
检查人()
1.10检查变压器、短网、导电系统开关等良好;检查全部电绝缘点如电极筒与大套之间绝缘良好;导电接触元件与护屏、大套之间绝缘良好;底环与筋板及拉筋绝缘良好、与水冷密封套绝缘良好;电炉设备绝缘良好;电极相间、电极对地之间绝缘良好。
(绝缘试验500V电压摇表测试不得低于0.5MΩ,标准要求用36V灯泡通电不亮为准或用380伏电焊机进线和绝缘部分接着无打火为良好。
)
检查人()
1.11电极大套固定导轮润滑良好。
检查人()
1.12氮气密封系统完好,料管氮气密封压力98Pa(阀门开启灵活)。
检查人()
1.13水路吹扫完成(详见冷却水路系统清洗及试压试漏),通水后检查无漏水现象,各回水流量正常,水路管线挂牌,并逐个开关确认标牌与水路一致。
检查人()
1.14检查导电接触元件上碟簧弹力是否正确达到要求;弹簧总成上的锁紧螺钉是否拧紧。
检查人()
1.15出炉风机、炉底风机检查、调试正常。
检查人()
1.16物资准备
1.16.1电极壳焊接工具到位。
检查人()
1.16.2便携式CO自动检测仪。
检查人()
1.16.3耙子、捣子、钢钎、铁棒、测量电极用的圆钢、量角器、电筒等处理料面所需工具准备齐全。
检查人()
1.16.4堵子、铲子、吹氧管、氧瓶及减压阀、耐压胶管、铁揪、圆钢、大锤、撬棍、泥球、炭棒等所需出炉工具准备齐全。
检查人()
1.16.5测电极糊柱高度的工具(绝缘梯子等)准备齐全。
检查人()
1.17各生产区域照明满足要求。
检查人()
1.18电石生产工艺规程、操作规程、安全规程已编制完善。
检查人()
1.19各岗位通讯设备完好,保证畅通。
检查人()
1.20原料输送、炭材干燥、石灰生产满足开炉所需要求。
检查人()
1.21所有操作人员必须熟悉开车方案和岗位操作规程,按要求穿戴好劳动防护用品,做好安全防护,闲杂人员等离开开车现场。
检查人()
2.开车操作
2.1砌筑假炉门:
三相电极相对应出炉嘴向电极中心砌假炉门,材质为粘土砖,由炉衬内侧砌筑至起动缸处,几何尺寸:
宽×高=250×500mm,炉门中心置φ150mm,长约3000mm圆木,用黄泥密封。
检查人()
2.2装炉
2.2.1炉体底部平铺焦炭,厚度为150mm,粒度为10─20mm。
检查人()
2.2.2三相电极下各置起动缸一只,钢板厚度3─6mm,直径×高=1400×1200mm。
检查人()
2.2.3起动缸内装满焦炭,粒度10─20mm。
检查人()
2.2.4起动缸之间用φ20─30mm圆钢连接,相间不少于4根。
检查人()
2.2.5起动缸间及电炉炉膛其余部位装入炉料,装料时石灰严禁进入导电柱内,起动缸旁及三角区混合料高度与启动缸基本持平,四周混合料高于启动缸约300-500mm。
配比为石灰:
焦炭=100:
65~70。
检查人()
2.2.6电极壳下部做成椎体状,底部用8mm钢板焊接密封,内装入电极糊,粒度不大于100mm,高度为把持器上约4m处。
检查人()2.2.7装炉完成后下放电极筒使之与启动缸内焦炭紧密接触防止送电初期电极放弧烧坏底部密封板。
检查人()
装炉示意图:
2.3送电
2.3.1电炉变压器经试送无短路,断路等现象后方可进行送电。
检查人()
2.3.2送电电压:
2级 星接线 V2=82.8V电极电压:
47.8V。
检查人()
2.4烘炉及焙烧电极
2.4.1送电前封闭通往石灰窑系统烟囱阀,打开粗气烟囱阀,炉盖检查门对称打开三个,冷却水,压缩空气投入运行。
检查人()
2.4.2开启电极加热元件:
3档24kW。
检查人()
2.4.3送电后不可过分下落电极。
检查人()
2.4.4电极负荷增加:
按电极加热及焙烧状况而定:
2.4.4.1首先将变压器接线方式改为“Y”。
检查人()
2.4.4.2有功功率达到21000kW后停止增升,稳定运行,一次电流最高不超过500A,二次电流不超过85kA,电压级根据电炉负荷与炉况均匀调整,开炉结束,此阶段大约需要3天时间。
检查人()
2.4.5电极随着消耗,可适当压放电极,保持应有的工作长度,电极糊柱高度,随着电极的压放适量装入电极糊,保持固有高度。
检查人()
2.5试产
2.5.1在烘炉及焙烧电极过程中起动缸内可适量加入焦炭,其它部位则加入炉料,以稳定电弧及负荷。
检查人()
2.5.2当负荷增至10000kW时,如炉况不稳定可随时出炉。
检查人()
2.5.3当负荷达到15000kW时,每8小时出炉暂定4~5次。
检查人()
2.5.4当负荷达到18000kW时,每8小时出炉暂定6~8次。
检查人()
2.5.5因电极入炉深度不平衡时,三相电极电压允许不平衡运行,电压级差最大允许三级。
检查人()
2.5.6开炉过程中随着负荷的增加,炉气量增大,当烟气不能从烟囱正常排出时,逐个关闭检查门,直至全部关闭转入闭炉操作,此时炉压设定值为0Pa。
检查人()
2.5.7烘炉阶段加料管闭料,随着负荷的增加及炉况变化,逐步过渡到连续加料。
检查人()
2.6正常生产
2.6.1电炉负荷达到18000kW正常连续运行72小时,闭炉操作。
连续加料标志试产结束,即开炉工作结束转入正常生产。
检查人()
2.7注意事项
2.7.1因电极无固化电极,送电后加热,易产生软断
2.7.2开炉阶段是电炉事故多发阶段,炉压不稳、电极折断、塌料等现象随时可能发生,因而特别注意人身及设备安全。
2.7.3安全防护严格执行安全操作规程。
2.8紧急停电
2.8.1在生产中遇下列情况之一须紧急停电:
电极软、硬断;导电接触元件放弧(刺火);炉内设备大量漏水;氢气含量突然大幅度上升;油、水管、液压系统突然故障;电极突然下滑;炉内大量翻电石和炉压过大;炉温急剧上升可采用紧急停电或电气设备自动断电。
冷却水路系统清洗及试压试漏
1.水路清洗
1.1人工清除水分布器回水槽,清理过程中注意杂物不得进入下水管。
检查水槽至循环水站管路是否通畅,并拆除阀门。
检查人()
1.2检查进水管路是否安装完成,各接头是否紧固,特别是短网部分水路。
检查人()
1.3关闭各支路进口阀门及各配水器进口阀门。
检查人()
1.4打开1#水分配器排污阀(全开),下部用胶管接至回水槽。
检查人()
1.5拆除各水分配器接点的压力表,并将进口阀关死。
检查人()
1.6关闭进水总阀、通知脱盐水站送脱盐水,保证压力0.5MPa,缓慢开启进水总阀,将进口阀开至1/5即可。
检查人()
1.7在送水过程中,用木锤轻敲各管路焊缝处,使焊渣及杂物等被水冲走,在排污口处用白布过滤,防止杂物等进入回水槽、直至出水无杂物,焊渣等,水流清澈,白布无杂物则结束。
关闭排污阀。
检查人()
1.8依以上方法进行2#、3#水分配器的清洗。
检查人()
1.9依次打开各接点阀门,排出清水即可。
检查人()
1.10检查回水槽至循环水站管路回流水是否是清水流出,并安装好阀门,并将阀门全部开满。
检查人()
1.11清洗完毕后,依次安装好各阀门及压力表,并紧固。
检查人()
1.12依次打开各支路进水阀,在管口用白布过滤,送水过程中轻敲各焊缝接口,直至白布上无杂物焊渣等,即为合格。
全格后,关闭支路阀门,依次进行下一支路清洗,直至全部合格。
检查人()
2.循环水路系统试压试漏
2.1关闭进水总阀,关闭各水分配器进水阀,排污阀,各支路进水阀。
2.2通知脱盐循环水送水,压力要求长期保持大于0.5MPa,不超过0.8MPa。
检查人()
2.3缓慢打开总管阀门,将脱盐水送至各水分配器进口阀,再缓慢打开1#水分配器进口阀,用水分配器进水阀将压力控制在额定压力0.5MPa,关进口阀保压30分钟,如压力下降,则说明1#水分配器及各支路泄漏现象,如有支路出现有回水现象,则说明该支路阀门内漏,需更换。
检查人()
2.4试压试漏合格后,打开排污阀进行泄压。
检查人()
2.5依以上方法分别对2#、3#水分配器进行试压试漏,直至合格。
检查人()
2.6将1#水分配器各支路出口接上胶管头,将一端密封,并紧固密封。
检查人()
2.7将1#水分配器全部支路阀打开,缓慢开启1#水分配器进水阀,先控制在水压0.4MPa,检查有无泄漏,然后将水压控制在0.5MPa保压30分钟,检查有无泄漏,直至全部合格,试压试漏结束后关闭1#水分配器。
检查人()
2.8对1#水分配器上各支路的胶管与高温部分进行防水材料的包扎。
检查人()
2.9依次进行2#、3#水分配器的各支路试压试漏,方法同上,合格后,最后进行防火材料的包扎。
检查人()
2.10将各分配器进水阀缓慢全开,水压保证在0.4MPa,使冷却水路全部处于正常状态,并对各水路进行编号,核对其微机信号与现场接点的温度、压力、流量等是否相符。
检查人()
2.11检查微机显示的温度、压力、流量等与现场水路编号是否相符,是否准确。
检查人()
油压系统吹扫方案
1.物质准备(单台炉)
柴油100L白布20米面粉10kg面盆3个草纸10捆
塑料袋400个黄油5kg圆板(10cm2)5个木锤5把
高压空压机1台氧气管20m氮气10瓶氧气表1块
盲板(现场制作)废油桶1个检查人()
2.安全要求及注意事项:
2.1清洗过程中禁止烟火,防止烧伤事故。
2.2吹扫过程中,人员不得面对出气管口,禁止用手去充当检验板,防止杂物冲出伤人。
2.3吹扫及清洗过程中注意防尘,防止污物进入设备管路内部,清洗吹扫完毕后封口。
3.油箱清洗
3.1用柴油清洗油箱,清洗杂物、除锈,用草纸、白布将残余柴油清除干净,废油用油桶回收。
检查人()
3.2面粉加水,和好面团,用面团将油箱内部、角落的铁锈粉及杂物粘起清除干净。
检查人()
3.3清洗完毕,将油箱密封,缝隙用白布遮盖。
检查人()
4.电磁阀及阀门清洗
4.1按顺序吹扫秩序依次拆除电磁阀及阀门,用柴油清洗,保证内部元杂物,动作灵活,清洗完毕后用塑料袋密封,防止灰尘杂物进入。
检查人()
4.2制作检验板:
用白布蒙住圆木板,在白布上均匀涂上薄黄油一层。
白布剪成20cm2、100块备用检查人()
5.油路吹扫
5.1总线油路吹扫:
按油泵流程依次拆除阀门,及电磁阀,并与清洗干净的油箱隔离。
检查人()
5.1.1用空气吹扫(空压机压力>=0.8MPa)底座,用木锤敲击管路,特别是焊缝处,用检验板在管口出口距离15cm-20cm时检验,要求10cm2污点小于5个,即为合格。
检查人()
5.1.2用氮气吹报置换,同样用此方法进行,检验,直至合格。
检查人()
5.1.3安装上清洗干净的电磁阀(到大力缸的暂不安装),阀门在出口处用塑料袋封好。
检查人()
5.1.4过滤器拆除清洗,滤网清洗干净后安装坚固合格。
检查人()
5.2油冷器吹扫:
5.2.1油路部分按5.1.1、5.1.2办法吹扫。
检查人()
5.2.2水路部分按5.1.1办法吹扫。
检查人()
5.2.3结束后,均安装合格,出口密封。
检查人()
5.3大力缸油路系统吹扫
5.3.1拆除大力缸进油口阀门,清洗合格。
检查人()
5.3.2先用空气后氮气吹扫(空压机压力>=0.8MPa)进口插在电磁阀底坐上,将B大力缸处出口管上盲板(现场制作),对A大力缸的油路吹扫,用检验板检查(同上)至合格,拆除B大力缸盲板,对A大力缸上盲板,对A大力缸支路进行吹扫至合格,结束后,装好清洗合格后的阀门、并紧固。
检查人()
5.3.3如上吹扫的大力缸为有杆腔结束后,更换进气口,吹扫大力缸无杆腔,方法同5.3.1、5.3.2、5.3.3。
检查人()
5.3.4大力缸全部吹扫结束后,安装上清洗合格的电磁阀及阀门,紧固。
检查人()
5.4压放系统油路吹扫
5.4.1拆除压放油路系统的电磁阀,阀门,并清洗合格。
检查人()
5.4.2对压放泵至各电极配油器管路吹扫,拆除油分配器、清洗合格。
检查人()
5.4.3将空气氮气(压力>=0.8MPa)插入泵出口的底坐上,按以上方法分别对各电极的配油路吹扫,并检验合格。
检查人()
5.4.4对各吹扫结束的管路做好密封防尘工作,用塑料袋封口。
检查人()
5.4.5分别对配油器到各电磁阀底座用同样方法吹扫。
检查人()
5.5各电磁阀到夹紧缸,压放缸的油路吹扫。
5.5.1拆除各支路电磁阀,分别从配油器底座到各电磁阀底座进行吹扫,并检查合格。
拆除的各电磁阀,阀门等清洗合格,密封备用。
检查人()
5.5.2将各电极夹紧缸的无杆腔的油管拆除,留下一个口,余支路用盲板封住,对夹紧缸无杆腔油路进行逆向吹扫(方法同上)注意与配合器隔离,吹扫结束后,分别拆除盲板,进行其他接口吹扫,结束后安装合格。
检查人()
5.5.3分别拆除各油缸(压放缸,夹紧缸)的无杆腔,有杆腔的接头,从电磁阀底座进、回油口,进行空气、氮气吹扫,直至合格。
(方法同上)。
结束后,将电磁阀,阀门等安装合格,各紧固件,安装到位,检查有无遗漏。
油路系统吹扫结束。
检查人()
油压系统试压试漏及试运行
1.物质准备
专用液压油8桶滤油机1台滤纸1000张打孔机1台
检查人()
2.在油压系统清洗吹扫结束之后进行
2.1通知电仪对各油泵、电磁阀等接线进行检查,确认安装合格。
检查人()
2.2用滤油机将油桶内油加至液压站油箱,加至油位1/2-2/3时停止。
检查人()
2.3首先对过滤泵进行盘车3-5圈,确认无异常后,打开进口阀,开启过滤泵,确认无异常后,开启过滤器进口阀,开始滤油,检查泵、电机温度、振动,注意检查各接口部分泄漏情况,并保持长期开启。
检查人()
2.4将1#泵出口先导阀逆时针打到全开位置,开启1#泵进口阀,按正常步骤启动1#油泵,开泵后,如泵无异常情况,顺时针调节1#泵出口先导阀,动作要缓慢,使压力缓慢上升,首先使压力达到2.5MPa,按要求进行各管路泄漏检查,手动捅电磁阀,使液压油换向,对另一支路进行试漏,若泄漏迅速停泵,重新进行补焊或重新紧固。
检查人()
2.5低压试漏结束后,无泄漏,再次将先导阀顺时针调节,将压力调至5MPa,并检查,同时手动捅电磁阀使另一支路充油保压一段时间,注意检查泄漏。
无泄漏时再升压至7.5MP,同时检查处理。
最后将先导阀顺时针拧到最大至最高压力1.25倍10MP保压30分钟,同上一样检查泄漏,如不泄漏则1#泵所供油路试压试漏完毕。
检查人()
2.6将1#油压调至10MP正常试运行。
检查人()
2.7重复以上过程对其余油泵油路(包括倒换备用泵)进行试压试漏、试运行。
检查人()
2.8与微机联动检查各油泵工作是否正常。
检查人()
2.9试压试漏结束合格后,油泵开起,按正常试运行,过滤泵长期开起,注意经常检查清洗滤网。
检查人()