11支撑剂工艺技术操作规程.docx
《11支撑剂工艺技术操作规程.docx》由会员分享,可在线阅读,更多相关《11支撑剂工艺技术操作规程.docx(11页珍藏版)》请在冰豆网上搜索。
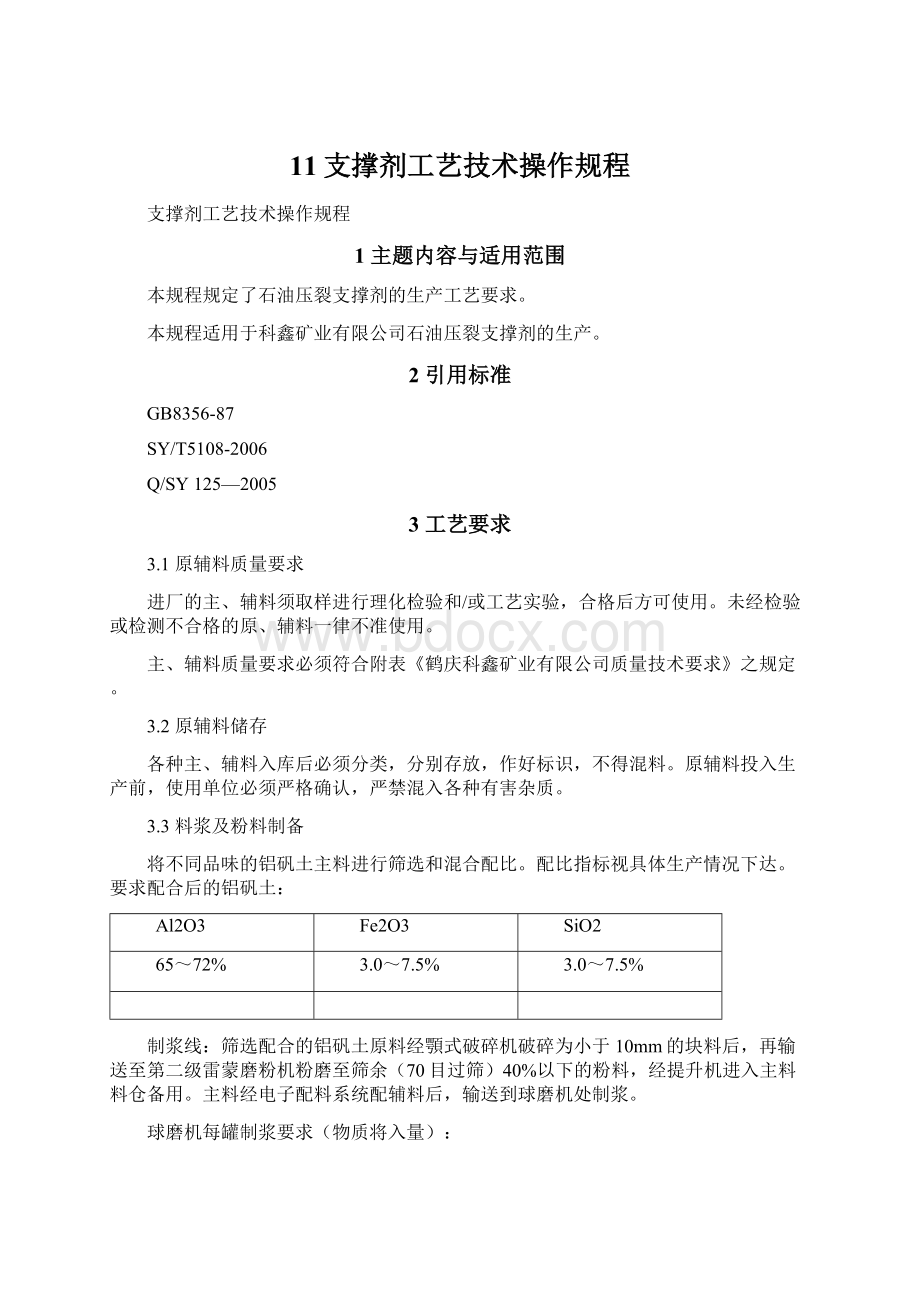
11支撑剂工艺技术操作规程
支撑剂工艺技术操作规程
1主题内容与适用范围
本规程规定了石油压裂支撑剂的生产工艺要求。
本规程适用于科鑫矿业有限公司石油压裂支撑剂的生产。
2引用标准
GB8356-87
SY/T5108-2006
Q/SY125—2005
3工艺要求
3.1原辅料质量要求
进厂的主、辅料须取样进行理化检验和/或工艺实验,合格后方可使用。
未经检验或检测不合格的原、辅料一律不准使用。
主、辅料质量要求必须符合附表《鹤庆科鑫矿业有限公司质量技术要求》之规定。
3.2原辅料储存
各种主、辅料入库后必须分类,分别存放,作好标识,不得混料。
原辅料投入生产前,使用单位必须严格确认,严禁混入各种有害杂质。
3.3料浆及粉料制备
将不同品味的铝矾土主料进行筛选和混合配比。
配比指标视具体生产情况下达。
要求配合后的铝矾土:
Al2O3
Fe2O3
SiO2
65~72%
3.0~7.5%
3.0~7.5%
制浆线:
筛选配合的铝矾土原料经顎式破碎机破碎为小于10mm的块料后,再输送至第二级雷蒙磨粉机粉磨至筛余(70目过筛)40%以下的粉料,经提升机进入主料料仓备用。
主料经电子配料系统配辅料后,输送到球磨机处制浆。
球磨机每罐制浆要求(物质将入量):
水
主料
辅料
13~14m³
20~25t
视具体情况而定(850kg以内)
每罐料浆在球磨一定时间后(20~24h),取浆检测,料浆细度(400目过筛)达到99%以上即可放浆。
制粉线:
筛选配合的铝矾土原料经顎式破碎机破碎为小于10mm的块料后,输送入主料料仓备用。
主料经超细磨粉机粉磨为细度(400目过筛)小于3%的细粉。
辅料经人工配料后输送入辅料料仓备用。
辅料经超细磨粉机粉磨为细度(400目过筛)小于3%的细粉。
主料辅料细粉经混凝土搅拌机充分搅拌混合后,输送至造粒车间备用。
3.4造粒
3.4.1制湿(干)粉
料浆经导流槽输送至泥浆池。
料浆经搅拌机充分搅拌后由泥浆泵输送至压滤机处制泥饼。
泥饼经回转窑窑尾余热干燥后备用。
制粉平台根据泥浆干燥程度不同,分别将泥饼制成干粉和湿粉。
3.4.2造粒
3.4.2.1在糖衣机里加入100~200kg左右湿粉,运转1~2分钟,待湿粉混合均匀后,开启喷雾装置,使喷出水液全部雾化(不许有水注、水滴现象)后,将喷雾口置于糖衣机口,反复喷雾加湿,当湿粉被均匀润湿开始成核后,逐步加入湿粉或干细粉,再喷雾润湿,再加细粉……如此反复至生产出符合粒径要求的颗粒(成球),最后加入少量干细粉,使颗粒滚压紧密(球压紧),直至球度、圆度、表面光洁度及密度符合附表1、2要求及以下质量技术指标。
(为提高生球的均匀性每罐坯球重量应控制在350公斤以下)
3.4.2.2均匀加水,少量反复多次加粉,以使坯球逐步均匀长大(正常使用湿粉的每罐成球时间不应低于2小时),以防止内部空洞、干包和过湿现象发生,生球水分宜控制在8~15%之间。
3.4.2.3半成品坯球体积密度(粒径在0.6~0.5mm之间,即30目到35目之间)控制在1.82~1.84cm³以上。
颗粒圆度、球度均应≥0.9,表面光滑。
3.5干燥及筛分
3.5.1半成品筛分后的筛下料返回糖衣机处理,筛上料返回粉碎机生产湿粉。
合格坯球输送入回转窑半成品仓备用。
3.6烧成
3.6.1按回转窑操作规程开启回转窑,待窑烧成制度内达到工艺要求后,开启下料除尘,开始下料(应逐步提高烧成温度达到最佳烧成状态)。
3.6.2最高烧成温度应控制在1300℃~1480℃,烧成时间控制在1.0~2.0小时,加料速度控制在2~5吨/小时,窑速控制在400~1250转/小时。
3.6.3随时注意观察回转窑烧成制度,保证“风、料、气”三平衡。
3.6.4回转窑烧出的产品每15分钟取一次样,1小时的子样混合成一个综合样送检。
3.6.5经冷却筒冷却后的产品温度应控制在100℃以内,根据现场快速观察分析结果,按照合格品与欠烧、过烧等不合格品分别入仓,严禁混料。
3.6.6烧成过程中根据实际情况适当调整烧成参数。
3.7筛分除尘
3.7.1烧成的合格产品进入1#、2#料仓,过烧、欠烧等不合格产品进入3#料仓。
3.7.2按振动筛操作规程开启振动筛,然后开启除尘器。
3.7.3烧成的合格产品经皮带机输送至振动筛,进行筛分、除尘处理。
3.7.4经筛分、除尘处理后的产品必须立即装入包装袋或进入成品料仓,以避免杂质、灰尘的污染。
4成品入库
4.1包装袋应标明产品规格、重量、执行标准、生产厂家、批号等,合格后方可使用。
4.2产品入库应按附表3(成品内控指标)验收标准执行;产品出厂应按SY/T5108-2006标准或合同规定的其它标准(如:
API标准)执行,必要时可根据客户要求进行质量检验。
产品检验合格后方可入库。
4.3产品取样、验收、入库、发货按公司相关规定执行。
成品编号与编号之间留出分隔道和运输
4.4产品出厂前按客户要求经集装袋(吨袋)包装出厂,每个集装袋必须取样检测,检测合格方可出厂。
4.5合格产品外发时遵循先生产先发货的原则,以便于产品质量跟踪。
5附则
违反本规程者按公司相关质量管理办法及技术规程处理。
附1:
(支撑剂成品内控验收指标)
1、破碎率及筛析验收指标:
6/12目(µm)
8/16目(µm)
12/18目(µm)
12/20目(µm)
16/20目(µm)
SY/T5108-2006
SY/T5108-2006
SY/T5108-2006
SY/T5108-2006
SY/T5108-2006
4750
3350
2360
2360
1700
3350
2360
1700
1700
1180
2360
2000
1400
1400
1000
2000
1700
1180
1180
850
1700
1400
1000
1000
710
1400
1180
850
850
600
1180
850
600
600
425
底盘
底盘
底盘
底盘
底盘
破碎率52MPa
破碎率52MPa
破碎率52MPa
破碎率52MPa
破碎率69MPa
≤25.0%
≤25.0%
≤25.0%
≤25.0%
≤20.0%
筛析
大于4750µm
≤0.0%
大于3350µm
≤5.0%
小于1700µm
≤1.5%
合格率
>92.0%
大于3350µm
≤0.0%
大于2360µm
≤5.0%
小于1180µm
≤1.5%
合格率
>92.0%
大于2360µm
≤0.1%
大于1700µm
≤5.0%,
小于1000µm
≤1.5%
合格率
>92.0%
大于2360µm
≤0.1%
大于1700µm
≤5.0%,
小于850µm
≤1.5%,
850~1000µm
≤9.0%,
合格率
>92.0%
大于1700µm
≤0.1%
大于1180µm
≤5.0%
小于850µm
≤1.5%
850~1000µm≤9.0%,
合格率
>92.0%
16/30目(µm)
20/40目(µm)
30/50目(µm)
40/70目(µm)
SY/T5108-2006
SY/T5108-2006
SY/T5108-2006
SY/T5108-2006
1700
1180
850
600
1180
850
600
425
1000
710
500
355
850
600
425
300
710
500
355
250
600
425
300
212
425
300
212
150
底盘
底盘
底盘
底盘
破碎率69MPa
破碎率52MPa
破碎率69MPa
破碎率86MPa
≤20.0%
≤5%
6.0%
≤10.0%
筛析
大于1700µm
≤0.1%
大于1180µm
≤5.0%
600~850µm
≤9.0%
小于600µm
≤1.5%
合格率
>92.0%
大于1180µm
≤0.1%
大于850µm
≤5.0%
600~850µm
≥65.0%
425~450µm
≤9.0%,
小于425µm
≤1.5%
合格率
>92.0%
大于850µm
≤0.1%
大于600µm
≤5.0%,
300~425µm
≤9.0%,
小于300µm
≤1.5%
合格率
>92.0%
大于600µm
≤0.1%
大于425µm
≤5.0%
212~300µm≤9.0%
小于212µm
≤1.5%
合格率
>92.0%
备注:
客户有特殊要求以合同指标为准。
2、圆度与球度
10/14目、12/18目、12/20目、16/20目、16/30目、20/40目人造陶粒的球度、圆度应不小于0.90。
30/50目、40/70目人造陶粒的球度、圆度应不小于0.85
3、产品浊度(FTU)验收指标:
初检按照签定合同浊度指标要求减10FTU进行验收,复检与出厂检验按合同指标执行;合同未规定浊度指标则初检按小于等于70FTU进行验收,初检浊度指标在70FTU~80FTU之间产品量小于等于20%本批总量,且其余指标均合格者,可一并按合格品验收;复检与出厂检验按小于等于80FTU进行验收。
4、酸溶解度
酸溶解度指标应按照60吨每批次进行检测。
各种粒径规格支撑剂允许的酸溶解度值见下表。
支撑剂酸溶解度
支撑剂粒径规范
μm
酸溶解度的最大允许值
%
3350~1700,2360~1180,1700~1000,
1180~850,1700~850,1180~600,
850~425
≤5
600~300
≤6
425~250,425~212,212~106
≤7
5、视密度
视密度指标初检与出厂检验应按照60吨每批次进行检测。
6、注:
主要生产检测仪器设备的控制
(1)产筛分产品用筛网:
符合GB5330—85标准。
(2)检验试验筛:
按照GB/T6003.1—1997(符合国际标准ISO3310/1—1990)标准配置。
(3)执行标准:
按行业标准SY/T5108—1997、或API标准、或客户要求执行。
附2:
鹤庆县科鑫矿业有限公司
质量技术要求
一、矿石质量要求
1、采矿队必须科学采矿,保证矿石不被污染。
2、采出的矿石必须人工分级选矿。
装车运输时必须分矿石级别装车、分类(分面矿和块矿)装车。
3、矿石运达公司矿场时,必须分类卸车、分级卸车,便于取样化验。
4、若运往场地矿石杂质多、质量差,公司现场人员应和采矿队现场管理人员一道公正扣除杂质。
5、化验人员应按时取样,分矿石卸放类别取样,分矿石类别做样,取样时每天取了几个样,现场管理人员要清楚明白并认可。
按规定及时向管理人员反馈化验结果,反对将不同类别矿石混在一起取综合样。
如果所取样中有废矿,公司现场管理人员应和采矿队现场管理人员同时在相应矿石磅单上签字确实。
6、矿石质量指标与参数按《采矿协议》标准执行。
7、矿石分级标准:
级别项目
Al2O3
Fe2O3
SiO2
一级矿
>76%
<2%
<2%
二级矿
>68%
<6%
<3.5%
三级矿
>60%
<10%
<3.5%
四级矿
>60%
<2%
<10%
Al2O3含量小于60%的视为不合格品,不予验收。
8、矿石搭配要求。
将不同品味(级别)的铝矾土主料进行筛选和混合配比。
配比指标视具体生产情况下达。
要求配合后的铝矾土:
Al2O3
Fe2O3
SiO2
65~72%
3.0~7.5%
3.0~7.5%
二、制浆工序/制粉工序质量技术要求
1粉磨工序
1.1加工要求:
1.1.1原料经顎式破碎机粉碎,粒度0~10mm范围,≥95%。
1.1.2辅料库提供配好的辅料,用皮带输送机输送至微粉磨机磨成细粉备用。
1.1.3主料经过顎式破碎机破碎后输送至微粉磨机磨成细粉备用。
1.1.4将主料与辅料按一定配比加入混凝土搅拌机充分混合均匀(搅拌时间不少于15分钟)后,运至造粒工段粉料仓备用。
1.1.5调整好进料量,要求微粉磨机加工粉细度达到400目过筛率≥97%
2制浆工序
1.1加工要求
1.1.1原料经顎式破碎机粉碎,粒度0~10mm范围,≥95%
1.1.2主料经过顎式破碎机破碎后输送至微粉磨机磨成细粉备用。
要求微粉磨机加工粉细度达到400目过筛率≥97%
1.1.3主料、辅料经过电子配料系统按要求配合后加入球磨机制浆。
要求辅料配比准确度为100%
1.1.4料浆的化学成分要求:
Al2O3
Fe2O3
SiO2
Al2O3+Fe2O3+SiO2
65~66%
6.8~7.5%
4.5%<
>77%
三、造粒质量要求
1、制干(湿)粉
1.1人工选取不同干湿程度的泥饼分别经破碎机制成干粉和湿粉。
1.2湿粉细度要求:
不得有未粉碎的颗粒或泥块、泥团或其他杂物,用检测筛顶筛检测筛余<3%。
2、造粒
2.1颗粒圆度、球度>0.9,表面光滑,无粉尘;
2.2半成品坯球体积密度(粒径在0.6~0.5mm之间,即30目到35目之间)控制在1.82~1.84cm³以上2.3使用湿粉造粒时间不少于1.5小时,使用筛下料造粒时间不少于1小时。
四、半成品筛分
1.以30/50目为标准时
1.1合格品:
检测筛组合:
20/35要求:
+35>95%
1.2筛上料:
检测筛组合:
20/底盘要求:
底盘<5%
1.3筛下料:
检测筛组合:
35/底盘要求:
35目以上<5%
2.以20/40目为标准时
2.1合格品:
检测筛组合:
18/30要求:
+30>95%
2.2筛上料:
检测筛组合:
18/底盘要求:
底盘<5%
2.3筛下料:
检测筛组合:
25/底盘要求:
25目以上<2%
3.颗粒圆度、球度均应≥0.9,表面光滑,粉尘。
五、烧成工序
1.加工要求:
1.1坯球经除尘后方可入窑煅烧,入窑量由振动给料机控制。
1.2烧成温度:
(高温区)1250~1400℃(实际温度以烧结工艺单为准)。
1.3烧成时间控制在1.02.5小时。
1.4进料速度:
2~5吨/小时。
1.5回转窑主传电机转速:
100~300转/分钟(按实际情况进行调整)
1.6一次风流量:
2400~4000m³/h(按实际情况进行调整)
1.7煤气流量≤2600m³/h,
1.8给料速度≤5吨/小时
1.9根据生产实际调整适宜的烧成温度(±5℃)
1.10冷却筒出来的产品温度小于100℃
1.11烘窑温度达到1000℃以上才能投料
1.12集尘室温度≤300℃
1.13各班的操作方法必须一致。
先按2.5吨/小时投料,待烧成稳定后才能逐步增加。
(给料速度)每次只能增加500kg/小时。
给料速度增加后,必须稳定8小时,然后才能继续增加给料速度,直至5吨/小时。
2检测指标:
(以30/50目为指标)
内容
单位
指标要求
圆度
1.0max
≥0.90
球度
1.0max
≥0.90
体积密度
g/cm3
1.70~1.85
视密度
g/cm3
3.0~3.35
浊度
FTU
≤70
酸溶解度
wt%
≤5.0
69MPa抗破碎率
wt%
≤6.0
六、筛分、除尘、包装工序
1加工要求:
1.1筛网规格:
根据实际生产要求而定。
1.2筛分要求:
筛分后产品的筛析达标,不能有杂质、灰尘进入。
2.产品入库检测
2.1严格按支撑剂成品内控验收指标内容要求执行。
2.2检测合格入库产品必须按规格、密度等级要求堆码,堆码整齐,每班筛分的各种规格的产品各为一个小编号。
编号与编号之间留出分隔道和运输通道。