心轴配合件的加工工艺设计.docx
《心轴配合件的加工工艺设计.docx》由会员分享,可在线阅读,更多相关《心轴配合件的加工工艺设计.docx(52页珍藏版)》请在冰豆网上搜索。
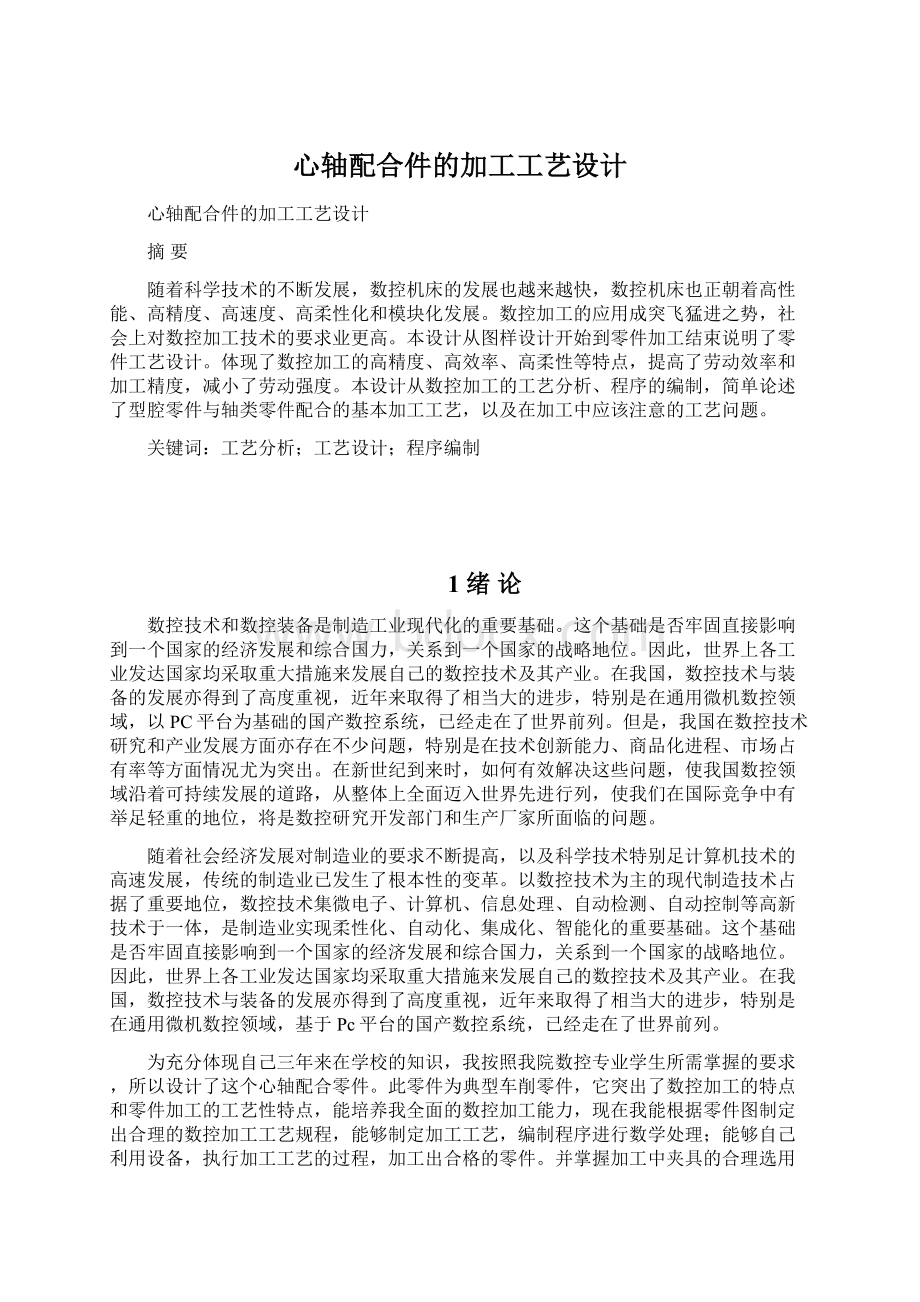
心轴配合件的加工工艺设计
心轴配合件的加工工艺设计
摘要
随着科学技术的不断发展,数控机床的发展也越来越快,数控机床也正朝着高性能、高精度、高速度、高柔性化和模块化发展。
数控加工的应用成突飞猛进之势,社会上对数控加工技术的要求业更高。
本设计从图样设计开始到零件加工结束说明了零件工艺设计。
体现了数控加工的高精度、高效率、高柔性等特点,提高了劳动效率和加工精度,减小了劳动强度。
本设计从数控加工的工艺分析、程序的编制,简单论述了型腔零件与轴类零件配合的基本加工工艺,以及在加工中应该注意的工艺问题。
关键词:
工艺分析;工艺设计;程序编制
1绪论
数控技术和数控装备是制造工业现代化的重要基础。
这个基础是否牢固直接影响到一个国家的经济发展和综合国力,关系到一个国家的战略地位。
因此,世界上各工业发达国家均采取重大措施来发展自己的数控技术及其产业。
在我国,数控技术与装备的发展亦得到了高度重视,近年来取得了相当大的进步,特别是在通用微机数控领域,以PC平台为基础的国产数控系统,已经走在了世界前列。
但是,我国在数控技术研究和产业发展方面亦存在不少问题,特别是在技术创新能力、商品化进程、市场占有率等方面情况尤为突出。
在新世纪到来时,如何有效解决这些问题,使我国数控领域沿着可持续发展的道路,从整体上全面迈入世界先进行列,使我们在国际竞争中有举足轻重的地位,将是数控研究开发部门和生产厂家所面临的问题。
随着社会经济发展对制造业的要求不断提高,以及科学技术特别足计算机技术的高速发展,传统的制造业已发生了根本性的变革。
以数控技术为主的现代制造技术占据了重要地位,数控技术集微电子、计算机、信息处理、自动检测、自动控制等高新技术于一体,是制造业实现柔性化、自动化、集成化、智能化的重要基础。
这个基础是否牢固直接影响到一个国家的经济发展和综合国力,关系到一个国家的战略地位。
因此,世界上各工业发达国家均采取重大措施来发展自己的数控技术及其产业。
在我国,数控技术与装备的发展亦得到了高度重视,近年来取得了相当大的进步,特别是在通用微机数控领域,基于Pc平台的国产数控系统,已经走在了世界前列。
为充分体现自己三年来在学校的知识,我按照我院数控专业学生所需掌握的要求,所以设计了这个心轴配合零件。
此零件为典型车削零件,它突出了数控加工的特点和零件加工的工艺性特点,能培养我全面的数控加工能力,现在我能根据零件图制定出合理的数控加工工艺规程,能够制定加工工艺,编制程序进行数学处理;能够自己利用设备,执行加工工艺的过程,加工出合格的零件。
并掌握加工中夹具的合理选用,了解刀具的材料、特点、以及如何选用刀具等一系列问题,这次毕业设计有利于培养我们各个方面的能力。
2机床的选择
根据心轴、左配合件、右配合件的直径尺寸、加工精度要求及生产类型不同,应采用不同的机床进行加工,此配合零件形状较复杂,又是轴套类零件,根据学校的实际情况考虑,我们学院数控基地有数控加工中心、数控铣床、数控车床、电火花切割。
根据加工的需要因此都选择用数控车床加工。
如图6-1所示。
图2-1C26136HK车床
3零件的加工工艺设计
3.1零件图的分析
心轴配合件有三部分组成。
其中心轴如图3-1所示,心轴部分由圆锥面、圆弧面、阶梯轴、螺纹组成。
圆锥轴套如图3-2所示由内圆弧、内圆锥面组成。
圆弧轴套如图3-3由通孔、外圆弧、内圆弧面、内螺纹、倒角组成。
三部分在数车加工中有一定的代表性。
综合考察了我运用大学所学知识解决实际问题的能力。
图3-1心轴
图3-2圆锥轴套
图3-3圆弧轴套
3.2零件加工工艺性分析
3.2.1零件图尺寸的标注
为使零件图样符合数控加工的要求,图样的尺寸标注应符合数控加工的特点。
对数控加工来说,零件图上应以同一基准引注尺寸或直接给出坐标尺寸。
保持设计基准、工艺基准、测量基准与编程原点设置一致。
对于该配合件,所有标注如图3-1、3-2、3-3所示,尺寸完整,便于加工。
3.2.2零件的结构分析
制定工艺规程时,首先应分析零件图及该零件所在部件的装配图。
通过分析零件图样和部件的装配图,明确被加工零件在产品中的位置与作用;找出该零件上有多少加工表面;找出该零件主要的技术要求和加工中的关键要求,了解各项公差与技术要求指定的依据,在编制工艺过程中,有针对性的解决这些问题。
在圆弧的加工中除了一处用了半径为3mm的圆弧,其他的地方圆弧尺寸都是统一的,减少换刀次数。
便于数控编程,避免频繁换刀而增加的零件加工面上的接刀痕迹,降低表面质量。
由于两配合件都是通孔,为了减少加工时间,需要在车削加工以前进行钻孔、镗孔加工。
3.2.3表面质量与精度的分析
该配合件三部分的加工精度等级都为IT14级,外轮廓四周、内孔及螺纹要求表面粗糙度为Ra1.6
只有心轴的键槽处为Ra3.2
要求都很高,粗糙度不容易保证,而且公差要求较高,加工精度和表面质量要求较高,这就是加工该零件的难度。
精度要求是机械加工中考验操作者技术水平的重要指标。
3.3毛坯选择
毛坯的选择主要是确定毛坯的种类、制造方法和制造精度等级。
毛坯的形状、尺寸越接近成品,切削余量就越小,但从加工成本考虑,切削余量越小,制造毛坯和余量加工的成本就越高。
在选择毛坯时应从制造毛坯和余量机械加工两方面来考虑。
该配合件由三部分组成。
三部分所需材料都一样。
要考虑毛坯的种类、形状与尺寸、现有的生产条件。
毛坯的种类有铸件、锻件、压制件、冲压件、焊接件、型材和板材等。
选择原则有:
(1)根据图纸规定的材料及机械性能选择毛坯;
(2)根据零件的功能选择毛坯;
(3)根据生产类型选择毛坯;
(4)根据具体生产条件选择毛坯。
轴类零件的材料一般为碳素结构钢和合金结构钢两类,这次毕业设计毛坯选择根据以上四条原则本次选择碳素结构钢类,其中以中碳钢45钢应用最多,该零件材料为45钢,轴类零件的常用毛坯是型材圆棒料和锻件,直径相差不大的阶台轴常采用热轧或冷拉的圆棒料。
从经济考虑,45钢的取材容易,价格适中,对于学生是比较理想的加工原材料。
平时上实训课时经常接触,对于45钢的性能比较了解。
操作起来容易掌控。
根据零件图可知此阶梯轴零件各台阶直径相差不大,因此选择圆棒料。
由于毛坯大小主要考虑加工余量、加工装夹方面情况来选择,加工余量根据机械加工手册计算机械加工余量,按零件图轮廓尺寸计算,心轴零件图最大尺寸直径φ58mm,长度为120mm,圆锥轴套零件图最大尺寸直径φ58mm,长度45mm,圆弧轴套零件图最大尺寸直径φ58mm,长度35mm。
考虑到粗加工和精加工的切削量。
粗加工时切削量较大,而且零件的加工精度要求较高,因此粗加工需要循环加工两次,每次粗加工时背吃刀量选择2mm,精加工时背吃刀量为0.5mm。
所以心轴毛坯大小定为直径φ65mm,长度为150mm的棒料。
圆锥轴套件毛坯大小定为直径φ65mm,长度80mm的棒料。
圆弧轴套件毛坯大小定为直径φ65mm,长度65mm的棒料。
本次设计心轴配合件分为三部分,毛坯选择时考虑到配合度,因此毛坯直径都是一样大。
3.4定位基准的选择
3.4.1选择定位基准的原则
选择定位基准主要应从保证工件的位置精度和装夹方便这两方面来考虑。
因此基准的选择应从精基准到粗基准。
精基准的选择原则有基准重合、基准统一、自为基准、互为基准、精准可靠,便于装夹。
粗基准的选择原则有非加工表面原则、加工余量最小原则、重要表面原则、不重复使用原则、便于工件装夹原则。
本次毕业设计所做的心轴配合件的三部分基准选择时,精基准的选择原则是基准重合、自为基准。
粗基准的选择原则是加工余量最小原则、便于工件装夹原则。
所选原则都是从零件加工的实际需要出发作出的选择。
3.4.2定位基准的选择
选择定位基准时,保证工件精度要求,分析定位基准选择的顺序应从精基准到粗基准。
参照以上原则,经综合分析:
加工心轴配合件的三部分时粗基准以左端面为准,加工外圆柱面及外圆锥面时,以左端面及轴心线作为精基准,在加工内螺纹及内镗孔加工时,以外圆作为精基准。
心轴配合件的三部分加工时选择定位基准的原则都一样因此在装夹毛坯时都是以三爪自定心卡盘为定位基准。
心轴配合件三部分定位基准简图如图3-4所示。
图3-4心轴配合件定位基准的选择
3.5加工工艺路线设计
拟定加工工艺路线是制定加工工艺过程中的关键环节。
3.5.1心轴的加工方案
根据零件图综合分析,采用先粗后精,程序段最少,走到路线最短的加工要求,制定以下加工方案。
先加工心轴左端再加工右端
心轴左端:
车端面→倒角C1→粗车Φ24→粗车Φ38→粗车圆锥面Φ40→粗车Φ52→倒角C1→粗车Φ54→精车Φ24→精车Φ38→精车圆锥面Φ40→精车Φ54→切槽2X2mm→切槽5X7mm
心轴右端:
车端面→倒角C1→粗车Φ30→粗车Φ34→粗车R3→粗车Φ40→粗车Φ54→粗车R26→精车Φ30→精车Φ34→精车R3→精车Φ40→精车Φ54→精车R26→切槽8X2mm→粗车螺纹M30→精车螺纹M30
3.5.2圆锥轴套加工方案
根据零件图综合分析,采用先粗后精,程序段最少,走到路线最短的加工要求,制定以下加工方案。
装夹左端外圆→车端面→Φ3中心钻打中心孔→Φ20麻花钻钻孔→Φ20镗刀粗镗内圆锥面Φ40→粗镗内孔Φ24→精镗内圆锥面Φ40→精镗内孔Φ24→粗车Φ58→粗车R2→粗车Φ46→粗车Φ54→粗车R2→粗车Φ58→精车Φ58→精车R2→精车Φ46→精车Φ54→精车R2→精车Φ58→切断→装夹铜皮包裹的已加工面→车左端面→倒角C1→粗镗内孔Φ36→精镗内孔Φ36
3.5.3圆弧轴套加工方案
根据零件图综合分析,采用先粗后精,程序段最少,走到路线最短的加工要求,制定以下加工方案。
装夹左端外圆→车端面→Φ3中心钻打中心孔→Φ25麻花钻钻孔→Φ20镗刀粗镗内孔Φ27→精镗内孔Φ27→倒角C2→粗车内螺纹M30→精车内螺纹M30→粗车Φ46→粗车R3→粗车Φ58→精车Φ46→精车R3→精车Φ58→切断→夹持右端外圆→车左端面→粗车R2→粗车R3→粗车Φ30→倒角C1.5→精车R2→精车R3→精车Φ30
3.6夹具的确定
三部分零件图尺寸要求所需的精度适中,普通夹具可以满足需要。
所加工的零件为轴套类零件,所选择的材料为棒料。
因此在加工此零件时,以三爪自定心卡盘和尾座顶尖这两种车床中最常用的夹具来装夹毛坯,同时完成粗精加工。
本次毕业设计所选夹具简图如图3-4,尾座如图3-5所示。
图3-5三爪卡盘简图
3.7刀具的选择
刀具材料可以决定一个零件加工的质量、精度和加工效率。
常用的刀具材料如下:
表3-1刀具材料的特征和用途
材料
主要特征
用途
优点
高速钢
比工具钢硬
低速或不连续切削
刀具寿命较长,加工的表面较平滑
高性9能高速钢
强韧、抗边缘磨损性强
可粗切或精切几乎任何材料,包括铁、钢、不锈钢、高温合金和非金属材料
切削速度比高速钢高,强度和韧性较粉末冶金高速钢高
粉末冶金高速钢
良好的抗热性和抗碎片磨损
切削钢、高温合金、不锈钢、铝、碳钢及其他不易加工的材料
切削速度可比高性能高速钢高15%
硬质合金
耐磨损、耐热
可锻铸铁、碳钢、合金钢、不锈钢的精加工
寿命比一般工具钢高10~20倍
陶瓷
高硬度、耐热、冲击性好
高速粗加工,铸铁和钢的精加工
可用于高速加工
心轴配合件运用于汽车的装配中,材料为45钢,根据表6-1,我选取硬质合金作为刀具材料。
(1)圆弧轴套的刀具选择:
①粗车外圆面时,选用90o外圆车刀,粗车时副偏角可选稍微大些,但又不能与工件轮廓超干涉,因此选择35o;
②精车外圆面时,选用93o外圆车刀,精车时副偏角可选稍微小些,因此选择30o;
③Φ3mm的中心钻;
④钻通孔,用Φ20的钻头;
⑤粗精镗内圆柱面是用Φ20镗刀;
⑥60o的螺纹车刀;
⑦9o内圆车刀;
⑧3mm的切断刀。
(2)心轴部分的刀具选择:
①粗车外圆面时,选用90o外圆车刀,粗车时副偏角可选稍微大些,但又不能与工件轮廓超干涉,因此选择35o;
②精车外圆面时,选用93o外圆车刀,精车时副偏角可选稍微小些,因此选择30o;
③5mm宽的切槽刀;
④60o的螺纹车刀。
(3)圆锥轴套的刀具选择:
①粗车外圆面时,选用90o外圆车刀,粗车时副偏角可选稍微大些,但又不能与工件轮廓超干涉,因此选择35o;
②精车外圆面时,选用93o外圆车刀,精车时副偏角可选稍微小些,因此选择30o;
③选择φ3mm中心钻,钻中心孔以利于钻削底孔时刀具找正;
④φ20mm的标准麻花钻头,钻内孔底孔;
⑤粗、精镗内孔选用φ20mm内孔镗刀;
⑥5mm宽的切断刀。
3.8切削用量的选择
正确的选择切削用量,对保证产品质量,提高效率,降低加工成本具有重要作用。
切削用量的选择主要是根据工件材料、加工精度和表面粗糙度的要求进行,同时还要兼顾刀具的耐用度、工艺系统的刚度和机床功率等条件。
切削用量是表示机床主运动和进给运动大小的重要参数,包括切削速度、进给量和背吃刀量。
3.8.1圆弧轴套切削用量的确定
本次加工心轴配合件中的三部分要分别计算,根据三原则合理选择切削用量
(1)背吃刀量的确定:
背吃刀量
:
又称切削深度,一般指工件已加工表面和待加工表面间的垂直距离,单位为mm,主要根据加工余量和工艺系统的刚度确定。
1粗加工时,在留下精加工、半精加工的余量后,尽可能一次走刀将剩下的余量切除;若余量过大不能以此切除,也应该先多后少的不等余量法加工;当冲击载荷或工艺系统刚度较差,可适当降低
,使切削力减小。
②精加工时,背吃刀量应根据粗加工留下的余量确定,采用逐渐降低
的方法,逐步提高加工精度和表面质量。
一般精加工时,取
=0.05~0.8mm;半精加工时,取
=1.0~3.0mm。
根据以上内容分析得,在车外轮廓时,粗加工时背吃刀量选择2mm,半精加工时背
吃刀量选择1mm,精加工时背吃刀量选择0.5mm;在加工内轮廓时,粗加工时背吃刀量选择0.8mm,半精加工时背吃刀量选择0.5mm,精加工时背吃刀量选择0.25mm;在加工内螺纹时,背吃刀量选择按表3-2进行选择。
表3-2常用螺纹切削的进给次数与背吃刀量
公制螺纹
螺距
1.0
1.5
2.0
2.5
牙深
0.649
0.947
1.299
1.624
背吃刀量及进给次数
1次
0.7
0.8
0.9
1.0
2次
0.4
0.6
0.6
0.7
3次
0.2
0.4
0.6
0.6
4次
0.16
0.4
0.4
5次
0.1
0.4
6次
0.15
(2)计算主轴转速
①车外圆时的主轴转速
主轴转速是指每分钟主轴转的转数,车外圆时主轴转速应根据零件上被加工部位的直径,并按零件和刀具材料及性质等条件所允许的切削速度来确定。
主轴转速的计算公式是:
(式3-1)
式中:
为切削速度(m/min);
d为工件待加工表面或刀具的最大直径(mm)。
切削速度
:
在进行切削加工时,刀具切削刃的某一点相对于待加工面在主运动方向上的瞬时速度,也可以理解为是主运动的线速度,单位为m/min。
切削速度是切削用量中对切削加工影响最大的因素。
切削速度的确定直接影响工件表面质量的好坏,要加工出符合要求的零件,在选择切削速度上就要考虑多方面的因素。
在大学的学习课程中对于机械加工工艺的重视程度非常高,而其中的切削三要素又是重中之重。
在考量切削速度上,我翻阅了切削用量简明手册,归纳总结平时在实训课上所学到的知识和一些经历,根据零件图的技术要求要综合考虑切削条件和要求,选择适当的切削速度。
以顺利完成这次零件加工的心轴配合件。
这次零件加工为了让每一步的加工都有数据支持,我特意从切削用量简明手册中摘录了一些有用的切削数据绘制成表格以便于自己使用。
下面的表格就是常见的切削速度列表如下,见表3-3所示。
表3-3常用切削速度单位:
m/min
材料
铸铁
钢及其合金
铝及其合金
铜及其合金
高速钢
硬质合金
高速钢
硬质合金
高速钢
硬质合金
高速钢
硬质合金
车削
—
60~100
15~25
60~110
15~200
300~450
60~10
150~200
扩
通孔
10~15
30~40
10~20
35~60
30~40
—
30~40
—
沉孔
8~12
25~30
8~11
30~50
20~30
—
20~30
—
镗
粗镗
20~25
35~50
15~30
50~70
80~150
100~200
80~150
100~200
精镗
30~40
60~80
40~50
90~120
15~300
200~400
150~200
200~300
铣
粗铣
10~20
40~60
15~25
50~80
15~200
350~500
100~150
300~400
精铣
20~30
60~120
20~40
80~150
20~300
500~800
150~200
400~500
铰孔
6~10
30~50
6~20
20~50
50~75
200~250
20~50
60~100
螺纹
2.5~5
—
1.5~5
—
5~15
—
5~15
—
钻孔
15~25
—
10~20
—
50~70
—
20~50
—
②车外轮廓及内圆面的主轴转速:
根据表3-3得,车外轮廓时,选粗车切削速度
=90m/min,精车切削速度
=100m/min。
利用公式(3-1)计算主轴转速(粗车工件直径D=50mm,精车工件直径取平均值)。
粗车:
=
=373.248(r/min)≈400(r/min)
精车:
=
=606.157(r/min)≈600(r/min)
由于车内孔比车外圆困难,内孔车刀刀杆细而长,刚性差,车削时弹性变形大,而且排削困难、又不便观察,因此主轴转速应比车外圆时稍慢,粗车内孔时的主轴转速定为400r/min,精车内孔时的主轴转速定为600r/min。
③车螺纹时的主轴转速:
在车削螺纹时,车床的主轴转速将受到螺纹的螺距(或导程)大小、驱动电动机的升降频特性及螺纹插补运算速度等多种因素影响,大多数普通车床数控系统车螺纹时的主轴转速为:
(式3-2)
式中:
为工件螺纹的螺距或导程;
k为保险系数,一般取80。
零件图中螺纹导程
=1.5mm,由公式(3-2)得:
因此,车削内螺纹时取主轴转速
=300r/min。
(3)计算进给速度
进给速度是指切削单位时间内工件与进给方向相对位移,单位为mm/min。
进给速度的大小直接影响表面粗糙度的值和车削效率。
主要根据零件的加工精度和表面粗糙度以及刀具、工件的材料性质参考用量手册选取。
每转进给量,进给速度的计算公式:
(式3-3)
式中:
为进给量(mm/r或mm/行程);
为主运动的转速r/min。
进给量
:
刀具在进给运动方向上相对于工件的位移量,可用刀具或工件每转或每行程的位移量来描述和度量,单位为mm/r或mm/行程。
进给量的选择可根据以下方法:
1粗加工时,
主要受刀杆、刀片、机床、工件等的强度和刚度所承受的切削力限制,一般根据刚度来选择。
工艺系统刚度好时,可用大些的
;反之,适当降低
,粗车时一般选取为(0.3~0.8)mm/r。
②半精加工、精加工时,
根据工件的
要求选择。
要求小的,取较小的
,因此,在精车、半精车时一般选取(0.1~0.3)mm/r。
根据以上原则,选择粗车外圆时每转进给量为0.5mm/r,精车时每转进给量0.2mm/r,粗车内圆时每转进给量为0.3mm/r,精车时每转进给量为0.15mm/r,根据公式(3-3)得:
加工外圆时:
粗车:
=0.5×600=300(mm/min)
精车:
=0.2×1000=200(mm/min)
加工内圆时:
粗车:
=0.3×400=120(mm/min)
精车:
=0.15×600=90(mm/min)
3.8.2心轴切削用量的确定
(1)背吃刀量的确定
背吃刀量的选择要根据机床、工件和刀具的刚度来决定,在刚度允许的情况下,就尽可能使背吃刀量等于工件的加工余量。
这样可以减少走刀次数,提高生产效率。
因此轮廓粗车循环时选背吃刀量为2mm,精车循环时选背吃刀量为0.5mm。
(2)主轴转速的计算
车直线、圆弧及螺纹时的切削速度可通过查表3-3获得,粗车时的切削速度
=90m/min,精车的切削速度
=100m/min,根据公式(3-1)得:
粗车:
=
=573.248(r/min)≈600(r/min)
精车:
=
=806.157(r/min)≈800(r/min)
车螺纹时的主轴转速,根据公式(3-2)得:
因为是车削外螺纹,转速可稍微高一些,选择车螺纹时的主轴转速为
=400r/min。
(3)进给速度的计算
先取进给量,然后用公式(3-3)计算进给速度。
粗车时,选取进给量
=0.4mm/r,;精车时,选取进给量
=0.15mm/r。
粗车:
=0.4×600=24(mm/min)
精车:
=0.15×800=120(mm/min)
3.8.3圆弧轴套加工方案
(1)背吃刀量的选择:
粗车外轮廓时
2mm,精车外轮廓时
0.5mm;粗车内孔时的
0.8mm,精车内孔时
0.25。
(2)主轴转速的确定:
粗车外轮廓时,切削速度取90mm/r;
精车外轮廓时,切削速度为100mm/r;
再根据公式(7-1),计算得:
粗车:
=
=573.248(r/min)≈600(r/min)
精车:
=
=806.157(r/min)≈800(r/min)
由于车内孔比车外圆困难,内孔车刀刀杆细而长,而且排削困难、又不便观察,因此主轴转速应比车外圆时稍慢,粗车内孔时的主轴转速定为400r/min,精车内孔时的主轴转速定为600r/min。
(3)进给速度的确定:
进给速度的确定根据公式(7-3)来计算,首先确定每转进给量,粗车时一般选取为(0.3~0.8)mm/r,精车时一般取(0.1~0.3)mm/r,精车时每转进给量0.2mm/r,粗车内圆时每转进给量为0.3mm/r,精车时每转进给量为0.15mm/r,根据公式(7-3)
加工外圆时:
粗车:
=0.5×600=300(mm/min)
精车:
=0.2×1000=200(mm/min)
加工内圆时:
粗车:
=0.3×400=120(mm/min)
精车:
=0.15×600=90(mm/min)
以上就是心轴配合件的切削用量的选择,通过查表和计算,得出了以上所有与加工有关的数据。
当进行数控编程时编程人员必须确定每道工序的切削用量并以指令的形式输入程序中。
切削用量包括主轴转速背吃刀量及进给速度等。
对于不同的加工方法需要选用不同的切削用量。
切削用量的选择原则是:
保证零件加工质量和表面粗糙度充分发挥具切削性能保证合理的刀具切削性能和耐用度,并充分发挥机床的性能最大限度地提高生产率减低成本。
综合考虑各方面的因素,考虑