外文文献翻译.docx
《外文文献翻译.docx》由会员分享,可在线阅读,更多相关《外文文献翻译.docx(8页珍藏版)》请在冰豆网上搜索。
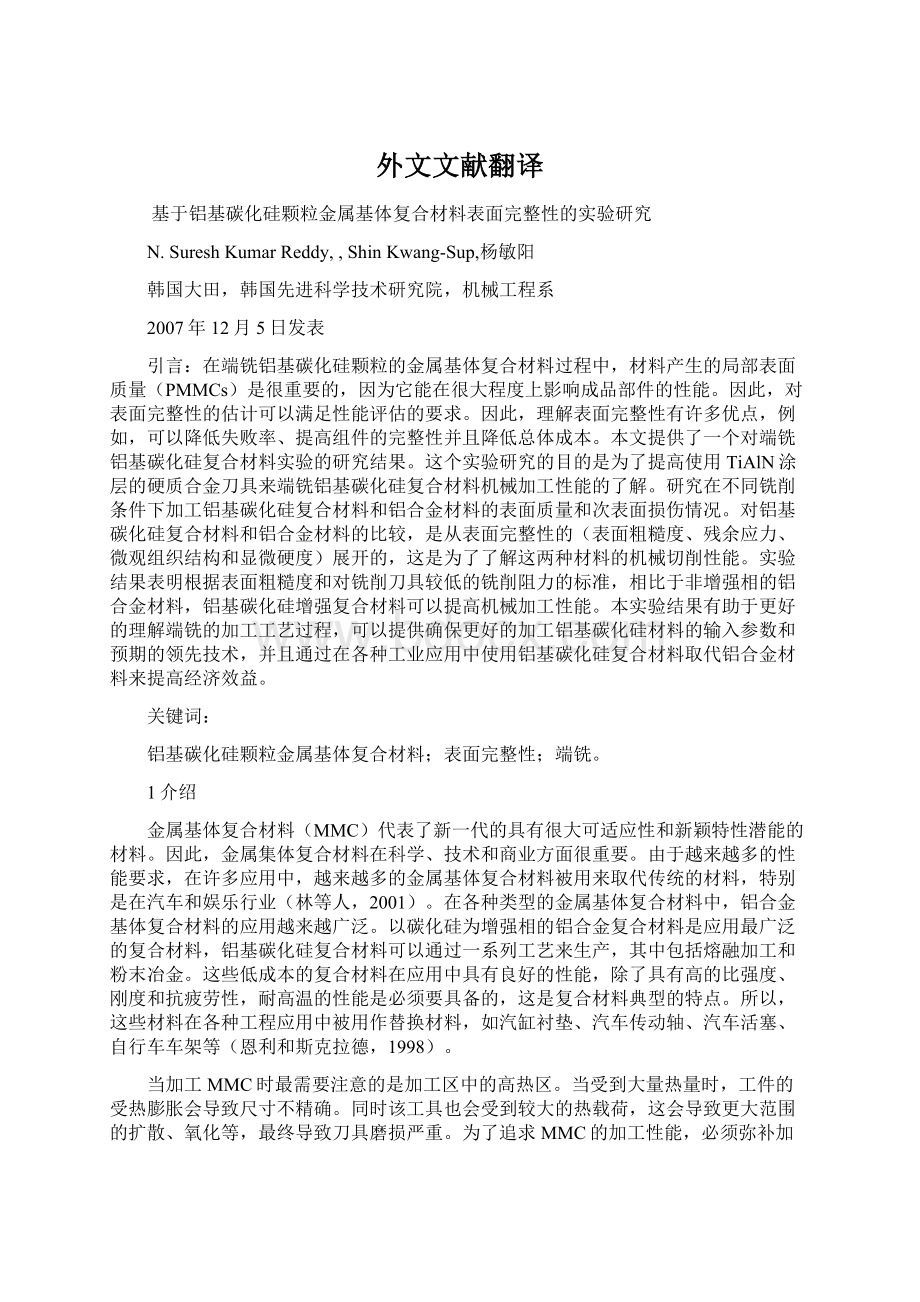
外文文献翻译
基于铝基碳化硅颗粒金属基体复合材料表面完整性的实验研究
N.SureshKumarReddy,,ShinKwang-Sup,杨敏阳
韩国大田,韩国先进科学技术研究院,机械工程系
2007年12月5日发表
引言:
在端铣铝基碳化硅颗粒的金属基体复合材料过程中,材料产生的局部表面质量(PMMCs)是很重要的,因为它能在很大程度上影响成品部件的性能。
因此,对表面完整性的估计可以满足性能评估的要求。
因此,理解表面完整性有许多优点,例如,可以降低失败率、提高组件的完整性并且降低总体成本。
本文提供了一个对端铣铝基碳化硅复合材料实验的研究结果。
这个实验研究的目的是为了提高使用TiAlN涂层的硬质合金刀具来端铣铝基碳化硅复合材料机械加工性能的了解。
研究在不同铣削条件下加工铝基碳化硅复合材料和铝合金材料的表面质量和次表面损伤情况。
对铝基碳化硅复合材料和铝合金材料的比较,是从表面完整性的(表面粗糙度、残余应力、微观组织结构和显微硬度)展开的,这是为了了解这两种材料的机械切削性能。
实验结果表明根据表面粗糙度和对铣削刀具较低的铣削阻力的标准,相比于非增强相的铝合金材料,铝基碳化硅增强复合材料可以提高机械加工性能。
本实验结果有助于更好的理解端铣的加工工艺过程,可以提供确保更好的加工铝基碳化硅材料的输入参数和预期的领先技术,并且通过在各种工业应用中使用铝基碳化硅复合材料取代铝合金材料来提高经济效益。
关键词:
铝基碳化硅颗粒金属基体复合材料;表面完整性;端铣。
1介绍
金属基体复合材料(MMC)代表了新一代的具有很大可适应性和新颖特性潜能的材料。
因此,金属集体复合材料在科学、技术和商业方面很重要。
由于越来越多的性能要求,在许多应用中,越来越多的金属基体复合材料被用来取代传统的材料,特别是在汽车和娱乐行业(林等人,2001)。
在各种类型的金属基体复合材料中,铝合金基体复合材料的应用越来越广泛。
以碳化硅为增强相的铝合金复合材料是应用最广泛的复合材料,铝基碳化硅复合材料可以通过一系列工艺来生产,其中包括熔融加工和粉末冶金。
这些低成本的复合材料在应用中具有良好的性能,除了具有高的比强度、刚度和抗疲劳性,耐高温的性能是必须要具备的,这是复合材料典型的特点。
所以,这些材料在各种工程应用中被用作替换材料,如汽缸衬垫、汽车传动轴、汽车活塞、自行车车架等(恩利和斯克拉德,1998)。
当加工MMC时最需要注意的是加工区中的高热区。
当受到大量热量时,工件的受热膨胀会导致尺寸不精确。
同时该工具也会受到较大的热载荷,这会导致更大范围的扩散、氧化等,最终导致刀具磨损严重。
为了追求MMC的加工性能,必须弥补加工过程中的缺点。
新的涂层工具具有巨大的潜力来提升这一类材料的机械可加工性。
在这个方向,氮化钛涂层铝基(TiAlN)硬质合金刀具是一个潜在的替代品。
进一步的分析表明,在PMMC表面和次表面的铣削变形的问题还没有得到解决(林等人,1998,恩利和斯克拉德,1998)。
此外,已经做了不严格的调查来找出铣削参数在加工金属基体复合材料过程中对次表面变形的影响。
这是非常重要的,因为这些因素对加工组件的性能起着重要作用。
因此,鉴于这些复合材料不断增长的工程应用需求,需要详细和系统的研究复合材料的加工特性,这些对于在实际工程应用中的快速应用是非常必要的。
这种研究将会有助于提高这些材料所要求的公差特性的有效性和经济性。
从金属切削的理论可以知道,表面完整性的研究是了解材料加工特性最有效的途径。
因此,铝基碳化硅复合材料加工特性的测量代表了加工过程分析最重要的方面之一,这种材料在未来将会得到大量应用。
因此,本次研究的目的是为了研究具有氮化钛涂层刀具端铣铝基碳化硅复合材料的可加工性。
是为了研究在不同铣削条件,铣削铝基碳化硅复合材料和铝基复合材料产生的表面质量和次表面损伤的程度。
在表面完整性(粗糙度、残余应力和硬度)的基础上,对铝基碳化硅复合材料和铝基复合复合材料的比较,是为了了解这两种材料的可加工性。
2试验方法
实验研究是通过使用铝基碳化硅复合材料展开的。
在这项研究中使用的碳化硅颗粒的化学分析结果如表一所示。
使用体积分数为20%的碳化硅颗粒来制造复合材料。
通过使用激光粒度仪的“马尔文激光粒度分析模型”来测定颗粒的粒径。
被加工的材料是颗粒大小为32微米的体积分数为20%的铝基碳化硅颗粒复合材料。
研究中使用的2024铝合金复合材料的相关化学分析如表2所示。
2.1铣削条件
铣削是一个非常复杂的切削过程,涉及切削速度、进给速度、切削深度、刀具几何形状等参数。
通过一系列实验对影响表面光洁度最大的因素进行了研究。
实验的影响因素是切削速度、进给速度和切削深度。
实验的情况如图3所示。
实验是在干燥条件下进行的。
采用高精度的数控铣刀和立式铣头来进行实验。
切削刀具是TiAlN固体涂层的直径为20毫米的硬质合金四齿端铣刀。
实验中使用了三种不同的刀具。
每个刀具都被用于8个实验,在每次实验后,都会使用光学显微镜来测量已使用的铣刀,来确定后刀面或表面的磨损程度。
在这些实验中,刀具的寿命标准是0.3毫米。
实验中分别使用了赋值和截止长度为0.8到5毫米的表面粗糙度测试仪对表面粗糙度进行了检测。
表面粗糙度是取自加工表面四个位置(分别成90°),在加工表面每处重复取值两次的平均值。
通过光学显微镜对垂直于工件表面的显微硬度进行分析,实验中使用了负载为25克的维氏显微硬度计。
在本实验中没能换个,由于没有成文的X射线衍射(XRD)残余应力的测量标准,对使用了sin2ψ技术X射线处理的表面进行残余应力的测量。
选择铁α{211}反射和CrKα辐射进行测试,其中技术参数渗透率为5微米、峰值范围是2θ为140–170°。
3结果与讨论
表面完整性是影响工件加工质量的重要因素之一,因为表面完整性会影响工件的功能特性,例如相容性、抗疲劳性和表面摩擦。
这也是评估材料可加工性的标准之一。
因此,表面完整性也可以成为一个重要的性能测试指标。
因此,对于为了评估端铣的效果,来测试表面完整性,这是很必要的。
在这个背景下,可以通过进行实验,来测量切削速度、进给量和背吃刀量的影响。
在实验之前和之后刀具磨损的测量结果,表明具有TiAlN涂层的刀具可以承受在所选择的加工状态下产生的热量。
具有TiAlN涂层的铣刀可以提高加工性能,这是由于在很高的工作温度下,涂层可以保持较高的硬度和抗氧化能力。
此外,在这项实验中,所有的注意事项表明,在刀具顶端中不会提示对工件材料的附着要求。
然而,它会造成从刀具顶端前角到前刀面的一个小间隙。
一个可能的解释,通过分析在刀具前刀面的正应力分布,可以测量刀具前刀面工件材料的附着力。
3.1表面粗糙度
在这个实验中,选择的表面粗糙度对应的变化量如图1所示。
从图1中对可以看出,相比于加工其他所有类型的铝合金材料,加工铝基碳化硅复合材料得到的表面粗糙粗是很低的。
这是由于在高温下铝基碳化硅复合材料加工后增加工件材料的流动性导致的。
这可能会有助于芯片更容易的形成,从而在铝基碳化硅复合材料加工条件下,降低其表面粗糙度。
但是,不断上升的温度通常会导致工件材料侧流上升。
而不断上升的工件材料的侧流又会造成更高的表面粗糙度。
但是,这有两个因素将会导致表面粗糙度的上升或下降。
考虑到在高温下增加了塑性将会减少应力,一个因素将会导致粗糙度的下降;又由于在高温下增加了侧流,其它因素将会增加粗糙度。
在这个实验中,我们可以发现,当采用了较高的进给速度,将不会大幅度增加边缘流动性(凯撒和阿贝威,1999)。
所以,在这些条件下,相比于第二个因素,第一个因素的效果将会处于决定性地位。
因此,相比于加工铝合金材料,加工铝基碳化硅复合材料的粗糙度将会很低。
图1Variationofsurfaceroughnesswithcuttingspeedatdifferentdepthofcutsandfeeds.
从图一中可以观察,在研究中,在其它条件不变的情况下,随着进给速度的增加,铝基碳化硅复合材料的表面粗糙度也在增加。
这是因为最大芯片厚度在增加,由于进给速度的增加,将导致切削力和表面粗糙度的增加。
此外,还可以看出,随着切削速度的增加,表面粗糙度在降低。
这种趋势是可以被预料到的,因为随着切削速度的增加,机械加工变的更加绝热,并且在剪切区域产生的热量,在材料通过这个区域时不能在很短的时间内排出。
因此,温度升高软化材料辅助晶界位错和表面粗糙度的降低可以在图1中看出。
在加工条件下,对于铝基碳化硅复合材料而言,表面粗糙度最小值对应的最优值(相对于输入加工参数附录A.1所示)的计算方法是利用遗传算法计算(赛睿库马瑞得和威客若,2006),如表4所示。
通过这项工作中的遗传算法可以观察到,铝基碳化硅复合材料的表面粗糙度最小值,发现在0.96到1.53微米内变化。
在最佳的铣削条件下,在切削速度是188mm/min、进给量是0.10mm/rev和背吃刀量是0.24mm的条件下,表面粗糙度的最小值是0.96微米。
通过遗传算法的应用来获得最佳的铣削状态的方法,在计算机辅助处理中将会是很实用的。
通过一系列的加工方法产生较高的工件质量、具有较高的公差要求,并且在自动化机械的自适应控过程中,优化加工铝基碳化硅复合材料铣削条件,需要较高的表面质量、较好的尺寸精度。
实验研究带来的益处,将使得机械制造工艺更具竞争力和经济性。
3.2显微硬度
对横截面样品进行了显微硬度测量。
图2表示在显微硬度的变化中,截面以下深度的函数。
从显微硬度测量的结果可以知道,铝基碳化硅复合材料和铝合金材料没有明显的改善次表面的性能。
在加工表面下,随着铣削深度的增加,显微硬度也在不断增加。
这可能是由于如下原因,在加工过程中,随着切削过程的温度变化,造成退火工件已加工表面的软化。
图2Microhardnessdepthvariationsofmachinedsurfacesatdifferentlevelsofcutconditions
从图2中可以看出,加工影响层的深度受到铣削参数的影响。
随着切削速度、进给量和背吃刀量的增加,加工影响层的深度也在增加。
此外,随着任何切削参数的增加,材料的硬化程度也在增加。
这可能是因为如下,切削温度的增加可能是加工中次表面硬化的一个原因;因为切削温度将会导致基体材料的热变形。
这是值得注意的,在加工表面和20微米深处的测量硬度有分散情况。
这是因为在碳化硅颗粒周围颗粒拔出、颗粒断裂和裂纹生长处于优先地位。
3.3残余应力
正如文献中所指出的,在加工中由于生高温,可能造成微观结构变化。
在地面上加工的条件下,根据材料的不同,这可能会导致产生拉伸或者压缩应力。
根据研究可知(马尔,1989),残余应力可以由3个因素引起:
热膨胀的影响、工件显微组织结构变化的影响和机械性能影响。
在加工过程中,产生的热量与热膨胀的程度成正比。
在外层的温度是最高的,随着向核心内层的方向,工件温度在不断下降。
在加工过程中,热源是自发扩散的,外层的扩散比内层的扩散多,造成了残余压应力留在表层。
当热源不再自发扩散(冷却)时,外层的收缩更多,而内层不允许收缩这么多。
在加工中受到的影响,主要来源于渗透到工件中的磨料颗粒。
图3表明在加工过程中,铝合金材料和铝基碳化硅复合材料出现的残余应力。
对于材料的机械加工特性来说,残余压应力是有益的,可以增加工件的疲劳强度和使用寿命。
另一方面,对于机械强度、腐蚀和磨损情况来说,残余拉应力是有害的。
相比于铝合金材料来说,加工铝基碳化硅复合材料的工件会产生很高的残余压应力,这是一个有益的方面。
与铝材料相比,铝基碳化硅复合材料残余压应力的检测值有明显增加。
正如前面所提到的,残余应力的出现是可以预料的。
在切削区,一旦铝基碳化硅复合材料产生了很高的作用,这将产生反作用。
通过缓慢的冷却过程,所有的热量都将渗入工件,并且可能改变工件表面附近的微观结构。
图3Comparativeresultsofresidualstressatadepthofapproximately5 μmbelowthesurface(S=150m/min,f =0.1mm/rev, d=0.2mm, ts=10s).
3.4微观组织
为了解释硬度的增强,使用透射显微镜来观察横截面的加工表面。
工件的加工在非常温和的条件下进行,所有测试工件都进行了微观结构的分析(如图4)
。
因此,避免了造成工件表面性能过多的改变。
通过微观结构的分析可知,频繁的加工表面会造成位错桩的产生,这是用于硬化的基体材料和复合材料。
图4Sub-surfacemicrostructureat S=100m/min, f=0.1mm/rev,d=0.1mm/min.
这个位错结构是由于残余应力(包括切削力和切削温度),并且造成材料的加强(位错类型进一步的分析是超出了本实验范围的,但是鼓励读者自行学习)。
在远离加工表面的区域,位错密度要低很多。
此外,在接近加工表面的基体颗粒的质量远比那些存在于远离加工表面的颗粒质量好。
小的晶粒的形成,可能是加工表面附近硬度增加的另一个原因。
此外,在铝基碳化硅复合材料的加工中,硅酸盐析物也起着重要的作用。
4结论
本次实验室在以前实验的基础上进行的,将有助于建成工业化国家。
本项实验研究将会有助于我们更好的理解、提高铣削端铣的铣削性能,并且通过选择恰当的工艺参数来提高生产率。
通过选择适当的铣削刀具和铣削参数,相比于铝合金材料,对铝基碳化硅复合材料的加工具有明显优势。
这项研究同时告诉我们,,在更广泛的烟叶生产中,通过使加工过程具有经济性和可行性,适当的选择铣削参数可以提高铝基碳化硅复合材料的加工性能、优化端铣过程。
附录A
A.1.表面粗糙度模型
基于铝基碳化硅复合材料的实验结果,采用响应面法(RSM)(蒙哥马利,2001),开发得到的第二级的表面粗糙度模型如下:
在Ra估计的表面粗糙度对应的对数刻度(微米),x1,x2,x3分别表示切削速度的对数变换(米/分钟)、进给量(毫米/转)和背吃刀量(毫米)。
A.2.遗传程序加工参数的输入值与输出值
参考文献
References
1.El-GallabandSklad,1998
M.El-Gallab,M.Sklad
MachiningofAl/SiCparticulatemetalmatrixcomposites.PartI:
toolperformance
J.Mater.Process.Technol.,83(1998),pp.151–158
2.Article|PDF(1675K)|ViewRecordinScopus|Citingarticles(193)
KishawyandElbestawi,1999
H.A.Kishawy,M.A.Elbestawi
Effectsofprocessparametersonmaterialsideflowduringhardturning
Int.J.Mach.ToolsManuf.,39(1999),pp.1017–1030
3.Article|PDF(2438K)|ViewRecordinScopus|Citingarticles(84)
Linetal.,1998
J.T.Lin,D.Bhattacharyya,W.G.Ferguson
ChipformationinthemachiningofSiC-particle-reinforcedaluminium–matrixcomposites
Compos.Sci.Technol.,58(1998),pp.285–291
4.Article|PDF(949K)|ViewRecordinScopus|Citingarticles(57)
Linetal.,2001
C.B.Lin,Y.W.Hung,W.-C.Liu,S.-W.Kang
Machiningandfluidityof356Al/SiC(p)composites
J.Mater.Process.Technol.,110(2001),pp.152–159
5.Article|PDF(3595K)|ViewRecordinScopus|Citingarticles(26)
Malkin,1989
S.Malkin
Grindingmechanisms&grindingtemperaturesandthermaldamage
S.Malkin(Ed.),GrindingTechnology:
TheoryandApplicationsofMachiningwithAbrasives(firsted.),EllisHorwoodLimited,Chichester(1989)
6.Montgomery,2001
D.C.Montgomery
DesignandAnalysisofExperiments
JohnWileyandSons(ASIA)Pvt.Ltd.,Singapore(2001)
7.SureshKumarReddyandVenkateswaraRao,2006
N.SureshKumarReddy,P.VenkateswaraRao
Selectionofoptimalparametriccombinationforachievingbettersurfacefinishinendmillingusinggeneticalgorithms
Int.J.Adv.Manuf.Technol.,28(5–6)(2006),pp.463–473