减速箱体工艺及装备设计方案论证.docx
《减速箱体工艺及装备设计方案论证.docx》由会员分享,可在线阅读,更多相关《减速箱体工艺及装备设计方案论证.docx(9页珍藏版)》请在冰豆网上搜索。
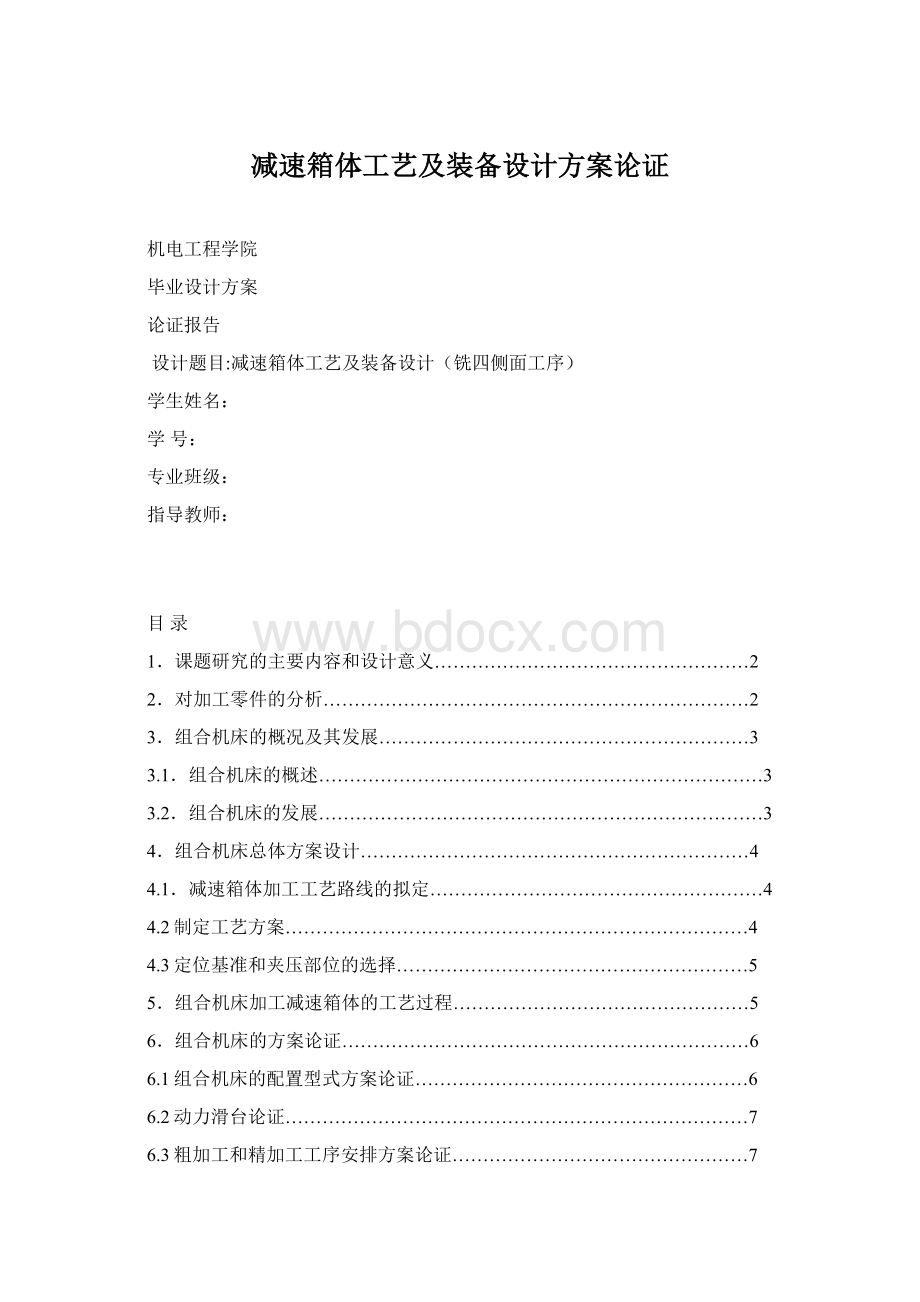
减速箱体工艺及装备设计方案论证
机电工程学院
毕业设计方案
论证报告
设计题目:
减速箱体工艺及装备设计(铣四侧面工序)
学生姓名:
学号:
专业班级:
指导教师:
目录
1.课题研究的主要内容和设计意义……………………………………………2
2.对加工零件的分析……………………………………………………………2
3.组合机床的概况及其发展……………………………………………………3
3.1.组合机床的概述………………………………………………………………3
3.2.组合机床的发展………………………………………………………………3
4.组合机床总体方案设计………………………………………………………4
4.1.减速箱体加工工艺路线的拟定………………………………………………4
4.2制定工艺方案…………………………………………………………………4
4.3定位基准和夹压部位的选择…………………………………………………5
5.组合机床加工减速箱体的工艺过程…………………………………………5
6.组合机床的方案论证…………………………………………………………6
6.1组合机床的配置型式方案论证………………………………………………6
6.2动力滑台论证…………………………………………………………………7
6.3粗加工和精加工工序安排方案论证…………………………………………7
6.4工序集中原则…………………………………………………………………7
6.5工艺基面的论证………………………………………………………………8
6.6平面铣削加工工艺的论证……………………………………………………8
6.7经济性和可靠性论证…………………………………………………………8
6.8工艺切削头论证…………………………………………………………8
7.结论…………………………………………………………………………9
参考文献…………………………………………………………………………10
减速箱体工艺及装备设计方案论证
1.课题研究的主要内容和设计意义
本次毕业设计是进行减速器箱体加工工艺文件的设计;铣四侧面工序的组合机床的总体方案设计及铣削头和本工序夹具结构设计。
具体内容包括:
了解现有的工艺和装备情况,完成减速箱体的工艺路线安排和工艺卡设计一份,铣四侧面工序的组合机床的总体方案设计(零号图1张);铣削头结构设计(零号图1张);铣四侧面工序的夹具结构设计(零号图1张)及零件图设计(零号图1张);完成设计说明书的编写。
意义:
提高减速箱体加工精度和生产效率;降低工人的劳动强度;提供了真正的工程设计训练。
2.对加工零件的分析
本次要设计的是减速箱体工艺及工装设计。
减速箱体(如图1所示)属于箱体类零件,它是机器及其部件的基础件。
箱体类零件将机器及其部件中的轴、轴承、套和齿轮等零件按一定的相互位置关系装配成一个整体,并按预定传动关系协调其运动。
因此,箱体的加工质量不仅影响其装配精度及运动精度,而且影响到机器的工作精度、使用性能和寿命。
此外,为满足箱体加工中的定位需要及箱体与机器总装要求,箱体的装配基准面与加工中的定位基准面应有一定的平面度和表面粗糙度要求。
图2-1减速箱体
通过对箱体类零件的分析,了解到如若采用通用机床或者其他专用机床,那么在工厂需要大量的立钻、镗床、铣床等,占用了很大的厂房面积和很多的工人,而采用组合机床,由于采用多轴多面加工,就能大大缩小占地面积,几十倍的提高劳动生产率。
同时组合机床比通用机床的生产效率高,产品质量稳定、工作可靠,劳动强度低。
因此对于减速箱体的加工选择组合机床。
3.组合机床的概况及其发展
3.1组合机床的概述
组合机床是以通用部件为基础,配以少量专用部件,对一种或若干种工件按预先确定的工序进行加工的机床。
组合机床一般采用多轴、多刀、多工序、多面或多工位同时加工的方式,生产效率比通用机床高几倍至几十倍。
由于通用部件已经标准化和系列化,可根据需要灵活配置,能缩短设计和制造周期。
因此,组合机床兼有低成本和高效率的优点,在大批、大量生产中得到广泛应用,并可用以组成自动生产线。
组合机床一般用于加工箱体类或特殊形状的零件。
加工时,工件一般不旋转,由刀具的旋转运动和刀具与工件的相对进给运动,来实现钻孔、扩孔、锪孔、铰孔、镗孔、铣削平面、切削内外螺纹以及加工外圆和端面等。
有的组合机床采用车削头夹持工件使之旋转,由刀具作进给运动,也可实现某些回转体类零件(如飞轮、汽车后桥半轴等)的外圆和端面加工。
3.2组合机床的发展
二十世纪70年代以来,随着可转位刀具、密齿铣刀、镗孔尺寸自动检测和刀具自动补偿技术的发展,组合机床的加工精度也有所提高。
铣削平面的平面度可达0.05毫米/1000毫米,表面粗糙度可低达2.5~0.63微米;镗孔精度可达IT7~6级,孔距精度可达O.03~O.02微米。
专用机床是随着汽车工业的兴起而发展起来的。
在专用机床中某些部件因重复使用,逐步发展成为通用部件,因而产生了组合机床。
最早的组合机床是1911年在美国制成的,用于加工汽车零件。
初期,各机床制造厂都有各自的通用部件标准。
为了提高不同制造厂的通用部件的互换性,便于用户使用和维修,1953年美国福特汽车公司和通用汽车公司与美国机床制造厂协商,确定了组合机床通用部件标准化的原则,即严格规定各部件间的联系尺寸,但对部件结构未作规定。
组合机床和组合机床自动线是一种专用高效自动化技术装备,目前,由于它仍是大批量机械产品实现高效、高质量和经济性生产的关键装备,因而被广泛应用于汽车、拖拉机、内燃机和压缩机等许多工业生产领域。
其中,特别是汽车工业,是组合机床和自动线最大的用户。
如德国大众汽车厂在Salzgitter的发动机工厂,90年代初所采用的金属切削机床主要是自动线(60%)、组合机床(20%)和加工中心(20%)。
显然,在大批量生产的机械工业部门,大量采用的设备是组合机床和自动线。
因此,组合机床及其自动线的技术性能和综合自动化水平,在很大程度上决定了这些工业部门产品的生产效率、产品质量和企业生产组织的结构,也在很大程度上决定了企业产品的竞争力。
现代组合机床和自动线作为机电一体化产品,它是控制、驱动、测量、监控、刀具和机械组件等技术的综合反映。
近20年来,这些技术有长足进步,同时作为组合机床主要用户的汽车和内燃机等行业也有很大的变化,其产品市场寿命不断缩短,品种日益增多且质量不断提高。
这些因素有力地推动和激励了组合机床和自动线技术的不断发展。
1组合机床品种的发展重点在组合机床这类专用机床中,回转式多工位组合机床和自动线占有很重要的地位。
因为这两类机床可以把工件的许多加工工序分配到多个加工工位上,并同时能从多个方向对工件的几个面进行加工,此外,还可以通过转位夹具(在回转工作台机床上)或通过转位、翻转装置(在自动线上)实现工件的五面加工或全部加工,因而具有很高的自动化程度和生产效率,被汽车、摩托车和压缩机等工业部门所采用。
根据有关统计资料,德国在1990~1992年期间,回转式多工位组合机床和自动线的产量约各占组合机床总数的50%左右。
为了使组合机床能在中小批量生产中得到应用,往往需要应用成组技术,把结构和工艺相似的零件集中在一台组合机床上加工,以提高机床的利用率。
这类机床常见的有两种,可换主轴箱式组合机床和转塔式组合机床。
组合机床未来的发展将更多的采用调速电动机和滚珠丝杠等传动,以简化结构、缩短生产节拍;采用数字控制系统和主轴箱、夹具自动更换系统,以提高工艺可调性;以及纳入柔性制造系统等。
4.组合机床总体方案设计
4.1减速箱体加工工艺路线的拟定
工艺路线的拟定是组合机床设计的关键一步。
因为工艺路线在很大程度上决定了组合机床的结构配置和使用性能。
因此,应根据工件的加工要求和特点,按一定的原则、结合组合机床常用工艺方法、充分考虑各种影响因素,并经技术分析后拟定出先进、合理的工艺路线。
根据粗精加工分开原则和工序集中原则初步拟定的工艺路线如下:
10以两面孔定位粗铣基准面
20以两面孔定位钻基准面孔
30以基准面及基准面孔定位粗铣四侧面
30以基准面及基准面孔定位镗纵,横向孔
40以两面孔定位精铣基准面
50以基准面及基准面孔定位精铣四侧面
50以基准面及基准面孔定位精镗纵,横向孔
60以基准面及基准面孔定位钻左,右面孔
70以基准面及基准面孔定位进行左,右螺孔攻丝
4.2制定工艺方案
工艺方案制定得正确与否,将决定机床能否达到“体积小,重量轻,结构简单,使用方便,效率高,质量好”的要求。
为了使工艺方案制定得合理、先进,必须从认真分析被加工零件图纸开始,深入现场全面了解被加工零件的结构特点、加工部位、尺寸精度、表面粗糙度和技术要求,定位、加紧方式,工艺方法和加工过程所采用的刀具、辅具,切削用量情况及生产率要求等,分析其优缺点,总结设计、制造、使用单位和操作者丰富的实践经验,以求理论紧密联系生产实际,从而确定零件在组合机床上完成的工艺内容及方法,结构形式、数量及切削用量。
4.3定位基准和夹压部位的选择
铣减速箱体的四侧面,对于箱体类零件,其定位通常选用“一面两孔”,而且将被加工的减速箱体正好符合这些特征要素。
“一面两孔”的定位方法很简便的消除工件的六个自由度,使工件获得稳定的固定位置。
这种定位方法使夹紧方便,夹紧结构简单。
容易使夹紧力对准支承,消除夹紧力引起工件变形对加工精度的影响,同时这也使整个工艺过程实现基准统一。
减速箱体的夹紧,其夹紧方式采用在基准面上端面用压板夹紧。
这样有利于刀具的通过和在有足够的夹紧力下工件产生的变形小。
如图
(2)
图4-3-2减速箱体零件的夹紧
5.组合机床加工减速箱体的工艺过程
根据机械加工,先面后孔,先基准再其他的原则,由组合机床加工减速箱箱体的工艺安排是先铣削基准面,后钻基准面上的八个孔,再铣减速箱底面的四个侧面,接着铣削减速箱四侧面的凸台,接着钻四侧面凸台上的孔,最后镗孔。
这些工艺安排在三台组合机床上完成,一台组合机床完成铣基准面和四侧面,另一台完成钻底面八个孔和四侧面凸台上的十二个螺纹孔,最后利用组合镗床完成四侧面孔的镗削加工。
6.组合机床的方案论证
6.1组合机床的配置型式方案论证
组合机床有大型和小型两种,大、小型组合机床虽然有共性,但又都有其特殊性。
不同的配置型式适应不同的加工工件。
对于本次加工的箱体类零件,提出了以下两个机床的配置方案:
方案一:
卧式单面组合机床,固定夹具
方案二:
卧式双面组合机床,固定夹具
如图(3)所示
单工位组合机床通常是用于加工一个或两个工件,特别适用于大中型箱体的加工。
根据配置动力部件的数量,这类机床可以从单面或同时从几个方面对工件进行加工。
各种配置形式组合机床中的加工精度不同,在组合机床上,影响加工精度的因素很多,但总的来说可分为夹具误差和加工误差的影响。
这些误差的大小与所选的组合机床有很大的关系。
本次要加工减速箱体的四侧面,要求平面的精度达到3.2微米,对精度要求较高。
图6-1-3组合机床
方案一和方案二都选择卧式组合铣床,这样使得定位工件的夹紧力方向与加工方向垂直。
这样做法的精度自然要比立式组合铣床的高。
但是方案一,由于用的是单面组合机床一次就加工一个面,这样以来加工效率就大大降低;同时单侧加工容易产生较大的切削力和振动。
切削力大可能导致工件的变形,影响加工工件的精度。
方案二,一次加工工件的两面,这样不仅提高的工件的加工效率而且双侧面加工可以平衡加工工件的切削力。
虽然方案二须两道加工工序,但是定位基准是统一的,所以可以满足加工的精度要求。
综合以上的论述,选择方案二卧式双面单工位组合机床。
6.2动力滑台论证
方案一:
HY系列液压动力滑台
方案二:
HJ系列机械动力滑台
液压滑台是由滑台、滑座和油缸三部分组成。
油缸固定在滑座上,活塞杆则固定在滑台下面。
当压力油进入油缸的后腔或前腔时,便可根据滑台沿滑座的导轨向前或向后移动。
液压滑台的特点:
在相当大的范围内进给量可以无级变速,可以获得较大的进给力,零件磨损小,使用寿命长。
但是液压滑台的调整维修比较麻烦,进给量受温度影响。
机械滑台由滑台、滑座及传动装置三部分组成。
机械滑台的传动装置采用两个电机及差速器传动。
滑台的快速运动的制动由装在快速电机后端的傍磁式铁实现,工作可靠,转换精度高。
机械滑台进给量稳定,慢速无爬行,安全可靠,调整维修方便。
综上所论可知:
机械滑台操作方便,经济成本较低,同时也能满足加工精度要求,故选择方案二。
6.3粗加工和精加工工序安排方案论证
方案一:
粗精加工分开加工方式
方案二:
粗精加工一起加工方式
虽然粗精加工分开进行具有很多的优点,比如粗精加工分开进行可以使工件得到较好的冷却,减少热变形和内应力变形的影响,有利于保证加工精度。
还可以避免粗加工产生振动的不利影响,有利于精加工机床的精度持久的保持等等,但是粗、精加工分开进行的结果使机床的台数增多,而且,由于减速箱体的生产批量较小,一年只有200台,如果采用粗、精加工分开的方式加工,则会使机床负荷率降低,投资很大,经济性差,此外,由于生产批量较小,允许有较多的调刀时间,因此采用方案二粗、精加工一起加工的方式加工减速箱体。
6.4工序集中原则
方案一:
工序分散加工,一次只加工一个面
方案二:
工序集中加工,一次同时加工两个面
工序集中是近代机械加工主要发展方向之一。
组合机床正是基于这一原则发展而来,即运用多刀集中在一台机床上完成一个或几个工件的不同表面的复杂工艺过程,从而有效地提高生产率。
但是,工序过于集中会使机床机构太复杂,增加机床设计和制造难度,机床使用调整不便,甚至影响机床使用性能。
合理决定工序集中程度,遵循以下原则:
适当考虑相同类型工序的集中;有相对位置精度要求的工序应集中加工。
综合考虑,选择方案二。
6.5工艺基面的论证
工艺基面选择的正确,将能实现最大限度的工序集中,从而减少机床台数,也是保证加工精度的重要条件。
箱体类零件是机械加工中工序多,精度要求高的零件。
这类零件一般都要求有较高精度的面、孔需要加工,又常常要在几次装夹下进行。
因此,定位基准选择“一面两孔”是最常用的方法。
它的特点是:
可以简便地消除工件的六个自由度,使工件获得稳定可靠的定位。
有同时加工零件五个表面的可能,既能高度集中工序,又有利于提高各面上孔的位置精度。
“一面两孔”可作为零件从粗加工到精加工全部工序的定位基准,使零件整个工艺过程基准统一,从而减少由基准转换带来的累计误差,有利于保证零件加工精度。
同时,使机床各工序的许多部件实现通用化,有利于缩短设计,制造周期,降低成本。
易于实现自动化定位,夹紧,并有利于防止切屑落于定位及面上。
综合以上特点,加工减速箱体选择“一面两孔”的定位方法。
6.6平面铣削加工工艺的论证
方案一:
铣头进给运动,工件不动
方案二:
铣头不作进给运动,由动力滑台带动工件进给运动
目前,为了提高平面的加工效率,采用组合铣床加工平面日益增多。
这种组合铣床是由通用铣头和动力滑台等主要部件组成的。
加工时一般铣头不作进给运动。
进给运动是由进给动力滑台带动工件实现的。
如若采用工件不动,由铣头实现进给的铣削方法,则加工的可靠性差,而且也不经济。
所以选择方案二,铣头不作进给运动,由动力滑台带动工件进给运动。
6.7经济性和可靠性论证
在满足工件要求的前提下,机床避免复杂刀具,力求简单和较高的通用化程度。
这样可以降低机床成本,提高工作的可靠性。
根据加工精度的需要选择相当精度等级的通用部件;根据生产率的要求合理安排工艺流程,合理利用机床,以取得好的经济效果。
6.8工艺切削头论证
铣削时采用TX系列的铣削头,包括主轴组件和传动装置,由于减速箱体是铸铁件,可采用齿轮传动。
7结论
综上所述,从以上各个方面对加工减速箱体工艺工装的方案进行初步论证得出总体方案:
先确定“一面两孔”的定位方案,用粗加工和精加工一起加工方法铣出基准面,再加工出基准孔;然后定位夹紧好工件,采取铣头不动,动力滑台带动工件进给运动方式同时铣削两侧面,然后再用同样的方法重新夹紧工件铣另两侧面,动力滑台采用机械滑台,铣削时采用TX系列的铣削头,这种方案是可行的。
参考文献
[1]谢家瀛.组合机床设计简明手册.机械工业出版社.2008
[2]大连组合机床研究所主编.机械工程手册第62篇.北京:
劳动人事出版社,1987
[3]金振华.组合机床及其调整与使用.机械工业出版社.1984
[4]张接信.组合机床及其自动化.人民交通出版社.2009
[5]沈阳工业大学大连铁道学院吉林工学院上海:
上海科学技术出版社,1992
[6]李如松.组合机床和自动线的技术发展[EB/OL].(2005-12-05).http:
//www.icad.com.cn.
[7]徐旭东,周菊琪.现代组合机床技术及其发展[J].中国知网.1994.7.12
[8]李秀敏.组合机床行业现状与发展思考[J].航空制造技术,2003
[9]薛永威.电镀金刚石铰刀.大连机床厂.1979
[10]清华大学、上海工业大学编,气动技术,1978