CA6140车床齿轮零件的加工工艺及夹具设计.docx
《CA6140车床齿轮零件的加工工艺及夹具设计.docx》由会员分享,可在线阅读,更多相关《CA6140车床齿轮零件的加工工艺及夹具设计.docx(61页珍藏版)》请在冰豆网上搜索。
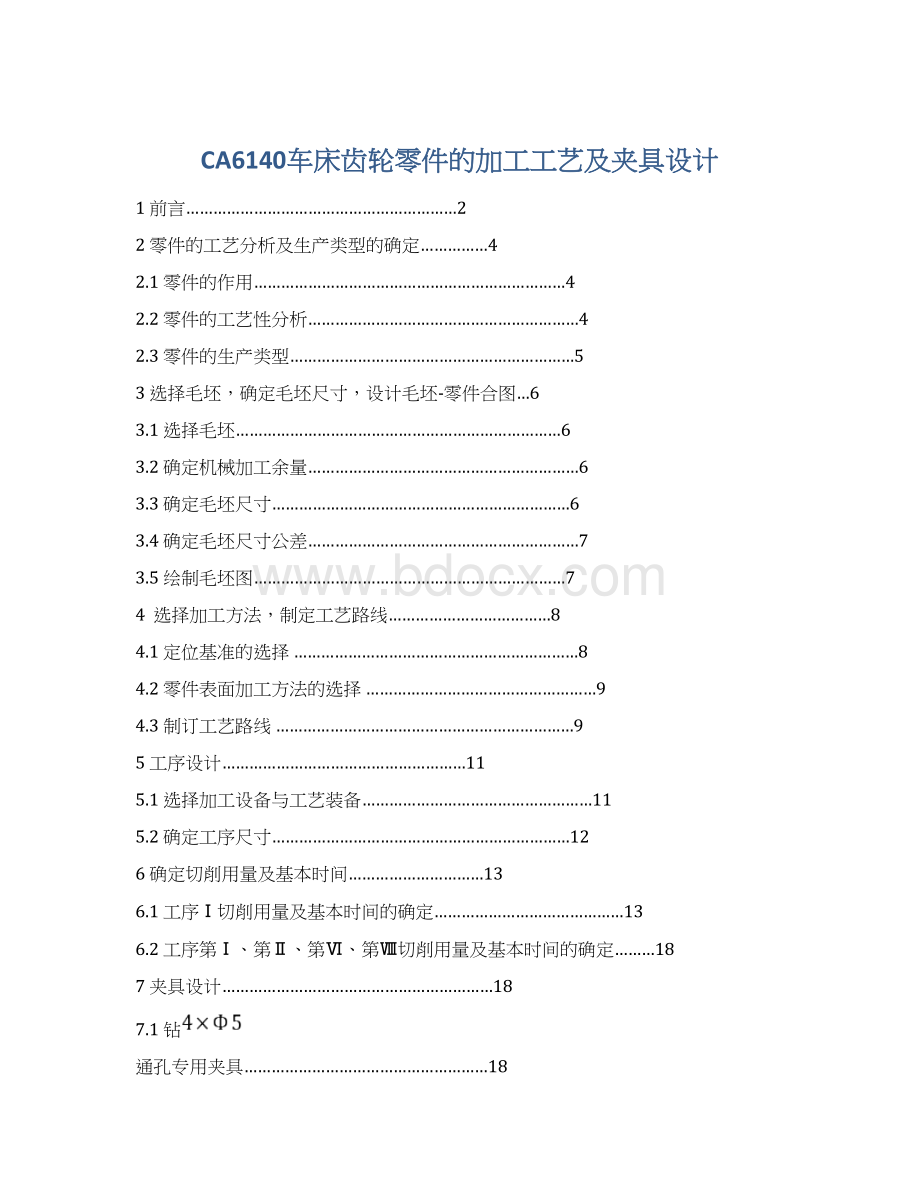
CA6140车床齿轮零件的加工工艺及夹具设计
1前言……………………………………………………2
2零件的工艺分析及生产类型的确定……………4
2.1零件的作用……………………………………………………………4
2.2零件的工艺性分析……………………………………………………4
2.3零件的生产类型………………………………………………………5
3选择毛坯,确定毛坯尺寸,设计毛坯-零件合图…6
3.1选择毛坯………………………………………………………………6
3.2确定机械加工余量……………………………………………………6
3.3确定毛坯尺寸…………………………………………………………6
3.4确定毛坯尺寸公差……………………………………………………7
3.5绘制毛坯图……………………………………………………………7
4选择加工方法,制定工艺路线………………………………8
4.1定位基准的选择………………………………………………………8
4.2零件表面加工方法的选择……………………………………………9
4.3制订工艺路线…………………………………………………………9
5工序设计………………………………………………11
5.1选择加工设备与工艺装备……………………………………………11
5.2确定工序尺寸…………………………………………………………12
6确定切削用量及基本时间…………………………13
6.1工序Ⅰ切削用量及基本时间的确定……………………………………13
6.2工序第Ⅰ、第Ⅱ、第Ⅵ、第Ⅷ切削用量及基本时间的确定………18
7夹具设计……………………………………………………18
7.1钻
通孔专用夹具………………………………………………18
7.2铣21x22mm槽口的专用夹具………………………………………20
8小结…………………………………………………………23
9人员分配表…………………………………………………24
10参考文献………………………………………………………………25
1前言
本次设计的主要目的是要得到以下几方面的锻炼:
1能熟练运用机械制造工艺设计中的基本理论以及在生产实习中学到的实践知识,正确地解决一个零件在加工中的定位、夹紧以及工艺路线安排、工艺尺寸确定等问题,保证零件的加工质量。
2提高结构设计的能力。
通过设计夹具的训练,应当获得根据被加工零件的加工要求,设计出高效、省力、经济合理而且能保证加工质量的夹具的能力。
3学会使用手册及图表资料。
掌握与本设计有关的各种资料的名称、出处、能够做到熟练运用。
就我个人而言,通过这次设计,基本上掌握了零件机械加工工艺规程的设计,机床专用夹具等工艺装备的设计等。
并学会了使用和查阅各种设计资料、手册、和国家标准等。
最重要的是综合运用所学理论知识,解决现代实际工艺设计问题,巩固和加深了所学到的东西。
并在设计过程中,学到了很多课堂上没有学到的东西。
能够顺利的完成这次毕业设计,首先得助于王老师的悉心指导。
在设计过程中,由于对零件加工所用到的设备的基本性能和加工范围缺乏全面的了解,缺乏实际的生产经验,导致在设计中碰到了许多的问题。
但在我们小组成员的共同努力下,我们通过请教老师和咨询同学,翻阅资料、查工具书,解决设计过程中的一个又一个的问题。
在这个过程中,使我对所学的知识有了进一步的了解,也了解了一些设计工具书的用途,同时,也锻炼了相互之间的协同工作能力。
在此,十分感王老师的细心指导,感谢其他同学的热心帮助。
在以后的学习生活中,我将继续刻苦努力,不断提高自己。
随着科学技术的发展,各料、新工艺和新技术不断涌现,机械制造工艺正向高质量、高生产率和低成本方向发展。
电火花、电解、超声波、种新材激光、电子束和离子束加工等工艺的出现,已突破传统的依靠机械能、切削力进行切削加工的范畴,可以加工各种难加工材料、复杂的型面和某些具有特殊要求的零件。
数控机床的出现,提高了更新频繁的小批量零件和形状复杂的零件加工的生产率及加工精度。
特别是计算方法和计算机技术的迅速发展,大大推进了机械加工工艺的进步,使工艺过程的自动化达到了一个新的阶段。
目前,数控机床的工艺功能已由加工循环控制、加工中心,发展到适应控制。
加工循环控制虽可以实现每个加工工序的自动化,但不同的工序中刀具的更换及工件的重新装夹,仍须人工来完成。
加工中心是一种高度自动化的多工序机床,能自动完成刀具的更换,工件的转位和定位,主轴和进给量的变换等,使工件在机床上只安装一次就能完成全部加工。
因此,他可以显著缩短辅助时间,提高生产率,改善劳动条件,适应控制数控机床是一种具有“随机应变”功能的机床,他能在加工中,根据切削条件的变化,自动调整切削条件,是机床保持最佳状态下进行加工,因而有效提高加工效率,扩大品种,更好的保证了加工质量,并达到最大的经济效率。
夹具的发展趋势
工艺装备的设计、制造、使用和管理,体现着一个企业的工艺技术水平,夹具设计与制造又是制造环境中的生产准备周期时间和加工成本的重要因素,工装设计水平的高低,很大程度上反映出企业制造能力的高低。
夹具设计与制造是机电产品设计与制造的一项重要步骤,传统的夹具设计制造时需大量的工时消耗和金属材料的消耗。
目前,基于特征参数化技术已在机电产品设计与制造的各个阶段得到广泛的应用,夹具设计也必须向标准化、系统化、参数化方向发展。
而且,为了适应我国加入WTO后机电产品的创新能力和尽快机电产品设计制造的全程仿真,快速组合夹具的发展正是适应了这种要求。
夹具是机械加工不可缺少的部件,在机床技术向高速、高效、精密、复合、智能、环保方向发展的带动下,夹具技术正朝着高精、高效、模块、组合、通用、经济方向发展。
本说明书主要是关于CA6140车床齿轮的有关工艺规程的设计说明,由于本身及小组成员能力水平有限,设计存在许多错误和不足之处,恳请老师给予指正,
2零件的工艺分析及生产类型的确定
2.1零件的作用
所给定的零件是CA6140车床主轴箱中运动输入轴Ⅰ轴上的一个离合器齿轮。
它位于Ⅰ轴上,用于接通或断开主轴的反转传动路线,与其他零件一起组成摩擦片正反转离合器。
主运动传动链由电机经过带轮传动副φ130mm/φ230mm传至主轴箱中的轴Ⅰ。
在轴Ⅰ上装有双向多片摩擦离合器M1,使主轴正转、反转或停止。
当压紧离合器左部的摩擦片时,轴Ⅰ的运动经齿轮副56/38或51/43传给轴Ⅱ,使轴Ⅱ获得2种转速。
压紧右部摩擦片时,经齿轮50、轴Ⅶ上的空套齿轮34传给轴Ⅱ上的固定齿轮30。
这时轴Ⅰ至轴Ⅱ间多一个中间齿轮34,故轴Ⅱ的转向相反,反转转速只有1种。
当离合器处于中间位置时,左、右摩擦片都没有被压紧,轴Ⅰ运动不能传至轴Ⅱ,主轴停转。
此零件借助两个滚动轴承空套在Ⅰ轴上,只有当装在Ⅰ轴上的内摩擦片和装在该齿轮上的外摩擦片压紧时,Ⅰ轴才能带动该齿轮转动。
该零件φ68K7mm的孔与两个滚动轴承的外圈相配合,φ71mm沟槽为弹簧挡圈卡槽,φ94mm的孔容纳内、外摩擦片,4~21mm槽口与外摩擦片的翅片相配合使其和该齿轮一起转动,5×1.5mm沟槽和4×φ5mm的孔用于通入冷却润滑油。
2.2零件的工艺性
2.2.1主要技术要求:
零件图上的主要技术要求为:
模数:
2.25
齿数:
50
精度:
7-6-6-FLJB179-83
热处理:
齿部G52
2.2.2加工表面的尺寸及要求:
1、左端φ68K7外圆表面精度等级为IT7,表面粗糙度为Ra0.8。
并且槽相对φ68K7孔的轴线成90度均匀分布。
2、21mm宽槽口相对φ68K7孔的轴线成90°均匀分布,其径向设计基准是φ68K7mm孔的轴线,轴向设计基准是φ106.5mm外圆柱的左端平面。
3、4×φ5mm孔在5×1.5mm沟槽内,孔中心线距沟槽一侧面的距离为3mm,圆锥角度为90度。
4个φ5mm孔分别与21mm槽宽错开45度均匀分布。
4、由于加工时不能选用沟槽的侧面为定位基准,故要精确地保证上述要求比较困难,但这些小孔为油孔,位置要求不高,只要钻到沟槽之内接通油路就可,加工不难。
5、Φ90外圆表面精度等级为IT14,表面粗糙度为Ra3.2。
6、左端外圆表面φ106.5
精度等级为IT12,表面粗糙度为Ra6.3。
7、φ94外圆表面精度等级为IT14,表面粗糙度为Ra6.3。
8、φ71内孔槽内圆表面精度等级为IT11,表面粗糙度为Ra3.2。
9、φ117h11龄轮外圆表面IT11Ra3.2,齿面Ra11,齿部热处理G52.
10、右端面Ra3.2,左端面Ra6.3。
11、倒(圆)角。
2.3零件的生产类型
零件材料是45钢,零件年产量5000已经是大批量,而且零件加工的轮廓尺寸不大,在考虑提高生产率保证加工精度后可采用铸造成型。
零件形状并不复杂,因此毛坯形状可以与零件的形状尽量接近,内圆需要铸造出。
毛坯尺寸通过确定加工余量后再决定。
3选择毛坯,确定毛坯尺寸,设计毛坯-毛坯零件图
3.1选择毛坯
正确地选择毛坯是工艺技术员应该高度重视的问题。
零件加工过程中工序的内容或工序数目、材料消耗、热处理方法、零件制造费用等都与毛坯的材料、制造方法、毛坯的误差及其余量有关。
机械加工中常用的毛坯种类很多,主要有铸件、锻件、型材、焊接件、冷冲压件、其它(工程材料、粉末冶金等)。
在相同材料的条件下,锻件的机械强度和冲击韧性比铸件高,对于承受重载荷、交变载荷和冲击载荷工作的零件常选用锻件。
该零件材料为45钢,而且属于薄壁的圆盘类中小型零件,考虑加工工序较多,会经常承受交变载荷及冲击载荷,因此应该选用锻件,可得到连续和均匀的金属纤维组织,保证零件工作可靠。
又由于零件年产量为5000件,属大批量生产,而且零件的轮廓尺寸不大,故可采用模锻成形,可获得较好的尺寸精度和较高的生产率。
模锻毛坯具有以下特点:
1.其轮廓尺寸接近零件的外形尺寸,加工余量及材料消耗均大量减少;
2.其制造周期短,生产率高,保证产品质量。
3.2确定机械加工余量
根据锻件质量、零件表面粗糙度、形状复杂系数查《金属机械加工工艺人员手册》中锻件内外表面加工余量表,查得单边余量在厚度方向为1.7~2.2 mm,水平方向为1.7~2.2 mm。
锻件中心两孔的单面余量按手册中锻件内孔直径的单面机械加工余量表,可查得为2.5 mm。
3.3确定毛坯尺寸
根据查得的加工余量适当选择稍大点即可,只有φ68K7 mm孔,因为表面粗糙度要求达到Ra 0.8,考虑磨削孔前的余量要大,可确定精镗孔单面余量为0.5 mm。
其他槽、孔随所在平面锻造成实体。
具体加工余量的选择大小如表7-1所示。
3.4确定毛坯尺寸公差
3.4.1锻件公差等级。
由该零件的功用和技术要求,确定其锻件公差等级为普通级。
3.4.2锻件质量m。
根据零件成品质量1.36 kg,估算毛坯质量为mf = 2.5 kg。
3.4.3零件表面粗糙度。
由零件图知,除φ68K7 mm孔以外,其余各加工表面为Ra≥1.6。
毛坯尺寸公差根据锻件质量、材质系数、形状复杂系数从手册中查锻件的长度、宽度、高度、厚度公差表可得。
具体如表3-1所示。
表3-1
零件尺寸
单面加工余量
锻件尺寸
偏差
117H11
2
121
106.5
1.75
110
94
2
89
90
2
94
68K7
3
62
64
2
68
94孔深31mm
1.8
29.2
20
1
21
12
1.8
13.8
3.5绘制毛坯图
根据确定的毛坯尺寸和加工余量,可绘制毛坯