壁挂面板Moldflow流动方案对比分析.docx
《壁挂面板Moldflow流动方案对比分析.docx》由会员分享,可在线阅读,更多相关《壁挂面板Moldflow流动方案对比分析.docx(11页珍藏版)》请在冰豆网上搜索。
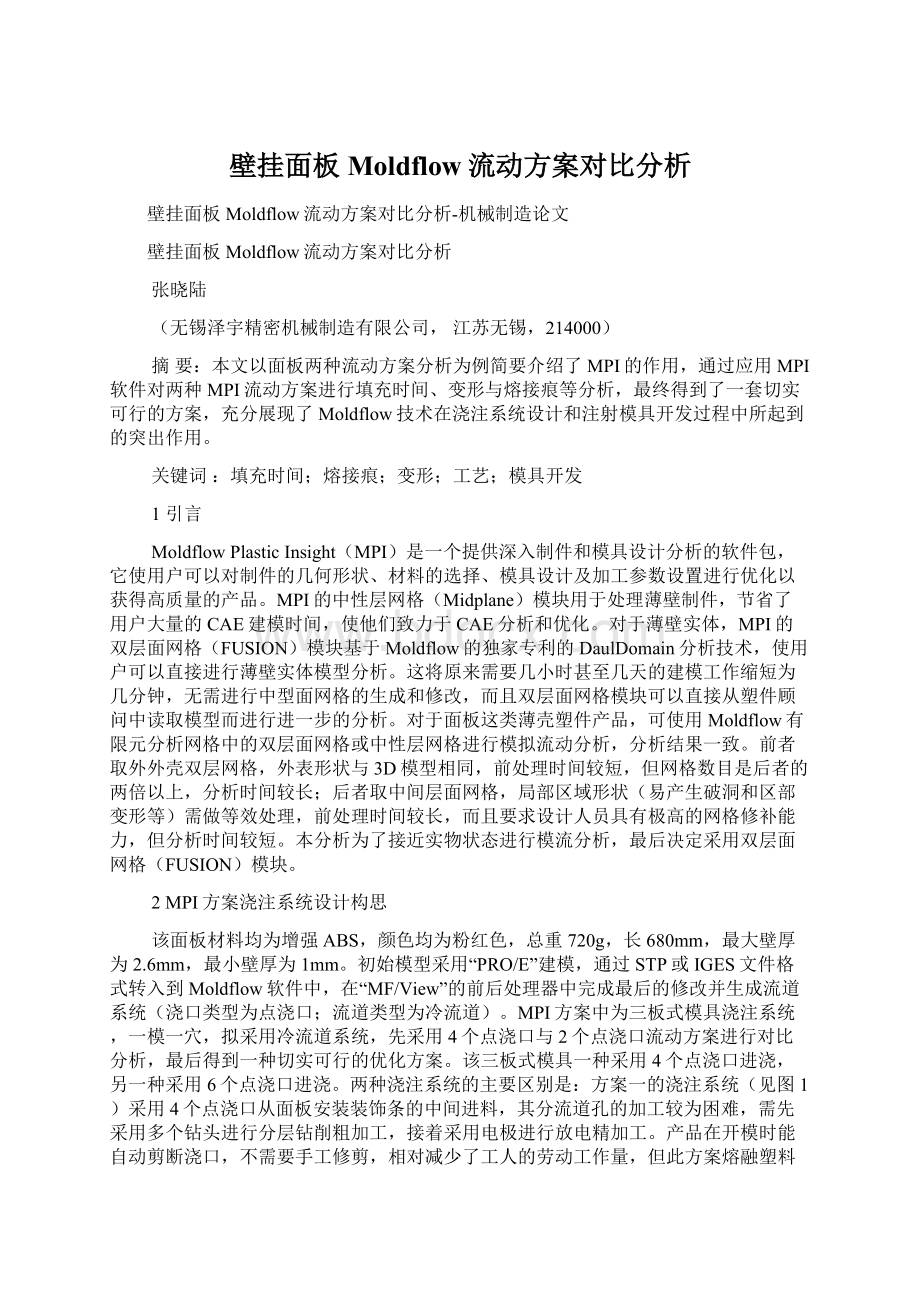
壁挂面板Moldflow流动方案对比分析
壁挂面板Moldflow流动方案对比分析-机械制造论文
壁挂面板Moldflow流动方案对比分析
张晓陆
(无锡泽宇精密机械制造有限公司,江苏无锡,214000)
摘要:
本文以面板两种流动方案分析为例简要介绍了MPI的作用,通过应用MPI软件对两种MPI流动方案进行填充时间、变形与熔接痕等分析,最终得到了一套切实可行的方案,充分展现了Moldflow技术在浇注系统设计和注射模具开发过程中所起到的突出作用。
关键词:
填充时间;熔接痕;变形;工艺;模具开发
1引言
MoldflowPlasticInsight(MPI)是一个提供深入制件和模具设计分析的软件包,它使用户可以对制件的几何形状、材料的选择、模具设计及加工参数设置进行优化以获得高质量的产品。
MPI的中性层网格(Midplane)模块用于处理薄壁制件,节省了用户大量的CAE建模时间,使他们致力于CAE分析和优化。
对于薄壁实体,MPI的双层面网格(FUSION)模块基于Moldflow的独家专利的DaulDomain分析技术,使用户可以直接进行薄壁实体模型分析。
这将原来需要几小时甚至几天的建模工作缩短为几分钟,无需进行中型面网格的生成和修改,而且双层面网格模块可以直接从塑件顾问中读取模型而进行进一步的分析。
对于面板这类薄壳塑件产品,可使用Moldflow有限元分析网格中的双层面网格或中性层网格进行模拟流动分析,分析结果一致。
前者取外外壳双层网格,外表形状与3D模型相同,前处理时间较短,但网格数目是后者的两倍以上,分析时间较长;后者取中间层面网格,局部区域形状(易产生破洞和区部变形等)需做等效处理,前处理时间较长,而且要求设计人员具有极高的网格修补能力,但分析时间较短。
本分析为了接近实物状态进行模流分析,最后决定采用双层面网格(FUSION)模块。
2MPI方案浇注系统设计构思
该面板材料均为增强ABS,颜色均为粉红色,总重720g,长680mm,最大壁厚为2.6mm,最小壁厚为1mm。
初始模型采用“PRO/E”建模,通过STP或IGES文件格式转入到Moldflow软件中,在“MF/View”的前后处理器中完成最后的修改并生成流道系统(浇口类型为点浇口;流道类型为冷流道)。
MPI方案中为三板式模具浇注系统,一模一穴,拟采用冷流道系统,先采用4个点浇口与2个点浇口流动方案进行对比分析,最后得到一种切实可行的优化方案。
该三板式模具一种采用4个点浇口进浇,另一种采用6个点浇口进浇。
两种浇注系统的主要区别是:
方案一的浇注系统(见图1)采用4个点浇口从面板安装装饰条的中间进料,其分流道孔的加工较为困难,需先采用多个钻头进行分层钻削粗加工,接着采用电极进行放电精加工。
产品在开模时能自动剪断浇口,不需要手工修剪,相对减少了工人的劳动工作量,但此方案熔融塑料流动较为不平衡,熔接痕可能也要多点,必要时需根据实际情况调整点浇口的尺寸,以方便转移熔接痕的位置;方案二的浇注系统(见图2)采用2个点浇口直接点到面板中间装饰条安装面上,流道的加工更为复杂,同样须先采用钻头分级预钻2个孔,后采用电极进行电火花精加工。
产品在开模时能自动剪断浇口,不需要手工修剪,相对减少了工人的劳动工作量,流动较为平衡,产品成型的熔接痕可能也要少点。
3MPI方案的基本成型条件
充填条件:
模具温度(Moldtemperature):
60℃最大剪切应力(MaximumShearStress):
0.25MPa注射时间(Injectiontime):
1.5~3.5s最大注射压力(Max.InjectPressure):
120MPa零件净重(PartWeight):
720g最大熔融温度(MeltTemperatureMaximum):
250℃最小熔融温度(MeltTemperatureMinimum):
195℃熔融温度(Melttemperature):
240℃保压条件:
压力(PRESSURE)[%HP]:
一段为70;时间(STEPDURATION)[s]:
一段为4
4MPI流动方案对比分析
4.1方案一流动对比分析
在Moldflow软件中设置Cool+Flow+Warp分析程序,先创建4个点浇口的浇注系统,然后设置上下各八路水道,并确定水路流向,最后进行Cool+Flow+Warp分析得到图3、4、5、6、7、8、9的分析结果。
由图3可知方案一填充时间为1.853s,填充较为平衡,填充时间基本合理。
由图4可知方案一切换点的压力为52.74Mpa,塑件成型基本没问题。
由图5可知整体变形最大4.434mm,整体变形过大,需要适当调整。
由图6、7、8可知X、Z方向变形过大,Y方向变形可勉强接受,故需适当调整浇注系统或冷却系统进行优化设计,以确保产品的变形能得到有效控制。
由图9可知熔接痕比较明显,在实践中很难通过调整注射工艺参数来消除熔接痕现象。
4.2方案二变形与熔接痕分析
在Moldflow软件中设置Cool+Flow+Warp分析程序,先创建2个点浇口的浇注系统,然后设置上下各八路水道,并确定水路流向,最后进行Cool+Flow+Warp分析得到图10、11、12、13、14、15、16的分析结果。
由图10可知方案二填充时间为2.363s,填充较为平衡,填充时间同样基本合理。
由图11可知方案二切换点的压力为65.46Mpa,比方案一稍高,但塑件成型基本没问题。
由图12可知整体变形最大2.943mm,比方案一大大下降,但整体变形仍然过大,需要适当调整,并且调整2个点浇口大小与每路水道增设翻水孔来使塑件变形得到有效控制。
由图13、14、15可知X方向变形仍然过大,Y、Z方向变形可勉强接受,故需进一步适当调整浇注系统或冷却系统进行优化设计,以确保产品的变形能得到有效控制。
由图16可知熔接痕数量很少,在实践中通过适当调整注射工艺参数可以适当消除熔接痕现象。
4.3结论及建议
由以上两种方案的分析结果可知,方案二的整体变形与X、Y、Z方向变形最小,熔接痕不明显,但填充时间与切换点压力稍大一点,不过对成型没有任何影响;方案一的整体变形与X、Y、Z方向变形方向变形均偏大,熔接痕明显,但填充时间与切换点压力要小一点。
根据以上分析最终决定选取方案二进行进一步优化分析,最终得到一套切实可行的方案,考虑到篇幅有限在这里就不再赘述。
如果该模具批量较大,公司也比较富有,还可适当考虑采用热流道方案进行分析,有兴趣的读者可以试试。
5结束语
通过应用Moldflow软件对两种MPI方案进行填充时间、变形与熔接痕等对比分析,不仅得到了一套切实可行的MPI方案,而且还丰富了工艺人员的Moldflow知识,为将来开发更加复杂的产品打下了坚实的技术基础。
随着Moldflow软件在注塑行业的不断推广使用,必将会大大缩短新产品的开发周期和费用,提高塑料制品的生产效率和质量,从而为中国的制造企业带来良好的经济效益。
参考文献:
[1]北京市塑料工业公司编.塑料成型工艺.北京:
中国轻工业出版社,1996.
[2]塑料模具设计手册编写组.塑料模具设计手册[M].北京:
机械工业出版社,2002.