拨叉机械加工工艺规程及夹具设计有cad源图课程设计.docx
《拨叉机械加工工艺规程及夹具设计有cad源图课程设计.docx》由会员分享,可在线阅读,更多相关《拨叉机械加工工艺规程及夹具设计有cad源图课程设计.docx(11页珍藏版)》请在冰豆网上搜索。
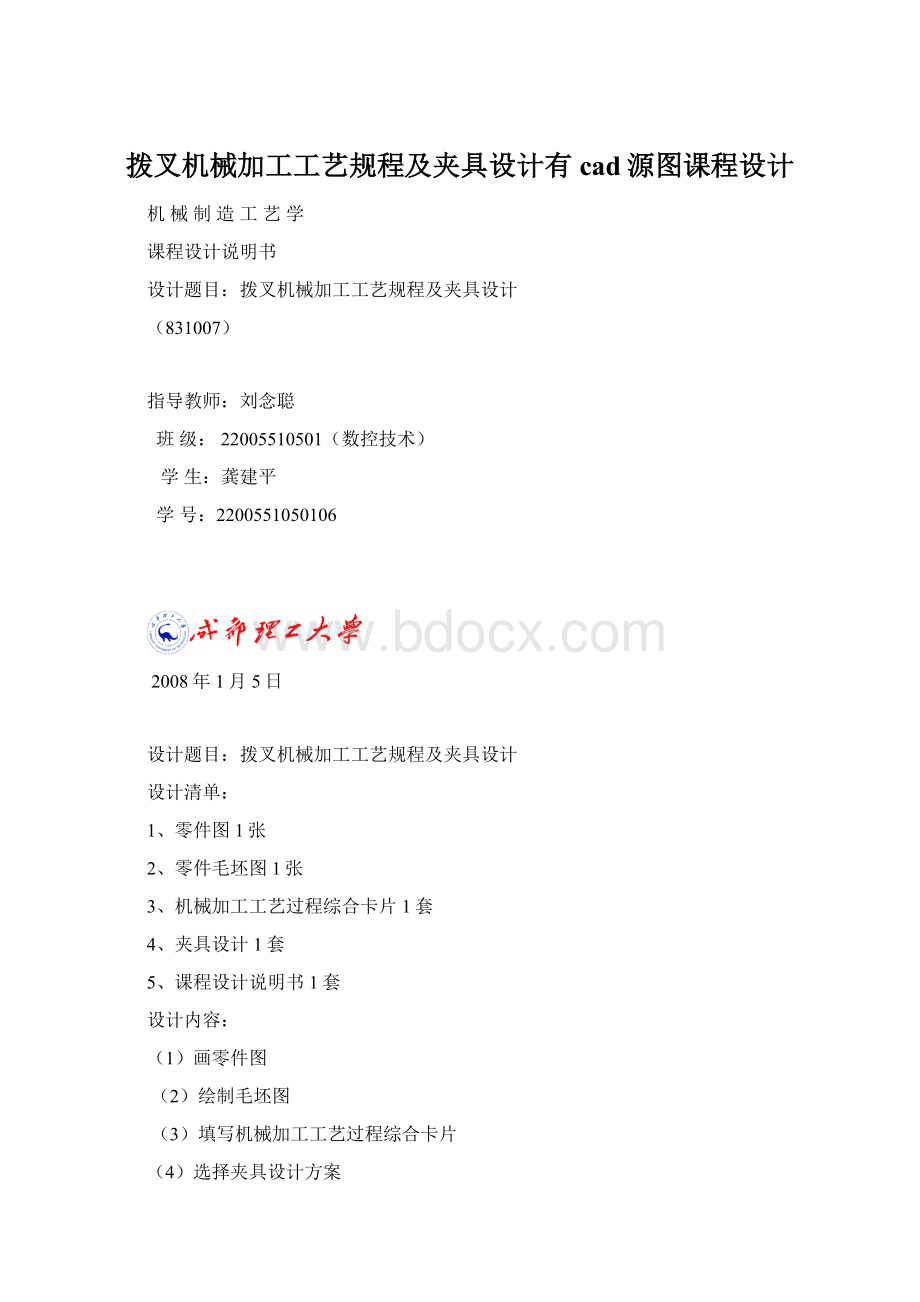
拨叉机械加工工艺规程及夹具设计有cad源图课程设计
机械制造工艺学
课程设计说明书
设计题目:
拨叉机械加工工艺规程及夹具设计
(831007)
指导教师:
刘念聪
班级:
22005510501(数控技术)
学生:
龚建平
学号:
2200551050106
2008年1月5日
设计题目:
拨叉机械加工工艺规程及夹具设计
设计清单:
1、零件图1张
2、零件毛坯图1张
3、机械加工工艺过程综合卡片1套
4、夹具设计1套
5、课程设计说明书1套
设计内容:
(1)画零件图
(2)绘制毛坯图
(3)填写机械加工工艺过程综合卡片
(4)选择夹具设计方案
(5)绘制某一工序夹具草图及零件图
(6)编写课程设计说明书
原始资料:
拨叉零件图831007,生产纲领为100000件/年。
一、分析零件图
(一)零件作用
拨叉是传动系统中用来拨动滑移齿轮,以实现系统调速、转向的零件。
其小头通过与轴的过盈配合来传递凸轮曲线槽传来的运动;大头的内部突起处与滑移齿轮的凹槽配合。
(二)零件的工艺分析
1、零件选用材料为HT200,俗称灰口铸铁。
灰铸铁生产工艺简单,铸造性能优良,但塑性较差,脆性高,不适合磨削。
2、该零件主要加工表面及技术要求分析如下:
(1)、零件上端面及孔φ50H13的上下端面与孔φ22H7的垂直度公差等级为9-10级。
表面粗糙度为Ra≤3.2um。
加工时应以上端面与孔φ22H7的内表面为基准。
又由于上端面须加工,根据“基准先行”的规则,故应先加工上端面,再加工孔φ22H7,最后加工孔φ50H13的上下端面。
(2)、尺寸30、20、65、φ50、φ70都有其公差要求,加工时需要保证这些尺寸。
使其满足30-0.24+0.084、20-0.21-0.07、65-0.190φ500+0.46φ700+0.46。
(3)、φ22H7孔内表面Ra≤1.6,需要进行精铰。
φ70H13孔内表面Ra≤6.3,铣端面时就可以保证。
φ20H13内孔表面Ra≤3.2只需半精镗即可。
(4)、M8的孔只需要钻孔与攻丝,可放在后期工序中。
(5)、φ8锥销孔只要求加工一半,故可以与M8孔同时钻出。
(6)、花键方向保持与图样一致。
两件铸在一起表面应无夹渣、气孔。
根据各加工方法的经济精度及一般机床所能达到的位置精度,该零件没有很难加工的表面尺寸,上述表面的技术要求采用常规加工工艺均可以保证。
二、确定生产类型
已知零件每年的生产量为100,000件,质量为1.0Kg,可确定其生产类型为大批生产。
故初步确定工艺安排的基本倾向为:
加工过程划分阶段;工艺适当集中;加工设备已通用设备为主;大量采用专用工装。
三、确定毛坯
1、确定毛坯种类
根据零件材料确定毛坯为铸件。
并依其结构形状、尺寸大小和生产类型,毛坯的铸造方法选用金属模机械砂型。
根据表15-5铸件尺寸公差等级采用 CT9级。
2、确定铸件余量及形状
根据表15-7,取加工余量为MA-G级。
查表15-8确定各表面的铸件机械加工余量。
铸件的分型面选择及各加工表面铸件机械加工余量见下表:
表面代号
基本尺寸(mm)
加工余量等级
加工余量(mm)
说明
T1
T2
T3
D1
D2
D3
D4
40
70
70
22
50
70
70
H
H
H
H
H
H
H
3.5
3.0
3.0
1.0
3.0
3.0
3.0
顶面,降一级,单侧加工
顶面,单侧加工
底面,单侧加工
孔径过小,保证铸造,余量减小孔,降一级,双侧加工
孔,降一级,单侧加工
孔,降一级,单侧加工
3、画零件毛坯图(图附后)
四、机械加工工艺过程设计
(一)选择定位基准
(1)、选择粗基准为了方便装夹,以及依据以不加工表面为基准和毛坯表面质量较好者为基准的原则,选底端面为粗基准。
(2)、选择精基准依据基准重合原则,应选用统一的基准有利于保证零件的精度。
多用“一面两孔”的定位方式定位,所以选择小头孔轴线和底面为精基准。
(二)制订工艺过程
1、根据各表面加工要求和各种加工方法所能达到的经济精度(查表15-32、15-33、15-34),选择加工方法:
(1)、上端面T1:
粗铣(R6.3)——精铣(R3.2)
(2)、上端面T2:
粗铣(R6.3)——精铣(R3.2)
(3)、底端面T3:
粗铣(R6.3)——精铣(R3.2)
(4)、切断面T4:
粗铣(R6.2)
(5)、小端头孔D1:
扩孔(R6.3、IT10)——铰孔(R1.6、IT7)
(6)、中间孔D2:
粗镗(R6.3)——半精镗(R3.2、IT7)
(7)、中间孔D3:
粗镗(R6.3、IT13)
2、工艺过程的确定:
工序号
工序内容
定位基准
010
020
030
040
050
060
070
080
090
100
110
120
130
140
铸坯
粗铣小头孔的两端
粗铣中间孔上端面
粗铣中间孔下端面
扩两小端头孔
精镗中间孔
精镗小头孔上端面
半精镗中间孔
精铣中间孔上端面
精铣中间孔下端面
精铰两端小头孔
铣断
钻2XΦ8、M8螺纹孔,攻M8螺纹
去毛刺
检验
D1、T5
D1、T1
D1、T1
D2、D5、T5
D1、D5、T5
D1、T5
D1、T5
D1、T5
D1、T1
D2、T5、D5
D1、T5
D1、D2、T5
五、选择加工设备与工艺设备
(一)、选择机床
1、工序010、020、030、060、080、090均为铣端面,可采用立式升降台铣床:
XQ5025A。
2、工序040、100、120均为钻、扩孔工艺,可采用摇臂钻床Z3025B。
3、工序050、070为镗孔,采用T68镗床。
(二)、选择夹具
各工序广泛采用专用夹具。
在钻空M8时,其夹具可采用一面两空定位。
(三)、选择刀具
1、在铣床上加工的工序,均采用硬质合金铣刀即可保证加工质量。
2、加工孔φ22H7时,由于采用扩、铰的加工方案,故工序040可用扩孔刀具一次加工。
而工序100精铰φ22H7,因加工余量小,则选用高速钢铰刀。
3、在镗孔φ50H13时,由于对精度要求不高,故采用硬质合金镗刀即可。
(四)、选择量具
1、对端面的尺寸精度要求不高,采用通用量具即可。
2、对孔φ22H7,为保证加工精度,工序100采用专用塞规进行测量。
为保证30-0.24+0.084、20-0.21-0.07的尺寸精度,采用专用极限量规。
为保证各端面的垂直度,故采用千分表进行检测。
六、确定工序尺寸
(一)、孔类加工工艺尺寸
孔类加工的设计基准与工艺基准重合,尺寸计算简单。
铸造尺寸按要求其公差带对称分布,其余偏差一律按“入体原则”确定(孔类表面为双侧,公差加倍表示)。
圆柱表面工序尺寸及公差:
加工表面
加工内容
加工余量(mm)
精度等级
表面粗糙度Ra(um)
工序尺寸
工序余量
最小
最大
φ22H7
铸件
精铰
扩孔
2
0.2
1.8
CT9
IT7
IT10
1.6
3.2
φ20-+0.8
φ220+0.021
φ210+0.052
0.148
1
1.021
2.652
φ50H13
铸件
粗镗
半精镗
6
4
2
CT9
IT13
IT9
6.3
3.2
φ44-0+1.0
φ480+0.46
φ500+0.074
2.9
1.54
5.6
2.074
φ70H13
铸件
粗镗
6
6
CT9
IT13
6.3
φ64-+1.1
φ700+0.046
4.9
7.146
φ8
铸件
钻孔
精铰
8
7.8
0.2
IT12
IT8
12.5
1.6
φ7.80+0.15
φ80+0.022
7.8
0.05
7.95
0.222
M8
铸件
钻孔
攻丝
8
6.8
1.2
IT13
IT7
12.5
3.2
φ6.80+0.18
φ80+0.012
6.8
0.82
6.98
1.012
(二)、面类加工工序
各端面加工定位基准多次相互转换,使之尺寸及偏差关系复杂,余量核算也较复杂。
现用工序尺寸联系图表法确定其工序尺寸。
1、按规定符号建立工序尺寸联系图。
其中C类尺寸为铸件尺寸,A类为机械加工工序尺寸,B类尺寸为最终保证尺寸。
2、查表确定工序基本余量。
根据手册表15-57取孔上端面粗铣余量为2.2mm,底端面粗铣余量为1.7mm,上端面、底端面精铣余量为0.8mm。
3、由最终工序向前推算工序基本尺寸及毛坯尺寸。
4、查表15-32及表15-33确定工序尺寸的经济加工精度。
5、由各加工方法的经济精度确定工序尺寸偏差。
(a)对直接保证设计尺寸的工艺尺寸,可按设计尺寸偏差要求确定其尺寸偏差。
(b)铸件尺寸按要求其公差带对称分布。
(c)其余独立的中间工艺尺寸按“入体方向”确定偏差。
6、校核设计尺寸。
加工
表面
加工
内容
加工
余量
精度
等级
工序
尺寸
表面粗糙度
工序余量
最小
最大
孔φ22上端面
铸件
3.5
CT9
66.5-+2
精铣
0.8
IT9
630+0.074
3.2
0.726
1.1
粗铣
2.7
IT12
63.80+0.30
6.3
0.4
4.7
孔Φ50上端面
铸件
3
CT9
41-+1.7
精铣
0.8
IT9
380+0.052
3.2
0.748
0.92
粗铣
2.2
IT12
38.80+0.12
6.3
0.38
3.9
孔φ50下端面
铸件
3
CT9
38-+1.7
精铣
0.8
IT9
350+0.052
3.2
0.748
0.92
粗铣
2.2
IT12
35.80+0.12
6.3
0.38
3.9
七、切削用量
工序Ⅰ粗铣小头孔端面,以底面为粗基准
由机械手册可以直接查出铣削速度:
采用立粗齿铣刀,。
则
计算工时
工序Ⅱ粗铣中间孔上端面
由机械手册可以直接查出铣削速度:
采用立粗齿铣刀,。
则
计算工时
工序Ⅲ粗铣中间孔下端面侧
由机械手册可以直接查出铣削速度:
采用错齿三面刃铣刀,。
则
计算工时
工序VI精铣小头孔上端面
由于是精加工铣削速度放大30%,其值:
采用镶齿三面刃铣刀,。
则
计算工时
工序VII半精镗中间的孔
需要镗至φ650+0.074,单边余量,查手册一次镗削余量。
3次镗完
切削速度,进给量
镗一次所以需要工时:
完成整个加工需要的工时就为
八、填写工艺规程卡片
九、夹具的设计
(一)、明确任务,分析资料
1、本夹具设计工序120的钻2-φ8的孔钻、攻丝M8的孔。
本工序要求如下:
(1)、保证图上所标尺寸;
(2)、保证2-φ8、M8孔中心线与孔Φ20H7的中心线在同一平面上。
2、分析资料
(1)、本道工序为后期加工,其他尺寸都已经保证,工件有合适的定位基准;
(2)、本工序加工的要求主要保证位置尺寸,对孔的要求不高;
(3)、大批生产,要求精度不高,所以夹具采用简化结构,降低夹具设计与制造的成本,提高经济效益。
(二)确定结构方案
1、定位方式:
为保证加工时零件的