JBT运输机械用减速器Word文档下载推荐.docx
《JBT运输机械用减速器Word文档下载推荐.docx》由会员分享,可在线阅读,更多相关《JBT运输机械用减速器Word文档下载推荐.docx(9页珍藏版)》请在冰豆网上搜索。
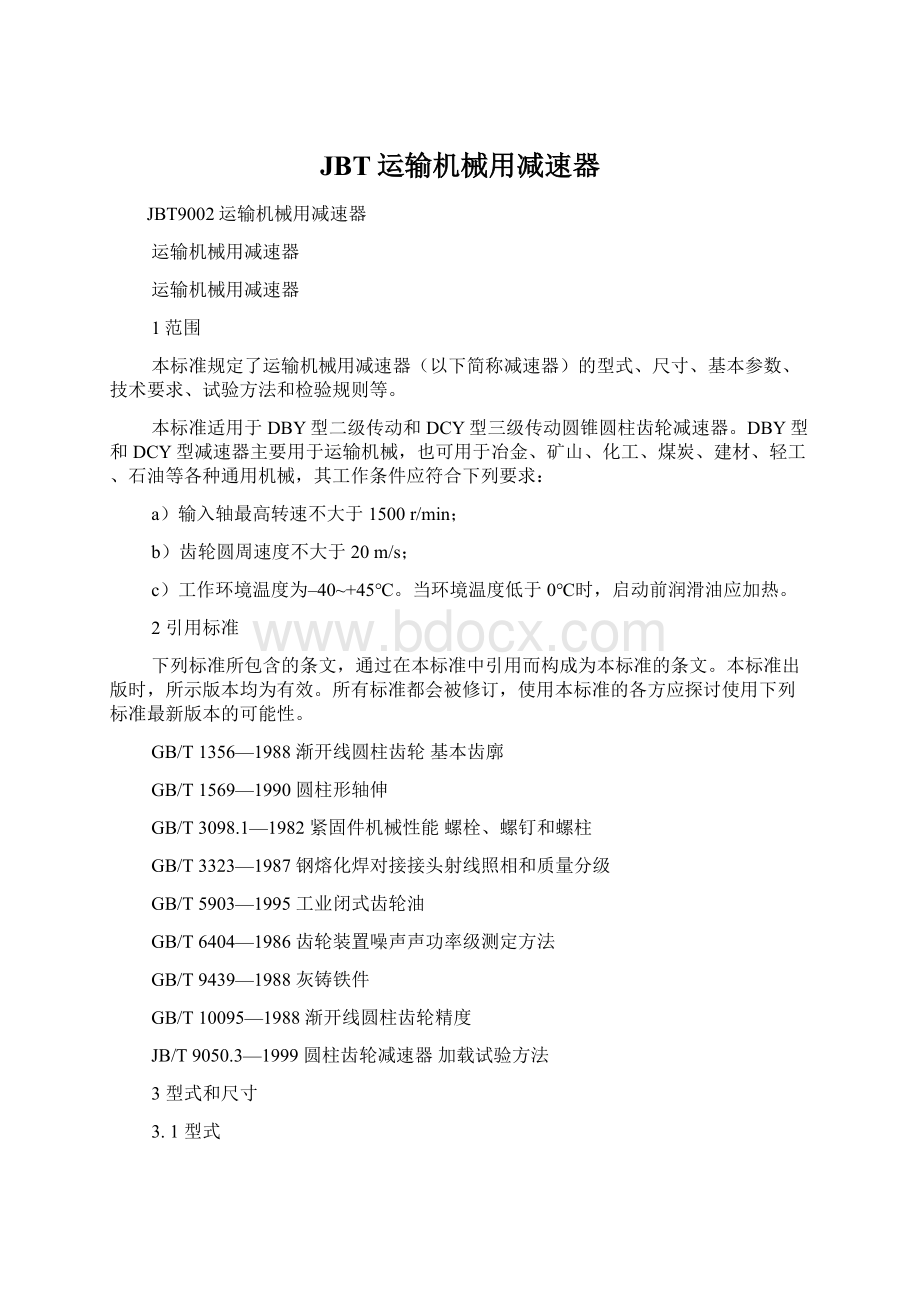
DBY型为二级传动硬齿面齿轮减速器;
DCY型为三级传动硬齿面齿轮减速器。
DBY型和DCY型减速器的第一级传动为圆锥齿轮,第二、第三级传动则为渐开线圆柱斜齿轮。
减速器按出轴形式可分Ⅰ、Ⅱ、Ⅲ、Ⅳ四种装配型式,按旋转方向可分顺时针(S)和逆时针(N)两种方向,见图1,图2。
ⅠⅡⅢⅣ
图1DBY型减速器装配型式
图2DCY型减速器装配型式
3.2外形尺寸
3.2.1DBY型减速器的外形尺寸应符合图3、表1的规定。
3.2.2DCY型减速器的外形尺寸应符合图4、表2的规定。
图3
表1mm
表2mm
图4
3.3减速器的输入轴、输出轴及齿轮轴轴伸尺寸应符合GB/T1569的规定。
3.4型号和标记
标记示例:
名义中心距为280mm,公称传动比为31.5,装配型式为第Ⅲ种,输入轴为顺时针方向旋转的三级传动减速器的标记为:
减速器DCY280–31.5–ⅢSJB/T9002—19994基本参数及承载能力
4.1中心距
4.1.1DBY型减速器的中心距应符合表3的规定,DCY型减速器的中心距应符合表4的规定。
表3mm
表4mm
4.2公称传动比
4.2.1减速器的公称传动比应符合表5的规定。
表5
4.2.2减速器的实际传动比与公称传动比的相对误差:
DBY型减速器不大于4%,DCY型减速器不大于5%。
4.3齿轮模数
4.3.1圆锥齿轮大端模数m为3~15mm。
4.3.2圆柱齿轮模数mn为2.5,2.75,3,3.5,4,4.5,5,5.5,6,7,8,9,10,12,14,16,18,20,22,25mm。
4.4齿轮的基本齿形
4.4.1圆锥齿轮为格里森弧线齿或克林根贝尔格延伸外摆线齿,齿形参数应符合表6的规定。
表6
4.4.2圆柱齿轮基本齿廓应符合GB/T1356的规定。
4.5减速器的承载能力及选用应符合附录A(标准的附录)的规定。
5技术要求
5.1机体和机盖
5.1.1机体和机盖铸铁件应符合GB/T9439中的HT200。
允许采用焊接的机体和机盖,焊接件焊缝应达到GB/T3323中的Ⅰ级焊缝的规定。
5.1.2
机体、机盖合箱后,允许机盖凸缘比机体凸缘宽,每边宽出量应符合表7的规定。
表7mm
5.1.3机体、机盖自由结合时,分合面应密合,用0.05mm的塞尺检查其缝隙,塞尺塞入深度应不超过分合面宽度的1/3。
5.1.4机体、机盖应消除内应力。
5.1.5分合面精加工后,平面度为7级精度,表面粗糙度Ra为3.2μm。
5.1.6轴承孔尺寸公差带为H7,表面粗糙度Ra为3.2μm。
5.1.7轴承孔的圆柱度为7级精度。
5.1.8轴承孔圆柱面与其端面的垂直度为7级精度。
5.1.9轴承孔的中心距极限偏差±
fa应符合表8的规定。
表8
5.1.10轴承孔的中心线平行度公差,在轴承跨距上测量,在水平和垂直方向fx、fy应符合表9的规定。
表9
5.1.11机体、机盖轴承孔中心线应与分合面重合,其偏差应不大于0.3mm。
5.1.12机体不准渗油。
5.1.13机体两垂直孔轴线的垂直度公差δy,在机体孔端面至两轴线交点的距离上测量,见图5,其值按式
(1)进行计算。
图5
δy=E∑?
Bs
·
·
(1)
Rom?
cosδ1
式中:
δy——机体两垂直孔轴线的垂直度公差,μm;
EΣ——齿轮副轴交角极限偏差,见表10;
Bs——机体孔端面至两轴线交点的测量距离,mm;
Rom——中心锥距,mm;
δ1——小齿轮分锥角,(°
)。
表10μm
5.2齿轮、齿轮轴和轴
5.2.1齿轮、齿轮轴采用锻件,材料为20CrMnMo,力学性能应符合表11的规定,允许采用力学性能相当或较高的锻造材料。
不准采用铸造齿轮。
渗碳、淬火齿轮齿面精加工后,有效硬化层深度为0.15~0.25mn,模数较大取较小值,模数较小取较大值。
且齿面不得有裂纹、烧伤等缺陷。
输出轴的材料为42CrMo,力学性能应符合表11的规定,允许采用力学性能相当或较高的材料。
表11
5.2.2渗碳淬火齿轮齿面硬度:
齿轮轴为58~62HRC,齿轮为54~58HRC。
5.2.3齿轮基准孔尺寸公差带及基准孔和齿坯基准端面的形状和位置公差、表面粗糙度应符合表12的规定。
表12
μm
定。
表13
5.2.5齿轮轴和轴的尺寸公差带、形位公差及表面粗糙度应符合表14的规定。
表14
5.2.6齿轮与轴的配合,当公称直径为50~80mm时采用H7/p6,公称直径大于80mm时采用H7/s6。
轴与齿轮配合处的轴颈、轴肩的形位公差、表面粗糙度应符合表15的规定。
表15μm
5.2.7键槽的加工尺寸公差带、形位公差、表面粗糙度应符合表16的规定。
表16μm
5.2.8圆柱齿轮顶圆直径的偏差:
当以齿顶圆作为测量和定位基准时,其偏差应符合表17的规定。
允许在顶圆柱两端面各加工20~30mm宽的定位面,其径向跳动公差应符合表18的规定,其表面粗糙度Ra为1.6μm。
当顶圆不作为测量齿厚的基准时,尺寸偏差为IT11,但不大于0.1mn。
表17
表18
5.2.9圆柱齿轮齿厚公差按GB/T10095的规定。
当分度圆直径d≤125mm时为6JL;
d>125~800mm时为6KM;
d>800mm时为6LN。
5.2.10圆柱齿轮的检验项目组合应符合表19的规定,允许采用等效的其它检验项目组合。
表19
5.2.11圆柱齿轮齿圈径向跳动公差Fr、齿形公差ff、齿距极限偏差±
fpt、基节极限偏差±
fpb及公法线长度变动公差Fw应符合表20的规定。
表20μm
5.2.12圆柱齿轮齿距累积公差Fp或Fpk应符合表21的规定。
表21
5.2.13圆柱齿轮齿向公差Fβ应符合表22的规定。
表22
5.2.14圆柱齿轮齿厚极限偏差Ess、Esi应符合表23的规定。
表23
表23(完)
5.2.15圆柱齿轮公法线平均长度偏差Ewms、Ewmi与公差Twm应符合表24的规定。
表24μm
表24(完)
5.2.16圆锥齿轮精度不低于6级,轮齿工作面表面粗糙度Ra为1.6μm。
5.2.17圆锥齿轮检测项目组合应符合表25的规定。
表25
齿轮副精度包括Ⅰ、Ⅱ、Ⅲ公差组和侧隙四方面要求。
当齿轮副安装在实际装置上时,应检验安装误差项目ΔfAM、Δfa、ΔEΣ。
5.2.18圆锥齿轮的齿距累积公差Fp、Fpk应符合表26的规定。
齿距极限偏差±
fpt、齿形相对误差的公差fc、齿轮副周期误差的公差fz′kc和接触斑点应符合表27的规定。
表26
表27μm
nminnmax计算。
Jnmax=Ess1+Ess2+s1+s2+Es
Δ1+EsΔ2cosα·
(2)
()
Ess——齿厚上偏差(表29);
EsΔ——制造误差的补偿值(表29);
Ts——齿厚公差(表31);
α——齿形角。
表28μm
表29μm
5.2.20圆锥齿轮齿圈跳动公差Fr应符合表30的规定。
齿厚公差Ts应符合表31的规定。
表30μm
表31μm
5.2.21圆锥齿轮齿坯顶锥母线跳动公差和基准端面跳动公差应符合表32的规定,齿坯轮冠距和顶锥角极限偏差应符合表33的规定。
表32μm
表33μm
5.2.22圆柱齿轮和圆锥齿轮齿顶沿齿长方向倒圆为0.1mn(见图6);
齿形端面倒角为0.25mn(见图7),齿轮端面倒角为0.5mn,但最大不超过4mm(见图8)。
图6图7
图8
5.2.23允许按图9要求,对圆柱齿轮副的小齿轮进行齿向修形,修形量计算按式(3)、式(4)。
?
s1=
+2.0
4fHβ0
(3)
2.2mn+Δb/2≥Δb1≤0.1b2+Δb/2·
(4)
Δs1——小齿轮齿向修形量,μm;
fHβ——齿向偏差允许值(见表34),μm;
b1——小齿轮宽,mm;
b2——大齿轮宽,mm;
Δb——大小齿轮宽度差,mm;
Δb1——小齿轮齿向修形长度,mm。
图9
表34μm
5.3装配
5.3.1轴承内圈必须紧贴轴肩或定距环,用0.05mm塞尺检查应不能塞入。
5.3.2圆锥滚子轴承(接触角β=10°
~16°
)的轴向间隙应符合表35的规定。
用手转动轴,轴承运转必须轻快灵活。
表35
5.3.3圆柱齿轮传动的最小法向侧隙应符合表36的规定。
表36
5.3.4齿轮副接触斑点:
圆柱齿轮按高度应不少于50%;
按长度应不少于70%。
齿面两端的倒圆修形区与齿顶修缘区不计入接触区。
5.3.5机体、机盖内表面及其它零件非加工表面应涂防锈漆,外露加工表面涂防锈油脂,内部加工表面涂防锈油。
5.3.6减速器的清洁度:
用200目滤网过滤机体内部润滑油的杂质,滤得的杂质经煤油清洗和烘干后的净重G0,应不大于表37的规定。
表37mg
5.3.7在额定载荷下,减速器的传动效率DBY型不低于96%,DCY型不低于94%。
5.3.8减速器噪声值应符合下列规定:
减速器名义中心距a≤500mm时,噪声(声压)应不大于85dB(A);
名义中心距a>500mm时,噪声(声功率)应不大于图10曲线值。
图10
5.3.9减速器用紧固螺栓的性能等级应符合GB/T3098.1所规定的8.8级。
拧紧力矩应符合表38的规定。
表38
5.4.1减速器一般采用油池润滑,自然冷却。
当减速器工作平衡温度超过90℃或承载功率超过热功率PG1时,可采用循环油润滑,或采用加冷却管的油炉润滑。
当减速器连续停机超过24h后再启动时,应使齿轮和轴承充分润滑正常后方可带负荷运转。
5.4.2减速器润滑油应选用GB/T5903中的L–CKC220、L–CKC320。
5.4.3减速器的油温最高温升应不超过65℃,油池最高油温应不超过90℃。
5.4.4轴承一般采用飞溅润滑,润滑油与齿轮润滑油品相同。
轴承及油池温升应不超过25℃。
6试验方法
6.1减速器的试验按JB/T9050.3的规定进行。
6.2减速器的噪声测量方法按GB/T6404的规定。
7检验规则
7.1出厂检验
7.1.1减速器须经制造厂质量检验部门检验合格后方能出厂,出厂时必须附有产品质量合格证明文件。
7.1.2出厂检验项目包括:
a)型式、外形尺寸及油漆外观质量;
b)噪声、温升、空载三项试验;
c)齿轮精度;
d)清洁度。
7.2减速器的型式检验
7.2.1凡属下列情况之一时,应进行型式检验:
a)试制的新产品(包括老产品转厂);
b)当产品在设计、工艺、材料等方面有较大改变足以影响产品性能时;
c)停产2年后,再恢复生产时;
d)成批大量生产的产品,每3年进行一次;
e)国家质量监督部门提出进行型式检验的要求时。
7.2.2型式检验的减速器数量,每次不少于二台(其中一台作陪试件)。
7.2.3减速器型式检验项目:
a)全部出厂检验项目;
b)负载试验;
c)超载试验;
d)疲劳寿命试验。
7.2.4减速器型式检验项目符合要求时为合格。
如被检验项目有一项不合格时,则应对此项目加倍抽试,如仍不合格,则该批产品型式检验为不合格。
8标志、包装、运输及贮存
8.1减速器应在明显位置固定产品标牌,标牌内容应包括:
a)产品名称和型号;
b)输入功率;
c)输入转速;
d)公称传动比;
e)制造厂名、出厂日期;
f)出厂编号。
8.2减速器轴伸与键应涂防锈油脂,并用塑料布包严并捆扎结实。
齿轮、轴、轴承应涂润滑油脂。
8.3减速器应垫稳,固定于有防水石油沥青油毡的包装箱内或装于底脚板下。
8.4在运输吊装过程中,应平稳起升、缓放,保证产品不受损伤。
8.5运输和贮存时应注意防水、防潮。
8.6随机文件应齐全,每台减速器均应随机附带产品出厂合格证明书、产品使用说明书和装箱单。
9制造质量保证及可靠性指标
9.1在用户遵守本标准及有关文件规定的运输、保管、安装和使用条件下,减速器自发货之日起1年内,如因制造质量问题发生损坏,或不能正常工作时,制造厂应无偿为用户修理或更换。
9.2在正常使用条件下,减速器的平均使用寿命不少于10年。