培训资料新型Assel轧管机docxWord文档下载推荐.docx
《培训资料新型Assel轧管机docxWord文档下载推荐.docx》由会员分享,可在线阅读,更多相关《培训资料新型Assel轧管机docxWord文档下载推荐.docx(46页珍藏版)》请在冰豆网上搜索。
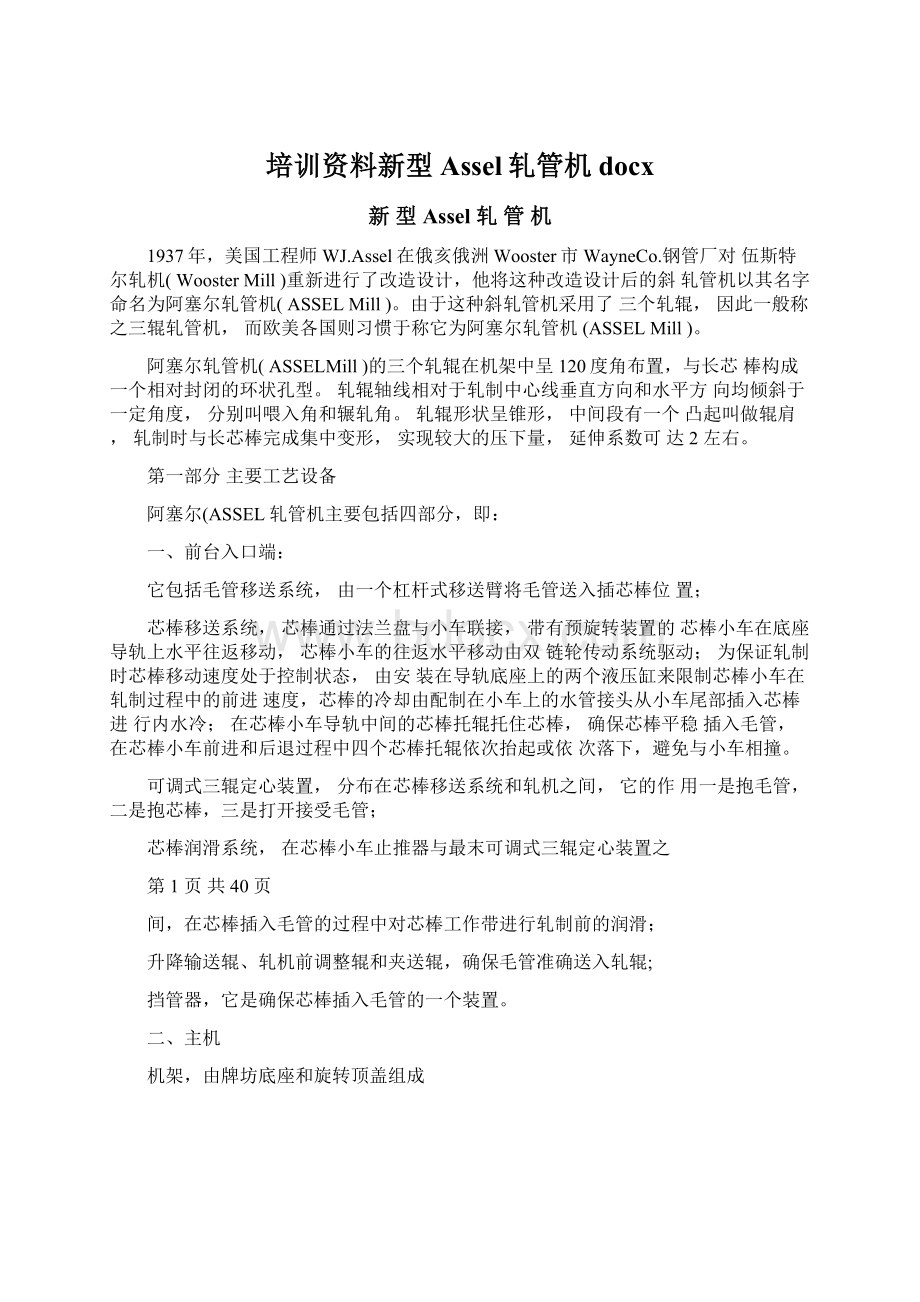
压下丝杠完成的,它们可单独操作,也可以同时操作,当两个压下丝杠进行反向运动时,可调整轧辊的辗轧角,确定辗轧角后,两个丝杠同时压下或抬起可调整轧辊的孔喉尺寸。
在两个压下丝杠之间,机架内有一个液压缸与轧辊座连接,它的作用是保持辊箱的稳定,避免压下丝杠端部与转鼓之间产生间隙。
轧辊座安装在转鼓内,当调整前进角时,转鼓就由一个主轴传动系统旋转到适当角度。
每个转鼓都有一个独立的传动系统,前进角从0°
〜12°
范围内无级可调,每个转鼓都有两个液压夹紧缸锁紧。
在出料侧的压下螺丝、轧辊调整装置和轧辊轴承座之间,安装了一个液压快开装置,它的作用时在轧制快结束时投入工作。
它用一个连接环限制行程并满足运行要求,当活塞向内运动时,轧辊提起,以实现对毛管尾部的物压下轧制,以此防止毛管尾端形成三角形喇叭口。
整个牌坊机架放置在紧固于基础上的两个底板上。
三、后台出口端;
为防止荒管表面划伤和薄壁管发生表面扭曲现象,在轧机出口处
装有一个辊式导向装置,它同两条与轧制方向平行排列的长驱动辊相连,长驱动辊以均匀的转速导卫钢管前进,当轧制结束时,上导辊抬起,两个下导辊之间的输送辊抬起,夹送辊压下,通过输送辊驱动将荒管送往后面的输送辊道。
长驱动辊底座根据荒管直径的不同可整体上下调整中心线。
四、传动系统;
每个轧辊均有独立的传动系统,由万向接轴,减速机和电机组成,轧机采用后台传动方式。
第二部分主要调整参数
基本概念(均以上辊为例)喂入角:
轧辊轴线和轧制线分别在水平面上进行投影,它们的投影线之间的夹角称为喂入角(feedangle前进角、送进角、)
辗轧角:
轧辊轴线和轧制线分别在垂直平面上进行投影,它们的投影线之间的夹角称为辗轧角(spreadangle)
一、轧辊喉径和辗轧角的调整
Assel轧机的三个工作辊在轧机机架里成120°
布置,轧辊安装在轧辊座上,轧辊座安装在转鼓里。
每个转鼓都由两个压下丝杠调整,一个在入口侧,一个在出口侧,两个压下丝杠可分别单独调整,以得到适合的“轧辊喉径”和“辗轧角”。
1、辗轧角设定
以轧辊座的底面作为测量表面,当这表面与轧制中心线平行时,辗轧角为零。
在机架牌坊的出、入口设有测量点,三个转鼓共有6个测量点,测出的数据存入计算机。
当轧辊座上两块止推板到轧制中心距离相等时,辗轧角为5°
2、辗轧角和轧辊喉径的调整
辗轧角的调整:
辗轧角(B)调整时,轧机出口和入口侧的压下丝杠做反向调整,以出口打
开,入口压下为正调整(辗轧角增加)。
出口丝杠行程=标准行程+轧辊半径*(1-cos(B-5))+350*tan(B-5)入口丝杠行程=标准行程一轧辊半径*(1-cos(B-5))+350*tan(B-5)轧辊喉径的调整:
在Assel孔型中安装测量棒(©
159),同时在轧机出口和入口分别安装测量架。
将轧辊座上出口和入口的测量栓与测量架上的测量栓分别对正。
此时的辗轧角为5°
,测量棒与测量架拆除后,压下丝杠做同向同步调整就相应的改变轧辊喉径。
调整后喉径=原喉径+2*丝杠调整距离
轧辊中心与轧制中心的距离=(轧辊直径+轧辊喉径)/2
当轧辊直径改变时,需重新在计算机中输入轧辊直径
通常情况下,辗轧角和轧辊喉径的设定和调整通过计算机控制完成。
二、喂入角的设定和调整
Assel轧机的轧辊安装在三个转鼓里,通过对转鼓的旋转调节,可以得到某
一喂入角
轧辊的0°
喂入角,对应于轧辊的拆装位置,轧机的喂入角0~12°
可调
//'
X7
图中给出的是上辊喂入角的调节方式,在Assel轧机上,上辊(1#辊)和左
辊(3#辊)的喂入角调节行程是一致的,而右辊(2#辊)由于调节装置安装方向与前两个辊相反,因此它的调节行程与另两个辊不同。
第三部分Assel轧管机的工作程序
一、前台
穿孔后的毛管通过横移车移送至Assel轧机前台,然后由毛管移送臂将毛管送入轧机入口侧辊道上,移送臂回到原位。
辊道输送毛管至挡板前,定心辊抱住毛管,停在等待芯棒插入的位置上。
芯棒在辊子的支撑下,由原始位置通过芯棒小车的驱动高速插入毛管中
(1.5m/s)。
芯棒的工作段在穿过石墨润滑箱时被喷上石墨润滑剂。
芯棒的支撑辊随着芯棒小车的前进逐个落下。
芯棒到达插入位置后,挡板升起,夹送辊落下,输送辊道启动,毛管和芯棒同步前进。
芯棒在到达工作位置之前,由芯棒小车上的带有超越离合器的辅助驱动装置进行预旋转,带动毛管旋转进入AsseL轧机的工作辊中。
在芯棒到达工作位置之前,芯棒小车与限动梁联锁。
限动梁开始控制芯棒的前进速度
(0.07~0.2m/9,使芯棒的前进速度低于钢管的前进速度。
随着毛管被Assel轧
辊咬入,入口侧输送辊道全部集体落下至低位。
随着轧制过程中钢管不断地旋转前进,钢管尾部每离开一架三辊定心,该架三辊定心从原来的抱毛管位,变为抱芯棒位。
在轧制结束后,前台输送辊升起至托芯棒位,三辊定心集体打开至低位,芯棒小车高速退回原始位置(4m/s),限动梁在液压缸的带动下退回原位。
在芯棒小车回退过程中,芯棒托辊逐架抬起,托住芯棒。
芯棒的工作段通过石墨润滑箱时被喷上石墨润滑剂。
轧辊在开始咬入前处于低速旋转,当毛管随芯棒进入轧辊后开始一次咬入,在此时毛管只在直径上受到压缩,随着钢管前进,在轧辊的台肩开始毛管内表面接触芯棒表面进行减壁,实现二次咬入。
正常咬入后轧辊转速提高到设定的轧制速度,进行高速轧制。
在轧制结束后轧辊转速降回低速。
通常咬入速度是轧制速度的70%
在生产薄壁管时,为防止荒管前端产生喇叭形扩口,在毛管被轧辊咬入前,上轧辊的辊缝预先设定在比正常轧制辊缝稍大的位置,当毛管头部通过轧辊的台肩后,上轧辊快速恢复到正常轧制位置,我们把轧辊的这个动作叫做“快关”。
同样是在轧制薄壁管时,为了防止钢管尾部形成三角形而造成的轧卡,在钢管尾端通过轧辊台肩之前,上轧辊的辊缝被打开到一个较大的位置,对钢管尾部不减壁,从而避免了尾三角的形成。
通常情况下,当Assel轧后荒管径壁比(D/S)>12时,采用快开动作,当径壁比〉16时,使用快关动作。
三、后台
在开始轧制时,由于芯棒端部首先伸出轧机进入后台,离轧机最近的双导辊
首先托住芯棒端部,随着荒管从轧机中轧出,双导辊变换至托荒管位
在轧制开始时,后台的长导辊处于高速转动状态,它的旋转方向与轧辊旋转方向一致,长导辊辊面线速度与荒管的表面线速度保持一致。
当荒管进入双导辊时,导辊的辊面与荒管的表面几乎不产生滑动摩擦,一方面避免了对荒管表面的划伤,另一方面由于长导辊几乎对荒管的旋转不产生阻力,也避免了荒管的扭转。
荒管进入长导辊后,首先是两个连在一起的上导辊从打开位压下至抱荒管位,随着荒管的不断前进,后台的上导辊逐架由打开位压下至抱荒管位。
当荒管尾部离开轧机,轧制结束时,长导辊立即从高速转动降低到一个很低的转速,在长导辊最前端的两个连在一起的上导辊此时有一个抱紧荒管的动作,确保在抽芯棒时,荒管不会被芯棒带回轧机。
芯棒从荒管中抽出后,后台全部上导辊打开,长导辊中间的输送辊升起,后台的夹送辊压下,共同将荒管输送出长导辊,在长导辊后的三个固定输送辊继续将荒管输送至定径前升降辊道。
第三部分Assel轧机的变形过程
Assel轧机的变形区是由三个相同的轧辊和芯棒组成的,三个轧辊同向旋转。
轧机中心线和轧制线一致,从轧制线到三个轧辊的距离相等,一般在生产壁厚较大的钢管时采用回退式轧制方式,主要是厚壁管的脱棒间隙较小,不便于抽棒。
通常情况下均采用限动轧制方式进行轧制。
Assel轧管变形区横截面
Assel轧机的变形过程与二辊斜轧延伸机相类似,轧辊辊型也由咬入区(入口椎)、脊部(台肩)、均整区和出口区组成。
脊部均整区
咬入区\/出口区
毛管被轧辊一次咬入后,进入入口锥,入口锥角一般约为2.5~3°
,由于毛
管内径大于芯棒直径,首先进行减径,当直径上的压下量等于毛管内径与芯棒的间隙值(插棒间隙)时,毛管内表面开始接触芯棒表面,此时一次咬如阶段结束。
由于辊面台肩急剧压下,而钢管内壁受到芯棒的限制因此开始减壁,进入二次咬入阶段。
一次咬入主要是减径区,该区的主要作用是建立足够的曳如入力,以克服来自轧辊脊部(台肩)的轴向阻力,实现二次咬入。
有时为了实现二次咬入,在入口锥提前减壁。
一般在入口锥的壁厚压下量等于(0.18~0.25)Hs,Hs为台
肩高度。
毛管到达台肩时,壁厚有较大的压下量,钢管的延伸变形主要集中在台肩完成。
因为钢管的内径保持不便(减壁变形时钢管内径就等于芯棒直径),这时的
壁厚压下量就等于直径压下量的一半。
毛管通过台肩后进入均整区,均整区的辊面在辗轧角为5°
的情况下是与轧制制线平行的,因此该区的变形量很小,该区的作用是辗轧壁厚,进行定壁。
最后钢管经出口锥归圆轧出。
Assel轧管机在轧制过程中,钢管横截面的变化是从圆到圆三角形,最后再归圆的过程。
出口变形区内入口
由于变形区不是完全封闭的,有较大的辊缝存在。
在轧制进行到钢管的尾端时,金属容易被挤入辊缝而形成尾三角,尾三角会卡在轧辊缝隙中造成后卡。
通常采用在轧辊出口设置快开装置,提前放大轧辊与芯棒的距离,对钢管尾部不减壁的方法解决尾三角后卡的问题。
采用快开方式在一定程度上解决了Assel轧制薄壁管时的后卡,但是如果轧机快开的控制不准确,往往造成钢管尾端增厚段过长,最终造成钢耗过大。
第四部分Assel轧管机的液压快开装置
一、设置快开装置的目的
在Assel轧管机上辊转鼓的出口侧装有一个液压快开装置,它可以在轧制薄
壁钢管的头部和尾部时进行动作,避免Assel轧机在轧制薄壁钢管时的头部喇叭口缺陷和尾部三角形缺陷。
控制头部喇叭口的目的是为了给生产线上的下一道工序提供更稳定优质的原料;
控制尾部三角的目的是防止轧机本身发生轧卡。
二、快开装置的动作过程以及控制方法
快开液压缸的基本位置是满冲程,即液压缸伸出最大行程。
该装置的动作分为“快关”和“快开”两种方式。
在该液压缸内装有位置检测元件,可以对液压缸的动作行程进行设定。
1、“快关”
当采用“快关”方式进行动作时,在轧机开始轧制前,液压缸回收一定的行
程,由于该液压缸的上部顶住了轧机上辊出口侧的压下丝杠,下部顶住上轧辊座
的出口侧,它回收了一定的行程,而轧辊座的入口仍保持在原压下位置,上轧辊座在上辊平衡液压缸的拉动下,带着上轧辊,以轧辊座入口的固定点为旋转中心,向上旋转一定的角度。
由于轧辊向上抬起,造成辊面与芯棒之间的距离加大,当毛管头部在此处通过时,可以减少轧辊对毛管壁厚的压下,由于壁厚压下量的减小从而减小了钢管的横变形,因此可以减轻甚至消除Assel轧管薄壁管生产时的喇叭口现象。
在毛管头部通过轧辊台肩后,为了保证钢管管体的壁厚精度,上轧辊需要迅速恢复正常轧制位置,快开液压缸应立即恢复满行程的工作位置。
但是由于此时的轧辊压下正处于钢管轧制过程中,属于带钢压下,需要的压力很大,同时压下动作要求在极短的时间内完成(约0.3秒)。
为此在原有的快开液压缸外设置了一增压缸来保证“快关”动作的及时和准确。
2、“快关”动作的局限性
由于“快关”动作需要在毛管咬入前打开轧辊距离,但是为了保证毛管顺利进行一次咬入,轧辊距离不能打开过大(如果快关动作打开的轧辊距离过大,会造成轧机入口的辊距增大,将难以实现毛管的一次咬如)。
因此“快关”动作对毛管头部减比壁量的影响是有限的,最终对薄壁管喇叭口缺陷的改善能力也受到限制。
Meer公司推
为了弥补“快关”动作消除薄壁管头部喇叭口能力上的不足,
荐使用阶梯芯棒配合“快关”动作共同完成对“喇叭口”的消除
3、“快开”
“快开”动作应用于薄壁管轧制的最终阶段。
在快开动作前,液压缸一直处于满行程的基本位置。
在毛管尾部进入轧辊台肩进行减壁变形之前的一个很短的时间内,快开液压缸卸压,依靠钢管对上轧辊的反作用力,以及上辊平衡缸的拉力,将上辊打开一定的距离,从而不对毛管的尾部减壁,减少钢管尾部的横变形,避免尾三角的产生。
由于是在轧制过程的最终阶段进行“快开”动作,不需要考虑钢管的一次咬入问题,因此可以采用尽量大的快开行程打开辊距,所以快开动作对尾三角的解决效果应该是能够令人满意的。
4、“快关”、“快开”动作的控制方式
在Assel主机的一侧,装有两个热金属检测器,分别为HMD1和HMD2,其中的HMD1负责在开始轧制时检测毛管头部的位置,控制“快关”动作的实现,HMD2负责在结束前检测毛管尾部的位置,控制“快开”动作的实现。
由于在钢管轧制过程中,轧机的冷却水会产生较大的雾气,因此HMD1和HMD2均
具有抗雾气干扰能力,从而保证检测信号的准确性。
第五部分轧制工具
Assel轧管机的主要轧制工具包括轧辊和芯棒。
1、轧辊
共有三个轧辊,在机架上间隔120°
角布置。
轧辊轴线与轧制线在不同平面上的投影分别形成辗轧角和喂入角。
轧辊总体呈锥形,入口辊径小,出口辊径大。
在轧辊的中部有一个突起,叫做轧辊台肩(hump)。
台肩的作用是对钢管进行集中减壁。
轧机上安装的三个轧辊应成套配置,确保每一套三个轧辊的辊型和辊径一致,要求轧辊装配精确,避免轧辊轴向窜动,确保三个轧辊的台肩在变形区内保持在同一垂直平面内。
要求三个轧辊的化学成分和表面硬度应均匀一致,避免在
轧辊使用过程中由于三个轧辊磨损程度不一致而带来的产品缺陷。
2、轧辊的更换
传统的Assel轧管机,在更换轧辊过程中需要反复打开机架上盖(三次),然后将三个轧辊分别由天车吊走和吊入。
新型Assel轧管机采用了三辊集中更换的新技术。
只需要在换辊前将轧辊调整到规定的换辊位置,打开机架上盖后,三个
轧辊同时由天车吊走,三个新辊同时吊入。
在一次换辊过程中只需要打开一次机架上盖可以节省换辊时间,提高轧机工作效率。
集中换辊吊运装置
3.芯棒
在轧制过程中,芯棒与轧辊共同完成对钢管的减壁和均壁工作,因此要求芯
棒具有很好的高温耐磨性能,具有精确的直径、良好的平直度和同心度,以及光
滑的表面。
第六部分Assel轧机工艺参数
阿塞尔轧管机的主要作用是把穿孔毛管的壁厚进行碾轧减薄延伸,因此在轧管过程中涉及到的主要工艺参数有变形参数、速度参数和温度参数。
变形参数:
毛管尺寸、荒管尺寸、延伸系数、辗轧角、孔喉直径和芯棒直径、插棒间隙、脱棒间隙等。
速度参数:
喂入角、轧辊转数、芯棒限动速度等。
温度参数:
轧制温度等
通常Assel轧机在设定工艺参数前,首先要确定下一道工序(定径)所要求的原料规格,即本机组应轧出的荒管尺寸,根据荒管规格以及工具准备情况确定本机组所需的毛管规格。
孔喉直径与芯棒直径配合保证荒管的壁厚辗轧角:
根据轧辊辊面锥角确定,本轧机为5°
,辗轧角调整出现偏差可造成钢管壁厚不均、内螺纹等缺陷。
喂入角:
0~12°
可调,喂入角加大,轧制出口速度加快,扩径值增加,但是随着喂入角的增大,轧制稳定性降低,壁厚不均呈增大趋势,容易产生内螺纹。
因此应在生产厚壁管时采用较大的喂入角,薄壁管生产采用较小的喂入角。
但是在生产薄壁管时喂入角也不宜过小,因为喂入角过小,轧制速度慢,尤其是薄壁管时,轧制时间过长容易造成钢管头尾温差加大,形成在钢管长度方向上的壁厚不均。
插棒间隙:
需要扩径轧制时,采用小插棒间隙。
需要缩径轧制时,采用大插棒间隙。
插棒间隙过大容易造成轧辊开口度不足,咬入困难,并且对钢管的内外表面质量会带来不利影响。
插帮间隙过小容易造成插棒困难,甚至包芯棒。
轧辊转数:
轧辊转数对钢管的影响与喂入角的影响一致。
考虑到轧机力能参数的情况下,在轧制高强度、难变形金属时,应采用较低的轧辊转数或较小的喂入角。
芯棒限动速度:
芯棒限动速度过慢,会造成芯棒工作段的磨损集中在一个较
短的范围内,会时芯棒表面质量恶化,影响钢管内表面质量,同时也会增加芯棒的消耗量
第七部分
三套轧管的新型Assel轧管机采用了多项当代最新技术,具备了产品范围宽、壁厚精度高、规格变换灵活的特点。
但是从综合的角度看,这套轧机最适宜生产的产品还是中厚壁管,因此我们在未来的生产中应充分发挥Assel轧管机的强项,在产品结构上与钢管公司原有一套、二套形成优势互补,为钢管公司早日实现“三个三百”的目标做出贡献。
工业炉
第一节简述
环形加热炉是目前世界上用于加热圆管坯的最理想的工业炉炉型。
环形加热炉在钢管生产线中的作用是根据不同钢管的品种材质,将合格的定尺管坯由常温(20C)加热到所需要
的轧制温度,以供穿孔及轧制。
此炉型的特点是炉底呈环形,在炉底驱动装置的作用下承载管坯由入料区旋转至出料区,再由出料机将加热好的管坯从出料炉门取出。
在管坯随炉底运动过程中被设置在炉墙、炉顶等处的烧嘴加热、均热达到合格的出料温度。
为了达到理想的加热质量,从热工控制上将炉子从圆周方向上分成若干控制区,依次形成预热、加热、均热等区,各区亦可再分若干控制区以提高控制精度,我厂环形炉就分成6
个控制区,预热区(0区)、加热区(1区-3区)、均热区(4区)出料区(5区)。
各控制区按不同的温度进行控制,实现对管坯的合理加热,达到要求的加热质量。
加热及均热区的基本加热设备是烧嘴,烧嘴将助燃空气、燃料按合理的比例(空燃比)混合燃烧形成火焰加热管坯。
其中燃料由管道系统供送,助燃空气是由鼓风机(助燃风机)经由换热器加热,再由空气管道分配至各区烧嘴参与燃烧。
而温度的调节由自动化控制系统通过调节管道上的阀门开度实现燃料及配风的流量来实现。
燃料燃烧产生的烟气通过烟囱排入大气。
炉底、炉墙、烟道、烟囱等是由耐火材料砌筑而成的,以达到保温节能的效果。
与其它的炉型相比,环形炉具有以下优点:
★环形炉最适合加热圆管坯,并能适应各种不同直径和长度的复杂坯料组成,易于按管坯规格的变化调整加热制度。
★管坯在炉底上间隔放置,坯料能三面受热,加热时间短,温度均匀,加热质量好。
★管坯在加热过程中随炉底一起转动,与炉底之间没有相对运动和摩擦,氧化铁皮不易脱落。
炉子除装出料门外无其它开口,严密性好,冷空气吸入少,因而氧化烧损较少。
★炉内管坯可以出空,也可以留出不装料的空炉底段,便于更换管坯规格,操作调度灵活。
★装料、出料和炉内运转都能自动运行,操作的机械化和自动化程度高。
环形炉的缺点是:
炉子是圆形的,占用车间面积较大,平面布置上比较困难;
管坯在炉底上呈辐射状间隔布料,炉底面积的利用较差,单位炉底面积的产量较低。
我厂环形炉,中径21m,年加热管坯量约为13.5万吨,造价近3000万人民币。
第二节炉子结构及辅助设备
1.结构概述:
环形炉由转动的炉底和固定的炉墙、炉顶组成。
管坯运动方向
外环炉墙
内环炉墙炉内隔墙
烟气流动方向
旋转炉底
环形炉运转示意图
管坯由装料机A送入炉底上,随炉底一起转动,在转动过程中,被安装在环形炉内外墙上的烧嘴和炉顶的烧嘴加热,转动一圈后,由出料机B将被加热好的管坯取出。
环形炉炉内烟气按照与炉底转动相反的方向流动,加热管坯后废气经由装料端内环侧墙上的排烟口排除
炉外。
2.基本参数
2.1炉子基本尺寸
2.1.1
炉底中心平均直径:
21.000m
2.1.2
炉膛内部宽度:
4.67m
2.1.3
炉底有效宽度:
4.188m
2.1.4
炉膛高度:
1.800m
2.1.5
装出料机夹角:
18o(8个料位)
22加热能力:
2.2.1设计32吨/小时
2.2.2最大45吨/小时
2.3管坯规格及布料方式:
2.3.1管坯规格:
直径(mr)(130)、150、200、(210)
长度(mr)1000〜4000
2.3.2管坯材质:
低合金钢、合金钢、碳素钢
2.3.3布料角度:
2.25°
2.3.4炉内有效料位:
152支
2.3.5布料方式:
单排、交错
2.3.5
各区料位数
:
0区(预热区):
36
位
1
区(加热一区):
32
2
区(加热二区):
24
3
区(加热三区):
4
区(均热区):
28
5
区(出料区):
8
共计:
160
2.3.6
管坯加热温度:
1280C
2.3.7
允许温差:
±
10C
2.4
燃