浅谈模具精加工改进001Word格式文档下载.docx
《浅谈模具精加工改进001Word格式文档下载.docx》由会员分享,可在线阅读,更多相关《浅谈模具精加工改进001Word格式文档下载.docx(15页珍藏版)》请在冰豆网上搜索。
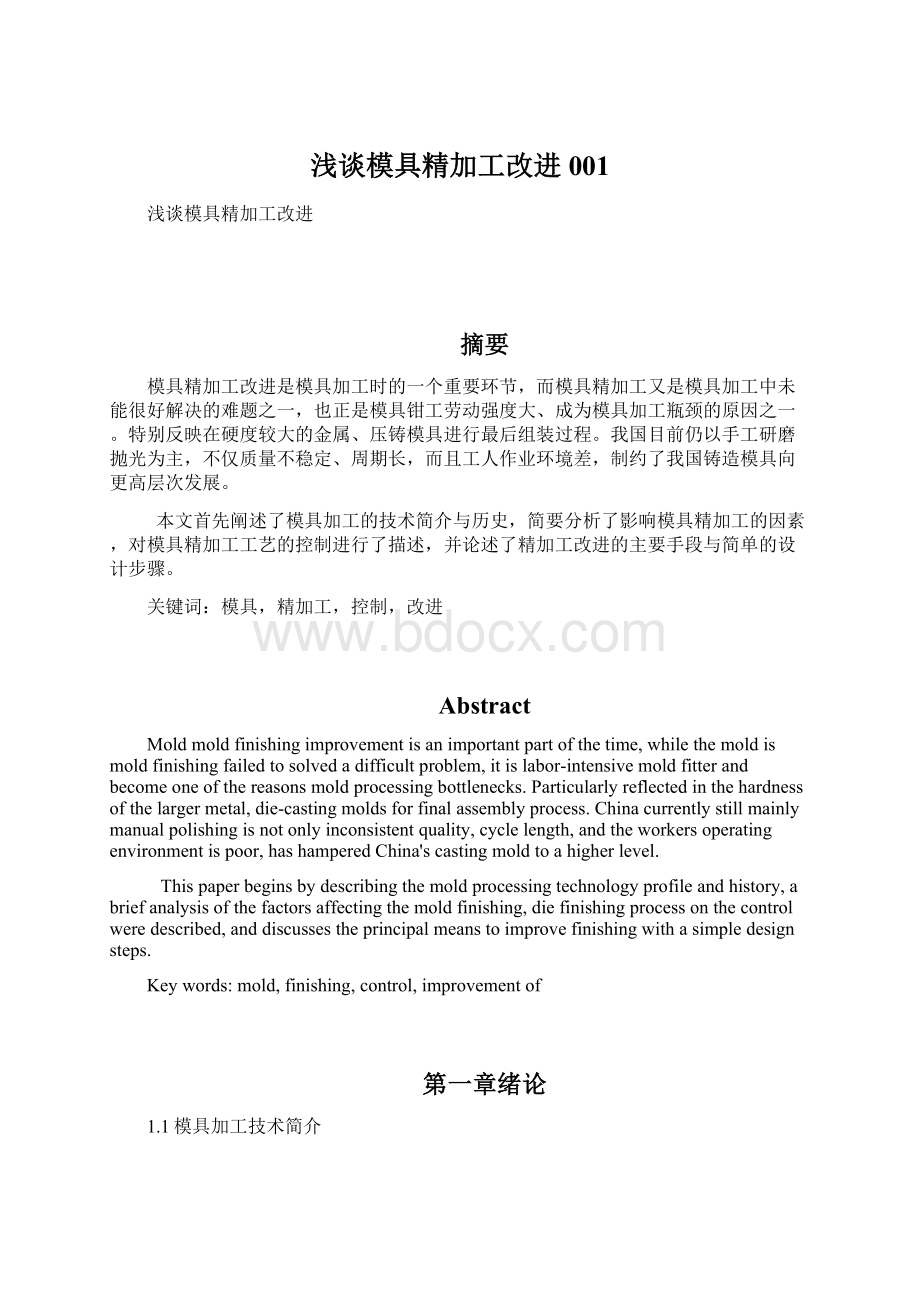
传统精加工技术主要是以手工研磨抛光为主和现在发展起来的机械精加工;
非传统精加工主要包括化学抛光、电化学抛光、电解研磨、电化学机械光整加工、超声波加工、磁流变抛光、激光抛光技术以及电火花抛光等。
1.2模具加工的历史
我国模具工业起步较晚,基础薄弱,长期以来模具制造一直作为保证企业产品生产的手段被视为生产后方,因此发展缓慢。
1987年模具首次被列入机电产品目录,当时全国共有模具生产厂点约6000家,总产值约30亿元。
随着我国改革开放的日益深化,市场经济进程的加快,独立于产品制造企业的模具及其标准件、配套件企业大量出现,模具产业得到快速发展,在市场竞争中,模具企业生产技术不断提高和规模不断扩大,模具行业得到很快发展。
目前,我国模具产值已排名世界第三,2003年达到450亿元。
1988年,由原国家经贸委下达计划,由机械部和中国模具工业协会实施,在全国范围内组织了上百个模具企业和有关科研单位、大专院校,共同进行模具技术攻关,取得了丰硕成果。
这些成果主要有:
冲压模具的设计制造技术、塑料模具的设计制造技术、铸压模具的设计制造技术、锻造模具的设计制造技术、模具表面处理技术、模具材料、模具计算机辅助设计与制造技术、模具标准件、模具加工关键设备、模具寿命研究等方面。
由于这些成果的取得及推广应用,使我国模具技术前进了一大步。
“七五”后期和“八五”期间,国家对模具工业加大了投入,分批分期改造了一批具有特色专长的专业模具厂和模具标准件厂,引进了一大批模具加工关键设备及精密塑料模、级进模、精冲模等设计制造技术,对提高我国模具生产技术水平起到了推动作用。
同时,许多大专院校开始设立模具专业,由前联邦德国、日本援建及我国自己投资兴办的模具技术培训中心也陆续建立,模具技术人员及技术工人的培养开始步入轨道。
1989年3月,国务院颁布了《关于当前产业政策要点的决定》,在机械工业中,模具被列为技术改造序列的第一位,极大地促进了模具技术的发展。
1989年,经国家计委批准,在华中理工大学成立“塑性成形模拟及模具技术国家重点实验室”,其主要研究方向为模具和新型模具材料。
“八五”期间,国家对模具技术的发展主要是对“重点企业技术开发项目”进行支持。
“精密多工位级进模”、“大型复杂锻造模、压铸型”和“塑料注射模具设计制造技术”三个项目被列入“大型精密模具设计制造技术”国家重点项目,都通过了鉴定,达到了目标,使我国模具设计制造技术又前进了一大步。
第二章影响模具精加工工艺的因素
2.1数控编程工序
数控编程一般可分为4个阶段:
准备工作阶段、技术方案阶段、数控编程阶段和程序定型阶段。
1.准备工作阶段:
根据生产任务书,按要求接收技术数据,检查数据的准确性、时效性。
明确生产计划,能否按时完成。
2.技术方案阶段:
数控编程前的首要工作是制定技术方案。
公司把数控工艺和刀路程序设计合并由程序设计员一人负责。
技术方案阶段主要任务是根据车间的制造资源,编制数控加工的工艺方案。
为了做好技术方案,必须了解加工环境和制造资源,包括:
机床、刀具、夹具、软件、工艺资源、毛坯(如毛料、锻件、铸件、热处理、切削性能、预加工)等,还要对零件的技术要求弄清楚,如公差要求、光洁度、薄壁件的允许变形、装配关系等。
数控工艺方案的设计是有难度的,因为要处理的信息量大,各种信息之间的关系又极为错综复杂,这主要*程序设计员的工作经验来进行。
因此,工艺方案的设计质量完全取决于技术人员的水平和经验。
在高速铣技术广泛应用的今天,数控工艺方案的设计重要性被提到了更高的地位。
高速铣要求对加工的全过程进行控制,任何疏忽都会引起严重的后果,因此,高速铣的工艺方案的编制好坏,将会对高速铣成败起到决定性的作用。
3.数控编程阶段:
在编程准备期间,主要的依据是三维数据和工艺文件。
程序设计员要分析零件的几何特征,构思加工过程,结合机床具体情况,考虑工件的定位,选用夹具。
数控编程的第一步要正确定义加工坐标系,选择好对刀点。
选择的编程原点应方便编程、便于测量检查、便于操作,同时考虑引起的加工误差较小。
第二步是按照数控工艺方案一步一步地在计算机上编制刀具轨迹。
第三步是验证程序的正确性,可行性。
可以通过计算机仿真模拟或试切削样件。
第四步是优化程序。
4.程序定型阶段:
由主管领导审核数控编程刀路,合格后填写数控加工程序单,绘制加工简图。
到现场了解程序执行情况,总结程序编制经验。
2.2数控工艺的特点和数控加工工艺规划
程序定型阶段:
数控工艺的特点和数控加工工艺规划的编制:
(1)数控工艺要考虑加工零件的工艺性,确定加工零件的装夹与定位,选择刀具,制定工艺路线、切削方法及工艺参数等,而这些在常规工艺中可以简化。
(2)数控工艺设计主要用于指导数控编程,我公司把数控工艺员和编程员的职责和二为一,由程序设计员负责整套模具的数控加工过程,提高了工作效率。
(3)数控加工的自动化程度高,影响因素多,在数控加工中,质量和安全是自关重要的,必须得到保证。
(4)数控工艺的编制要有严密的条理性。
数控工艺复杂,影响因素多,需要对数控加工的全过程深思熟虑,要有很好的条理性,才能编好数控工艺。
加上数控加工的自动化程度高,它的自适应能力就低,一旦出现问题,工人很难现场纠正,轻者造成加工缺陷,重者引起安全事故,因此要预先有条理的做好数控工艺的设计
(5)数控工艺的继承性好。
凡是在生产中证明是好的数控工艺,可以做成模板,作为档案保存起来,在以后加工同类零件时调用,可以节约时间,保证质量。
数控加工工艺规划可以认为是由零件初始状态(毛坯)到最终状态(零件)间的一系列工艺过程的状态空间。
数控工序的排序应满足如下的一般规则:
1.先主后次。
2.先面后孔,先铣后钻。
3.先粗后精。
4.先做内腔加工后做外形加工。
5.按工序的顺序,刀具直径由大到小。
6.上道工序的加工不能影响下道工序的装夹与定位。
7.用相同的工装和夹具应安排在一起做完,减少重复装夹与定位。
8.数控工序要集中。
9.不要把削弱零件刚性的工序排在前面。
一个好的数控加工工艺规划还要考虑以下几个方面:
是否能满足零件的技术要求,是否能提高数控加工的效率,低的加工成本,好的质量控制。
因此,通常一份完整的数控加工工艺规划,大概包括如下内容:
1.数控机床选择。
2.加工方法选择。
3.确定零件的装夹方式并选择夹具。
4.定位方法。
5.检验要求及检验方法。
6.选择刀具。
7.加工中的误差控制和公差控制。
8.定义数控工序。
9.数控工序排序。
10.切削参数选择。
11.编制数控工艺程序单。
模塑公司通过在模具行业中的比较,购买了国际一流的数控加工软件:
UGNX4.0和POWERMILL6.0,通过多年的使用表明是非常适合模具加工行业的,尤其是两种软件丰富实用的加工策略各不相同,互相补充使数控加工的质量和效率得到了很大的提高。
POWERMILL在偏置区域清除粗加工时可以加入螺旋功能,进行实际切削时更加平稳,消除了相邻刀路之间连接的进刀方向突变,减少切削进给的加速和减速,保持更稳定的切削负荷,延长了刀具寿命,对机床也起到了保护作用。
交*等高精加工使用户可定义一个分界角,浅滩区域内将使用等高策略,其它部分使用三维偏置策略,并且可以在陡峭和平坦区域之间加入重叠距离,两者相辅相成。
参数偏置精加工既可以保证曲面上刀路间的行距不超过设定的数值,又可以显著减少三维偏置策略中在刀具路径中可能出现的尖角,可以有效改善三维偏置加参考线的方法在工件表面的相交刀路产生的切削纹理,工件的外观质量更好。
第三章模具精加工控制分析
3.1零件的热处理
一幅模具是由众多的零件组配而成,零件的质量直接影响着模具的质量,而零件的最终质量又是由精加工来完成保证的,因此说控制好精加工关系重大。
在国内大多数的模具制造企业,精加工阶段采用的方法一般是磨削,电加工及钳工处理。
在这个阶段要控制好零件变形,内应力,形状公差及尺寸精度等许多技术参数,在具体的生产实践中,操作困难较多,但仍有许多行之有效的经验方法值得借鉴。
模具零件的加工,一个总的指导思想是针对不同的材质,不同的形状,不同的技术要求进行适应性加工,它具有一定的可塑性,可通过对加工的控制,达到好的加工效果。
根据零件的外观形状不同,大致可把零件分三类:
轴类、板类与异形零件,其共同的工艺过程大致为:
粗加工——热处理(淬火、调质)——精磨——电加工——钳工(表面处理)——组配加工。
热处理质量好坏直接关系着后续的加工质量以致最终影响零件的使用性能及寿命,同时热处理又是机械行业的能源消耗大户和污染大户。
近年来,随着科学技术的进步及其在热处理方面的应用,热处理技术的发展主要体现在以下几个方面:
1)清洁热处理
热处理生产形成的废水、废气、废盐、粉尘、噪声及电磁辐射等均会对环境造成污染。
解决热处理的环境污染问题,实行清洁热处理(或称绿色环保热处理)是发达国家热处理技术发展的方向之一。
为减少SO2、CO、CO2、粉尘及煤渣的排放,已基本杜绝使用煤作燃料,重油的使用量也越来越少,改用轻油的居多,天然气仍然是最理想的燃料。
燃烧炉的废热利用已达到很高的程度,燃烧器结构的优化和空-燃比的严格控制保证了合理燃烧的前提下,使NOX和CO降低到最低限度;
使用气体渗碳、碳氮共渗及真空热处理技术替代盐浴处理以减少废盐及含CN-有毒物对水源的污染;
采用水溶性合成淬火油代替部分淬火油,采用生物可降解植物油代替部分矿物油以减少油污染。
(2)精密热处理
精密热处理有两方面的含义:
一方面是根据零件的使用要求、材料、结构尺寸,利用物理冶金知识及先进的计算机模拟和检测技术,优化工艺参数,达到所需的性能或最大限度地发挥材料的潜力;
另一方面是充分保证优化工艺的稳定性,实现产品质量分散度很小(或为零)及热处理畸变为零。
(3)节能热处理
科学的生产和能源管理是能源有效利用的最有潜力的因素,建立专业热处理厂以保证满负荷生产、充分发挥设备能力是科学管理的选择。
在热处理能源结构方面,优先选择一次能源;
充分利用废热、余热;
采用耗能低、周期短的工艺代替周期长、耗能大的工艺等。
(4)少无氧化热处理
由采用保护气氛加热替代氧化气氛加热到精确控制碳势、氮气的可控气氛加热,热处理后零件的性能得到提高,热处理缺陷如脱碳、裂纹等大大减少,热处理后的精加工留量减少,提高了材料的利用率和机加工效率。
真空加热气淬、真空或低压渗碳、渗氮、氮碳共渗及渗硼等可明显改善质量、减少畸变、提高寿命。
轴承零件的热处理质量控制在整个机械行业是最为严格的。
轴承热处理在过去的20来年里取得了很大的进步,主要表现在以下几个方面:
热处理基础理论的研究;
热处理工艺及应用技术的研究;
新型热处理装备及相关技术的开发。
3.2零件的磨削加工
磨削加工采用的机床有三种主要类型:
平面磨床、内外圆磨床及工具磨具。
精加工磨削时要严格控制磨削变形和磨削裂纹的产生,即使是十分微小的裂纹,在后续的加工使用中也会显露出来。
因此,精磨的进刀要小,不能大,冷却液要充分,尺寸公差在0.01mm以内的零件要尽量恒温磨削。
由计算可知,300mm长的钢件,温差3℃时,材料有10.8μm左右的变化,10.8=1.2×
3×
3(每100mm变形量1.2μm/℃),各精加工工序都需充分考虑这一因素的影响。
精磨时选择好恰当的磨削砂轮十分重要,针对模具钢材的高钒高钼状况,选用GD单晶刚玉砂轮比较适用,当加工硬质合金、淬火硬度高的材质时,优先采用有机粘结剂的金刚石砂轮,有机粘结剂砂轮自磨利性好,磨出的工件粗糙可达Ra=0.2μm,近年来,随着新材料的应用,CBN砂轮,也即立方氮化硼砂轮显示出十分好的加工效果,在数控成型磨,坐标磨床,CNC内外圆磨床上精加工,效果优于其它种类砂轮。
磨削加工中,要注意及时修整砂轮,保持砂轮的锐利,当砂轮钝化后,会在工件表面滑擦、挤压,造成工件表面烧伤,强度降低。
板类零件的加工大部分采用平面磨床加工,在加工中常会遇到一种长而薄的薄板零件,此类零件的加工较难。
因为加工时,在磁力的吸附作用下,工件产生形变,紧贴于工作台表面,当拿下工件后,工件又会产生回复变形,厚度测量一致,但平行度达不到要求,解决的办法可采用隔磁磨削法,磨削时以等高块垫在工件下面,四面挡块抵死,加工时小进刀,多光刀,加工好一面后,可不用再垫等高块,直接吸附加工,这样可改善磨削效果,达到平行度要求。
轴类零件具有回转面,其加工广泛采用内外圆磨床及工具磨床。
加工过程中,头架及顶尖相当于母线,如果其存在跳动问题,加工出来的工件同样会产生此问题,影响零件的质量,因此在加工前要做好头架及顶尖的检测工作。
进行内孔磨削时,冷却液要充分浇到磨削接触位置,以利于磨削的顺利排出。
加工薄壁轴类零件,最好采用夹持工艺台,夹紧力不可过大,否则容易在工件圆周上产生“内三角”变形。
3.3电加工的控制
现代的模具工厂,不能缺少电加工,电加工可以对各类异形、高硬度零件进行加工,它分为线切割与电火花二种。
慢走丝线切割加工精度可达±
0.003mm,粗糙度Ra=0.2μm。
加工开始时,要先检查机床的状况,查看水的去离子度,水温,丝的垂直度,张力等各个因素,确保良好的加工状态。
线切割加工是在一整块材料上去除加工,它破坏了工件原有的应力平衡,很容易引起应力集中,特别是在拐角处,因此当R<0.2(特别是尖角)时,应向设计部门提出改善建议。
加工中处理应力集中的方法,可运用矢量平移原理,精加工前先留余量1mm左右,预加工出大致形状,然后再进行热处理,让加工应力在精加工前先行释放,保证热稳定性。
加工凸模时,丝的切入位置及路径的选择要仔细考虑。
如图3所示,工件左端夹持,加工时选择路线①比路线②要好,因为路线①工件与材料的夹持部位联接紧密,加工稳定,若采用路线②,第一遍进刀后,工件成悬壁状,受力差,影响后续几遍加工。
路线③,采用打孔穿丝加工,效果最佳。
高精线切割加工,通常切割遍数为四次,可以保证零件质量。
当加工带有锥度的凹模时,见图4,本着快速高效的立场,第一遍粗加工直边,第二边锥度加工,接着再精加工直边,这样可不需进行X段垂直向精加工,只精加工刃口段直边,既节约时间又节约成本。
电火花加工先要制作电极,电极有粗、精之分。
精加工电极要求形状符合性好,最好用CNC数控机床加工完成。
电极的材质选择上,紫铜电极主要用于一般钢件加工。
Cu-W合金电极,综合性能好,特别是加工过程中消耗量明显比紫铜小,配合足量的冲刷液,很适合难加工材料加工及截面形状复杂件精加工。
Ag-W合金电极比Cu-W合金电极性能更优,但其价格高,资源少,一般较少采用。
制作电极时,需要计算电极的间隙量及电极数量,当进行大面积或重电极加工时,工件和电极装夹要牢固,保证具有足够的强度,防止加工松动。
进行深台阶加工时,对电极各处的损耗及因排液不畅引起的电弧放电,要予以注意。
3.4表面处理及组配
零件表面在加工时留下刀痕、磨痕是应力集中的地方,是裂纹扩展的源头,因此在加工结束后,需要对零件进行表面强化,通过钳工打磨,处理掉加工隐患。
对工件的一些棱边、锐角、孔口进行倒钝,R化。
一般地,电加工表面会产生6-10μm左右的变质硬化层,颜色呈灰白色,硬化层脆而且带有残留应力,在使用之前要充分消除硬化层,方法为表面抛光,打磨去掉硬化层。
在磨削加工、电加工过程中,工件会有一定磁化,具有微弱磁力,十分容易吸着一些小东西,因此在组装之前,要对工件作退磁处理,并用乙酸乙脂清洗表面。
组装过程中,先参看装配图,找齐各零件,然后列出各零件相互之间的装备顺序,列出各项应注意事项,然后着手装配模具,装配一般先装导柱导套,然后装模架和凸凹模,然后再对各处间隙,特别是凸凹模间隙进行组配调整,装配完成后要实施模具检测,写出整体情况报告。
对发现的问题,可采用逆向思维法,即从后工序向前工序,从精加工到粗加工,逐一检查,直到找出症结,解决问题。
第四章模具加工的最新发展
很少有金属加工的分支行业能像模具制造这样具有活力,因此,不断寻求最新的技术和创新的观念是任何模具厂处于领先地位必不可少部分这里介绍一些利于创造机会或为模具加工提供领先地位的技术进展。
4.1并行加工
观念:
模具的型芯和型腔合并成一个零件在多任务机床上被并行加工。
背景:
这个观念由Mazak公司(Florence,Kentucky)的e系列Integrex加工中心在IMTS2004展会上进行演示。
使用具有柔性的倾斜铣削主轴(B轴)和反向的车削主轴(C轴),长方形工件的四个侧面和背面上的冷却孔由铣削完成。
型芯和型腔零件在工件仍合并成一体时被加工。
通过车削主轴的旋转和铣削主轴倾斜的协调优化刀具的定向能获得表面粗糙度的改善和刀具寿命的提高工件还可周期性地反转以利倾倒切屑。
然后型芯和型腔被分离,每个部分仍被牢固地夹持在反向的车削主轴。
对两个部分各自露出两个新的侧面进行平面铣削,而模具两个部分上的冷却孔在一次装夹中被全部钻出。
与传统加工相比,这个方法极大地缩减了装夹次数和工序。
由于模具的两个部分相互之间保持极好的定向直到被分离所以精度也提高了。
使能技术:
在这个应用里,旋转轴的位置精度是关键。
多任务机床在铣削主轴上使用一个提供0.0001度分辨率的滚子凸轮。
主、从车削主轴的分度增量也是0.0001度。
据机床商介绍,转速12,000rpm的铣削主轴的振幅为1.5微米(0.00006英寸)。
极低的主轴振幅可保护高速铣削应用的小直径刀具。
4.2平行加工
观念:
大型模具零件被分割后在较小的加工中心上加工。
加工完后的部件再装配成一个完整的型芯或型腔。
在某些情况下,部件被设计成镶嵌件以装配到模架上的型腔里。
背景:
在分割一个大型模具零件之后,每个部件可能在较小的加工中心上加工,而不需要放到具有大工作台的大型立式机床上加工。
虽然也可应用较小的立式机床,但较小的卧式加工中心更加理想,因为它具有排屑和生产能力方面的优势。
因为它们的工作范围相应地更小,较小的机床倾向于具有更高的形位精度。
由于移动轴的质量小造车网,较小的机床对于等高线切削能获得更高的加速度和减速度(acc/dec)。
更高的acc/dec速率能显著地减少整个加工时间-因为更高的acc/dec,通常需要20小时的加工能在15小时内完成。
在较小的机床上,换刀问题能很容易处理。
例如,一把精加工刀具不用换切削刃就能完成模具部件精加工是很有希望的。
最重要的是,两台或三台机床同时运转能在生产上超过一台大型机床。
例如,20小时的加工在两台小机床上能在7.5小时内完成(分担工时,然后是更快的acc/dec速率的因素)。
一组较小的机床还可安排得比一台大型机床更有柔性。
当大型模具能设计成适合于分块加工,仅拥有较小机床的模具厂仍能承接那些原本超出其加工能力的任务。
此外,较小的机床代表了一种更低的资本投资。
模具厂必须把两台或更多小机床的总成本同具备相同能力的大型加工中心的成本进行比较。
最后,设计用于平行加工的模具也许表现了改善维护和修复的机会。
例如,分割模具也许是可行的,所以易于磨损剧烈的区域可以被单独分割开来。
通过移开这块需要被替换、维修或修补的部件,停机时间可降到最小。
使能技术:
较小的机床必须具有极高的形位精度,以便组装的模具部件的接合面能真正做到无缝连接。
4.3主轴枪钻加工
钻削具有复合角的水管线路的能力使得提高大型模具的冷却性能成为可能。
五轴枪钻加工机床通过消除多次复杂装夹从而获得良好的经济性成为可能。
用于汽车保险杠、汽车仪表板和其它塑料件的那些模具依靠快速而有效的冷却来获得有竞争力的生产周期。
当只拥有固定工作台和固定主轴的枪钻加工机床时,模具设计者有两个途径来提高大型模具的冷却速率。
方法之一是增加穿过模架的直线水管线路。
另一种方法是钻削具有复合角的水管线路,以便管线更贴近型腔表面。
第一个方法意味着显著增加花在枪钻加工上的时间。
第二个方法未必意味着更长的钻削时间,但它大量增加装夹时间,因为模具部件必须对于每个要求的角度进行手动定位。
每个加工的装夹时间通常要比钻削时间长得多。
这些方案都不是很有吸引力,而且它们甚至不能满足客户希望降低模具价格的