粉末冶金考试资料Word文件下载.docx
《粉末冶金考试资料Word文件下载.docx》由会员分享,可在线阅读,更多相关《粉末冶金考试资料Word文件下载.docx(20页珍藏版)》请在冰豆网上搜索。
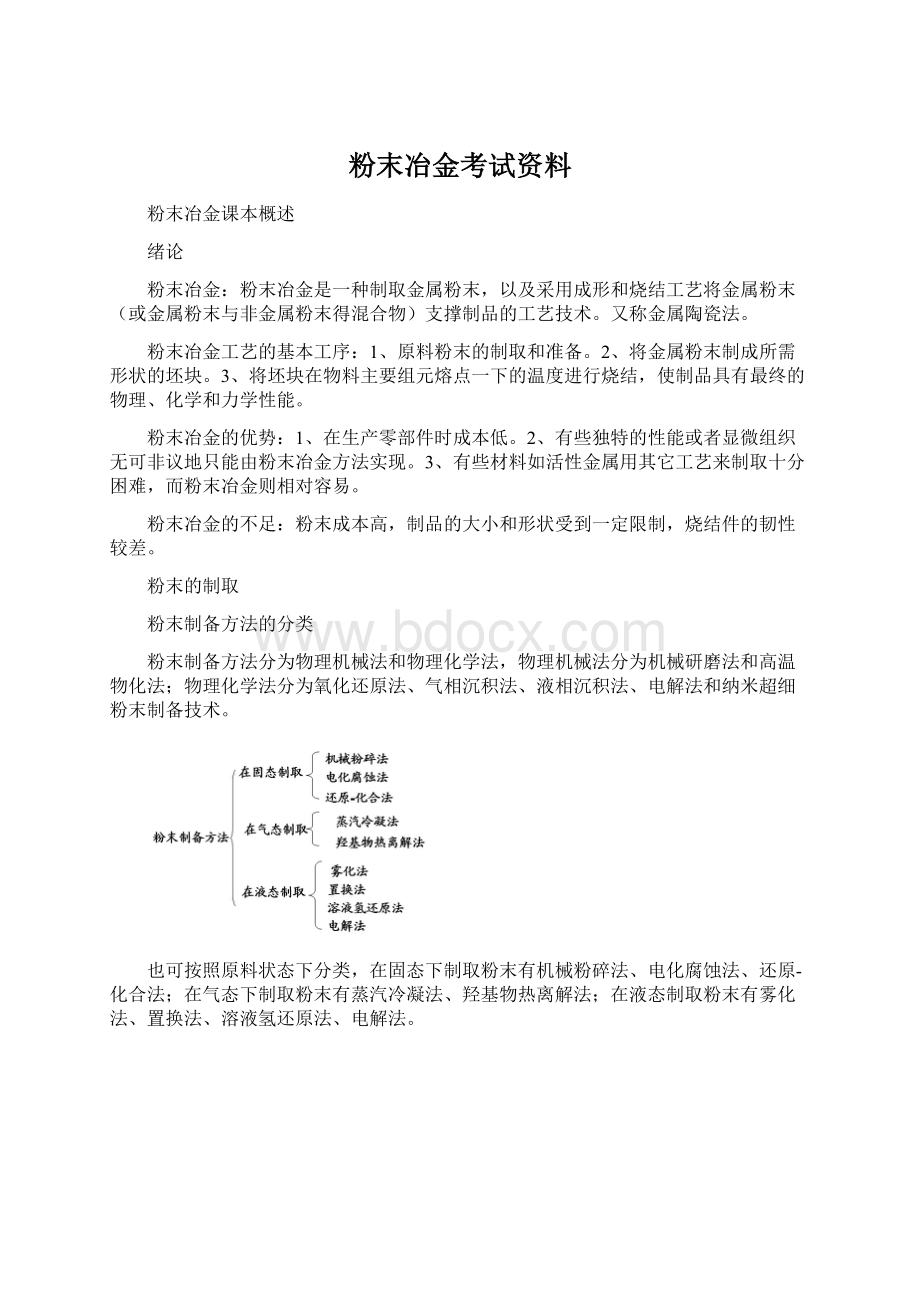
(1/18~1/24)D。
球磨铁粉选用10~20mm的钢球。
5、物料除可以在空气介质中干磨外还可以在液体介质中进行湿磨。
液体介质可以是汽油,水,酒精,丙酮等。
6、物料是脆性材料还是塑性材料对研磨过程有很大影响。
脆性材料虽然硬度高,但很快被粉碎,塑性材料则相反。
人工脆化很有意义。
装填系数:
球体体积与球磨筒容积之比。
湿磨的主要优点:
可减少金属氧化;
防止金属颗粒的再聚集长大;
减少物料的成分偏析;
防止粉末飞扬,改善劳动环境。
强化球磨的方法:
提高研磨速率,可强化研磨效果,有振动球磨和行星球磨。
机械合金化(MA):
是在高速搅拌球磨的条件下,利用金属粉末混合物的重复冷焊和断裂进行合金化的。
也可在金属粉末中加入非金属粉末来实现机械合金化。
是一种高能球磨法。
机械合金化与机械混合法的不同:
1、粉末中引入了大量的缺陷和纳米结构,使合金过程的热力学和动力学不同于普通的固态反应。
合成常规法难以合成新型合金,如固态下溶解度较小,甚至在液态下几乎不互溶的体系,通过MA可以形成固溶体。
雾化法
雾化法:
是将液态金属或合金直接破碎成细小的液滴,其大小一般在150μm,而成为粉末。
制粒:
用于制造大颗粒粉末的工艺称为制粒。
是让熔融金属通过小孔或筛网自动注入空气或水中,冷凝后便得到金属粉末。
二流雾化(水雾化或气雾化):
借助高压水流或者气流的冲击来破碎液流。
离心雾化:
用离心力破碎液流称为离心雾化。
真空雾化:
在真空中的雾化叫做真空雾化。
超声波雾化:
利用超声波能量来实现液流的破碎称为超声波雾化。
雾化的形式:
平行喷射,垂直喷射,V型喷射,锥形喷射,旋涡环形喷射。
雾化喷嘴:
自由降落式喷嘴,侧线式喷嘴。
水雾化中,雾化粉末粒度D与水速ν有关,D=C/νsinα。
还原法
碳还原法
固体碳还原氧化铁的过程:
Fe2O3->
Fe3O4->
FeO->
Fe
当温度高于570℃时有
3Fe2O3+C=2Fe3O4+COFe3O4+C=3FeO+COFeO+C=Fe+CO
当温度低于570℃时有
1/4Fe3O4+C=3/4Fe+CO
气体还原法
钨粉只能用氢气来制取。
钨的氧化物有四种,WO3,WO2.90,WO2.72,WO2总反应为:
WO3+3H2=W+3H2O影响钨粉纯度的主要因素有原料,氢气,还原温度时间和料层厚度,添加剂。
金属热还原
主要应用于制取稀有金属粉末,如钽铌等。
总反应式是MeX+Me1=Me1X+Me+Q
金属热还原法应满足一下条件:
1、还原反应中的Q较大,使还原过程能够依靠反应热效应自发进行。
2、还原过程中所形成的渣和残余的金属还原剂应该容易与金属分离开来。
3、金属还原剂与被还原金属不能形成合金或其它化合物。
气相沉积法
气相沉积法有以下几种形式:
1、金属蒸汽冷凝。
2、羟基物热离解。
3、气体还原。
4、化学气相沉积。
羟基物热解离法(羟基法):
就是离解金属羟基化合物而制取金属粉末的方法。
不仅可以生产纯金属粉末,合金粉末也可制的包覆粉末。
制的的粉末很纯,可制Ni粉。
180℃时Ni+4CO=Ni(CO4);
280~300℃时Ni(CO4)=Ni+4CO
气象还原法:
是指用氢还原气态金属卤化物的方法。
可以制的金属粉末,合金粉末,包覆粉末。
此法得到的粉末都是很细或者超细的。
可制的超细钨粉:
W+3Cl2->
WCl6WCl6->
W+6HCl
化学气相沉积(CVD):
是从金属卤化物还原化合沉积制取难熔化合物粉末和各种涂层的方法。
包括碳化物,硼化物和氮化物等方法。
碳化物:
金属卤化物+CmHn+H2->
MeC+HCl+H2
液相沉积法
金属置换法:
用一种金属从水溶液中取代出另一种金属的过程。
液态氢还原法:
用气体从溶液中还原金属盐溶液制取金属粉末的方法。
反应式为
可以制取铜镍钴等金属粉末,也可以制取合金粉末和包覆粉末。
液相共沉淀法制取复合粉末有两种方案:
1、使基体金属和弥散相金属盐或氢氧化物在同种溶液中同时析出达到均匀分布,然后经干燥,分解,还原过程以得到基体金属和弥散相的复合粉末。
2、将弥散相制成最终粒度,然后悬浮在含基体金属的水溶液中作为沉淀结晶核心。
待基体金属以某种化合物沉淀后,经过干燥还原就得到以弥散相为核心,基体金属包覆在弥散相核心外面的包覆粉末。
△电解法
电解法:
在一定的条件下,粉末可以在电解槽的阴极上沉积出来。
电解法因为成本较高,生产中占得比重较小,所得粉末较纯,粉末形状一般为树枝状,压制性较好,也可以制取超细粉末。
电解的步骤:
1、扩散2、电化学反应、晶核析出、晶粒择优长大—枝晶化
水溶液电解时,在阴极析出的沉淀物形态与水溶液中的阳离子浓度C和电解时的电流密度有关。
熔盐电解法可以制去钛钽铌锆等纯金属粉末,也可以制取如钽铌等合金粉末,以及制取各种难熔化合物粉末。
粉末的性能及测定
粉末体:
分散程度在0.1~1mm之间的称为粉末体,简称粉末,是由大量颗粒及颗粒之间的空隙所构成的集合体。
单颗粒:
粉末中能分开并独立存在的最小实体称为单颗粒。
一次颗粒:
二次颗粒中原始的组织就称为一次颗粒。
二次颗粒:
单颗粒如果以某种形式聚集就构成所谓的二次颗粒。
粉末颗粒的结晶构造:
1、粉末颗粒通常为多晶结构。
2、粉末颗粒晶体具有严重的不完成性。
因此粉末贮存有较高的晶格畸变能,具有较高的活性。
粉末的表面状态:
粉末颗粒的表面状态十分发复杂,粉末颗粒愈细外表面愈发达。
粉末颗粒的缺陷越多,内表面越大。
外表面:
是能看到的明显表面。
内表面:
包括裂纹,微缝以及与颗粒外表面连通的空腔,空隙等,但不包括封闭在颗粒内的潜孔。
粉末的性能:
1、单颗粒的性质:
(1)、由粉末材料决定的性质,如点阵结构、理论密度、熔点等。
(2)、由粉末生产方式决定的性质,如粒度,密度,颗粒形状。
2、粉末体的性质:
除单颗粒的性质外,还有平均粒度,粒度组成,比表面,松装密度等。
3、粉末的空隙性质:
总空隙体积,颗粒间的空隙体积,颗粒内空隙性质等。
粉末的化学成分:
粉末的化学成分包括主要金属的含量和杂质的含量。
杂质包括:
(1)、与主要金属结合,形成固溶体或化合物的金属或非金属成分。
如硅锰。
(2)、从原料和粉末生产过程中带入的机械夹杂。
如二氧化硅。
(3)、粉末表面吸附的氧,水蒸气和其它气体。
(4)、制粉工艺带进的杂质,如水中电解粉末中的氢。
金属粉末的化学成分分析有:
菲水滴定法,酸不溶法。
颗粒的形状及其分析方法:
颗粒的形状是指粉末颗粒的几何形状。
可将粉末试样均匀分散在玻璃试片上,用放大镜或各式显微镜观察,或用图像分析法分析。
粉末的粒度及其测定:
粒度(粒径):
用直径表示颗粒大小称为粒径或者粒度。
粒度组成(粒度分布):
用不同粒径的颗粒占全部粉末的百分含量来表征粉末颗粒大小的状况。
粉末颗粒的测定方法:
1、筛分析法:
泰勒筛制:
以网目数(目)表示筛网的孔径和粉末的粒度。
目数越大,网孔愈细。
目数:
指筛网1英寸(25.4mm)长度长的网孔数。
显微镜法:
可以采用垂直投影法测量粒度或者线性切割法测量粒度。
平均粒度值:
(1)、算术平均径:
Da=ΣnD/Σn
(2)、长度平均径:
Dl=ΣnD²
/ΣnD
(3)、体面积平均径:
Dvs=ΣnD³
/ΣnD²
(4)、质量平均径:
Dvs=ΣnD4/ΣnD³
2、沉降分析法
沉降分析法:
是粉末在静止的气体或者液体介质中依靠重力克服介质的阻力和浮力自然沉降,由此引起悬浊液的浓度,压力相对密度,透光性和沉降质量的变化。
测定这些参数随时间的变化规律,就可反映粉末的粒度组成。
分为液体沉降和气体沉降。
适用范围是50~0.01μm。
沉降法的优点:
粉末取样较多代表性好,使结果和统计的再现性提高。
沉降天平法:
沉降公式:
3、淘析法:
淘析法:
颗粒在流动的介质中发生非自然沉降而分级称为重力淘析或简称淘析。
气体淘析就是风选,液体淘析也称水利淘析。
淘析法用于极细的和超细粉末的分级,具有设备简单,操作方便和效率高等特点,但不精确。
淘析法的原理是:
流体逆着粉末向上运动,粉末按颗粒沉降速度大于或者小于流体线速度而彼此分开。
改变流速可以按不同临界粒径分级。
粉末的比表面及其测定:
粉末的比表面:
1g质量的粉末所具有的总表面积。
致密固体的比表面称容积比表面。
粉末比表面的测试方法:
透过法和气体吸附法。
气体吸附法:
气体吸附法测定比表面积的灵敏度和精确度最高,分为静态法和动态法两大类,静态法又包含容量法,重量法互溶简易单点吸附法。
(多点法)多分子吸附BET公式:
其中P-吸附平衡时的气体压力
P0-吸附气体的饱和蒸汽压
V-被吸附气体的体积
Vm-固体表面被单分子层气体覆盖所需气体的体积
C-常数
即在一定的P/P0值范围内,用实验来测得不同P值下的V,并换算成标准状态下的体积。
以P/V(P0-P)对P/P0作图得到的应为一条直线,1/VmC为直线的截距,C-1/VmC为直线的斜率,于是Vm=1/(斜率+截距),于是粉末的克比表面:
S=VmNAAm/22400W。
单点吸附法:
S=4.36Vm/W
质量法:
用吸附秤直接精确称量粉末试样在吸附前后的质量变化来确定比表面的方法。
透过法:
透过法分为气体透过法和液体透过法。
金属粉末工艺性能的测试
松装密度:
粉末试样自然的充满规定的容器时,单位容积的粉末质量。
松装密度可以用漏斗法、斯柯特容量计法或振动漏斗法来测定。
振实密度:
指将粉末装入振动容器中,在规定条件下,经过振实后所测得的粉末密度。
一般振实密度比松装密度高20%~50%。
影响松装密度和振实密度的因素:
1、粉末颗粒形状愈规则,其松装密度就越大;
粉末表面愈光滑,松装密度愈大。
2、粉末颗粒愈粗大,其松装密度就愈大。
3、粉末颗粒越致密,松装密度就越大。
4、粉末颗粒范围窄的粗细粉末,松装密度都较低。
流动性:
粉末颗粒的流动性是指50g粉末从标准的流速漏斗流出所需的时间,单位为s/50g。
其倒数是单位时间流出粉末的质量,称为流速。
影响流动性的因素:
1、粉末颗粒愈大,颗粒形状愈规则,粒度组成中极细粉末所占比例小,流动性将变好。
2、粉末氧化能提高流动性。
3、颗粒表面吸附水分、气体或加入成形剂会降低粉末流动性。
压制性:
压制性是压缩性和成形性的总称。
压缩性就是金属粉末在规定的压制条件下被压紧的能力。
成形性是指粉末压制后,压坯保持既定形状的能力。
压制性的测定:
测定压缩性通常在标准模具中,在规定的润滑条件下加以测定。
压缩性用规定的单位压力下的粉末所达到的压坯密度来表示。
成形性是用粉末得以成形的最小单位压力表示,或用压坯强度来衡量。
影响压制性的主要因素是颗粒的塑性和颗粒的形状。
金属粉末有效密度的测定:
开孔(半开孔):
孔与颗粒外表面连通。
闭孔:
颗粒内不与外表面相通的潜孔。
真密度:
颗粒质量与除去开孔和闭孔的颗粒体积相除的商值。
真密度就是材料的理论密度。
似密度(有效密度、重瓶密度):
颗粒质量用包括闭孔在内的颗粒体积除得的商。
测量方法有比重瓶法,吊斗法。
表观密度:
可以质量用包括开孔和闭孔在内的颗粒体积除得的密度值。
比重瓶法:
粉末试样预先干燥后再装入规定容积V的比重瓶,约占瓶内容积的1/3~1/2,连通瓶子一起称重。
然后加入少量能溶湿粉末的液体直至盖过粉末试样。
经真空除气,将润湿液体充满,直至于瓶塞中毛细孔溢出。
擦净瓶子外出的液体,再一次称量比重瓶。
有效密度
m1-比重瓶的质量
m2-比重瓶加粉末试样的质量
m3-比重瓶加粉末试样和充满液体后的质量
ρ液-液体密度
成形
粉末冶金成形是将松散的粉末体加工成具有一定尺寸,形状以及一定密度和强度的坯块。
粉末成形的方法有普通模压法或用特殊方法成形。
特殊方法有等静压成形,连续成形,无压成形等。
1、成形前原料的准备:
成型前原料的准备包括粉末退火,混合,筛分,制粒以及加润滑剂。
目的是要制备具有一定化学成分和一定粒度,以及适合的其它物理化学性能的混合料。
(1)、退火
a、退火的目的:
是使氧化物还原,降低碳和其它杂质的含量,提高粉末的纯度。
同时消除粉末的加工硬化,稳定粉末的晶体结构。
此外,还可以将某些超细金属粉末表面钝化,防止其自燃。
b、退火的温度:
根据金属粉末的种类而不同,一般T退=(0.5~0.6T熔)。
c、退火介质:
退火一般用还原性气氛,有时也可以用惰性气氛或者真空。
(2)、混合
a、混合:
是将两种或者两种以上的不同成分的粉末混合均匀的过程。
B、合批:
将成分相同而力度不同的粉末进行混合。
c、混合的方法有机械法和化学法。
机械混合常用的混料机有球磨机,V型混合器,锥形混合器,酒桶式混合器,螺旋混合器。
分为干混和湿混。
制备硬质合金的时候用湿混,对湿混的介质要求是:
不与物料发生化学反应;
沸点低,易挥发;
无毒性;
来源广泛,成本低等。
化学混料是将金属或化合物粉末与添加金属的盐溶液均匀混合,或者是各组元全部以金属的某种盐的溶液形式混合,然后经沉淀,干燥和还原等处理而得到均匀分布的混合物。
d、混合结果的测定:
物料的混合结果可以根据混合料的性能来测定。
如检测其粒度组成,松装密度,流动性等。
e、填充剂:
为了保证制品的连通空隙,加入填充剂。
其作用是即可防止形成闭空隙,还会加剧扩散过程从而提高制品的强度。
填充剂往往以盐的水溶液方式加入。
(3)、筛分
筛分的目的:
是把不同颗粒大小的原始粉末进行分级,而使粉末能够按照粒度分为大小范围更窄的若干等级。
(4)、制粒
是将小颗粒的粉末制成大颗粒或团粒的工序,常用来改善粉末的流动性。
(5)、加润滑剂
在成形前,加入的能改善成形过程的物质,即润滑剂或者成形剂或者在烧结中造成一定空隙的造孔剂。
2、金属粉末的压制现象
压模压制:
是指松散的粉末在压模内经受一定的压制压力后,成为具有一定尺寸、形状、密度、强度的压坯。
侧压力:
粉末体在压模内受压时,压坯会向周围膨胀,膜壁就会给压坯一个大小相等方向相反的反作用力,这个力就叫做侧压力。
弹性后效:
在压制过程中当卸掉压制压力并把压坯从压膜种压出后,由于弹性内应力的作用,压坯将发生弹性膨胀,这种现象称为弹性后效。
粉末颗粒变形与位移的几种形式:
变形有三种情况:
弹性变形,塑性变形和脆性断裂。
位移的形式有:
粉末颗粒的接近,分离,滑动,转动,因粉碎而产生的移动。
金属粉末的压坯强度:
压坯反抗外力的作用,保持其几何形状尺寸不变的能力。
压坯强度的测试方法:
压坯抗弯强度试验法,测定压坯边角稳定性的转鼓实验法,和测试破坏强度的方法。
粉末颗粒之间的联结力有两种:
粉末颗粒之间的机械啮合力。
粉末颗粒表面原子间的引力。
3、粉末成形的方法
粉末成形的传统方法是钢压模成形。
其过程为粉末->
压制成形->
烧结,其局限性在于1、无法制备出形状复杂精细的零部件。
2、组织均匀性差。
3、加工工序多。
4、材料利用率低。
5、生产成本高。
等静压成形
等静压成形是借助高压泵的作用把流体介质压入耐高压的钢体密封容器内,高压流体的等静压直接作用在弹性弹性模套内的粉末上,使粉末体在同一时间内各个方向均衡受压而获得密度分布均匀和强度较高的压坯。
等静压成形的特点:
1、流体介质传递压力是各向相等的。
2、弹性模具本身受压缩的变形,和粉末颗粒受的压缩大体上是一致的。
3、弹性模量与接触粉末之间不会产生明显的相对运动,他们之间的外摩擦力就很小。
4、由于各方向压力相等,静摩擦力在压坯的纵断面上任意点都应相等。
压坯的密度分布沿纵断面是均匀的。
5、沿压坯同一横向断面上,由于粉末颗粒间的内摩擦影响压坯的密度从外向内逐渐降低。
金属粉末轧制
金属粉末轧制的优点:
与熔铸轧制法相比其优点是:
1、能够生产常规轧制法难于或无法生产的板带材。
2、能够轧制出成分比较均匀的带材。
3、粉末轧制的板材具有各向异性的特点。
4、工艺过程短,节约资源。
5、成材率高,一般可达50%~80%。
与模压法相比,优点是制品的长度原则上不受限制,且密度比较均匀。
金属粉末轧制的局限:
生产的带材厚度受轧辊直径的限制,宽度也受轧辊宽度的限制。
而且只能制取形状简单的板带材以及与直径与厚度比值很大的衬套。
用金属粉末轧制生产的薄板的影响因素:
1、粉末的性能会影响粉末的轧制过程。
2、气氛对轧制带材的厚度和密度有重要影响。
3、强迫供应粉末会促进提高带材密度。
④注射成形:
粉末注射成形包括陶瓷注射成形和金属注射成形,以及金属或陶瓷粉末加上适当粘接剂,通过注射成形手段来达到成形目的,最后经过脱脂及烧结来获得粉末冶金产品。
⑤高能成形:
利用炸药爆炸时产生的瞬间冲击波压力作用于金属时,粉末变形就像流变一样易于进行。
烧结
烧结:
把压坯或封装粉末体加热到其基本组元熔点一下的温度,并在此温度下保温,从而使粉末颗粒相互结合起来,改善其性能,这种热处理就叫做烧结。
烧结的目的:
依靠热激活作用发生原子迁移,粉末颗粒形成结合,使烧结体的强度增大,大多数情况下密度也增高。
烧结的基本过程:
1、开始阶段-粘结面的形成。
2、中间阶段-烧结颈的长大。
3、最终阶段-闭空隙球化和缩小阶段。
烧结的原动力:
空隙表面的自由能的降低。
烧结中的物质迁移:
烧结中存在两种类型的物质迁移——物质的迁移和体积的迁移。
烧结体显微组织中孔隙变化:
颗粒接触—接触点长大—形成多面晶体和连通空隙—形成球形孔隙
单元系烧结:
由纯金属,化合物或者固溶体组成的烧结体系。
多元系烧结:
由金属--金属,金属--非金属,金属--化合物组成的烧结体系。
液相烧结:
烧结过程中出现液相的粉末烧结过程。
固相烧结:
是指在低于物质熔点的温度下进行的烧结。
熔浸:
将粉末压坯与液相金属接触或浸在液体金属中,让压坯的孔隙被金属液充填,冷却下来就得到致密材料或零件,这种工艺称为溶浸。
固相烧结
多元系固相烧结有三种情况:
均匀固溶体,混合粉末,烧结过程中固溶体分解。
无限互溶的混合粉末烧结的影响因素:
烧结温度,烧结时间,粉末粒度,粉末原料的愈合金化。
在有限互溶混合粉末烧结中烧结体性能的影响因素:
均匀化的完善程度,烧结体的孔隙度,异相间的接触与同相间接触的完善程度,未溶组元的形状和数量。
互不相溶的混合粉末烧结条件:
1、必要条件:
γAB<
γA+γB,充分条件:
|γA-γB|。
液相烧结
液相烧结的条件:
1、润湿性:
润湿角越小,液相渗进固相界面越深,润湿性越好。
2、溶解度:
固相在液相中有一定的溶解度是液相烧结的又一条件。
3、液相数目:
液相数量占烧结体积的20%~50%最好。
液相烧结的基本过程:
1、生成液相和颗粒重新分布阶段。
2、溶解和析出阶段。
3、固相的粘接及形成刚性骨架阶段。
液相烧结的优缺点:
优点:
1、加快烧结速度。
1>
液相的形成加快了原子的迁移速率2>
在无外压情况下,毛细管力的作用加快了坯体的收缩。
3>
液相的存在降低了颗粒间的摩擦,有利于颗粒重排。
2、晶粒尺寸控制优化显微结构和性能。
3、可得全致密的P/M材料或制品,延伸率高。
尖角处优先溶于液相,易于获得有效的颗粒间填充。
缺点
变形收缩大,尺寸精度控制困难。
液相烧结时的致密化系数:
α=(ρ烧-ρ压)/(ρ理-ρ压)×
100%其中ρ烧ρ压ρ理分别为烧结体,压坯,烧结体理论密度。
影响致密化的因素:
液相数量,液相对固相的润湿性,各个界面的界面能,固相颗粒的大小,固相与液相间的相互溶解度以及压坯密度等。
液相烧结的致密化过程:
1、液相流动2、溶解-析出3、固相烧结
熔浸
将粉末压坯与液体金属接触或埋在液体金属内,让压坯的空隙被金属液填充,冷却下来就得到致密材料或零件,这种工艺称为熔浸或熔渗。
熔浸必须具备的基本条件:
1、骨架材料与熔浸材料的熔点相差较大,不致造成零件变形。
2、熔浸金属应能很好溶湿骨架材料,即润湿角θ<
90°
。
3、骨架与熔浸金属之间不发生互溶或溶解度不大,以避免在熔浸过程中产生新相而致使液相消失。
4、熔浸金属的量应以填满压坯中的空隙为限度,过多或过少均为不利。
熔浸与液相烧结的区别:
1、熔浸的致密化主要靠易熔成分从外面来填满压坯中的空隙,而不是靠压坯本身的收缩。
2、熔浸的零件基本不发生收缩,烧结所需时间也短。
强化烧结
活化烧结:
采用化学或物理的措施,使烧结温度降低,烧结过程加快,或使烧结体密度和其他性能得到提高的方法称为活化烧结。
活化烧结从方法上可以分为两种类型:
1、依靠外界因素活化烧结过程。
如加活性剂等。
2、提高粉末活性。
活化烧结有预氧化烧结,添加少量合金元素,在气氛或填料中添加活化剂。
电火花烧结:
又称为电活化压力烧结,它是利用粉末间火花放电所产生的高温,并且同时受外应力作用的一种特殊烧结方法。
全致密工艺
全致密工艺:
是将压力和温度同时并用,已达到消除空隙的目的。
全致密工艺的方法有:
热压,热挤,热锻,喷雾沉积,大气压固结。
1、热压热压就是将粉末装在压模内,在加压的同时把粉末加热到熔点以下,使之加速烧结成比较均匀致密的制品。
2、热挤在提高温度的情况下,进行金属粉末的挤压,以使制品达到全致密的方法。
3、热锻不仅可以使制品得到致密的最终形状和尺寸,而且还可以获得均匀的细晶粒组织和结构,显著提高制品的强度和韧性。
4、喷雾沉积通过雾