轴类零件的加工工艺及编程.docx
《轴类零件的加工工艺及编程.docx》由会员分享,可在线阅读,更多相关《轴类零件的加工工艺及编程.docx(17页珍藏版)》请在冰豆网上搜索。
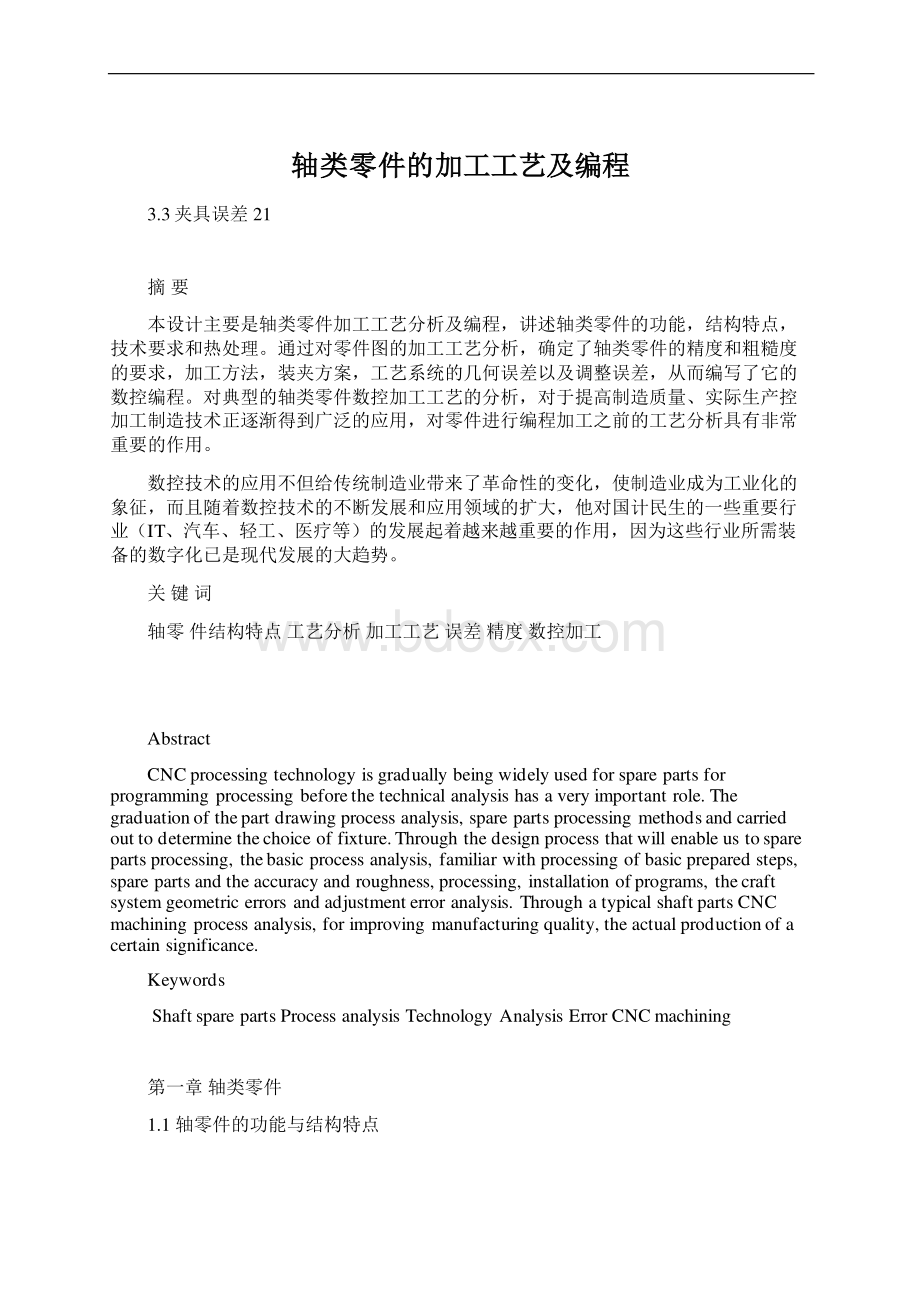
轴类零件的加工工艺及编程轴类零件的加工工艺及编程3.3夹具误差21摘要本设计主要是轴类零件加工工艺分析及编程,讲述轴类零件的功能,结构特点,技术要求和热处理。
通过对零件图的加工工艺分析,确定了轴类零件的精度和粗糙度的要求,加工方法,装夹方案,工艺系统的几何误差以及调整误差,从而编写了它的数控编程。
对典型的轴类零件数控加工工艺的分析,对于提高制造质量、实际生产控加工制造技术正逐渐得到广泛的应用,对零件进行编程加工之前的工艺分析具有非常重要的作用。
数控技术的应用不但给传统制造业带来了革命性的变化,使制造业成为工业化的象征,而且随着数控技术的不断发展和应用领域的扩大,他对国计民生的一些重要行业(IT、汽车、轻工、医疗等)的发展起着越来越重要的作用,因为这些行业所需装备的数字化已是现代发展的大趋势。
关键词轴零件结构特点工艺分析加工工艺误差精度数控加工AbstractCNCprocessingtechnologyisgraduallybeingwidelyusedforsparepartsforprogrammingprocessingbeforethetechnicalanalysishasaveryimportantrole.Thegraduationofthepartdrawingprocessanalysis,sparepartsprocessingmethodsandcarriedouttodeterminethechoiceoffixture.Throughthedesignprocessthatwillenableustosparepartsprocessing,thebasicprocessanalysis,familiarwithprocessingofbasicpreparedsteps,sparepartsandtheaccuracyandroughness,processing,installationofprograms,thecraftsystemgeometricerrorsandadjustmenterroranalysis.ThroughatypicalshaftpartsCNCmachiningprocessanalysis,forimprovingmanufacturingquality,theactualproductionofacertainsignificance.KeywordsShaftsparepartsProcessanalysisTechnologyAnalysisErrorCNCmachining第一章轴类零件1.1轴零件的功能与结构特点轴类零件是机械零件中的关键零件之一,在机器中,主要用于支撑齿轮、带轮、凸轮、以及连杆等传动件。
它的主要功能是支承传动零件、传递扭矩、承受载荷,以及保证装在轴上的零件等有一定的回转精度。
轴类零件是回转体零件,其长度大于直径。
加工表面通常有内外圆柱面、内外锥面、螺纹、键槽、横向孔和沟槽等。
轴类零件按结果形状可分为阶梯轴、光轴、空心轴和偏心轴等类,如图1.1所示。
a)b)c)d)图1.1轴的种类a)阶梯轴b)光轴c)空心轴d)偏心轴1.2轴类零件的技术要求轴类零件是机器中经常遇到的典型零件之一。
它主要用来支承传动零部件,传递扭矩和承受载荷。
轴类零件是旋转体零件,其长度大于直径,一般由同心轴的外圆柱面、圆锥面、内孔和螺纹及相应的端面所组成。
根据结构形状的不同,轴类零件可分为光轴、阶梯轴、空心轴和曲轴等。
(1)尺寸精度。
尺寸精度包括直径尺寸精度和长度尺寸精度。
精密轴颈为IT5级,重要轴颈为IT6IT8级,一般轴颈IT9级。
轴向尺寸一般要求较低,当阶梯轴的阶梯长度要求较高时,其公差可达0.0050.01mm。
(2)几何形状精度。
几何形状精度主要指轴颈的圆度、圆柱度,一般应在直径公差范围内。
当几何形状精度要求较高时,零件图上应注出规定允许的偏差。
(3)相互位置精度。
相互位置精度,主要指装配传动件的轴颈相对于支承轴劲的同轴度及端面对轴心线的垂直度等,通常用径向圆跳动来标注。
普通精度轴的配合轴颈相对支承轴径向圆跳动为0.010.03mm,高精度的轴通常为0.0050.01mm。
端面圆跳动为0.0050.01mm(4)表面粗糙度。
轴类零件的表面粗糙度和尺寸精度应与表面工作要求相适应。
通常支承轴颈的表面粗糙度值Ra为3.20.4m,配合轴颈的表面粗糙度值Ra为0.80.1m。
1.3轴类零件的材料与热处理轴类零件应根据不同的工作状况,选择不同的材料和热处理规范。
一般轴类零件常用中碳钢,如45钢,经正火、调质及部分表面淬水等热处理,得到所要求的强度、韧性和硬度。
对中等精度而转速较高的轴类零件,一般选用40Cr等合金结构钢,经过调质和表面淬火处理,使其具有较高的综合力学性能。
对在高转速、重载荷等条件下工作的轴类零件,可选用20CrMnTi、20Mn2B、20Cr等低碳合金钢,经渗碳淬火处理后,使其具有很高的表面硬度,心部则获得较高的强度和韧性。
对高精度、高转速的轴,可选用38CrMoAl氮化钢,经调质和表面氮化后,使其具有很高的心部强度和表面硬度,优良的耐磨性和耐疲劳性,热处理变形也较小。
为改善工件材料切削性能而进行热处理的工序(如退火,正火等),应安排在切削加工之前;为消除内应力而进行的热处理工序(如退火,人工时效等),最好安排在粗加工之前,也可安排在切削加工之前;为了改善工件材料的物理性质而进行的热处理工序(如调质,淬火等)通常安排在粗加工之前,精加工之后进行。
其中渗碳淬火一般安排在切削加工后,磨削加工前。
而表面淬火和渗氮等变形小的热处理工序,允许安排在精加工后进行;为了提高零件表面耐磨性或耐蚀性而进行的热处理工序以及装饰为目的热处理工序或表面处理工序(如镀铬,镀锌,氧化,发黑等)一般放在工艺过程的最后。
1.4轴类零件的毛坯数控车削加工零件时,加工过程是自动的,毛坯余量的大小,如何装夹等问题在选择毛坯就要仔细考虑好,否则,一旦毛坯不适合数控车削,加工将很难进行下去,根据经验,确定毛坯的余量和装夹应注意一下两点:
(1)毛坯加工余量应充足并尽量均匀
(2)分析毛坯的装夹适应性。
轴类零件的毛坯常采用棒料、锻件和铸件等毛坯形式。
一般光轴或外圆直径相差不大的阶梯轴采用棒料,外圆直径相差较大或较重要的轴常采用锻件,某些大型的或结构复杂的轴(如曲轴)可采用铸件。
根据生产规模的不同,毛坯的锻造方式分为自由锻造和模锻两种,中小批生产的采用自由锻、大批生产时采用模锻。
第二章零件图的加工工艺分析图图2轴类零件图2.1工件的工艺分析图2所示是本设计的轴类零件图。
该零件表面由圆柱、圆锥、顺圆弧、逆圆弧以及螺纹等表面组成,零件图尺寸标注完整,加工要求明确,零件材料为45号钢,比较容易切削加工。
通过以上分析,采用以下工艺措施。
对图样上带公差的尺寸,因公差的尺寸较小,故编程地不必取平均取,而取基本尺寸即可。
左右端面均为多个尺寸的设计基准,相应工序加工前,应该先将左右端面车出来。
2.2工件装夹方案及设备选择设定零件的轴线为定位基准,以工件右端面与零件轴线的交点为工件坐标系的原点,左端采用三爪自定心卡盘定心夹紧。
加工顺序的确定按由内到外、由粗到精、由近到远的原则确定,在一次装夹中尽可能加工出较多的工件表面。
由于该零件为单件小批量生产,走刀路线设计不必考虑最短进给路线或最短空运行程路线,外轮廓表面车削走刀路线沿零件轮廓顺序进行。
根据被加工零件的外形和材料等条件,选用数控车床。
2.3夹具的选择数控车床上的夹具主要有两类:
一类用于盘类或短轴类零件,工件毛坯装夹在带可调卡爪的卡盘(三爪、四爪)中,由卡盘传动旋转;另一类用于轴类零件,毛坯装在主轴顶尖和尾架顶尖间,工件由主轴上的拨动卡盘传动旋转。
夹具的定位与安装:
一般使用。
装夹方便,自动定心方便,但夹紧力较小。
适用于中尺寸、形状规则、长度不宜过长的工件。
提高夹持精度的措施。
使用铸铁套圈。
精加工的表面不至于被卡爪夹坏,工作时套圈套在工件上,卡盘夹紧套圈。
铸铁套圈也适于薄壁工件镗孔时的装夹,因为它增加了卡爪和工件的接触面积,可以减少装夹力引起的工件变形。
在本设计中,由于工件为轴类零件。
所以我们选择三角卡盘和顶尖。
2.4加工顺序及进给路线加工顺序按由粗到精、由近到远的原则确定。
先车削加工工件右端面后车削加工工件外圆,从右到左进行粗车(留0.30.2mm精车余量),然后从右到左进行精车,最后车削螺纹。
数控车床Fanuc-0I系统的循环指令能以设定的切削参数和进刀路线对零件表面轮廓进行粗、精加工(图3)。
图3车削加工路线2.5选择切削刀具在数控车床加工中,产品质量和生产率在相当大的程度上受到刀具的制约。
虽然数控刀具的切削原理与普通车床刀具基本相同,但由于数控加工特性的要求,在刀具参数的选择上,特别是切削部分的几何参数选择上,就要满足一定的要求,才能达到数控车床的加工要求,充分发挥数控车床的优势。
金属切削过程中,刀具切削部分在高温下承受着很大切削力与剧烈摩擦。
在断续切削工作时,还伴随着冲击与振动,引起切削温度的波动。
因此,在刀具选择时,刀具必须满足强度高、精度高、适应高速和大进给量切削、可靠性好、使用寿命长、断屑及排屑性能好等性能。
一般刀具材料在室温下应具有60HRC以上的硬度。
材料硬度越高耐磨性越好,但抗冲击韧性就相对降低。
所以要求刀具材料在保持有足够的强度与韧性条件下,尽可能有高的强度与耐磨性。
高耐磨性是指在高温下仍能维持刀具切削性的一种特性,通常用高温硬度值来衡量,也可用刀具切削时允许的耐热温度值来衡量。
它是影响刀具材料切削性能的重要指标。
耐热性能越好的材料允许的切削速度就越高。
刀具材料还需要较好的工艺性与经济型。
工具钢应有较好的热处理工艺性:
淬火变形小,淬透层深,脱碳曾浅;高硬度材料需要有可磨削加工性;需焊接的材料,宜有较好的导热性与焊接工艺性。
此外,在满足以上性能要求时,宜尽可能满足资源丰富,价格廉价的要求。
根据零件的加工精度和表面的粗糙度要求及工件材料的性质选择适当的刀具。
经分析,本零件需用粗车刀(端面,圆弧)、精车刀(端面,圆弧)、螺纹刀。
2.6选择切削用量切削用量包括主轴转速(切削速度)、切削深度或宽度、进给速度(进给量)等。
对于不同的加工方法,需选择不同的切削用量。
合理选择切削用量的原则是:
(1)粗车时,首先考虑选择一个尽可能大的背吃刀量ap,其次选择一个较大的进给量f,最后确定一个合适的切削进度v。
增大背吃刀量ap可使走刀次数减少,增大进给量f有利于断屑,因此根据以上原则选择粗车切削用量对于提高生产效率,减少刀具消耗,降低加工成本是有利的。
(2)精车时,加工精度和表面粗糙度要求较高,加工余量不大且均匀,因此选择较小(但不太小)的背吃刀量ap和进给量f,并选用切削性能高的刀具材料和合理的几何参数,以尽可能提高切削速度v。
(3)零件的加工高度H(1/4-1/6)RD,以保证刀具有足够的刚度。
背吃刀量ap(mm),亦称切削深度。
背吃刀量取1mm,主要根据机床、夹具、刀具和工件的刚度来决定。
在刚度允许的情况下,应以最少的进给次数切除加工余量,最好一次切除余量,以便提高生产效率。
精加工时,则应着重考虑如何保证加工质量,并在此基础上尽量提高生产效率。
吃刀深度:
粗车时ap=3mm;精车时ap=0.25mm。
主轴转速:
车削直线和圆弧轮廓时,根据零件材料与加工要求查得,粗车切削速度Vc=90mm/min,精车切削速度Vc=120mm/min,按公式Vc=dn/1000,计算粗车主轴转速n=500r/min,精车主轴转速n=1200r/min。
车削螺纹主轴转速