CaOSiOAlOMgO渣系生产高强合金结构钢MgOAlO夹杂物的形成研究样本Word文档格式.docx
《CaOSiOAlOMgO渣系生产高强合金结构钢MgOAlO夹杂物的形成研究样本Word文档格式.docx》由会员分享,可在线阅读,更多相关《CaOSiOAlOMgO渣系生产高强合金结构钢MgOAlO夹杂物的形成研究样本Word文档格式.docx(9页珍藏版)》请在冰豆网上搜索。
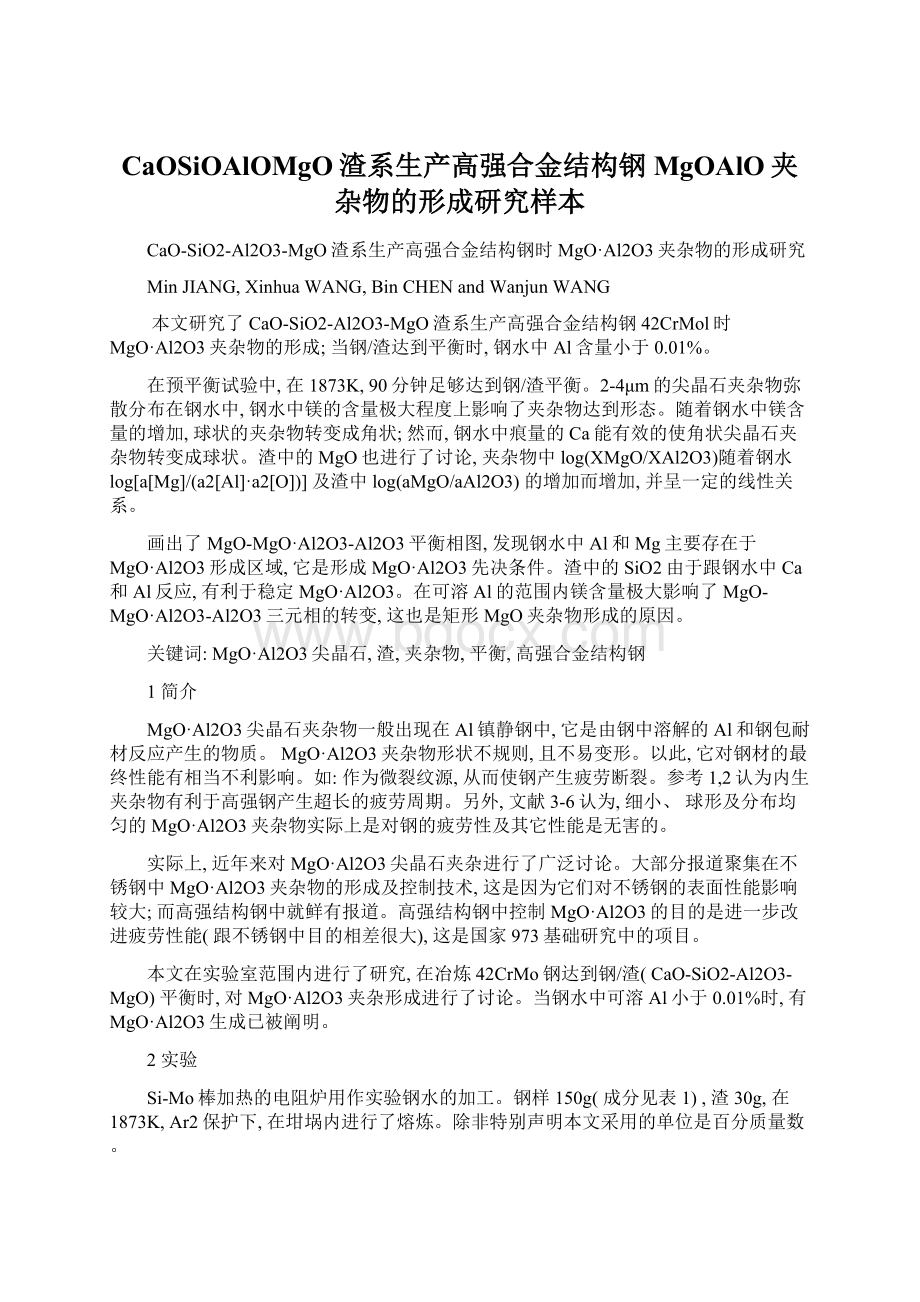
渣中的SiO2由于跟钢水中Ca和Al反应,有利于稳定MgO·
Al2O3。
在可溶Al的范围内镁含量极大影响了MgO-MgO·
Al2O3-Al2O3三元相的转变,这也是矩形MgO夹杂物形成的原因。
关键词:
MgO·
Al2O3尖晶石,渣,夹杂物,平衡,高强合金结构钢
1简介
MgO·
Al2O3尖晶石夹杂物一般出现在Al镇静钢中,它是由钢中溶解的Al和钢包耐材反应产生的物质。
Al2O3夹杂物形状不规则,且不易变形。
以此,它对钢材的最终性能有相当不利影响。
如:
作为微裂纹源,从而使钢产生疲劳断裂。
参考1,2认为内生夹杂物有利于高强钢产生超长的疲劳周期。
另外,文献3-6认为,细小、球形及分布均匀的MgO·
Al2O3夹杂物实际上是对钢的疲劳性及其它性能是无害的。
实际上,近年来对MgO·
Al2O3尖晶石夹杂进行了广泛讨论。
大部分报道聚集在不锈钢中MgO·
Al2O3夹杂物的形成及控制技术,这是因为它们对不锈钢的表面性能影响较大;
而高强结构钢中就鲜有报道。
高强结构钢中控制MgO·
Al2O3的目的是进一步改进疲劳性能(跟不锈钢中目的相差很大),这是国家973基础研究中的项目。
本文在实验室范围内进行了研究,在冶炼42CrMo钢达到钢/渣(CaO-SiO2-Al2O3-MgO)平衡时,对MgO·
Al2O3夹杂形成进行了讨论。
当钢水中可溶Al小于0.01%时,有MgO·
Al2O3生成已被阐明。
2实验
Si-Mo棒加热的电阻炉用作实验钢水的加工。
钢样150g(成分见表1),渣30g,在1873K,Ar2保护下,在坩埚内进行了熔炼。
除非特别声明本文采用的单位是百分质量数。
在1873K保持一定时间后(平衡时间已经过预平衡实验证实),从坩埚中取出进行快速水冷。
2.1预平衡实验
在平衡实验之前进行了预平衡实验,以找出达到钢/渣平衡所需时间。
在1873K,坩埚中钢渣保持不同的时间,然后对试样进行水冷,再分别对钢渣试样进行制备,进行化学成分分析。
2.2平衡实验
在找出钢/渣平衡时间之后,在1873K进行了平衡实验,实验过程中在静态状态下进行,使得钢中氧化物自然上浮。
试样后的试样进行了快速水冷。
钢、渣试样分别制备并进行了化学分析;
在试样截面上随机选择了30个夹杂物进行了SEM-EDS分析,并统计夹杂物的形貌、尺寸、化学成分等信息。
在当前实验中,把0.5g金属试样、10cm3水和5cm3HNO3放入到200cm3的烧杯中,然后加热直到没有气泡逸出。
然后烧杯中加入5cm3HCL,并继续加热以熔化试样。
实验中使用的水和酸都是高纯度的。
试样熔化之后,过滤到100cm3的烧瓶中,滤纸上保留了残留物。
试样中的Al含量(冷却到室温)看做是酸溶铝,进行了ICP发射光谱分析。
并采用此法分析了钢中酸溶Ca和Mg含量。
但必须指出,酸中也溶解了部分MgO·
Al2O3夹杂,溶解量取决于夹杂物自身的尺寸、数量。
因此,分析的酸溶Al和Mg同实际钢样中有一定差别。
试样中全氧量采用熔化及红外吸收的方法测定,渣子的成分采取x射线荧光光谱分析仪进行分析。
3结果和讨论
3.1达到平衡所需时间
预平衡试验中钢水及渣子的成分见表2。
实验发现,在保持90分钟后钢水中全氧的含量基本稳定。
这表明对于钢水中夹杂物的上浮90分钟已足够。
保持60分钟后,钢水中的Al基本稳定,如图1所示。
能够说90分钟,钢/渣之间足以达到平衡。
3.2钢样中MgO·
Al2O3夹杂的测定
平衡实验后,钢样及渣子的成分见表3。
SEM-EDS结果表明MgO·
Al2O3夹杂弥散分布在钢样中。
特别是,除了No.4实验中角状颗粒外(见图2-8)它们比较细小(2-4μm),球状、均匀分布的颗粒。
尖晶石夹杂物中MgO的含量随着钢水中Mg的增加而升高。
特别是所有钢样中含Mg最高的试样No.6(10ppm)中MgO颗粒多呈矩形。
这种现象后面将进行详细讨论。
显而易见,钢水中Mg含量的增加将会改变尖晶石夹杂的形态,从球状变成尖角状,而夹杂物中痕量的Ca有利于夹杂物呈球状,见图2-8。
3.3铝脱氧平衡
当在钢/渣之间建立起平衡时,钢水中的Al和Mg也同渣建立起平衡,能够用如下反应
表示。
(Al2O3)=2[Al]+3[O].........................
(1)
式中:
Ki是平衡常数;
a[i]是钢中i组分的活度,它以无限稀溶液为标态进行计算;
aj
是渣中j组分的活度,它的标态是纯固态。
[Al]、[O]活度能够经过以下方程计算:
式中:
eji是元素i、j之间的一级相互作用系数,见表4;
参考12的作者推导出在1873k计算Al在CaO-SiO2-Al2O3-MgO渣系中的活度。
其表示式如下:
根据表3中渣子的成分,用等式(5)估算出Al2O3活度,并带入等式
(2)(3)和(4)就能够计算出溶解氧的含量。
从而得到在1873K,钢水中氧与渣中Al2O3达到平衡时的值,见表3。
3.4渣中饱和态MgO行为
文献12画出了MgO在(CaO+MgO)-SiO2-Al2O3准三元系中的等溶线,见图9.。
粗线代表了不同相的边界,细线代表了MgO的等溶线。
从图上能够看出在SiO2值一定时,随着Al2O3含量的增加,含MgO饱和相中MgO的溶解量增加,一直到达MgO-MgO·
Al2O3双饱和相边界,其后在MgO·
Al2O3饱和相中开始递减。
图9中三角形表示了表2中所列渣子的成分,实验No.1和No.3中渣子的成分分别靠近图中MgO·
Al2O3饱和相的MgO和C2S边界。
这里MgO的溶解度约5-10%。
由于MgO在No.1和No.3渣样中的含量分别是7.38%、6.98%,能够看做是1。
No.5、No.7实验中,渣子的成分靠近MgO-MgO·
Al2O3相边界,此处MgO溶解量是10-15%。
No.5、No.7实验中,渣中MgO含量是11.5-12.31%。
此两个渣中MgO活度也能够看做1。
至于其它渣样,MgO含量高于其溶解度,因此这些渣中MgO活度也看做为1。
3.5钢/渣界面及MgO·
Al2O3夹杂物之间的平衡
根据文献16,夹杂物的成分作为钢成分和温度的函数,只要在钢和夹杂物之间建立起平衡,就能够经过热力学计算来估算其值。
在夹杂物/钢/渣平衡态下,夹杂物的成分理论近似于渣子成分,但又仿佛不可能。
文献17实验证明了钢/夹杂物之间的反应很快,以至于在夹杂物和钢水之间能够建立起局部平衡。
理论上,夹杂物钢水之间的平衡可用方程6-9表示。
经过方程7-10能够推导出等式11,即夹杂物成分能够表示为溶解氧、Mg、Al的活度,MgO和Al2O3的活度系数及温度的函数。
式中,Xi和γi分别是夹杂物中i元素的摩尔分数及活度系数。
因此,当钢水中成分对方程11中活度系数影响不大时,在某一固定温度下,夹杂物中MgO和Al2O3浓度比率的对数,log(XMgO/XAl2O3)和log[a[Mg]/(a2[Al]·
a2[O])],是带有一个单位斜率的线性关系。
在1873K,观测到的log(XMgO/XAl2O3)和log[a[Mg]/(a2[Al]·
a2[O])]之间的关系如图10所示,用分散的实心圆点表示。
虚线是在1873K回归分析得到的实验数据的曲线。
同时发现,观测到的log(XMgO/XAl2O3)和log[a[Mg]/(a2[Al]·
a2[O])]也呈现良好的线性关系,其斜率约为0.65。
如上所述,MgO的活度可看做1。
渣中氧化铝的活度能够经过方程10计算。
在1873k观测到的log(XMgO/XAl2O3)同log[aMgO/aAl2O3]关系,见图11,实心正方形所示。
虚线是经过回归分析得到的实验数据曲线。
它们同样存在良好的线性关系,斜率约为0.7。
此处必须指出,由于No.6钢样中SEM-EDS分析的夹杂物是纯MgO,XAl2O3值是零,logXAl2O3无意义,因此,图10和11中的数据点是6个而不是7个。
两个原因能说明图10和11中为什么数据点分散分布以及为什么它们斜率不一致。
渣中SiO2极大影响夹杂物中MgO含量的原因,因此,当前研究中尖晶石中MgO含量不但取决于Mg含量,而且依赖于渣中SiO2。
这就是造成数据点分散分布及回归分析曲线的斜率不一样的原因。
3.6MgO/MgO·
Al2O3/Al2O3平衡相图
为了研究MgO/MgO·
Al2O3和MgO·
Al2O3/Al2O3边界,采用热力学计算以得到钢中这三个不同相的平衡相图。
使用的方程是12-17。
计算MgO/MgO·
Al2O3边界是12-14(参考文献19)
计算MgO·
Al2O3/Al2O3边界是15-17(参考文献19)
根据参考20,当在1873K计算MgO/MgO·
Al2O3边界,MgO·
Al2O3活度取0.8,由于Al2O3在MgO溶解度很低,MgO活度取0.99。
当计算MgO·
Al2O3/Al2O3边界,活度取0.47,由于MgO几乎不溶于Al2O3,Al2O3活度取1。
在当前研究中,当计算Mg的活度系数时,氧浓度被考虑进去。
同Mg相比,在活度计算中,由于eOAl原小于eOMg溶解氧量的影响能够忽略。
带入方程3、8及14、17能够得出平衡相图,见图12。
当前研究中,在溶解铝的范围内,能够发现钢水中少量Mg的增加将促进MgO和MgO·
Al2O3的转换。
显然,钢水中Mg和Al的量主要存在于尖晶石形成的区域,这是MgO·
Al2O3夹杂形成的主要原因。
在No.6实验中,如上所讨论的,MgO夹杂物主要是矩形,它的数据点(粗箭头所示)位于MgO/尖晶石边界的右侧。
图形与实验的数据结果相当吻合。
文献21,在假设在脱氧过程中尖晶石是理想的固溶体条件下,评估了钢水中尖晶石夹杂物稳定形成区域。
当钢水中Al含量低于0.001时,MgO夹杂在钢水中直接形成。
然而,在当前研究中,由于在实验开始,钢水中没有Mg存在,故没有MgO的直接生成。
所有的MgO夹杂来自于MgO·
尖晶石夹杂区域窄于文献21所预测的结果。
文献10、19评估了采用CaO–(SiO2)–Al2O3–MgO–CaF2渣系冶炼304不