宏业生化膜分离操作规程.docx
《宏业生化膜分离操作规程.docx》由会员分享,可在线阅读,更多相关《宏业生化膜分离操作规程.docx(10页珍藏版)》请在冰豆网上搜索。
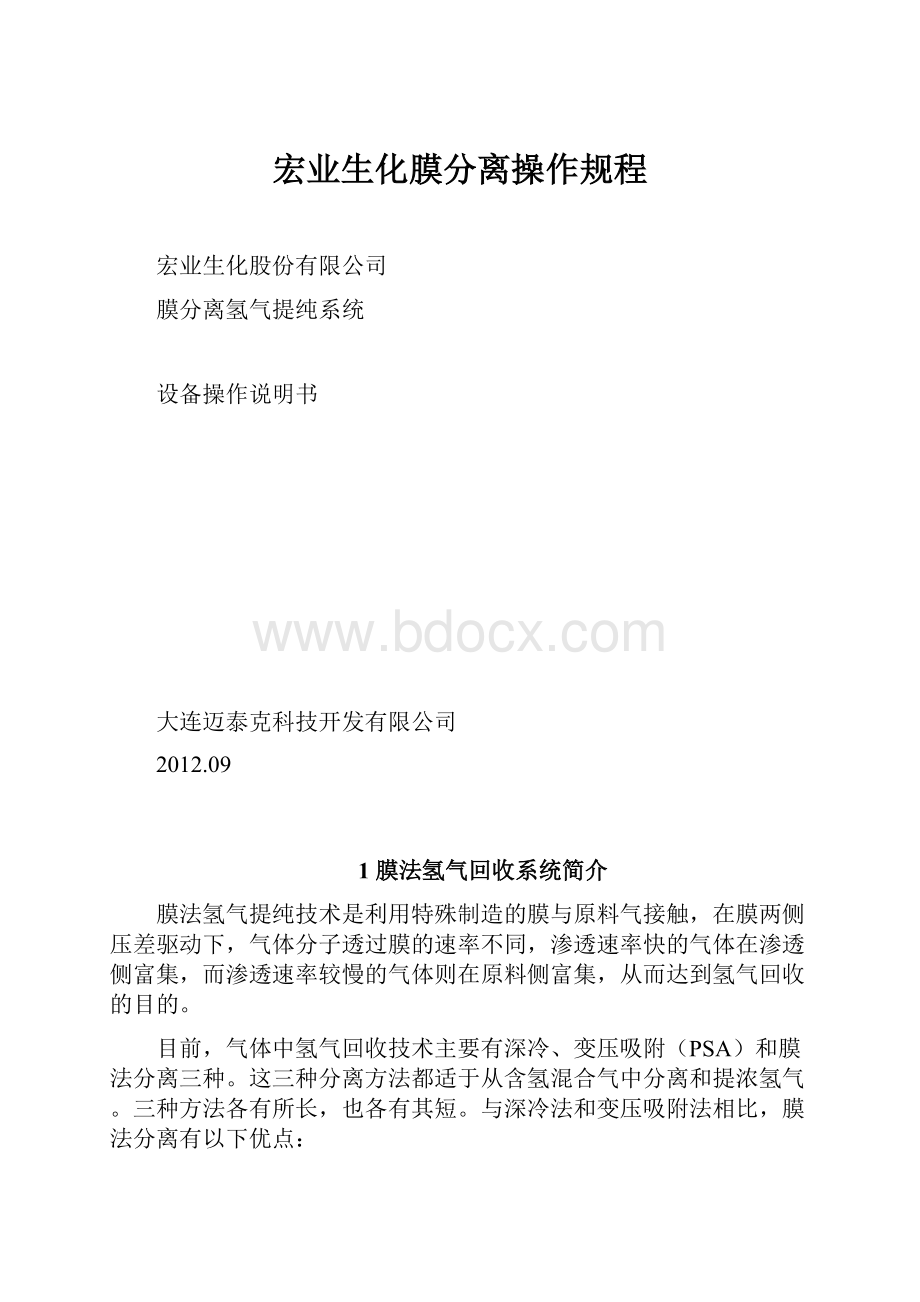
宏业生化膜分离操作规程
宏业生化股份有限公司
膜分离氢气提纯系统
设备操作说明书
大连迈泰克科技开发有限公司
2012.09
1膜法氢气回收系统简介
膜法氢气提纯技术是利用特殊制造的膜与原料气接触,在膜两侧压差驱动下,气体分子透过膜的速率不同,渗透速率快的气体在渗透侧富集,而渗透速率较慢的气体则在原料侧富集,从而达到氢气回收的目的。
目前,气体中氢气回收技术主要有深冷、变压吸附(PSA)和膜法分离三种。
这三种分离方法都适于从含氢混合气中分离和提浓氢气。
三种方法各有所长,也各有其短。
与深冷法和变压吸附法相比,膜法分离有以下优点:
1)分离是物理过程,没有相变,利用原料气的压力进行分离,能耗低。
2)无运动部件,操作简便,使用寿命长。
3)设备结构紧凑、占地面积小。
4)操作弹性大。
5)经济效益显著,投资回收期短。
从80年代以来,膜法气体分离技术迅猛发展,膜法氢气回收技术现已经广泛应用于化肥和石化行业含氢尾气中氢的回收。
2设计依据
本设备是以甲方提供的进气工况条件和产气要求的指标为基础来进行设计的。
2.1进气工况
项目
单位
数据
气量
Nm3/h
2000~5300
压力
MPa.G
2.3
温度
℃
40
组成
CO
mol%
0.1
H2
mol%
95.9
N2
mol%
3
CH4
mol%
1
3工艺流程说明
3.1工艺流程示意图
本设计采用的流程如图3.1所示:
图3.1膜分离氢气提纯工艺流程简图
带控制点的工艺流程图见MTC-12-03-S-G-01。
3.2工艺流程说明
生产系统送来的原料气以40℃的温度和2.3Mpa(G)的压力进入膜分离系统。
首先经过聚结过滤器(X101),把原料气中夹带的雾滴除去,进入加热器
(E101),将原料气加热到50℃左右,以保证进膜前的气体远离露点,否则冷凝下来的液滴会凝聚在膜分离器的纤维表面,从而影响膜分离器的分离效果,甚至对膜造成损害。
加热器采用套管式热交换器,原料气走管程,蒸汽走壳程。
原料气的温度通过调节阀TV101调节蒸汽的流量来控制。
为了安全起见,在加热器之后,进膜前的管路上设有高温报警联锁停车控制回路(TICSA-101)。
原料气经过加热器加热后,进入膜分离器(M101A-D)。
该膜分离器内部装填中空纤维膜丝,原料气从下端底面进入膜分离器。
在纤维芯侧,在恒定压差作用下,氢气以较快的速率透过纤维膜丝,在壳程与纤维芯侧得到富氢产品,称为氢气或渗透气;扩散速率较慢的组分则滞留在纤维芯侧,称为尾气,进入PSA。
进入和离开膜分离系统的气体流量由原料气流量计(FT-101),及尾气流量计(FT-102)测量显示,操作时可通过手动设定PICSA-101的压力及尾气调节阀(PV-102)的阀位来调节氢回收率、渗透气中的氢浓度和进入PSA的压力。
4系统运行
4.1开车前的检查
4.1.1机械设备部分
4.1.1.1检查各设备的进出口管线是否安装正确。
4.1.1.2检查设备是否已经固定在基础上。
4.1.2管道部分
4.1.2.1检查各管路、管件的连接是否正确,与外界管道是否正确连接。
4.1.2.2安全阀、调节阀已经正确安装在系统中。
4.1.2.3各手动阀门的启闭正常,止回阀方向正确。
4.1.2.4检查仪表气源管路,确保所有调节阀的气源线均已经安装完毕。
4.1.2.5安全阀的启跳点,已由生产厂调好,但建议在车间对其启跳点再校验一次。
再次安装安全阀时必须小心注意其位置,不要安错地方。
并从此次开始就要填写维修周期表。
4.1.2.6对所有调节阀进行行程调整,检查动作的满量程及方向。
4.1.2.7关闭膜分离器进气阀V2、V3、,尾气出气阀V9,氢气出气阀V6,以及膜前、后所有阀门,以保护膜分离器。
用氮气对其他管线进行试漏。
4.1.2.8预处理系统管线试漏完毕后,用不含原料气的纯净氮气对膜系统管线试漏,试漏过程中注意管线的压力等级。
4.1.2.9将所有阀门置于关闭位置。
4.1.3电气和仪表
4.1.3.1所有用电设备及仪表均已经上电,并做好静电接地。
电气阀门定位器都接上仪表空气。
4.1.3.2确认所有仪表正确安装,并已经调试完毕,各报警点和联锁点设定在合适的位置。
检查现场压力表是否完整无缺。
4.2氮气置换
确保整个系统在引入任何工艺气体之前,或在与大气相通之前必须用氮气彻底置换,并按以下步骤进行:
4.2.1预处理系统
4.2.1.1检查并关闭膜分离装置的所有工艺阀门,排净阀及放空阀。
4.2.1.2打开仪表切断阀。
所有压力表阀打开后,压力指示为“0”,确保系统完全泄压。
4.2.1.3向系统送氮气,打开V15、V16,待预处理系统升压至10MPa时。
关闭氮气供应管路上的截止阀V15、V16,停十分钟。
4.2.1.4慢慢打开放空管线VT102上的阀V26,待系统压力接近零时关闭。
4.2.1.5用氮气重复升压,降压,对系统进行置换。
重复上述操作,直至置换排出气体中氧含量低于工厂标准。
一般需三次升压、降压操作。
4.2.1.6要置换聚结过滤器底部管道,打开截止阀V18、V21及LV101。
4.2.1.7当需要泄压时,通过VT102上的阀V26泄压。
4.2.2膜分离器
4.2.2.1打开进膜气体旁通管线上的节流阀V2,再打开膜前、后阀门V4、V5、V7,慢慢打开注氮阀V15、V16,向膜分离器送氮气(确保氮气中不含原料气)。
对膜分离器的升压速度不要超过0.3MPa/min。
当膜分离器压力接近10MPa时,关闭V15、V16,停十分钟通过渗透气放空阀V27泄压(注意缓慢泄压,防止膜分离器内压力突升突降)。
4.2.2.2重复上述操作,直至置换合格。
4.2.2.3当膜分离器的置换完成后,除仪表切断阀外,所有阀门关闭。
4.2.2.4关闭去预处理的氮气管线的截止阀V15、V16。
4.2.2.5除维修要求外,预处理及膜分离器可处于氮气压力保护下。
当需要泄压时,通过渗透气至放空管线VT103上的阀V27泄压。
(注意缓慢泄压)
4.3开车步骤
在预处理的开车平稳后,温度、压力达到要求,方可切入膜分离器管线,投入运行。
4.3.1预处理开车
系统用氮气吹扫、置换合格后,准备开车,开车步骤如下:
4.3.1.1确认与外界接口的管线联通且阀门开启。
4.3.1.2检查压缩空气管线,确保仪表用气,仪表空气压力≥0.4MPa。
4.3.1.3关闭氮气进口阀门V15、V16。
4.3.1.4关闭所有管线手动阀门和自动阀门。
4.3.1.5确认仪表的切断阀(表根阀)、变送器的切断阀都已打开。
4.3.1.6确信处于膜分离器入口的闸阀V3和旁通阀V2是关闭的。
(重要)
4.3.1.7打开过滤器排液口阀V18、V21,蒸汽进口阀V10、V11、V14,疏水器前后切断阀。
4.3.1.8膜前放空阀V26稍开。
4.3.1.9稍开合成原料气进气阀V1,开始对预处理系统进行升压和升温。
4.3.1.10对预处理的升压和升温操作可以采用两种方法,一种是手动给定PICSA-101和TICSA-101的设定值,系统压力和温度稳定后再增加设定值。
PICSA-101设定值应以较小的幅度逐步增加,控制升压速率不超过0.3MPa
/min。
TICSA-101的温度设定值也应以较小的幅度逐步增加,以免系统超温。
4.3.1.11对预处理的升压和升温操作也可以采用另外一种方法,手动给定PV-101和TV-101的阀位。
在控制室将预处理压力设定值设为2.3MPa(G)、膜前温度设定值设为50℃。
PV-101、TV-101控制方式设为手动并给定较小的阀位,控制升压速率不超过0.3MPa/min。
4.3.1.12设定过滤器液位设定值为40%,同时将控制方式置于“自动”。
4.3.1.13观察过滤器上的差压值PDIA-101为0.01~0.015MPa,随着过滤器工作时间的变长,差压值会逐渐的增大,当差压值超过0.1MPa时,证明过滤器性能不好,有堵塞状况,此时应该停车清洗或更换过滤器滤芯。
4.3.1.14检查所有设备及仪表。
疏水阀工作是否正常。
4.3.1.15调节预处理放空阀V26开度,建立原料气流量。
4.3.1.16打开过滤器底部排放阀V28,观察在预处理开车阶段,原料气是否干净,根据具体的实际情况决定过滤器底部排放阀V28的开、闭状态。
4.3.1.17一旦预处理部分的原料气压力建立起来,并且温度也达到了设计要求,各项指标都平稳,这时预处理开车完成,准备进行膜分离器开车。
4.3.2膜分离器开车
注意:
在开车及膜分离器运行期间,必须避免对膜分离器快速升压或流量骤增。
膜分离器的原料气在温度、压力高于限定值时工作,可对膜分离器造成损害。
预处理开车成功后,可以准备膜分离器的运行,运行步骤如下:
4.3.2.1打开膜分离器前后阀门V4、V5、V7(开车时根据实际的气量决定开几组膜分离器)。
4.3.2.2慢慢打开进膜旁路阀V2,给膜分离器逐步升压。
观察膜前压力表PI-104,控制升压速率不要超过0.3MPa/min。
4.3.2.3当膜内渗透侧(即氢气侧)压力PI-106高于系统外管网的压力PI-107时,慢慢打开V6,使渗透气送入外管网,PI-107稳定在0.5MPa。
4.3.2.4继续缓慢向膜内充压,当膜前压力接近设定压力时,现场打开尾气侧手动阀V9,将尾气调节阀PV-102置于较小开度。
4.3.2.5缓慢打开膜前手动闸阀V3,关闭进膜的旁路阀V2和膜前放空阀门V26,在此过程中注意观察膜前压力控制是否稳定,防止压力突升对膜分离器造成损害。
4.3.2.6一旦气体全部切换至膜分离器,调整PICSA-101的压力设定值和调整调节阀PV-101的开度至希望的原料气流量和压力。
4.3.2.7系统运行稳定之后,按照PSA要求把PICSA-102的压力设定值慢慢提高至指标。
运行时可调整膜前压力PICSA-101及加热温度TICSA-101的设定值使其满足氢气纯度和氢气回收率的要求。
做好各项记录。
取样分析原料气入口A-101,过滤器滤液A-106,膜分离器原料气A-102,氢气A-103、A-104,尾气A-105。
分析氢气、一氧化碳、甲烷、液体成分等指标。
4.4停车步骤
正常停车时,应先停膜分离器,然后停预处理。
4.4.1正常停车
4.4.1.1控制室将运行模式切换为“停止”,此时PV-101、TV-101、PV-102、LV-101自动关闭,系统进入停车状态。
4.4.1.2关闭膜进口阀V3、膜进口旁通阀V2、进系统阀V1及尾气出口阀V9。
切断系统并确认。
(重要)
4.4.1.3当膜内压力降到高于渗透气压力0.5MPa时,关闭渗透气的阀门V6,并打开渗透侧放空阀V27,给膜分离器卸压。
4.4.1.4若短时间停车,膜内可保有一定压力。
4.4.1.5打开膜前放空阀V26,卸掉膜前压力。
4.4.1.6若长时间停车预处理系统卸压后,打开过滤器排液阀V28及V19,排掉过滤器中残存的液体,用氮气对系统置换并用氮气保护。
4.4.1.7关闭蒸汽进口阀V10,打开蒸汽管线排污阀V12。
4.4.1.8检查各阀门状态,除膜前放空V26,过滤器排液阀V28及V19,保持开启外,其余阀门关闭。
4.4.2联锁停车
由原料气压力高于上上限,过滤器液位高于上上限,原料气温度高于上上限,引起的联锁停车,同正常停车。
注:
(1)设定值可根据现场工况调整。
(2)所有报警值和联锁值可以调整。
操作参数设定值表
序号
名称
设定值/显示值
报警上上限
报警上限
报警下限
报警下下限
1
PICSA-101
2.3MPa
2.6MPa
2.5MPa
─
─
2
LICSA-101
─
60%
50%
─
─
3
TICSA-101
50℃
60℃
55℃
─
─
4
PICSA-102
2.1MPa
─
─
1.8MPa
—
5
PDIA-101
─
─
100KPa
─
─
如有侵权请联系告知删除,感谢你们的配合!