国际低合金会议论文08热机械控制工艺对高强度低合金钢组织和性能的影响.docx
《国际低合金会议论文08热机械控制工艺对高强度低合金钢组织和性能的影响.docx》由会员分享,可在线阅读,更多相关《国际低合金会议论文08热机械控制工艺对高强度低合金钢组织和性能的影响.docx(16页珍藏版)》请在冰豆网上搜索。
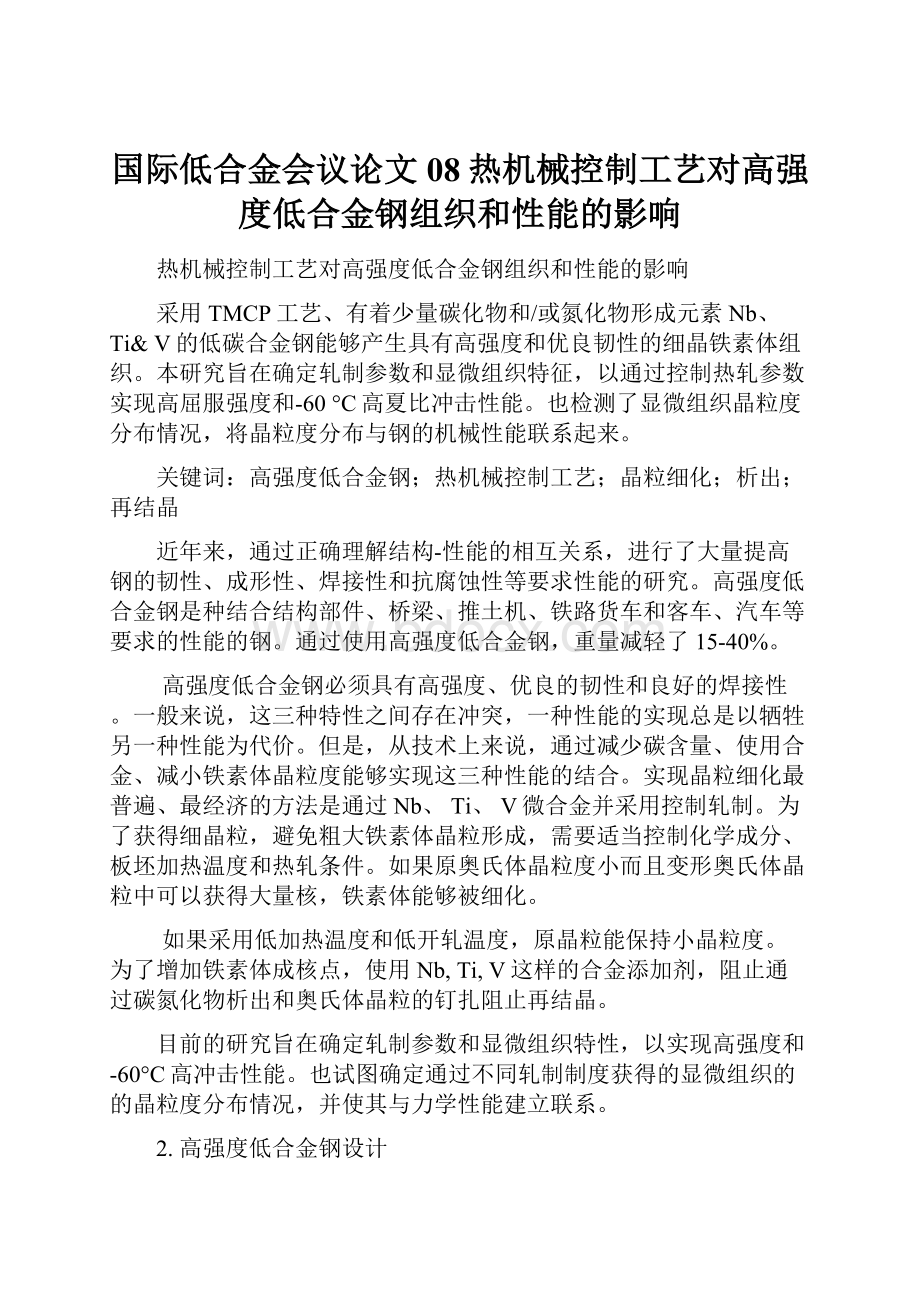
国际低合金会议论文08热机械控制工艺对高强度低合金钢组织和性能的影响
热机械控制工艺对高强度低合金钢组织和性能的影响
采用TMCP工艺、有着少量碳化物和/或氮化物形成元素Nb、Ti&V的低碳合金钢能够产生具有高强度和优良韧性的细晶铁素体组织。
本研究旨在确定轧制参数和显微组织特征,以通过控制热轧参数实现高屈服强度和-60°C高夏比冲击性能。
也检测了显微组织晶粒度分布情况,将晶粒度分布与钢的机械性能联系起来。
关键词:
高强度低合金钢;热机械控制工艺;晶粒细化;析出;再结晶
近年来,通过正确理解结构-性能的相互关系,进行了大量提高钢的韧性、成形性、焊接性和抗腐蚀性等要求性能的研究。
高强度低合金钢是种结合结构部件、桥梁、推土机、铁路货车和客车、汽车等要求的性能的钢。
通过使用高强度低合金钢,重量减轻了15-40%。
高强度低合金钢必须具有高强度、优良的韧性和良好的焊接性。
一般来说,这三种特性之间存在冲突,一种性能的实现总是以牺牲另一种性能为代价。
但是,从技术上来说,通过减少碳含量、使用合金、减小铁素体晶粒度能够实现这三种性能的结合。
实现晶粒细化最普遍、最经济的方法是通过Nb、Ti、V微合金并采用控制轧制。
为了获得细晶粒,避免粗大铁素体晶粒形成,需要适当控制化学成分、板坯加热温度和热轧条件。
如果原奥氏体晶粒度小而且变形奥氏体晶粒中可以获得大量核,铁素体能够被细化。
如果采用低加热温度和低开轧温度,原晶粒能保持小晶粒度。
为了增加铁素体成核点,使用Nb,Ti,V这样的合金添加剂,阻止通过碳氮化物析出和奥氏体晶粒的钉扎阻止再结晶。
目前的研究旨在确定轧制参数和显微组织特性,以实现高强度和-60°C高冲击性能。
也试图确定通过不同轧制制度获得的显微组织的的晶粒度分布情况,并使其与力学性能建立联系。
2.高强度低合金钢设计
高强度低合金钢的设计基于下列准则:
*一直以高屈服强度和低冲击转换温度作为目的。
一直确定合金元素类型和数量并牢记在心。
选择建立在屈服强度每增加一个单位,冲击转换温度最小增加量的基础上。
*通过低碳当量、最小MS温度降低量、低可溶解溶质含量,实现优良的焊接性能。
同样要求非金属夹杂物的含量最小,以防止层状断裂。
*热轧薄型钢的良好成形性。
*富有竞争力的价格
可以看出,为了获得较低冲击转换温度,通常选择低碳铝镇静晶粒细化高锰钢更易。
由于铝是一种晶粒细化剂,能形成氮化铝从而消除大量Ni,铝同样受青睐。
限制锰含量原因是锰含量太高会导致转换温度降低,并导致贝氏体的产生。
由于内应力和冲击性能,二者均会影响屈服强度。
因此锰含量一般限制为1.5%。
从低转换温度、更好的冲击能量、热影响区裂纹敏感性和韧性的角度考虑,应采用低碳含量。
应避免上贝氏体和马氏体的形成。
Ni含量必须保持最低水平,以获得较好的冲击性能并避免劈裂。
硫和氧含量也应尽可能保持最低水平,以提高横向冲击功。
最好将硫化物夹杂的形成改为球状。
磷含量需要保持低于0.030%的水平,以实现较好的性能。
硅、锡、磷这样的固溶硬化元素和间隙充溶氮使流动应力和硬化速率增加,但对延性参数有着各种影响。
硫对减少整体延性的影响体现出第二相粒子比如MnS的影响。
热轧带钢通常要求冷成形为结构构件。
通过各种工艺,钢的成形能力取决于:
1)对于一个给定的应变的低应力,支配着成形载荷
2)加工硬化速率
3)缩颈和塑性失稳前最大均匀延性
4)可获得的总延性
3.0微合金元素:
众所周知,微合金元素通过下列强化机理使将钢材获得强度和韧性:
晶粒细化
析出硬化和弥散硬化
微合金元素除“溶质拖曳作用”外,还通过第二相对显微组织产生影响。
由于每种元素和化合物的溶度积和力学性能不同,所以存在特性的差异,因此每种合金元素具有特定的优点或添加目的。
Ti与氧和Ni有着密切的关系,从而减少钢水中有害的氧和Ni。
此外,Ti还形成细小析出物TiC/TiN和TiCN。
加热过程中,精细分散、稳定的析出物能够控制奥氏体晶粒度,引起晶粒细化和析出硬化。
V在加热温度时在奥氏体中溶解,因此不对奥氏体晶粒度产生影响。
但是碳化钒和碳氮化物在奥氏体向铁素体转换过程中析出。
形成的析出物非常细小,因此提高了强度和韧性。
通过输出辊道上的加速冷却可以进一步减小析出物的尺寸。
从溶质拖曳作用的角度看,Nb是最有效的微合金元素。
在以下方面,溶质拖曳作用有助于热机控制轧制过程中的晶粒细化:
1.防止道次间隔期间二次晶粒长大。
2.通过NbC析出阻止再结晶的开始。
作为一种微合金元素,Nb对强化的影响两倍于V对强化的影响。
由于加热过程中的奥氏体晶粒度细化,通过控制奥氏体晶粒度,Nb提高了强度和韧性。
其次,Nb阻止了热机轧制过程中奥氏体加工过程中的再结晶。
4.0组织性能关系
屈服强度
Ashley和Orowan从显微组织特点的角度,对微合金钢的屈服强度进行了完整的描述。
他们考虑到弥散的第二相对屈服强度中额外增加部分的量化影响。
ThemodifiedHall-Petchequationis
改性Hall-Petch方程为:
式中,X为析出粒子,即用微米表示的碳化物、氮化物和碳氮化物的直径,是粒子的体积分数。
在该方程式中,有三种种强化因素
1)
为通过有格隙型固溶体和置换型固溶体引起的固溶强化
2)
为晶粒细化引起的强化
3)
为第二相弥散引起的强化
根据上述方程,
直接取决于
,屈服强度
反过来取决于粒子尺寸(1/X)。
当晶粒度为3-5体积比为μm时,0.0003-0.0004的Nb钢使屈服强度增加大约100MPa,超过固溶强化和晶粒细化的增加量。
从图1可清楚看出这种作用。
图2为铁素体晶粒度对屈服强度和冲击转换温度的影响。
图1Assbby-Orowan关系
Fig.2EffectofFerriteGrainSizeontheYieldStressand
ImpactTransitionTemperatureof0.1%CSteel
图2铁素体晶粒度对0.1%C钢屈服应力和冲击转换温度的影响
根据Pickering,普碳钢的屈服强度可在成分的基础上确定
YieldStrength屈服强度(MN/m2)=15.4[3.5+2.1%Mn+5.4%Si+23%Nf+1.13d-1/2]--------------
(2)
根据方程,珠光体对低碳钢的屈服强度几乎没有影响。
游离氮产生较为明显的影响,但是其溶解度有限。
图2示出晶粒细化产生的显著的强化作用。
抗拉强度:
还可借助于皮克林经验公式算出低碳钢的抗拉强度:
Tensilestrength屈服强度(MN/m2)=15.4[19.1+1.8(Mn)+5.4(Si)+0.25(Pearlite)+1.13d-1/2--------------(3)
显然,珠光体和晶粒细化有助于抗拉强度的提高。
冲击转换温度:
冲击转换温度可描述为:
ITT°C=-19+44(Si)+700(Nf)-1/2+2.2(Pearlite)–11.5d1/2
这表明,晶粒细化提高了韧性并引起冲击转换温度的显著下降。
硅和游离氮提高了ITT,游离氮产生有害影响。
珠光体同样产生有害影响。
显然多边形铁素体晶粒度提高了屈服应力,也降低了冲击转换温度。
这样晶粒细化是最适宜的强化机理。
在高强度合金钢中,这可通过控制轧制实现。
本文重点论述控制轧制参数的优化。
图3示出高强度低合金钢中要求的性能、冶金因素和生产工艺参数之间的关系。
5.0高强度低合金钢的变形行为
比较了两种成分相似的钢的变形行为,一种是普碳钢,一种是V微合金钢。
表1为两种钢的化学成分。
表1所研究钢的化学成分
为了理解高强度低合金钢的变形行为,将普碳钢(C-钢)和V微合金钢(V-钢)处于相似的温度、变形时间和保温时间条件下。
细晶要求是代表高强度、低韧脆转换温度的高强度低合金钢的基本要求。
强碳化物形成元素的出现:
1)防止晶粒长大。
2)通过析出提高强度。
两种研究用钢为铝镇静钢。
采用TM研究析出物的特性。
在1204°C将一个热电偶插入钢中,然后在表2示出的轧制温度下采用50%的压下量。
图3高强度钢要求的性能、冶金因素和冶金方法之间的关系
轧制至指定温度后,以不同的保存时间(0、12、120分钟)将试样保存在马弗炉中,然后在通过水淬或空冷冷却至室温之后,比较显微组织的变化。
在轧制温度时未给定保温时间。
表2研究中采用的热机械处理
热轧和等温处理后C钢的微观结构变形行为如图4光学显微镜所示。
图5示出V钢的轧制行为。
Fig5.SchematicillustrationofbehaviorexhibitedbytheausteniteinV-Steel
图5V钢中奥氏体展示行为示意图
普碳钢(C钢)与微合金(V钢)的比较揭示出下列内容:
a)1121°C轧制使两种钢都出现等轴晶粒,随着两种钢的保温时间的增加,晶粒变得粗大,但V钢的粗化现象无C钢严重。
b)1038°C轧制使两种钢出现很少或不出现晶粒粗化现象。
图6示出两种钢在1121°C和1038°C的行为。
图6保温时间对两种钢奥氏体晶粒直径的影响
c)954°C轧制导致一些柱状晶粒和细小的等轴晶粒的混合物的出现。
在碳钢中,随着保温时间增加,柱状晶粒被等轴晶粒代替,但在V钢中未观察到这种现象。
d)871°C轧制,保温3分钟后,出现粗大和极度拉长的晶粒。
e)788°C轧制导致更多柱状晶粒出现。
TEM显微图片显示出1038°C时显示动态再结晶的AlN析出物。
基于上述情况,最好对三种情况下高强度低合金钢的变形行为进行分析:
I区:
温度超过1121°C:
在该区,变形过程中发生奥氏体动态再结晶,等温过程中出现晶粒粗化。
碳钢和V微合金钢的变形行为相似。
II区:
温度接近1038°C及其以下:
两种钢开始显示出不同的热轧行为。
在此区间,变形过程中出现奥氏体动态再结晶,但在等温后未观察到晶粒粗化现象。
该区间温度延伸到950°C。
显微组织由粗大的柱状γ晶粒组成,这些晶粒被细小的等轴晶粒包围。
对于C钢,延长保温时间将柱状晶粒变为等轴晶粒,V钢情况不是这样。
II区:
温度为870°C-728°C:
两种钢中新轧制的奥氏体有着相同的较大的柱形晶粒,但C钢中的奥氏体形成内部边界,这些边界在保温期间充当水淬火过程中先共析铁素体成核点。
从V钢中可发现V(CN)在明确定义的亚晶粒结构中大量析出。
因此两种钢的行为的主要区别发生在热轧后的保温期间。
这些V(CN)使奥氏体中形成的亚晶粒结构稳定。
这些亚晶粒结构是奥氏体动态动态回复的结果。
V(CN)在保温时间变得粗大。
所有高强度低合金钢有着相似的变形行为。
仅仅由于析出温度才出现差异。
Ti钢在1020°C出现大面积析出现象。
Nb在945°C出现大面积析出现象。
V钢在871°C出现这样的情况。
高强度低合金钢的变形行为可通过三个区进行明确定义。
I区:
再结晶区γ变形
II区:
非再结晶区变形
III区:
(γ+α)两相区变形
在工业过程中,一般在第一区,总变形为60-65%,但在每道次,通过静态和动态再结晶,不超过15%的粗晶粒被打碎成细晶粒。
在此阶段无析出现象。
控制轧制工艺包括所有三个阶段(I区、I区、III区),如图7所示:
图8加热至1100°C保持3个小时后的显微组织
在第二区,变形带在拉长的未结晶晶粒中形成。
α晶粒在变形带上和γ晶界上成核,产生细晶组织。
(γ+α)的变形产生一个亚结构。
在变形后的冷却过程中,当变形晶粒转变为亚晶粒时,未结晶γ转变为等轴晶粒。
6.0试验工作
通常观察到在高强度低合金钢控制轧制过程中,为了使碳化物和Nb、Vand微合金元素Nb、V和Ti的碳氮化物析出,在轧制之间应当有一个待温期。
在实践中,待温降低了轧机的生产率。
为了避免待温,均热后在1200°C提供一个3小时的初始待温期。
选择三个不同的开轧温度(SRT):
1100°C、1050°C和1000°C。
在其中一个轧制制度中,加热温度从1200°C降低到1100°C,研究了其对最终显微组织和力学性能的影响。
表3给出所有轧制制度使用的钢的化学成分:
将厚度为130mm的板坯轧制为钢材,然后将其锻造成100mm×100mm的横断面。
从这个横断面切割出100x100x200的断面以备轧制。
表4示出轧制制度。
在RHT、SRT、ERT变化的同时,使每道次压下量保持几乎相同水平。
轧制在国防冶金研究实验室(DMRL)内两台轧制能力为300T的两辊可逆式轧机上进行。
辊身直径为600mm。
轧辊最大开度和最小开度分别为100mm和3mm。
轧机速度可在0-80metres/min之间变化,但在试验期间保持40m/min的恒速。
轧制应变速率在6to10s-1之间变化。
钢坯从100mm轧成10mm厚度。
由于回弹效应,最终厚度为12mm。
为了获得原奥氏体晶粒度,将两个试样加热至1200°C和1100°C,然后水淬火。
对试样进行金相、晶粒度和晶粒度分布情况、珠光体含量检测、拉伸试验以及冲击试验。
珠光体含量和晶粒度分布见表5。
7.0结果:
轧制前、加热至1100°C的锻造材料的显微组织见图8。
表5为不同轧制制度的晶粒度分布情况和不同轧制制度下试样中珠光体的含量。
在1100°C的低加热温度时,与1200°C的加热温度时的175μm相比,开轧时的奥氏体晶粒度很小,仅25μm。
调整总变形量,粗轧阶段大约为压下量大约为57%(100-57mm),终轧阶段大约为77%。
820°C时完成轧制,钢板采用空冷。
根据加热至1100°C的CR-A扫描电子显微镜照片,图9显示出晶粒细小,尺寸均匀。
而对于加热至1200°C的CR-B,图10显示出晶粒比较粗大,不均匀,珠光体集中在一些区域。
CR-C,加热至1200°C,待温至1050°C,然后轧制至556°C,也显示出细小的晶粒和均匀的显微组织和晶粒度,图10所示。
第四批,CR-D板坯被加热至1200°C,保温至1000°C,1000°C开轧,700°C终轧。
不同区域的轧制压下率为“再结晶区30%(100-70mm),非结晶区64%(70-25mm),两相区60%(25-10mm)。
钢板从终轧温度开始空冷。
从图11中扫描显微镜照片可以观察到,晶粒度最小,分布非常均匀,但由于低温轧制,出现严重的珠光体连接。
表5示出4种轧制方案的珠光体含量和晶粒度分布。
表6为从拉伸试验和室温和-60°C夏比冲击试验中获得的数据。
表6拉伸试验和冲击试验中获得的性能
观察到,在所有的情况下,都满足Ys(390Mpa)、Ts(510Mpa)和伸长(16%minimum)的要求值。
对于CR-B与CR-D,不满足-60°C的夏比冲击功要求数值(CVN-60-80Joules)。
对于CR-B,粗轧和终轧之间留出待温时间。
获得的粗大的不均匀晶粒度可能由终轧时的轻压下道次引起。
因此,-60°C的CVN低于要求的数值。
在CR-D情况下,轧制在720°C结束,该温度低于两相区的Ar3温度。
采用轧制制度,-60°C的CVN值(37J)较低有如下原因:
1)带状组织的演变
2)显微组织中偏析珠光体
3)低温轧制引起的残余应力
4)厚度方向各项异性和脆化的发展
8.0结论:
1)为了获得较高屈服强度和-60°C夏比冲击数值,晶粒度应细小、均匀分布。
显微组织中珠光体应均匀分布。
2)加热温度保持在1100-1200°C之间,可获得优良的-60°C夏比冲击韧性。
在RHT1200°C,SRT1050°C,1050°C-850°C连续轧制的情况下,获得最佳冲击韧性数值。
3)两相区轧制产生细小的晶粒,但产生下列问题:
a)严重弯曲
b)残余应力
c)厚度方向各向异性和脆化
4)高温时任何阶段的轻压下道次导致出现粗大和不均匀的晶粒,影响-60°C夏比冲击值
5)1050°C-950°C温度范围内待温较好