制动主缸机加工技术研究及改造应用.docx
《制动主缸机加工技术研究及改造应用.docx》由会员分享,可在线阅读,更多相关《制动主缸机加工技术研究及改造应用.docx(8页珍藏版)》请在冰豆网上搜索。
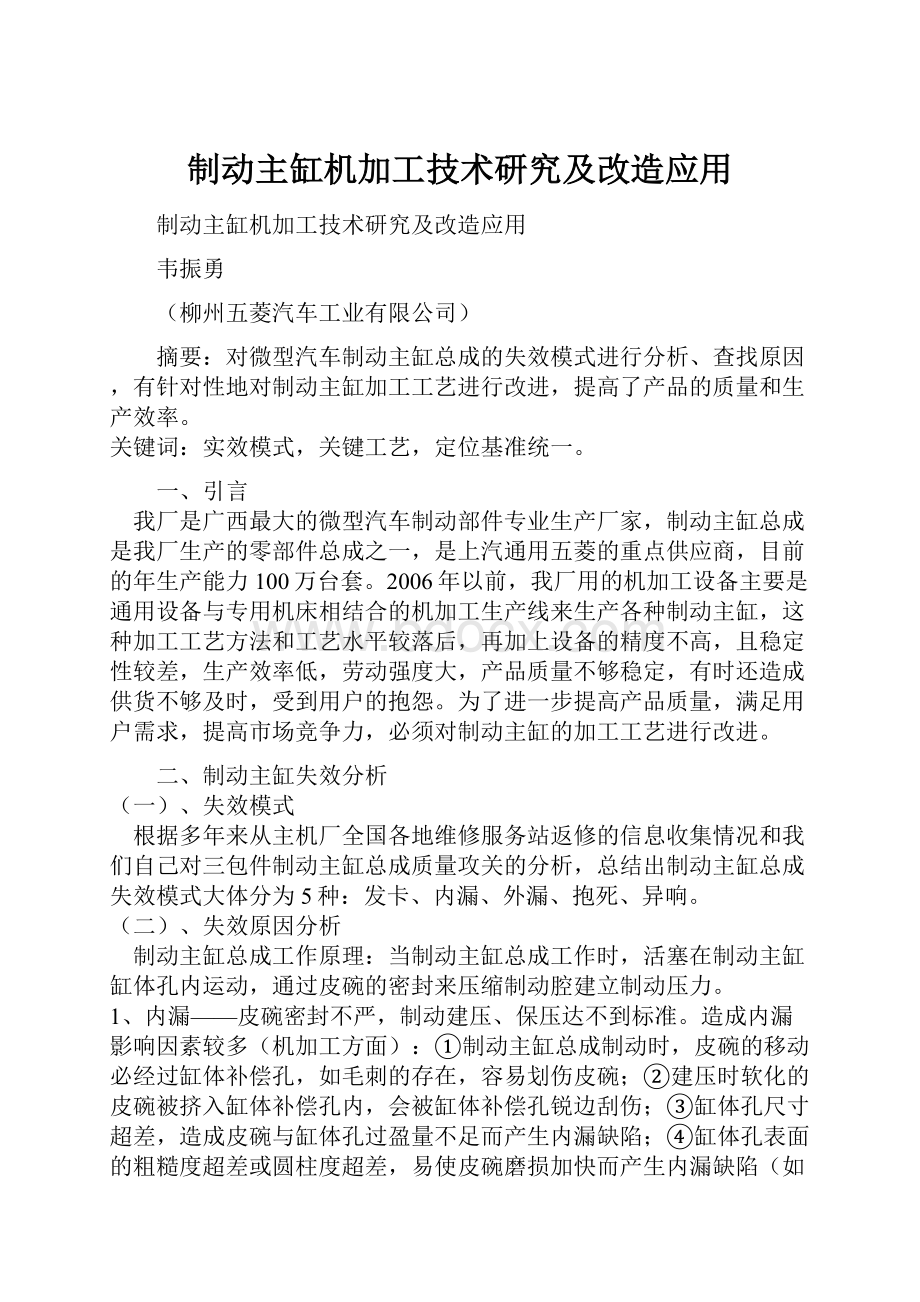
制动主缸机加工技术研究及改造应用
制动主缸机加工技术研究及改造应用
韦振勇
(柳州五菱汽车工业有限公司)
摘要:
对微型汽车制动主缸总成的失效模式进行分析、查找原因,有针对性地对制动主缸加工工艺进行改进,提高了产品的质量和生产效率。
关键词:
实效模式,关键工艺,定位基准统一。
一、引言
我厂是广西最大的微型汽车制动部件专业生产厂家,制动主缸总成是我厂生产的零部件总成之一,是上汽通用五菱的重点供应商,目前的年生产能力100万台套。
2006年以前,我厂用的机加工设备主要是通用设备与专用机床相结合的机加工生产线来生产各种制动主缸,这种加工工艺方法和工艺水平较落后,再加上设备的精度不高,且稳定性较差,生产效率低,劳动强度大,产品质量不够稳定,有时还造成供货不够及时,受到用户的抱怨。
为了进一步提高产品质量,满足用户需求,提高市场竞争力,必须对制动主缸的加工工艺进行改进。
二、制动主缸失效分析
(一)、失效模式
根据多年来从主机厂全国各地维修服务站返修的信息收集情况和我们自己对三包件制动主缸总成质量攻关的分析,总结出制动主缸总成失效模式大体分为5种:
发卡、内漏、外漏、抱死、异响。
(二)、失效原因分析
制动主缸总成工作原理:
当制动主缸总成工作时,活塞在制动主缸缸体孔内运动,通过皮碗的密封来压缩制动腔建立制动压力。
1、内漏——皮碗密封不严,制动建压、保压达不到标准。
造成内漏影响因素较多(机加工方面):
①制动主缸总成制动时,皮碗的移动必经过缸体补偿孔,如毛刺的存在,容易划伤皮碗;②建压时软化的皮碗被挤入缸体补偿孔内,会被缸体补偿孔锐边刮伤;③缸体孔尺寸超差,造成皮碗与缸体孔过盈量不足而产生内漏缺陷;④缸体孔表面的粗糙度超差或圆柱度超差,易使皮碗磨损加快而产生内漏缺陷(如图一所示)。
2、发卡——主要指前活塞与活塞导套配合处卡滞。
前活塞与活塞导套之间配合保持一定的间隙,活塞导套相对前活塞来说起到导向作用,而前活塞沿活塞导套反复运动,如果缸体头部内孔与缸体孔的同轴度超差,将会造成前活塞与活塞导套配合处发生卡滞现象,导致制动主缸总成出现不良故障。
因此必须满足缸体头部内孔与缸体孔同轴度要求。
制动主缸是汽车部件中的法规安全件,其质量是顾客最为关注的产品特性。
通过制动主缸失效模式分析可以看出,制动主缸机加工需重点控制几个关键工艺要求:
两孔同轴度要求、缸体孔圆柱度等要求、缸体补偿孔无锐边及毛刺要求是十分必要的。
(图一)
三、制动主缸关键工艺分析
(一)、关键工艺概述
根据对生产过程的质量控制、生产管理、制动主缸三包失效件分析和PMEA(过程潜在失效模式分析)以及国内外同行业产品的分析和总结,制动主缸机加工需重点控制几个关键工艺要求(见图二所示。
)
1、两孔同轴度要求:
缸体头部内孔(φ35mm)与缸体孔(φ20.6mm)同轴度要求达到φ0.03mm以内。
2、缸体孔圆柱度等要求:
缸体孔圆柱度不大于0.021mm,且加工精度较高,及缸体孔表面粗糙度高达Ra1.6以内。
3、缸体补油孔(φ0.5mm)无锐边及毛刺要求:
缸体补偿孔必须无锐边及毛刺,避免它们的存在将皮碗刮伤。
(二)、关键工艺改进前加工状况
1、工序5采用普通车床完成制动主缸头部内孔、外圆及端面的加工,但无法加工尾部中心孔。
工序15尾部中心孔是以缸体头部内孔作为定位,采用普通立钻设备加工。
由此可知,5序和15序不是一次性加工完成的,很难保证两序间的同轴度要求。
而30序加工缸体孔时主要以缸体头部内孔定位,再利用缸体尾部中心孔辅助定位夹紧。
由于5序、15序同轴度经常超差的影响,很难保证缸体孔同轴度达到0.03mm要求,每班约有10%左右制动主缸同轴度超差(如图二、三所示)。
(图二)
(图三)
2、主要采用普通小台钻钻削缸体补油孔,然后再使用普通立钻重挤缸体补油孔去除补油孔毛刺及锐边,实际检测结果表明,采用此工艺不理想无法达到工艺要求。
活塞来回运动时很容易刮伤皮碗,影响制动主缸总成内漏等缸陷的发生,这也是我厂制动主缸总成三包数量有所上升的原因之一。
3、采用普通立钻加工需经钻孔、扩孔、粗铰孔、精铰孔和辊光三道工序五个工步的加工方法完成。
此工艺不足之处:
工步多,加工时间长,多次重复定位;且缸体壁上有较多的穿孔,铰孔时容易起棱型,造成缸孔圆度不好,辊光后也只能起到改善缸孔时表面精糙度,无法修正铰孔时产生的棱型。
(三)、关键工艺改进后加工状况
5序制动主缸缸体头部内孔、外圆、端面及尾部中心孔是同时加工完成的,较好保证尾部中心孔与缸体头部内孔、外圆同轴度的要求,确保后序定位基准的统一;20序采用倒立式加工方式,切屑根据自身重力向下随着切削液一起流出,有利于缸体加工表面质量的提高;25序采用最新加工工艺,制动主缸补油孔不采用钻削,而采用由冲头直接冲出补油孔,并达到去除补油孔锐边及毛刺的效果(见图四所示)。
(图四)
1、工序5——采用CNC双头数车加工制动主缸头部内孔、外圆、端面及缸体尾部中心孔。
主要利用制动主缸外圆及前安装发兰的后端面定位,夹具采用自定心液压夹紧机构通过夹紧制动主缸上表面,第一主轴为交流伺服主轴,滑台采用数控,当它加工制动主缸外圆时,第二主轴也同时加工缸体尾部中心孔,这样能较好保证尾部中心孔与制动主缸体外圆同轴度要求(见图五所示)。
(图五)
2、工序20——采用四主轴数控倒立钻加工制动主缸缸体孔。
设备左边双工位属粗加工工位,主要进行钻孔,进给由液压滑台驱动;设备右边双工位属精加工工位,主要进行扩铰+镜面修光缸体孔,进给由数控滑台驱动,可以稳定可靠保证轴向加工尺寸。
该序以缸体头部内孔进行主定位,再利用缸体尾部中心孔辅助定位及夹紧,满足缸体孔φ0.03mm同轴度工艺要求。
(见图六所示)。
(图六)
3、工序25——采用反冲孔数控设备完成缸体补偿孔加工。
主要以缸体头部外圆进行主定位,再利用缸体尾部中心孔辅助定位及夹紧。
该序工艺亮点就是补偿孔不是采用钻头钻出,而是由冲头冲出:
先钻出一个工艺孔,工艺孔的深浅决定冲头的冲穿厚度,冲头装夹在冲杆上,朝着预留合理的壁厚冲穿即可形成补油孔并在补偿孔边缘形成一个倒圆角,这样就达到去除锐边及毛刺的效果(见图七所示)。
(图七)
四、试验验证分析
(一)、试验样件
根据制动主缸机加工技术研究确定的关键工艺改进前后的生产状况,分别进行试验样件的机加工(如表一所示)。
(表一)
(二)、试验标准
将试验样件1和试验样件2按汽车液压制动主缸试验方法和性能要求进行高温耐久性能试验验证(如表二所示)。
(表二)
(图八)
(三)、试验结果
试验结果对比分析:
制动主缸经过80°C×120h高温性能试验后,主缸理论的工作次数为12万次左右。
从整个试验过程来看,试验样件1工作次数在12万次左右就已经失效了;而试验样件2工作次数经过12万次时,制动主缸总成运行效果可以,无泄露、失效等异常现象发生。
试验样件2最终失效的工作次数高达22万次左右(如表三、图六、图七所示)。
(表三)
(图六:
试验样件1试验后照片)
(图七:
试验样件2试验后照片)
(四)、试验结论
从试验验证结果表明试验件样件2优于试验样件1,关键工艺改进后的制动主缸总成的耐用度和失效次数均比以前提高了将近一倍。
五、结束语
对微型汽车制动主缸总成的失效模式进行分析,通过针对性地对制动主缸关键工艺进行优化改进,提升了产品质量,进一步降低制动主缸总成的失效发生。
参考文献
[1](美)L.埃克霍恩(L.Eichhorn),(美)D.克林恩乔克(D.Corinchock)著,叶淑贞译 汽车制动系统 北京工业出版社 1998.8
[2]金加龙 汽车底盘构造与维修 电子工业出版社 2008
WeiZhen-Yong
Abstract:
Analysemini-cars’inefficacyframeworkofbrakemastercylinder,findoutthereasons,Torerormtheprocessingcraftofthebrakemastercylinderwelltargetedandimprovethequalityofproductsandtheefficiencyofproduction.
Keywords:
Efficacyframework,criticalcraft,theunificationofthelocationstandar