数控车实训的指导书.docx
《数控车实训的指导书.docx》由会员分享,可在线阅读,更多相关《数控车实训的指导书.docx(54页珍藏版)》请在冰豆网上搜索。
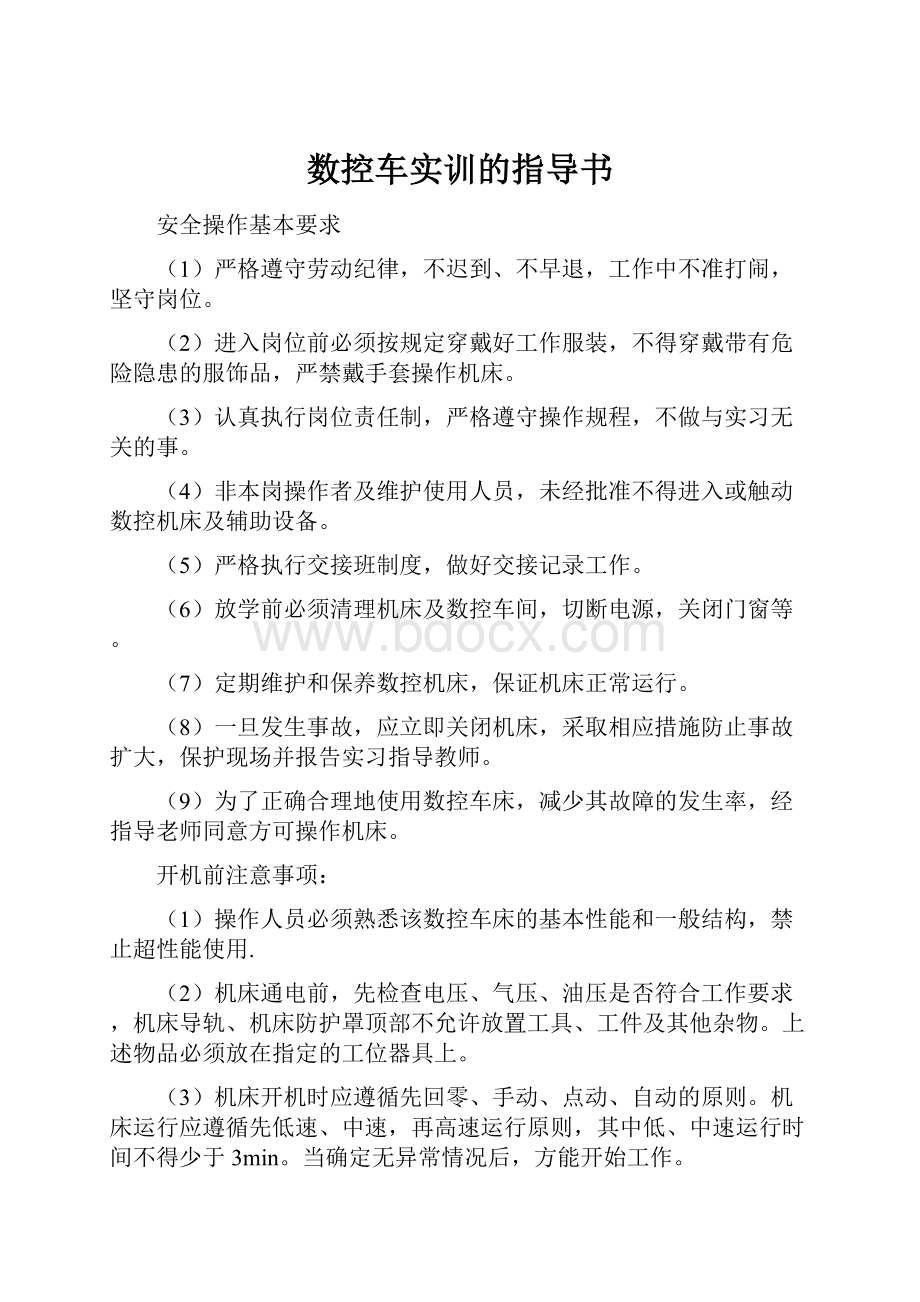
数控车实训的指导书
安全操作基本要求
(1)严格遵守劳动纪律,不迟到、不早退,工作中不准打闹,坚守岗位。
(2)进入岗位前必须按规定穿戴好工作服装,不得穿戴带有危险隐患的服饰品,严禁戴手套操作机床。
(3)认真执行岗位责任制,严格遵守操作规程,不做与实习无关的事。
(4)非本岗操作者及维护使用人员,未经批准不得进入或触动数控机床及辅助设备。
(5)严格执行交接班制度,做好交接记录工作。
(6)放学前必须清理机床及数控车间,切断电源,关闭门窗等。
(7)定期维护和保养数控机床,保证机床正常运行。
(8)一旦发生事故,应立即关闭机床,采取相应措施防止事故扩大,保护现场并报告实习指导教师。
(9)为了正确合理地使用数控车床,减少其故障的发生率,经指导老师同意方可操作机床。
开机前注意事项:
(1)操作人员必须熟悉该数控车床的基本性能和一般结构,禁止超性能使用.
(2)机床通电前,先检查电压、气压、油压是否符合工作要求,机床导轨、机床防护罩顶部不允许放置工具、工件及其他杂物。
上述物品必须放在指定的工位器具上。
(3)机床开机时应遵循先回零、手动、点动、自动的原则。
机床运行应遵循先低速、中速,再高速运行原则,其中低、中速运行时间不得少于3min。
当确定无异常情况后,方能开始工作。
(4)检查刀架是否有越位、超极限状态。
(5)检查电气元件是否牢固,是否有接线脱落。
(6)检查机床接地线是否和车间地线可靠连接。
(7)严格按机床说明书中的开机顺序进行操作。
(8)一般情况下开机过程中必须先进行回机床参考点操作,建立机床坐标系.
(9)机床通电后,CNC装置尚未出现位置显示或报警画面时,请不要碰MDI面板上的任何键。
MDI上的有些键专门用于维护和特殊操作,在开机的同时按下这些键,可能使机床产生数据丢失等误操作。
4、日常清理及维护
⑴每班工作后应擦净车床导轨面(包括中滑板和小滑板),要求无油污、无铁屑,并浇油润滑,使车床外表清洁和场地整齐。
⑵要求车床三个导轨面及转动部位清洁、润滑,油眼畅通,油标油窗清晰,清洗护床油毛毡,并保持车床外表清洁和场地整齐等.
⑶车床的润滑都采用30号机油。
主轴箱和溜板箱内的润滑油一般三个月更换一次,换油时应在箱体内用煤油洗清后再加油。
1.1数控车床编程基础知识
1、编程坐标系
为了便于描述数控车床的运动,数控研究人员引进了数学中的坐标系,用机床坐标系来描述机床的运动。
机床坐标系是一个右手笛卡尔直角坐标系如下图所示:
:
2、工件坐标系原点的设定
工件坐标系的原点一般设定在工件轴心线与右端面的焦点处。
如下图所示。
3、运动方向的规定
对于各坐标轴的运动方向,均将增大刀具与工件间距离的方向确定为个坐标轴的正方向。
Z坐标轴
Z坐标轴的运动方向是由传递切削力的主轴所决定的,与主轴轴线平行的标准坐标轴即为Z坐标轴,其正方向是增大刀具和工件之间距离的方向。
X坐标轴
X坐标轴平行于工件装甲面,一般的水平面内,他是刀具或工件定位平面内运动的主要坐标。
4、了解程序的构成,部分基础指令代码作用
(1)程序名
最多可以存储384个程序,为了识别及区分各个程序,每个程序都有唯一的程序名(程序名不允许重复),程序名位于程序的开头,由Q以及后面的四位数字构成
例如:
O0001(0000~9999)
(2)程序段
程序段由若干个代码字构成,以“;”或“※”结束,是CNC程序运行的基本单位。
例如:
N0030G00X20Z30;
N:
程序段号
一个程序段中可输入若干个代字码,也允许无代字码而只有“;”号(EOB)结束符。
有多个代字码时,代字码之间必须输入一个或一个以上空格。
基础指令的认识
主代码格式
G00快速定位G00X(U)____Z(W)____
G01直线插补G01X(U)____Z(W)____F____
G02顺时针插补G02X(U)____Z(W)____R____
G03逆时针插补G03X(U)____Z(W)____R____
在前置刀架的条件下,G03是代表顺时针插补,G02是逆时针插补。
辅助代码
M03主轴转向控制M03M04M05
T调用刀具T0101
S主轴转速S500
F进给速度F100
3、课堂例题编程讲解:
程序如下:
O2011
T0101M03S800
G00X100Z100
X36Z0
G01X0F150
G00X25Z2
G01Z-15F200
G00X27Z2
X21
G01Z-5
G00X23Z2
X18
G01ZOF150
X20Z-1
Z-5
X24Z-8
Z-15
G03X28Z-20R5
G00X100Z100
T0202M03S400
G00X26Z-15
G01X20F50
X34
G00Z-24
G01X0
G00X100Z100
T0101M05
M30
注意事项:
在前置刀架的条件下,G03是代表顺时针插补,G02是逆时针插补。
不要弄反。
学生活动以及作业布置:
用这节课所学指令编程知识,独立编出以下工件程序
评分标准:
每编错一行程序扣5分
1.2数控车床的对刀方法以及自动加工
1、识别各类车刀,见下图
2、刀具的装甲
(1)、外圆车刀的装夹装夹在刀架上的外圆车刀不宜伸出太长,否则刀杆的刚度降低,在切削时容易产生振动,直接影响加工工件的表面粗糙度,甚至有可能发生崩刃现象,车刀的伸出长度一般不超出刀杆厚度的2倍。
车刀刀尖应与机床主轴中心线等高,如不等高,应用垫刀片垫高。
垫刀片要平整,尽量减少垫刀片的片数,一般只用2~3片,以提高车刀的刚度。
另外,车刀刀杆中心线应与机床主轴中心线垂直,车刀要用两个刀架螺钉压紧在刀架上,并逐个轮流拧紧。
拧紧时应使用专用扳手,不允许再加套管,以免使螺钉受力过大而损伤。
(2)、纹车刀的装夹螺纹车刀装夹的正确与否,对螺纹的精度将产生一定的影、响。
若装刀有偏差,即使车刀的刀尖角刃磨得十分准确,加工后的螺纹牙形仍会产生误差。
因此要求装刀时刀尖与机床主轴中心线等高,左右切削刃要对称,为此要用对刀螺纹样板进行对刀。
(3)、切断刀的装夹切断刀不宜伸出太长,装刀时要装正,以保证两个副偏角对称,否则将使一侧副刃实际上没有副偏角或者是负的副偏角,造成刀头这一侧受力较大而折断。
切断刀的主切削刃必须与机床主轴中心线等高,以避免切不断工件、切断刀崩刃或折断的情况出现。
(4)、镗孔刀的装夹用车刀加工内孔通常称为镗孔,使用的车刀为镗孔刀。
在装刀时,刀尖应与机床主轴中心线等高,刀杆基面必须与主轴中心线平行,刀头可略向里偏斜一些,以免镗到一定深度时,刀杆后半部与工件表面相碰,刀杆伸出在允许的情况下尽量短一些,但应保证刀杆的工作长度长于孔深度3~5mm
3、毛坯的安装与装夹
工件的装夹与找正数控车床一般使用三爪自动定心卡盘装夹工件。
工件装夹、找正仍需遵守普通车床的要求,对于圆棒料装夹时工件要水平安放,右手拿工件稍作转动,左手配合右手旋紧夹盘扳手,使用校正划针校正工件,经校正后再将工件夹紧,工件找正工作随即完成
4、对刀的基本概念
(1)对刀是数控加工中较为复杂的工艺准备工作之一,对刀的好与差将直接影响到加工程序的编制及零件的尺寸精度。
通过对刀或刀具预调,还可同时测定其各号刀的刀位偏差,有利于设定刀具补偿量。
(2)刀位点刀位点是指在加工程序编制中,用以表示刀具特征的点,也是对刀和加工的基准点。
(3)对刀对刀是数控加工中的主要操作。
结合机床操作说明掌握有关对刀方法和技巧,具有十分重要的竟义。
在加工程序执行前,调整每把刀的刀位点,使其尽量重合于某一理想基准点,这一过程称为对刀。
理想基准点可以设定在刀具上,如基准刀的刀尖上;也可以设定在刀具外,如光学对刀镜内的十字刻线交点上。
5、对刀的基本方法
目前绝大多数的数控车床采用手动对刀,其基本方法有以下几种:
(1)定位对刀法:
定位对刀法的实质是按接触式设定基准重合原理而进行的一种粗定位对刀方法,其定位基准由预设的对刀基准点来体现。
对刀时,只要将各号刀的刀位点调整至与对刀基准点重合即可。
该方法简便易行,因而得到较广泛的应用,但其对刀精度受到操者技术熟练程度的影响,一般情况下其精度都不高,还须在加工或试切中修正。
(2)光学对刀法:
这是一种按非接触式设定基准重合原理而进行的对刀方法,其定位基准通常由光学显微镜(或投影放大镜)上的十字基准刻线交点来体现。
这种对刀方法比定位对刀法的对刀精度高,并且不会损坏刀尖,是一种推广采用的方法。
(3)试切对刀法:
在以上各种手动对刀方法中,均因可能受到手动和目测等多种误差的影响以至其对刀精度十分有限,往往需要通过试切对刀,以得到更加准确和可靠的结果。
6、试切对刀的方法步聚
GSK980TDb系统:
对1号外圆刀:
Z向:
手轮—正转用手轮把车刀X轴方向车一刀端面(约0.5㎜),再X轴方向退刀—刀补(切换到“刀具偏置磨损”界面),光标移到序号01刀位)—Z0—输入
X向:
手轮—正转用手轮把车刀Z轴方向车一刀外圆,再Z轴方向退刀,—主轴停止—测量外圆直径—刀补(切换到“刀具偏置磨损”界面)—(光标移到序号01刀位)—X25.32(假如外圆测量值是φ25.32)—输入
对2号切断刀:
方法和对1号外圆刀相同。
(注意:
把光标移到序号02刀位。
在对Z向时,由于1号刀已车好端面,因此2号刀不能再车端面,只能轻碰端面。
)
对3号螺纹刀:
方法和对1号、2号刀相同。
(注意:
把光标移到序号03刀位。
在对Z向时,由于车刀刀尖是60度,因此刀尖不能轻碰端面,刀尖只能与端面基本对齐。
)
FANUCSeriesoiMate-TD系统:
对1号外圆刀:
软件的形状用于对刀,磨损用于修改刀补
Z向:
JOG—正转用手轮把车刀X轴方向车一刀端面(约0.5㎜),再X轴方向退刀—OFF/SET(偏置/设置)按软件刀偏—选形状,光标移到1号刀的Z轴偏置,按Z0,按软件测量
X向:
JOG—正转用手轮把车刀Z轴方向车一刀外圆,再Z轴方向退刀,—停止—测量外圆直径—OFS/SET按软件刀偏—选形状,光标移到1号刀的X轴偏置,按X25.32(假如外圆测量值是φ25.32),按软件测量
对2号切断刀:
方法和对1号外圆刀相同。
(注意:
把光标移到002号刀位偏置。
在对Z向时,由于1号刀已车好端面,因此2号刀不能再车端面,只能轻碰端面。
)
对3号螺纹刀:
方法和对1号、2号刀相同。
(注意:
把光标移到序号03刀位。
在对Z向时,由于车刀刀尖是60度,因此刀尖不能轻碰端面,刀尖只能与端面基本对齐。
)
6、输入课题三讲解的例题程序,自动加工工件评分
7、自动加工的方法以及注意事项:
GSK980TDb系统:
修改刀补:
1、为了预防外圆车小,应在图纸标注直径尺寸上预留0.3,修改方法是:
刀补(切换到“刀具偏置磨损”界面)—光标移到所须刀号的下一位(举例:
如果是修改01刀号,光标则移到01刀号的下一行)U—0.3—输入
2、如果外圆还大0.32,修改方法是:
刀补(切换到“刀具偏置磨损”界面)—光标移到所须刀号的下一位(举例:
如果是修改01刀号,光标则移到01刀号的下一行)U—-0.3—输入
自动加工零件:
先把车刀移动到转刀架不碰工件的安全位置。
编辑—程序—复位(或光标移到程序第一行)—自动—循环启动(加工第一件零件时,应把快速倍率调到25%,左手放在急停按键旁,如果出现紧急情况或发现车刀走的线路不是自己预想的编程线路立即按急停,重复加工第二件零件以上可把快速倍率调回到100%,左手可以不用放到急停按键旁)
注:
批量加工时,工件从夹爪伸出的长度应比对刀时伸出的长度多0.5mm,预留车端面。
每件装夹的长度尽量一样。
直接按循环启动
编辑—程序—复位(或光标移到程序第一行)—MEMWQ(自动)—循环运行(加工第一件零件时,应把快速倍率调到25%,左手放在急停按键旁,如果出现紧急情况或发现车刀走的线路不是自己预想的编程线路立即按急停。
程序暂停:
(1)在自动加工运行程序时,想中途停下检查零件尺寸,操作方法是:
进给保持—手动—主轴停止
(2)暂停后,想再继续加工,操作方法是:
手动—正转—自动—循环启动
在程序中任选一段运行:
选段时,应选有刀号的这一行。
举例:
如果槽的直径还大,应该先修改刀补,再打开程序,把光标移到T0202M42S400这一行,按自动—循环启动
G70精车选段举例:
有一零件编程,外圆用G71(或G72、G73)粗车、用G70精车。
车完后发现外圆直经还大,应该先修改刀补,再车一刀外圆符合图纸尺寸要求。
返修时,为了不浪费时间,可直接从G70开始运行,方法是:
先把刀架转动到T0101位置。
把车刀移动到G71粗车的循环起点(该起点同样也是G70精车的循环起点)。
把光标移动到程序的G70P_Q_这一行。
按手动—正转—自动—循环启动(精车完这行后,如果不想往下加工,可按复位)
注:
不能在循环程序中间选段。
FANUCSeriesoiMate-TD系统:
修改刀补:
1、为了预防外圆车小,应在图纸标注直径尺寸上预留0.3,修改方法是:
OFS/SET—在软件按刀偏—磨损—在相应的刀号X轴上按0.3—按软件+输入—执行
2、如果外圆还大0.32,修改方法是:
OFS/SET—在软件按刀偏—磨损—在相应的刀号X轴上按-0.3—按软件+输入—执行
自动加工零件:
先把车刀移动到转刀架不碰工件的安全位置。
编辑—程序—复位(或光标移到程序第一行)—MEMWQ(自动)—循环运行(加工第一件零件时,应把快速倍率调到25%,左手放在急停按键旁,如果出现紧急情况或发现车刀走的线路不是自己预想的编程线路立即按急停。
重复加工第二件零件以上可把快速倍率调回到100%,左手可以不用放到急停按键旁)
注:
批量加工时,工件从夹爪伸出的长度应比对刀时伸出的长度多0.5mm,预留车端面。
每件装夹的长度尽量一样。
直接按循环运行
程序暂停:
(1)在自动加工运行程序时,想中途停下检查零件尺寸,操作方法是:
暂停—手动—停止
(2)暂停后,想再继续加工,操作方法是:
手动—正转—自动—循环运行
运行程序时按复位和暂停的区别:
在运行程序时想中途停下,如按复位键,再想继续加工,将会从程序
第一行往下运行如按暂停键,想再继续加工,则是从程序暂停的那一
行往下运行。
在程序中任选一段运行:
选段时,应选有刀号的这一行。
举例:
如果槽的直径还大,应该先修改刀补,再打开程序,把光标移到T0202M03S400这一行,按自动—循环运行
G70精车选段举例:
有一零件编程,外圆用G71(或G72、G73)粗车、用G70精车。
车完后发现外圆直经还大,应该先修改刀补,再车一刀外圆符合图纸尺寸要求。
返修时,为了不浪费时间,可直接从G70开始运行,方法是:
(1)先把刀架转动到T0101位置。
(2)把车刀移动到G71粗车的循环起点(该起点同样也是G70精车的循环起点)。
(3)把光标移动到程序的G70P_Q_这一行。
(4)按手动—正转—自动—循环运行(精车完这行后,如果不想往下加工,可按复位)
注:
不能在循环程序中间选段。
指导老师做示范:
(1)操作车床对三把刀(90°外圆车刀、切断刀、外螺纹车刀)。
(2)编辑程序输入课题三讲解的例题程序,让车床自动加工出该图实
物。
并且要求尺寸合格。
小结:
先理解对刀的基本概念和对刀的基本方法才能正确掌握试切对刀的方法。
先自动连续加工再掌握加工暂停和从程序中间选段运行。
学生活动及任务布置:
(1)、用试切对刀法进行对90°外圆偏刀、切断刀、螺纹车刀的对刀。
(2)、做到严格遵守安全操作规程
(3)、学会让车床自动走程序加工工件,并且尺寸合格。
要求:
正确使用量具,保证尺寸正确性。
加工出已下工件实物。
1.3数控车固定循环指令(G71G70G75G92)
一、外圆粗车循环(G71)
G71U-R-;
G71P-Q-U-W-F-;
N(NS)
……
……F
……S
……T
N(NF)
此处的U为每刀的进刀量,R为退刀量。
P为精加工开头程序段的第一个程序段号Q为精加工结束程序段的最后一个程序段号,此外的U、W为留余量。
在精加工形状描绘的段号内,F、S、T功能都无效,只在G71指令中有效。
代码意义:
G71代码分为三个部分:
⑴:
给定粗车时的切削量、退刀量和切削速度、主轴转速、刀具功能的程序段;
⑵:
给定定义精车轨迹的程序段区间、精车余量的程序段;
⑶:
定义精车轨迹的若干连续的程序段,执行G71时,这些程序段仅用于计算粗车的轨迹,实际并未被执行。
系统根据精车轨迹、精车余量、进刀量、退刀量等数据自动计算粗加工路线,沿与Z轴平行的方向切削,通过多次进刀→
切削→退刀的切削循环完成工件的粗加工。
G71的起点和终点相同。
本代码适用于非成型毛坯(棒料)的成型粗车。
精车轨迹:
由代码的第⑶部分(ns~nf程序段)给出的工件精加工轨迹,精加工轨迹的起点(即ns程序段的起点)与G71的起点、终点相同,简称A点;精加工轨迹的第一段(ns程序段)只能是X轴的快速移动或切削进给,ns程序段的终点简称B点;精加工轨迹的终点(nf程序段的终点)简称C点。
精车轨迹为A点→B点→C点。
粗车轮廓:
精车轨迹按精车余量(Δu、Δw)偏移后的轨迹,是执行G71形成的轨迹轮廓。
精加工轨迹的A、B、C点经过偏移后对应粗车轮廓的A’、B’、C’点,G71代码最终的连续切削轨迹为B’点→C’点。
Δd:
粗车时X轴的切削量,取值范围0.001~99.999(单位:
mm,半径值),无符号,进刀方向由ns程序段的移动方向决定。
U(Δd)执行后,指定值Δd保持,并把数据参数NO.051的值修改为Δd×1000(单
位:
0.001mm)。
未输入U(Δd)时,以数据参数NO.051的值作为进刀量。
e:
粗车时X轴的退刀量,取值范围0~99.999(单位:
mm,半径值),无符号,退刀方向与进刀方向相反,R(e)执行后,指定值e保持,并把数据参数NO.052的值修改为e×1000(单位:
0.001mm)。
未输入R(e)时,以数据参数NO.052的值作为退刀量。
ns:
精车轨迹的第一个程序段的程序段号;
nf:
精车轨迹的最后一个程序段的程序段号。
Δu:
X轴的精加工余量,取值范围-99999.999~99999.999(单位:
mm,直径),有符号,粗车轮廓相对于精车轨迹的X轴坐标偏移,即:
A’点与A点X轴绝对坐标的差值。
U(Δu)未输入时,系统按Δu=0处理,即:
粗车循环X轴不留精加工余量。
Δw:
Z轴的精加工余量,取值范围-99999.999~99999.999(单位:
mm),有符号,粗车轮廓相对于精车轨迹的Z轴坐标偏移,即:
A’点与A点Z轴绝对坐标的差值。
W(Δw)未输入时,系统按Δw=0处理,即:
粗车循环Z轴不留精加工余量。
K:
当K不输入或者K不为1时,系统不检查程序的单调性除了圆弧或椭圆或抛物线的起点和终点的Z值相等或圆弧大于180度;当K=1时,系统检查程序的单调性
F:
切削进给速度;S:
主轴转速;T:
刀具号、刀具偏置号。
M、S、T、F:
可在第一个G71代码或第二个G71代码中,也可在ns~nf程序中指定。
在G71循环中,ns~nf间程序段号的M、S、T、F功能都无效,仅在有G70精车循环的程序段中才有效。
1、运行轨迹如下图所示:
如左图所示:
车刀每次向前进给一个U值,退刀一个R值。
按给定的精加工形状,留余量后进行粗加工,在完成所有粗加工后,车刀会在留好余量的轮廓形状线上走一刀,最后再退到指令的起点位置。
G70外圆精车循环
在经过G71粗车后,可用G70P-Q-;进行精加工。
在运行该指令时,车刀会沿着精加工形状线运行一次。
不过要注意的是在运行该指令时的定位一定要与车刀的退出点平齐。
2、课堂讲解例图:
程序如下:
二、G75切槽复合循环
(1)、G75代码格式:
G75R(e);
G75X(U)Z(W)P(Δi)Q(Δk)R(Δd)F;
(2)、代码意义:
轴向(Z轴)进刀循环复合径向断续切削循环:
从起点径向(X轴)进给、回退、再进给……直至切削到与切削终点X轴坐标相同的位置,然后轴向退刀、径向回退至与起点X轴坐标相同的位置,完成一次径向切削循环;轴向再次进刀后,进行下一次径向切削循环;切削到切削终点后,返回起点(G75的起点和终点相同),径向切槽复合循环完成。
G75的轴向进刀和径向进刀方向由切削终点X(U)Z(W)与起点的相对位置决定,此代码用于加工径向环形槽或圆柱面,径向断续切削起到断屑、及时排屑的作用。
(3)、相关定义:
径向切削循环起点:
每次径向切削循环开始径向进刀的位置,表示为An(n=1,2,3……),An的X轴坐标与起点A相同,An与An-1的Z轴坐标的差值为Δk。
第一次径向切削循环起点A1与起点A为同一点,最后一次径向切削循环起点(表示为Af)的Z轴坐标与切削终点相同。
径向进刀终点:
每次径向切削循环径向进刀的终点位置,表示为Bn(n=1,2,3……),Bn的X轴坐标与切削终点相同,Bn的Z轴坐标与An相同,最后一次径向进刀终点(表示为Bf)与切削终点为同一点;轴向退刀终点:
每次径向切削循环到达径向进刀终点后,轴向退刀(退刀量为Δd)的终点位置,表示为Cn(n=1,2,3……),Cn的X轴坐标与切削终点相同,Cn与AnZ轴坐标的差值为Δd;径向切削循环终点:
从轴向退刀终点径向退刀的终点位置,表示为Dn(n=1,2,3……),Dn的X轴坐标与起点相同,Dn的Z轴坐标与Cn相同(与AnZ轴坐标的差值为Δd);
切削终点:
X(U)Z(W)指定的位置,最后一次径向进刀终点Bf。
R(e):
每次径向(X轴)进刀后的径向退刀量,取值范围0~99.999(单位:
mm,半径值),无符号。
R(e)执行后指定值保持有效,并把系统参数NO.056的值修改为e×1000(单位:
0.001mm)。
未输入R(e)时,以系统参数NO.056的值作为径向退刀量。
X:
切削终点Bf的X轴绝对坐标值(单位:
mm)。
U:
切削终点Bf与起点A的X轴绝对坐标的差值(单位:
mm)。
Z:
切削终点Bf的Z轴的绝对坐标值(单位:
mm)。
W:
切削终点Bf与起点A的Z轴绝对坐标的差值(单位:
mm)。
P(Δi):
径向(X轴)进刀时,X轴断续进刀的进刀量,取值范围0<Δi≤9999999(单位:
0.001mm(IS-B)或0.0001mm(IS-C),直径值),无符号。
Q(Δk):
单次径向切削循环的轴向(Z轴)进刀量,取值范围0<Δk≤9999999(单位:
0.001mm(IS-B)或0.0001mm(IS-C)),无符号。
R(Δd):
切削至径向切削终点后,轴向(Z轴)的退刀量,取值范围0~99999.999(单位:
mm),无符号。
省略R(Δd)时,系统默认径向切削终点后,轴向(Z轴)的退刀量为0。
省略Z(W)和Q(Δk),默认往正方向退刀。
2、运行轨迹如下图:
3、课堂例图讲解:
编程示例: