扶梯桁架焊接及焊缝质量检验要求日立.docx
《扶梯桁架焊接及焊缝质量检验要求日立.docx》由会员分享,可在线阅读,更多相关《扶梯桁架焊接及焊缝质量检验要求日立.docx(24页珍藏版)》请在冰豆网上搜索。
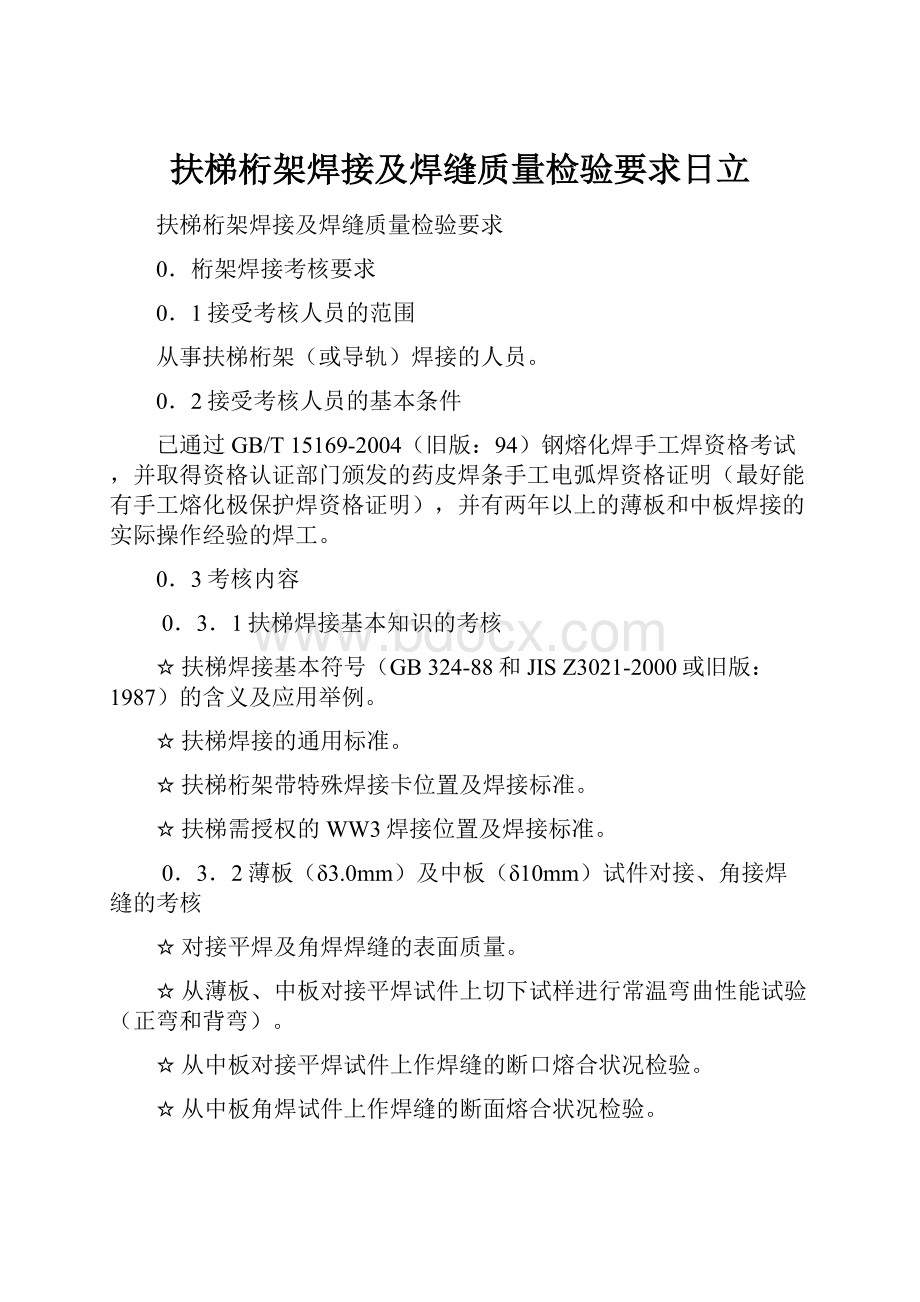
扶梯桁架焊接及焊缝质量检验要求日立
扶梯桁架焊接及焊缝质量检验要求
0.桁架焊接考核要求
0.1接受考核人员的范围
从事扶梯桁架(或导轨)焊接的人员。
0.2接受考核人员的基本条件
已通过GB/T15169-2004(旧版:
94)钢熔化焊手工焊资格考试,并取得资格认证部门颁发的药皮焊条手工电弧焊资格证明(最好能有手工熔化极保护焊资格证明),并有两年以上的薄板和中板焊接的实际操作经验的焊工。
0.3考核内容
0.3.1扶梯焊接基本知识的考核
☆扶梯焊接基本符号(GB324-88和JISZ3021-2000或旧版:
1987)的含义及应用举例。
☆扶梯焊接的通用标准。
☆扶梯桁架带特殊焊接卡位置及焊接标准。
☆扶梯需授权的WW3焊接位置及焊接标准。
0.3.2薄板(δ3.0mm)及中板(δ10mm)试件对接、角接焊缝的考核
☆对接平焊及角焊焊缝的表面质量。
☆从薄板、中板对接平焊试件上切下试样进行常温弯曲性能试验(正弯和背弯)。
☆从中板对接平焊试件上作焊缝的断口熔合状况检验。
☆从中板角焊试件上作焊缝的断面熔合状况检验。
☆焊缝无损探伤检验(X射线或超声波探伤,在焊缝的外观、冷弯及断口或断面检验后,根据需要进行)
0.3.3模拟产品焊缝的焊接考核
☆模拟油盘的焊接检验。
☆模拟继手端部与主弦材的焊接检验。
0.3.4桁架产品重要部位截取试件焊接考核(根据需要进行)
☆继手和弦材部的焊接检验
☆主弦材弯折部的焊接检验
☆两端托梁与上弦材端部的焊接检验
0.4考核用设备
用本公司认可的CO2焊机及焊丝进行CO2气体保护的半自动手工工焊,焊丝直径为Φ1.2mm。
0.5考核周期
从事扶梯桁架(或导轨)焊接的焊工,需通过考核后才能上岗操作。
已通过考核的焊工每年要进行一次复审,当停止该项工作半年以上,应重新考核后才可以再次从事该项工作。
0.6考核合格标准
在所考核的项目中有任何一项不合格均判为不合格。
1桁架焊缝质量检验要求
1.1桁架带特殊焊接卡的焊缝质量要求
1.1.1焊缝缺陷要求:
焊接接头质量需满足GB/T12469-90《焊接质量保证钢熔化焊接头的要求和缺陷分级》III级标准。
具体有:
NO
检验项目
标准及等级要求
检验范围
1
外观检验及断口宏观检验
GB/T12469-90《焊接质量保证钢熔化焊接头的要求和缺陷分级》III级
焊工考核及复审制作的对接、角接试件—全检
产品—外观检验全检
2
无损检验—磁粉探伤
JB/T6061-1992《焊缝磁粉检验方法和缺陷磁痕的分级》II级,即:
应无裂纹、未熔合以及双面焊和加垫板的单面焊中的未焊透。
桁架产品重要部位截取试件—抽检
3
无损检验—手工超声波探伤
GB/T11345-1989《钢焊缝手工超声波探伤方法和探伤结果分级》检验等级A、评定等级II级
产品—抽检
1.1.2接头机械性能要求:
NO
检验项目
标准及等级要求
检验范围
1
对接焊接接头横向正弯及背弯试验
GB2653-89《焊接接头弯曲及压扁试验方法》
JISZ3122-1990《突合せ溶接継手の曲げ試験方法》
焊工考核及复审制作的对接、角接试件—全检
2
对接焊接接头拉伸试验
GB2651-89《焊接接头拉伸试验方法》
JISZ3121-1993《突合せ溶接継手の引張試験方法》
焊工考核及复审制作的对接、角接试件—根据需要
1.2需授权的WW3焊接位置焊缝质量要求
NO
检验项目
标准及等级要求
检验范围
1
外观检验及断口宏观检验
GB/T12469-90《焊接质量保证钢熔化焊接头的要求和缺陷分级》IV级
焊工考核及复审制作的模拟产品—全检
桁架产品—全检
2
水渗试验(吹气试验)
检查油盘的致密性
水渗试验(吹气试验)工艺流程
1.3其它位置焊缝质量要求
NO
检验项目
标准及等级要求
检验范围
1
外观检验及断口宏观检验
GB/T12469-90《焊接质量保证钢熔化焊接头的要求和缺陷分级》IV级
桁架产品—抽检
2外观检验(GB/T12469-90《焊接质量保证钢熔化焊接头的要求和缺陷分级》III级)
2.1检验方法:
利用长度测量工具和检验尺、样板、量规等检查焊缝外形尺寸、余高及焊缝直度;利用肉眼或5倍放大镜检查焊缝表面缺陷。
2.2焊缝外观及外形尺寸检验标准(GB/T12469-90III级标准规定,图示参照GB6417.1-2005《金属熔化焊接头缺欠分类及说明》)
合格要求:
焊缝外形尺寸符合设计图样的规定;焊接接头无裂纹、气孔、未熔合、未焊透、咬边等,焊缝与母材过渡圆滑。
NO
图示
缺陷名称
标准要求
III级
IV级
1
表面凹陷、未焊满(指不足设计要求)
≤0.2+0.02δ且≤1mm,每100mm焊缝内缺陷总长≤25mm
≤0.2+0.04δ且≤2mm,每100mm焊缝内缺陷总长≤25mm
2
根部收缩
缩沟
≤0.2+0.02δ且≤1mm
长度不限
≤0.2+0.04δ且≤2mm
长度不限
3
连续咬边
间断咬边
≤0.05δ且≤0.5mm;连续长度≤100mm且焊缝两侧咬边总长≤10%焊缝全长
≤0.1δ且≤1mm
长度不限
4
裂纹
不允许
5
弧坑裂纹
不允许
个别长≤5mm的弧坑裂纹允许存在
6
电弧擦伤
不允许
个别电弧擦伤允许存在
7
飞溅
清除干净
NO
图示
缺陷名称
标准要求
III级
IV级
8
焊接接头不良
缺口深度≤0.05δ且≤0.5mm;每米焊缝不得超过一处
e5<3mm
缺口深度≤0.05δ且≤0.5mm;每米焊缝不得超过一处
e5<3mm
9
焊瘤
不允许
10
未焊透(按设计焊缝厚度为准)
根部未焊透
不加垫单面焊允许值≤0.15δ且≤1.5mm;每100mm焊缝内缺陷总长≤25mm
≤0.1δ且≤2mm;每100mm焊缝内缺陷总长≤25mm
11
夹渣
深≤0.1δ
长≤0.3δ
且≤10mm
深≤0.2δ
长≤0.5δ
且≤20mm
12
表面气孔
每50mm焊缝长度内允许直径≤0.3δ且≤2mm的气孔二个,孔间距≥6倍孔径
每50mm焊缝长度内允许直径≤0.4δ且≤3mm的气孔二个,孔间距≥6倍孔径
13
角焊缝厚度不足(按设计焊缝厚度计)
e≤0.3+0.05δ且≤1mm
每100mm焊缝长度内缺陷总长度≤25mm
e≤0.3+0.05δ且≤2mm
每100mm焊缝长度内缺陷总长度≤25mm
14
角焊缝焊脚不对称
≤2+0.15a
≤2+0.2a
2.3焊缝外观及外形尺寸检验标准(GB/T12469-90未要求项目)
NO
图示
缺陷名称
标准要求
III级
IV级
1
未熔合
不允许
每100mm焊缝长度内缺陷总长度≤25mm
2
焊缝直度
任意250焊缝长度焊缝不直度≤2
3
焊缝宽度差
amax-bmin≤2,焊缝宽度以每边超过坡口宽2为准
4
烧穿
不允许
5
焊缝余高(表面加强高)
平焊0~3,其它0~4
任意250焊缝长度内e2max-e2min≤2
背部下塌K≤2
6
接头坡口错位
e4<0.15δ
但最大为3
角变形量≤3°
3焊缝的断口检验和断面缺陷
3.1断口检验方法
在所需检测部位的焊缝表面加工沟槽,沟槽深不得超过焊缝有效厚度的1/3,然后用拉力机械或锤子将试件折断,以检查断口表面缺陷。
对角焊缝试样可直接将角接头压断或折断。
3.2焊缝断口圆形缺陷和条形缺陷检验标准(参照GB/T3323-2005《金属熔化焊焊接接头射线照相》II级缺陷评级)
3.2.1长宽比≤3的气孔、夹渣缺陷定义为圆形缺陷;长宽比>3的气孔、夹渣缺陷定义为条形缺陷
3.2.2缺陷评定区:
对评定厚度T≤25取10mm×10mm缺陷最严重的部位。
3.2.3圆形缺陷应将缺陷尺子换算成缺陷点数,如下表:
缺陷长径/mm
≤1
>1~2
>2~3
>3~4
>4~6
>6~8
>8
点数
1
2
3
6
10
15
25
3.2.4对评定厚度T≤25的试件,缺陷长径≤0.5mm不计点数。
3.2.5圆形缺陷II级评定标准
点状缺陷
板厚
≤10
>10~15
>15~25
缺陷点数
≤3个
≤6个
≤9个
对应缺陷尺寸
Φ3一个
或Φ1一个加Φ2一个
或Φ1三个
Φ4一个
或以3.2.3表折算的点数
Φ5一个
或以3.2.3表折算的点数
3.2.6条形缺陷II级评定标准
条形缺陷
板厚
≤12
12缺陷尺寸
≤4mm
≤
T
允许缺陷总长
在平行于焊缝轴线上的任意直线上,相邻两缺陷间距均不超过6L的任何一组缺陷,其累计长度在12T焊缝长度内不超过T
3.3焊缝未焊透标准
不加垫板的单面焊中未焊透的允许长度,按下表进行评定。
角焊缝的未焊透是指角焊缝的实际熔深未达到理论熔深值,按下表进行评定。
板厚
≤9
9条形缺陷尺寸
≤6mm
≤
T
允许缺陷总长
在平行于焊缝轴线上的任意直线上,相邻两缺陷间距均不超过3L的任何一组缺陷,其累计长度在6T焊缝长度内不超过T
5对接焊接接头横向正弯及背弯试验
5.1弯曲检验设备:
可在压力机或万能试验机上进行
5.2弯曲装置
圆形压头弯曲试验(GB2653-89)
参数:
D由所弯曲的材料种类决定
NO
a
D
R
A
b
L
r
1
3
13
20以上
20
2.5D+80以上
120
20
D+2a+3
≤D+3a
22
0.6
2
10
40
40
200
30
63
2
5.2.1圆形压头弯曲装置(GB2653-89、JISZ3122-1990)
5.2.2、模具弯曲装置(JISZ3122—1990《突合せ溶接継手の曲げ試験方法》)
(1)、弯曲模具压板
NO
名称
A
B
C
D
E
F
R
R'
1
3mm板模具压板
65
50
65
12
96
13
6
5
2
10mm板模具压板
65
50
150
18
150
40
20
12
(2)、弯曲模具底座
NO
名称
A
B
C
D
E
F
G
H
R
R'
1
3mm板模具底座
65
55
135
9
58
22.5
28
45.5
11.25
6.5
2
10mm板模具底座
65
55
270
16
160
63
78.5
140
31.5
20
5.4试样加工要求
试样的焊缝余高应采用机械方法去除,面弯、背弯试样的拉伸表面应加工齐平,并至少受拉面试样有一侧与母材齐平,试样受拉伸表面不得有划痕和损伤。
试样的棱边应锉圆,其半径不应大于2mm,经过加工的试样其宽度厚度偏差均为±1mm。
5.5弯曲试验合格标准(JISZ3122—1990《突合せ溶接継手の曲げ試験方法》)
5.5.1弯曲试验结果:
A1(完好)—试样弯曲处的外表面金属基本上无肉眼可见因弯曲变形产生的缺陷。
A2(微裂纹)—试样弯曲外表面金属基体上出现细小裂纹,其长度不大于2mm,宽度不大
于0.2mm时。
A3(裂纹)—试样弯曲外表面金属基体上出现开裂,其长度大于2mm,宽度大于0.2mm而
小于等于0.5mm时。
A4(裂缝)—试样弯曲外表面金属基体上出现明显开裂,其长度大于5mm时。
A5(裂撕)—试样弯曲外表面出现沿宽贯穿的开裂其深度超过试样厚度的三分之一时称为裂
撕。
5.5.2弯曲试验合格标准:
当试样弯曲至180°后,弯曲外表面评定为A1或A2级时,则评定试样合格。
4板对接、角接试件焊接考核(GB/T15169-2004:
钢熔化焊焊工技能评定)
板状试件两端25mm不作考核。
4.1薄板对接单面焊缝检验试件(检验油盘焊接项目)
☆薄板试验材料的尺寸,如图。
☆薄板试验材料的形式:
板厚:
坡口形式:
α=0°
焊缝间隙:
0~2.5
焊缝形式:
对接单面焊
焊缝位置:
平焊
☆试件数量:
3件
外观目测1件
无损检验1件
冷弯及断口检查1件
☆试件检验项目
试件
形式
试件
厚度
检验项目及试件、试样数量(件)
外观
目测
无损
检验
冷弯试验
断口
检查
断面
检验
正弯
背弯
侧弯
板对接
3
1
1
1
1
1
4.2中厚板对接单面焊和对接单面加垫焊缝检验试件
☆中厚板试验材料的尺寸,如图。
☆薄板试验材料的形式:
板厚:
坡口形式:
V型α=60°
焊缝间隙:
单面焊0~3,单面加垫焊3~6
焊缝形式:
对接单面焊和对接单面加垫焊
焊缝位置:
平焊
☆试件数量:
单面焊3件,单面加垫焊1件
单面焊:
外观目测1件,无损检验1件
冷弯及断口检查1件
单面加垫焊:
外观目测及断口检查共1件
☆试件检验项目
试件
形式
试件
厚度
检验项目及试件、试样数量(件)
外观
目测
无损
检验
冷弯试验
断口
检查
断面
检验
正弯
背弯
侧弯
单面对接
10
1
1
1
1
1
单面加垫
10
1
1
4.3中厚板角接角焊缝检验试件
☆中厚板试验材料的尺寸,如图。
☆薄板试验材料的形式:
板厚:
坡口形式:
α=0°
焊缝间隙:
0
焊缝形式:
角接角焊缝
焊缝位置:
平焊
☆试件数量:
外观目测及断口检查共3件
☆试件检验项目
试件
形式
试件
厚度
检验项目及试件、试样数量(件)
外观
目测
无损
检验
冷弯试验
断口
检查
断面
检验
正弯
背弯
侧弯
角焊缝
10
1
3
6模拟产品试件焊接考核
6.1模拟油盘的焊接考核
6.1.1模拟产品的形状
外形尺寸(L500×W200×H120)
件①δ=1.5,尺寸500×1202件
件②δ=1.5,尺寸250×123
(开料244×123后弯折)2件
件①δ=3.0,尺寸500×2001件
6.1.2模拟产品的考核
☆焊接参数:
电流100~120A,电压
20~22V,应准确成45°焊接,焊缝
应连续,不能将钢板焊穿后再补焊。
☆焊缝表面质量及焊缝外形尺寸的考核
满足GB/T12469-90IV级
☆焊缝的水渗试验(吹气试验)
将容器垫高,注入清水,清水高度为100mm,在容器外侧用压缩空气(要求压力≥0.41MPa,喷嘴到焊缝表面的距离不得超过30mm)吹向焊缝,检查焊缝有无漏气,不产生气泡为合格。
6.1.3模拟产品焊接的评定
当6.1.2两项考核均合格时判定该产品焊接考核合格。
6.2模拟继手与主弦材的焊接考核
6.2.1模拟产品的形状
件1:
L125×80×10L=135(125边一端部冲缺口20mm)
件2:
L125×80×10L=200
6.2.2模拟产品的考核
焊接工艺的考核:
包括焊接层数、焊脚长度、焊缝厚度、焊接电流、电压等。
焊缝表面质量考核满足GB/T12469-90III级
6.2.3模拟产品焊接的评定
当焊接符合工艺要求及焊缝表面质量符合GB/T12469-90III级要求时,判定该产品焊接考
核合格。
6.3桁架产品重要部位截取试件考核
6.3.1主要部位形状
☆主弦材弯折部
件1、2L125×80×10L=400各1件,开口及弯折参照主弦材作业方法
件3L125×80×10L=9201件
件4如下图1件
☆两端托梁与上弦材部
件①L125×80×10L=2001件
件②L125×80×10L=3001件
(开缺口60×80)
件③L200×2000×20
L=2001件
☆继手和弦材部
件①继手232000211件
件②L125×80×10
L=6002件
6.3.2焊缝作业标准
焊接标准
序号
焊接简图
焊层数
电流/A
电压/V
注意事项
1、2
1~4
260~280
30~34
该焊缝为整个桁架中最重要的焊缝,要严格按左图的焊接形式进行焊接。
为了减少焊接应力,保证焊缝的质量,在焊完一层后应使用敲渣锤清理焊缝表面的熔渣。
图纸标注焊层数为11层,为满足焊趾圆弧过渡的需要,根据需要增加12、13层的补焊
5~11
260~280
30~34
12、13
130~150
20~25
3-10
12
14
15
1~3
260~280
30~34
焊脚长度为9mm以上的焊缝,如果只用1层焊接,会由于裂缝、咬边等原因,造成焊接不良,所以要采用左图的焊接形式
11、13
1~3
260~280
30~34
要防止焊缝与工件之间的未熔合
16、17
1~2
160~200
15~25
为缓和应力集中,应按如左图方式焊接
6.3.3焊接的评定
当焊接符合工艺要求及焊缝表面质量符合GB/T12469-90III级要求时,判定该产品焊接考
核合格。
7其它
7.1检验工具
7.1.1继手部焊缝检验样板—用于检验焊脚长度、焊缝厚度及R值
7.2未指定焊缝高度的角接焊缝的通用标准(公司标准)
板厚δ(mm)
2~3
4~6
7~9
10~12
13~16
17~23
焊脚尺寸Kmin(mm)
2
3
4
5
6
8
7.3其它检验方法
7.3.1焊接接头横向拉伸试验(GB2651-89《焊接接头拉伸试验方法》;JISZ3121-1993《突合せ溶接継手の引張試験方法》)
金属焊接接头横向拉伸试验测定接头的抗拉强度(屈服点),还可以发现试样断口处的缺陷,并可以验证所选用的焊接材料及焊接工艺正确与否。
板状试样尺寸
a:
板厚a≤20
GB2651-89
JISZ3121-1993
总长L
根据试验机确定
250以上:
取250
夹持部分宽度B
b+12
52
b
≥25
b=40
过渡圆弧r
25
r=50
平行部分长度
>
s+12
=
s+12
试样应从焊接试件上垂直于焊缝轴线截取,焊缝轴线应位于试件平行长度的中心。
试样应采用机械加工制备,要注意防止表面应变硬化或材料过热。
在受试长度
范围内,表面不应有横向刀痕或划痕。
若产品技术条件无规定时,试样表面应用机械方法去除焊缝余高,使与母材原始表面齐平。
板接头板状试样
7.3.2焊缝或熔敷金属的拉伸试验(GB2652-89《焊缝及熔敷金属拉伸试验方法》)
金属材料焊缝或熔敷金属的拉伸试验(GB2652-89《焊缝及熔敷金属拉伸试验方法》)测定其拉伸强度和塑性(伸长率、断面收缩率),还可以发现试样断口处的缺陷,并可以验证所选用的焊接材料及焊接工艺正确与否。
焊缝拉伸试样尺寸
一般尺寸
短试样
长试样
d0
r(min)
L
L
单双肩
螺纹
3±0.05
2
2
5d0
+d0
10d0
+d0
6±0.1
3
3.5
a)单肩试样b)双肩试样c)螺纹试样
10±0.2
4
5
7.3.3焊接接头的金相检验(GB10866-1989锅炉受压元件焊接接头金相和断口检验方法)
焊接接头金相检验的目的是用来检查焊缝、热影响区和焊件的金相组织情况及确定内部缺陷等。
通过对焊接接头金相组织的分析,可以了解焊缝金属中各种显微氧化物的数量、晶粒度及组织状况,从而对焊接材料、工艺方法和参数的合理性做出相应的评价。
焊接接头的金相检验方法首先是在试板焊缝长度方向的中段截取试样,试样尺寸为10~20mm,试样数量不少于6个。
焊缝表面保持原状,而将横断面加工至Ra3.2~1.6,即按常规金相操作进行研磨和抛光,然后用腐蚀剂进行腐蚀,吹干后,用放大镜或金相显微镜进行观察或摄制成金相照片。
(1)宏观检验——用肉眼或低倍放大镜进行直接观察。
分外观检查和低倍分析。
外观检查可以直接发现错边、咬边、裂纹及表面气孔等缺陷,还可以从断口分析确定裂源及扩展方向、断裂性质和断裂类型等。
低倍分析可以了解接头粗晶组织、熔池的形状和深度,即显示焊缝轮廓、熔合线、焊接热影响区的宽度,焊缝柱状晶的生长变化形态,焊道层次,焊接区内的各种缺陷等。
(2)微观检验——用100~1500倍金相显微镜观察金属的显微组织,确定焊接接头各部分的组织特征,晶粒大小,并可估计接头的机械性能、冷却速度,还能查明焊接时焊缝金属和热影响区内碳化物析出情况,以及焊接接头的显微缺陷(如气孔、夹渣、微裂纹、未焊透等)和组织缺陷。