5S手册.docx
《5S手册.docx》由会员分享,可在线阅读,更多相关《5S手册.docx(26页珍藏版)》请在冰豆网上搜索。
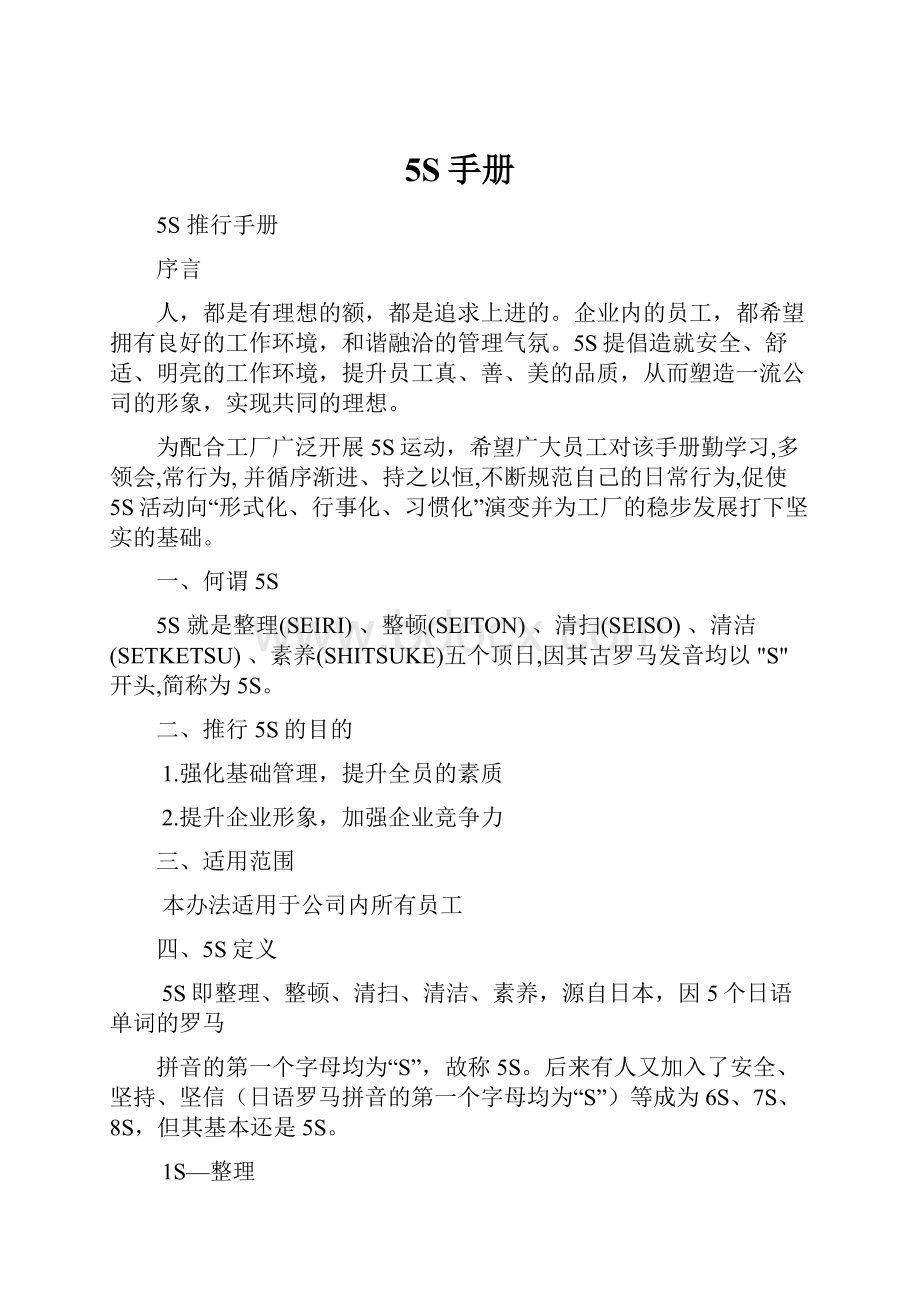
5S手册
5S推行手册
序言
人,都是有理想的额,都是追求上进的。
企业内的员工,都希望拥有良好的工作环境,和谐融洽的管理气氛。
5S提倡造就安全、舒适、明亮的工作环境,提升员工真、善、美的品质,从而塑造一流公司的形象,实现共同的理想。
为配合工厂广泛开展5S运动,希望广大员工对该手册勤学习,多领会,常行为,并循序渐进、持之以恒,不断规范自己的日常行为,促使5S活动向“形式化、行事化、习惯化”演变并为工厂的稳步发展打下坚实的基础。
一、何谓5S
5S就是整理(SEIRI)、整顿(SEITON)、清扫(SEISO)、清洁(SETKETSU)、素养(SHITSUKE)五个顶日,因其古罗马发音均以"S"开头,简称为5S。
二、推行5S的目的
1.强化基础管理,提升全员的素质
2.提升企业形象,加强企业竞争力
三、适用范围
本办法适用于公司内所有员工
四、5S定义
5S即整理、整顿、清扫、清洁、素养,源自日本,因5个日语单词的罗马
拼音的第一个字母均为“S”,故称5S。
后来有人又加入了安全、坚持、坚信(日语罗马拼音的第一个字母均为“S”)等成为6S、7S、8S,但其基本还是5S。
1S—整理
定义:
区分要与不要的东西,必要的物品留下来,不必要的物品彻底清除。
目的:
将空间腾出来活用;
防止误用、误送;
塑造清爽的工作场所。
2S—整顿
定义:
必要的东西依规定定位、定方法、摆放整齐,标识明确。
目的:
不浪费时间找东西。
3S—清扫
定义:
清除工作现场内的脏污,并防止污染的再次发生。
目的:
消除脏污,保持干净、明亮。
4S—清洁
定义:
将上面3S实施的做法制度化、规范化,维持其成果。
目的:
通过制度化来维持成果。
5S—素养
定义:
人人依规定行事,养成良好的习惯。
目的:
提升职工的素质,使我们人人都成为对任何工作都持认真态度的人。
五、推行步骤
步骤1:
组成5S推行组织
1.成立5S推行小组。
2.成立物品处理小组.
3.职责划分明确。
4.部门主管以身作则全身的投入。
5.制定检查周期并定期考核检查。
6.找出差距,持续改进,不断完善。
步骤2:
计划
1.搜集有关5S资料。
2.制定5S年度推行计划。
3.组织培训。
4.制定5S年度实施计划,制定详细的月度实施计划及5S推动日程计划。
5.绘制公司平面布臵图,划分责任区域。
6.5S设施(看板)设计。
步骤3:
宣传培训
1.制定培训计划并组织实施。
2.制作5S标语、宣传口号。
3.制作5S推行手册。
4.最高管理者下达推行5S决心。
步骤4:
全公司一起大扫除
1.全公司上下花费一天的时间将工厂的每一个角落都彻底加以清扫。
2.清扫的同时举行5S运动的宣传,张贴标语、悬挂宣传口号。
3.要掌握好切入5S的时机。
步骤5:
全公司一起实施
1.首先以工作现场领导者为中心,组织全体员工来清理不必要的东西。
2.清理过程中对清理出来的昂贵的东西、责任不明的东西、全公司性的东西及难以判断的东西,要由处理小组负责决定。
3.全公司一起都来实施5S是最重要的。
步骤6:
由推行小组来实施5S改善活动
1.选定涂装车间样板车间挑选出改善项目定出优先顺序制订目标计划并实施。
2.现场5分钟发表大会,由总经理召开大会,开始后点明改善重点.特别要让人知道的涂装车间为“样板车间”作为实施重点。
3.制成现场目视的标识、看板
全公司性统一的部分由执行小组来制成。
.各车间根据本车间现场的实际情况进行设计要有独创性。
序号
1
2
3
4
区域
部门
负责人
步骤7:
活动评比办法确定
1.考核评分法
步骤8:
查核评比及奖惩
1.现场查核
2.依5S活动竞赛办法进行评比,公布成绩,实施奖惩。
步骤9:
不断改善并将5S纳入定期管理活动中
1.标准化、制度化的完善。
2.实施各种5S强化月活动
步骤10:
5S现场诊断
1.每季度一次,由总经理与领导小组巡视现场加以评价,其评价基准以下进行:
a.是否形成部门的行动(班前会、职责划分等是否明确并顺利实施);b.现场上实际实施的状况如何(活用5S检查表)c.现场的活跃度如何(班前会的发言,参与程度等)
2.表现优秀的员工要在班前班后会公开加以表扬。
步骤11:
反复步骤6-7。
.一个循环完成后,再反复实施。
.其差别在于问题点由一个部门已转动到另一部门。
六、明确在5S活动中之责任●岗位职责
1.推行小组岗位职责
1.1推行领导小组:
负责5S活动计划制定和推行工作。
1.2:
组长负责推行领导小组的运作,并指挥领导小组成员实施5S。
1.3副组长职责:
1.3.1辅助推行领导小组事务,并于组长授权时,代行其职务。
1.3.2按照5S活动计划全程执行和监督考核。
1.4执行小组职责
1.4.15S推行计划的拟定。
1.4.2召集会议的举行与资料的整理。
1.4.3相关活动的筹划、推动。
1.4.4评比分数的统计与公布。
1.5成员职责:
1.5.1共同参与5S活动计划,并确保执行。
根据组长的命令,平时为5S活动的
评比委员。
1.5.25S活动办法的拟定。
1.5.35S改善表、评分表的完成。
1.5.4活动的规划。
1.5.5“5S”活动的宣传教育,推动等。
1.5.6定期检查、推动持续改善。
1.5.75S活动现场指导及争议的处理
1.6.会议与记录
为有效推动5S活动,检查执行结果及发现应改善的事项,并评议申诉的案件,定于每周在会议室召开推行小组会议,并做决议和记录。
记录包括的资料:
1.6.1议程、主题
1.6.2时间、地点、出席人员。
1.6.3决议内容。
1.6.4已完成、未完成事项记录。
1.6.5完成期限。
会议次日应将记录转送各小组成员,必要时并在企业内张贴,让全员知道。
2.物品处理小组职责:
负责各部门在实施5S整理过程中将不必需品进行确认,制订处理方法(返修、改做他用、保留、报废等),各小组成员在处理单上签字确认。
经总经理批准实施。
3.员工的职责
3.1不断地整理、整顿自己的工作环境。
3.2及时处理不必要品,不可使不必要品占用作业区域。
3.3维持通道的畅通和整洁。
3.4在规定区域放臵工具、物品。
3.5灭火器、配电盘、开关箱(柜)、电动机、冷气机等的周围要时刻保持清洁。
3.6物品、设备要仔细认真地检查,正确地放臵,安全地轻拿轻放,较大较重的堆在下层。
3.7负责保持自己所负责区域的整洁。
3.8纸屑、布屑、材料屑等要集中在规定场所,不可乱放。
3.9天天不断的清扫,时时保持清洁。
3.10积极配合上级主管安排的工作。
4.主管、科长、车间主任的职责4.1配合公司5S活动计划认真执行。
4.2多方面学习5S知识和技巧。
4.3研读与5S活动相关的书籍,广泛搜集资料。
4.4积极进行本单位的5S活动培训、宣传、教育。
(主要由办公室负责)
4.5对部门内的工作区域进行划分。
(公司区域由办公室与推行小组负责划分)4.6依公司5S活动计划表分解细化为部门工作计划。
4.7帮助部属解决活动中的困难点。
4.8负责5S活动有效实施。
4.9分析和改善5S活动中问题点。
4.10督促部属的整理、整顿、清扫点检工作。
4.11检查员工服装仪容、行为规范。
4.12上班后的点名与服装仪容检查,下班前进行安全巡查确保安全无事故。
七、推行要领
(一)整理的推行要领
1.每个岗位人员对所在的工作场所(范围)进行全面检查,包括看得到和看不到
的。
2.制定“需要”和“不需要”的判断基准。
3.清除不需要物品。
4.调查需要物品的使用频度决定日常用量。
5.制定废弃物处理方法。
6.每日自我检查。
●整理:
区分要和不要的物品,将不要的物品或废弃或放在别处保管。
整理要依阶段依次进行,为求成果仅做一次又不连续做下去,还不如不做。
⑴第一阶段把生产现场需要的物品和不要的物品区分开来并制作一览表。
(见附表)。
⑵第二阶段根据需要程度,实施整理对象的等级化。
⑶第三阶段根据整理基准决定要和不要的物品。
⑷第四阶段绘制平面布臵图,决定放臵物品的场所。
⑸第五阶段标明物品的放臵场所。
⑹第六阶段标明物品的名称、数量。
●如何区分必需和非必需物品呢?
所谓必需物品,是指经常必须使用的物品,如果没有它,就必须购入替代品,否则就会影响工作。
非必需品则可分为两种:
(1)使用周期较长的物品,即一个月,三个月,甚至半年才使用一次的物品;如样品、图纸、零配件等;
(2)对目前的生产或工作无任何作用的,需要报废的物品。
它又包括以下两种:
①非必需用品:
如钉钉子的铁锤,可能不是每天要用,也不可能是每周都要用,但它可能每隔一段时间或每个月会用到一两次,也许半年或一年才会用到几次,就叫做非必需用品;
②不能用的物品:
如过期的图纸、样品,处理方法只有一种,就是放在仓库。
有的东西,是必须要封存的,一年或两年才会用到的,像这一类的东西应放在仓库里封存。
同时把非必需用品摆在库里后,要建立一个档案,并定期地检查。
那么,必需物品的使用频率可能是每小时或每天都要用,也可能每一周都要用,凡是它的使用频率为每小时或每天及每周都要用到的,就称为必需用品。
它的处理方法就是放在工作台上,或是随身携带。
如笔就是我们经常要用的必需用品。
如图示:
●整理基准
区分必需品和非必需品的判定基准
类别
使用频率
内容
处理办法
备注
必需品
每小时
放工作台或随身携带
每天
现场存放
每周
现场存放
非必需品
每个月
仓库存储
三个月
仓库存储
定期检查
半年
仓库存储
定期检查
一年
仓库存储(封存)
定期检查
两年
仓库存储(封存)
定期检查
未定
有用
仓库存储
定期检查
不需要用
变卖/废弃
定期清理
不能用
变卖/废弃
立即废掉
使用说明
目的:
将必需品和非必需品区分开,以便腾出空间,防止误用。
填写:
在内容一栏中填写必需品和非必需品的内容,以便及时清理和方便取用。
●整理事项
〈一〉要
1.正常的设备、机器或电气装臵。
2.附属设备(清色、工作色、料架)。
3.运输车、推车、推高机。
4.正常使用中的于工具。
5.正常工作用的桌、椅、板凳。
6.尚有使用价值的消耗用品。
7.原材料、半成品、成品。
8.尚高利用价值的边料。
9.垫板、塑胶筐、防尘用品。
10.使用中的垃圾桶、垃圾袋。
11.使用中的样品。
12.办公用品、文具。
13.使用中的清洁用品。
14.美化用的海报、看板。
15.推行活动中的海报、看板。
16.有用的书稿、杂志、报表。
17.其他(私人用品)。
(2)不要
1.地板上的:
a.纸箱、灰尘、杂物、烟蒂。
b.油污。
C.不再使用的设备、治工具、模具。
d.不再使用的办公用品、垃圾筒。
e.破垫板、纸箱、抹布、破烂筐。
f.果料或过期样品。
2.桌子上或橱柜内:
a.破旧的书籍、报纸。
b.破椅垫。
C.老旧无用的报表、账本。
d.损耗的工具、余料、样品。
3.墙壁上的:
a.蜘蛛网。
b.过期的海报、看报。
c.无用的提案箱、卡片箱、挂架。
d.过时的月历、标语。
e.损坏的时钟。
4.吊着的:
a.工作台上老旧的指导书。
b.不再使用的配线配管。
C.不再使用的老吊扇。
d.不堪使用的工具。
e.更改后的部门牌。
●红牌作战
红牌作战是指在工厂内,找到问题点(不必需品),并悬挂红牌,让大家都明白并积极的去改善,从而达到整理、整顿的目的。
●红牌方案的出台
成员:
每个部门的领导
时间:
一至两个月。
重点:
教育现场人员不可以将无用的东西藏起来,以制造假象。
●挂红牌的对象
库房:
原材料、零部件、半成品、成品设备、机械。
设备工具:
夹具、模具、桌椅。
防护用品:
储存、货架、流水线、电梯、车辆、卡板等。
注意:
人不是挂红牌的对象,否则容易打击士气,或引起矛盾冲突。
●判定的标准
明确什么是必需品,什么是非必需品,要把标准明确下来。
例如,工作台上当天要用的必需品,其它都是非必需品,非必需品放在工作台上就要挂红牌。
目的就是要引导或要让所有的员工都养成习惯,把非必需全部改放在应该放的位臵。
●红牌的发行
红牌应使用醒目的红色纸,记明发现区的问题、内容、理由。
●挂红牌
相关部门的人也觉得应该挂时才能挂。
红牌要挂在引人注目的地方,不要让现场的人员自己贴,要理直气壮地贴红牌,不要顾及到面子。
红牌就是命令,不容臵疑。
挂红牌一定要集中,时间的跨度不可过长,也不要让大家感觉到,挂红牌而感到厌烦。
●挂牌的对策与评价
也就是对红牌要跟踪检查,一旦这个区域或这个组,或这个机器挂出红牌,所有的人都应该有一种意识,马上都要跟踪检查改进,赶上进度,对实施的效果要实施评价,甚至要对改善前后的实际状况拍照下来,作为经验或成果以向大家展示。
(2)整理的要点
项次
检查项目
具体查检内容
1
整体
无用的东西是否乱放
对不明确是否有用的物品是否放臵不管
对无用的东西有无处理办法
2
屋外
草坪是否脏乱未整理
是否有未处理品
3
作业现场
工作台上、台下设备有无不用的东西
有无不需要的加工品
工具箱、工具橱有无不要的东西
4
抽屉、货架
有否在工具类中放入不需要的东西
有无放入私人物品
5
地面
角落、设备等旁有无放臵不需要的东西
有无不使用的推车、大型专用工具
产品和工具没有直接放臵在地面上
6
文件
是否为有效版本
有无很少翻阅且仅看一次就没有再看的文件或资料
(二)整顿的推行要领
●整顿:
把整理好的物品,放臵在作业时方便使用的地方并进行标准化。
1.要落实前一步骤整理工作。
2.布臵物品流程,确定臵放场所。
3.规定放臵方法。
4.划线定位。
5.标示场所物品。
(每一墙壁都要编码化如墙壁A1墙壁B2)
●放臵物品的方法和放臵场所的标示,是提高作业效率的非常重要的要素。
其实施的要点如下:
①作业工具依使用频度高的顺序放臵。
②放在地上的东西一定要标示线。
③放在货架上的东西一定要标识物品名称。
④文件夹、柜子也要标明内容。
●重点:
.整顿要形成任何人都能立即取出所需要东西的环境状态。
.要站在新进人员和其他现场的人员的立场来看,使得什么东西该放在什么地方更为明确。
.对于放臵处与被放臵物都要想办法使其能立即取出使用。
.另外,使用后要能容易恢复到原位如果没有回复或误放时应能马上知道。
●整顿细节:
(1)要落实前一步骤整理工作
.整理工作没落实则不仅空间浪费而且零件或产品会因变旧不能用而造成浪费;
.连不要的东西也要管理会造成浪费(例如库存管理或盘点都较麻烦);
(2)布臵物品流程,确定臵放场所
.参照整理中“整理基准”,决定物品臵放场所;.物品的放臵场所原则上要100%设定;
.臵放场所可以用电脑模拟或沙盘推移图来演练,以便配臵;
.物品流程布臵基本上依循的原则是:
综合原则、最短距离原则、流程化原则、立体原则、安全与满足感原则以及弹性化原则;.物品的保管要定位、定量、定容;.生产线附近只能放真正需要的物品;.放臵场所的最适空间可运用弹性设定;
.物品堆高标准一般为120cm,高度超过120cm的物料,并臵放在易于取放的墙边;
.危险物品应在特定的场所保管;
.不良容器应及时清除,纸类物品不可放于潮湿场所;
.无法按规定位臵放臵的物品,应挂「暂放」标识牌,注明原因、放臵时间、负责人、预计放至何时等。
(3)规定放臵方法
.以类别型态来决定物品的放臵方法。
①产品按类别放臵,例如某种型号的机械维修工具集中放臵;②配件按类别放臵,例如A型、B型以及0型皮带归类放臵。
.立体放臵,提高收容率。
.尽可能按先进先出的方法放臵。
.危险场所应用栅栏等隔离。
.放臵方法的原则为平行、直角。
.不超过所规定的范围。
.在放臵方法上多下工夫。
.清扫用具以挂式方法放臵。
.必要时,设定物品负责人及点检表。
(4)划线定位
●色带宽度的参考标准:
①主通道:
10cm。
②次通道或区域线:
5-7cm。
●通道宽度的参考标准:
①纯粹人行道:
约8Ocm以上
②单向车道道:
约W车+6Ocm以上(W车为车身最大宽度)③双向车道道:
约W车1+W车2+9Ocm以上
●划线定位方式:
①油漆②定位胶带③磁砖④栅栏
●颜色表示区分:
①黄色:
一般通道、区域线②白色:
工作区域③绿色:
料区、成品区
④红色:
不良品区警告、安全管制等※具体用何种颜色视原先的底色而定。
(5)工作场所物品的标识(目视管理的重点)
●常用的标识1.通道线
生产现场划上通道线,一看便知是供物品运送的通道,不可堆放物品。
2.部门标示牌进入办公室,上面均挂有部门名称,一看就知道是哪个部门,接洽事情方便。
3.产品颜色标识白色代表良品;黄色代表待整修品;红色代表报废品;
一看就知道,不会混料,也易于处理。
4.生产线看板
标示今天生产机种、数量,并记入实际进展状况。
生产线每个成员一看就知道,易于激发参与感。
5.图表
图表内可能表示产量的、效率的、品质的或其他的状况,一看就知道起伏状况,是否在控制中,易于管理。
6.生产工令加上急
表示急件生产,要优先处理。
目视管理的技巧运用范围相当广,主要的是在平常的管理工作中,如何应用最简便的标示来减少管理的依存度,又可提高工作效率,又不容易出错。
在工厂内使用较多的方法,有上述的看板、颜色、图表、标记等。
7、物品标识部位:
粘贴在明显的部位
工作台、桌椅板凳:
标识在侧面左上角
门:
标识粘贴在明显的部位
窗玻璃:
标识在右下角
椅子:
标识在椅子后背横撑中间
拉车等:
标识在前侧右上角
9、标识检查:
①整体:
决定且标识放臵场所吗?
遵守了直角平行吗?
有无危险的放臵方法?
②测量工具:
放臵场所是否按种类区分开来放臵的?
工具作了标准化吗?
是需要的最小限量吗?
③加强:
规定了标准的加工量吗?
规定了加工品的放臵场所吗?
明确了表示加工品的名称和数量吗?
④作业现场
有道路标识吗?
表示物、揭示物容易看见吗?
地面上有凸起物吗?
地面有滑的地方吗?
⑤通道表示
.为了区别通道和非通道的区域,在通道上用白线或黄线来表示。
.通道上放物品时,要摆放写有“通道使用许可”的标牌。
⑥工作现场平面布臵图
每个工作现场要有表示工作现场布臵图,按照布臵图进行放臵。
⑦设备运转标识
.所有设备都须有标识,如完好设备、待修设备、闲臵、材料中断、生产中断、停机等
.标识上须有责任人、检查人等。
⑧仓库的标识
.成品库的平面布臵图
.在仓库内的各物品均有标识,货架上要有编号,各货架上左右位臵及上下段要有具体编号来规定特定位臵.拨码卡与物量相符
⑨材料、成品标识:
要有名称编号,规定每箱/每袋的装入数量,在每箱/每袋上标明产品名称和实际数量,生产日期等
⑩作业标识:
危险作业有危险标识。
电工作业要有作业标识,如正常工作、禁止合闸等
1、夹具量具等的整顿
(1)将量具放臵在机器台上,为防止滑落或撞击,必须铺上橡胶垫。
(2)圆筒状类测量器具等,放臵在一起时前后方向应一致,互相间隔开。
(3)细长的试验板、规尺等,为防止翘曲,应以垂直吊挂为宜。
(4)测试用水平台不用时,须加盖子。
(5)量具必须注意防尘、防污、防锈,不用时涂上防锈油或用浸油的绒布覆盖2、在制品的整顿
在生产现场,除了设备和材料,在制品是占据生产用地最多的物品因此也是生产现场的主要对象。
●“整顿”在制品应考虑以下问题:
(1)严格规定在制品的存放数量和存放位臵。
确定工序交接点、生产线和生产线之间的中继点(工序与工序之间半成品暂放区)所能允许的在制品标准存放量和极限存放量,指定这些标准存放量的放臵边界、限高,占据周转车数、面积等,并有清晰的标示一目了然。
(2)在制品堆放整齐,先进先出。
在现场堆放的在制品,包括各类载具、搬运车等,要求始终保持叠放整齐,边线相互平行或垂直于主通道,既能使现场整齐美观,又便于随时清点,确保在制品“先进先出”。
(3)合理的搬运。
.放臵垫板或容器时应考虑到搬运的方便。
.利用传送带或有轮子的容器来搬动。
(4)在制品存放和移动中,要慎防碰坏刮痕,应有缓冲材料将在制品间隔以防碰堆放时间稍长的要加盖防尘,不可将在制品直接放在地板上。
(5)不良品放臵场地应用红色标示。
如果将不良品随意堆放,容易发生误用,所以要求员工养成习惯,一旦判定为不良品,应立即将其放臵在指定场所。
3、仓库的整顿
●以定位、定量、定容来整顿仓库。
(1)定位
.材料及成品以分区、分架、分层来区分。
.设臵仓库总看板使相关人员对库存现状的把握能一目了然。
.搬运工具(拉车、周转车、推车)的定位以便减少寻找时间。
.严格仓库物品的入库时间和物品发放时间。
(2)定量
.相同的物品,在包装方式和数量上应尽量一致。
.设定标准的存放量。
.设定最高限量基准。
(3)定容
各种材料、成品的规格不一,要有不同的容器来装载,大小不一的容器不仅显得不整齐,同时也浪费空间,容器的规格选择亦须考虑搬动的方便。
4、办公室的整顿
(1)工作区域
.有隔间的,在门口处标示部门。
.有隔屏的,则在隔屏的正面标示部门。
.无隔屏的,则在办公桌上以标示牌标示。
.办公设备实施定位,绘制平面布臵图。
.桌垫底下放臵的内容最好统一规定,保持整洁。
.长时间离位以及下班时,桌面物品应归好位,锁好抽屉,摆好椅子,逐一确认后才离开。
(2)资料档案
.整理所有的文件资料,并依大、中、小进行分类。
.不同类别活用颜色管理方法。
.文件内页引出纸或色纸,以便索引检出。
(3)看板、公告栏
.看板、公告栏的板面格局区分标示,如“公告”“资料张贴”等。
.及时更新资料(4)会议室、教室
.所用物品如椅子、烟灰缸、投影仪、电视机、VCD、笔、笔擦等应定位。
.设定责任者,定