超声相控阵检测教材第八章现场实际应用.docx
《超声相控阵检测教材第八章现场实际应用.docx》由会员分享,可在线阅读,更多相关《超声相控阵检测教材第八章现场实际应用.docx(34页珍藏版)》请在冰豆网上搜索。
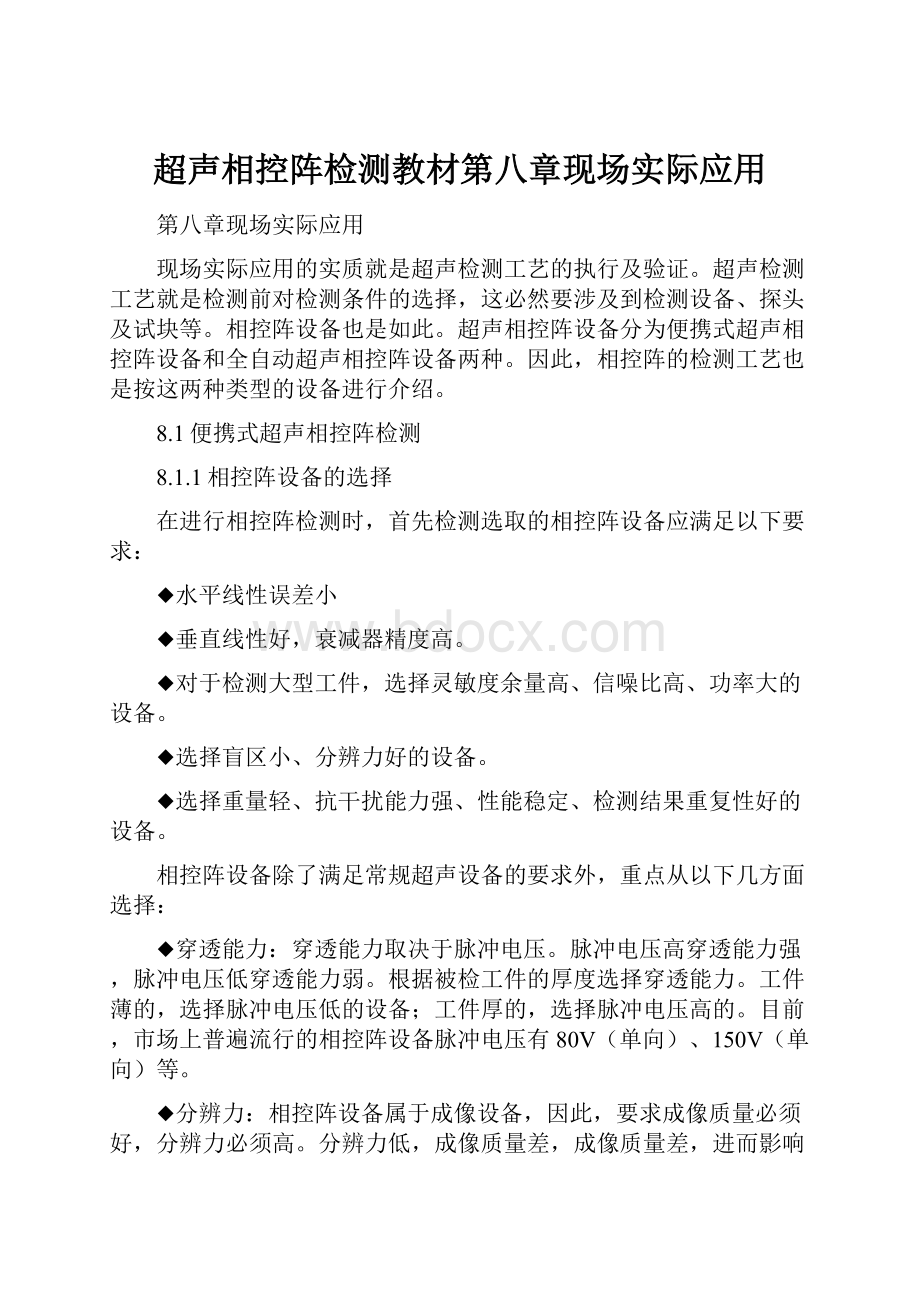
超声相控阵检测教材第八章现场实际应用
第八章现场实际应用
现场实际应用的实质就是超声检测工艺的执行及验证。
超声检测工艺就是检测前对检测条件的选择,这必然要涉及到检测设备、探头及试块等。
相控阵设备也是如此。
超声相控阵设备分为便携式超声相控阵设备和全自动超声相控阵设备两种。
因此,相控阵的检测工艺也是按这两种类型的设备进行介绍。
8.1便携式超声相控阵检测
8.1.1相控阵设备的选择
在进行相控阵检测时,首先检测选取的相控阵设备应满足以下要求:
◆水平线性误差小
◆垂直线性好,衰减器精度高。
◆对于检测大型工件,选择灵敏度余量高、信噪比高、功率大的设备。
◆选择盲区小、分辨力好的设备。
◆选择重量轻、抗干扰能力强、性能稳定、检测结果重复性好的设备。
相控阵设备除了满足常规超声设备的要求外,重点从以下几方面选择:
◆穿透能力:
穿透能力取决于脉冲电压。
脉冲电压高穿透能力强,脉冲电压低穿透能力弱。
根据被检工件的厚度选择穿透能力。
工件薄的,选择脉冲电压低的设备;工件厚的,选择脉冲电压高的。
目前,市场上普遍流行的相控阵设备脉冲电压有80V(单向)、150V(单向)等。
◆分辨力:
相控阵设备属于成像设备,因此,要求成像质量必须好,分辨力必须高。
分辨力低,成像质量差,成像质量差,进而影响缺陷定量。
因为成像质量差,能将两个相邻且独立的缺陷连在一起,进而使缺陷放大。
◆图像显示:
相控阵设备是成像设备,对成像显示方式主要有两种类型:
1)按声程显示成像
2)按真实几何结构成像。
按真实几何结构成像显示优点:
图像显示直观、易懂,数据分析容易,很容易让人接受。
见图8-1所示。
(a)按声程显示成像
(b)按真实几何结构成像
图8-1成像显示方式
◆抗干扰能力
便携式设备适用范围广,环境复杂。
因此要选择抗干扰能力强、性能稳定及检测结果重复性好的相控阵设备。
8.1.2探头的选择
1、基本术语
1)相控阵探头晶片
相控阵探头的晶片由压电复合材料制作。
压电复合材料的探头信噪比比一般压电陶瓷探头高10dB~30dB。
是将一块整体压电复合材料的晶片切割成无数微小的晶片(如图8-2所示),每个晶片能单独激发。
图8-2一维线性相控阵探头参数术语
A—主动孔径
W—晶片宽度(也叫被动孔径)
e—阵元晶片长度g—阵元晶片之间距离
P—e+g
t—晶片厚度(高度)
2)声束
相控阵声束的三个重要的术语:
◆主瓣(M)
◆旁瓣(S)
◆柵瓣(G)
图8-3典型的线性相控阵声束指向性图(8晶片线性相控阵探头,偏转角为30°)
2、探头参数
相控阵探头参数的选择主要从以下几方面考虑:
◆频率
◆阵元间距
◆阵元宽度
◆阵元数量
◆偏转角
1)频率
频率的影响:
(1)频率高,灵敏度高。
由于波的绕射,使超声波检测灵敏度约为λ/2,因此提高频率,有利于发现更小的缺陷。
(2)频率高,主瓣宽度小。
频率高,脉冲宽度小,分辨力高,有利于区分相邻缺陷。
(3)频率高,聚焦效果好。
频率高,波长短,半扩散角小,声束指向性好,能量集中,有利于发现缺陷并对缺陷定位。
(4)频率高,近场长度大。
(5)频率高,衰减大。
2)阵元间距
阵元间距影响:
(1)影响主瓣和栅瓣
阵元间距越大,主瓣宽度越窄,但是间距变大,会出现栅瓣(如图8-4所示),所以有一个极限值(0.1mm),小于这个值则不会出现栅瓣。
(2)对旁瓣影响不大
旁瓣随着阵元间距的增大而变化不大,这说明阵元间距对旁瓣影响不大。
图8-4不同阵元间距的声束指向性
3)阵元宽度
阵元宽度影响:
(1)阵元宽度大,声压值高,检测灵敏度高。
(2)阵元宽度对栅瓣位置没有影响,且对主瓣宽度和旁瓣影响不大。
旁瓣有所降低,但最大旁瓣高度基本不变。
随着阵元宽度变大,主瓣高度降低,又因为最大旁瓣高度不变,相当于旁瓣级升高。
所以,在满足其它要求不变的情况下,应尽量选择宽度小的阵元。
也就是说,阵元宽度变大,旁瓣级也升高,但是最大旁瓣高度基本不变。
4)阵元数量
(1)阵元数对旁瓣的影响
阵元晶片数增多,旁瓣级减小,如图8-5所示。
图8-5阵元数与旁瓣的关系
由图8-5可知,当N从0增大时,旁瓣急剧减小;当N>16并继续增大时,旁瓣趋于-13.5dB的极限值。
可见,N对旁瓣的抑制作用非常明显,当设计相控阵探头对旁瓣有严格要求时,应首先考虑增加阵元数N。
(2)阵元数对主瓣的影响
阵元数的增加不但可以减小主瓣宽度,还可以降低旁瓣。
如图8-6和图8-7所示。
图8-6不同阵元数的指向性图8-7阵元数与主瓣宽度的关系
由图可得,当N>32时,阵元数的增加对主瓣宽度和旁瓣都影响不大。
所以阵元数取32以上即可。
(3)阵元数增多,主动孔径(A)变大,也就是晶片尺寸变大,超声波能量大(也就是声压值高),检测灵敏度高。
(4)阵元数增多,聚焦效果好,见图8-8所示。
图8-8晶片数不同,聚焦效果不同
5)偏转角
偏转角影响主瓣和栅瓣。
偏转角也就是扇形扫查中角度范围。
线性相控阵探头偏转角在一定范围内时,探头可获得较好的指向性.随着偏转角的增大,主瓣变宽(如图8-9所示),声束能量降低,所以在进行扇形扫查时要做角度增益补偿。
偏转角继续增大时,主瓣角宽度继续增大,而且会产生栅瓣。
栅瓣的出现也与楔块的角度有关。
可见在实际检测中,必须把偏转角度确定在一个合理的范围,才能获得可靠的检测效果。
图8-9扇形扫描动态图(偏转角)
◆相控阵探头参数选择总结:
表8-1检测焊接接头时相控阵探头参数选择推荐表
工件厚度(㎜)
相控阵探头
一次激发的晶片数(个)
主动孔径(㎜)
标称频率(MHz)
8~15
16
8
7.5
>15~80
16
8
5/4
>80~150
32
16
5/4
8.1.3参考试块的选择
参考试块用于检测校准的试块。
例如JB/T4730.3-2005中的CSK-ⅡA及CSK-ⅢA试块。
RB-3试块也是用于校准的参考试块。
这些试块仅能适用于检测工件厚度小于等于100mm的焊缝,工件厚度大于100mm的焊缝要另行设计试块。
8.1.4DAC曲线的制作
DAC曲线制作与常规超声检测制作DAC曲线一致。
距离—波幅曲线制作:
调节“增益”,使第一个反射体的最大波高达到满屏高度的80%(误差为±5%),该波高为基准波高;然后保持灵敏度不变,依次探测其他反射体,找到最大反射波高;将不同的深度及其对应的最大波高连接起来,即可成为距离—波幅曲线。
制作完DAC曲线后,再进行扇形范围内的角度补偿。
得到扇形角度范围内的一系列DAC曲线。
◆DAC曲线需要注意以下几点:
(1)制作DAC曲线时,一般选择扇形扫查范围内的中间角度制作DAC曲线。
(2)最大声程处反射体波高不得低于满屏高度的20%。
低于此值应分开制作DAC曲线。
即按一次波和二次波分开制作。
例如检测工件厚度为30mm的焊缝,检测采用一次波和二次波检测。
因此制作DAC曲线时必须达到60mm深孔的位置,也就是说60mm深孔的波高不得低于满屏高度的20%。
如果低于20%,则按一波和二次波分开制作DAC曲线。
如果不分开制作,用一次波灵敏度检测,对二次波检测范围灵敏度不够,会漏检。
如果用二次波灵敏度检测,对于一次波检测范围灵敏度过高,成像质量极差,定量偏差很大。
(3)如果采用聚焦声束检测,只有在焦柱长度范围内对应的深度范围应用DAC曲线是有效的。
8.1.5扇形扫查角度范围的选择
扇形角度范围选择原则:
(1)扇扫起始角度必须大于第一临界角对应的折射角。
根据折射定律计算第一临界角α1。
例如楔块声速为2337m/s,,钢中纵波声速为5950m/s,钢中横波声速为3230m/s。
α1=23.1°,再计算出折射角β,β=32.8°。
所以扇扫起始角度大于32.8°。
(2)扇扫角度范围不要过大,过大会出现栅瓣,产生鬼影。
(3)扇形角度范围一般为38°-70°。
大于70°受温度影响严重。
特殊情况也可设置为35°-80°。
图8-10是楔块材料为有机玻璃计算出来的角度。
(4)扇形角度范围一般要根据检测对象来确定:
◆扇形角度范围选择可根据设备中的理论计算软件来设置,通过演示看是否合理,见图11所示。
◆理论软件中焊缝宽度参数的输入,要在实际焊缝上测量后再输入。
图8-10有机玻璃/钢界面上的声压往复透射率
楔块材料为有机玻璃。
当αL=27.6°(αⅠ)-57.7°(αⅡ)时,钢中只有折射横波,无折射纵波。
折射横波的往复透射率最高不超过30%,这时对应的αL=30°,βS=37°。
图8-11计算扇形角度范围及探头距离的软件
◆如果可以在被检焊缝两侧扫查,角度范围要小些。
因为范围太大,角度增益补偿大。
影像重叠部分大。
图8-12的设置角度范围太大,重叠部分也大,造成图像叠加,就不如图8-13设置。
但是这两种设置不如按一次波和二次波分开设置合理,见图8-14所示。
图8-12扇形角度范围为35°-80°图8-13扇形角度范围为35°-75°
(a)一次波扇形角度范围为50°-75°(b)二次波扇形角度范围为35°-55°
图8-14将一次波和二次波分开设置
◆由于结构原因,只能在单侧检测,角度范围要大些,要尽可能保证焊缝全覆盖,如图8-15所示。
图8-15扇形角度范围为35°-80°
8.1.6探头前端距焊缝边缘的距离
探头前端距焊缝边缘的距离(L)设置很关键,它决定检测覆盖范围,还要考虑探头是否上焊缝、也就是说线性扫查是否可行的,换句话说就是采用几次波检测的问题。
要根据理论软件计算来设置,如图8-16所示。
图8-16L参数示意图
8.1.7扫查方式
用相控阵探头对焊缝进行检测时,无需象普通单探头那样在焊缝两侧频繁地来回前后左右移动,而相控阵探头沿着焊缝长度方向平行于焊缝进行直线扫查,对焊接接头进行全体积检测。
该扫查方式可实现快速检测,检测效率非常高,如图8-17所示。
图8-17PA探头平行于焊缝方向扫查
8.1.8工艺参数设置及缺陷分析
1、T=3.5mm的试板
1)预制根部未焊透
根部未焊透规格:
77㎜×2㎜×1.5㎜
图8-18预制根部未焊透
2)采用相控阵检测
(1)PA探头参数
7.5MHz、32晶片的相控阵探头,p=0.5mm、e=0.4mm、g=0.1mm。
(2)采用Ф2x20mm横通孔试块制作DAC曲线。
(3)采用三次波和四次波分开设置进行检测。
(4)PA探头前端距焊缝边缘的距离为10mm。
(5)检测结果
根部未焊透检测结果:
长度76.9mm、深度2.4mm、幅度大于130%,位于Ⅲ区,判为Ⅲ级。
(a)采用三次波和四次波检测图
(b)未焊透缺陷
图8-19根部未焊透检测结果
3)RT检测结果
未焊透缺陷在RT底片上显示长度为65㎜,见图8-20所示。
图8-20未焊透缺陷在RT底片上显示
4)解剖验证
解剖验证未焊透自身高度为1.3㎜,见图8-21所示。
图8-21解剖未焊透自身高度为1.3㎜
2、T=19mm的试板
1)预制根部裂纹及坡口未熔合
(a)预埋缺陷位置
①根部裂纹规格:
85㎜×0.3㎜×3.0㎜②坡口未熔合规格:
50㎜×3.5㎜×4.3㎜
(b)预埋缺陷布置图
图8-22预埋缺陷图
2)PA检测结果
1)PA探头参数
4MHz、32晶片的相控阵探头,p=0.5mm、e=0.4mm、g=0.1mm。
(2)采用Ф2x20mm横通孔试块制作DAC曲线。
(3)采用一、二次波进行检测。
(4)扇形角度范围(40°-70°)
(5)PA探头前端距焊缝边缘的距离为15mm。
(6)PA检测结果
PA检测发现一个裂纹和一个坡口未熔合。
裂纹长度为85㎜,坡口未熔合的长度为48㎜,见图8-23所示。
(a)PA检测图
(b)根部裂纹
(c)坡口未熔合
图8-23PA检测结果
3)TOFD检测结果
TOFD检测结果见图8-24所示。
(1)根部裂纹
采用TOFD测量根部裂纹的深度为17.7㎜,自身高度为2.3㎜,长度为82㎜。
(2)坡口未熔合
采用TOFD测量坡口未熔合的深度为6.1㎜,高度为4.9㎜,长度为47.5㎜。
图8-24TOFD检测结果
4)RT检测结果
(1)根部裂纹缺陷在RT底片上显示长度为79㎜,见图8-25所示。
图8-25根部裂纹缺陷在RT底片上显示
(2)坡口未熔合缺陷在RT底片上显示长度为25㎜,见图8-26所示。
图8-26坡口未熔合缺陷在RT底片上显示
5)解剖验证
(1)解剖验证根部裂纹自身高度为2.5㎜,见图8-27所示。
图8-27解剖根部裂纹自身高度为2.5㎜
(2)解剖验证坡口未熔合自身高度为4.5㎜,见图8-28所示。
图8-28解剖坡口未熔合自身高度为4.5㎜
3、T=14㎜的试板
1)预制中间裂纹
中间裂纹规格:
65㎜×0.3㎜×3.5㎜
图8-29预埋中间裂纹示意图
2)PA检测
PA检测发现中间裂纹,其长度为67.4㎜,深度为7.8㎜,幅度为DAC+15.7dB,位于Ⅲ区,评为Ⅲ级,见图8-30所示。
(a)PA检测图
(b)中间裂纹
图8-30中间裂纹检测结果
3)TOFD检测
TOFD检测发现中间裂纹,该缺陷深度为6.4㎜,自身高度为2.5㎜,长度为63㎜,见图8-31。
图8-31TOFD检测中间裂纹
4)RT检测
中间裂纹缺陷在RT底片上显示长度为58㎜,见图8-32所示。
图8-32中间裂纹在RT底片上显示
5)解剖验证
解剖验证中间裂纹自身高度为2.5㎜,见图8-33所示。
图8-33解剖中间裂纹自身高度为2.5㎜
4、角焊缝
T=14㎜的单X型坡口与T=19㎜的板焊成的T型角焊缝检测
1)预制根部未焊透与坡口未熔合
根部未焊透的规格:
45㎜×2.0㎜×2.0㎜;坡口未熔合的规格:
25㎜×3.5㎜×2.9㎜
图8-34T-X型角焊缝预制缺陷图
2)实物图
图8-35T-X型角焊缝实物图
3)PA检测
PA检测发现中间未焊透和坡口未熔合缺陷。
中间未焊透缺陷长度为17.9㎜,深度为8.4㎜,自身高度为2.2㎜,幅度大于130%,位于Ⅲ区,评为Ⅲ级。
坡口未熔合缺陷长度为18㎜,深度为2.1㎜,自身高度为3.2㎜,幅度DAC+2.8dB,位于Ⅲ区,评为Ⅲ级。
见图8-36所示。
(a)中间未焊透
(b)坡口未熔合
图8-36T-X型角焊缝PA检测结果
8.2全自动超声相控阵检测
8.2.1为什么采用全自动超声相控阵检测
超声TOFD(TimeofFlightDiffraction)技术即超声波衍射时差技术,自1975年在英国问世以来,便受到人们的普遍重视并应用于焊缝的检测。
近年来,超声TOFD检测在我国石化、电力及特种设备等行业已经开始应用,并得到认可。
TOFD技术的优势是测量缺陷的自身高度,为断裂力学“工程临界分析法”(ECA)的评判提供关键的指标,但在实际应用中也暴露出TOFD技术的不足,即:
(1)TOFD存在盲区
TOFD在工件上下表面存在盲区。
(2)TOFD检测效率低
TOFD扫查有两种方式,一种是非平行扫查,另一种是平行扫查。
平行扫查效率极低,但定量精度高,一般不采用此扫查方式,仅在实验室或对某一缺陷精确定量和定位时采用。
非平行扫查速度快,但不能判定缺陷在焊缝的哪一侧,给定位增加难度,有时需要进行多次扫查来确定缺陷的位置,致使检测效率降低。
检测中常采用非平行扫查方式。
(3)TOFD缺陷的评定
众所周知,TOFD技术不是基于幅度法进行检测的,检出率远高于其他检测方法(例如手动超声波检测、机械超声波检测及射线检测等)这是总所周知的事实。
不论是大缺陷还是小缺陷都能检出,这给缺陷评定增加难度,控制不好返修率相当高,甚至出现有的缺陷返修后看不见的现象。
因此,必须采用合理的方法与TOFD技术联合使用才能体现出TOFD技术的特点,也就是说采用幅度法与非幅法组合技术检测环向对接接头,有着十分重要的意义。
具体说就是采用相控阵技术与TOFD技术组合应用检测环向对接接头。
8.2.2组合方式
组合检测技术中的幅度法是以超声相控阵检测技术为主。
幅度法和非幅度法组合有两种方式,即:
(1)相控阵技术中的线形扫描与TOFD组合,就是我们常说的全自动超声相控阵检测技术(以下简称PA-AUT)。
该组合方式用于检测壁厚为6~60㎜的环向对接接头,主要用于检测管道环向对接接头。
(2)相控阵技术中的扇形扫描与TOFD组合,就是厚壁焊缝全自动超声相控阵检测技术(以下简称BIG-PA-AUT)。
该组合方式用于检测壁厚为6~200㎜的环向对接接头,主要用于检测锅炉、压力容器及管道等环向对接接头。
8.2.3管道全自动超声相控阵检测(PA-AUT)
8.2.3.1AUT的概念
所谓全自动超声波检测就是将焊缝沿厚度方向分成若干区,每个区用一对或两对聚焦探头(声束)检测,同时还采用非聚焦探头(声束)检测,因此要求检测系统是多通道;检测结果以图像形式显示,分为A扫描、B扫描及超声衍射波时差法(TOFD)三种显示方式;扫查器在管道环向采用自动扫查和自动声耦合,对整个焊缝厚度方向的分区进行全面检测,并自动将检测结果和声耦合显示在图像上。
8.2.3.2检测原理
(1)采用分区法检测
①分区法的概念
分区法是指将焊缝沿厚度方向分成若干个区;每个区用一对或两对聚焦探头(声束)检测,同时还采用非聚焦探头(声束)检测;扫查器在管道环向扫查一周,即可对整个焊缝厚度方向的分区进行全面检测。
②区域划分
区域划分就是将被检焊缝按检测的要求分成若干个区。
焊缝的区域划分根据焊缝的坡口参数及焊接填充次数进行,不同厚度的焊缝填充次数是不一样的,因此分区也是不一样的。
图8-37是典型的焊缝分区,该分区是焊接分区,与检测分区可能不一样,但有时也可能相同。
图8-37焊缝焊接分区及缺欠简图
分区的原则是根据检测标准、规范而定,一般来讲每个区高度为1㎜~3mm,分区高度越细越好,缺欠定量越精确。
分区高度也不易过大,过大易漏检,也不易太小,太小调试困难,一般最小为1mm,最大为3mm,也可大于3mm,根据检测需要而定。
图8-38是焊缝的检测分区。
图8-38厚度为14.6mm焊缝的检测分区
③典型的分区法检测探头配置
图8-39是管道环焊缝检测实例。
壁厚为12.6mm,采用自动气体保护焊焊接。
图8-39全自动多探头超声波声束分布示意图
图8-39的示意图为全自动多探头超声波检测系统声束布置图,而全自动相控阵超声波检测系统仅用两个探头就能实现声束分布,而不是多个探头,如图8-40所示。
图8-40全自动相控阵超声波声束分布示意图
(2)采用三种扫描方法
采用A扫描(即带状图)、B扫描和TOFD三种方法检测。
其中带状图采用聚焦探头(声束)检测,B扫描和TOFD采用非聚焦探头(声束)检测。
①带状图是由A扫描横波聚焦声束形成的。
主要负责检测焊缝坡口面上的面积型缺欠,如坡口未熔合等。
这里谈到带状图就得涉及到线形扫描。
见图8-41、图8-42所示。
图8-41焊缝单侧线形扫描图(AUT中带状图的原理)
图8-42带状图对应的检测分区
②B扫描就是体积通道,也叫图形通道,由横波非聚焦声束形成的。
它主要负责检测焊缝盖面、填充区及根部等区域的体积型缺陷,如气孔等,如图8-43所示。
(a)横波非聚焦声束检测根部缺欠
(b)横波非聚焦声束检测填充区及盖面区缺欠
(c)横波非聚焦声束检测区域整体组合图
图8-43B扫描检测区域图
③TOFD是由纵波非聚焦声束形成的。
它主要负责检测盲区以外的体积型和面积型缺欠,如气孔、未熔合等,如图8-44所示。
图8-44TOFD检测区域图
显示记录
标准的输出显示记录包括双门带状图通道(又叫A扫描通道)、图形通道或体积通道(又叫B扫描通道)、TOFD通道、耦合通道、编码器扫查的位置及标记缺欠显示,见图8-45和图8-46所示。
图8-45全自动多探头超声检测显示图
图8-46PA-AUT焊缝的输出显示记录图
扫查方式
全自动超声波采用线形扫查对管道环向焊缝进行检测。
线形扫查就是探头距焊缝边缘一定距离沿焊缝方向做平行于焊缝的直线运动。
采用两个探头在焊缝单面双侧同时进行扫查。
如图8-47所示。
图8-47AUT的线性扫查方式
AUT检测设备
AUT检测设备分为两种设备,即全自动多探头超声波检测系统(见图8-48)和全自动相控阵超声波检测系统(见图8-49)。
在AUT概念中“每个区用一对或两对聚焦探头(声束)检测,同时还采用非聚焦探头(声束)检测”。
这就话中的“探头”指的是多探头系统,“声束”指的是相控阵系统。
检测采用分区法,所以要求AUT系统是多通道的,否则无法满足检测要求。
图8-48全自动多探头超声波检测系统的扫查器及探头盘
图8-49ISONICPA-AUT系统简图
探头
PA-AUT检测采用分区法,需要设备具有足够多的通道,这就要求相控阵探头具有足够多的晶片数。
目前PA-AUT检测使用的相控阵探头晶片数一般为60晶片和64晶片。
就能满足壁厚为6mm-50mm焊缝的检测要求。
探头频率一般采用5MHz和7.5MHz。
线形相控阵探头其它性能指标与便携式超声相控阵设备中的相控阵探头一样。
试块
全自动超声波检测试块与常规手动超声波检测试块不同之处就是全自动超声波检测试块按焊缝的坡口型式、焊层厚度及可能产生的缺欠类型设计的。
全自动超声波试块上人工反射体的布置就是完整的坡口型式。
(1)试块的材料
试块的材料应是被检管道的一段,也可以用规格相同声学性能相似的材料制成。
试块的材料在Φ2mm平底孔灵敏度检测时,不得出现大于Φ2mm平底孔回波幅度1/4的缺欠信号。
(2)分区原则
根据焊缝坡口参数及焊接层数来分区,每个区高度一般为2mm~3mm,在坡口熔合线上设置两个对称的人工反射体来调节灵敏度和缺欠定位。
该反射体为主反射体,采用聚焦探头检测。
(3)人工反射体的设置
①在坡口面上设置人工反射体直径为2~3mm的平底孔。
平底孔轴线应垂直于坡口面且在坡口面长度方向等分;见图8-50(c)、(d)。
②在外表面的熔合线上设置方型槽,其深为1mm、宽为2mm、槽长为10~20mm。
也可在根焊区设槽,长度为10~20mm,其深度和角度应与被检焊缝根部坡口形式一致;见图8-50(a)、(c)。
③在焊缝中心线上设置一个直径为2mm的通孔或制作一个宽1mm、长5mm的通槽,该孔或槽轴线应与焊缝截面中心线相重合且垂直于管壁;见图8-50(e)
④必要时,可在钝边处设一个平底孔,其轴线垂直于钝边并与钝边中心重合。
见图8-50(b)。
⑤除上述规定的反射体外,还可以增加体积通道反射体、TDFD验证反射体,也可增加横向缺欠等附加反射体,但不得与规定的反射体相抵触。
见图8-50(f)。
图8-50AUT试块一侧人工反射体简图
图8-51AUT试块的实物图
检测标准
目前AUT检测主要有以下几个:
国内标准:
SY/T6755-2009在役油气管道对接接头超声相控阵及多探头检测
SY/T0327-2003石油天然气钢质管道对接环焊缝全自动超声波检测
Q/SYXQ6-2002西气东输管道工程管道对接环焊缝全自动超声波检测
国外标准:
API1104、ASTME1961、DNV2000。
检测设置
根据检测标准进行设置。
现对检测设置作简要介绍。
要实现在管子上移动一周完成整条焊缝中各个分区的检测,应进行系统设置和