焦化厂生产技术操作规程.docx
《焦化厂生产技术操作规程.docx》由会员分享,可在线阅读,更多相关《焦化厂生产技术操作规程.docx(94页珍藏版)》请在冰豆网上搜索。
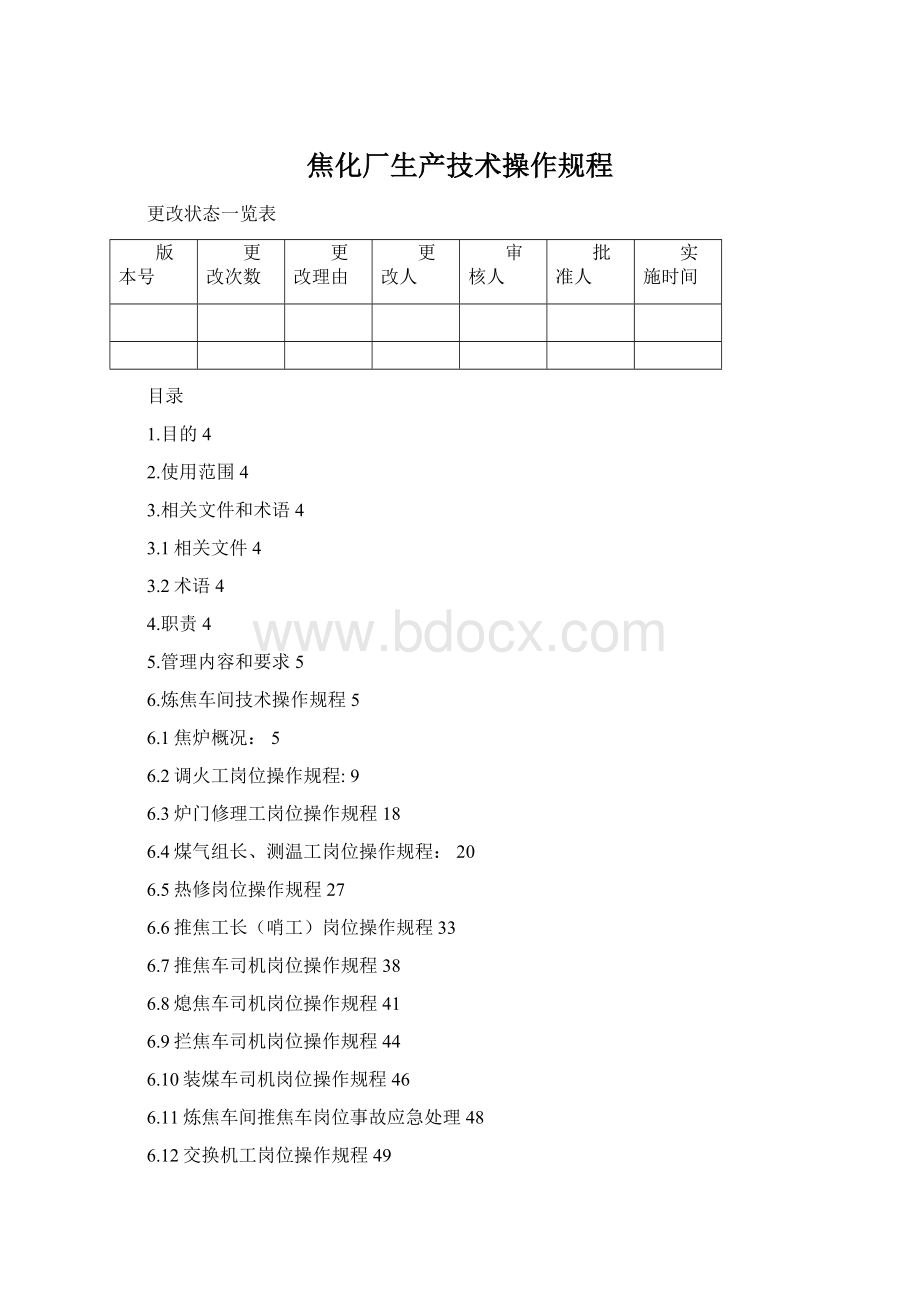
焦化厂生产技术操作规程
更改状态一览表
版本号
更改次数
更改理由
更改人
审核人
批准人
实施时间
目录
1.目的4
2.使用范围4
3.相关文件和术语4
3.1相关文件4
3.2术语4
4.职责4
5.管理内容和要求5
6.炼焦车间技术操作规程5
6.1焦炉概况:
5
6.2调火工岗位操作规程:
9
6.3炉门修理工岗位操作规程18
6.4煤气组长、测温工岗位操作规程:
20
6.5热修岗位操作规程27
6.6推焦工长(哨工)岗位操作规程33
6.7推焦车司机岗位操作规程38
6.8熄焦车司机岗位操作规程41
6.9拦焦车司机岗位操作规程44
6.10装煤车司机岗位操作规程46
6.11炼焦车间推焦车岗位事故应急处理48
6.12交换机工岗位操作规程49
6.13煤塔司磅工岗位操作规程52
6.14铁件工岗位技术操作规程53
7.回收车间生产技术操作规程55
7.1班长职责55
7.2煤气鼓风机岗位操作规程55
7.3冷凝岗位操作规程61
7.4循环水岗位操作规程65
7.5空压机操作规程68
7.6电捕焦油器操作规程70
7.7制氮机岗位技术操作规程72
7.8粗苯岗位操作规程74
8.备运车间技术操作规程79
8.1煤场管理岗位操作规程79
8.2煤场喷水工岗位操作规程80
8.3漏煤工岗位操作规程80
8.4配煤工岗位操作规程81
8.5运煤皮带机岗位操作规程83
8.6粉碎机岗位操作规程84
8.7放焦工岗位操作规程85
8.8运焦皮带工岗位操作规程86
附表188
附表288
附表389
1.目的
为规范各岗位作业程序,使各项工作有条不紊的进行,达到标准化要求,特编制本指导作业技术规程。
2.使用范围
本技术操作规程适用于焦化厂各生产车间的各个工艺流程及岗位操作。
3.相关文件和术语
3.1相关文件
《文件管理程序》
3.2术语
3.2.1程序文件
对相关的控制活动规定具体实施内容、范围、目的、职责、方法和步骤,以实现管理要求的文件。
3.2.2作业文件
对某些操作或控制过程做出更加具体规定的文件,是程序文件的支持性文件。
如:
管理制度、管理办法、规程、作业指导书、记录等。
4.职责
4.1各单位及相关人员根据生产技术操作规程的规定具体落实各岗位、各工艺的技术操作标准。
4.2各岗位必须严格按照本规程进行标准化、规范化操作。
5.管理内容和要求
焦化厂包括炼焦车间、回收车间、备运车间、机动科、生产技术科化验室五个单位,与质量体系运行有关的单位必须依照本规程进行岗位、工艺间的操作管理。
6.炼焦车间技术操作规程
6.1焦炉概况:
TJL—80型焦炉炉体结构为双联火道、带废气、复热、下喷式。
一座焦炉有38个炭化室,39个燃烧室,40个蓄热室。
6.1.1设计参数
周转时间:
17小时(18)
炭化室干煤装煤炉量:
17.9吨/孔
年产焦炭:
100万吨
日装干煤量:
3841吨;产焦量:
2882吨;日产煤气量:
130.60万
焦仓贮焦量:
197×3吨
6.1.2焦炉的主要尺寸:
炭化室有效:
23.9m3(24.08)
炭化室长度:
14080mm
炭化室有效长度:
13380mm
炭化室高度:
4300mm
炭化室有效高度:
4000
炭化室平均宽度:
450
机侧宽度:
425
焦侧宽度:
475
炭化室锥度:
50
炭化室中心距:
1143
燃烧室立火道间距:
480
燃烧室立火道个数:
28个
机侧立火道个数:
14个
焦侧立火道个数:
14个
炭化室炉墙厚度:
100
燃烧室加热水平:
700
斜道室全高:
832
蓄热室宽度:
321.5
蓄热室主墙厚度:
300
蓄热室单墙厚度:
200
炉顶区厚度:
1178
焦炉烟囱高:
109.7米;
根部直径:
外半径5.1,内半径4.74;
顶部直径:
外半径2.4,内半径2.17;
焦炉塔高:
31米
6.1.3工艺流程
6.1.3.1生产流程:
回炉煤气加热荒煤气导出
配合煤 煤仓 装煤车 炭化室 推焦车 拦焦车
熄焦车 晾焦台 运焦皮带 贮焦仓 用户
6.1.3.2焦炉燃烧系统气体流向:
1)加热煤气流向:
回炉煤气总管 煤气预热器 煤气主管 煤气节流孔板 加减旋塞 孔板盒 支管 交换旋塞 横管 喷嘴 直立砖煤气道
火道灯头砖
2)空气流向:
废气开闭器进风口 小烟道 蓄热室(篦子砖 格子砖)斜道区 立火道底部斜道口
3)废气流向:
上升气流立火道底部(燃烧产生废气) 跨越孔 下降气流立火道(小部分由废气循环孔轴回上升气流立火道) 斜道区 小烟道 废气开闭器 分烟道 总烟道 烟囱排出
4)焦炉荒煤气流向:
循环氨水喷洒
炭化室顶空间 上升管 桥管 阀体 集气管 吸气管 气液分离器 回收车间
6.1.4质量标准
类种
水分%不大于
硫分%(S)
抗碎强度
M40(不小于)
耐磨强度
M10(不小于)
(挥发分Vr)
不大于
水分(Wa)
%
焦末含量%
不大于
一级
二级
三级
一级
二级
三级
一级
二级
三级
四级
一级
二级
三级
四级
大块焦(大于40毫米)
12.00
12.01~13.50
13.50~15.00
0.60
0.61~0.80
0.81~1.00
80.0
76.0
72.0
65.0
8.0
9.0
10.0
11.0
1.9
4.0±1.0
4.0
大中块焦(大于25毫米)
5.0±2.0
5.0
中块焦(25~40毫米)
不大于12.0
12.0
6.1.5煤气性质
焦炉煤气为无色、有味、能引起急、慢性中毒的气体。
6.1.5.1焦炉煤气组成(V%)。
名称
H2
CH4
CO
CxHn
CO2
N2
O2
低发热值
重度
着火
爆炸极限
kcal/m3
Kg/nm3
℃
%
焦炉煤气
55~60
23~27
5~8
2~4
1.5~3
3~7
<0.5
4100~
4500
0.45~0.52
600~650
5.6~30.4
高炉煤气
1.5~3.0
0.2~0.5
25~30
——
9~12
55~60
0.2~0.4
800~1000
1.29~
1.30
>700
6.1.5.2焦炉煤气特点
1)焦炉煤气低发热值:
16720---18810KJ/m3。
2)焦炉煤气发热值较高,且波动小,便于调火操作。
3)调节炉温时,增减煤气流量后,炉温变化快,一般2-3小时炉温就可反映出来。
4)用焦炉煤气加热时,由于其热值高,产生的废气量较少,而且废气重度也小,所以焦炉加热系统阻力小。
5)焦炉煤气含氢量大,不可燃烧成份少,燃烧速度快,火焰较短。
在焦炉加热时,会使焦饼上下温差变大,对高向调温不利。
6.1.6焦炉的等级标准
特级、一级、二级为完好焦炉:
炉体完整,无重大缺陷隐患,各种护炉铁件能起可靠保护作用,主要仪器,仪表齐全并能正常运行,安全防护装置完整可靠,已有的环保设施正常运行,同时各项指标符合下列要求:
6.1.6.1生产能力:
设计能力100万吨
炉龄(年)
特级
一级
二级
<15
>98
>95
>90
15~25
>95
>90
>85
>25
>90
>85
>80
6.1.6.2炼焦耗热量:
KJ/Kg煤(含水7%)
炉龄(年)
煤气类别
特级
一级
二级
<15
焦炉煤气
2135
2220
2505
贫煤气
2430
2515
2640
15~25
焦炉煤气
2180
2260
2345
贫煤气
2470
2555
2680
>25
焦炉煤气
2220
2305
2385
贫煤气
2515
2595
2720
6.1.7炉体状况
等级
特级/1等
一级1等或特级2等
二级/1等或一级/2等或特级/3等
二级/2等或一级/3等
二级/3等
炉体年伸长率
<0.03
<0.04
<0.05
<0.06
<0.07
炉头火道
完整,无重大剥蚀
剥蚀,曾出现个别倒塌
曾有倒塌深度不超过一、二火道
曾有倒塌,深度不超过二火道
曾有倒塌,深度不超过二火道
燃烧室
正常工作,全炉无不工作火道
正常工作,全炉不工作火道不超过0.2%
正常工作,全炉不工作火道不超过0.5%但一个燃烧室不超过2个火道
能正常工作全炉不工作火道不超过0.7%但一个燃烧室不超过4个火道
能正常工作全炉不工作火道不超过1%,但不能联成手片。
炉墙
平整,垂直裂缝每条缝宽小于5mm,无横裂缝
平整,有少量剥蚀,一处最大面积不超过0.1m2垂直裂缝不超过8mm无横裂缝
有剥蚀,最大处不超过0.25m2垂直裂缝宽不超过10mm,无横裂缝,有个别错台,个别炭化室宽度有变化,但不影响正常推焦
剥蚀最大处不超过0.5m2垂直裂缝宽不超过15mm一个墙面裂缝不超过2条,无横裂缝,有错台及炭化室宽有变化,但不影响正常推焦
剥蚀最大处不超过1m2垂直裂缝宽不超过20mm一个墙面裂缝不超过2条,无横裂缝,有错台及炭化室宽有变化,但不影响正常推焦
护炉铁件
炉柱平均曲度小于30mm横拉条平均直径不小于原件的90%个别的不小于85%,弹簧负荷符合规定保护板、炉门框无大裂缝
炉柱平均曲度小于40mm横拉条平均直径不小于原件的85%个别的不小于80%,无失效弹簧,保护板、炉门框无大裂缝
炉柱平均曲度小于50mm横拉条平均直径不小于原件的80%,无失效弹簧,保护板、炉门框无大裂缝
炉柱平均曲度小于50mm横拉条平均直径不小于原件的80%,弹簧仍超保护作用,保护板、炉门框无大裂缝
炉柱平均曲度小于50mm横拉条平均直径不小于原件的80%,弹簧仍超保护作用,保护板、炉门框无大裂缝
6.2调火工岗位操作规程:
6.2.1调火工岗位职责
1)熟悉炉体构造,加热系统流程,煤气及废气设备的性能。
2)按时完成工作计划,保证各部温度,压力达到技术指标。
3)熟悉焦炉的温度,压力制度及控制调节方法。
根据生产任务和配煤供量,执行规定的加热制度,保证焦饼在炭化室内全长,全高成熟,均匀准时成熟,并保持焦炉有较高的热工效率。
4)及时准确地计算各种数据,认真填写并保管好各项记录。
5)负责所使用的煤气,废气设备的维护,清扫加油检查调节。
6)按时提出各种备品,备件,工具材料,合理使用并保管好各种各工具及仪器,仪表。
7)掌握本岗位的特殊操作及事故处理。
6.2.2炼焦车间调火工技术规定
6.2.2.1温度制度:
1)燃烧室所有立火道任一点的温度不超过1450℃,不低于1100℃。
2)延长结焦时间,标准温度不得低于1100℃,炉火温度不低于950℃。
3)各炉头火道温度与全炉平均温度差小于±50℃,不低于1100℃。
4)蓄热室温度不超过1320℃,不低于900℃。
5)焦饼中心温度1000±50℃(上部不低于950℃,上下两点差不超100℃)。
6)炉顶空间温度为800±30℃,不超过850℃(结焦2/3周期时测定)。
7)小烟道温度不超过450℃,不低于250℃
8)分烟道温度不超过400℃
9)回炉煤气温度50±2℃
10)直行温度的稳定性用K安(安定系数)来考核,K安≥0.95。
11)直行温度的均匀性用K均(昼夜平均温度均匀系数)来考核,K均≥0.95。
12)横墙温度的均匀性用K横(横墙均匀系数)来考核,K横≥0.95。
13)炉头温度的均匀性用K炉头(炉头均匀系数)来考核,K炉头≥0.95。
6.2.2.2压力制度
1)燃烧室立火道看火孔压力保持5—10pa
2)集气管的煤气压力应保证吸气管下部,炭化室底部压力在结焦末期不小于5pa。
3)除边部蓄热室外,每个蓄热室顶部吸力与标准蓄热室吸力相比读数差:
上升气流为±2pa(边道±4pa),下降气流为±3pa(边道±5pa)。
4)用焦炉煤气加热时,总管压力不低于1500pa,主管不低于700pa。
5)空气过剩系数加热时应控制在1.2—1.5范围内。
6)炼焦相当耗热量不超过2220—2400Kj/Kg范围。
6.2.2.3测量操作规程
1)测量各种温度压力时设备正常,加热制度保持不变。
2)测量时不得将煤粉或杂物掉入立火道内,每次打盖不准超过五个。
3)火道测量在下降气流时进行,测量点在鼻梁砖与灯头砖之间。
4)直行温度应在相邻两个交换内测完,计算平均值,记录上帐,并注明测量仪表的校正值、测量时间、日期、加热制度和测量人。
5)下大雨时不准测量。
6.2.3一般操作
6.2.3.1直行温度的测量:
计算K均(直行均匀系数)和K实(直行温度稳定性)
1)换向后10分种开始测量,机侧测量第7火道,焦测测量第22火道;
2)从焦侧交换机端燃烧室开始测量,由机侧返回,两个交换测完,测温速度要均匀。
3)每隔4小时测量一次,每次测量结果按不同时间温度分段,加上冷却温度校正值,换算为换向20秒的温度并分别计算出机、焦测全炉平均温度以及温度系数,认真准确及时抄写在台账上。
4)
将一昼夜所测的各燃烧室机、焦侧的温度分别计算平均值,求出与机、焦昼夜平均温度的差,其差值大于20℃以上的为不合格火道,边炉差值大于30℃以上的为不合格火道。
式中:
M——焦炉燃烧室数
A机、A焦——机、焦侧不合格火道数
式中:
N——昼夜全炉温度次数
A机、A焦——机焦侧平均温度与标准温度差±7℃以上的次数
5)个别燃烧室火道温度出现超过1450℃时应加滤光片重复测量一次。
6)在加热制度不变的情况下,一一燃烧室温度两次测量相差±30℃以上,同侧温度平均相差±10℃以上应检查原因,进行处理,原因不明应重测或抽测。
7)对高低温度应分析原因,结合横排温度情况进行处理。
8)因故无法测温,等恢复后立即抽测,并记录清楚,缺测需由班长同意,签字。
9)接班抽测直行温度,并经常检查标准火道燃烧情况,发现问题及时处理。
6.2.3.2横排温度的测量
1)每天测温度调节10排,交换后5分钟开始测量,单号燃烧室由机侧开始,双号燃烧室由焦测开始,从第3至26立火道温度逐渐上升。
2)每次测量时间不应超过13分钟,两个交换内测完。
3)将所测数绘出每个燃烧室和10排平均及全炉平均横排曲线并计算出温度导数,曲线上两个标准火道之间的两侧温度差50℃斜率引一直线为标准线。
每个燃烧室实侧火道温度曲线与标准线±20℃以上为不合格,10排横超过±10℃以上为不合格,全炉横排以±7℃为不合格。
4)对不合格的应分析原因,并进行处理,若需要更换烧嘴,在下降气流进行。
5)经常检查各立火道的斜道吸煤气出口无堵塞,及时发现及时处理,横排温度均匀系数K横下式计算:
6.2.3.3炉头温度测量
1)交换5分钟开始测量,每次从交换机端燃烧室焦侧开始,由机侧返回,两个交换侧完。
2)将测量数值分别计算出机焦侧炉头火道的平均温度,计算炉头温度均匀系数K炉头,测量温度与同侧平均温度差超过±50℃以上为不合格。
3)发现温度过高或过低炉头火道要分析原因,及时处理。
6.2.3.4蓄热室顶部温度测量:
1)交换后立即测量上升气流蓄热室。
2)测量由交换机端蓄热室开始,每个交换测机侧或焦侧的单号或双号蓄热室,便将四个交换测完全炉。
3)测完要及时把测温孔盖好,做好记录,算出机、焦两侧的平均温度指出蓄热室最高最低温度,记录上账,当接近温度极限时,应增加测温次数。
4)测温时发现个别过高,过低有串漏下火等现象应检查原因及时处理。
6.2.3.5小烟道温度的测量:
1)小烟道温度检查蓄热室的热交换情况是否良好,并能发现炉体不严密造成的漏火、下火情况。
2)将缠好的石棉绳的玻璃温度计插入下降气流废气盘测孔内250——300MM深处,全炉必须一致,交换前10分钟按插入顺序开始迅速准确读出温度值。
3)为了减少误差,读数时不应拔出石棉绳,只拔出温度计。
4)测完计算每侧平均温度并上帐,小烟道温度不超过450℃,最低不超过250℃,分烟道不超过400℃,发现高低温,下火吸力不好等现象要检查分析原因及时处理。
6.2.3.6炉顶空间温度的测量
1)选取结焦时间和炉温都正常的炭化室,在其结焦周期2/3时,换上带眼炉盖,用长1.3米,温度不低于1000℃的热电偶垂直插入装煤孔至顶空间位置,15分钟后用毫伏计测量。
2)如需要考察整个结焦时间的空间温度变化,可在装煤后立即插入热电偶,直至测到出焦前半小时为止,每次测完后应将热电偶拔出。
6.2.3.7焦饼中心温度的测量
1)选择炉温和结焦时间正常的炉室。
2)准备好测焦饼中心温度管,带眼炉盖和管帽,测点位置在管内2.3米、3.5米、4.9米处。
3)装完煤后,将管分别插入带孔炉盖盖好管帽,插下焦饼中心温度管,使其贴着炉盖,用黄泥封好炉盖。
4)装煤后2小时,结焦中期和推焦前半小时测量两边燃烧室横排温度。
5)推焦前4小时开始测量,每半小时测量一次,推焦前30分钟测量最后一次。
测量各焦饼中心管距炭化室600㎜,1900㎜和3200㎜上、中、下三点温度。
6)测完焦饼后,推焦前半小时关闭翻板,拉开上升管盖,然后拔出焦饼中心温度管,垂直放好备用。
7)在出焦时应观察焦饼的成熟情况,并负责取焦样送化验室做焦质分析,并将原料配比,装煤比,煤质水分,焦质分析结果,焦饼温度、煤线、焦线等数据按规定记录填写。
焦饼中心温度计算公式:
T中心=(T机上+T机中+T机下+T焦上+T焦中+T焦下)/6
8)焦炭推出后,测炭化室墙面温度,测量点上部是火道跨越口处,测量顺序是从上到下测两面炉墙,上、中、下三点要成一条直线,测点应避开有石墨的地方。
9)测量结束后,对本测量结果进行分析,做出结论,并记录上帐,以指示加热制度的指定或修订。
6.2.3.8冷却温度的测量
1)在焦炉正常操作和加热制度稳定的情况下,选择9个相邻的燃烧室,分别在机焦侧,在标准火道下降气流进行测量。
2)整个测量过程中禁止改变煤气加热量,烟道吸力,进风口开度以及提前火延长推焦等现象。
3)看火孔只许在测量时打开,每次测量后立即盖严,一个人测一个火道温度,机焦侧全部测完不能超过2个交换。
4)换向后一分钟测第二次,以后每隔一分钟测一次,直到下次交换前3分钟为止。
5)将测量数据分别算出9个燃烧室机焦侧换向后每分钟的平均温度和换向后20秒的平均温度,并算出与20秒的温度之差值。
然后画出冷却曲线,确定新的直行温度校正值。
6)当结焦时间改变1小时以上,并时间较长时,当配煤比变化比较大以及加热制度有较大变化时,要随时重新测量冷却温度,焦饼中心温度和炉顶空间温度等。
6.2.3.9W曲线的测量
1)装煤后第一个交换开始测量炭化室两侧的燃烧室一排的机侧标准火道和另一排焦侧标准火道,交换后10分钟开测。
2)根据测量温度和测量时间,绘出W曲线。
3)由曲线分析炉体传热和结焦情况。
6.2.3.10蓄热室顶部吸力测量与调节:
1)选择炉体状况较好,对全炉有充分代表性的做标准蓄热室,一般要求具备以下条件:
a)相应的燃烧系统阻力正常,吸力稳定。
b)横排温度曲线较好,空气过剩系数正常。
c)蓄热室无漏火、下火现象。
d)尽可能位于中部区。
e)与标准蓄热室有关的炭化室不要处于装煤后初期或推焦前期。
2)测量过程中,加热制度应保持稳定不变。
尽可能在检修期间测调吸力,炉顶看火孔盖,装煤口盖,上开管盖应关闭。
3)检查并测量记录,全炉各蓄热室的废气翻板开度,进风口开度,铊杆提起高度,并注意检查蓄热封墙和废气盘两叉口严密情况。
4)按仪表规程验好斜型型压计,吹气检查测压管是否畅通,是否严密。
5)将微压计负端标准蓄热室的测压管,正端接其它蓄热室测压管。
6)交换后5分钟开始测量,逐个接通各被测蓄热室的测压管,插管接头四周应严密,胶管不能折叠。
7)微压计标出数即各蓄热室与标准蓄热室的压力差,当仪表液柱低于零点表示被测量的吸力大于标准蓄热室,仪表上液柱高于零点则相反。
8)上升气流吸力以符合炉温加热正常为准则,机焦侧蓄热室顶部及力与标准蓄热室顶部吸力比较,上升气流不得超过±2pa下降气流不得超过±3pa达不到要求分析原因处理,并将测量结果记录完好。
9)全炉吸力测量后,参照温度变化和火焰燃烧,过剩空气系数等情况进行调节,调节时应考虑上升和下降之间相邻蓄热室之间的吸力的相应关系。
10)开、关废气翻板调节蓄热室顶部下降气流吸力,调节废气盘进风口尺寸,调整上升气流蓄热室顶部吸力。
6.2.3.11蓄热室阻力测量
1)将检验好的微压计正端与蓄热室相连,负端与人烟道测压孔相连,两管垂直于气流方向同时插入。
2)交换后5分钟从交换机端开始测上升,下降时每个蓄热室的小烟道与蓄热室顶部之间在的压力差P,该压力差即为蓄热室阻力,边疆四个交换测完。
3)测完做好记录。
6.2.3.12燃烧系统五点压力测量:
1)按规3台微压计检验准确,并用三通管互相校正,应没有误差或找出差值,并准备好连接管和插入管。
2)将两个标准蓄热室机焦侧分别进行,但该炭化室应处结焦中期。
3)将两台微压计的正端管分别插入两个标准的蓄热室顶部,炉顶微压计正确插入该两蓄热室同一系统燃烧室同侧的标准测温火道内。
4)将微压计调好后分别接好各测压管,设专人联系,在换向后5分钟,同时五点开始测量,测上升气流蓄热室与下降气流蓄热室吸力差,测量完毕,换算出各点压力,绘制成五点压力曲线图,并记录当时的加热制度,注明时间、人员等。
6.2.3.13看火孔压力的测量:
1)校验好微压剂,准备Dg15mm长150mm下端带盖的铁管以及胶管。
2)选择加热制度正常,在不出炉或检修时进行测量。
3)将胶管一端与铁管连好,另一端与斜型压力计的负端相连,检查各接头和胶管严密不漏,交换后五分钟将交换测完全炉,测完后做好记录。
6.2.3.14炭化室底部压力测量:
1)事前检查吸力气管正下方的炭化室炉门下部,有无测压孔,何时出焦,并校验好压力表。
2)装煤后将Dg15mm长900mm头部末端用石棉绳堵严的铁管插入炭化室内,插入深度为700mm。
3)出焦前2小时测量每隔半小时测一次(共测四次),最后一次为推焦前半个小时,测时派专人看管,不许打开上升管盖,并检查高压氨水是否半严。
4)将测压用铁条钎子透通,直至黄烟外冒,然