车门内护板的设计.docx
《车门内护板的设计.docx》由会员分享,可在线阅读,更多相关《车门内护板的设计.docx(50页珍藏版)》请在冰豆网上搜索。
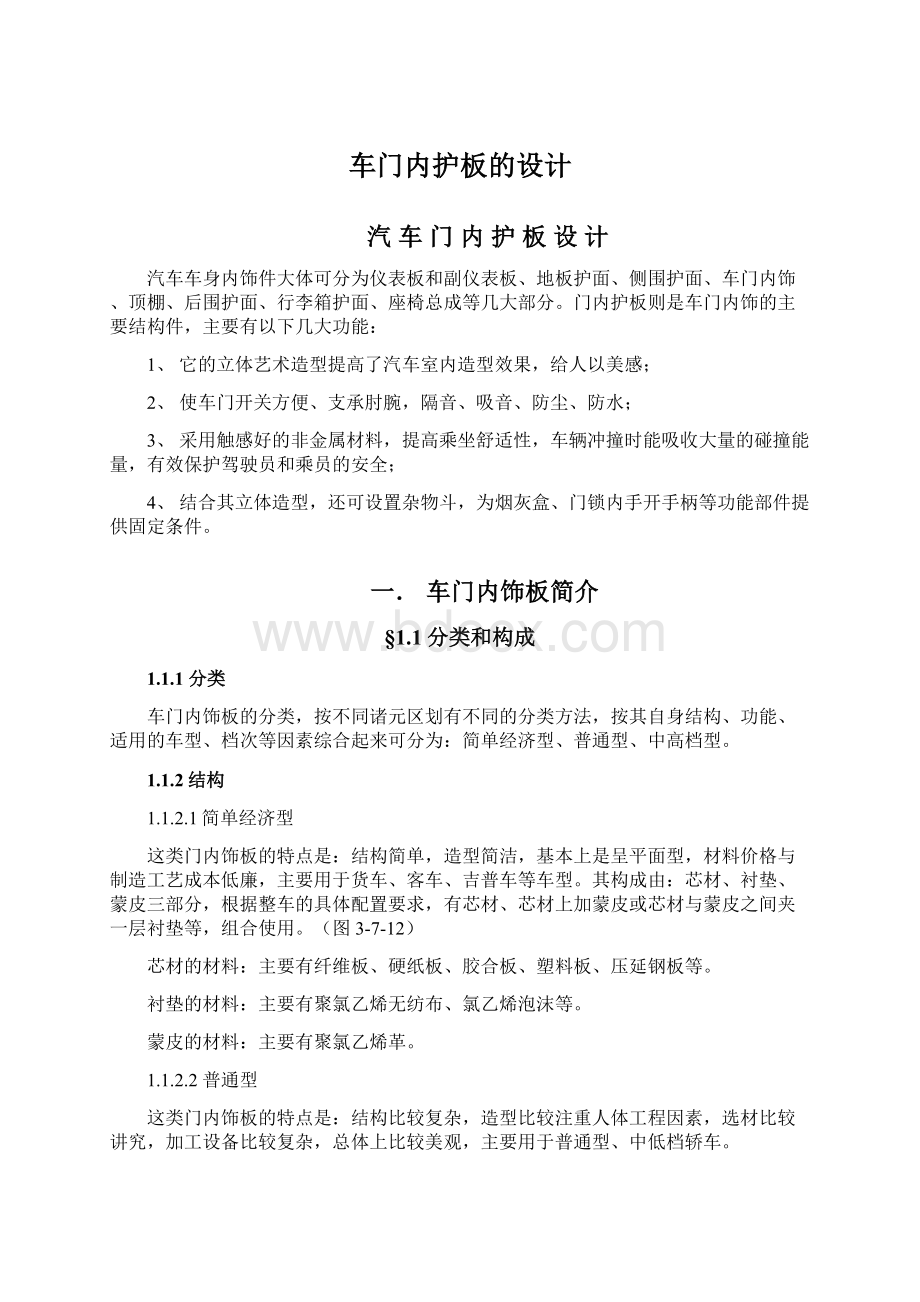
车门内护板的设计
汽车门内护板设计
汽车车身内饰件大体可分为仪表板和副仪表板、地板护面、侧围护面、车门内饰、顶棚、后围护面、行李箱护面、座椅总成等几大部分。
门内护板则是车门内饰的主要结构件,主要有以下几大功能:
1、它的立体艺术造型提高了汽车室内造型效果,给人以美感;
2、使车门开关方便、支承肘腕,隔音、吸音、防尘、防水;
3、采用触感好的非金属材料,提高乘坐舒适性,车辆冲撞时能吸收大量的碰撞能量,有效保护驾驶员和乘员的安全;
4、结合其立体造型,还可设置杂物斗,为烟灰盒、门锁内手开手柄等功能部件提供固定条件。
一.车门内饰板简介
§1.1分类和构成
1.1.1分类
车门内饰板的分类,按不同诸元区划有不同的分类方法,按其自身结构、功能、适用的车型、档次等因素综合起来可分为:
简单经济型、普通型、中高档型。
1.1.2结构
1.1.2.1简单经济型
这类门内饰板的特点是:
结构简单,造型简洁,基本上是呈平面型,材料价格与制造工艺成本低廉,主要用于货车、客车、吉普车等车型。
其构成由:
芯材、衬垫、蒙皮三部分,根据整车的具体配置要求,有芯材、芯材上加蒙皮或芯材与蒙皮之间夹一层衬垫等,组合使用。
(图3-7-12)
芯材的材料:
主要有纤维板、硬纸板、胶合板、塑料板、压延钢板等。
衬垫的材料:
主要有聚氯乙烯无纺布、氯乙烯泡沫等。
蒙皮的材料:
主要有聚氯乙烯革。
1.1.2.2普通型
这类门内饰板的特点是:
结构比较复杂,造型比较注重人体工程因素,选材比较讲究,加工设备比较复杂,总体上比较美观,主要用于普通型、中低档轿车。
其结构主要有:
芯材、蒙皮、局部衬垫和装饰条等构成,这类车门内饰板有时下部还设有防护板,以提高饰板使用寿命和方便清洁
芯材的材料:
主要有注塑件、聚丙烯加填充料板材等。
蒙皮的材料:
主要有织物、聚氯乙烯针泡革。
衬垫的材料:
主要有海绵、较厚的聚氯乙烯无纺布、半硬质聚氨酯主要用于搁手部委。
饰条的材料:
主要有聚氯乙烯、ABS、热融薄膜构成的复合材料。
1.1.2.3中高档型
这类车门内饰板的特点是:
结构复杂,造型与配置上充分考虑到舒适、安全、人体工程等因素,功能齐全,选材讲究,加工设备与制造工艺复杂,总体上美观中呈豪华。
其结构主要由芯材、蒙皮、软化件单体、隔音垫、防撞吸振块、指示照明灯等构成(图3-7-14)。
芯材的材料:
主要有注塑件等。
蒙皮的材料:
主要有带有较厚泡沫层的聚氯乙烯针泡革、真皮等。
在一些乘员经常触摸的部位一般均覆盖有软触漆。
隔音垫材料:
主要有再生棉毡、泡沫、泡沫橡胶等。
防撞吸振材料:
主要有PU聚氨酯发泡、PP聚丙烯发泡。
指示照明灯罩材料:
主要有PC聚碳酸酯、丙乙酸酯等。
软化体单件:
由芯材、衬垫和蒙皮组成的小构件,主要置于门内饰板相对乘员人体手臂与肩等部位接触处。
图3-7-13普通型门内饰板
§1.2决定车门内饰技术状态的诸因素
车辆的类型与档次及所满足的功能。
与乘员人体工程学相关的安全性、舒适性、操作性。
如尽量减少车内宽度、搁手作用、软化要求及门锁内扳手、玻璃升降机摇手柄、车门内拉手等操作的方便性。
能承受必要的最低限度的外力和重力。
有良好的工艺性、生产率、拆装方便,以便维修。
总体上与车厢内饰及整车外部协调。
在选材上应考虑到:
重量小、便于加工,具有高频加热性能;安全性、外形美观、手感好;隔音、防水、阻燃、隔热等性能。
§1.3与车门内饰板相关的零部件
操作件:
车门内扳手、玻璃升降机摇手柄(或电动升降按钮)、门锁
附件:
搁手(简单经济型车门内饰板有单独的搁手,普通型与中高档型车门内饰板搁手往往由车门内饰板本体自身造型构成)、地图袋或杂物箱(盒)、烟灰盒、扬声器、照明灯、指示灯或安全气囊等。
这些零部件的配置随车辆类型与档次不同而不同。
§1.4、几种车门内护板
二.车门内饰板的设计流程
Stylingdesign
Engineering&packagingdesign
Modeling&makeengineeringdrawing
1.市场调查、客户需求研究
2.设计风格定位
3.造型方案初始效果图
4.最终完善效果图
5.TAPEDRAWING
11.假人布置
12.人体工程学研究
13.内护板结构布置(5个主断面)
15.产品零件造型
输出信息
一、
三.车门内饰板设计流程介绍
a)在此阶段,分析需要设计的车型的市场定位及所有竞争车型的情况,同时了解客户对设计的总体要求,并且分解到具体零件的设计要求上。
b)车身内饰的整体设计风格可以有运动型、家庭型、舒适型、豪华型、亲和型等等,根据拟用的整体风格来考虑和决定门内饰板上的特征,力求与其它内饰件达到造型上的和谐统一。
c)通常设计师要绘制很多张设计效果图,通过评审,提炼后完5张效果图提供给客户选择。
d)在参考了客户的选择之后,完成一到两张能够达到照片效果的效果图。
需要应用一些电脑软件来完成。
e)用粘贴胶带在1:
1的图纸上绘制门内饰板的外形和特征,将效果图的信息转换到车身空间上。
f)在这一阶段,需要有工程设计的信息输入,完成初始曲面后可以用于加工初始油泥模型。
有了5个主断面的信息,可以决定油泥加工原料的尺寸。
g)SITTINGBUCK是根据汽车车身的尺寸,用木材、FOAMBLOCK、POLYWOOD等材料制作与车身一致的框架用于放置油泥模型。
油泥模型的制作需要很高的技巧和创造性的工作。
一般油泥完成后需要进行评审,评审时通常需求对车门内饰板进行一些装饰,如在表面裹缚表皮或喷涂油漆和皮纹,使得其外观接近实际产品。
在制作油泥模型时,需要有人体布置、人体工程学、车门内饰板布置、制造工艺、装配工艺等多方面的信息输入。
油泥模型的精度一般可达到±2mm,德国大众公司往往将模型的精度控制在1毫米,但需要时间和费用。
h)可以用多种方法扫描油泥模型,如接触式的三坐标扫描,激光扫描和高精度光学照相机拍照等,可以采集到反映油泥模型形状的数学点云。
i)高质量A表面是产品具有高质量外观和配合的基础。
对CLASSASURFACE的要求不同主机厂有不同的要求,不同的CAD软件能够达到不同的精度。
ALLIAS和ICEAMSUF是主要的CAD软件,相比较ICEAMSUF更专业一些。
CLASSA曲面质量可以用CAD软件的高光、反射线、高斯曲率等工具检查曲面是否有波纹,面片之间是否有缝隙和是否曲率连续。
CLASSA曲面的精度要达到0.01毫米,相切的面片的角度偏差不超过1.4分(0.02度)。
通常也可以将所有面片连成一个SKIN,然后偏一个厚度,生成一个壳体,如果能够成功,说明曲面的缝隙和连续性是可以接受的。
在这个阶段必须注意的是,CLASSA曲面必须完全按照结构设计提供的断面,并且完成所有可见面上的园角和第一个翻边,定义所有的间隙大小,这样可以保证工程师在以后的造型中完全按照造型师的设计。
j)在CLASSA曲面发布之前,一般需要用数控加工一个模型,与油泥模型比较。
只是因为在做CLASSA表面时,往往都根据扫描点云作一些微调,需要在发布前再作一次检查。
k)人体布置是根据SAE或ISO标准的要求,确定假人在车中的位置。
包括H点、眼椭圆、脚踪点、肩膀宽度等信息,为人机工程研究提供参数。
l)对车门内护板的进行人机工程研究
m)5个主断面,即方案的设计
n)这个阶段是设计的关键阶段,将在后文详细介绍一些设计规则和要点。
完成结构设计可以说车门内饰板的设计的80%已经完成,它包括所有零部件的工作方式,安装方式,空间布置等,可以输出给外表面造型。
o)零件造型是根据结构设计图纸和已发布的外表面,建立产品的三维数学模型。
在造型的过程中,可能发现一些结构设计的错误、或发现更好的设计结构。
p)产品工程图纸的作用随着CAD技术的提高而不断的减弱,工程图纸上可以只包括一些技术信息、关键装配尺寸公差信息、GD&T信息,所有的产品尺寸可以在3维模型上得到。
现在有些软件甚至可以在3维模型上标注GD&T信息。
这些信息主要是为了检验产品,制作产品检具提出要求。
四.结构规范
车门内饰板一般是塑料件,其结构复杂
凸台,加强筋,卡角,预埋件,螺纹,花纹,标记等复杂塑料结构在车门护板上都有体现,并且它们的设计都很有技巧性,因此我们总结了一些关于复杂塑料结构的设计的技巧和注意事项
§4.1脱模斜度
脱模斜度是为了便于产品从模具中脱出而设置的。
具体数值视成品形状、成形材料的类别、模具结构、表面精度以及加工方法等会有所不同。
在不影响产品品质的前提下﹐脱模斜度愈大愈好。
4.1.1箱体与盖类(图1-1)
当H≤50mm时,S/H=1/30~1/50;
当50<H≤100mm时,S/H≤1/60;
4.1.2格子板形(图1-2)
当格子的间距P≤4mm时,脱模斜度α=1/10P。
格子C尺寸越大,脱模斜度越大。
图1-2格子板形制品
当格子高度H超过8mm,脱模斜度不能取太大值时,可采用图(b)的形式,使一部分进入动模一侧,从而使脱模斜度满足要求。
4.1.3加强筋(图1-3)
A=(1.0~1.8)Tmm;B=(0.5~0.7)Tmm
4.1.4凸台(图1-4、表1-1)
表1-1凸台尺寸(用于3mm自攻螺纹)
图1-4凸台类制品
高凸台制品(H>30mm)的脱模斜度:
型芯:
型腔:
型芯的脱模斜度应大于型腔。
4.1.5最小脱模斜度(表1-3)
脱模斜度影响制品的脱出情况。
如果脱模斜度很小,脱模阻力增大,顶出机构就会失去作用。
在一般情况下,不能小于最小脱模斜度,以防止制品留模。
表1-2最小脱模斜度
项目
最小脱模斜度(º)
项目
最小脱模斜度(º)
一般情况
特殊情况
一般情况
特殊情况
一般情况
3
2
格子、孔
5
4
脱模斜度不能太大时
1/2
1/4
皮革纹
6
4
突出部位肋
5
4
§4.2产品外形及肉厚
产品外形尽量采用流线外形﹐避免突然的变化﹐以免在成形时因塑料在此处流动不顺引起气泡等缺陷;并且此处模具易产生磨损。
基本原则——均匀壁厚。
即:
充模、冷却收缩均匀,形状性好,尺寸精度高,生产率高。
1.在连接固紧处、嵌件埋入处和塑料熔体在孔窗的汇合(熔接痕)处,要具有足够的厚度。
2.制品上相邻壁厚差的关系(薄壁:
厚壁)为:
热固性塑料:
压制1:
3,挤塑1:
5;
热塑性塑料:
注塑1:
1.5
(2)
3.当无法避免不均匀的壁厚时,制品壁厚设计可采用逐步过渡的形式(图1-10,图1-11),或者改制成两个制品然后再装配为一个制品(图1-12)等方法。
制品壁厚的设计可参照表1-4~表1-9。
表1-4塑料制品的最小壁厚及常用壁厚推荐值
表1-5热固性塑料模塑制品壁厚尺寸
表1-6各种成型树脂的成型条件与壁厚
表1-7壁厚T与流程L关系公式mm
表1-8制品厚度设计
§4.3加强筋,凸台,圆角
4.3.1加强筋
图1-13制品肋的合理设计
(1)用高度较低、数量稍多的筋代替高度较高的单一加强筋,避免厚筋底冷却收缩时产生表面凹陷(图1-13)。
当筋的背面出现凹陷影响美观时,可采用图1-14所示的装饰结构予以遮掩。
(2).肋根部厚度T’约为(0.5~0.7)T
肋间间距>4T;肋高L<3T
PC,PPO
T’<0.6T
PMMA,ABS
T’<0.5T
PA,PE
T’<0.5T
PS
T’<0.6T
(3)筋的布置方向最好与熔料的充填方向一致(见表1-9中示例)。
(4)筋的根部用圆弧过渡,以避免外力作用时产生应力集中而破坏。
但根部圆角半径过大则会出现凹陷。
(5)一般不在筋上安置任何零件。
图1-16防止制品变形、增加刚性的结构设计
(6)加强筋在防止制品变形、增加制品刚性方面的应用如图1-16所示。
图1-15制品的内壁凸台
a)良b)不良
表1-9加强筋设计注意事项
(7)加强筋设计注意的问题参见表1-9。
4.3.2凸台
1.BOSS的长度一般不超过本身直径的两倍﹐否则必须加加强肋。
(长度太长时会引起气孔﹐烧焦﹐充填不足等)
2.BOSS的位置不能太接近转角或侧壁,如图1-15最后一组凸台。
3.BOSS的形状以圆形为主﹐设计在底部时取3个(其它形状则加工不易﹐且流动性也不好)。
4.BOSS周围可用除去部分肉厚来防收缩下陷,如图1-16。
5.考虑壁厚的均匀时,可以巧妙利用凸台来达到减厚目的。
4.3.3圆角
制品的两相交平面之间尽可能以圆弧过渡,避免因锐角而造成应力集中等弊病(参见图1-17~图1-20)。
制品圆角的作用有:
(1)分散载荷,增强及充分发挥制品的机械强度。
(2)改善塑料熔体的流动性,便于充满与脱模,消除壁部转折处的凹陷等缺陷。
图1-17
(3)便于模具的机械加工和热处理,从而提高模具的使用寿命。
§4.4孔的设计
4.4.1孔的模塑成型
图1-21
1、盲孔成型(型芯一端固定,参见图
1-21、图1-22)。
图中,D——孔径、L——孔深
注射、传递模塑D≤1.5mm,L=D;D>1.5mm,L=(2~4)D
压缩模塑L=(2~2.5)D。
图1-23
图1-24
2、通孔的成型
(图1-23~图1-26)。
3、复杂型孔的成型(图1-27)
4、孔的成型尺寸参数(表1-10~表1-12)
4.4.2孔的设计要点
(1)孔与孔的中心距应大于孔径(两者中的小孔)的2倍,孔中心至边缘的距离为孔径的3倍。
热塑性和热固性塑料制品的孔心距、孔边距还可参见图1-28和表1-13。
(2)制品壁上的孔(即孔轴线与开模方向相垂直),为避免侧向抽芯,可用图1-29中的侧壁凹槽代替。
但图中的m-n面的加工难度加大。
(3)塑料熔体围绕型芯流动汇合而形成塑料制品孔时,会在孔的边缘熔体汇合处形成熔接痕(图1-30),熔接痕的存在削弱了制品的强度。
解决的措施有:
1)孔与孔之间应适当加大距离,以避免熔接痕的重合连接(图1-30)。
2)型孔按盲孔设计,留有1/3壁厚的连皮,以便让熔体从型芯头上越过,使之不出现熔体汇合的熔接痕。
最后钻(冲)掉孔的连皮(图1-31)。
3)热塑性塑料和层压酚醛塑料的薄壁孔形件(如散热器窗),可用冲裁模冲压出型孔。
(4)需要钻孔的制品,模塑孔时应做出钻头的定位或导向部分的形状(图1-32和图1-33)。
(5)自攻螺纹孔、沉头螺钉孔的锥面孔,为防止孔表面破裂,锥面始端距表面应不小于0.5mm(图1-34)。
表1-14
(6).表1-14中列出了常见孔的设计注意事项。
(7)孔周边的肉厚宜加强(尤其针对有装配性、受力的孔),切开的孔周边也宜加强。
如图1-35。
§4.5塑料制品螺纹设计要点
(1)为使螺纹牙尖充填饱满、便于脱模以及在使用中有较好的旋合性,模塑螺纹的螺距应≥0.75mm,螺纹配合长度≤12mm,超过时宜采用机械加工。
(2)塑料螺纹与金属螺纹,或与异种塑料螺纹相配合时,螺牙会因收缩不均互相干涉,产生附加应力而影响联接性能。
解决的办法有:
限制螺纹的配合长度,其值小于或等于1.5倍螺纹直径。
增大螺纹中径上的配合间隙,其值视螺纹直径而异,一般增大的量为0.1~0.4mm。
(3)塑料螺纹的第一圈易碰坏或脱扣,应设置螺纹的退刀尺寸(参见图1-36、图1-37和表1-l5)。
(4)为了便于脱模,螺纹的前后端都应有一段无螺纹的圆柱面(图1-38、图1-39),其长度为h1和h2,前端直径d小于螺纹小径,后端直径D大于螺纹的大径。
图1-40为此种结构的应用举例。
图1-39
图1-40
图1-41
(5)同一制品上前后两段螺纹的螺距应相等,旋向相同,目的是便于脱模(见图1-41a)。
若不相同,其中一段螺纹则应采用组合型芯成型(图1-41b)。
(6)塑料制品瓶口螺纹的结构及尺寸见表1-16~表1-19。
图1-42和
表1-16
表1-17
表1-18
图1-43为软质塑料所用的锯齿形螺纹。
§4.6塑料制品中的嵌件
塑料成型过程中所埋入的或成型后压入的螺栓、接线柱等金属或其它材质零件,统称为塑料制品中的嵌件。
嵌件可增加制品的功能或对制品进行装饰。
嵌件的模塑使操作变繁,周期加长,生产率降低(带有自动装夹嵌件的机械手或自动线不在此列)。
4.6.1嵌件的结构形式
1、常见的金属嵌件(图1-42)
2.嵌件可以根据需要自行设计,设计应遵循一些准则。
3、嵌件材料
铜、铝、钢、硬质异种塑件、陶瓷、玻璃等都可作为嵌件材料,其中,黄铜不生锈、耐腐蚀、易加工且价格适中,是嵌件的常用材料。
4.6.2嵌件在塑料制品中的固定
(1)为避免制品底部过薄出现波纹形缩痕而影响外观及强度,应取嵌件底面距制品壁面的最小距离T>D/6(图1-43)。
(2)嵌件与制品侧壁的间距不能过小,以保证模具有一定的强度(图1-44)。
(3)凸台中设置嵌件时,为保证嵌件结合稳定以及塑料基体的强度,嵌件应伸人到凸台的底部(需保证最小底厚),嵌件头部作成圆角(图1-45)。
(4)小型圆柱形嵌件可用中间开槽或表面菱形滚花结构植于塑料基体之中(图1-46),滚花槽深1~2mm。
(5)板、片状嵌件可用孔窗固定法固定,但薄形嵌件(厚度小于0.5mm)宜用切口或打弯的方法固定(图1-47)。
图1-48
(6)杆形嵌件可用将头部打扁、冲缺、压弯、劈叉等形式固定(图1-48),也可用将圆杆的中间部分压扁的方法固定(图1-49)。
(7)管形冲压嵌件,可在冲压时加工出膨凸部分,用以增强紧固力(图1-50)。
4.6.3嵌件周围塑料的裂纹和联接强度
1、裂纹产生的原因
(1)塑料收缩的内应力和自然老化(图1-51)。
图1-52
(2)嵌件的结构和安放位置不合理(图1-52)。
4.6.4装配式嵌件(制品模塑后再装入嵌件)
1、饭金加工(装配)法,如铆接(图1-53)、折弯(图1-54)。
2、用工具将嵌件压入或旋入制品中(图1-55、图1-56)。
3、热插法。
热固性塑料制品出模时,在热态下将嵌件插入,冷却后即牢固地结合在一起(图1-57)。
塑料收缩量应在其弹性范围内,否则塑料会裂开。
4、其它装配方法。
①粘结:
热固性塑料用环氧树脂粘结,热塑性塑料用溶剂类粘结剂粘结。
②超声波装配:
热塑性塑料软化后压人。
§4.7塑料制品的凸凹纹(滚花)
图1-58塑料制品的凹凸纹
a)不正确,不能垂直顶出;b)正确;c)最常用的滚花侧面(S=(4~6)R1,h=3/4R1
1、凸凹纹的作用:
(1)增大接触面积,防止使用中的滑动。
(2)装饰或掩盖制品的某些部位。
(3)增加装配时的结合牢固性。
2、凸凹纹的设计要点:
(1)凸凹纹的条纹方向应与脱模方向一致,便于脱模(图1-58a、b)。
(2)条纹的间距应尽可能大些,便于模具制造及制品脱模,一般为3mm,最小不小于1.5mm,参见图1-58c中的S值。
凸凹纹的宽度(图中的R1)不应小于0.3~0.5mm,高度(h)不应超过其宽度(h=3/4R1)。
(3)凸凹纹截面形状多为半圆形,少数采用平顶的梯形(图1-59)。
(4)为了不削弱模具分型面的强度,以及便于修整制品飞边,设计凸凹纹时需要留出图1-60所示的0.8mm宽的平直部分。
表1-21
(5)表1-21和表1-22是凸凹纹各部设计的推荐尺寸,供参考。
表1-22
§4.8标记、符号
塑料制品上的文字或符号的表现形式有:
(1)制品上为凸字(模具上为凹字)。
便于用机械加工的方法加工模具,制模方便。
但制品的凸字易碰坏
(2)制品上为凹字(模具上为凸字)。
采用电火花、电铸、冷挤压等方法加工模具,制模费事。
但制品上的凹字不易碰坏,还可在凹字内涂色((3)文字、符号处单独做成镶块,便于更换。
透明制品上有凹入的文字时,塑料熔体流经模具上相应的凸出文字后会产生影响制品外观的熔接痕。
消除措施是控制文字的深度,即
字深:
制品壁厚=1:
3
五.装配规范
§5.1咬接
a.材料
咬接设计取决于使用的材料容许的变形。
举个例子,由于聚酰胺在干燥状态下比常规状态下能容许的变形更低,有必要加倍注意这种材料的应用,玻璃纤维含量对材料的所允许变形也有很大的影响,因此对倒钩允许的倾斜度也有影响
b.t的高度应该小于ymax
c.为防应力集中R应大于T一般为1.2T左右
§5.2螺纹连接
a.三种形式(锣栓式,预埋件式,自攻式)
b.需注意的一些东西
§5.3粘接
粘合剂可用来连接相同原料聚合物的塑料制件,一般用来边接由不同材料制造的制件。
使热固性塑料制件相互连接,或使塑料制件与金属连接。
粘合剂的
a.优点
●美观、设计灵活;
●均匀的应力分布;
●能够连接不同的材料;
●能够提供大气\水\气体的严密封口;
●柔软粘合剂能缓冲振动;
●能与薄而软的基材一起使用;
●提供电绝缘和热绝缘性。
b.粘合剂的各种局限性
⏹接头性能不定性;
⏹永久组装;
⏹综合化学过程;
⏹需要干净表面;
⏹没有接头检测;
⏹达到最大强度的时间。
C.粘合剂选择
特定应用的粘合剂的选择取决的因素包括:
使用环境、应力值、基材表面化学、基材刚性特性、基材热膨胀系数、填缝要求和应用方法。
d.溶剂粘接
溶剂粘接是可以组装某些热塑性制件的方法,最常用于无定形热塑性塑料制件上。
溶剂粘接是形成坚固的无定形热塑性制件密封组装的简单的、相对便宜的方法。
溶剂的低黏度要求被粘接制件应该是不弯曲的且用相对紧的公差模制。
§5.4焊接
通常认为热塑性焊接是不可逆的.少数工艺如感應焊接可生産可逆組裝件.至於選擇哪種方法應在製件沒計初作出,因爲焊接方法對製件設計的要求可能是重要的,且不同焊接方法同差別顯蓍.
1.超聲焊接
2.振動焊接
3.旋轉焊接
4.熱板焊接
5.感應焊接
6.接觸(電阻)焊
7.熱氣焊接
8.擠出焊接
熱氣焊接技術通常用來焊接塑膠管,片或半成品製品而不是注塑成型製件.但許多熱塑性模塑製件,特別是熱塑性汽車盤是用熱氣焊接技術修復的,另外熱氣焊接有時用來製備塑膠樣模製件.
只讲