一切削力的来源.docx
《一切削力的来源.docx》由会员分享,可在线阅读,更多相关《一切削力的来源.docx(29页珍藏版)》请在冰豆网上搜索。
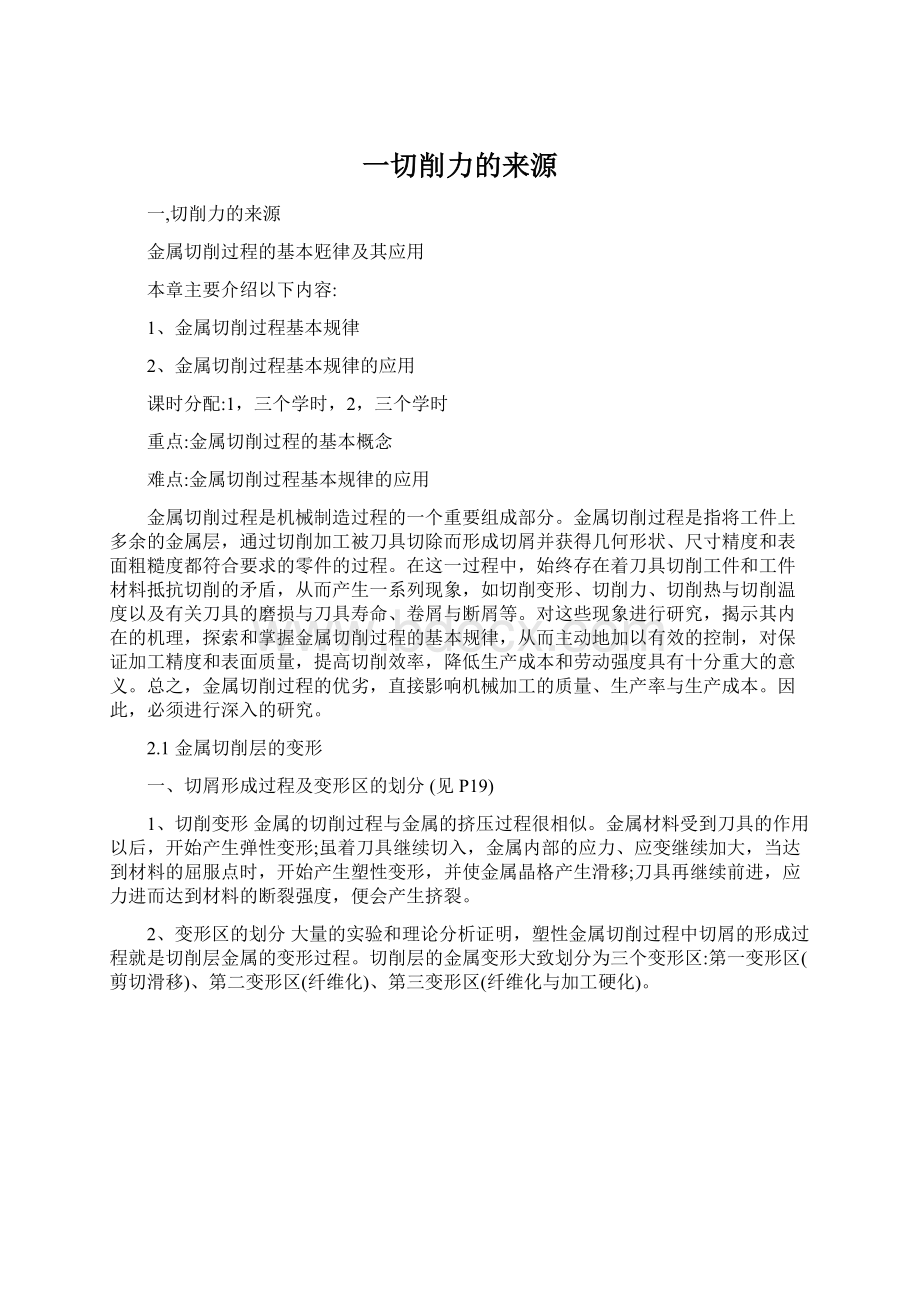
一切削力的来源
一,切削力的来源
金属切削过程的基本觃律及其应用
本章主要介绍以下内容:
1、金属切削过程基本规律
2、金属切削过程基本规律的应用
课时分配:
1,三个学时,2,三个学时
重点:
金属切削过程的基本概念
难点:
金属切削过程基本规律的应用
金属切削过程是机械制造过程的一个重要组成部分。
金属切削过程是指将工件上多余的金属层,通过切削加工被刀具切除而形成切屑并获得几何形状、尺寸精度和表面粗糙度都符合要求的零件的过程。
在这一过程中,始终存在着刀具切削工件和工件材料抵抗切削的矛盾,从而产生一系列现象,如切削变形、切削力、切削热与切削温度以及有关刀具的磨损与刀具寿命、卷屑与断屑等。
对这些现象进行研究,揭示其内在的机理,探索和掌握金属切削过程的基本规律,从而主动地加以有效的控制,对保证加工精度和表面质量,提高切削效率,降低生产成本和劳动强度具有十分重大的意义。
总之,金属切削过程的优劣,直接影响机械加工的质量、生产率与生产成本。
因此,必须进行深入的研究。
2.1金属切削层的变形
一、切屑形成过程及变形区的划分(见P19)
1、切削变形金属的切削过程与金属的挤压过程很相似。
金属材料受到刀具的作用以后,开始产生弹性变形;虽着刀具继续切入,金属内部的应力、应变继续加大,当达到材料的屈服点时,开始产生塑性变形,并使金属晶格产生滑移;刀具再继续前进,应力进而达到材料的断裂强度,便会产生挤裂。
2、变形区的划分大量的实验和理论分析证明,塑性金属切削过程中切屑的形成过程就是切削层金属的变形过程。
切削层的金属变形大致划分为三个变形区:
第一变形区(剪切滑移)、第二变形区(纤维化)、第三变形区(纤维化与加工硬化)。
3、切屑的形成及变形特点(见P20)
1)第一变形区(近切削刃处切削层内产生的塑性变形区)金属的剪切滑移变形
切削层受刀具的作用,经过第一变形区的塑性变形后形成切屑。
切削层受刀具前刀面与切削刃的挤压作用,使近切削刃处的金属先产生弹性变形,继而塑性变形,并同时使金属晶格产生滑移。
在下图中,切削层上各点移动至AC线均开始滑移、离开AE线终止滑移,在沿切削宽度范围内,称AC是始滑移面,AE是终滑移面。
AC、AE之间为第—变形区。
由于切屑形成时应变速度很快、时间极短,故AC、AE面相距很近,一般约为0.02一0.2mm,所以常用AB滑移面来表示第—变形区,AB面亦称为剪切面。
剪切面AB与切削速度Vc之间的夹角称为剪切角。
作用力Fr与切削速度Vc之间的,
夹角ω称为作用角。
第一变形区就是形成切屑的变形区,其变形特点是切削层产生剪切滑移变形。
2)第二变形区(与前刀面接触的切屑层产生的变形区)内金属的挤压磨擦变形
经过第一变形区后,形成的切屑要沿前刀面方向排出,还必须克服刀具前刀面对切屑挤压而产生的摩擦力。
此时将产生挤压摩擦变形。
应该指出,第一变形区与第二变形区是相互关联的。
前刀面上的摩擦力大时,切屑排出不顺,挤压变形加剧,以致第一变形区的剪切滑移变形增大。
3)第三变形区(近切削刃处已加工表面内产生的变形区)金属的挤压磨擦变形
已加工表面受到切削刃钝圆部分和后刀面的挤压摩擦,造成纤维化和加工硬化。
二、切削变形程度的度量方法
1、相对滑移ε
相对滑移ε是用来量度第1变形区滑移变形的程度。
如右图,设切削层中A'B'线沿剪
切面滑移至A"B"时的距离为?
y,事实上?
y很小,故可认为滑移是在剪切面上进行,其滑移量为?
s。
则相对滑移ε表示为:
1、变形系数?
h
变形系数?
h是表示切屑的外形尺寸变化大小的一个参数。
如右图所示,切屑经过剪切变形、又受到前刀面摩擦后,与切削层比较,它的长度缩短、厚度增加,这种切屑外形尺寸变化的变形现象称为切屑的收缩。
变形系数?
h表示切屑收缩的程度,即
从上图可知,剪切角变化对切屑收缩的影响,增大剪切面AB减短,切屑厚度hch,,
减小,故?
h变小。
它们之间的关系如下:
从上面两个公式可知,剪切角与前角γ是影响切削变形的两个主要因素。
如果增大,0
前角γ和剪切角,使相对滑移ε、变形系数?
h减小,则切削变形减小。
0
注意:
由于切削过程是一个非常复杂的物理过程,切削变形除了产生滑移变形外,还有挤压、摩擦等作用,而ε值主要从剪切变形考虑;而?
h主要从塑性压缩方面分析。
所以,ε与?
h都只能近似地表示切削变形程度。
三、剪切角的确定
剪切角是影响切削变形的一个重要因素。
若能预测剪切角的值,则对了解与控制,,
切削变形具有重要意义。
为此,许多学者进行了大量研究,并推荐了若干剪切角的计算式。
其中,按最少能量原则来确定剪切
角的计算式为:
按最大剪应力的理论,求出剪切角
计算式为:
从上面公式可看出:
与γ、β有关。
增大前角γ、减小摩擦角β,使剪切角增大,,,00
切削变形减小,这一规律已被普遍用于生产实践中。
从上面公式也可看出:
第2变形区产生的摩擦对第1变形区剪切变形的影响规律。
四、积屑瘤的形成及其对切削过程的影响(见P24)
在切削速度不高而又能形成连续切屑的情况下,加工一般钢料或其它塑性材料时,常常在前刀面处粘着一块剖面有时呈三角状的硬块。
这块冷焊在前刀面上的金属称为积屑瘤(或刀瘤)。
它的硬度很高,通常是工件材料的2—3倍,在处于比较稳定的状态时,能够代替刀刃进行切削。
1、积屑瘤是如何形成的?
1)切屑对前刀面接触处的摩擦,使前刀面十分洁净。
2)当两者的接触面达到一定温度同时压力又较高时,会产生粘结现象,即一般所谓的“冷焊”。
切屑从粘在刀面的底层上流过,形成“内摩擦”。
3)如果温度与压力适当,底层上面的金属因内摩擦而变形,也会发生加工硬化,而被阻滞在底层,粘成一体。
4)这样粘结层就逐步长大,直到该处的温度与压力不足以造成粘附为止。
2、形成积屑瘤的条件:
主要决定于切削温度。
此外,接触面间的压力、粗糙程度、粘结强度等因素都与形成积屑瘤的条件有关。
1)一般说来,塑性材料的加工硬化倾向愈强,愈易产生积屑瘤;
2)温度与压力太低,不会产生积屑瘤;反之,温度太高,产生弱化作用,也不会产生积屑瘤。
3)走刀量保持一定时,积屑瘤高度与切削速度有密切关系。
3、积屑瘤对切削过程的影响
1)实际前角增大
它加大了刀具的实际前角,可使切削力减小,对切削过程起积极的作用。
积屑瘤愈高,实际前角愈大。
2)使加工表面粗糙度增大
积屑瘤的底部则相对稳定一些,其顶部很不稳定,容易破裂,一部分连附于切屑底部而排出,一部分残留在加工表面上,积屑瘤凸出刀刃部分使加工表面切得非常粗糙,因此在精加工时必须设法避免或减小积屑瘤。
3)对刀具寿命的影响
积屑瘤粘附在前刀面上,在相对稳定时,可代替刀刃切削,有减少刀具磨损、提高寿命的作用。
但在积屑瘤比较不稳定的情况下使用硬质合金刀具时,积屑瘤的破裂有可能使硬质合金刀具颗粒剥落,反而使磨损加剧。
4、防止积屑瘤的主要方法
1)降低切削速度,使温度较低,粘结现象不易发生;
2)采用高速切削,使切削温度高于积屑瘤消失的相应温度;
3)采用润滑性能好的切削液,减小摩擦;
4)增加刀具前角,以减小切屑与前刀面接触区的压力;
5)适当提高工件材料硬度,减小加工硬化倾向。
五、切削变形变化规律
从相对滑移ε、变形系数?
h计算式中可知,剪切角与前角γ是影响切削变形的两,0
个主要因素。
如果增大前角γ和剪切角,使相对滑移ε、变形系数?
h减小,则切削变,0
形减小。
1、前角:
增大前角γ,使剪切角增大,变形系数?
h减小,因此,切削变形减小。
0
生产实践表明:
采用大前角刀具切削,刀刃锋利、切入金属容易,切屑与前刀面接触长度减短、流屑阻力小,因此,切削变形小、切削省力。
2、切削速度:
切削速度Vc是通过积屑瘤使剪切角改变和通过切削温度使摩擦系数μ变,
化而影响切削变形的。
3、进给量:
进给量f增大,使变形系数?
h减小。
4、工件材料:
工件材料硬度、强度提高,切削变形减少。
2.2切屑的类型及控制
一、切屑的类型及其分类(见P20)
由于工件材料不同,切削过程中的变形程度也就不同,因而产生的切屑种类也就多种多样,如下图示。
图中从左至右前三者为切削塑性材料的切屑,最后一种为切削脆性材料的切
屑。
切屑的类型是由应力-应变特性和塑性变形程度决定的。
1、带状切屑
它的内表面光滑,外表面毛茸。
加工塑性金属材料(如碳素钢、合金钢、铜和铝
合金),当切削厚度较小、切削速度较高、刀具前角较大时,一般常得到这类切屑。
它的切削过程平衡,切削力波动较小,已加工表面粗糙度较小。
2、挤裂切屑
这类切屑与带状切屑不同之处在外表面呈锯齿形,内表面有时有裂纹。
这种切屑大多在切削黄铜或切削速度较低、切削厚度较大、刀具前角较小时产生。
2、单元切屑
如果在挤裂切屑的剪切面上,裂纹扩展到整个面上,则整个单元被切离,成为梯形的单元切屑,如图c所示。
切削铅或用很低的速度切削钢时可得到这类切屑。
以上三种切屑只有在加工塑性材料时才可能得到。
其中,带状切屑的切削过程最平稳,单元切屑的切削力波动最大。
在生产中最常见的是带状切屑,有时得到挤裂切屑,单元切屑则很少见。
假如改变挤裂切屑的条件,如进一步减小刀具前角,减低切削速度,或加大切削厚度,就可以得到单元切屑。
反之,则可以得到带状切屑。
这说明切屑的形态是可以随切削条件而转化的。
掌握了它的变化规律,就可以控制切屑的变形、形态和尺寸,以达到卷屑和断屑的目的。
如果在挤裂切屑的剪切面上,裂纹扩展到整个面上,则整个单元被切离,成为梯形的单元切屑,如图c所示。
切削铅或用很低的速度切削钢时可得到这类切屑。
以上三种切屑只有在加工塑性材料时才可能得到。
其中,带状切屑的切削过程最平稳,单元切屑的切削力波动最大。
在生产中最常见的是带状切屑,有时得到挤裂切屑,单元切屑则很少见。
假如改变挤裂切屑的条件,如进一步减小刀具前角,减低切削速度,或加大切削厚度,就可以得到单元切屑。
反之,则可以得到带状切屑。
这说明切屑的形态是可以随切削条件而转化的。
掌握了它的变化规律,就可以控制切屑的变形、形态和尺寸,以达到卷屑和断屑的目的。
4.崩碎切屑
这是属于脆性材料(如铸铁、黄铜等)的切屑。
这种切屑的形状是不规则的,加工表面是凸凹不平的。
从切削过程来看,切屑在破裂前变形很小,和塑性材料的切屑形成机理也不同。
它的脆断主要是由于材料所受应力超过了它的抗拉极限。
加工脆硬材料,如高硅铸铁、白口铁等,特别是当切削厚度较大时常得到这种切屑。
由于它的切削过程很不平稳,容易破坏刀具,也有损于机床,已加工表面又粗糙,因此在生产中应力求避免。
其方法是减小切削厚度,使切屑成针状或片状;同时适当提高切削速度,以增加工件材料的塑性。
以上是四种典型的切屑,但加工现场获得的切屑,其形状是多种多样的。
二、切屑控制的措施
在现行切削加工中,切削速度与金属切除率达到了很高的水平,切削条件很恶劣,常常产生大量“不可接受”的切屑。
所谓切屑控制(又称切屑处理,工厂中一般简称为“断屑”),是指在切削加工中采取适当的措施来控制切屑的卷曲、流出与折断,使形成“可接受”的良好屑形。
在实际加工中,应用最广的切屑控制方法就是在前刀面上磨制出断屑槽或使用压块式断屑器。
2.3切削力
一、切削力的来源,切削合力及其分解,切削功率(见P26)
(一)切削力的来源
研究切削力,对进一步弄清切削机理,对计算功率消耗,对刀具、机床、夹具的设计,对制定合理的切削用量,优化刀具几何参数等,都具有非常重要的意义。
金属切削时,刀具切入工件,使被加工材料发生变形并成为切屑所需的力,称为切削力。
切削力来源于三个方面:
1(克服被加工材料对弹性变形的抗力;
2(克服被加工材料对塑性变形的抗力;
3(克服切屑对前刀面的摩擦力和刀具后刀面对过渡表面与已加工表面之间的摩擦力。
(二)切削合力及其分解
上述各力的总和形成作用在刀具上的合力Fr(国标为F)。
为了实际应用,Fr可分解为相互垂直的Fx(国标为Ff)、Fy(国标为Fp)和Fz(国标为Fc)三个分力。
在车削时:
Fz——主切削力或切向力。
它切于过渡表面并与基面垂直。
Fz是计算车刀强度,设计机床零件,确定机床功率所必需的。
Fx——进给抗力、轴向力或走刀力。
它是处于基面内并与工件轴线平行与走刀方向相反的力。
Fx是设计进给(走刀)机构,计算车刀进给功率所必需的。
Fy——切深抗力、或背向力、径向力、吃刀力。
它是处于基面内并与工件轴线垂直的力。
Fy用来确定与工件加工精度有关的工件挠度(详见第七章),计算机床零件和车刀强度。
它与工件在切削过程中产生的振动有关。
(三)切削功率(见P29)
1、单位切削力
单位切削力p是指切除单位切削层面积所产生的主切削力,可用下式表示:
单位切削力p可查手册,利用单位切削力P来计算主切削力Fz较为简易直观。
2、切削功率Pm
消耗在切削过程中的功率称为切削功率Pm(国标为Po)。
切削功率为力Fz和Fx所消耗的功率之和,因Fy方向没有位移,所以不消耗功率。
于是
Pm=(Fz*Vc+Fx*nw*f/1000)×10-3
其中:
Pm—切削功率(KW);
Fz—切削力(N);
Vc—切削速度(m/s);
Fx—进给力(N);
nw—工件转速(r/s);
f—进给量(mm/s)。
式中等号右侧的第二项是消耗在进给运动中的功率,它相对于F所消耗的功率来说,一般很小(<1%,2%),可以略去不计,于是
-3Pm=FzV×10
按上式求得切削功率后,如要计算机床电动机的功率(PE)以便选择机床电动机时,还应考虑到机床传动效率。
PE?
Pm/,m
式中:
m—机床的传动效率,一般取为0.75,0.85,大值适用于新机床,小值适用于旧机床。
3、单位切削功率
单位切削功率Ps是指单位时间内切除单位体积金属Zw所消耗的功率。
二、切削力的测定
在生产实际中,切削力的大小一般采用由实验结果建立起来的经验公式计算。
在需要较为准确地知道某种切削条件下的切削力时,还需进行实际测量。
随着测试手段的现代化,切削力的测量方法有了很大的发展,在很多场合下已经能很精确地测量切削力。
切削力的测量成了研究切削力的行之有效的手段。
目前采用的切削力测量手段主要有:
1(测定机床功率,计算切削力
用功率表测出机床电机在切削过程中所消耗的功率PE后,可按下式计算出切削功率Pm
Pm=Pe,m
在切削速度Vc为已知的情况下,利用Pm即可求出切削力F。
这种方法只能粗略估算切削力的大小,不够精确。
当要求精确知道切削力的大小时,通常采用测力仪直接测量。
2(用测力仪测量切削力(见P27)
测力仪的测量原理是利用切削力作用在测力仪的弹性元件上所产生的变形,或作用在压电晶体上产生的电荷经过转换后,读出Fz、Fx、Fy的值。
在自动化生产中,还可利用测力传感装置产生的信号优化和监控切削过程。
按测力仪的工作原理可以分为机械、液压和电气测力仪。
目前常用的是电阻应变片式测力仪。
三、切削力的经验公式和切削力估算(见P28)
目前,人们已经积累了大量的切削力实验数据,对于一般加工方法,如车削、孔加工和铣削等已建立起了可直接利用的经验公式。
测力实验的方法有单因素法和多因素法,通常采用单因素法。
即固定其它实验条件,在切削时分别改变背吃刀量ap和进给量f,并从测力仪上读出对应切削力数值,然后经过数据整理求出它们之间的函数关系式。
通过切削力实验建立的车削力实验公式,其一般形式为:
注意:
切削力实验公式是在特定的实验条件下求出来的。
在计算切削力时,如果切削条
件与实验条件不符,需乘一个修正系数KF,它是包括了许多因素的修正系数乘积。
修正系数也是用实验方法求出。
四、切削力的变化规律(见P30)
实践证明,切削力的影响因素很多,主要有工件材料、切削用量、刀具几何参数、刀具材料刀具磨损状态和切削液等。
1、工件材料
(1)硬度或强度提高,剪切屈服强度ηs增大,切削力增大。
(2)塑性或韧性提高,切屑不易折断,切屑与前刀面摩擦增大,切削力增大。
2、切削用量
(1)背吃刀量(切削深度)ap、进给量增大,切削层面积增大,变形抗力和摩擦力增大,切削力增大。
由于背吃刀量ap对切削力的影响比进给量对切削力的影响大(通常XFz=1,YFz=0.75-0.9),所以在实践中,当需切除一定量的金属层时,为了提高生产率,采用大进给切削比大切深切削较省力又省功率。
(2)切削速度vc(见P31图2.20)
1)加工塑性金属时,切削速度Vc对切削力的影响规律如同对切削变形影响一样,它们都是通过积屑瘤与摩擦的作用造成的。
(以车削45钢为例,见下图)
2)切削脆性金属时,因为变形和摩擦均较小,故切削速度Vc改变时切削力变化不大。
3、刀具几何角度(见P32)
(1)前角:
前角增大,变形减小,切削力减小。
(2)主偏角:
主偏角Kr在300-600范围内增大,由切削厚度hD的影响起主要作用,使主切削力Fz减小;主偏角Kr在600-900范围内增大,刀尖处圆弧和副前角的影响更为突出,
故主切削力Fz增大。
一般地,Kr=600-750,所以主偏角Kr增大,主切削力Fz增大。
(见P33图2.22)
Kr增大,使Fy减小、Fx增大。
实践应用,在车削轴类零件,尤其是细长轴,为了减小切深抗力Fy的作用,往往采用较大的主偏角κr>600的车刀切削。
(3)刃倾角λs:
λs对Fz影响较小,但对Fx、Fy影响较大。
λs由正向负转变,则Fx减小、Fy增大。
实践应用,从切削力观点分析,切削时不宜选用过大的负刃倾角λs。
特别是在工艺系统刚度较差的情况下,往往因负刃倾角λs增大了切深抗力Fy的作用而产生振动。
4、其它因素(见P34)
(1)刀具棱面:
应选较小宽度,使Fy减小。
(2)刀具圆弧半径:
增大,切削变形、摩擦增大,切削力增大。
(3)刀具磨损:
后刀面磨损增大,刀具变钝,与工件挤压、摩擦增大,切削力增大。
2.4切削热和切削温度
切削热与切削温度是切削过程中产生的又一重要物理现象。
切削时做的功,可转化为等量的热。
功削热除少量散逸在周围介质中外,其余均传入刀具、切屑和工件中,并使它们温度升高,引起工件变形、加速刀具磨损。
因此,研究切削热与切削温度具有重要的实用意义。
一、切削热的产生和传导(见P35)
切削热是由切削功转变而来的。
如下图所示,其中包括:
剪切区变形功形成的热Q、P切屑与前刀面摩擦功形成的热Q、已加工表面与后刀面摩擦功形成的热Q,因此,切削时rfαf共有三个发热区域,即剪切面、切屑与前刀面接触区、后刀面与已加工表面接触区,如图示,三个发热区与三个变形区相对应。
所以,切削热的来源就是切屑变形功和前、后刀面的摩擦功。
产生总的切削热Q,分别传入切屑Qch、刀具Qc、工件Qw和周围介质Qr。
切削热的形成及传导关系为:
切削塑性金属时切削热主要由剪切区变形热和前刀面摩擦热形成;切削脆性金属时则后刀面摩擦热占的比例较多。
二、切削温度的计算与测量(见P36)
尽管切削热是切削温度上升的根源,但直接影响切削过程的却是切削温度,切削温度一般指切削区域的平均温度θ。
通过切削区域产生的变形功、摩擦功和热传导,可以近似推算出切削温区值。
切削温度是由切削时消耗总功形成的热量引起的。
单位时间内产生的热q等于消耗的切削功率Pm,即
切削温度的测量方法很多,见下图。
?
自然热电偶法自然热电偶法主要是用于测定切削区域的平均温度。
?
人工热电偶法人工热电偶法是用于测量刀具、切屑和工件上指定点的温度,用它可求得温度分布场和最高温度的位置。
三、影响切削温度的主要因素(见P37)
根据理论分析和大量的实验研究知,切削温度主要受切削用量、刀具几何参数、工件材料、刀具磨损和切削液的影响,以下对这几个主要因素加以分析。
分析各因素对切削温度的影响,主要应从这些因素对单位时间内产生的热量和传出的热量的影响入手。
如果产生的热量大于传出的热量,则这些因素将使切削温度增高;某些因素使传出的热量增大,则这些因素将使切削温度降低。
1、切削用量的影响
切削用量是影响切削温度的主要因素。
通过测温实验可以找出切削用量对切削温度的影响规律。
通常在车床上利用测温装置求出切削用量对切削温度的影响关系,并可整理成下列一般公式:
切削速度对切削温度影响最大,随切削速度的提高,切削温度迅速上升。
进给量对切削温度影响次之,而背吃力量ap变化时,散热面积和产生的热量亦作相应变化,故ap对切削温度的影响很小。
2、刀具几何参数的影响
切削温度θ随前角γo的增大而降低。
这是因为前角增大时,单位切削力下降,使产生的切削热减少的缘故。
但前角大于18?
20?
后,对切削温度的影响减小,这是因为楔角变小而使散热体积减小的缘故。
(见P37图2.28)
主偏角Κr减小时,使切削宽度hD增大,切削厚度hD减小,因此,切削变形和摩擦增大,切削温度升高。
但当切削宽度hD增大后,散热条件改善。
由于散热起主要作用,故随着主偏角kr减少,切削温度下降。
负倒棱b在(0—2)f范围内变化,刀尖圆弧半径r在0—1.5mm范围内变化,基本上γ1e
不影响切削温度。
因为负倒棱宽度及刀尖圆弧半径的增大,会使塑性变形区的塑性变形增大,但另一方面这两者都能使刀具的散热条件有所改善,传出的热量也有所增加,两者趋于平衡,所以对切削温度影响很小。
3、工件材料的影响
工件材料的强度(包括硬度)和导热系数对切削温度的影响是很大的。
由理论分析知,单位切削力是影响切削温度的重要因素,而工件材料的强度(包括硬度)直接决定了单位切削力,所以工件材料强度(包括硬度)增大时,产生的切削热增多,切削温度升高。
工件材料的导热系数则直接影响切削热的导出。
4、刀具磨损的影响
在后刀面的磨损值达到一定数值后,对切削温度的影响增大;切削速度愈高,影响就愈显著。
合金钢的强度大,导热系数小,所以切削合金钢时刀具磨损对切削温度的影响,就比切碳素钢时大。
5、切削液的影响
切削液对切削温度的影响,与切削液的导热性能、比热、流量、浇注方式以及本身的温度有很大的关系。
从导热性能来看,油类切削液不如乳化液,乳化液不如水基切削液。
四、切削温度对工件、刀具和切削过程的影响
切削温度高是刀具磨损的主要原因,它将限制生产率的提高;切削温度还会使加工精度降低,使已加工表面产生残余应力以及其它缺陷。
(1)切削温度对工件材料强度和切削力的影响
切削时的温度虽然很高,但是切削温度对工件材料硬度及强度的影响并不很大;剪切区域的应力影响不很明显。
(2)对刀具材料的影响
适当地提高切削温度,对提高硬质合金的韧性是有利的。
(3)对工件尺寸精度的影响
(4)利用切削温度自动控制切削速度或进给量
(5)利用切削温度与切削力控制刀具磨损
2.5刀具的磨损与破损、刀具寿命及刀具状态监控
一、刀具磨损的形态及其原因
切削金属时,刀具一方面切下切屑,另一方面刀具本身也要发生损坏。
刀具损坏的形式主要有磨损和破损两类。
前者是连续的逐渐磨损,属正常磨损;后者包括脆性破损(如崩刃、碎断、剥落、裂纹破损等)和塑性破损两种,属非正常磨损。
刀具磨损后,使工件加工精度降低,表面粗糙度增大,并导致切削力加大、切削温度升高,甚至产生振