石油炼制重点.docx
《石油炼制重点.docx》由会员分享,可在线阅读,更多相关《石油炼制重点.docx(26页珍藏版)》请在冰豆网上搜索。
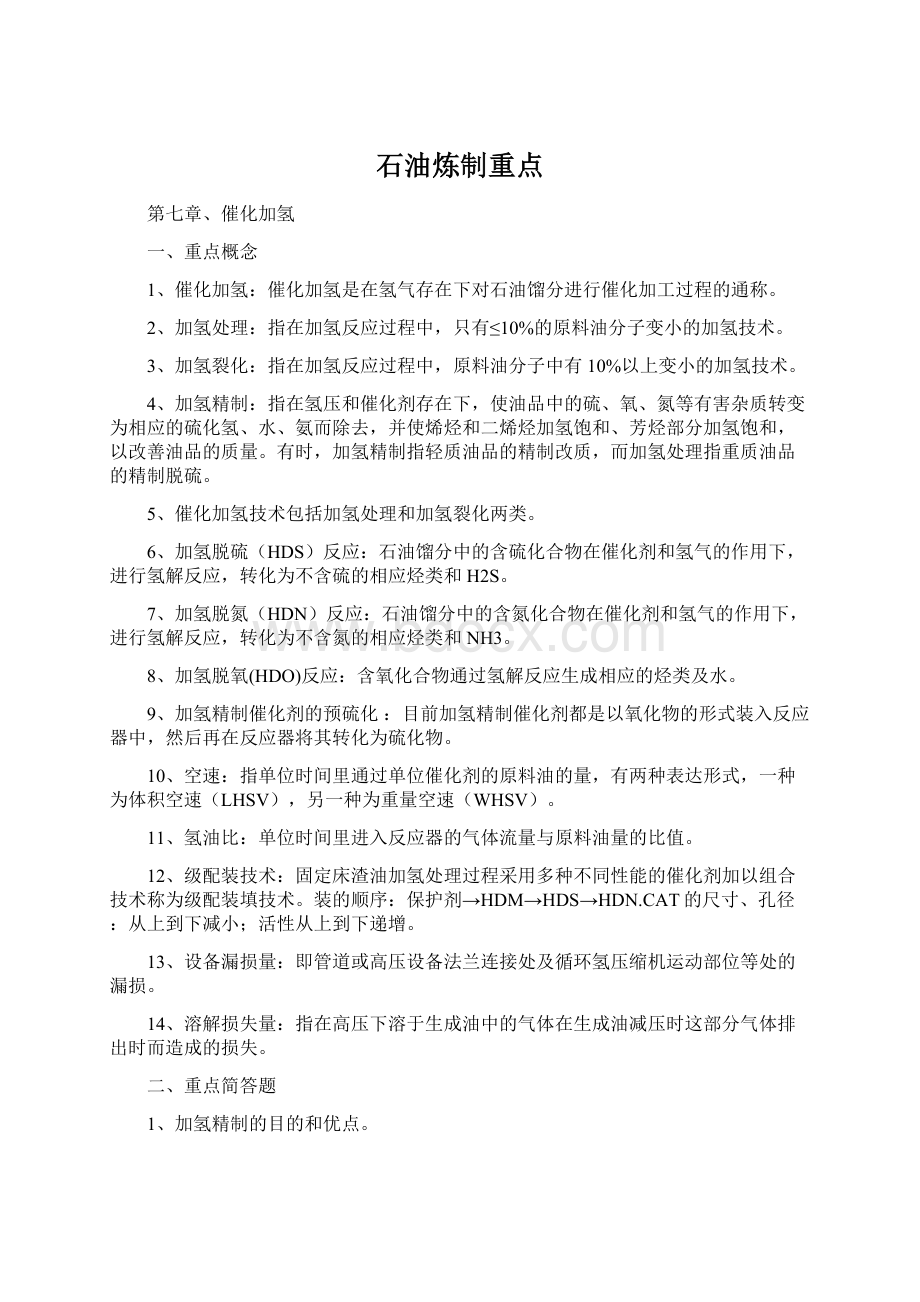
石油炼制重点
第七章、催化加氢
一、重点概念
1、催化加氢:
催化加氢是在氢气存在下对石油馏分进行催化加工过程的通称。
2、加氢处理:
指在加氢反应过程中,只有≤10%的原料油分子变小的加氢技术。
3、加氢裂化:
指在加氢反应过程中,原料油分子中有10%以上变小的加氢技术。
4、加氢精制:
指在氢压和催化剂存在下,使油品中的硫、氧、氮等有害杂质转变为相应的硫化氢、水、氨而除去,并使烯烃和二烯烃加氢饱和、芳烃部分加氢饱和,以改善油品的质量。
有时,加氢精制指轻质油品的精制改质,而加氢处理指重质油品的精制脱硫。
5、催化加氢技术包括加氢处理和加氢裂化两类。
6、加氢脱硫(HDS)反应:
石油馏分中的含硫化合物在催化剂和氢气的作用下,进行氢解反应,转化为不含硫的相应烃类和H2S。
7、加氢脱氮(HDN)反应:
石油馏分中的含氮化合物在催化剂和氢气的作用下,进行氢解反应,转化为不含氮的相应烃类和NH3。
8、加氢脱氧(HDO)反应:
含氧化合物通过氢解反应生成相应的烃类及水。
9、加氢精制催化剂的预硫化:
目前加氢精制催化剂都是以氧化物的形式装入反应器中,然后再在反应器将其转化为硫化物。
10、空速:
指单位时间里通过单位催化剂的原料油的量,有两种表达形式,一种为体积空速(LHSV),另一种为重量空速(WHSV)。
11、氢油比:
单位时间里进入反应器的气体流量与原料油量的比值。
12、级配装技术:
固定床渣油加氢处理过程采用多种不同性能的催化剂加以组合技术称为级配装填技术。
装的顺序:
保护剂→HDM→HDS→HDN.CAT的尺寸、孔径:
从上到下减小;活性从上到下递增。
13、设备漏损量:
即管道或高压设备法兰连接处及循环氢压缩机运动部位等处的漏损。
14、溶解损失量:
指在高压下溶于生成油中的气体在生成油减压时这部分气体排出时而造成的损失。
二、重点简答题
1、加氢精制的目的和优点。
答:
⑴加氢精制的目的在于脱除油品中的硫、氮、氧杂原子及金属杂质,同时还使烯烃、二烯烃、芳烃和稠环芳烃选择加氢饱和,从而改善油品的使用性能。
⑵加氢精制的优点是,原料油的范围宽,产品灵活性大,液体产品收率高(>100%(体)),产品质量好。
而且与其它产生废渣的化学精制方法相比还有利于保护环境和改善工人劳动条件。
因此无论是加工高硫原油还是加工低硫原油的炼厂,都广泛采用这种方法来改善油品的质量。
2、加氢过程的化学反应
答:
化学反应有加氢脱硫(HDS)、加氢脱氧(HDO)、加氢脱氮(HDN)、加氢脱金属(HDM)、不饱和烃的加氢饱和
其特点:
①各类硫化物加氢脱硫反应很强的放热反应,因而过高的反应温度对硫化物的加氢脱硫反应是不利的。
反应温度越高,反应的平衡转化率越低。
在相同的反应温度下,反应压力越低,平衡转化率越低,在相同的反应压力下,反应温度越高,平衡转化率越低。
在较高的温度下,压力的影响较显著,在低压下,温度下影响比较明显。
随着含硫化合物分子中环烷环和芳香环数目的增加,其加氢反应速率是降低的,这主要是由于空间位阻作用所致。
反应活性因分子结构和分子大小而异,各种硫化物在加氢精制反应的活性顺序如下:
RSH>RSSR’>RSR’>噻酚
②此类反应均是放热反应,但是有时随着反应温度的升高,总的加氢脱氮速率有一个极大值。
③含氧化合物的加氢精制条件下分解很快,但是对杂环氧化物,当有较多取代基时,反应活性较低。
3、馏分越重,加氢脱氮越困难的原因?
答:
①馏分越重,含氮量越多;②馏分越重,其氮化物的分子结构就越复杂,空间位阻效应越强,环化合物也增多。
4、随着反应温度的升高,总的加氢脱氮速率有一个极大值的原因?
答:
加氢脱氮反应包括加氢与C-N键断裂。
但氢解反应时速率控制步骤时,其反应速率数值决定于与温度有关的速率常数和饱和杂环化合物分压(其与平衡常数有关)。
当温度升高时,速率常数增加,而饱和杂环化合物加氢饱和的平衡常数降低,左右相反,故其有一个极大值。
5、加氢精制反应的反应速率大致顺序为:
答:
脱金属>二烯烃饱和>脱硫>脱氧>单烯烃饱和>脱氮>芳烃饱和
6、加氢裂化过程的化学反应:
答:
反应包括烷烃与烯烃的加氢裂化反应(C+离子原理)、环烷烃的加氢裂化反应、芳烃的加氢裂化反应。
7、加氢精制催化剂(具有加氢和裂化两种功能)的预硫化的原因?
答:
活性金属组分的氧化物并不具有加氢活性,只有以硫化物状态存在时才具有较高的活性,但是这些金属的硫化物在运输过程中容易氧化,所有催化剂要预硫化。
8、催化剂失活的原因?
答:
①重质原料中的重金属元素会沉积在催化剂上,堵塞其微孔,促使加氢精制催化剂永久性失活;
②加氢精制催化剂在运转过程中产生的积炭,积炭占有活性中心,使其暂时失活;
③水蒸气占有微孔中心,让催化剂活性降低。
9、加氢精制的影响因素?
答:
①反应压力,由于加氢是体积缩小的反应,从热力学的角度而言,提高压力对化学平衡是有利的,同时在高压下,催化剂表面的上反应物和氢气浓度都增大,其反应速度也随之加快。
②反应温度,加氢是强放热反应,所以从化学平衡的角度来看,过高的反应温度对反应是不利的,同时过高的反应温度还会由于裂化反应加剧而降低液体收率以及催化剂因积炭而过快失活。
③空速,降低空速可以使反应物与催化剂的接触时间延长、精制深度加深、有利于提高产品质量。
但是过低的空速会使反应时间过长,由于裂化反应显著而降低液体产物的收率,氢耗也会随之增大,同时对于大小一定的反应器,降低空速意味着降低其处理能力。
④氢油比,在压力、空速一定时,氢油比影响反应物与生成物的气化率、氢分压以及反应物与生成物与催化剂的接触的实际时间。
较高的氢油比使原料的气化率提高,同时也增大了氢分压,这些都有利于提高加氢反应速率。
但是从另一方面来看,氢油比增大意味着反应物分压降低和反应物与催化剂的实际接触时间缩短,这又是对加氢反应是不利的。
10、加氢裂化的影响因素
答:
①原料,加氢裂化原则上可以处理各种类型的原料,其产物组成很大程度上取决于原料的组成,一般而言,原料中环状烃越多,产物中的环状烃也就越多。
②反应压力,由于加氢裂化总体上是分子数减少的过程,因此提高反应压力对其热力学平衡是有利的,尤其是对芳烃加氢饱和的反应影响尤为显著,氢分压增大能使加氢裂化的反应速率加快、转化率提高。
③反应温度,反应温度是加氢裂化比较敏感的操作参数,由于加氢是强的放热反应,如果反应温度过高,其平衡常数和平衡转化率就很低。
同时过高的反应温度会使加氢裂化反应速度过快。
④空速,空速是控制加氢反应的重要因素,降低空速意味着增加反应时间,加氢裂化反应深度随之增加,气体产物增多,氢耗也有所增加,而装置的处理能力相应地降低。
改变空速还能改变产物的分布,提高空速时,其转化深度降低,轻质产物的收率减少,而中间馏分油的收率增加。
⑤氢油比,加氢精制由于反应热效应不大,可以采用降低的氢油比,在加氢裂化过程中,由于反应热效应较大,氢耗也较高,低分子烃类的生成量也较大,所以为了保证足够的氢分压,采用较高的氢油比。
11、阐述氢油比是如何影响加氢精制过程的?
答:
氢油比对加氢精制的影响主要有三个方面:
一是影响反应的过程;二是对加氢催化剂寿命产生影响;三是对装置操作费用及设备投资的影响。
仅就反应而言,当氢油比比较低时,产物的相对分子质量减少而使汽化率增加,再有反应热引起的床层温升,从而导致反应器出口的氢分压与入口相比有相当大的降低。
可见,氢油比的增减实际就是反应过程的氢分压增减。
氢油比对脱硫率的影响规律:
当反应温度较低而空空速较高时,脱硫率随着氢油比增加而提高,到一定的程度又有所下降;但是当反应温度较高、空速较低时,随着氢油比的增加而脱硫率没有下降的趋势。
氢油比对脱氮率的影响规律:
无论反应温度与空速的高低,其脱氮率都没有一个最高点。
总之,氢油比低,导致氢分压下降,造成脱硫率、脱氮率有所下降;氢油比过高时,反应床层中的气流速度相当,减少了催化剂床层的液体藏量,从而减少了液体反应物在催化剂床层的停留时间,以致使脱硫率、脱氮率有所降低。
另一方面,硫化氢的浓度增加,有利于提高脱硫率,流率增加使硫化氢浓度降低,也会降低脱氮率效果。
12、三种加氢工艺对比?
(1)单段加氢裂化工艺:
一个反应器,一段加氢裂化的目的是生产中间馏分,对催化剂的要求是具备较高的加氢、脱硫、脱氮活性,在一定场合也要求具备一定的异构化活性。
特点:
催化剂的裂化性能较低;中馏分选择性好且产品分布稳定;流程简单,设备投资少且操作容易;床层反应温度较高,末期气相产率较高;原料适用性差,其干点与含N量不能过高;运转周期相对较短。
优点:
流程简单,设备投资少。
(2)两段加氢裂化工艺:
两个反应器,分别装不同性能催化剂,第一个主要进行加氢精制,第二个主要进行加氢裂化。
与单段、但段串联工艺比较有以下特点:
气体产率低,液体产率高;产品质量好,芳烃含量非常低;氢耗较低;产品方案灵活;原料适应性强,可加工更重质、更劣质原料。
优点:
对原料适应性强,可加工各种原料;产品灵活性大。
(3)单段串联加氢裂化:
第一反应器装入脱硫脱氮活性好的催化剂;第二个反应器装入分子筛加氢裂化催化剂。
与单段工艺比较具有以下特点:
产品方案灵活,仅通过改变操作方式及工艺条件或者更换催化剂,可以根据市场需求对产品结构在相当大范围内进行调节;原料适用性强,可以加工更重的原料;可以在相对较短的温度操作,降低干气的产率,因而热裂化被有效抑制,可大大降低干气产率。
三种流程比较:
①一段流程航煤收率高而汽油收率低;流程结构和投资以一段流程为最优。
②串联流程生产较灵活,但航煤收率偏低。
③二段流程生产灵活性最大,航煤收率高。
④一段流程对原料要求较高;二段流程、串联流程对原料要求不高,可处理高比重、高干点、高硫、高残炭、高氮的原料油。
总之,一段加氢裂化流程较简单,航煤收率高,但汽油收率较低,操作不够灵活,只能处理较好的原料油;串联流程操作较灵活,可最大限度地生产汽油、航煤和柴油,但航煤收率偏低;两段流程操作最灵活,可处理高比重、高干点、高硫、高残炭及高氮的原料,汽油、煤油、柴油收率较高,但流程较复杂,操作费用较高。
13、加氢裂化采用不同加氢工艺的原因?
答:
工艺类型和流程的选择与原料性质、产品要求和催化剂等因素有关。
加氢裂化的原料可为轻质馏分、中间馏分、减压馏分减压渣油等,不同的原料有不同的性质,必须以其性质来选择工艺,况且一般的产品要求都不同,催化剂的要求也不同,故其要求要选择适当的工艺来生产,达到效率的最大化。
14、加氢技术快速增长的主要原因是什么?
答:
⑴随着原油变重、变差,原油中硫、钒、镍、铁等含量呈上升趋势,炼厂加工含硫原油和重质原油的比例逐年增大,不大量采用加氢技术已经无法满足生产需要。
⑵世界经济的快速发展,对轻质油品的需求持续增长,特别是中间馏分油——喷气燃料和柴油,因此需对原油进行深度加工,加氢技术是炼油厂深度加工的有效手段。
⑶环境保护的需求。
为了实现可持续发展要使用清洁燃料。
15、加氢裂化催化剂的加氢活性与酸性活性为什么要很好地配合?
答:
改变催化剂的加氢活性和酸性活性的比例关系,可改变裂化和异构化反应进行的程度,也就改变了烷烃加氢裂化的产品组成。
如果催化剂的酸性活性相对较高,则产物的异构化程度也较高,并会使二次裂化反应过于强烈,反应产物中的较小分子及不饱和烃增多,严重时还会造成生焦;如果催化剂的加氢活性相对较高,则产物的异构化程度较低,异构产物与正构产物的比值将低于催化裂化产品中的相应比值,且在加氢裂化过程中形成的烯烃会很快加氢饱和(所得产品的饱和程度较大),而来不及再进一步裂化或吸附于催化剂表面而脱氢缩合生成焦炭。
因此,加氢裂化催化剂的加氢活性与酸性活性要很好地配合。
16、氢分压对加氢过程的影响。
答:
氢分压对加氢过程的影响可以得出以下几点基本结论:
(1)氢分压与物料组成和性质、反应条件、过程氢耗和总压等因素有关;
(2)随着氢分压的提高,脱硫率、脱氮率、芳烃加氢饱和转化率也随之增加;
(3)对于VGO原料而言,在其他参数相对不变的条件下,氢分压对裂化转化深度产生正的影响;
(4)重质馏分油的加氢裂化,当转化率相同时,其产品的分布基本与压力无关;
(5)反应氢分压是影响产品质量的重要参数,特别是产品中的芳烃含量与反应氢分压有很大的关系;
(6)反应氢分压对催化剂失活速度也有很大影响,过低的压力将导致催化剂快速失活而不能长期运转;
目前工业上装置的操作压力一般在7.0MPa~20.0MPa之间。
17、为什么说氢油比的变化其实质是影响反应过程的氢分压?
答:
仅就反应而言,氢油比的变化其实质是影响反应过程的氢分压。
氢油比对氢分压的主要影响:
一是当过程的氢油比较低时,随着反应过程的氢耗的产生,反应生成物中分子量的减少而使汽化率增加;由反应热引起的床层温升,这些都导致反应器催化剂床层到反应器出口的氢分压与入口相比有相当大的降低。
二是在其他参数不变时,如果增加氢油比,则从入口到出口的氢分压的下降将显著减少。
这就是说,氢油比的增加实质上是增加了反应过程的氢分压。
18、为什么石脑油加氢精制一般都采用两段加氢精制工艺过程?
答:
石油二次热加工中的焦化石脑油馏分质量较差,一般含有20%左右的二烯烃,总烯烃含量可高达40%,同时还含有大量的硫、氮化合物,所以一般都采用两段加氢精制工艺过程。
第一段在低温下加氢,饱和易结焦的二烯烃;二段再采用较苛刻的操作条件,进行脱硫、脱氮和烯烃饱和。
焦化石脑油采用一段法是可以生产优质石脑油的。
但是由于烯烃含量高,床层温升很大,可达125℃。
如此大的温升不仅不好操作,而且会缩短催化剂使用周期。
在两段加氢精中,适当降低第一反应器入口温度,使部分烯烃饱和转移到第二反应器来进行反应,总温升合理的分配在两个反应器的床层中,既易操作,又有利于延长催化剂使用周期,因此焦化石脑油制取合格的乙烯裂解料,应采用两段加氢精制为宜。
19、与其他石油二次加工产品比较,加氢裂化产品的特点。
答;
(1)加氢裂化的液体产率高;
(2)加氢裂化的气体产率很低;
(3)加氢裂化产品的饱和度高,烯烃极少,非烃含量也很低,故产品的安定性好。
柴油的十六烷值高,胶质低;
(4)原料中多环芳烃在进行加氢裂化反应时经选择断环后,主要集中在石脑油馏分和中间馏分中,使石脑油馏分的芳烃潜含量较高,中间馏分中的环烷烃也保持较好的燃烧性能和较高的热值。
而尾油则因环状烃的减少,BMCI值降低,适合作为裂解制乙烯的原料;
(5)加氢裂化过程异构能力很强,无论加工何种原料,产品中的异构烃都较多。
(6)通过催化剂和工艺的改变可大幅度调整加氢裂化产品的产率分布。
20、为什么生产中总希望新氢纯度越高越好?
答:
如果新氢纯度低,其中必含有较多的其他组分(N2、CH4等),这些组分不能溶解于生成油中,而是有相当大部分积存在循环气中,降低了氢气纯度。
为了维持循环氢的纯度,需要释放一部分循环氢,并同时补充一部分新氢,这样就增大了新氢耗量。
所以,生产中总希望新氢纯度越高越好,因为既能降低新氢耗量,又能降低系统的总压。
加氢裂化工艺条件的总结表:
项目
加氢裂化
原料
轻质馏分、中间馏分、减压馏分、减压渣油
温度
280~420℃
催化剂
由一种ⅥB族金属和第Ⅷ族的金属组合的二元活性组分所构成。
如Co-Mo、Ni-Mo、Ni-W、Co-W等。
压力
1.5~17.5MPa
氢油比
50~1000m3/m3
空速
0.1~12h-1
气相产品
C3、C4多而C1、C2少,异构烃含量高
液相产品
石脑油:
异构烃含量高,芳烃含量少,基本无不饱和烃,非烃化合物少
中间馏分油:
优质的喷气燃料:
烯烃含量低,芳烃含量少,结晶点(冰点)低,烟点高。
优质的低硫柴油:
硫含量低(<0.01%),芳烃含量低,十六烷值高(>60),着火性能好,安定性好。
加氢裂化尾油
第八章催化重整总结
一、概念题
1、催化重整:
是以汽油为原料,在催化剂的作用和氢气存在下,生产高辛烷值汽油或苯、甲苯、二甲苯等石油化工原料的工艺过程,即是指在催化剂的作用下,烃类分子重新排列成新分子结构的工艺过程。
2、重整:
烃类分子在一定条件下发生化学反应重新排列成新的分子结构。
3、氢解反应:
含N、S、O等杂质在氢气存在条件下转化为氨气、硫化氢和水而除掉的反应。
4、芳烃潜含量:
原料中C6~C8环烷烃全部转化为芳烃再加上原料中的芳烃含量。
5、重整转化率(芳烃转化率):
重整生成油中的实际芳烃含量与原料的芳烃潜含量之比。
二、重点公式
1、芳烃潜含量%(重)=苯潜含量%(重)+甲苯潜含量%(重)+C8芳烃潜含量%(重)
2、
3、
4、
5、
三、简答题
1、重整生产目的及其构成
答:
1)生产高辛烷值汽油组分
其包括以下系统:
(1)原料预处理系统
(2)重整反应系统
(3)溶剂抽提系统(4)芳烃精馏系统
2)生产轻质芳烃(C6~C8)
其包括以下系统:
(1)原料预处理系统
(2)重整反应系统
2、催化重整的化学反应及其特点
答:
1)芳构化反应
(1)六元环烷脱氢,反应速度最快、强吸热反应、分子越大,平衡转化率越高,体积增大的反应和可逆反应;
(2)五元环烷异构脱氢,
反应速度较快、强吸热反应、体积增大的反应和可逆反应;
(3)烷烃环化脱氢,反应速度最慢,吸热反应、体积增大的反应和可逆反应。
2)异构化反应,是轻度放热的可逆反应,按正碳离子反应机理进行。
提高温度对这一反应不利,但实际上是温度高异构物产率高,这是因为温度高反应速度高。
3)加氢裂化反应,该反应包括裂化、加氢、异构化,按正碳离子反应机理进行,是中等放热的不可逆反应。
不能得到芳烃,是非理想反应;裂化使分子变小而提高辛烷值,但生成小分子烃类使汽油产率降低;反应速度较慢,提高温度和氢分压使反应速度加快
4)氢解反应----由金属中心催化
5)积炭反应(叠合和缩合)
3、为什么重整反应器采用多个串联,中间加热的形式?
答:
重整是指烃类分子重新排列成新的分子结构,而不改变分子大小的加工过程。
催化重整是指原料油中的正构烷和环构烷在催化剂存在下转化为异构烷和芳烃的过程。
其主要包括以下反应:
1芳构化反应,其为强吸热反应;②异构化反应,其为轻度放热反应;
2加氢裂化反应,其为中等放热反应,
总的而言,催化重整反应是强吸热反应。
所有的重整过程均采用固定床系列反应器:
第一反应器的主要反应是环烷脱氢,第二反应器发生C5环烷异构化生成环己烷的同系物和脱氢环化,第三反应器发生轻微的加氢裂化和脱氢环化。
经预处理后的精制油,由泵抽出与循环氢混合,然后进入换热器与反应产物换热,再经加热炉加热后进入反应器。
由于重整反应是吸热反应以及反应器又近似于绝热操作,物料经过反应以后温度降低,为了维持足够高的温度条件(通常是500℃左右),重整反应部分一般设置3~4个反应器串联操作,每个反应器之前都设有加热炉,给反应系统补充热量,从而避免温降过大。
最后一个反应器出来的物料,部分与原料换热,部分作为稳定塔底重沸器的热源,然后再经冷却后进入油气分离器。
总的来说,因为重整反应时多种反应,其各个反应对催化剂的要求要不同,且同一种反应在一个反应器也不能完成反应,故重整反应器采用多个串联;因催化重整反应总体而言是吸热反应,且去反应温度为480—530℃,为了保证目的产物的产率,故在每一个反应器的前面都设置一个加热炉,即采用中间加热的形式。
所以,重整反应器采用多个串联,中间加热的形式。
4、催化重整中的芳构化反应有哪些特点?
答:
芳构化反应一般包括六元环烷脱氢、五元环烷异构脱氢和烷烃环化脱氢。
其反应特点分别为:
反应速度最快、强吸热反应、体积增大的反应和可逆反应;反应速度较快、强吸热反应、体积增大的反应和可逆反应;反应速度最慢,吸热反应、体积增大的反应和可逆反应。
从上面几个反应可以看出,这类反应的特点是吸热、体积增大、生成苯并产生氢气、反应速度快、可逆反应,它是重整过程生成芳烃的主要反应。
5、为什么要对原料进行预处理?
包括哪些内容?
答:
重整原料的选择主要有三方面的要求,即馏分组成、族组成和毒物及杂质含量。
重整原料通常为石脑油(直馏汽油馏分)(主要原料),加氢裂化汽油,处理后的焦化汽油等。
重整原料中含有少量的砷、铅、铜、铁、硫、氮等杂质会使催化剂中毒失活。
水和氯的含量控制不当也会造成催化剂减活或者失活。
为了保证催化剂在长周期运转中具有较高的活性,必须严格控制重整原料中杂质含量,所以要对原料进行预处理。
原料预处理包括原料的预分馏,预脱砷,预加氢三部分,有时还有专门为重整原料脱水和脱硫。
其目的是得到馏分范围,杂质含量都合乎要求的重整原料。
原料预处理目的是切割符合重整要求的馏分和脱除对重整催化剂有害的杂质及水分。
预分馏的作用是切取合适沸程的重整原料。
在预分馏塔,切去<80℃或<60℃的轻馏分,同时也脱去了原料油的部分水分。
预加氢作用为脱除原料油中对催化剂有害的杂质,同时也使烯烃饱和以减少催化剂的积碳。
当原料油的含砷量较高时,则须按催化剂的容砷能力(一般为3~4%)和要求使用的时间来计算催化剂的装入量,并适当降低空速。
也可以采用在预分馏之前预先进行吸附法或化学氧化法脱砷。
6、加氢裂化中的循环氢油什么作用?
重整过程中循环氢有何作用?
答:
加氢裂化中的循环氢油的作用:
氢油比是指进入到反应器中标准状态下的氢气与冷态进料(20℃)的体积之比。
使用循环氢油有助于提高汽油比。
在一定的程度上,提高氢油比可以使原料的气化率提高,增大氢分压,这不仅有利于加氢反应,有利于减缓催化剂的积炭速度,延长操作周期,但是却增加了动力消耗和操作费用。
同时,氢油比增大意味着反应物分压降低和反应物与催化剂的实际接触时间缩短,这又是对加氢反应是不利的,所以不能超出一定的范围。
此外,循环氢起着热载体的作用,加氢过程是放热反应,大量的循环氢可以提高反应系统的热容量,从而降低因加氢反应放热引起的反应温度上升的幅度。
在加氢精制过程中,反应的热效应不大,可采用较低的氢油比;在加氢裂化过程中,热效应较大,氢耗量较大,可采用较高的氢油比。
重整过程中循环氢的作用:
重整过程中,使用循环氢是为了抑制催化剂结焦,它同时还具有热载体和稀释气的作用。
在总压不变时,重整过程用循环氢有利于提高氢油比,提高氢油比意味着提高氢分压,有利于抑制催化剂上的积炭,但会增加压缩机功耗,减小反应时间。
一般对于稳定性较好的催化剂和生焦倾向较小的原料,可采用较小的氢油比,反之则采用较大的氢油比。
简而言之,就是改善反应器内温度分布,起热载体作业;抵制生焦反应,保护催化剂活性寿命;稀释反应原料,使物料更均匀地分布于床层中。
7、催化重整的馏程是如何选择的?
答:
石脑油由原油蒸馏或石油二次加工切取相应馏分而得。
其沸点范围依需要而定,通常为较宽的馏程,如30-220℃。
不同的目的产品需要不同馏分的原料,这是重整的化学反应所决定的。
以生产目的来进行馏程选择,如用作催化重整原料生产芳烃时,芳构化反应是催化重整反应的重要反应,碳六烃的沸点在60℃—80℃,碳七的沸点在90℃—110℃,碳八的沸点在120℃—144℃,故可取60℃——145℃馏分(称轻石脑油),但在生产实际常用60~130℃馏分作原料,因为130~145℃馏分是在航空煤油的馏程范围内;用作催化重整原料生产高辛烷值汽油组分时,当碳原子数≤C6时,其本身就已有很高的辛烷值,C6环烷转化成苯或者裂解成小分子,从而减低其辛烷值和降低产率,故其原料一般去≥C6馏分,一般取80℃——180℃馏分(称重石脑油);
总之而言,催化重整的馏程是依生产目的不同与馏分的沸点来选择