粉末冶金现状及发展.docx
《粉末冶金现状及发展.docx》由会员分享,可在线阅读,更多相关《粉末冶金现状及发展.docx(8页珍藏版)》请在冰豆网上搜索。
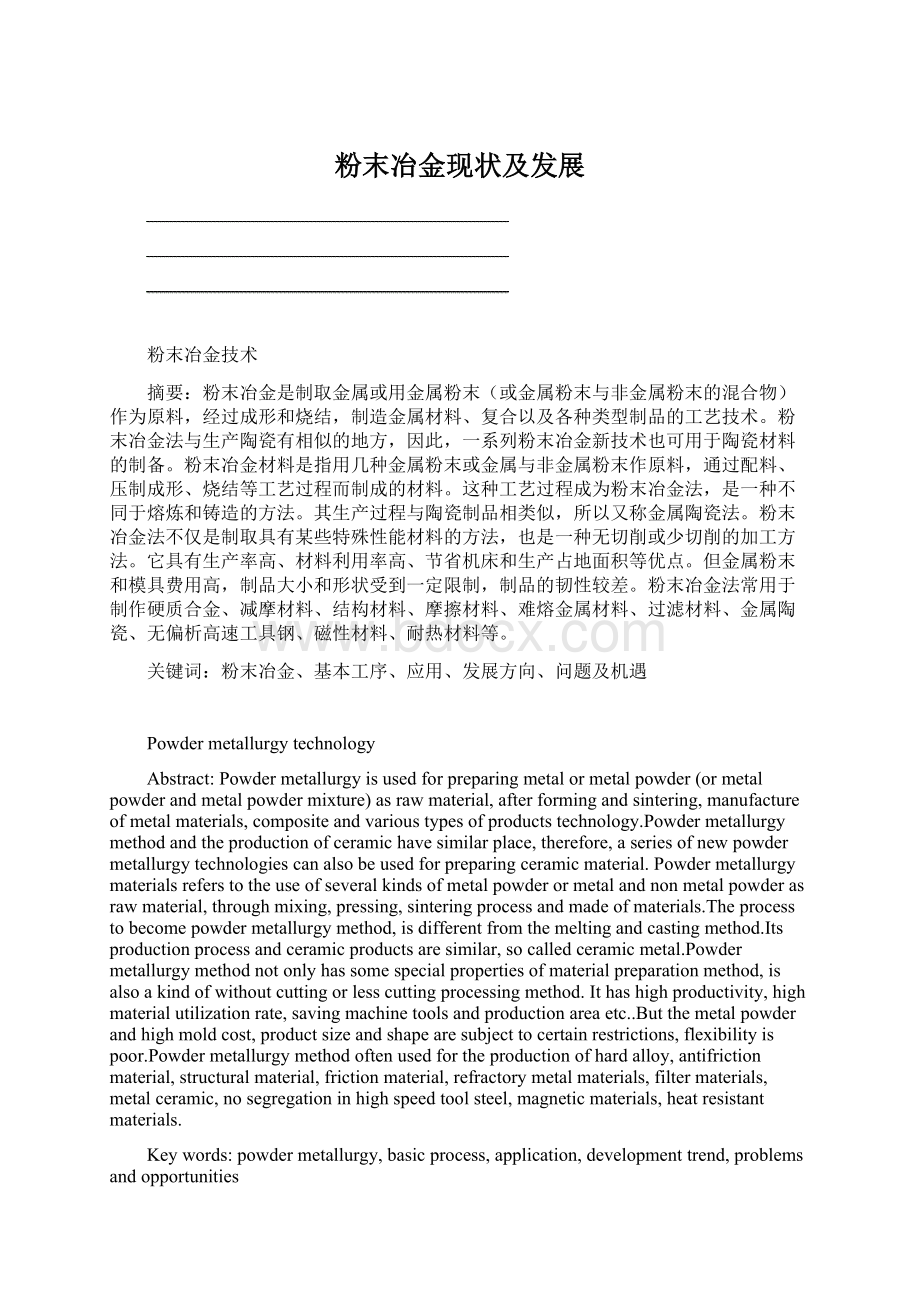
粉末冶金现状及发展
粉末冶金技术
摘要:
粉末冶金是制取金属或用金属粉末(或金属粉末与非金属粉末的混合物)作为原料,经过成形和烧结,制造金属材料、复合以及各种类型制品的工艺技术。
粉末冶金法与生产陶瓷有相似的地方,因此,一系列粉末冶金新技术也可用于陶瓷材料的制备。
粉末冶金材料是指用几种金属粉末或金属与非金属粉末作原料,通过配料、压制成形、烧结等工艺过程而制成的材料。
这种工艺过程成为粉末冶金法,是一种不同于熔炼和铸造的方法。
其生产过程与陶瓷制品相类似,所以又称金属陶瓷法。
粉末冶金法不仅是制取具有某些特殊性能材料的方法,也是一种无切削或少切削的加工方法。
它具有生产率高、材料利用率高、节省机床和生产占地面积等优点。
但金属粉末和模具费用高,制品大小和形状受到一定限制,制品的韧性较差。
粉末冶金法常用于制作硬质合金、减摩材料、结构材料、摩擦材料、难熔金属材料、过滤材料、金属陶瓷、无偏析高速工具钢、磁性材料、耐热材料等。
关键词:
粉末冶金、基本工序、应用、发展方向、问题及机遇
Powdermetallurgytechnology
Abstract:
Powdermetallurgyisusedforpreparingmetalormetalpowder(ormetalpowderandmetalpowdermixture)asrawmaterial,afterformingandsintering,manufactureofmetalmaterials,compositeandvarioustypesofproductstechnology.Powdermetallurgymethodandtheproductionofceramichavesimilarplace,therefore,aseriesofnewpowdermetallurgytechnologiescanalsobeusedforpreparingceramicmaterial.Powdermetallurgymaterialsreferstotheuseofseveralkindsofmetalpowderormetalandnonmetalpowderasrawmaterial,throughmixing,pressing,sinteringprocessandmadeofmaterials.Theprocesstobecomepowdermetallurgymethod,isdifferentfromthemeltingandcastingmethod.Itsproductionprocessandceramicproductsaresimilar,socalledceramicmetal.Powdermetallurgymethodnotonlyhassomespecialpropertiesofmaterialpreparationmethod,isalsoakindofwithoutcuttingorlesscuttingprocessingmethod.Ithashighproductivity,highmaterialutilizationrate,savingmachinetoolsandproductionareaetc..Butthemetalpowderandhighmoldcost,productsizeandshapearesubjecttocertainrestrictions,flexibilityispoor.Powdermetallurgymethodoftenusedfortheproductionofhardalloy,antifrictionmaterial,structuralmaterial,frictionmaterial,refractorymetalmaterials,filtermaterials,metalceramic,nosegregationinhighspeedtoolsteel,magneticmaterials,heatresistantmaterials.
Keywords:
powdermetallurgy,basicprocess,application,developmenttrend,problemsandopportunities
一、世界粉末冶金工业概况
2003年全球粉末货运总量约为88万吨,其中美国占51%,欧洲18%,日本13%,其它国家和地区18%。
铁粉占整个粉末总量的90%以上。
从2001年起,世界铁粉市场持续增长,4年时间增加了近20%。
汽车行业仍然是粉末冶金工业发展的最大动力和最大用户。
一方面汽车的产量在不断增加,另一方面粉末冶金零件在单辆汽车上的用量也在不段增加。
北美平均每辆汽车粉末冶金零件用量最高,为19.5公斤,欧洲平均为9公斤,日本平均为8公斤。
中国由于汽车工业的高速发展,拥有巨大的粉末冶金零部件市场前景,已经成为众多国际粉末冶金企业关注的焦点。
粉末冶金铁基零件在汽车上主要应用于发动机、传送系统、ABS系统、点火装置等。
汽车发展的两大趋势分别为降低能耗和环保;主要技术手段则是采用先进发动机系统和轻量化。
欧洲对汽车尾气过滤为粉末冶金多孔材料又提供了很大的市场。
在目前的发动机工作条件下,粉末冶金金属多孔材料比陶瓷材料具有更好的性能优势和成本优势。
工具材料是粉末冶金工业另一类重要产品,其中特别重要的是硬质合金。
目前制造业的发展朝着3A方向,即敏捷性(Agility)、适应性(Adaptivity)和可预测性(Anticipativity)。
这要求加工工具本身更锋利、刚性更好、韧性更高;加工材料的范围扩大到吕合、镁合金、钛合金以及陶瓷等;尺寸精度要求更高;加工成本要求更低;环境影响要减到最小,干式加工比例更大。
这些新要求加快了粉末冶金工具材料的发展。
硬质合金的晶粒(<200nm=和超粗晶粒(>6um);涂层技术发展很快,CVD、PVD、PCVD技术日益完善,涂层种类也很多,从常用的CVDTiCN/Al2O3/TiN到CVDPCBN(聚晶立方BN)以及PVDTiAIN,Al2O3,cBN(立方BN)和SiMAlON等,满足加工场合的需要。
信息行业的发展也为粉末冶金工业提供了新的契机。
日本电子行业用的粉末冶金产品已经达到了每年4.3亿美元,其中热沉材料占23%,发光与点极材料占30%。
前者主要包括散热材料,如Si/SiC,Cu-Mo,Cu-W,Al-SiC,AlN以及Cu/金刚石等材料;后者则主要包括钨、钼材料。
二、粉末冶金技术简介
粉末冶金是制取金属粉末并通过成形和烧结等工艺将金属粉末或与非金属粉末的混合物制成制品的加工方法,既可制取用普通熔炼方法难以制取的特殊材料,又可制造各种精密的机械零件,省工省料。
但其模具和金属粉末成本较高,批量小或制品尺寸过大时不宜采用。
粉末冶金工艺的基本工序是:
1、原料粉末的制备。
现有的制粉方法大体可分为两类:
机械法和物理化学法。
而机械法可分为:
机械粉碎及雾化法;物理化学法又分为:
电化腐蚀法、还原法、化合法、还原-化合法、气相沉积法、液相沉积法以及电解法。
其中应用最为广泛的是还原法、雾化法和电解法。
2、粉末成型为所需形状的坯块。
成型的目的是制得一定形状和尺寸的压坯,并使其具有一定的密度和强度。
成型的方法基本上分为加压成型和无压成型。
加压成型中应用最多的是模压成型。
3、坯块的烧结。
烧结是粉末冶金工艺中的关键性工序。
成型后的压坯通过烧结使其得到所要求的最终物理机械性能。
烧结又分为单元系烧结和多元系烧结。
对于单元系和多元系的固相烧结,烧结温度比所用的金属及合金的熔点低;对于多元系的液相烧结,烧结温度一般比其中难熔成分的熔点低,而高于易熔成分的熔点。
除普通烧结外,还有松装烧结、熔浸法、热压法等特殊的烧结工艺。
4、产品的后序处理。
烧结后的处理,可以根据产品要求的不同,采取多种方式。
如精整、浸油、机加工、热处理及电镀。
此外,近年来一些新工艺如轧制、锻造也应用于粉末冶金材料烧结后的加工,取得较理想的效果。
粉末冶金材料和工艺与传统材料工艺相比较:
1.粉末冶金工艺是在低于基体金属的熔点下进行的,因此可以获得熔点、密度相差悬殊的多种金属、金属与陶瓷、金属与塑料等多相不均质的特殊功能复合材料和制品,比如金属与非金属组成的摩擦材料等,控制制品的孔隙率和孔隙大小,可生产各种多孔性才材料和多孔含油轴承。
2.提高材料性能。
用特殊方法制取的细小金属或合金粉末,凝固速度极快、晶粒细小均匀,保证了材料的组织均匀,性能稳定,以及良好的冷、热加工性能,且粉末颗粒不受合金元素和含量的限制,可提高强化相含量,从而发展新的材料体系。
3.利用各种成形工艺,可以将粉末原料直接成形为少余量、无余量的毛坯或净形零件,大量减少机加工量。
提高材料利用率,降低成本。
粉末冶金工艺的优点:
1、绝大多数难熔金属及其化合物、假合金、多孔材料只能用粉末冶金方法来制造。
2、由于粉末冶金方法能压制成最终尺寸的压坯,而不需要或很少需要随后的机械加工,故能大大节约金属,降低产品成本。
用粉末冶金方法制造产品时,金属的损耗只有1-5%,而用一般熔铸方法生产时,金属的损耗可能会达到80%。
3、由于粉末冶金工艺在材料生产过程中并不熔化材料,也就不怕混入由坩埚和脱氧剂等带来的杂质,而烧结一般在真空和还原气氛中进行,不怕氧化,也不会给材料任何污染,故有可能制取高纯度的材料。
4、粉末冶金法能保证材料成分配比的正确性和均匀性。
5、粉末冶金适宜于生产同一形状而数量多的产品,特别是齿轮等加工费用高的产品,用粉末冶金法制造能大大降低生产成本。
粉末冶金工艺的缺点:
1、在没有批量的情况下要考虑零件的大小.
2、模具费用相对来说要高出铸造模具.
三、粉末冶金技术的应用与发展
1、用用于机械零件的制造
现代粉末冶金技术在机械制造中的应用范围正沿两个方向扩展:
一是制取承受高负荷的零件;二是制取几何尺寸复杂、尺寸精度高的零件,并使最终机械加工量减至最小限度。
在承受高负荷零件的制造中,后致密化技术中的锻造(以下简称粉末锻造)和热等静压起到了非常重要的作用。
粉末锻造又称预型坯热端,是粉末冶金预热段组成的复合工艺。
用这种方法制成的零件,其密度可达理论密度的99.4%。
它主要用于铁基零件,用用的材料主要是碳钢和低合金钢,也用也高温合金。
用这种方法制造的锦基高温合金零件的强度—温度性能已经超过了传统方法制造的同一合金零件。
热等静压是在高温高压下同时实现粉末的成型和烧结,一次制成成品零件。
用热等静压制得的零件晶粒细小均匀,密度接近理论密度,并且分布均匀,且具有优异的机械性能和物理性能。
制造形状复杂、尺寸精度高的零件所辖用的工艺方法主要有粉末锻造、注射成型、热等静压和粉末冶金的组合工艺。
用于这一用途的粉末锻造有两种:
一种是采用松装烧结制成接近最终制品的压坯,再放入模内进行锻压的方法。
这种方法制成的铁基零件密度虽较低(约为7.2g/cm3),但粉末分布均匀(密度差不超过0.05g/cm3),适用于制造汽车发动机水泵叶轮,四磁芯电磁仪表零件及多管接头零件。
另一种是前述的预型坯热锻法。
它特别适用于制造环形零件,如齿轮、离合器毂、凸轮和轴承座等。
用注射成型法可使所制零件密度达到理论密度的96%。
以波音707和波音727飞机机翼传动机构的螺纹部分用镍圈为例,这种圈结构复杂且有内螺纹,过去用锻坯需经14道工序加工而成,采用注射成型,可以制造几乎无余量的零件,只需少量的磨削和校准,并且该零件具有高的抗腐蚀性和好的机械性能。
热等静压工艺拟用于用高温合金制造的滚刀、涡轮发动机轴承和轮,及用钛合金制造的飞机涡轮发动机和机身零件,可减少机加工作量,提高材料利用率。
粉末冶金组合工艺可用于制造形状复杂、用常规方法不能制造的零件或大型粉末冶金零件;可用于制造不同部位具有不同化学成分、密度及物理—力学性能的零件;还可与不同材料(如钢或铝等)组合烧结成适用于某种专门用途的零件。
2、应用于合金性能的改进
随着对材料要求的不断提高,传统的铸锭冶金(IM)方法对合金的性能改进已趋于顶峰,粉末冶金(PM)技术成为改进和研制合金的一种手段。
2.1铝合金
到目前为止,用PM方法改进或研制的铝合金按性能可分为4类:
高强度,高弹性模量,低密度,热强和功能铝合金。
7090,7091,MR61,MR64,CW67,IN9021和IN9052属PM高强度铝合金。
前5种是RSP(快冷合金粉末)合金,是在7系合金的基础上添加少量的Co,Zr或Cr作为附加剂和稳定剂而制得的;后两种是用机械合金化方法制得的,它们在抗拉强度、抗蚀性、断裂韧性等方面具有良好的综合性能。
PM高弹性模量、低密度铝合金大多数是在IN2024合金的基础上(也有降低Cu,Mg含量及用Zr取代Cr的)添加1%~3%Li的铝锂合金。
Al-Cu-Li-Zr,Al-Li-Zr及Al-Cu-Mg-Li-Zr是发展高弹性模量、低密度铝合金的主要方向。
对于要求更高模密比的合金,可考虑用Be或Mn来取代或部分取代Cu,Mg,或研制Al-Li-Be合金。
另外,PM方法解决了IM方法生产铝锂合金的困难,还可细化晶粒和第二相粒子,消除偏析,提高合金的塑性和韧性。
在热强铝合金方面,研究较多的是Al-Fe系合金。
已商品化的CV78比现有的IN2219的使用温度提高50~90,用它代替钛合金制造喷气式发动机涡轮,成本可降低65%,重量减轻15%。
正在研究并已开始使用的有8009和FVS1212。
8009高温强度高,断裂韧性好,已用于锻造各种航宇零件和汽车部件,以及薄、厚板和挤压型材;FVS1212具有高的刚性和优异的高温性能。
功能铝合金分为两组:
一组为耐磨和尺寸稳定铝合金。
它广泛用于光学机械仪表和其他仪表。
另一组是低膨胀系数铝合金。
这类合金一般为Al-Si合金,含Si量为10%~30%,另外再加石墨强化,还有增加Ni,Mg,Fe,Zr等,以改善其抗热性。
它们具有低的膨胀系数和高的弹性模量,可用于仪表、发动机等行业。
2.2高合金材料
高合金材料如高速钢采用PM方法生产,可得到碳化分布均匀的细晶粒组织,具有较高的抗弯强度和冲击强度,韧性可提高50%,热处理变形约为IM高速钢的1/10。
还大大提高了耐磨削性能,用它制造的刀具寿命可提高3~5倍。
此外,粉末冶金制品的工序较少,材料利用率可由50%~60%提高到95%。
2.3高温合金
采用先进的粉末冶金技术可以制得纯净的合金粉末,并且合金组织均匀,无偏析。
采用PM技术,可使现有的高温合金的工作温度提高100,疲劳寿命提高100倍,蠕变强度大约提高20%。
2.4磁性材料
与熔铸方法相比,PM磁性材料有如下优点:
可以生产出具有特殊性能的磁性材料,如铁氧体、磁介质等;能用单畴粉末制造出优质永磁材料;材料晶粒细、强度大、无缩孔及偏析等弊病。
用PM方法制造体积小、形状复杂的小型磁体具有极大的竞争力。
采用PM方法生产材料最显著的一个特点是材料设计的自由度高,通过改变材料的成分或工艺方法以改变材料的晶体结构,可获得不同功能的材料。
3、应用于新型材料的研制
3.1金属基复合材料
用于制造金属基复合材料的工艺方法有:
PM法、压铸法和搅拌铸造法。
与搅拌铸造法相比,PM法制取复合材料的温度低,减轻了基体与增强体之间的界面反应,减少了界面上硬质化合物的生成,从而得到较好力学性能的材料;PM法可以制造用搅拌铸造法不能制取的材料,如用搅拌铸造法制造碳化硅钛基复合材料时,碳化硅晶须溶于钛合金基体,采用PM法可避免这一现象发生。
与压铸法相比,PM法增强体的体积分数可以任意调节,成分比较准确,制取的材料力学性能好,用PM法生产的材料无比重偏析。
因此,PM法已成为开发金属基复合材料的主要工艺方法之一。
3.2弥散强化高温材料
弥散强化类高温材料最早用于铁基材料的研究,近年来扩展到铝基材料。
ODM751是新近研究的氧化物弥散强化的铁基材料,这种材料有优良的抗蠕变和抗腐蚀综合性能,耐温可达1350,它主要用于温度高于900,要求高强度、高腐蚀性的场合,如热交换器、蓄热器、热电偶外壳等。
已生产的弥散强化铝基材料有原苏联的我国的LT71,LT72和西方国家的SAP930,SAP895,SAP865等。
这类材料靠Al2O3弥散强化。
它的热强性在200~500范围内比任何铝合金都高,500的高温瞬时强度可达80~90MPa,热稳定性好,长时间加热后力学性能损失小,在500及其以下任何温度长时间加热,对其室温性能无明显影响,抗蚀性与纯铝相近。
它可用于飞机的防火板、航空及化学工业用的热交换器及制造原子堆汽轮导管支持元件。
另外,近年来弥散强化铝合金研究的有:
Al-C,Al-TiC,Al-ZrC,Al-NbC,Al-Cr2O3,Al-MoC,Al-WC等,其中Al-C材料已用于内燃机活塞,它的强化相是Al4C。
金属间化合物的研究主要采用机械合金化方法,已有初步成果的有NiAl,TiAl和MoSi2。
这类材料的单体和复合材料具有密度低,模量、高温强度及高温蠕变强度高的特点。
高压涡轮叶片用NiAl高的导热系数使制成的部件温度均匀,且其热点温度至少可降低50,另外,它的抗高温氧化性也好。
MoSi2的熔点高,抗氧化性好,但要在实际中应用,其室温塑性和韧性还有待进一步提高。
3.4梯度功能材料
目前,梯度功能材料的开发仅有热功能梯度材料。
它是基于航宇结构、核聚变反应堆和未来高速飞行的需要而研制的。
它的一面是高强度的金属材料,另一面为耐高温粉末材料(如高温结构陶瓷、金属间化合物),中间层为高强度的纤维(如氧化锆、碳化硅纤维等)和微粒(如陶瓷或金属间化合物粉末,碳粒或玻璃微粒等)。
这种结构既保证了高强度和高耐热性,又保证了材料的组织与工作的温度梯度相适应,减小了在高温下受热表面和金属材料层间的热膨胀失配而引起的应力。
4、其他方法的应用
4.1超塑性材料
采用PM法可获得极细的晶粒,合金界面上的氧化物质点和析出相均能起钉扎晶界的作用,使材料具有高的组织稳定性。
另外,PM法制备的超塑性材料还可实现高应变速率的超塑性,高的应变速率能提高超塑性成形效率。
因此,在材料的超塑性研究中,PM技术受到了极大的关注并取得了可喜的成果。
4.2高抗蚀性材料
高的抗腐蚀和抗应力腐蚀能力是粉末冶金的主要特性,洛克希德-乔治亚公司已用PM铝合金设计和制造了3个试验性飞机零件,其中两个是挤压梁,一个是锻造襟翼滑轨加强缘条。
这些零件安装在3架洛克希德C-141运输机上进行试验。
它的寿命比用IM法加工的零件长得多,使更换费用大大减少。
四、粉末冶金技术国内与国外差距
1、产品水平低
在产品精度方面,少数企业尺寸精度可达IS07—8级,形位公差可达8—9级,与国外水平相比低1—2级,但一般企业约相差2—3级。
产品质量不够稳定,产品内在重量和外观质量均有较大的差距
2、工艺装备落后
多数企业仍采用性能较差的设备、能耗大、效率低、炉温均匀性差,质量不稳定;国内还没有形成一个专业生产粉末冶金模具、模架的企业
五、粉末冶金材料和制品的今后发展方向:
粉末冶金制品的应用范围十分广泛,从普通机械制造到精密仪器;从五金工具到大型机械;从电子工业到电机制造;从民用工业到军事工业;从一般技术到尖端高技术,均能见到粉末冶金工艺的身影。
粉末冶金材料和制品的今后发展方向:
1、有代表性的铁基合金,将向大体积的精密制品,高质量的结构零部件发展。
2、制造具有均匀显微组织结构的、加工困难而完全致密的高性能合金。
3、用增强致密化过程来制造一般含有混合相组成的特殊合金。
4、制造非均匀材料、非晶态、微晶或者亚稳合金。
5、加工独特的和非一般形态或成分的复合零部件。
六、国内粉末冶金技术面临的问题及机遇
随着我国汽车工业快速发展,高附加值的零部件需求将加速增长。
与此同时,汽车产业链全球化的采购系已经形成,带给国内零部件企业商机显而易见。
然而,我们是否能够握当前机遇,不仅是我国汽车零部行业突破当前困局的机遇,更是产业升级的契机。
因此,充分利用自身势,扬长补短是产业突破困局的必手段。
虽然,当前我国的粉末冶金技术水平相对国外发达国家依然有着不小的距离。
但由于我国拥有原料供给的区域优势,作为产业竞争力提升的基础,依然有较强的竞争力。
与此同时,自上世纪90年代开始,我国粉末冶金制品行业也呈加速发展(主要集中在东部及沿海地区),东部和沿海地区的年产量增长幅度均在10%以上。
以山东为例,该省的生产企业由于引进了国外先进设备技术,生产高强度、高精度粉末冶金零件,把粉末冶金制品的质量、技术提高到一个新的水平;粉末注射成型、粉末锻造、纳米技术、精细陶瓷等新技术的开发应用提高了行业整体技术水平,构成了一个完整的行业体系。
据不完全统计,目前全省已有各类粉末冶金企业40多家,产品应用各个领域。
最后在拥有区域优势的同时,建立产业基地,形成基地集群效应,从而实现市场和效益最大化、成本最小化。
同时,在行业内部合理分工,逐步形成分工明确的纵向多层次有机整体,依托国内市场发展制造能力,再通过国际合作迅速提升竞争力、获取竞争优势,并且通过国际合作所获得的企业在未来发展中的资本、技术、产品和管理的支撑,进入国际合作伙
伴的配套体系和融人全球采购体系,突破当前产业困局。
参考文献:
【1】粉末冶金新技术与新装备 刘文胜马运柱...矿冶工程20075
【2】现代粉末冶金材料和技术发展现状
(一) 黄伯云易健宏上海金属20073
【3】现代粉末冶金材料和技术发展现状
(二) 黄伯云易健宏上海金属20074
【4】钛及钛合金的粉末冶金新技术 周洪强陈志强材料导报:
网络版20061
【5】世界粉末冶金的发展现状刘咏黄伯云中国有色金属20061
【6】粉末冶金多孔材料性能研究 孙纪国王浩...导弹与航天运载技术20064
【7】粉末冶金文摘 亓家钟(摘择)粉末冶金技术20062
【8】GermanRM.PowderInjectionMolding[M].MPIF:
Princeton,1990.61~95.
【9】CapusJ,PickeringS,WeaverA.Hoeganaesoffershigherdensityatlowercost[J].MetalPowderReport,1994,49(78):
22~24.