半固态加工及其在铝镁合金中的应用.docx
《半固态加工及其在铝镁合金中的应用.docx》由会员分享,可在线阅读,更多相关《半固态加工及其在铝镁合金中的应用.docx(11页珍藏版)》请在冰豆网上搜索。
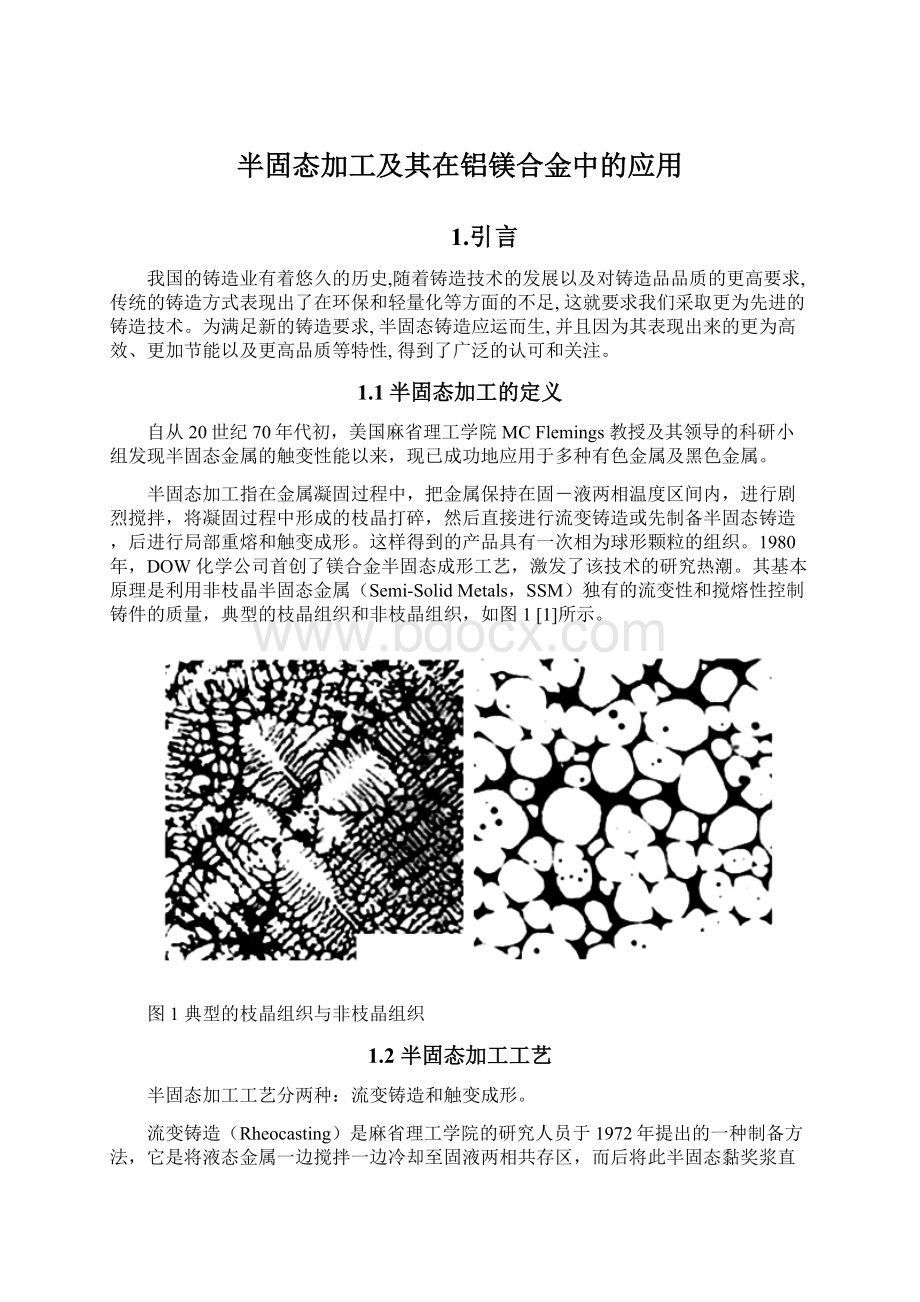
半固态加工及其在铝镁合金中的应用
1.引言
我国的铸造业有着悠久的历史,随着铸造技术的发展以及对铸造品品质的更高要求,传统的铸造方式表现出了在环保和轻量化等方面的不足,这就要求我们采取更为先进的铸造技术。
为满足新的铸造要求,半固态铸造应运而生,并且因为其表现出来的更为高效、更加节能以及更高品质等特性,得到了广泛的认可和关注。
1.1半固态加工的定义
自从20世纪70年代初,美国麻省理工学院MCFlemings教授及其领导的科研小组发现半固态金属的触变性能以来,现已成功地应用于多种有色金属及黑色金属。
半固态加工指在金属凝固过程中,把金属保持在固-液两相温度区间内,进行剧烈搅拌,将凝固过程中形成的枝晶打碎,然后直接进行流变铸造或先制备半固态铸造,后进行局部重熔和触变成形。
这样得到的产品具有一次相为球形颗粒的组织。
1980年,DOW化学公司首创了镁合金半固态成形工艺,激发了该技术的研究热潮。
其基本原理是利用非枝晶半固态金属(Semi-SolidMetals,SSM)独有的流变性和搅熔性控制铸件的质量,典型的枝晶组织和非枝晶组织,如图1[1]所示。
图1典型的枝晶组织与非枝晶组织
1.2半固态加工工艺
半固态加工工艺分两种:
流变铸造和触变成形。
流变铸造(Rheocasting)是麻省理工学院的研究人员于1972年提出的一种制备方法,它是将液态金属一边搅拌一边冷却至固液两相共存区,而后将此半固态黏奖浆直接传送至冷室压铸机铸造成工件,亦称搅动铸造(StirCasting),如图2所示。
由于半固态金属浆液的保存和输送不方便,该成形方法实际投入应用的较少。
触变铸造(Thixocasting),它是将经搅拌等工艺获得的具有非枝晶组织的半固态坯料冷却凝固后,制成所需要的尺寸,重新加热到半固态温度,然后进行压铸或挤压成形,如图2[1]所示。
由于半固态金属坯料的加热、输送很方便,并且成形过程容易控制,便于实现自动化,因此触变铸造是当今半固态铸造的主要工艺方式。
图2流变铸造和触变铸造工艺示意图
1.3半固态坯料的制备方法
半固态加工技术其核心工艺为制备半固态坯料。
发展到现在,坯料的制备已有多种方法:
机械搅拌法[2],电磁搅拌法[3,4],应变诱发熔化激活法[5],喷射成形法[6],紊流效应法[7],液相线铸造发[8]等。
其中电磁搅拌法在国外已应用于工业化生产。
(1)机械搅拌法应用较早,其设备构造简单,可以通过控制搅拌温度、搅拌速度和冷却速度等工艺参数,使初生树枝晶破碎而成为类球形。
随着搅拌程度由弱至强,晶粒依次表现为枝晶状、菊花状以及圆球状[9]。
研究表明[10],三种铸造显微组织的力学性能是从低变到高的,因此人们总是希望得到较为圆整的晶粒组织。
(2)电磁搅拌法是利用旋转电磁场在金属液里产生感应电流,金属液受洛伦磁力的作用产生运动,从而达到对金属液搅拌的目的。
目前,主要有两种方法产生旋转磁场:
一种是在感应线圈内通交变电流的传统方法;另一种是1993年由法国的Vives推出的旋转永磁体法,内部可产生高的磁场强度,通过改变永磁体的排列方式,可使金属液产生明显的三维流动,提高了搅拌效果,减少了搅拌时的气体卷入。
(3)应变诱发熔化激活法是将原合金进行足够冷变形,然后加热到半固态。
在加热过程,先发生再结晶,然后部分熔化,使初生相转变成颗粒形成半固态合金。
该方法由于增加了预变形工序,增加了生产成本,仅适合于小直径坯的生产。
(4)喷射成形法是在金属熔化成液态金属后,雾化为熔滴颗粒,受喷射气体作用,使得部分凝固的微滴直接沉积在收集板表面。
当每个熔滴的冲击能够产生足够的剪切力打碎熔滴内部形成的枝晶时,凝固后便成为颗粒状组织,经加热到局部熔化时,也可得到具有球形颗粒固相的半固态合金。
(5)紊流效应法是指在金属液通过特制的多流装置时,使金属液的流动产生紊流效应,打碎形成的枝晶,从而获得具有流变特性的半固态合金。
(6)液相线铸造法是在低于合金液相线温度保温形核后,进行铸造,获得具有均一细小非枝晶组织的半固态合金方法。
根据文献[11]建立的模型,即晶粒首先呈稳态球形生长,直到球形半径大于最小稳定半径,然后呈枝晶长大,可把液相线铸造晶核的长大过程分为三个阶段,球形长大、枝晶长大、枝晶抵触后的枝晶的熟化,如图3所示。
晶粒在互相抵触之前是完全呈球形长大,还是先以球形长大,然后以枝晶长大,取决于形核数目和冷却强度。
崔建忠等人[2,12,13]开发了液相线铸造法制浆新工艺,并对356、2618及7075等铝合金进行了系统研究,结果表明,在凝固初期,小的冷却强度有利于球形晶粒的形成。
在凝固后期,大的冷却强度则有利于保存获得的球形晶粒组织。
图3晶粒长大形成过程示意图
1.4半固态加工的特点
与传统加热的液态金属或固态金属成形相比,半固态铸造技术呈现出一系列的优点:
(1)半固态金属浆体含有一半左右的初生相,粘度可以调整。
而且可以进行机械搬运,便于自动化操作。
受压力作用时,半固态金属浆体的粘度迅速降低,便于成形。
(2)成形速度高。
(3)成形时,半固态金属不易喷溅,改善了充型过程,减轻了金属的裹气和氧化,提高了成形件的致密性,成形件可以进行热处理强化,其强度比液态金属的压铸件更高。
(4)金属浆体在充型前已析出一半左右的固相,减少了凝固收缩,成形件有更少的空洞,能承受更高的液体压力。
(5)半固态金属浆体不存在宏观偏析,因而成形件也不存在宏观偏析,成形件的性能更均匀。
(6)利用半固态金属可以进行机械零件的近终化成形,可大幅度减少零件毛坯的机加工量,显著降低生产成本。
(7)由于半固态金属充型温度低,减轻了模具的热冲击,提高了模具的寿命。
(8)加热半固态金属浆体比熔化金属坯体节约能源(25~30)%。
(9)半固态金属成形车间不需要处理液态金属,操作更安全,工作环境更优良。
(10)半固态金属的粘度较高,可以方便地加入增强相(颗粒或纤维),提高金属浆体的性能,提供了一个开发廉价产品的新途径。
(11)半固态金属的成形应力显著降低,因此金属半固态模锻的成形速度比金属固态模锻成形的速度更高,且可以成形很复杂的零件,缩短加工工序,降低成本,而性能与固态金属锻件相同。
1.5半固态铸造技术的应用
1.5.1汽车零件
八十年代,铝合金汽车部件(主刹车缸等)已经开始在欧洲生产使用,主要是因为传统的铸铁刹车缸已经不能满足汽车轻量化和提高燃料利用率等的性能要求,故而求助于铝合金。
但是,目前铝合金缸体的成形工艺多数采用压铸工艺,质量欠佳,铸件气密性差,强度不够,工作时容易发生介质油渗漏,导致事故发生。
瑞士的Buhler公司着力于半固态压铸的SC压铸机的研发,并于1993年生产出了第一台适用于铝合金半固态压铸的SC压铸机,与普通压铸机相比,产品质量提高,工艺周期大幅度缩短[14]。
众多实践生产表明,轿车、轻型车的转向节、泵体、转向器壳体、阀体、悬挂支架件和轮毂等高强度、高致密度、高可靠性要求的铸件,采用半固态铸造技术成形可以实现产品的低成本、高产以及高质量[15]。
美国Alumax公司于1994年建立的半固态铸造技术生成汽车零件的工厂,每年可生产2400万个零部件,零件单重从10g到10kg,直径达到500mm。
1995年,Thixomat公司的子公司-Lindberg公司利用半固态铸造工艺,为一些汽车公司生产了50余万件的半固态镁合金铸件。
意大利的StampalSpA公司利用半固态技术大批量生产了AlfaRomeoSpider跑车后悬挂系统的左右横向支承等汽车零件。
德国的EFU公司、法国的PechineySA公司等都已具备了大规模生产半固态金属零件的能力。
汽车铸件采用半固态成形工艺,质量明显优于压铸工艺,缸体单件质量轻,生产效率明显提高,如表1所示。
表1主刹车缸零件重量和生产率
目前,铝、镁合金半固态铸造技术在西方发达国家早已进入了工业化阶段,尤其在镁合金铸造方面的应用。
世界镁铸造件总产量的93%用压铸工艺生产。
主要是由于镁合金具有优良的压铸工艺性能。
然而,作为室温使用的主要压铸镁合金AZ91D,虽然具有较高的强度及良好的铸造性能[16],但与铝合金相比,其热裂倾向较大,而半固态铸造技术是一种不断发展的新技术,通过半固态铸造技术,降低了成形温度和凝固收缩,提高了镁合金强度[17,18],降低了生产成本,扩大了它的使用范围。
此外,汽车轮毂采用半固态铸造工艺,可以克服低压铸造工艺存在的废品率高、生产率底的弊端,生产的轮毂强度高,零件重量明显减轻,从而可以节约能耗。
两种工艺生产的零件性能比较,如表2所示。
表2半固态成形与低压铸造生产轮毂的性能比较
由表2可见,半固态成形轮毂比低压铸造轮毂,力学性能大幅度提高,生产率提高了9倍。
日本SpeedStarWheel公司于1994年开始利用半固态金属成形技术生产铝合金轮毂。
目前,大多数汽车部件采用半固态铸造技术,其成形件,如图4所示。
图4半固态铸造成形件
1.5.2电子产品
相比于一般常用的金属,镁合金具有较佳的比刚度、比强度、切削性、导热性以及可回收等诸多优点,此外亦具有防电磁波的特性。
应环保及轻量化的趋势,镁合金工件渐渐广泛应用于3C产品机壳及电子结构件,尤其笔记本电脑、移动电话及可携式电子产品的外壳及框架,如图5所示。
当采用镁合金制造手机、笔记本电脑和一些家用电器的外壳时,能显著增强产品的散热能力和抗震能力,并能有效地减轻对人体和周围环境的电磁辐射危害。
但是,传统镁合金压铸件的质量与产量稳定性较差,瑕疵率较高,后续处理工序复杂,使得制造成本增加。
采用半固态铸造工艺,成形温度低,产品性能有保障,生产率高,适合工业化生产。
目前,日本利用半固态铸造技术进行生产的厂家主要有:
SpeedStarWheels公司、东京理化工业所、朝日技术公司、MGPrecision公司、高田公司、Panasonic电气公司等。
日本Takata公司利用半固态成形技术和镁合金生产照相机和MD壳,MGPrecision公司利用半固态技术和镁合金生产微机机壳。
此外,随着航空、航天工业的迅猛发展,要求武器装备高性能、高可靠性、轻量化以及机动性强。
半固态铸造技术以其特殊性,逐渐替代了传统铸造工艺,在军用装备的改造方面同样发挥着重要作用。
图5电子产品外壳
2.金属半固态铸造技术的研究现状及发展趋势
(1)国外研究现状
有色金属及其合金的低熔点材料半固态成形研究:
①以美国、日本为首的先进国家针对铝、镁、铅、铜等的合金进行了研究,其重点放在成形工艺的开发上。
目前,国外进入工业应用的半固态金属主要是铝、镁合金,这些合金最成功的应用主要集中在汽车领域。
②半固态加工实验方面的研究主要是浆料的制备和半固态加工材料的成形。
③理论方面的研究主要是围绕与工艺实现和试样组织、性能有关方面进行的。
高熔点黑色金属的半固态成形研究,目前,高熔点黑色金属半固态加工进展缓慢,原因在于存在以下困难:
①选择的材料液固线温度区间较小;②高温半固态浆料难以连续稳定地制备;③熔体的温度、固相的比率和分布难以准确控制;
④浆料在高温下输送和保温困难;⑤成形温度高,工具材料的高温性能难以保证等等。
国外有学者尝试利用压铸机对Fe-2.5%C-3.1%Si铸铁和AISI440A不锈钢的半固态浆料直接进行流变成形,可以获得初生固相分布均匀的优质成形件。
Flemings等人利用机械搅拌方法制备了半固态Sn-15pctPb浆料连续轧制薄带。
但机械搅拌方法的固有缺点使其不能作为工业性连续轧制半固态高熔点金属薄带的搅拌方法。
近年来,日本学者尝试了将黑色金属半固态浆料与轧机直接相接合来连续轧制金属薄带,但没有详细报道研究结果。
(2)国内研究现状
①七十年代后期,我国陆续开展了利用机械搅拌法进行流变铸造或触变铸造研究。
中科院金属研究所较早进行了“铝合金半固态铸造”等的研究。
②八十年代中期,我国研究者大多转向半固态制备复合材料和个别通用牌号材料的流变特性的研究。
③九十年代以后北京科技大学、中科院金属所、北京有色金属研究总院、东南大学、东北大学、清华大学、哈尔滨工业大学、西北工业大学等单位在有色金属及其合金等低熔点材料半固态加工和钢铁等高熔点材料的半固态加工方面开展了广泛研究。
④近几年,我国在国家“863”计划等的支持下,已经在铝合金半固态加工技术开发和应用方面具备了向产业化转化的技术基础。
⑤北京科技大学和中科院金属所等单位合作在铸铁、弹簧钢、不锈钢和高碳钢等高熔点材料的半固态坯料制备、半固态喷铸成形和直接轧制等方面进行了较深入研究,并取得了阶段性成果。
⑥清华大学、东南大学等院校在半固态合金的流变和触变行为、成形过程的计算机模拟等基础理论研究方面开展了卓有成效的工作。
⑦在镁合金半固态成形基础及技术研究和应用方面,我国刚刚起步。
2000年,北京科技大学和北京有色金属研究总远开展“先进半固态镁合金制备与成形的基础研究”工作,目前在先进镁合金成分设计和成形性能方面已取得进展。
金属半固态铸造的发展趋势:
进一步完善金属半固态触变铸造技术;进一步扩大金属半固态铸造的应用范围;突破金属半固态浆料流变铸造的技术关键,缩短金属半固态铸造工艺流程。
我国的汽车、电子等工业正在快速发展,均是我国的支柱产业,因此金属半固态铸造成型技术在我国汽车、电子等工业中的应用前景光明。
3半固态加工在铝合金中的应用
由于铝合金在实际应用中十分广泛,且其具有较大的固-液两相区间范围,因此铝合金的半固态加工是研究的最为广泛也是最为成功的。
最早应用于半固态加工的铝合金为亚共晶铸造铝合金A356、A357,这两种铝合金在发达国家已实现工业化生产,后来又开发了过共晶成分的A390铝硅合金。
而目前高强度铝合金半固态加工主要集中于研究2XXX系列(如2014,2024,2618)、6XXX系列(如6082)和7XXX系列(如7075)。
从表3[19]中我们可以很清楚看到,经过半固态加工所得到的铝合金的力学性能普遍比普通铸造的铝合金高,与锻件性能相近。
表3不同加工方法所获得铝合金的力学性能比较
注:
SSM—半固态金属;PM—硬模铸造:
w—锻造;T6、T7—热处理制度
国外,铝合金的半固态成形加工主要应用于汽车工业中零件的生产,在轿车或轻型汽车部分采用半固态铝合金零件,以达到减重效果及提高性能。
这方面,欧美发达国家已进入工业运用阶段,通过半固态加工生产的汽车零件已进入市场;日本也初步具备了生产能力。
4半固态加工在镁合金中的应用
镁合金为最轻的结构材料(合金密度ρ为1400-1900kg/m3),且热量低、铸造生产率高、与其他结构材料比较切削更快耗能较少、高比强度、高阻尼以及完全可再生产,近年来在顺应环保及轻量化的趋势下,镁合金工件更是被广泛应用。
特别是汽车以及航空用镁合金部件的大量应用更是使镁合金成为各方关注和研究的热点。
常用镁合金成形方法主要有压铸、半固态铸造、挤压铸造等,其中压铸法运用最为广泛。
但用半固态铸造的镁合金无论在内部缺陷,还是力学性能方面都远优于压铸法,因此镁合金的半固态成形受到了广泛的关注。
相对于铝合金的半固态成形的基本成熟,由于镁合金锭料在二次加热时易氧化燃烧,所以一般的半固态加工技术并不适应于镁合金。
1988年10月,Dow化学公司宣布开发了一种新半固态金属镁成形工艺,并由Thixomat公司于1991年正式展出第一台用于镁合金的半固态触变成形机,从而使半固态金属镁成形技术迈向商业化进程[20]。
其工艺与流变铸造相比,不需要将材料搅拌成浆液;与触变成型相比,又少了制备半固态铸锭过程。
且集半固态浆料的制备、输送和成形于一体,避免了半固态铸锭保存输送及成形过程中产生的一系列问题,提高了生产效率。
另一种针对其它半固态铸造工艺的缺点开发出来的流变铸造,由于流变化生产的半固态金属浆料保存与输送难度较大,其实际应用受到限制。
但目前英国、台湾等地已经开发出用于实际应用的镁合金流变成形设备,预计在二十一世纪将大有作为,并形成镁合金加工技术的新突破[21]。
表4AZ91D半固态触变注射成形与传统压铸工艺质量与性能比较
由表4[22]可知半固态铸造AZ91D在内部缺陷、加工精度及力学性能等方面总体上优于普通铸造。
虽然目前镁合金半固态加工的工业化生产还很不成熟,但随着人力和物力的不断投入,其必将有良好的发展前景。
5.结论
半固态加工技术近年来发展十分迅速,半固态铸造铝镁合金在汽车行业中的应用更是前景看好。
我国的汽车行业蓬勃发展,特别是轿车行业正处于大力发展阶段,面对外来冲击,提高我国汽车在国际市场上的竞争力,非常有必要采用各种新工艺、新材料,而半固态铸造铝镁合金的使用不失为一种可行的取胜之道。
半固态铸造符合未来对于生产高质量、高性能、具有环保特性材质的要求,是未来铸造业发展的方向。
优质合金的广泛使用趋势,不仅能够扩大半固态铸造的实际应用领域,也会促进半固态铸造事业的不断深人和发展。
总体来说,半固态铸造事业会逐步取代落后的铸造方式,具有非常光明的发展前景
参考文献
[1]艾桃桃.半固态铸造技术的研究状况及应用.机械设计与制造,2010,2:
64—66
[2]崔建忠,路贵民.半固态浆制备技术新进展[J].哈尔滨工业大学学报,2000,32(4):
110—113
[3]LimSC,YoonEP.TheEffectofElectromagneticStirringontheMicrostructureofAl-7wt%SiAlloy[J].JMaterSciLett,1997,16
(2):
104—109
[4]VivesC.ElaborationofMetalMatrixCompositesfromThixotropicAlloySlurriesUsingaNewMagnetohydrodynamicCaster[J].MetalTransB,24B,1993(3):
493—510
[5]关原一敏,大西智,缣土重晴等.合金与半熔融成形加工[J].轻金属,1995,45(9):
560—565
[6]KiuchiM,SugiyamaS.ApplicationofMashyStateExtrusion[J].JMaterShapingTechnol,1990,8
(1):
39—46
[7]FlemingsMC.BehaviorofMetalAlloysintheSemisolidState[J].MetalTransB,1991,22B(3):
269—293
[8]XiaK,TausingG.LiquidusCastingofaWroughtAluminumAlloy2618forThixforming[J].MaterialsScienceandEngineering,1998,A246:
1—10
[9]FlemingsMC.BehaviorofMetalAlloysintheSemisolidState[J].MetallurgicalTransactions,1991,22A:
957—981
[10]吴树森,李东南,毛有武等.半固态流变压铸AZ91D镁合金的组织与性能[J].铸造,2002,51:
583—586
[11]NastacL,StefannescuDM.Macrotransportsolidificationkineticsmodelingofequiaxeddendriticgrown[J].MetallurgicalandMaterialsTransactions,1996,27A:
4061—4074
[12]路贵民,董杰,崔建忠.7075合金液相线半连续铸造与二次加热的合金组织[J].中国有色金属学报,2001,11
(2):
211—215
[13]董杰,路贵民,任栖锋等.液相线铸造法非枝晶半固态组织形成机理探讨[J].金属学报,2002,38
(2):
203—207
[14]KirkwoodPH.Semi-solidprocessingofalloys[J].Metalsandmaterials,1989
(1):
16—19
[15]许洛萍,邵光杰,李麟等.汽车轻量化用金属材料及其发展动态[J].上海金属,2002,24(3):
1—7
[16]BrownR.Magnesiumautomotivemeeting[J].LightMetalAge,1992,50(5—
6):
18—20
[17]毛卫民.半固态金属成形技术[M].北京:
机械工业出版社,2004:
2—6
[18]罗守靖,田文彤,谢水生等.半固态加工技术及应用[J].中国有色金属学
报,2000,10(6):
765—769
[19]谢水生,黄声宏.半固态加工技术及其应用.热加工工艺,2005,10:
5-6
[20]甄子胜,毛为民,赵爱民等.半固态镁合金的研究进展.特种铸造及有色合金,2001(6):
32—34
[21]吕苇白,杨湘杰,蔡卫华等.镁合金新型绿色产业的发展.江西冶金,2002,22(4):
23—27
[22]潘洪平,丁志勇,谢水生.镁合金加工技术的研究现状及应用.轻合金加工技术,2002,30(7):
7—10