24二氯苯酚与26二氯苯酚的生产工艺和分离方法文献综述.docx
《24二氯苯酚与26二氯苯酚的生产工艺和分离方法文献综述.docx》由会员分享,可在线阅读,更多相关《24二氯苯酚与26二氯苯酚的生产工艺和分离方法文献综述.docx(8页珍藏版)》请在冰豆网上搜索。
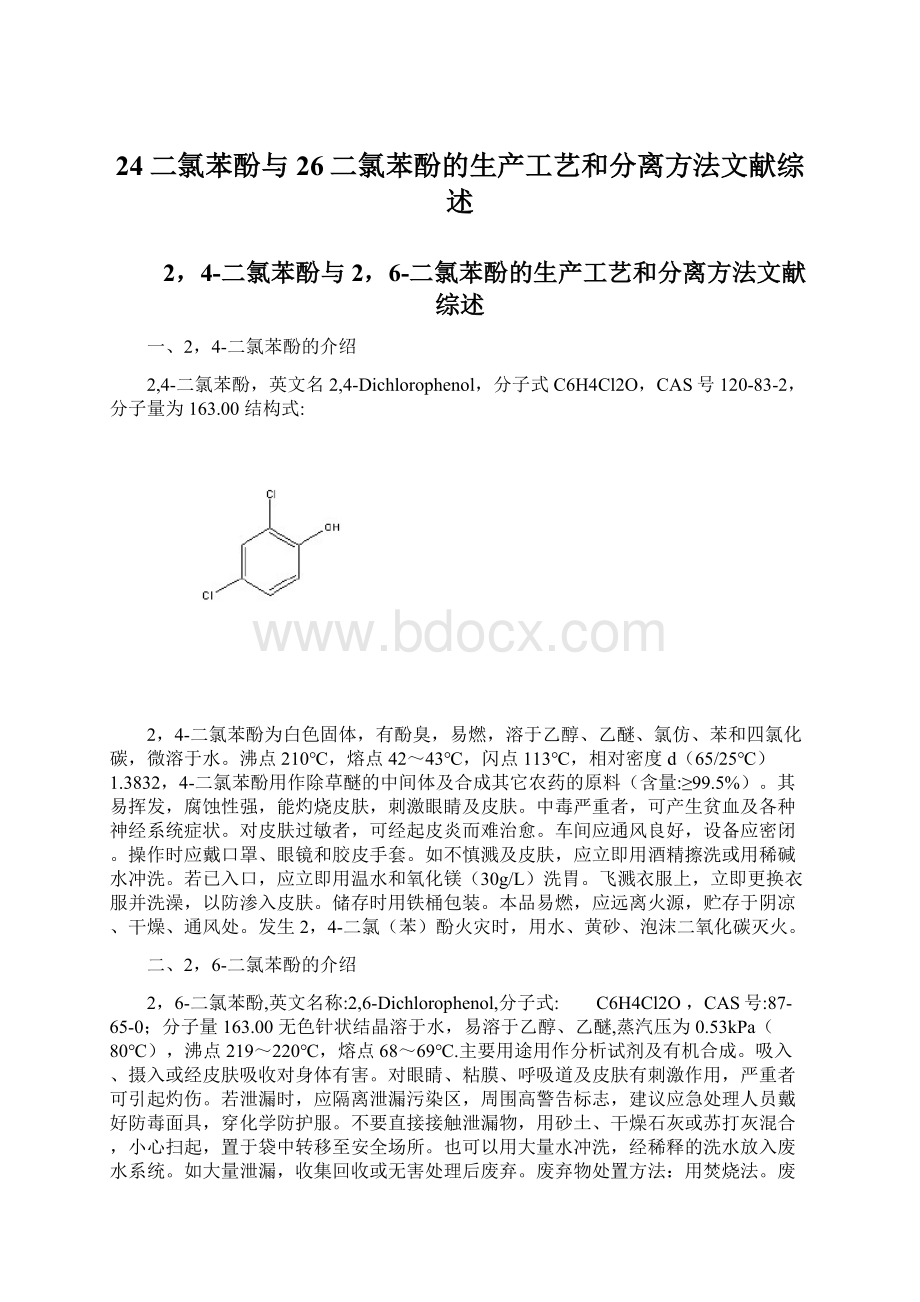
24二氯苯酚与26二氯苯酚的生产工艺和分离方法文献综述
2,4-二氯苯酚与2,6-二氯苯酚的生产工艺和分离方法文献综述
一、2,4-二氯苯酚的介绍
2,4-二氯苯酚,英文名2,4-Dichlorophenol,分子式C6H4Cl2O,CAS号120-83-2,分子量为163.00结构式:
2,4-二氯苯酚为白色固体,有酚臭,易燃,溶于乙醇、乙醚、氯仿、苯和四氯化碳,微溶于水。
沸点210℃,熔点42~43℃,闪点113℃,相对密度d(65/25℃)1.3832,4-二氯苯酚用作除草醚的中间体及合成其它农药的原料(含量:
≥99.5%)。
其易挥发,腐蚀性强,能灼烧皮肤,刺激眼睛及皮肤。
中毒严重者,可产生贫血及各种神经系统症状。
对皮肤过敏者,可经起皮炎而难治愈。
车间应通风良好,设备应密闭。
操作时应戴口罩、眼镜和胶皮手套。
如不慎溅及皮肤,应立即用酒精擦洗或用稀碱水冲洗。
若已入口,应立即用温水和氧化镁(30g/L)洗胃。
飞溅衣服上,立即更换衣服并洗澡,以防渗入皮肤。
储存时用铁桶包装。
本品易燃,应远离火源,贮存于阴凉、干燥、通风处。
发生2,4-二氯(苯)酚火灾时,用水、黄砂、泡沫二氧化碳灭火。
二、2,6-二氯苯酚的介绍
2,6-二氯苯酚,英文名称:
2,6-Dichlorophenol,分子式:
C6H4Cl2O,CAS号:
87-65-0;分子量163.00无色针状结晶溶于水,易溶于乙醇、乙醚,蒸汽压为0.53kPa(80℃),沸点219~220℃,熔点68~69℃.主要用途用作分析试剂及有机合成。
吸入、摄入或经皮肤吸收对身体有害。
对眼睛、粘膜、呼吸道及皮肤有刺激作用,严重者可引起灼伤。
若泄漏时,应隔离泄漏污染区,周围高警告标志,建议应急处理人员戴好防毒面具,穿化学防护服。
不要直接接触泄漏物,用砂土、干燥石灰或苏打灰混合,小心扫起,置于袋中转移至安全场所。
也可以用大量水冲洗,经稀释的洗水放入废水系统。
如大量泄漏,收集回收或无害处理后废弃。
废弃物处置方法:
用焚烧法。
废料同易燃溶剂混合后再焚烧。
焚烧炉要有后燃烧室,焚烧炉排出的气体要通过洗涤器除去有害成份。
空气中浓度较高时,应该佩带防毒面具。
紧急事态抢救或逃生时,佩带自给式呼吸器。
工作中接触时应该戴化学安全防护眼镜,穿相应的防护服,戴防化学品手套。
工作现场禁止吸烟、进食和饮水。
工作后,彻底清洗。
单独存放被毒物污染的衣服,洗后再用。
若是皮肤接触时应立即脱去污染的衣着,用肥皂水及清水彻底冲洗。
眼睛接触时应立即提起眼睑,用大量流动清水或生理盐水冲洗。
不慎吸入时应迅速脱离现场至空气新鲜处。
必要时进行人工呼吸。
就医。
若是不慎食入:
患者清醒时立即给饮植物油15~30ml,催吐,尽快彻底洗胃,就医。
对其灭火可以用雾状水、泡沫、二氧化碳、干粉、砂土。
三、2,4-二氯苯酚的生产工艺
2,4-二氯苯酚的生产方法主要有:
苯酚直接氯化法、混合酚氯化法,邻氯苯酚选择氯化法、对氯苯酚氯化法和苯酚催化氯化法五种。
1、苯酚直接氯化法(国内工业合成方法)
主反应:
主要副反应:
将1000kg苯酚放入80~90℃的热水池中,加热熔化后,利用真空抽入带盘管的1500升搪玻璃反应釜中,按每分钟7.5kg的速度通入氯气氯化,反应温度逐渐升高,通过盘管和央套冷却水将温度控制在70~75℃之间。
氯化尾气用水吸收制成含量25%左右的工业盐酸,剩余的尾气用石灰乳吸收制成造纸用漂白液。
通氯反应3小时后,逐渐降低通氯速度。
当氯化液相对密度达到1.402~1.405(40℃)时,即为氯化反应终点。
停止通氯,即可得含量90%左右的2,4-二氯苯酚。
其中含一氯酚(邻氯苯酚和对氯苯酚)≤1.5%,2,6-二氯苯酚≤8%,2,4,6-三氯苯酚≤05%。
氯化液经精溜提纯可制得含量95%的2,4-二氯苯酚。
国内生产2,4-滴系列产品的企业主要采用该工艺。
苯酚直接氯化法是国内外传统生产工艺,工艺简单,成本低,但是由于其中副产的2,6-二氯苯酚物理性质同2,4-二氯苯酚非常接近而难以分离导致产品纯度低,无法生产出纯度较高的2,4-二氯苯酚。
法国专利报道,用二苯硫醚做催化剂向苯酚通氯,当苯酚氯化转化率为72.7%时,其邻、对位比例为0.32。
如进行更深的氯化达到二氯代产物为主时,因一氯化时邻位的减少则二氯化时2,6-二氯酚也会相应变少,尽管该专利只报道到一氯化,但这种二氯化趋势还是应当看得到的。
“SulferLett”报道了与上文类似的苯酚催化氯化方法,其使用的催化剂以二丁基硫和二异丙基硫代替了二苯硫醚,以磺酰氯做氯化剂表现出较高的对位选择性,这种催化剂用于苯酚直接通氯如能有效,将为我们提供又一种新的途径。
2、混合酚氯化法
苯酚氯化制邻氯苯酚过程中,在氯化液精馏提纯邻氯苯酚(含量≥98.0%)时,剩余馏分即为混合酚,其中含邻氯苯酚≤1%,对氯苯酚≥82%,苯酚≤8%,2,4-二氯苯酚≥3%,2,6-二氯苯酚≤1%,混合酚与氯气反应可制得2,4-二氯苯酚,将混合酚抽入氯化反应釜中,从釜底通入氯气,控制氯化反应温度60±5℃,按先快后慢逐渐减慢的速度通入氯气,氯化进行3小时后,取样分析,当苯酚、邻氯苯酚,对氯苯酚含量总和≤1%时,即为反应终点,制得含量≥95%的2,4-二氯苯酚。
其中2,6-二氯苯酚含量≤3%,2,4,6-三氯苯酚含量≤1%,苯酚、一氯苯酚含量之和≤1%。
混合酚氯化法是用苯酚氯化制邻氯苯酚过程中副产的混合酚作为原料,虽然能够得到纯度较高的产品,但受邻氯苯酚市场影响,原料资源受限制。
3、邻氯苯酚氯化法
山东大学化学系以工业生产对氯苯酚过程中的副产物邻氯苯酚为原料,用无水三氯化铝和二苯硫醚做催化剂,用硫酰氯做氯化剂,在15±2℃温度范围内进行氯化反应,所要2,4-二氯苯酚达95%。
其余为2,6-二氯苯酚,未检测到2,4,6-三氯苯酚。
此法反应周期短,条件温和,对设备要求简单,环境污染少,纯度高,副产物可循环利用。
在实验室中,当SO2Cl2用量是理论量的107%左右时,反应温度为15℃左右,反应时间控制在2-2.5小时,可以制得较高纯度2,4-二氯苯酚。
此工艺具有反应周期短,操作方便,条件温和,产品纯度高等特点,是种较好的合成方法。
邻氯苯酚选择氯化法一方面受原料邻氯苯酚来源的限制,另一方面氯化后的产品中含有2,6-二氯苯酚,使产品纯度无法提高。
4、对氯苯酚氯化法
以对氯苯酚为原料,在催化剂作用下,控制氯化深度,一步合成反应式如下:
在实验室条件下,在55-60℃下,加氯苯酚量0.5%-0.8%的ZMF-1催化剂,通入理论氯气量的1.017倍的氯气,氯化反应6或7小时,其产品纯度达99%以上。
使用ZMF-1催化剂可促使对氯苯酚全部转化为2,4-二氯苯酚同时阻止2,4,6-三氯酚的生成。
用这种方法制备2,4-二氯酚可不经提纯,一次合成得到纯度为99%的2,4-二氯酚。
该方法重要的贡献在于提供了控制氯化深度的手段。
但由于对氯酚的价格昂贵,自对氯酚制备二氯酚大大增加了成本,是下游企业不易接受的。
如能结合高度对位选择的一氯化过程,将有可能得到较理想的选择性氯化手段。
5、苯酚催化氯化法
苯酚在铁催化下通氯气,在80~100℃氯化而制得。
根据资料介绍,铜的存在,特别是复合铜盐的存在能显著地提高对位的收率。
青岛天元化工股份有限公司研究所于近期进行了催化剂和反应条件的选择,已取得了阶段性成果,其直接合成纯度已达到94%左右。
四、2,4-二氯苯酚的提纯
分步结晶和精馏是主要的传统提纯方法。
分步结晶应用于氯代酚的分离有不少报道,但在处理固体物料时密闭操作难度较大,而氯代酚暴露于操作环境时有使人非常不愉快的味道甚至中毒,因此推广起来有难度。
近些年随着精馏技术的提高,即使沸点接近的物质也可以用精馏分离,一些企业已经采用精馏手段分离提纯2,4-二氯苯酚,但是氯代酚在精馏过程中长时间处于高温状态下,部分氯代酚形成的树脂状釜残液将给后处理和环境保护增加了负荷。
此外,精馏耗费大量能源,因此并不是很理想的方法。
选择制备高纯氯代酚的路线时最好结合企业实际情况从多种途径去考虑。
1、离解萃取
1.1 离解萃取过程简介
离解萃取是利用混合物各组分离解常数的不同,使一些(或一种)组分优先成盐而从原料液进入萃取体系里的另一相(一般是水相)中,而其余的一种(或一些)组分保留在原料相内,从而达到分离的目的。
这是一种离解的化学过程和萃取的物理过程相结合的分离手段。
离解萃取分离有机酸或有机碱的可能性,很早就有应用,1949年有人正式提出用“离解萃取”(dis-sociationextraction)这个术语来描述这种过程,到1971年Anwar系统地描述了离解萃取的理论和离解萃取的多级萃取过程,并提出了离解萃取连续分离有机碱的流程图〔4〕,其间涉及离解萃取分离混合氯代酚的研究也有不少。
苯酚氯化达到一定深度时,氯化产物以2,4-二氯酚为主,杂质中主要有2,6-二氯酚和2,4,6-三氯酚,邻、对氯酚含量可能不会超过1%。
2,4-二氯酚、2,6-二氯酚、2,4,6-三氯酚离解常数(×10-9)分别为18、160、380,酸性的差异会使杂质2,6-二氯酚和2,4,6-三氯酚优先成盐而进入水相,这样当物料与相互对流的有机溶液及无机碱水溶液不断接触时杂质2,6-二氯酚和2,4,6-三氯酚就逐渐转入水相,而有机相可得到较纯的2,4-二氯酚。
离解萃取有可能自混合氯代酚中分别得到各组分的高纯度产品,工艺成熟。
但其缺点是设备条件要求较高,投资相应较大,操作复杂,而且要使用大量有机溶剂和碱
2、离解萃取脱水沉淀
2.1 离解萃取脱水沉淀简介
离解萃取的化学过程是一个可逆平衡过程
如果以混合氯代酚中预计优先成盐的杂质2,6-二氯酚和2,4,6-三氯酚的摩尔当量为基础,定量加入氢氧化钠并逐渐移去全部水分,则平衡会向右移动,2,6-二氯酚和2,4,6-三氯酚会以钠盐形式在已经没有水相的条件下从有机相中沉淀出来,从而达到分离提纯的目的,可制得较纯的2,4-二氯酚。
3、吸附分离
3.1简介
吸附分离氯代酚是利用吸附剂对混合氯代酚中的一种或多种具有选择性的吸附性能,使一些酚吸附到沸石吸附剂上,而另一些酚,不易被吸附则较先由淋洗液洗脱,从而达到分离混合氯代酚的目的。
3.2沸石吸附分离2,4-二氯酚的实验
应用沸石做吸附剂分离混合氯代酚可以从含有2,4-二氯酚和2,6-二氯酚以及其它氯代酚的原料混合物中分离2,4-二氯酚或2,6-二氯酚。
实验仪器主要是一个可装80ml吸附剂的吸附器,每一个脉冲实验投入的原料液为含2,4-二氯酚和2,6-二氯酚各0.3g,正十四碳烷0.2g用解吸剂稀释到2ml。
解吸剂冲洗一定时间的吸附器以后,原料液以1.2ml/min的流速流入吸附器,1.7min以后停止原料液进入,改为解吸剂流入,解吸剂流速控制为1.2ml/min,直到色谱观察流出液中不再有原料组分,如此反复操作。
从上述实验中得到的物料的色谱图可证明:
Ca-X型沸石、Li-X型沸石表现出较好的选择吸附2,4-二氯酚的性能。
Ni-X型沸石和K-L型沸石表现出较好的选择性吸附2,4-二氯酚的性能。
沸石吸附分离氯代酚,文献报道较细,该法避免了使用碱或其它化学反应物,操作易行,设备简便,但效率低,不适宜工业化。
3.3铝-蒙脱吸附分离氯代酚
利用夹有蒙脱石的氢氧化铝即铝-蒙脱(Al-mont)做吸附剂对于2,4-二氯酚、2,4,6-三氯酚和五氯酚的混合物进行吸附,表明该吸附剂对三者有较好的选择性,其对2,4-二氯酚的吸附性远低于其它二者,当依次用水、10%丙酮和纯丙酮进行解吸时,用水即可使85%的2,4-二氯酚解吸而另二者并不能进入解吸液,用10%丙酮可使96%的2,4,6-三氯酚解吸并带出剩余的15%的2,4-二氯酚,五氯酚并不跟出来,再用丙酮可使五氯酚和剩余的4%的2,4,6-三氯酚得到解吸,表现出了较好的分离效果,对该法更深入的研究有可能引出一个较经济的氯代酚的分离方法。
制备高纯度低成本氯代酚是市场形势决定的氯代酚产业发展趋势,本文介绍了几种制备高纯氯代酚的方法。
这些方法中离解萃取和脱水沉淀技术较为成熟,但设备复杂操作难度大。
吸附分离技术工艺简单,但效率低,不适宜工业化。
而最合理最值得研究的技术应当是定向催化氯化技术。
对氯酚的制备可尽快应用定向催化氯化提高对位比例,降低对氯酚的成本,同时进一步研究二氯化的定向催化氯化以得到高纯度的二氯酚,这是方向,但对于邻对氯酚的分离以及对于那些对各种氯代酚都有需求或销售能力的企业和那些研究开发能力较弱而操作经验丰富的企业仍可采用离解萃取和吸附分离方法得到各种不同的氯代酚。
总之,应结合企业的状况和产品结构特点选定技术改造方向。
浙江工业大学金志敏、胡来文、杨振、陈刚2009年12月29日申请了《一种分离2,4-二氯苯酚和2,6-二氯苯酚的方法》的专利,专利号:
200910156611,该发明公开了一种分离2,4-二氯苯酚与2,6-二氯苯酚的方法,所述的方法为:
将2,4-二氯苯酚和2,6-二氯苯酚的混合物溶于有机溶剂中,加入碱性有机物,在40~80℃温度下搅拌反应,至反应液澄清,反应结束,反应液冷却后,静置析出晶体,过滤得到滤饼A和滤液A,2,4-二氯苯酚留在滤液A中,滤饼A为2,6-二氯苯酚粗品;所述碱性有机物为三乙烯二胺、吗啉、哌嗪、乙基哌嗪或甲基哌嗪;所述有机溶剂为乙醇、甲醇、丙酮或乙酸乙酯。
该发明分离的效率比较高,只需要一次结晶,2,4-二氯苯酚的总收率为90%~95%,纯度96%~99%,2,6-二氯苯酚的总收率为77%~89%,纯度90%~99%,而且操作简单,重复性好,实施成本低,有利于工业放大。
五、2,6-二氯苯酚的生产工研究
2,6-二氯苯酚是一种用途广泛的有机中间体,它的合成方法很多,但都不能令人满意。
无催化剂存在时用苯酚或2-氯酚为原料直接氯化,生成2,6-二氯苯酚和2,4-二氯苯酚的几率相等,且不能避免2,4,6-三氯苯酚的生成,目的物产量很低,且分离困难。
文献中其他几种主要方法的合成路线可示意如下:
①苯酚→4-羟基苯磺酸→3,5-二氯-4-羟基苯磺酸→2,6-二氯苯酚(最高产率70%)。
②4-氨基苯甲酸→重氮盐→4-羟基苯甲酸→3,5-二氯-4-羟基苯甲酸→2,6-二氯苯酚(59%)。
③4-硝基苯酚→2,6-二氯-4-硝基苯酚→2,6-二氯-4-氨基苯酚重氮盐→2,6-二氯苯酚。
④4-羟基苯甲酸乙酯→3,5-二氯-4-羟基苯甲酸乙酯→3,5-二氯-4-羟基苯甲酸→2,6-二氯苯酚(77%)。
这些方法虽然都不同程度地存在着合成路线长、工艺复杂、产率较低或原料不易得到等缺点,但长期以来未见有重大突破性改进的报道。
国内系采用1/4法进行工业化生产。
我们曾用对一轻基苯甲酸路线制得2,6-二氯苯酚,但该法需用三乙醇胺脱梭,在工业生产上成本较高。
为此,探索新的合成方法具有重要意义.本文以苯酚和丙酮为原料,经三步反应制得2,6一二氯苯酚.其合成路线如下:
苯酚在甲苯溶液中,以浓硫酸作为催化剂和脱水剂,以硫基乙酸为助催化剂,与丙酮在常温下缩合制得双酚A
(2)。
再以l,2一二氯乙烷为溶剂,与氯气作用得四氯双酚A(3)。
然后在三氯化铝催化下,脱烃制得2,6一二氯苯酚(l)[2〕。
总收率为71.4%~73.1%(以苯酚为基准计算)。
a.双酚A的制备要保持高转化率,加料次序很重要.最有效的方法是向苯酚与硫酸混合液中滴加丙酮,并适当控制反应速度.苯酚过量对抑制副反应有利,并得较纯产品.逐渐滴加丙酮,虽反应原料苯酚与丙酮的总比例保持不变,但反应的每一瞬间都使苯酚处于超量状态.因而能防止丙酮分子间的缩合发生.
b.缩合反应中,硫酸作为催化剂与脱水剂,起着十分重要的作用.为使双酚A得到好收率,所用硫酸浓度的最佳范围是70%一78%.随着反应的进行,硫酸被产生的水稀释,导致反应速度降低.当硫酸浓度低于60%时,几乎不发生缩合反应.所以,在反应过程中,可补加浓硫酸,使硫酸浓度恒定在73%一74%.
c.双酚A氯化时应严格忌水.否则,双酚A分子上的甲基会发生氯化.双酚A与氯气较适宜的比例为l:
4一l:
4.5.氯化反应的温度低于30℃以下时,反应速率很慢,时间长,收率也不理想.温度高于40℃以上时,产生的副产物较多.
d.氯化反应所用的溶剂,以用环己烷作溶剂时收率较高[3j.但操作条件难于把握,极易闪燃烧料.需在反应过程中通入N:
才能使反应正常进行.我们改用l,2一二氯乙烷为溶剂,达到了使用环己烷的收率.同时,使该反应操作简便,安全.
e.氯化反应的氯化剂,除了用氯气外,还可用磺酞氯等.但反应条件要剧烈一些,不易控制,使苯环上继续氯化,造成副反应.
f.脱烃反应所用溶剂除苯外,亦可用甲苯、二甲苯和三甲苯.其中用甲苯和二甲苯时的收率与用苯时的收率相近;用三甲苯时收率相对较低.所用催化剂除了三氯化铝外,我们在相同反应条件下用三氯化铁作催化剂,亦制得了
(1),但产品色泽和收率不太理想.
9.脱烃反应的温度以切一50℃为宜,温度过高容易产生副反应,影响收率.温度过低则脱烃反应难以进行.我们曾按本法在80一90℃进行脱烃反应,结果(l)的收率仅达43%.在20~30℃进行脱烃反应,从反应液中未分离出
(1).