飞机起落架故障分析.docx
《飞机起落架故障分析.docx》由会员分享,可在线阅读,更多相关《飞机起落架故障分析.docx(15页珍藏版)》请在冰豆网上搜索。
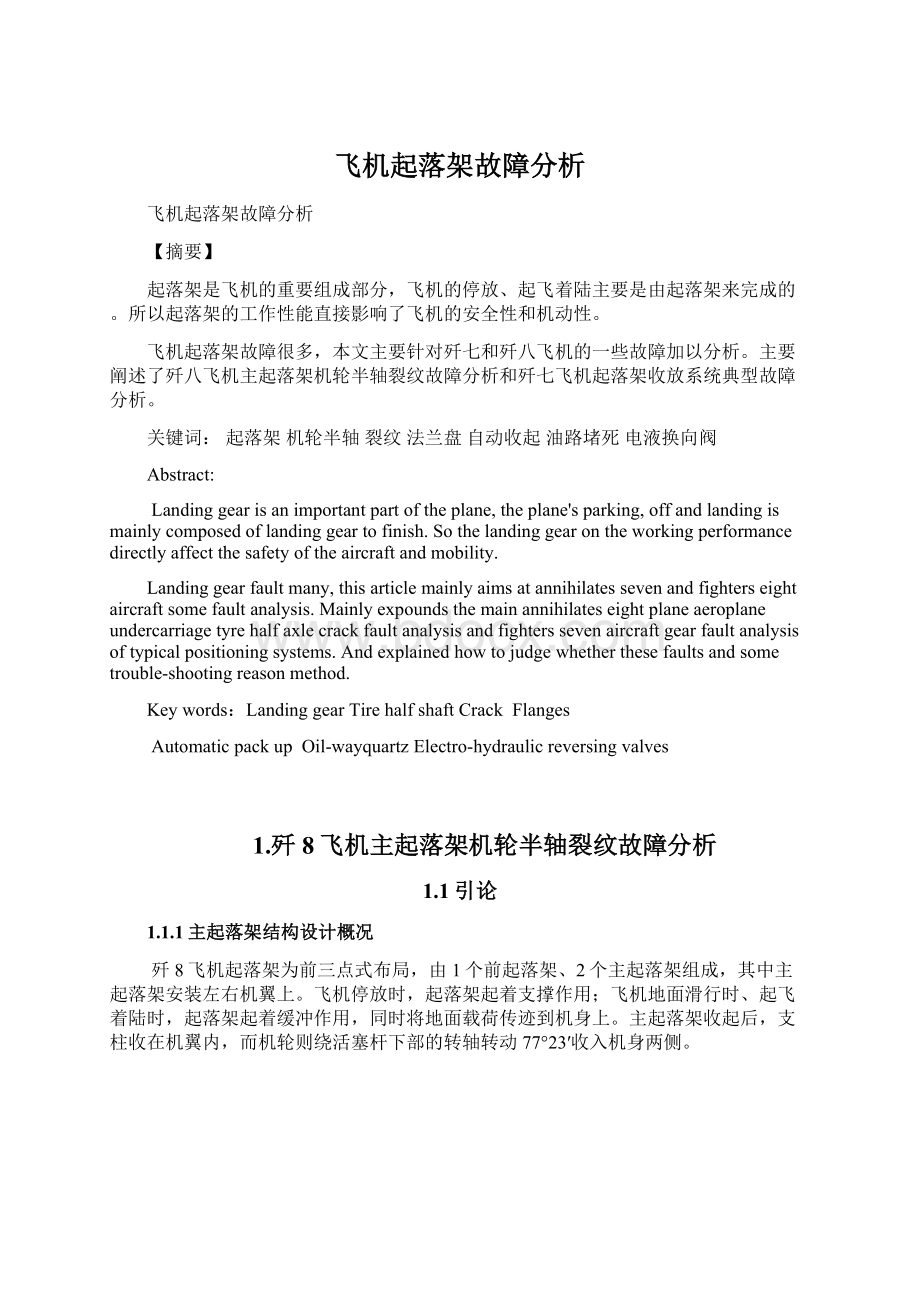
飞机起落架故障分析
飞机起落架故障分析
【摘要】
起落架是飞机的重要组成部分,飞机的停放、起飞着陆主要是由起落架来完成的。
所以起落架的工作性能直接影响了飞机的安全性和机动性。
飞机起落架故障很多,本文主要针对歼七和歼八飞机的一些故障加以分析。
主要阐述了歼八飞机主起落架机轮半轴裂纹故障分析和歼七飞机起落架收放系统典型故障分析。
关键词:
起落架机轮半轴裂纹法兰盘自动收起油路堵死电液换向阀
Abstract:
Landinggearisanimportantpartoftheplane,theplane'sparking,offandlandingismainlycomposedoflandinggeartofinish.Sothelandinggearontheworkingperformancedirectlyaffectthesafetyoftheaircraftandmobility.
Landinggearfaultmany,thisarticlemainlyaimsatannihilatessevenandfighterseightaircraftsomefaultanalysis.Mainlyexpoundsthemainannihilateseightplaneaeroplaneundercarriagetyrehalfaxlecrackfaultanalysisandfighterssevenaircraftgearfaultanalysisoftypicalpositioningsystems.Andexplainedhowtojudgewhetherthesefaultsandsometrouble-shootingreasonmethod.
Keywords:
LandinggearTirehalfshaftCrackFlanges
AutomaticpackupOil-wayquartzElectro-hydraulicreversingvalves
1.歼8飞机主起落架机轮半轴裂纹故障分析
1.1引论
1.1.1主起落架结构设计概况
歼8飞机起落架为前三点式布局,由1个前起落架、2个主起落架组成,其中主起落架安装左右机翼上。
飞机停放时,起落架起着支撑作用;飞机地面滑行时、起飞着陆时,起落架起着缓冲作用,同时将地面载荷传迹到机身上。
主起落架收起后,支柱收在机翼内,而机轮则绕活塞杆下部的转轴转动77°23′收入机身两侧。
图11-1
主起落架为支柱式结构,由缓冲支柱、带刹车机轮、收放作动筒、转轮机构、上位锁、终点开关和护板等组成,如图11—1所示。
其中缓冲支柱主要是由外筒、活塞杆、机轮半轴、扭力臂和装于支柱内部的柱塞式缓冲器所组成。
由锻铝合金制造的带刹车的机轮即安装在机轮半轴上。
轮轴的一端制有接头,与活塞杆下端耳片铰接,并制有连接转轮机构的耳片。
轮轴上还制有千斤顶顶窝和安装传递撞击载荷的止动螺栓的轴孔。
早期歼8飞机的支柱外筒、活塞杆、轮轴等主要受力件均采用超高强度钢GC4(40CrMnSiMoVA)模锻件制造,并进行喷丸强化及直接涂漆表面处理。
在后续机型中,支柱外筒、活塞杆、轮轴等主要受力件采用了更为先进的超高强度钢300M(40CrNi2Si2MoVA)模锻件制造,并进行喷丸强化及镀铬—钛、涂漆的表面处理和表面防护。
GC4钢是超高强度钢,具有良好的工艺性能和综合力学性能,对缺口和氢脆有较高的敏感性。
热压力加工成形性能良好,但对过热较敏感,不允许采用气焊和镀锌工艺。
300M钢也是一种中碳低合金超高强度钢,具有高淬透性,淬火加低温回火后强度达1960MPa,兼有优良的横向塑性、断裂韧度、抗疲劳性能,但对缺口和氢脆也有较高的敏感性,一般不推荐焊接。
无论是GC4钢还是300M钢,由于对应力集中的敏感性,所以在零件设计时,尽可能选用大的截面过渡半径,并用选用较小的粗糙度值,保持零件表面光滑。
此外,在生产和使用中要严格控制热处理、表面处理等工艺过程,防止产生氢脆。
对于GC4钢制造的机轮半轴,早期机型机轮半轴寿命为3000多个起落,后续机型机轮半轴寿命4000多个起落,并规定在弟二次大修时更换机轮半轴,载荷谱中没有考虑腐蚀因素。
1.1.2主起落架机轮半轴故障概况
歼8后续机型某架飞机在夜航第二个起落着陆过程中,当距跑道端头550m时,右侧主机轮及刹车组件脱离飞机,右主起落架机轮半轴折断、支柱着地,活塞杆连接机轮半轴耳片处和机轮半轴下表面磨损约15mm,飞机其他部位无损伤。
该右主起落架已使用了909个起落。
机轮半轴从法兰盘内外两侧断为3截,法兰盘外侧轮轴断开不规则,呈45°角;法兰盘内侧轮轴断口截面比较平整垂直.
在歼8飞机大修时,在主起落架机轮半轴上连续发现裂纹,这些机轮半轴起落次数约在1400个起落左右。
在普查中陆续发现,约有23%的飞机机轮半轴出现裂纹,其中近61%起落次数在1300起落以上,近20%在1000—1300起落之间,近19%在1000起落以下。
裂纹发生的部位在机轮半轴法兰盘外圆根部倒角变截面处,具体在安装止动螺钉的凹面台阶背面法兰盘弟1孔附近的变截面处角度α的范围内,见图11—3。
图11-3
裂纹方向均沿着变截面的交界线,裂纹长度最短的为3mm,最长的为80mm。
在出现裂纹的这些机轮半轴上未发现锈蚀情况。
1.2主起落架机轮半轴失效分析
1.2.1主起落架机轮半轴受力分析
机轮半轴在起落架上的安装及其结构如图11—4所示。
飞机在起飞、着陆、滑行、刹车和转弯等情况下,所有地面传来的载荷及飞机着陆接地时产生的撞击能量均通过机轮半轴传到活塞杆上。
应力分析结果表明,歼8机种主起落架机轮半轴的应力较高
图11-4
机轮刹车装置借助9个螺栓将刹车壳体安装在轮轴的法兰盘上,法兰盘R2圆角处与机轮刹车壳体有配合关系,刹车壳体该处倒角尺寸为2.5mm×45°。
机轮半轴的法兰盘主要承受飞机刹车时产生的扭矩,裂纹所在处的第1螺栓孔在刹车过程中受力较大,并且在R2圆角处的应力集中加大了剪切作用(图11-5);
图11-5
另外飞机着陆时机轮着地瞬间,地面载荷分别作用机轮垂直向上的载荷和逆航向载荷,二者的合力在α扇形区内作用给半轴,对其根部形成剪切和弯曲作用。
上述3种载荷传至半轴根部,必然会产生较大的工作应力。
再考虑R2圆角多大应力集中因素,其应力水平还将大幅度提高。
正是作用在R2圆角处的剪应力和弯曲正应力的共同循环作用,结果在该处产生疲劳裂纹。
1.2.2机轮半轴裂纹检测及断口分析
1外场机轮半轴断裂检查
目视观察,机轮断成3部分,法兰盘内侧轮轴断口比较平直,沿法兰盘R2处有近一周的封闭裂纹。
封闭裂纹断口为疲劳断口形貌特征,疲劳源为线性多源(周向沿加工痕迹长约25mm)。
源区位于轮轴法兰盘第一安装孔附近的内侧下方R2处,源区局部有擦伤,源区附近未发现明显的冶金缺陷。
疲劳裂纹从左下方沿法兰盘圆周方向逆时针扩展了300余度后,分成两叉,一叉沿法兰盘外侧轮轴快速扩展,另一叉沿法兰盘内侧轮轴快速扩展。
断口上疲劳弧线、放射棱线明显,粗大的放射线指示出疲劳扩展方向,端口上有多条明显的疲劳弧线。
在扫描电镜下观察,在源区附近和扩展区均可见到韧窝带或局部疲劳条带等疲劳微观特征,大部分区域为韧窝形貌。
基于上述观察结果,初步判断轮轴断裂属于高应力低调疲劳断裂。
轮轴由GC4钢模锻制造加工。
在法兰盘部位沿模锻件纵向切取试样进行测评,平均强度值符合设计要求(190±10Kgf/㎜²),且偏于上线,见表11—2。
表11—2显微硬度及换算值
序号
HVO.2
HRC(换算值)
强度值(换算值)/MPa
图样要求值/MPa
1
562
53
1928
1862±100
2
562
53
1928
3
577
54
2004
4
557
52.8
1921
平均值
564.5
53.2
1940
注:
表中HV指维氏硬度,0.2表示测量冲击压力为0.2Kgf。
对照国标GB10561(钢中非金属夹杂物显微评定方法),检测样品的硫化物等级为0.5级,氧化物夹杂等级为1级,夹杂物总和为1.5级,符合技术要求。
经检测,样品晶粒度等级为7.5级,符合技术要求。
用4%的硝酸酒精溶液侵蚀样品,在400倍显微镜下观察组织,金相组织为正常的淬火、回火组织。
化学成分检测结果见表11—3,其中碳含量偏于上线。
表11—3化学成分分析结果wt%
类别
C
Mn
Si
Cr
Mo
V
S
P
Al
测量值
0.42
0.98
1.31
1.36
0.53
0.08
0.002
0.021
0.03
标准值(YB1209—1983)
0.36
~
0.42
0.80
~
1.20
1.20
~
1.60
1.20
~
1.50
0.45
~
0.60
0.07
~
0.12
≤
0.025
≤
0.025
≤
0.10
经检测,法兰盘腹板与机轮表面粗糙度、安装孔直径、法兰盘厚度、过渡圆角等均符合设计要求。
由此可知,零件材质、尺寸符合设计要求;源区有磨损,附近未冶金缺陷和外来损伤,裂纹较平直,有氧化特征,为疲劳断口形貌。
疲劳源特征为线性多源,裂纹始于轮轴法兰盘第一安装孔附近的内侧下方R2处,属于高应力低周疲劳断裂。
2大修厂机轮半轴裂纹检查
经外观检查,发现长约45mm、最深处约2mm的裂纹,为穿透壁厚,裂纹位置同图11—2。
断口比较平直,有氧化特征,为多源疲劳断口形貌。
断口上有多条明显的疲劳弧线,并有较粗大的放射棱线,指向疲劳裂纹的扩展方向。
疲劳源特征为线性多源,源区位于轮轴法兰盘第一安装孔附近的内侧下方R2处。
源区局部有磨损,源区附近未见冶金缺陷。
经低倍检查,裂纹位于零件法兰盘内侧轮轴前端第一安装孔R2尺寸根部,沿法兰盘内侧轮轴R2处延伸。
裂纹具有台阶状线源疲劳开裂特征。
裂纹处未见划伤、碰伤以及明显的加工痕迹。
在扫描电子显微镜下观察断口,发现在源区附近及扩展区均存在韧窝带或局部疲劳条带等疲劳微观特征,其他大部分区域为韧窝结构,断口上疲劳部分有氧化特征。
用3%的硝酸酒精溶液浸蚀金相试样,在400倍显微镜下观察组织,基体金相组织为正常的淬火、回火组织。
裂纹较平直,开口度约为5um,从裂纹形貌上看具有疲劳开裂的特征。
在法兰盘部位沿模锻件纵向切取试样测试,平均强度值偏上线(显微硬度值换算后与实际强度值有一定的偏差),符合设计要求。
边缘显微硬度测试结果表明,零件边缘脱碳深度符合设计要求。
显微硬度测试结果见表11—4.
表11—4显微硬度测试结果
项目
距边缘25um(HKO.5)
距边缘50um(HKO.5)
距边缘75um(HKO.5)
中心(HKO.5)
1
496
540
556
569
2
499
543
553
566
3
497
542
557
571
4
495
543
552
568
5
493
541
554
570
平均值
496
541.9
554.4
5611.8
化学成分测试结果符合零件材质要求,见表11—5。
表11—5化学成分分析结果
类别
C
Mn
Si
Cr
Mo
V
S
P
Al
测量值
0.40
0.99
1.33
1.35
0.50
0.09
0.003
0.002
0.05
标准值(YB1209—1983)
0.36
~
0.42
0.80
~
1.20
1.20
~
1.60
1.20
~
1.50
0.45
~
0.60
0.07
~
0.12
≤
0.025
≤
0.025
≤
0.10
经检测,法兰盘腹板与机轮表面粗糙度、安装孔直径、法兰盘厚度、过渡圆角等均符合设计要求。
由此可知,零件材质、尺寸符合设计要求;源区有磨损,附近未见冶金缺陷和外来损伤,裂纹较平直,有氧化特征,为疲劳断口形貌。
疲劳源特征为线性多源,裂纹始于轮轴法兰盘第一安装孔附近的内侧下方R2处,属于高应力低周疲劳断裂,同外场断裂件检查结果。
1.3主起落架机轮半轴疲劳试验结果
1.3.1机轮半轴疲劳试验破坏部位
歼8后续机型主起落架疲劳试验时,机轮半轴在20000多次起落时发生断裂,折合使用寿命为4000多个起落。
断裂位置是根部销钉孔处,如图11—6所示。
从中可以看出,与外场飞机发现裂纹的部位完全不同。
图11-6
1.3.2试验结果与使用情况差异分析
机轮半轴在疲劳试验和外场使用中所暴露的破坏部位、寿命存在较大差别,主要因为:
(1)机轮半轴在疲劳试验模拟与飞机真实机轮的刚度存在差别
疲劳试验用假机轮与真实机轮不同。
前者采用钢材料制造,由焊接拼合制成,其刚度较大;而后者使用锻铝、钢等多种材料制成,轮毂上套装轮胎,其刚度比疲劳试验所用的假机轮刚度小的多。
因此,在实际使用中,由于真实机轮刚度较小,容易产生变形,会使侧向载荷的能力较弱。
而疲劳试验所用的假机轮由于刚度较大,不存在变形,侧向载荷直接通过轮轴传走,不会传到法兰盘上。
因此,疲劳试验中法兰盘的应力水平低于外场使用情况,这是出现二者寿命差异的因素之一。
(2)外场刹车载荷谱偏重
虽然疲劳试验采用的是实测过载谱,但由于使用情况的不断变化,实测的刹车谱已经不能反映出所有外场飞机使用刹车的实际情况。
统计数据表明,后续机型在外场使用中,超过正常着陆重量的着陆次数已达到23%左右。
由于主要在着陆滑跑过程中使用刹车,随着超过正常着陆重量着陆次数的增多,飞机使用刹车也比过去严重,因此对于机轮半轴法兰盘使用也比过去严重,导致其应力偏高、寿命偏短。
(3)超常着陆所产生的冲击载荷和摩擦载荷对半轴根部和法兰盘产生影响
飞机超正常着陆时,地面的垂直冲击载荷和摩擦载荷的合力通过机轮传给半轴,对半轴根部产生弯曲和剪切作用,使其应力水平进一步提高;同时,使机轮和半轴产生变形的趋势增大,对法兰盘的侧向作用载荷加大,使其应力水平同时增加。
而这些实际情况在疲劳试验中未得到真实模型。
1.3.3外场飞机使用特点分析
对外场4家单位的飞机起飞着陆情况进行调查发现,超过最大着陆重量的着陆情况没有发生过,而超过正常着陆重量的着陆次数已达到20%左右。
考虑到少数起落中还要求机身挂副油箱。
机翼中挂点挂1枚或者2枚导弹等因素,保守估计,超过正常着陆的起落次数将会达到23%左右。
而通常要求飞机超过正常着陆重量着陆的起落次数不应超过10%。
1.3.4主起落架机轮半轴失效分析结论
(1)本文b中所述的机轮半轴断裂个案与外场普查所发现的机轮半轴裂纹性质相同,均属于高应力低周疲劳断裂。
裂纹是在使用过程中产生的,其萌发和扩展经历一段循环周期。
(2)在实际使用中,因机轮和半轴会出现弹性变形,导致法兰盘上产生侧向载荷;23%的超过正常着陆重量着陆的起落次数会进一步增大侧向载荷作用,同时使半轴根部和法兰盘的应力水平提高。
(3)半轴在法兰盘根部过渡圆角处存在应力集中,导致该处应力水平提高。
(4)疲劳寿命实验中机轮半轴的考核结果未能真实模拟实际使用情况。
(5)半轴、法兰盘与机轮的材质、几何尺寸、表面粗糙度等均符合设计要求,未发现意外损伤。
1.4主起落架机轮半轴结构设计改进
1.4.1半轴结构设计改进原则
(1)基于成本和周期考虑,结构设计改进仅局部于机轮半轴和机轮,而不涉及更多零件组件的设计更改。
(2)对半轴结构细节进行设计改进,提高其抗疲劳开裂能力。
机轮进行协调性更改。
(3)加强对设计改进后机轮半轴的疲劳特征评定。
(4)对机轮半轴的设计改进方案不应涉及其锻造模具的更改,以节省周期和成本。
(5)经设计改进后,新的机轮半轴能够在外场条件下方便更换,以尽快满足外场部队的需要。
(6)加强对原主起落架机轮半轴的监控,保证飞机的使用安全。
1.4.2半轴结构细节设计改进
(1)将机轮半轴法兰盘厚度增加1mm,根部圆角半径增加1.5mm;
(2)将连接机轮半轴法兰盘和机轮刹车壳体的螺栓长度增加1mm;
(3)将机轮刹车壳体与半轴法兰盘配合部位的倒角宽度增加2mm;
(4)对喷丸工艺参数进行优化选取,提高半轴结构细节工艺强化的寿命增益。
1.5经验教训
1.5.1设计载荷谱、变形预测与实际使用情况相符
在机轮半轴故障整治过程中,通过深入分析发现,载荷谱中未计及23%超常着陆载荷、着陆瞬间由机轮传给半轴的冲击载荷和摩擦载荷的影响;在外力作用下,机轮和半轴的弹性变形导致法兰盘变形协调而产生附加作用力。
这些因素在设计载荷谱中均未考虑,与飞机主起落架的实际使用情况不符,导致机轮半轴、法兰盘的工作应力水平过高。
如果机轮半轴应力水平过高、细节设计考虑不够充分,就容易发生低周疲劳破坏,即高应力、低循环疲劳破坏。
1.5.2完善细节抗疲劳设计和强化工艺是提高结构抗疲劳开裂的重要技术途径
改进细节设计,可有效地消除刚度突变、降低应力集中程度,进而控制薄弱细节的工作应力水平,达到延长结构疲劳寿命的目的。
将机轮半轴法兰盘厚度增加1mm、根部圆角半径增加1.5mm、机轮刹车壳体与半轴法兰盘配合部位的倒角宽度增加2mm都是为改进细节设计所采取的具体措施。
合理的工艺强化措施可有效地获取疲劳寿命增益,对机轮半轴的喷丸工艺参数、喷丸部位进行优化选取,是为了完善半轴结构细节工艺强化措施。
1.5.3地面疲劳试验验证刚度模拟要真实
在主起落架疲劳试验中,机轮刚度模拟与飞机实际使用情况相差较大,由于结构变形协调,必然产生彼此牵连的附加载荷,对半轴结构细节疲劳特性可能会产生影响。
因此,地面疲劳试验所暴露的疲劳开裂部位、周期、形态等与真实情况可能存在差异,亦即由于模拟不够真实,可能导致地面疲劳考核试验的结果不能完全反映飞机的使用情况。
因此,地面疲劳试验验证模拟要尽量真实,这样才能有效暴露疲劳薄弱部位,达到验证或预测结构寿命的目的。
1.5.4制定合理的检修周期是确保使用安全的重要措施
如前面A-b所述,在909个起落时右主起落架半轴首次发生断裂事故;大修时发现机轮半轴上裂纹的起落次数约在1400个起落左右;普查中发现,约有23%的飞机机轮半轴出现裂纹,其中近61%起落次数在1300个起落以上,近20%在1000—1300个起落之间,近19%在1000个起落以下。
这些裂纹明显对飞机安全使用构成威胁,甚至是巨大隐患。
只有制定并执行安全检查,及时发现并排除半轴裂纹,才能保证飞机的使用安全。
2歼七飞机起落架收放系统典型故障分析
2.1歼七飞机前起落架自动收起的故障研究
起落架收放系统是飞机的重要组成部分,此系统的工作性能直接影响到飞机的安全性和机动性.
改进设计飞机起落架收放系统主要用于控制起落架的收上与放下,控制主起落架舱门和前起落架舱门的打开与关闭,是飞机一个重要的系统,其能否正常工作将直接影响飞行安全。
因此对该系统的维护和对所出现的故障进行分析研究,并进行有效的预防就显得十分重要。
某单位在对某新型飞机做出厂试飞准备时,当机组人员接上地面压力源和电源进行该机的停机刹车压力调整时,在供压13min后,前起落架开始缓慢收起,飞机机头失去支撑最终导致机头接地,造成雷达罩和前机身02段蒙皮撕裂、结构损坏和前起落架变形等严重后果。
本文将对前起落架自动收起的故障进行分析研究,并在此基础上针对性地提出预防措施。
2.1.1起落架收放控制原理分析
图2-1前起落架收放系统原理图
前起落架收放系统原理如图2-1所示。
正常收起落间隙时,起落架收放手柄(下简称手柄)处于收上位时,电液换向阀l使高压油进入收上管路,放下管路b回油管路相通。
在高压油的作用下,下位锁作动筒的活塞杆缩进,下位锁打开。
另一路高压油一方面液控单向阀13打开,使舱门作动筒10、12的回油略沟通;另一方面油通过限流活门9进入收放作动筒,使活塞杆伸出,起落架收起,作动筒8的回油经脚向活门7、应急转换活门4、电液换向阀1和应急排油活门2流入油箱。
当起落架收好后,协调活门11压通,高压油进入舱门作动筒lO、12的收上腔使舱门收起。
当手柄处于放下位置时,来油与放下管路接通,收上管路与回油路相通,起落架放下。
在系统中还设有地面联锁开关,当飞机停放时,联锁开关自动断开电液换向阀的电路,此时即使将手柄置于收起位置,电液换向阀也不会工作,从而防止了地面误收起落架。
2.1.2起落架自动收起原因分析
由起落架收放控制原理知道,前起落架放下位置是由带下位锁的后撑杆来保持的,所以要使前起落架收起,必要条件是下位锁开锁。
而下位锁开锁有两种情况:
第一种是机械原因,即放下起落架时下位锁处于假上锁状态,在维修和使用过程中受到某种外力扰动而开锁;第二种是液压原因,即有液压油进入下位锁开锁作动筒,使作动筒活塞杆缩进导致下位锁开锁。
而外部检查和事后的收放检查均未发现下位锁有假上锁的现象。
因此前起落架自动收起是由液压方面的原因引起的。
而由液压原因引起下位锁开锁的因素很多。
当电液换向阀工作不正常使来油与收上管路相通,或者联锁开关故障,地面又误将手柄置于收上位置,在电液换向阀工作时,当给飞机供油压时,都会使下位锁开锁。
但这两种情况会使前起落架以较快的速度收起而不会缓慢收起,另外也会同时收起主起落架。
但这与事故发生时的实际情况不符,因此基本可以排除。
2.2.1电液换向阀性能不良
起落架电液换向阀用于起落架收放管路的控制,是一种三位四通电液阀,当手柄在中立位置时(不通电),电液换向阀处于中立位置,
图2-2电液换向阀中立位置(断电)
此时供油路堵死,起落架的收、放管路均与回油路相通,如图2-2所示。
由于滑阀与阀套之间都有径向间隙6,由6形成两个相同的矩形节流缝隙,此缝隙的节流面积为A=W8,由于形6,且通过此节流口的流量很小,雷诺数m也很小,流动状态属于层流,故通过此节流口的流量Q为:
式中:
——节流口两侧压力差;
——动力粘度系数;
——节流口面积梯度。
则此时,通过2个节流口处的流量为:
式中:
——主液压系统供油压力;
——回油管路压力。
由上式可知,泄漏量的大小主要由节流口面积梯度形和径向间隙6确定,当间隙6越大,则泄漏量越大。
而形的大小主要与阀芯的直径有关,直径越大梯度越大;6的大小主要与阀口的形状、制造工艺和加工质量等有关,当设计合理、工艺水平和加工质量高、滑阀和阀套之间没有偏心时,则6就小。
如果是新阀,径向间隙小,故泄漏量也小;如果是旧阀,由于控制边被磨损,泄漏面积增大,则泄漏量也增大。
为测定泄漏量的大小,拆下电液换向阀,堵住通向作动筒的两个接头,在供压接头处.加液压20.59MPa.在回油接头处接上量杯。
3min后,在回油接头处漏油量为45mL,远大于所规定的不超过20mL的要求。
电液换向阀泄漏示意图如图2-3所示。
图2-3电液换向阀泄露示意图
2.2.2系统不完整,回油路堵死
为了提高起落架收放系统的可靠性,在系统设计中采用了余度技术。
即当正常收放起落架失效时,飞行员可以采用冷气应急放下起落架,以保证安全着陆,如图1所示。
为防止应急放起落架时,大量液压油回到密闭增压油箱,使油箱因回油过多而引起爆破,为此在电液换向阀的回油路上安装了应急排油活门。
应急放起落架时,将收上管