精细化工论文推荐范文8篇化工论文化学论文.docx
《精细化工论文推荐范文8篇化工论文化学论文.docx》由会员分享,可在线阅读,更多相关《精细化工论文推荐范文8篇化工论文化学论文.docx(14页珍藏版)》请在冰豆网上搜索。
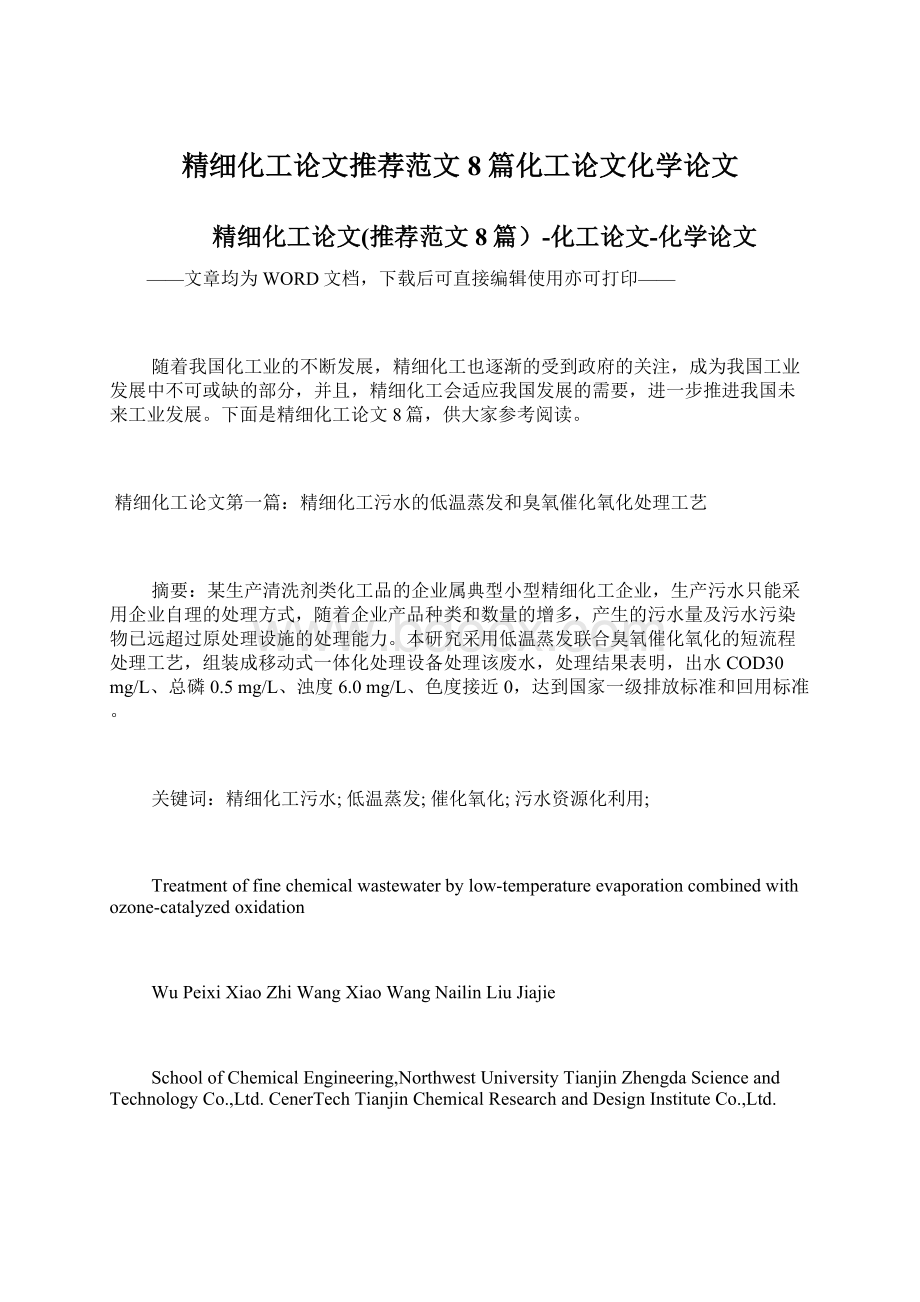
精细化工论文推荐范文8篇化工论文化学论文
精细化工论文(推荐范文8篇)-化工论文-化学论文
——文章均为WORD文档,下载后可直接编辑使用亦可打印——
随着我国化工业的不断发展,精细化工也逐渐的受到政府的关注,成为我国工业发展中不可或缺的部分,并且,精细化工会适应我国发展的需要,进一步推进我国未来工业发展。
下面是精细化工论文8篇,供大家参考阅读。
精细化工论文第一篇:
精细化工污水的低温蒸发和臭氧催化氧化处理工艺
摘要:
某生产清洗剂类化工品的企业属典型小型精细化工企业,生产污水只能采用企业自理的处理方式,随着企业产品种类和数量的增多,产生的污水量及污水污染物已远超过原处理设施的处理能力。
本研究采用低温蒸发联合臭氧催化氧化的短流程处理工艺,组装成移动式一体化处理设备处理该废水,处理结果表明,出水COD30mg/L、总磷0.5mg/L、浊度6.0mg/L、色度接近0,达到国家一级排放标准和回用标准。
关键词:
精细化工污水;低温蒸发;催化氧化;污水资源化利用;
Treatmentoffinechemicalwastewaterbylow-temperatureevaporationcombinedwithozone-catalyzedoxidation
WuPeixiXiaoZhiWangXiaoWangNailinLiuJiajie
SchoolofChemicalEngineering,NorthwestUniversityTianjinZhengdaScienceandTechnologyCo.,Ltd.CenerTechTianjinChemicalResearchandDesignInstituteCo.,Ltd.
Abstract:
Anenterprisethatproducesdetergentchemicalsisatypicalsmall-scalefinechemicalenterprise.Theproductionwastewatercanonlybetreatedbytheenterpriseitself.Withtheincreaseofproducttypesandquantity,theamountofwastewaterandwastewaterpollutantsproducedhasfarexceededthecapacityoftheoriginaltreatmentfacilities.Inthisstudy,amobileintegratedtreatmentequipmentwasassembledbyadoptingashort-rangetreatmentprocessusinglow-temperatureevaporationcombinedwithozone-catalyzedoxidation.ThetreatmentresultsshowedthattheeffluentCODwas30mg/L,totalphosphoruswas0.5mg/L,turbiditywas6.0mg/L,andchromaticitywascloseto0,meetingthenationalfirst-levelemissionstandardsandreusestandards.
精细化工工业是国民经济重要的支柱性产业,在生产过程中产生的精细化工有机废水具有成分复杂、有毒有害物质多、污染物浓度高、生物降解难度大等特征,其综合治理一直是环境领域的一大难题[1,2]。
尤其高盐、高有机污水目前处理困难,已成为制约行业发展的瓶颈。
某化工公司是一典型的小型精细化工企业,产品为工业和民用两类配方型清洗剂或消毒剂,生产方式为间歇式生产,每生产1釜产品后需对反应釜进行清洗,随着生产产品的不同,产生了酸性污水、碱性污水、含碘消毒污水3种清洗污水。
这3种污水的含盐量高、COD高、磷酸盐含量高、表面活性剂含量高、水量和水质波动大、处理难度大,消毒污水还具有色度高和含碘高的特点。
正是由于这些特点,无法直接排入园区污水处理系统,只能由企业自建污水处理设施,处理至达到园区接收标准。
该企业在生产装置投产时根据产品品种和污水特点建有1套小型污水处理设施,处理出水满足工业园污水接收标准(COD300mg/L,PO43-3.0mg/L)。
但随着产品品种增多和产量提高,污水量和水质发生很大变化,远远超过处理设施的处理能力,出水COD600mg/L,PO43-20mg/L,污泥产生量也越来越大。
而园区接收的企业排污水需达到国家一级排放标准,所以对污水处理设施进行提标改造势在必行。
根据企业目前的生产特点、污水水质以及场地的限制,本工程采用低温蒸发联合臭氧催化氧化短流程处理工艺,处理后出水COD30.0mg/L、PO43-0.5mg/L、浊度6.0mg/L、色度接近0,达到国家一级排放标准。
出水回用于工业品生产和和反应釜清洗,蒸发浓浆也回收用于工业品原料,实现了资源化利用。
1原有污水处理设施及运行状况
该企业生产装置建成投产时,产品品种少、产量小、污水量和水质波动大,3种污水每天产生量各约1.0~3.0m3,COD为270~4500mg/L、PO43-为100~370mg/L,企业依此水质条件和园区污水接收标准设计建设了处理设施,污水处理设施采用间歇式运行,过程控制相对落后,采用人工分析和控制。
1.1原污水处理设施设计参数及工艺流程
1.1.1设计参数
原处理设施设计处理量为10m3/d,设计进出水指标见表1。
表1设计进出水指标
1.1.2工艺流程
由于污水水质随产品种类不同波动较大,故原处理设施根据混合污水COD和磷酸盐质量浓度不同采用2种处理工艺:
Fenton处理工艺和PAC脱磷处理工艺。
(1)Fenton处理工艺。
当混合污水COD与磷酸盐质量浓度都超过园区接收标准时,采用Fenton处理工艺,工艺流程见图1。
图1Fenton处理工艺
由图1可知,3种污水进入污水调节池混合后,根据COD和总磷分析结果,泵入pH调节池1,用NaOH或H2SO4调节pH为3.0~5.0,然后加入FeSO47H2O,混合均匀后泵入Fenton反应池,加入H2O2,利用Fenton反应降低污水的COD,反应产生的Fe3+与PO43-结合达到脱磷的目的;待COD符合园区接收标准,将污水泵入pH调节池2,用NaOH调节pH为9.0~9.5,然后泵入中间水池,残留的Fe3+在弱碱性条件下产生沉淀,与除磷产生的污泥一起沉淀下来;中间水池清液进入清水池,用H2SO4调节pH,达标后排放,沉淀物经板框压滤机脱水,污泥外运处理,滤液则泵回pH调节池1中。
(2)PAC脱磷处理工艺。
当混合污水仅磷酸盐超过园区接收标准,COD不超标时,则采用PAC脱磷处理工艺,工艺流程见图2。
图2PAC脱磷处理工艺
由图2可知,3种污水进入污水调节池混合后,根据COD和总磷分析结果,泵入pH调节池1,用NaOH或H2SO4调节pH为6.5~7.5,然后加入PAC,混合均匀后依次泵入Fenton反应池和pH调节池2,利用PAC的絮凝作用达到脱磷的目的,在此两池中进行充分混凝反应后泵入中间水池;中间水池用作澄清池,混凝反应后的污水在其中充分澄清,出水达标后进入清液池达标排放,沉淀物经板框压滤机脱水后,污泥外运处理,滤液则泵回pH调节池1中。
1.2原污水处理设施的运行情况
原处理设施投运初期(2~3a),运行稳定、出水水质满足园区污水接收标准。
但运行过程中会产生很多含水率70%的污泥需外运处理,增加了污水处理费用。
采用人工分析和人工过程控制,也增加了劳动强度和出水水质的不确定性。
随着产品品种增加、产量提高,每天产生的污水量增至约15~20m3,水质也发生很大变化,原处理设施无法满足现污水量和水质的处理要求,主要表现为:
(1)污水量远超原处理设施的设计处理能力;
(2)3种污水的COD、磷酸盐远超原污水处理设施的设计进水水质指标。
为达园区接收标准,需进行多次Fenton处理,不仅消耗大量FeSO47H2O和H2O2,还产生大量需外运处理的污泥。
(3)污水中表面活性剂浓度高,容易产生泡沫,影响处理设施的正常运行。
2低温蒸发联合臭氧催化氧化工艺的研究及工业化实践
2.1现污水水质分析
现污水水质分析见表2。
由表2可知,3种污水呈高含盐量、高COD、高磷酸盐含量的特点,含碘消毒污水含碘量和色度大,污水污染源种类多,组成复杂。
表2现污水水质分析
2.2低温蒸发联合臭氧催化氧化处理工艺的研究
笔者根据实验研究,确定出负压低温蒸发联合臭氧催化氧化的短流程处理工艺,即在一定真空度、较低温度下,对混合污水进行蒸发预处理,蒸发出水再采用臭氧催化氧化进行深度处理,催化剂采用氧化铝基Mn-Fe-Cu负载型催化剂。
2.2.1温度和真空度对蒸发预处理效果的影响
在不同温度、不同真空度下进行蒸发预处理,对现污水的预处理结果见表3。
由表3可知,低温蒸发处理的脱磷效果明显,磷酸盐脱除率达到100%。
随着温度的升高,蒸发出水COD去除率降低,出水COD呈阶梯式逐渐升高,其中30℃升至50℃的出水COD升高得较少,而升至60℃时则急剧升高,但60℃升至70℃的出水COD升高得不多。
随蒸发温度升高,出水浊度和色度也逐渐升高,其中30℃升至40℃时,出水浊度和色度升高较小,40℃升至50℃时出水浊度和色度升高明显,50℃后出水浊度和色度几乎稳定。
表3不同温度、不同真空度下的蒸发预处理结果
2.2.2臭氧投加质量浓度对不同温度蒸馏出水深度处理效果的影响
用40、50、60℃条件下的蒸发出水作为实验用水,将蒸发出水调节pH为8.5~9.5后,采用臭氧氧化和臭氧催化氧化进行深度处理,对比2种方法在不同臭氧投加质量浓度下的深度处理效果,结果见表4。
表4臭氧氧化和臭氧催化氧化的深度处理效果对比
由表4可知,对蒸发出水进行臭氧氧化深度处理,随着臭氧投加浓度的升高,出水COD逐渐降低,浊度和色度降低明显;催化剂的使用提高了臭氧的氧化效率,COD去除率和降浊、脱色效率明显提高。
在催化剂作用下,对40℃和50℃的蒸发出水深度处理,臭氧投加质量浓度为300mg/L时,出水水质即可达到一级排放标准;臭氧投加质量浓度为400mg/L时,出水COD30mg/L,色度和浊度为0,可用作生产用水;而对60℃的蒸发出水深度处理,即使在高浓度臭氧条件下,出水也无法达到一级排放标准。
2.2.3不同温度负压蒸发处理的技术经济性分析
综合预处理和深度处理的实验结果发现,随着蒸发温度的升高,为达标排放或回用,需提高深度处理臭氧投加浓度而增大了处理成本,甚至增大了处理难度,60℃以上的蒸发出水,臭氧氧化处理已很难达到一级排放标准。
蒸发温度过低,则需提高真空度而增加动力成本,气温较高还需降温处理。
因此,30~50℃是负压低温蒸发预处理经济可行的温度范围。
对30~50℃的蒸发出水采用臭氧催化氧化深度处理,臭氧投加质量浓度为300mg/L时出水水质已达一级排放标准;臭氧投加质量浓度为400mg/L时出水水质已符合工业类产品生产用水。
因此,臭氧投加质量浓度宜控制为300~400mg/L。
2.3低温蒸发联合臭氧催化氧化一体化处理设备
将研究确定的低温蒸发联合臭氧催化氧化处理工艺组合成移动式橇装一体化处理设备,各节点水质采用在线分析,实现全过程自动控制。
一体化处理设备具有以下特点:
(1)流程短、占地少、自动化程度高;
(2)蒸发浓浆和出水回用,实现零排放,避免危废外运处理;(3)停用Fenton处理和絮凝处理,避免产生二次污泥带来的危废;(4)停用H2O2,有利于安全及企业长远发展。
2.3.1工艺流程
一体化处理设备的工艺流程见图3。
图3负压低温蒸发联合臭氧催化氧化一体化设备工艺流程
由图3可知,含碘污水在碘回收器中,利用余热(热水或废蒸汽)将含碘污水加热,使碘质升华,再采用污水作为冷却介质冷却后回收,脱碘后的污水和碱性污水、酸性污水混合进入污水缓冲罐;缓冲罐中的混合污水泵入负压蒸发装置进行蒸发处理,蒸发冷凝水流入pH调节罐1中调节pH为8.5~9.5,然后泵入臭氧催化氧化反应器中进行深度处理,浓浆回用;经臭氧催化氧化处理后的污水泵入pH调节罐2中调节pH后外排或直接回用。
2.3.2主要装置及参数
(1)碘回收器。
1台,316不锈钢,直径1.4m,高1.5m;底部设盘管式水(汽)加热管、压缩空气管,上部安装同样材质的冷凝器,污水作为冷凝器的冷却介质对升华后的碘质冷却回收;在常压、温度为45~75℃条件下运行。
(2)负压蒸发装置。
蒸发装置包括蒸发器、真空泵、供水泵、压缩机和冷凝器等部件。
蒸发器2台,316不锈钢,容积3m3;上部采用圆柱形,直径1.5m,高1.6m,内置纵向排列的盘管式加热器和自清洗组件;下部采用圆台形,便于浓浆排放;运行温度为30~50℃,运行真空度-80~-100kPa;污水由圆柱形底部采用文氏射流注入,低温蒸汽从顶部抽出。
蒸发装置工艺流程见图4。
图4负压蒸发装置工艺流程
由图4可知,在蒸发装置中,污水在一定温度和真空度下,在蒸发器中被蒸发,蒸发出的低温蒸汽进入压缩机被压缩,以提高其温度、压力、热值,然后进入冷凝器与待处理的污水进行热交换,待处理污水被加热后进入蒸发器中进行蒸发处理;蒸汽则被冷凝成水后进入下一工序。
(3)臭氧催化氧化反应器。
1台,316不锈钢,直径1.5m,高1.8m,中上部内置300mm厚氧化铝负载型颗粒催化剂;在催化剂格栅下方,臭氧及调节pH后的冷凝水分别通过布气管和布水管由下而上依次通入反应器,在反应器中还设置有污水和尾气的回流装置,自动反洗装置。
臭氧投加量为300~400g/t,反应时间为0.5~1.0h。
(4)臭氧发生器。
臭氧发生量为400g/h。
(5)pH调节罐。
316不锈钢,2个,容积2m3,带不锈钢搅拌。
2.3.3运行情况
在一体化处理装置运行时,根据生产产品种类及污水回用需要,利用原处理设施的污水调节池、2个pH调节池作为3种污水的分类应急存放池,清水池用作处理达标出水蓄水池。
自2018年10月橇装式一体化设备在现场运行以来,设备运行稳定,出水COD30mg/L、总磷0.5mg/L、浊度6.0mg/L、色度接近0,达到回用水质标准;浓浆含水率为30%~40%,回用作工业类产品原料,实现了污水和固废的零排放,一体化设备装备出水水质见图5。
图5一体化处理装置出水水质
3经济效益
原处理设施消耗化学品费用,每t污水约29.0元,年费用约10.585万元;日产生污泥量7m3,外运处理费用2500元/t,年处理费用630万元;动力费(水、电)1.25元/t,年费用4562.5元;年人工费30万元;合计671万元。
折算至目前每天20m3污水计算,则每年处理费用为1312万元。
一体化处理设备自2018年10月开始投入运行,每t污水消耗化学品费用约0.5元,年费用3650元;动力费(水、电)39元/t,年动力费用28.47万元;臭氧处理费用15元/t,年费用约10.95万元;年人工费用10万元;合计年处理费用为40.785万元。
年节约污水处理费用达1271.215万元。
一体化处理设备投入运行以来,日均回用深度处理后的污水16.0m3,年节约工业水费用4.96万元;日均回收蒸发浓浆约3.0m3,年回用产品原料费用约110万元。
低温蒸发一体化处理设备的应用,在实现了污水和固废零排放的同时,每年可通过节约和回用实现经济效益约1380.0万元。
4结论
(1)采用低温蒸发联合臭氧催化氧化工艺处理高盐、高有机物污染、成分复杂的难处理精细化工污水,出水水质可达到一级排放标准。
处理后的污水和蒸发浓浆满足生产用水水质和工业产品原料标准,将污水和浓浆回用,实现企业污水零排放。
(2)低温蒸发联合臭氧催化氧化工艺用于精细化工污水处理,能够解决精细化工企业高盐、高有机物污水难处理的发展瓶颈,具有很大的推广意义。
参考文献
[1]韦朝海,何勤聪,帅伟,等.精细化工废水的污染特性分析及其控制策略[J].化工进展,2009,28(11):
2047-2048.
[2]李雪,王艺蒙,韩亚会,等.探究精细化工废水的污染特性分析及其控制策略[J].化工中间体,2015(4):
126.
精细化工论文第二篇:
绿色精细化工发展现状与生产核心技术
摘要:
随着我国经济的发展与科学技术的不断进步,化工生产正在我们的生活中扮演着很重要的角色。
化工企业在推进化工技术创新的过程中,绿色与环保已经成为重点考虑的主题,这也为我国的精细化工企业确定了绿色的发展方向。
文章将会从绿色的角度出发,谈一谈精细化工的发展现状与关键技术。
关键词:
绿色;发展现状;关键技术;
1我国绿色精细化工的发展现状
生产精细化工产品是我国化工企业的主要目的,现今阶段又要考虑绿色环保的问题,以便于精细化工生产能够更好地作为现代化化工企业的核心部分。
就目前的情况来看,精细化工生产在我国正处于发展的上升阶段,核心技术发展仍然不够成熟,与欧美的一些化工强国相比,差距还是比较明显的。
拿制约精细化工发展的因素来说,影响因素是多元化的。
比如环境问题,目前的生产过程中容易受环境污染影响,导致生产的产品精细程度不高,一定程度上降低了企业的经济效益。
但是大部分企业出于资金的考虑,不愿意在环境保护问题上下功夫,然而在环境工作中投放的资金,与最终损失的经济效益相比,简直是九牛一毛。
同时精细化工生产也会带来严重的环境污染问题,会影响人民的生活,环境污染是一个全球性的问题,需要我们共同面对。
污染问题必须得到合理解决,保证我们社会生产建设健康发展。
1.1生产技术水平低
在当今的化工生产过程中,传统生产技术仍然饱受欢迎,生产路线也是按传统的做法。
在这种情形之下,使用的材料设备是比较陈旧的,新式的材料产品没有得到很好地利用。
当今的科研工作是站在当今时代的角度之上,而在一个没有新产品的生产背景之下,科研工作没有办法全面并且合理地开展,不容易形成科学、高效率的管理体系,化工产品的种类会逐渐单一,科研产品无法发挥真正的价值。
因此,在实际意义之上,化工领域的发展仍然没有得到推动,经济也没有进步。
企业的生产技术水平低,直接降低了市场竞争力。
1.2产业链不够完整,集中化程度不高
大多数化工企业的生产规模还是比较小的,中小型企业居多,空间分布密度低。
密度第一就反应了集中化程度不高,生产效率与产品质量都很难得到提高,整个化工企业没有呈链状连接。
这是生产现状中的一个重要问题。
1.3信息技术水平不高
当今时代是一个信息化时代,有效利用信息技术进行生产是一个很好的发展方向。
在这个过程当中,精细化工生产过程要合理地与先进的信息化技术进行融合。
然而大部分企业的信息技术发展非常落后,这就很难促进现代化化工企业发展。
2目前我国绿色精细化工生产的关键技术
2.1绿色催化技术
考虑到未来精细化工生产的发展方向,催化剂一直是化工行业的重要组成部分,使用绿色催化技术进行精细化工生产是一个大的发展方向。
绿色催化技术相比于传统的催化技术,能够更好地保护环境,减少污染问题。
具体来说,精细化工生产的催化技术体系主要分为以下几类。
2.1.1相转移催化技术
此技术的应用主要目的是提高反应效率,使得反应向所需要的方向进行,反应更加具有针对性与方向性,此种催化技术还能使反应的环境变得温和、能耗低。
2.1.2酶催化技术体系
从生物化学的角度来说,酶可以降低反应活化能。
在精细化工生产过程中,酶催化技术可以提高反应的针对性,完善相转移催化技术的工作,使反应过程更加高效、能耗更低。
2.1.3不对称催化技术体系
使用此技术体系主要是为了得到属性更加单一的分子,这分子可以广泛应用于医药、农业与光电材料产品中,为它们提供精细原材料,使得其他领域的产品生产过程更加绿色,更加环保。
2.2计算机分子模拟设计技术
此技术的应用主要是优化精细化工产品。
对产品的分子性能、加工方法与内部构造等特点进行充分考虑,使用计算机的辅助设计功能,把绿色环保与创新作为考虑方向,模拟产品内在结构的合成、反应与精制过程,找到影响产品质量与绿色环保生产的主要因素,在之后的生产过程中优化这些因素,力求生产无三废的化工产品。
2.3超临界流体技术
超临界流体技术在近几年的发展势头很猛烈,并且超临界流体的萃取技术格外受到重视,特别是超临界二氧化碳流体技术得到了很大的发展空间。
超临界二氧化碳流体技术需要合适的生产临界温度与临界压力,这样才能为二氧化碳萃取技术提取生理活性物质提供有效手段。
超临界二氧化碳还能作为一种绿色环保的精细化生产介质,可以实现化学反应中复杂、难度大的反应过程。
拿纳米材料或者薄膜材料来说,材料生产所需的条件非常苛刻,超临界流体技术就能很好地解决问题。
随着超临界技术的不断突破,未来在医药、高分子材料与食品等行业中还能够大显