自动变速器1.docx
《自动变速器1.docx》由会员分享,可在线阅读,更多相关《自动变速器1.docx(56页珍藏版)》请在冰豆网上搜索。
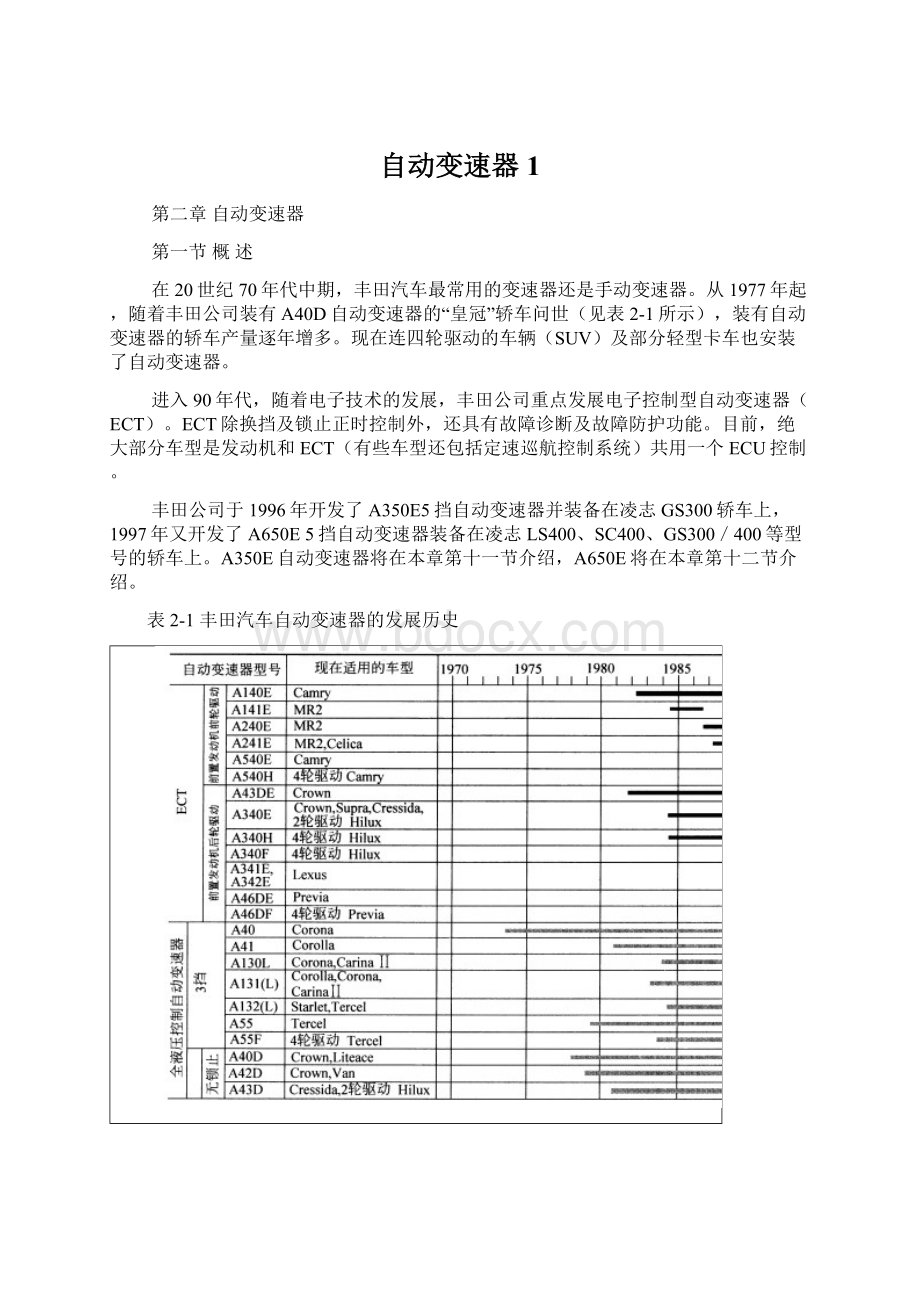
自动变速器1
第二章自动变速器
第一节概述
在20世纪70年代中期,丰田汽车最常用的变速器还是手动变速器。
从1977年起,随着丰田公司装有A40D自动变速器的“皇冠”轿车问世(见表2-1所示),装有自动变速器的轿车产量逐年增多。
现在连四轮驱动的车辆(SUV)及部分轻型卡车也安装了自动变速器。
进入90年代,随着电子技术的发展,丰田公司重点发展电子控制型自动变速器(ECT)。
ECT除换挡及锁止正时控制外,还具有故障诊断及故障防护功能。
目前,绝大部分车型是发动机和ECT(有些车型还包括定速巡航控制系统)共用一个ECU控制。
丰田公司于1996年开发了A350E5挡自动变速器并装备在凌志GS300轿车上,1997年又开发了A650E5挡自动变速器装备在凌志LS400、SC400、GS300/400等型号的轿车上。
A350E自动变速器将在本章第十一节介绍,A650E将在本章第十二节介绍。
表2-1丰田汽车自动变速器的发展历史
第二节液力变矩器
一、概述
液力变矩器的作用是传递来自发动机的扭矩,并且将扭矩成倍增大后传给变速器。
它安装在变速器齿轮传动系的输入端,壳体用螺栓固定在发动机的飞轮上。
丰田公司近期生产的车用液力变矩器都有锁止离合器,其结构如图2-1所示。
它是由泵轮、涡轮、定轮、单向离合器、锁止离合器等部件构成。
变矩器内充满油泵提供的自动变速器油。
变速器油被泵轮甩出,成为一股强大的油流,推动变矩器的涡轮转动。
图2-1液力变矩结构图
泵轮与变矩器壳体连成一体,变矩器壳体用螺栓固定在飞轮上,因为泵轮与曲轴相连,它总是和曲轴一起转动。
泵轮内部径向装有许多弯曲的叶片,叶片内缘装有让变速器油平滑流过的导环,其结构如图2-2所示。
图2-2泵轮的结构与安装示意图
同泵轮一样,涡轮也装有许多叶片(如图2-3所示),但涡轮叶片的弯曲方向与泵轮叶片的弯曲方向相反。
涡轮转轮装在变速器输入轴上,其叶片与泵轮叶片相对放置,中间留有一很小的间隙。
图2-3涡轮的结构与安装示意图
涡轮转轮与变速器输入轴相连,在变速器换挡杆置于“D”、“2”、“L”或“R”挡位,当车辆行驶时,涡轮转轮就与变速器的输入轴一起转动;当车辆停驶时,涡轮转轮不能转动。
在变速器换挡杆置于“P”或“N”挡位时,涡轮转轮与泵轮一起自由转动。
定轮位于泵轮与涡轮转轮之间,安装在定轮轴上,而定轮轴则经单向离合器固定在变速器壳体上。
定轮叶片截住离开涡轮转轮的变速器油液,改变其方向,使其冲击泵轮叶片背部,给泵轮一个额外的“助推力”,如图2-4所示。
图2-4定轮的结构及其功能
单向离合器使定轮以与发动机曲轴运转相同的方向转动。
但是,如果定轮要以与发动机曲轴运转相反的方向转动时,单向离合器就将定轮锁止住,使其无法朝相反方向转动。
所以定轮是转动还是被锁止,取决于变速器油液冲击定轮叶片的方向。
单向离合器的工作如图2-5所示。
当外座圈按图中箭头A方向转动时,就会推动楔块顶部,由于I1小于I,楔块就会倾翻,使外座圈转动。
但当外座圈要朝相反方向(B向)转动时,楔块就无法倾翻,因为I2大于I。
这样,楔块起到楔子的作用,锁住外座圈,使其无法转动。
另外,离合器中还安装了定位弹簧,使楔块总是朝着锁止外座圈的方向略为倾斜,以加强楔块的锁止功能。
楔块型单向离合器也用于控制行星齿轮系。
图2-5单向离合器的运作图
二、液力变矩器的工作原理
1、动力传输原理
如图2-6所示,将电风扇A与电风扇B靠近相对放置,然后打开电风扇A,电风扇B即使未接电源也会按电风扇A转动的方向转动。
这是因为电风扇A的转动会在两电风扇之间产生空气流动,由电风扇A产生的气流冲击电风扇B的叶片,使电风扇B随之转动。
换句话说,电风扇A与B之间的动力传递是以空气为介质而实现的。
图2-6空气传输动力示例
变矩器的工作原理也是如此,泵轮相当于电风扇A,涡轮转轮则相当于电风扇B。
不同的是变矩器是以变速器油为介质,而不是以空气为介质。
如图2-7所示,当泵轮被发动机曲轴驱动时,泵轮中的变速器油液就会随同泵轮以相同的方向转动。
当泵轮转速加快时,其离心力的作用使油液沿叶片表面及泵轮里面,离开泵心向外流动。
当泵轮转速进一步提高时,液体就被甩出泵轮,冲击涡轮叶片,使涡轮开始按泵轮转动的方向转动。
图2-7液力变矩器的动力传输过程
油液的能量在冲击涡轮叶片被耗散后,油液就沿着涡轮叶片向里流,在流至涡轮内部时,涡轮变曲的内表面使油液改变方向,流回泵轮。
就这样,循环又将从头开始。
如上所述,扭矩的传递,是通过油液在泵轮和涡轮之间流动来实现的。
2、扭矩成倍放大的原理
前面用两台电风扇作例子,解释了液力变矩器中扭矩传递的原理。
如果如图2-8所示,加上一条输送管道,气流将穿过电风扇B(被动电风扇)然后经管道,从电风扇A后面流回电风扇A(主动电风扇)。
这就会加强电风扇A的叶片所吹动的气流,气流通过电风扇B后所剩下的能量,将增强电风扇A叶片的转动。
图2-8空气传输动力扭矩放大示例
在变矩器中,定轮和空气管道的作用是相似的。
3、定轮单向离合器的功能
在变矩器中,液体的实际流动是由涡流和环流叠加而成的。
所谓涡流就是泵轮泵出的液流通过涡轮和定轮,然后再回到泵轮的液流。
车辆起动时,泵轮和涡轮的转速差越大,涡流就越大。
所谓环流就是变矩器内与变矩器转动方向相同的液流。
当泵轮与涡轮转速差较小时,环流就大,车辆以恒速行驶时就是如此。
环流随泵轮与涡轮转速差增大而成比例地变小。
从涡轮转轮进入定轮的液流方向取决于泵轮与涡轮的转速差。
当这一转速差相当大时,涡流的速度就高。
如图2-9所示,液体从涡轮转轮流至定轮的液体流动方向(图中虚线箭头)是阻止泵轮转动的。
液体冲击定轮叶片的正面,使定轮与泵轮反向转动。
但由于定轮被单向离合器锁住,并不转动,其叶片使液体流向改变(图中实线箭头),增强泵轮转动。
图2-9液力变矩器(在涡流相当大时)扭矩放大的液流示意图
当涡轮的转速接近泵轮转速时,环流速度就升高,而涡流速度则降低。
因而从涡轮转轮流至定轮的液流与泵轮的转动方向是一致的。
如图2-10所示,由于这时变速器油液冲击定轮叶片的背面,使定轮叶片对液流起阻挡作用。
在这种情况下,单向离合器使定轮与泵轮同方向转动,从而使液流返回至泵轮。
图2-10涡轮与泵轮转速接近时变矩器的液流示意图
如上所述,当涡轮转速达到泵轮转速的某一给定比例时,定轮就开始与泵轮同一方向转动。
这就是变矩器的工作点,也称为耦合点。
在达到耦合点以后,扭矩成倍放大效应不再发生,变矩器也仅起到普通液力变矩器的作用。
三、液力变矩器的性能
1、扭矩比
如前所述,变矩器扭矩的成倍放大与涡流成比例增大。
即在涡轮转轮停转时,扭矩达到最大。
如图2-11所示,变矩器的工作分为两个区域:
一个是变矩区,扭矩成倍放大;另一个是耦合区,只传递扭矩而无扭矩放大。
耦合器工作点就是这两个区域的分界线。
图2-11液力变矩器工作图
图中:
扭矩比(t)=
转速比(e)=
失速点是指涡轮停转,或转速比(e)为零时的定轮状态。
变矩器的最大扭矩比就在失速点,通常在1.7~2.5之间。
在失速点(例如,当换挡杆置于“D”挡位而车辆被阻止前进时),泵轮与涡轮之间的转速差达到最大。
在以后要介绍的失速测试中,变矩器性能与发动机输出功率测试是在失速点将发动机节气门全开(满负荷)的情况下进行的。
当涡轮开始转动,转速比上升时,涡轮与泵轮之间的转速差开始下降。
当转速比达到某一规定值时,涡流变得最小,因而扭矩比几乎为1:
1。
由于从涡轮转轮流出的液流以较高速比冲击定轮叶片的背后,单向离合器就使定轮与泵轮同向转动。
换言之,变矩器在耦合工作点时,开始起一台液力耦合器的作用,防止扭矩比降至1以下。
2、传动效率
变矩器的传动效率是指泵轮得到的能量传递至涡轮的效率,它与转速比(e)的关系如图2-12所示。
图2-12液力变矩器传动效率与转速比的关系
这里所说的能量是指发动机本身的输出功率,与发动机的转速和扭矩成正比。
传动效率(n)=
100%
=
转速比(e)×100%
在失速点时,泵轮转动而涡轮停住不转,这时传递到涡轮的是最大扭矩,而传动效率却为零。
当涡轮开始转动时,随着其转速升高,涡轮输出功率增大,传动效率激增。
在转速比达到耦合点前少许时,传动效率达到最大值,其后又开始下降,这是因为从涡轮转轮流出的部分油液开始流到定轮叶片背面。
在达到耦合点时,来自涡轮转轮的液流,大部分冲击定轮叶片背面,定轮开始转动,使传动效率不致进一步下降,变矩器则开始如同一台液力耦合器一样发挥作用。
由于扭矩在液力耦合器中是以接近1:
1传递的,在耦合区内的传动效率与转速比成正比例地直线上升。
但由于液流的摩擦及撞击,使液流温度也上升,液流的循环又使部分动能被消耗。
所以,变矩器的传动效率不可能达到100%,通常仅为95%左右。
四、液力变矩器的运作
液力变矩器在换挡杆位于“D”(前进挡)“2”、“L”(低速挡)或“R”(倒挡)挡位时工作情况,简述如下:
1、车辆停住,发动机怠速运转
发动机怠速运转时,自身产生的扭矩最小。
若使用了制动器停车(手制动或脚制动),此时涡轮上的载荷最大,这是因为涡轮无法转动。
但是,由于车辆停住时,涡轮与泵轮的转速比为零,而扭矩比却最大。
所以涡轮总是随时准备以大于发动机所产生的扭矩转动。
2、车辆启动时
当制动器松开时,涡轮就能与变速器输入轴一起转动。
当踩下加速踏板时,涡轮就以大于发动机所产生的扭矩转动,车辆开始前进。
3、车辆低速行驶时
随着车速的提高,涡轮的转速迅速接近泵轮的转速,从而使扭矩比也迅速接近1.0。
当涡轮与泵轮的转速比接近某一值(耦合器工作点)时,定轮开始转动,扭矩成倍放大效应下降。
换言之,变矩器开始只作为一台液力耦合器工作。
所以,车速几乎与发动机转速成正比例地直线上升。
4、车辆以中、高速行驶时
这时,变矩器仅仅起到一台液力耦合器的作用。
涡轮以与泵轮几乎一样的转速转动。
值得注意的是,在车辆正常启动的过程中,变矩器在车辆起步2~3秒后达到耦合点。
但是如果载荷太大,即使车辆中、高速行驶,变矩器也有可能在变矩区内工作。
五、锁止离合器
在耦合区(即没有扭矩成倍放大的情况),变矩器以接近1:
1的比例将来自发动机的输入扭矩传递至变速器。
但在泵轮与涡轮之间存在着至少4%~5%的转速差。
所以,变矩器并不是将发动机的动力100%地传递至变速器,而是有一定的能量损失。
为了防止这种现象发生,也为了降低油耗,当车速在大于60km/h时,锁止离合器会通过机械机构将泵轮与涡轮相连接。
这样,使发动机产生的动力几乎100%地传递至变速器。
如图2-13所示,锁止离合器装在涡轮转轮毂上,位于涡轮转轮前端。
减振弹簧在离合器接合时,吸收扭力,防止产生振动。
在变矩器壳体或变矩器锁止活塞上粘有一种摩擦材料,用以防止离合器接合时打滑。
图2-13锁止离合器脱开时的液流示意图
锁止离合器的接合和分离由变矩器中的液压油的流向改变来决定,其工作过程如下:
1、离合器分离时
当车辆低速行驶时,由继动阀控制(阀的工作在本章第四节讲述)的油液流动方向如图2-13所示。
加压油液流至锁止离合器的前端,锁止离合器前端及后端的压力就变得一样,锁止离合器处于脱开状态。
这时由于变矩器内油液因涡流产生大量热量,流出变矩器的油液要经冷却器冷却后再送回变速器。
2、离合器接合时
当车辆以中高速(≥50km/h)行驶时,继动阀控制(阀的工作在本章第四节讲述)的油液流动方向如图2-14所示,加压油液流至锁止离合器的后端。
这时,变矩器壳体受到锁止活塞挤压,从而使锁止离合器和前盖一起转动,即锁止离合器接合。
由于这时泵轮与涡轮转轮转速差为零,没有涡流产生,因而油液在变矩器内产生的热量很小,流出变矩器的油液不需要冷却,直接流回变速器。
图2-14锁止离合器接合时的液流图
锁止离合器分离或接合时的动力传输过程框图见图2-15。
涡轮
泵轮转轮
分离
动力输出
动力输入
锁定离合器
接合
图2-15液力变矩器动力传输过程图
第三节行星齿轮变速机构
利用行星齿轮系统进行传递动力和变速,具有体积小、结构简单、操纵容易和变速比大等优点,所以,行星齿轮系统在丰田自动变速器中得到广泛应用。
一、单排行星齿轮组变速原理
图2-16是单排行星齿轮组结构图。
单排行星齿轮组由太阳轮、行星架和齿圈3个基本零件构成,另外还有安装在行星架上的行星小齿轮。
工作时,行星小齿轮除绕行星小齿轮轴自转外,同时还要绕太阳轮公转,行星小齿轮的这种运动形式与太阳系行星的运动相似,所以称行星齿轮系统。
图2-16单排行星齿轮组结构图
工作时,太阳轮、行星架和齿圈三者具有同一旋转轴线,将三者中的任一个构件与主动轴相连,作为输入件,第二个构件与被动轴相连作为输出件,第三个构件被强制固定(简称制动),就能够实现动力传递,这种连接与制动可有6种不同的组合方案。
将任意二个构造锁成一体,各齿轮间均无相对运动,整个行星齿轮组成整体旋转作直接传动。
三个构件中,既无任何一个构造固定,也无任何两个构件被锁成一体,各构件都可以自由转动,输入轴转动时,输出轴可以不动,这种情况行星齿轮组不传递动力,从而得到空挡。
所以,包括直接传动和空挡在内,单个行星齿轮组可以得到8种不同的传动方案。
1、传动比
行星齿轮组传动比的计算公式如下:
传动比=
由于行星小齿轮总是作为惰轮工作,行星小齿轮齿数不影响行星齿轮组的传动比。
所以,行星齿轮组的传动比是由太阳轮、行星架和齿圈的齿数决定的。
由于行星架并非齿轮,没有轮齿,其齿数是虚拟的,并可用下式计算得出:
行星架齿数(ZC)=太阳轮齿数(ZS)+齿圈齿数(ZR)
可以看出,太阳轮齿数(ZS)最小,齿圈齿数(ZR)居中,虚拟的行星架齿数(ZC)最多。
从传动比的计算公式可知,用齿数小的构件做主动件,传动比大于1,获得的是减速传动;用齿数多的构件做主动件,传动比小于1获得的是增速传动。
所以,在行星齿轮组中,用太阳轮做主动件获得的总是减速传动,用行星架做主动件获得的总是增速传动。
下面假定太阳轮齿数(ZS)为24,齿圈齿数(ZR)为56,行星架齿数(ZC=ZS+ZR)为80,计算行星齿轮组各种组合方案的传动比。
2、减速传动
如图2-17所示,太阳轮固定,齿圈输入,行星架输出。
当齿圈顺时针转动时,行星轮则围绕太阳轮顺时针转动。
这样,行星架就获得了与齿圈相同转向的减速运动。
图2-17单排行星齿轮组减速传动示意图
传动比=
同样,齿圈固定,太阳轮输入,行星架输出,这种方案能获得太阳轮和行星架相同转向的减速传动,其传动比的计算如下式:
传动比=
3、增速传动
如图2-18所示,太阳轮固定,行星架输入,齿圈输出。
当行星架顺时针方向转动时,行星小齿轮就围绕太阳轮顺时针方向转动,这样,齿圈就获得了与行星架相同转向(顺时针)的增速运动,其传动比的计算如下式:
传动比=
同样,齿圈固定,行星架输入,太阳轮输出,这种方案能获得太阳轮和行星架相同转向的增速传动,其传动比的计算如下式:
传动比=
4、倒挡传动
如图2-19所示,行星架固定,太阳轮输入,齿圈输出。
当太阳轮顺时针转动时,固定在行星架上的行星小齿轮就逆时针转动,结果齿圈获得与太阳轮相反转向(逆时针方向)的减速运动,其传动比的计算如下式:
传动比=
-2.333
式中:
“-”号表示太阳轮和齿圈转动方向相反
同样,行星架固定,齿圈输入,太阳轮输出,这种方案太阳输和齿圈的转动方向也相返,不过其传动是增速传动,传动比的计算如下式:
传动比=
式中:
“-”号表示太阳轮和齿圈转动方向相反
图2-18单排行星齿轮组增速传动示意图图2-19单排行星齿轮组倒挡传动示意图
综上所述,单个行星齿轮组的工作情况可概括成表2-2。
从表中可以看出,行星架分别作为输入件,输出件,固定件,单个行星齿轮组可以依次得到增速传动、减速传动和倒挡传动。
表2-2单个行星齿轮组的传动方案
传动形式
输入件
固定件
输出件
传动比
减速传动
齿圈
太阳轮
行星架
ZC/ZR≈1.429
太阳轮
齿圈
ZC/ZS≈3.333
增速传动
行星架
太阳轮
齿圈
ZR/ZC≈0.7
齿圈
太阳轮
ZS/ZC≈0.3
倒挡传动
太阳轮
行星架
齿圈
-ZR/ZS≈-2.333
齿圈
太阳轮
-ZS/ZR≈-0.429
备注:
(1)假定太阳轮齿数(ZS)为24,齿圈齿数(ZR)为56,则行星架齿数(ZC=ZS+ZR)为80。
(2)传动比项目中的负号(“-”)表示太阳轮和齿圈转动方向相反。
二、3速行星齿轮机构
丰田汽车自动变速器,采用辛普森(Simpson)行星齿轮机构,即两套单排行星齿轮排列在同一轴上。
根据这两套齿轮在变速器中的位置,分别称作“前行星齿轮组”和“后行星齿轮组”。
这二套齿轮组由单个太阳轮连接起来,加上控制其转动的制动器和离合器,以及传递扭矩的轴承和轴,组合起来就构成3速行星齿轮机构,即有三个前进挡和一个倒挡。
图2-20是典型的3速行星齿轮机构。
中间轴主动齿轮,相当于前置发动机后轮驱动车辆变速器的输出轴,通过花键与中间轴连接,与中间轴被动齿轮啮合;前后太阳轮作一个整体转动,中间轴从轴心穿过。
前行星架和后行星齿圈,各自通过花键与中间轴连接。
下面先介绍3速行星齿轮机构的换挡执行元件,然后再介绍其工作过程。
图2-20丰田3速行星齿轮机构结构图
1、换挡执行元件的工作过程
(1)离合器的工作过程。
丰田汽车自动变速器采用多片摩擦式离合器,离合器片上贴有纸基摩擦材料,它具有磨损小,使用中不需要调整,传递扭矩的容量大等特点。
离合器的接合如图2-21所示。
当加压油液流至活塞缸,就推动活塞止逆球,使其关闭单向阀。
此时,缸内压力升高,活塞向左运动,迫使离合器片接触离合器盘。
由于离合器片与离合器盘之间的巨大摩擦力,使驱动侧盘与离合器从动盘以相同速度转动。
这样,离合器接合,输入轴与齿圈连接,动力从输入轴传送到齿圈。
图2-21离合器接合状态示意图
离合器的分离如图2-22所示。
当加压的液压传动装置卸压时,液压缸内的油液压力下降,这就使得止逆球因离心力的作用而离开底座,液压缸内的油液经单向阀流出。
此时,由于回位弹簧的作用,活塞又返回到原位,使离合器分离。
图2-22离合器分离状态示意图
3速行星齿轮机构使用2个离合器(C1和C2)。
如图2-23所示,离合器C1接合时,动力从输入轴传递至齿圈。
如图2-24所示,离合器C2接合时,动力从输入轴传递至太阳轮。
如图2-25所示,离合器C1和C2同时接合,太阳轮和齿圈均与输入轴固定连接,实现动力从输入轴到与行星架花键连接的中间轴直接传递。
图2-23离合器C1工作时动力传输图
图2-24离合器C2工作时动力传输图
图2-25离合器C1和C2同时工作时动力传输图
(2)制动器(B1、B2和B3)。
制动器有两种类型:
带式制动器和多片湿式制动器。
3速行星齿轮机构中的B1制动器采用带式制动器。
而B2和B3采用多片湿式制动器。
不过,在有些自动变速器中,B1制动器也采用多片湿式制动器。
1)带式制动器(B1)如图2-26所示,制动带缠于制动鼓的外缘上。
制动带的一端用一锁销固定在变速器的壳体上,而另一端与液压操纵的制动分泵活塞相接触。
制动分泵活塞压缩内弹簧,在活塞连杆上运动。
为了使制动带和制动鼓之间的间隙能够调整,有二种长度的活塞连杆供选择。
图2-26带式制动器的工作图
如图2-26所示。
当油压力施加在活塞上时,活塞就移至活塞缸的左边,压缩外弹簧,活塞连杆随同活塞移至左边,推动制动带的一端。
由于制动带的另一端固定在变速器壳体上,制动带的直径就变小,箍紧在制动鼓上,使之无法转动。
这时,在制动带与制动鼓之间产生很大的摩擦力,使行星齿轮组中与制动鼓固定连接的元件无法转动。
当活塞中的加压液体流出时,活塞和活塞连杆由于外弹簧的弹力而被推回,制动鼓就由制动带松开。
内弹簧有两个功能:
一个是吸收制动鼓的反作用力;另一个是减少制动带箍紧制动鼓时所产生的振动。
如图2-27所示。
当制动鼓高速转动时,制动带要箍紧它,就会受到一反作用力。
若活塞与活塞连杆制成一整体,由于反作用力的作用,活塞会产生振动。
为避免这种情况,活塞通过一内弹簧与活塞连杆相连。
当制动带受到反作用力时,活塞连杆被推回,压缩内弹簧,以吸收此反作用力。
图2-27内弹簧的减振工作图
当活塞缸内油压力上升时,活塞与活塞连杆进一步压缩外弹簧,并在活塞缸内运动,使制动带收缩,从而均匀地箍紧制动鼓。
当活塞缸内油压进一步上升,而活塞连杆在活塞缸内无法再运动时,只有活塞运动,压紧内、外弹簧。
当活塞开始接触活塞连杆垫圈时,活塞直接推动活塞连杆,制动带便以更大的压力箍紧制动鼓。
2)多片湿式制动器(B2和B3)的结构和离合器(C1和C2)相似,所不同的是制动片固定在变速器壳体上。
制动器B2通过1号单向离合器防止前后太阳轮逆时针转动。
制动器B3用以防止后行星齿轮架的转动。
如图2-28所示,当制动器活塞缸受到油压作用时,活塞在活塞缸内运动,使制动片与制动盘相互接触。
结果,在每个制动片与制动盘之间产生很大的摩擦力,使行星齿轮架锁定在变速器壳体上。
当加压油液被排出活塞缸时,由于回位弹簧的作用,活塞退回至原位,使制动器松开。
图2-28多片式制动器的结构运作图
在A40和340系列自动变速器中,有一个由外活塞和内活塞构成的双活塞型离合器(C2)和制动器(B3),用以缓冲离合器或制动器接合时产生的振动。
如图2-29所示,首先向小直径的内活塞施加油压,使盘和片接合少许,然后外活塞开始运作,施加较大油压。
这样,内活塞产生的较小压力,再加上外活塞产生的较大压力,使盘和片完全接合。
由于作用在离合器或制动器的压力被分为两个阶段施加,从而缓冲了离合器或制动器接合时产生的振动。
图2-29双活塞型离合器(或制动器)运作图
在制动器B2、B3的活塞中与离合器C1、C2不一样,它没有止逆球。
这是因为当油压卸压时,由于离心力的作用,没有油液留在活塞缸中。
因此,即使没有止逆球,液压油也能迅速地被排出。
离合器C1、C2和制动器B2、B3的情况一样,盘数和片数随自动变速器型号而异。
即使是同一型号的自动变速器,由于配套的发动机不同,其盘和片的数目也可能不同。
在更换新的离合器片、制动器片或制动带时,要先将其浸泡在自动变速器油中15min以上,使摩擦材料(纸底板)充分膨胀。
(3)单向离合器(F1及F2)。
单向离合器的结构和工作原理在本章的第二节中已作介绍。
1号单向离合器(F1)通过制动器B2运作,以防止前后中心齿轮逆时针转动。
2号单向离合器的外座圈固定在变速器壳体上。
后行星齿轮架(内座圈)逆时针转动时,被外座圈锁住;后行星轮架顺时针转动时,则可以自由转动。
所以,2号单向离合器(F2)可防止后行星齿轮架逆时针转动。
对于为什么要设置单向离合器F1和F2,将在本节中介绍。
2、换挡工作过程
图2-30是3速行星齿轮机构示意图。
表2-3是各换挡执行元件的功能。
表2-4是离合器、制动器在各挡位时的工作情况。
现将各挡位的传动路线叙述如下。
图2-303速行星齿轮机构
表2-33速行星齿轮机构换挡执行元件的功能
执行元件
功能
前进挡离