金属切削加工基础.docx
《金属切削加工基础.docx》由会员分享,可在线阅读,更多相关《金属切削加工基础.docx(24页珍藏版)》请在冰豆网上搜索。
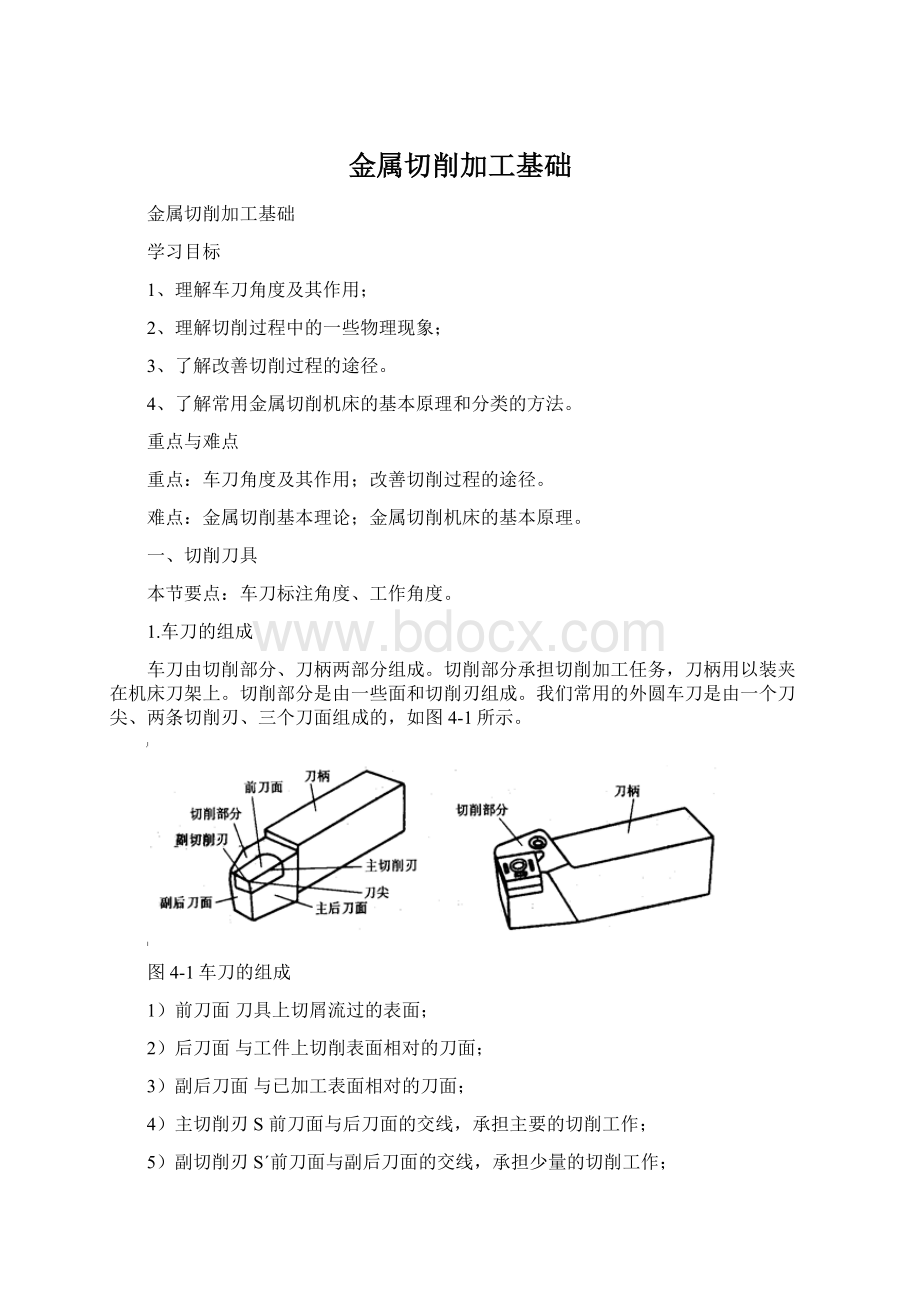
金属切削加工基础
金属切削加工基础
学习目标
1、理解车刀角度及其作用;
2、理解切削过程中的一些物理现象;
3、了解改善切削过程的途径。
4、了解常用金属切削机床的基本原理和分类的方法。
重点与难点
重点:
车刀角度及其作用;改善切削过程的途径。
难点:
金属切削基本理论;金属切削机床的基本原理。
一、切削刀具
本节要点:
车刀标注角度、工作角度。
1.车刀的组成
车刀由切削部分、刀柄两部分组成。
切削部分承担切削加工任务,刀柄用以装夹在机床刀架上。
切削部分是由一些面和切削刃组成。
我们常用的外圆车刀是由一个刀尖、两条切削刃、三个刀面组成的,如图4-1所示。
图4-1车刀的组成
1)前刀面刀具上切屑流过的表面;
2)后刀面与工件上切削表面相对的刀面;
3)副后刀面与已加工表面相对的刀面;
4)主切削刃S前刀面与后刀面的交线,承担主要的切削工作;
5)副切削刃Sˊ前刀面与副后刀面的交线,承担少量的切削工作;
6)刀尖是主、副切削刃的相交点,实际上该点而是由一段折线或小圆弧组成,小圆弧的半径称为刀尖圆弧半径,用表示,如图4-2所示。
图4-2刀尖形状
2.刀具几何角度参考系
为了便于确定车刀上的几何角度,常选择某一参考系作为基准,通过测量刀面或切削刃相对于参考系坐标平面的角度值来反映它们的空间方位。
刀具几何角度参考系有两类,刀具标注角度参考系和刀具工作角度参考系。
(1)刀具标注角度参考系
正交平面参考系如图4-3所示,正交平面参考系由以下三个平面组成:
图4-3正交平面参考系
基面是过切削刃上某选定点,平行或垂直于刀具在制造、刃磨及测量时适合于安装或定位的一个平面或轴线,一般来说其方位要垂直于假定的主运动方向。
车刀的基面都平行于它的底面。
主切削平面是过切削刃某选定点与主切削刃相切并垂直于基面的平面。
正交平面是过切削刃某选定点并同时垂直于基面和切削平面的平面。
过主、副切削刃某选定点都可以建立正交平面参考系。
基面、主切削平面、正交平面三个平面在空间相互垂直。
(2)刀具工作角度参考系
刀具工作角度参考系是刀具切削加工时的角度基准(不考虑假设条件),在此基准下定义的刀具角度称刀具工作角度。
它同样有正交平面参考系、法平面参考系和假定工作平面参考系。
3.刀具标注角度
如图4-4所示。
图4-4车刀的几何角度
(1)在基面内测量的角度
1)主偏角主切削刃与进给运动方向之间的夹角。
2)副偏角副切削刃与进给运动反方向之间的夹角。
3)刀尖角主切削刃与副切削刃之间的夹角。
刀尖角的大小会影响刀具切削部分的强度和导热性能。
它与主偏角和副偏角的关系如下:
(2)在主切削刃正交平面内(O-O)测量的角度
1)前角前刀面与基面间的夹角。
当前刀面与基面平行时,前角为零。
基面在前刀面以内,前角为负。
基面在前刀面以外,前角为正。
2)后角后刀面与切削平面间的夹角。
3)楔角前刀面与后刀面间的夹角。
(3)在切削平面内(S向)测量的角度
刃倾角主切削刃与基面间的夹角。
刃倾角正负的规定如图4-5所示。
刀尖处于最高点时,刃倾角为正;刀尖处于最低点时,刃倾角为负;切削刃平行于底面时,刃倾角为零。
图4-5刃倾角的正负规定
(4)在副切削刃正交平面内(O´-O´)测量的角度
副后角副后刀面与副切削刃切削平面间的夹角。
上述的几何角度中,最常用的是前角、后角、主偏角、刃倾角、副偏角和副后角,它们反映出刀具的切削特点。
4.刀具工作角度
切削过程中,由于刀具的安装位置、刀具与工件间相对运动情况的变化,实际起作用的角度与标注角度有所不同,我们称这些角度为工作角度。
现在仅就刀具安装位置对角度的影响叙述如下:
(1)刀柄中心线与进给方向不垂直时对主、副偏角的影响
当车刀刀柄与进给方向不垂直时,实际工作的主偏角和副偏角将发生变化。
如图4-6所示。
图4-6刀柄中心线不垂直进给方向对主、副偏角的影响
(2)切削刃安装高于或低于工件中心时,对前角、后角的影响
切削刃安装高于或低于工件中心时,按参考平面定义,通过切削刃作出的实际工作切削平面、基面将发生变化,所以使刀具实际工作前角和后角也随着发生变化,如图4-7所示。
图4-7切削刃安装高于工件中心时,对前角、后角的影响
金属切削原理及应用
本节要点:
切削力、切削温度、刀具寿命及影响因素;提高加工质量的途径。
金属切削过程是工件上多余的金属材料不断被刀具切下成为切屑,形成已加工表面的过程。
这一过程会发生一系列的物理现象(切削热、刀具磨损等),直接或间接影响工件的加工质量和生产率。
1.切屑的形成和切屑种类
(1)切屑的形成过程
金属切削的特点是被切金属层在刀具的挤压、摩擦作用下产生变形后转变为切屑形成已加工表面。
如图4-8所示,为了进一步分析切削层变形的规律,通常把被切削刃作用的金属层划分为三个变形区。
第
变形区位于切削刃和前刀面的前方,面积是三个变形区中最大的,为主变形区;第
变形区是与前刀面相接触的附近区域,切屑沿前刀面流出时,受到前刀面的挤压和摩擦,靠近前刀面的切屑底层会进一步发生变形;第
变形区是已加工表面靠近切削刃处的区域,这一区域金属受到切削刃钝圆部分和后刀面的挤压、摩擦与回弹,发生变形造成加工硬化。
图4-8金属切削过程中的滑移线和流线
(2)切屑的类型
当工件材料的性能不同或切削条件不同时,会产生不同类型的切屑,并对切削加工产生不同的影响,常见的切屑种类大致有四类,如图4-9所示。
图4-9切屑类型
a)带状切屑b)节状切屑c)粒状切屑d)崩碎状切屑
1)带状切屑切屑靠近前刀面的一面很光滑,另一面呈毛茸状,是带状切屑。
当切削塑性较大的金属材料(碳素钢、合金钢、铜和铝合金)或刀具前角较大,切削速度较高时,经常出现这类切屑。
2)挤裂切屑(又称节状切屑)则剪切面上的局部材料就会破裂成节状,但与前刀面接触的一面互相连接而未被折断,这就是挤裂切屑。
工件材料塑性越差或用较大进给量低速切削钢材时,较容易得到这类切屑。
3)粒状切屑(又称单元切屑)在切屑形成过程中,若整个剪切面上所受到的剪应力均超过材料的破裂强度时,则切屑就成为粒状切屑,形状似梯形。
4)崩碎切屑切削铸铁、黄铜等脆性材料时,切削层几乎不经过塑性变形阶段就产生崩裂,得到的切屑呈现不规则的粒状,工件加工后的表面也极为粗糙。
在生产中常见的是带状切屑,当进给量增大,切削速度降低,则可由带状切屑转化为挤裂切屑。
在形成挤裂切屑的情况下,如果进一步减小前角,或加大进给量降低切削速度,就可以得到粒状切屑,这说明切屑的形态是可以随切削条件而转化的。
2.切削力
(1)切削力的来源、合力及其分力
金属切削时,切削力来源于两个方面,一是克服在切屑形成过程中,工件材料对弹性变形和塑性变形的变形抗力,二是克服切屑与前刀面和后刀面的摩擦阻力。
变形力和摩擦力形成了作用在刀具上的合力F,常将合力F分解为互相垂直的
、
和
三个分力,如图4-10所示。
图4-10切削合力及其分力
切削力
——在主运动方向上的分力,它与加工表面相切,并与基面垂直。
是计算刀具强度,设计机床零件,确定机床功率等的主要依据。
进给力
——在进给运动方向上的分力,它处于基面内与进给方向相反。
是设计机床进给机构和确定进给功率的主要依据。
背向力
——在切深方向上的分力,它处于基面内并垂直于进给运动方向。
是计算工艺系统刚度等的主要依据。
它也是使工件在切削过程中产生振动的力。
由图8-18可以看出进给力
和背向力
的合力
作用在基面上且垂直于主切削刃。
、
、
、
之间的关系为:
(2)影响切削力的主要因素
工件材料
工件材料的强度、硬度越高,剪切屈服强度
也越高,切削时产生的切削力就越大。
工件材料的塑性、冲击韧度越高,切削变形越大,切屑与刀具间摩擦增加,则切削力越大。
刀具几何参数
前角
增大,切削变形减小,故切削力减小。
主偏角对切削力
的影响较小,而对进给力
和背向力
影响较大,由图4-11可知当主偏角增大时,
增大,
减小。
图4-11主偏角对
和
的影响
切削用量
切削用量对切削力的影响较大,背吃刀量和进给量增加时,变形抗力和摩擦力加大,切削力随之增大,切削塑性材料时,切削速度对切削力的影响,如图4-12所示,在低速范围内,随着切削速度的增加,积屑瘤逐渐长大,刀具实际前角增大,使切削力逐渐减小。
在中速范围内,积屑瘤逐渐减小并消失,使切削力逐渐增至最大。
在高速阶段,由于切削温度升高,摩擦力逐渐减小,使切削力得到平稳下降。
图4-12切削速度对切削力的影响
其它因素
刀具材料与工件材料之间的摩擦系数
会直接影响到切削力的大小。
一般按立方碳化硼刀具、陶瓷刀具、涂层刀具、硬质合金刀具、高速钢刀具的顺序,切削力依次增大。
切削液的润滑作用愈好,切削力的降低愈明显。
在较低的切削速度下,切削液的润滑作用更为突出。
3.切削热和切削温度
切削过程中,由于切削层变形及刀具与工件、切屑之间的摩擦产生的热称为切削热。
切削热产生后是通过切屑、工件、刀具以及周围介质(如空气、切削液)传导和辐射出去的。
切削热的产生与传导影响切削区的温度,切削区的平均温度称为切削温度。
切削温度过高是刀具磨损的主要因素;工件的热变形则影响工件的尺寸精度和表面质量。
实际上,切削热对加工的影响是通过切削温度体现的。
切削时消耗的功越多,产生的切削热就越多,所以工件的强度、硬度越高或增加切削用量,都会使切削温度上升。
但是切削用量的增加也增加了散热条件,如
增加一倍,切削温度升高20%~30%;
增加一倍,切削温度升高10%;
增加一倍,切削温度只升高3%。
为了有效地控制切削温度,选用大的背吃刀量和进给量比选用大的切削速度有利。
切削热对切削加工的影响是加快刀具的磨损;导致工件的膨胀,引起工件变形,影响加工精度。
浇注切削液对降低切削温度、减少刀具磨损和提高加工表面质量有明显的作用。
切削液的润滑可以减小摩擦,减少切削热的产生。
4.切削液的选择
切削液的作用
切削液进入切削区,可以改善切削条件,提高工件加工质量和切削效率。
切削液的主要作用如下:
1)冷却作用切削液能从切削区域带走大量的热,降低切削温度。
2)润滑作用切削液能渗入到刀具与切屑和加工表面之间,形成一层润滑膜或化学吸附膜,能减小它们之间的摩擦。
3)清洗作用切削液大量的流动,可以冲走切削区域和机床上的切屑以及脱落的磨粒。
4)防锈作用在切削液中加入防锈剂,可在金属表面形成一层保护膜,对工件、机床、刀具和夹具等都能起到防锈作用。
常用切削液的种类与选用
1)水溶液它的主要成分是水,其中加入了少量具有防锈和润滑作用的添加剂。
水溶液的冷却效果良好,多用于普通磨削加工。
2)乳化液它是将乳化油(由矿物油、表面活性剂和其它添加剂配成)用水稀释而成,用途广泛。
低浓度的乳化液冷却效果较好,主要用于磨削、粗车、钻孔加工等。
高浓度的乳化液润滑效果较好,主要用于精车、攻丝、铰孔、插齿加工等。
3)切削油它主要是矿物油(如机械油、轻柴油、煤油等),少数采用动植物油或复合油。
普通车削、攻丝时,可选用机油。
精加工有色金属或铸铁时,可选用煤油。
加工螺纹时,可选用植物油。
在矿物油中加入一定量的油性添加剂和极压添加剂,能提高其高温、高压下的润滑性能,可用于精铣、铰孔、攻丝及齿轮加工。
5.刀具磨损和刀具寿命
1)刀具的磨损形式
刀具的磨损形式有以下三种,如图4-13所示。
(a)后刀面磨损(b)前刀面磨损(c)前后刀面同时磨损
图4-13刀具磨损形式
2)前刀面磨损
切削塑性材料时,如果切削速度和切削厚度较大,刀具前刀面上会形成月牙洼磨损。
当月牙洼发展到前缘与切削刃之间的棱边变得很窄时,切削刃强度降低,容易导致切削刃破损。
前刀面月牙洼磨损值以其最大深度KT表示。
3)后刀面磨损
后刀面与工件表面实际接触面积很小,所以接触压力很大,存在着弹性和塑性变形,切铸铁和以较小的切削厚度切削塑性材料时,主要也是发生这种磨损。
后刀面磨损带宽度往往是不均匀的,可划分为三个区域,如图4-14所示。
图4-14后刀面磨损情况
C区刀尖磨损强度较低,散热条件又差,磨损比较严重,其最大值为VC。
N区边界磨损切削钢材时主切削刃靠近工件待加工表面处的后刀面(N区)上,磨成较深的沟,以VN表示。
这主要是工件在边界处的加工硬化层和刀具在边界处较大的应力梯度和温度梯度所造成的。
B区中间磨损在后刀面磨损带的中间部位磨损比较均匀,其平均宽度以VB表示,而其最大宽度以
表示。
4)前后刀面同时磨损
在常规条件下,加工塑性金属常常出现前后刀面同时磨损的情况。
刀具的磨损过程及磨钝标准
5)刀具的磨损过程
如图4-15所示,刀具的磨损过程可分为三个阶段:
图4-15刀具的磨损过程
①初期磨损阶段新刃磨的刀具表面较粗糙,并存在显微裂纹、氧化或脱碳等缺陷,而且切削刃较锋利,后刀面与加工表面接触面积较小,压应力较大,所以容易磨损。
②正常磨损阶段经过初期磨损后,进入比较缓慢的正常磨损阶段。
后刀面的磨损量与切削时间近似地成比例增加。
正常切削时,这个阶段时间较长,是刀具的有效工作时间。
③急剧磨损阶段当刀具的磨损带达到一定程度,后刀面与工件摩擦过大,导致切削力与切削温度迅速升高,磨损速度急剧增加。
生产中为了合理使用刀具,保证加工质量,应该在发生急剧磨损之前就及时换刀。
6)刀具的磨钝标准
刀具磨损到一定限度后就不能继续使用,这个磨损限度称为磨钝标准。
ISO标准统一规定以1/2背吃刀量处的后刀面上测定的磨损带宽度VB作为刀具的磨钝标准。
自动化生产中的精加工刀具,常以沿工件径向的刀具磨损尺寸作为刀具的磨钝标准,称为径向磨损量NB。
在国家标准GB/T16461-1996中规定高速钢刀具、硬质合金刀具的磨钝标准见表4-1。
表4-1高速钢刀具、硬质合金刀具的磨钝标准
工件材料
加工性质
磨钝标准VB(
)
高速钢
硬质合金
碳钢、合金钢
粗车
1.5~2.0
1.0~1.4
精车
1.0
0.4~0.6
灰铸铁、可锻铸铁
粗车
2.0~3.0
0.8~1.0
半精车
1.5~2.0
0.6~0.8
耐热钢、不锈钢
粗车、精车
1.0
1.0
8)刀具寿命
在实际生产中,为了更加方便、快速、准确地判断刀具的磨损情况,一般以刀具寿命来间接地反映刀具的磨钝标准。
刀具寿命T的定义为:
刀具由刃磨后开始切削,一直到磨损量达到刀具的磨钝标准所经过的总切削时间(单位min)。
刀具寿命反映了刀具磨损的快慢程度。
刀具寿命长表明刀具磨损速度慢;反之表明刀具磨损速度快。
影响切削温度和刀具磨损的因素都同样影响刀具寿命。
刀具寿命是一个具有多种用途的重要参数,如用来确定换刀时间;衡量工件材料切削加工性和刀具材料切削性能优劣;判定刀具几何参数及切削用量的选择是否合理等,都可用它来表示和说明。
6.提高切削加工质量的途径
零件的加工质量包括加工精度和表面质量两部分。
切削加工时,影响零件加工质量的因素很多。
以下主要讨论刀具以及切削用量对加工质量的影响。
合理选用刀具角度
1)前角对刀具的切削影响最大。
选择前角的原则是既要保证刃口锋利,也要保证其强度。
用硬质合金车削钢材时可取10°~25°;车削灰铸铁可取5°~15°;车削铝合金可取30°~35°。
强力切削时,为增强刀具的强度,则采用负的前角。
2)后角用来减小主后面与工件过渡表面之间的摩擦,并与前角共同影响刃口的锋利程度与强度。
后角的选择原则是在保证加工质量和刀具耐用度的前提下,尽可能取小值。
粗加工时后角应小些(可取6°~8°);精加工时应取较大的后角(10°~12°)。
3)主偏角的大小间接影响刀具的耐用度,工艺系统刚性差时,必须选用较大的主偏角。
一般主偏角在30°~75°之间选取,加工细长轴类的工件时要选用90°的主偏角。
4)副偏角的主要作用是减小副切削刃与已加工表面的摩擦。
外圆车刀的副偏角常取6°~10°。
粗加工时可取得大一些;精加工时可取得小一些。
为了降低已加工表面的粗糙度数值,有时还可磨出一段副偏角为零的修光刃。
5)刃倾角主要作用是影响刀尖的强度和控制切屑的流向。
粗车一般钢材和灰铸铁时,常取
=-5°~0°,以提高刀尖强度;精车时常取
=0°~5°,以防止切屑划伤已加工表面。
刃倾角及其作用见图4-16。
图4-16刃倾角对切屑流向的控制
合理选择切削用量
以车削为例的选择原则为:
粗加工主要目的在于尽快切除加工余量,以提高生产率,降低成本。
因此,在生产中应首先根据工件的加工余量合理选择背吃刀量。
若工艺系统刚度好,应尽可能选大值;若工艺系统刚度差,应按刚度选取。
然后,根据加工条件选择尽可能大的进给量,再按刀具耐用度的要求选择一个合适的切削速度。
精加工目的在于保证加工精度和表面质量。
为保证表面质量,首先应确定合理的切削速度。
硬质合金刀具耐热性好,可选用较高切削速度;高速钢刀具耐热性差,多选用较低的切削速度。
其次,再根据加工精度和表面粗糙度的要求,选择合适的进给量和背吃刀量。
三、金属切削机床
本节要点:
金属切削机床的分类与型号;机床的传动链与切削运动计算。
金属切削机床是用切削的方法将金属毛坯加工成机器零件的一种机器,人们习惯上称为机床。
机床是机械制造系统中最重要的组成部分,它为加工过程提供刀具与工件之间的相对位置和相对运动,为改变工件形状、质量提供能量。
1、机床的分类
根据国家标准GB/T15375-94,按加工性质和所用刀具的不同,机床可分为12大类:
车床、钻床、镗床、磨床、齿轮加工机床、螺纹加工机床、铣床、刨插床、拉床、特种加工机床、锯床和其它机床。
按机床通用性程度,可分为:
通用机床(或称万能机床)、专门化机床和专用机床三类。
通用机床适用于单件小批量生产,加工范围较广,可以加工多种零件的不同工序。
例如普通车床、卧式镗床、万能升降台铣床等;专门化机床用于大批量生产中,加工范围较窄,可加工不同尺寸的一类或几类零件的某一种(或几种)特定工序。
例如,精密丝杠车床、曲轴轴颈车床等;专用机床通常应用于成批及大量生产中,这类机床是根据工艺要求专门设计制造的,专门用于加工某一种(或几种)零件的某一特定工序。
例如,加工车床导轨的专用磨床、加工车床主轴箱的专用镗床等。
在同一种机床中,按加工精度的不同,可分为:
普通精度级、精密级和高精度级机床。
按机床的质量和尺寸不同,可分为:
仪表机床、中型(一般)机床、大型机床(质量达10t)、重型机床(质量30t以上)、超重型机床(质量在100t以上)。
按机床自动化程度,可分为:
手动、机动、半自动和自动机床。
此外,机床还可以按主要工作器官的数目进行分类,如:
单刀机床、多刀机床、单轴机床、多轴机床等。
2.机床型号的编制方法
机床的型号是用来表示机床的类别、主要参数和主要特性的代号。
目前,机床型号的编制采用汉语拼音字母和阿拉伯数字按一定规律组合表示。
例如,CM6132型精密卧式车床,型号中的代号及数字的含义如下:
CM6132
主参数代号(床身上最大回转直径320mm)
机床系别代号(卧式车床系)
机床组别代号(落地及卧式车床组)
机床通用特性代号(精密机床)
机床类别代号(车床类)
(一)通用机床型号的编制方法
(1)机床的类代号用大写的汉语拼音字母表示,并按相应的汉字字意读音。
当需要时,每类又可分为若干分类,分类代号用阿拉伯数字表示,放在类代号之前,但第一分类不予表示。
机床的类代号、分类代号及其读音见表8-5。
表4-2机床类代号和分类代号
类别
钻床
镗床
磨床
齿轮加工机床
螺纹加工机床
铣床
刨插床
拉床
锯床
其它
序号
Z
T
M
2M
3M
Y
S
X
B
L
G
Q
读音
钻
镗
磨
二磨
三磨
牙
丝
铣
刨
拉
割
其
(2)机床的通用特性和结构特性代号通用特性代号位于类代号之后,用大写汉语拼音字母表示。
。
如“CK”表示数控车床;“MBG”表示半自动高精度磨床。
对于主参数相同,而结构、性能不同的机床,在型号中用结构特性区分。
如CA6140中的“A”和CY6140中的“Y”,均为结构特性代号,它们分别表示为沈阳第一机床厂和云南机床厂生产的基本型号的卧式车床。
表4-3机床通用特性代号
通用特性
高
精度
精
密
自
动
半自动
数
控
加工中心(自动刀)
仿
形
轻
型
加重型
简式或经济型
柔性加工单元
数
显
高
速
代号
G
M
Z
B
K
H
F
Q
C
J
R
X
S
读音
高
密
自
半
控
换
仿
轻
重
简
柔
显
速
(3)机床的组别、系别代号组、系代号用两位阿拉伯数字表示,前一位表示组别,后一位表示系别。
每类机床按其结构性能及使用范围划分为用数字0~9表示的10个组。
在同一组机床中,又按主参数、主要结构及布局型式划分为用数字0~9表示的10个系。
(4)机床主参数、设计顺序号及第二主参数机床主参数是表示机床规格大小的一种尺寸参数。
例如,CA6140型卧式机床中主参数的折算值为40(折算系数是1/10),其主参数表示在床身导轨面上能车削工件的最大回转直径为400mm。
某些通用机床,当无法用一个主参数表示时,则用设计顺序号来表示。
第二主参数是对主参数的补充,如最大工件长度、最大跨距、工作台工作面长度等,第二主参数一般不予给出。
(5)机床的最大改进顺序号当机床的性能及结构有重大改进,并按新产品重新设计、试制和鉴定时,在原机床型号尾部加重大改进顺序号,即汉语拼音字母A、B、C……。
根据通用机床型号编制方法,举例如下:
(1)MG1432A:
表示高精度万能外圆磨床,最大磨削直径为320mm,经过第一次重大改进,无企业代号。
(2)Z3040×16/S2:
表示摇臂钻床,最大钻孔直径为40mm,最大跨距为1600mm,沈阳第二机床厂生产。
(3)CKM1116/NG:
表示数控精密单轴纵切自动车床,最大车削棒料直径为16mm,宁江机床厂生产。
(二)专用机床型号的编制方法
设计单位代号同通用机床型号中的企业代号。
设计顺序号按各单位设计制造专用机床的先后顺序排列。
例如,B1-015:
表示北京第一机床厂设计制造的第15种专用机床。
3、零件表面的切削加工成形方法和机床的运动
零件表面的切削加工成形方法
机械零件的任何表面都可以看作是一条线(称为母线)沿另一条线(称为导线)运动的轨迹。
如图4-17所示。
图4-17零件表面的形成
1—母线;2—导线
母线和导线统称为发生线。
切削加工中发生线是由刀具的切削刃与工件间的相对运动得到的。
刀具和工件之间的相对运动都是由机床来提供。
机床的运动
机床在加工过程中,必须形成一定形状的发生线(母线和导线),才能获取所需工件表面形状。
因此,机床必须完成一定的运动,这种运动称为表面成形运动。
此外,还有多种辅助运动。
(1)表面成形运动表面成形运动按其组成情况不同,可分为简单成形运动和复合成形运动二种。
如果一个独立的成形运动是单独的旋转运动或直线运动,则此成形运动称为简单成形运动。
例如,用车刀车削外圆柱面时(见