电器壳体塑料模设计.docx
《电器壳体塑料模设计.docx》由会员分享,可在线阅读,更多相关《电器壳体塑料模设计.docx(28页珍藏版)》请在冰豆网上搜索。
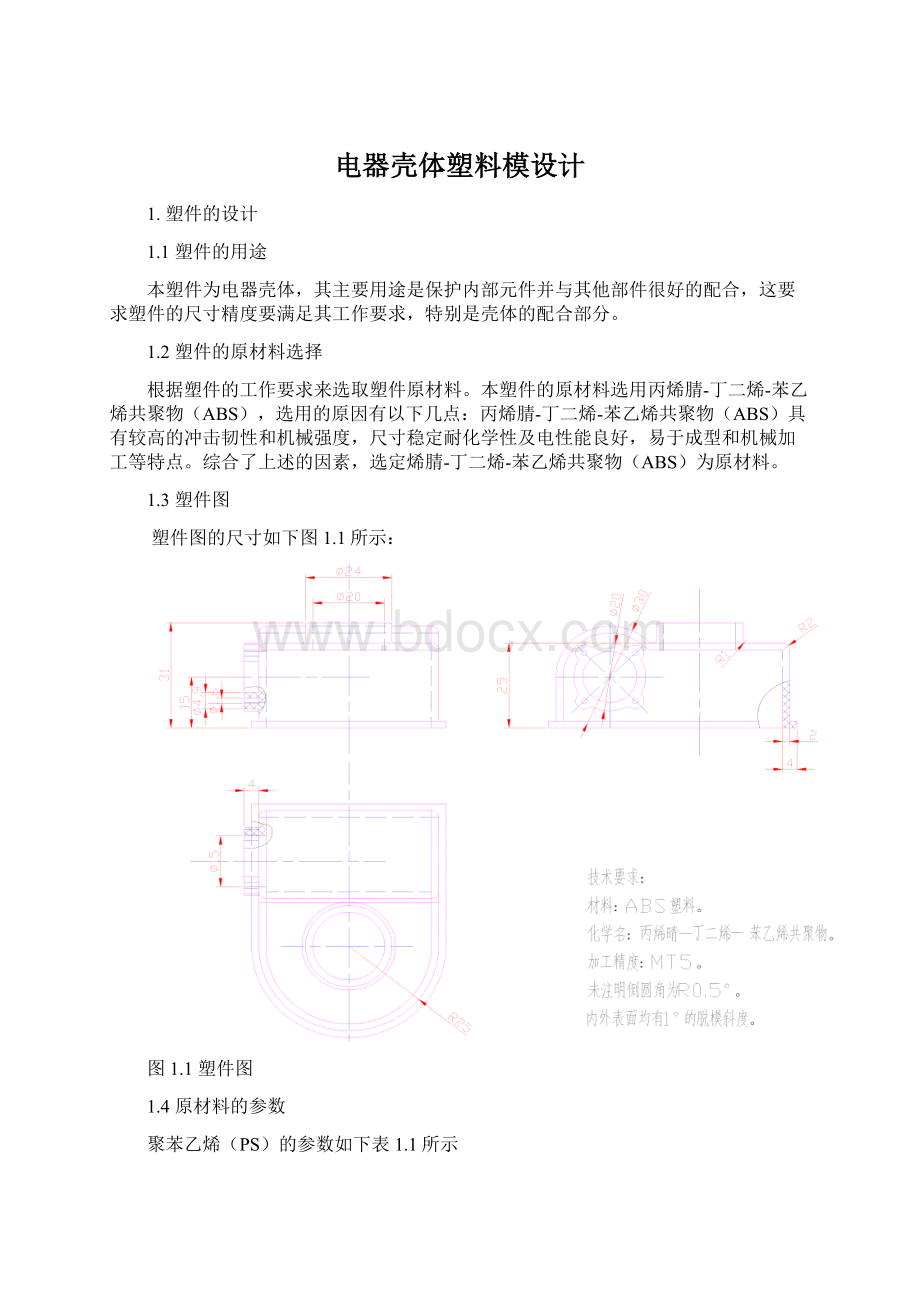
电器壳体塑料模设计
1.塑件的设计
1.1塑件的用途
本塑件为电器壳体,其主要用途是保护内部元件并与其他部件很好的配合,这要求塑件的尺寸精度要满足其工作要求,特别是壳体的配合部分。
1.2塑件的原材料选择
根据塑件的工作要求来选取塑件原材料。
本塑件的原材料选用丙烯腈-丁二烯-苯乙烯共聚物(ABS),选用的原因有以下几点:
丙烯腈-丁二烯-苯乙烯共聚物(ABS)具有较高的冲击韧性和机械强度,尺寸稳定耐化学性及电性能良好,易于成型和机械加工等特点。
综合了上述的因素,选定烯腈-丁二烯-苯乙烯共聚物(ABS)为原材料。
1.3塑件图
塑件图的尺寸如下图1.1所示:
图1.1塑件图
1.4原材料的参数
聚苯乙烯(PS)的参数如下表1.1所示
表1.1ABS的主要性能参数
性能
数据
成型收缩率/%
产品最高连续使用温度/℃
热变形温度/℃
拉伸强度(屈服点)/MPa
拉伸模量(屈服点)/MPa
洛氏硬度
体积电阻率/Ω·cm
介电常数/Hz
耐电弧/S
介电强度/kV·mm-1
0.4~0.7(0.5)
60~75
93~107
42.8~46.9
2346~2622
R108~118
(2~4)×1013
2.45×106~2.65×106
50~85
12~16
1.5原材料成型特性与工艺参数
表1.2ABS的成型与工艺参数
工艺参数
料筒温度/℃
后部
180~200
中部
210~230
前部
200~210
喷嘴温度/℃
180~190
模具温度/℃
50~70
注射压力/MPa
70~90
螺杆转速/(r·min-1)
30~60
1.6分析塑件
塑件产品生产批量小,所以采用一模一腔。
塑件简单采用整体型腔、型芯,侧孔采用导柱滑块成型。
采用两板式模具结构。
2.注射机的选用
2.1注射机的参数
选用卧式注射机的型号:
XS-Z-60;其主要参数如下表2.1所示
表2.1注射机的主要参数
项目
参数
项目
参数
理论注射容量/cm3
螺杆直径/mm
理论注射压力/MPa
塑化能力/g·s-1
注射速度/g·s-1
锁模力/Kn
中心顶出孔径/mm
60
25
122
4.0
35
500
50
模板最大开距/mm
模板最大厚度/mm
模板最小厚度/mm
喷嘴球半径/mm
模具定位环直径/mm
模板尺寸/mm
喷嘴前段孔径
180
200
70
12
55
330×440
3.5
2.2注射量的校核
根据生产经验,一个注射周期内所需注射的塑料容体的总量必须在注射机额定注射量的80%以内。
利用注射容量(cm3)来表示:
(2.1)
式中V—一个成型周期内所需注射的塑料容积,cm3;
Vz—单个塑件的容积,cm3;
Vj—浇注系统凝料和飞边所需的塑料容积,cm3;
n—型腔的数目。
21.76÷60,=36.3%<80%,符合设计要求
2.3锁模力的校核
在注射成型时,为了防止模具分型面被注射压力顶开,必须对模具施加足够的锁模力,否则在分型面处将产生溢料现象,因此注射机的额定锁模力必须大于注射压力。
(2.2)
式中F—注射机额定锁模力,N;
Az—制品在分型面上的垂直投影面积,mm2;
Aj—浇注系统在分型面上的垂直投影面积,mm2;
n—型腔的数目;
Pm—塑料熔体在型腔内的平均压力,MPa。
由于塑料熔体流经喷嘴,流道,浇口和型腔,将产生压力损耗,一般型腔内平均压力仅为注射压力P0的1/4~1/2,通常为20—40MPa.考虑到实际注射压力比注射机的额定注射压力小,所以选定型腔内平均压力为40MPa。
理论锁模力为500kN,选用注射机的锁模力符合设计要求。
2.4开模行程的校核
注射机采用液压式锁模机构,其最大开模行程与模具厚度有关。
塑件高(包括浇注系统)72mm,推出距离31mm,所以开模行程如下公式计算:
(2.3)
式中Sk—开模行程,mm;
H1—塑件高度(包括浇注系统),mm;
H2—塑件顶出距离,mm;
注射机的最大开模行程为180mm,所以符合要求。
3注射模具设计
3.1浇注系统的设计
3.1.1主流道衬套设计
主流道指紧接注射机喷嘴到分流道为止的那一段流道,熔融塑料进入模具时首先经过它。
它与注射机喷嘴在同一轴心线上,物料在主流道中不改变流动方向,主流道的形状一般为圆锥形或圆柱形,本设计为圆锥形。
主流道与喷嘴接触处作成半球形的凹坑,二者严密地配合,避免高压塑料熔体溢出,凹坑球半径R2应比喷嘴球半径R1大1mm~2mm,主流道小端直径比注射机喷嘴孔直径约大0.5mm~1mm,锥角一般取2º~6º,主流道的流道长度尽可能地短。
为了加工简单和模具的装配容易,所以设计成独立的流道衬套,选用优质钢材制作并经热处理提高硬度。
本设计的材料采用了ABS,塑件属于小型制品,浇口套与定位环设计为一体,根据材料的特性确定主流道的小端直径d为4mm,锥角取3º;凹坑球半径R2为14mm,在注射过程中注射机的喷嘴与凹坑球相撞,凹坑球半径大能避免注射机喷嘴漏料。
其主要形状和尺寸如下图3.1.1所示
图3.1.1主流道衬套
3.1.2分流道设计
分流道是连接主流道和塑件的那一部分流道,主要设计在分型面上,本设计是将分流道设计塑件上端孔的部分的分型面,分流道的断面为U形,这样有利于加工和熔料的流动。
分流道的分布形状如图3.1.2,考虑到开模时分流道与模具的分离,根据力学原理分别在左右瓣合模上设计一个分流道,利用滑块的运动使分流道与模具分离。
分流道的断面为半圆形,如图3.1.3所示。
图3.1.2分流道分布示意图图3.1.3分流道截面示意图
3.1.3浇口的设计
本设计采用边缘浇口,边缘浇口(又名为标准浇口、侧浇口)该浇口相对于分流道来说断面尺寸较小,属于小浇口的一种。
边缘浇口一般开在分型面上,具有矩形或近矩形的断面形状,其优点是浇口便于机械加工,易保证加工精度,而且试模时浇口的尺寸容易修整,适用于各种塑料品种,其最大特点是可以分别调整充模时的剪切速率和浇口封闭时间。
对于本设计来说,塑件是小型塑件可以利用边缘浇口的典型尺寸:
深1mm,宽2mm。
分流道与浇口连接处的形状、尺寸如图3.1.4所示。
图3.1.4浇口与分流道连接处
3.1.4浇口位置设计
浇口位置的选择很大程度决定了塑件的质量,所以浇口位置设计是注射模具设计一个很重要环节,本设计的浇口位置如图3.1.2所示,在这个地方进料能使物料同时到达模腔最远的地方。
3.1.5流动比的校核
浇口位置选择是否合适,利用流动比公式来计算,公式如下:
(3.1)
式中B—流动比;
Li—流路各段长度,mm;
δi—流路各段厚度,mm;
n—段数。
聚苯乙烯(PS)的流动比在压力60MPa下为300~280,选择这个浇口位置的流动比为49.65小于280,符合设计要求。
3.2分型面的选择
3.2.1主分型面选择
主分型面由塑件内表面及塑料件上面的孔的上端面及塑件下表面向四周延伸形成主分型面,如图3.2.1。
3.2.2侧向抽芯分型面选择
侧向抽芯分型面由侧孔的内端面及内表面、孔的外端面所在平面合并向外垂直延伸形成,如图3.2.2。
3.2.1主分型面3.2.2侧抽芯分型面
3.3排气系统设计
为使塑料熔体在填充模具型腔过程中同时要排除型腔及流到的原有的空气,所以要设计排气系统。
气体必须及时排出负责影响塑件质量。
本设计制品较小,模具型腔较小,塑件最后充满型腔的的部位在其模具分型面处。
所以本设计采用分型面间隙排气如图3.3.1
图3.3.1利用分型面排气
3.4成型零部件设计
3.4.1成型零部件的尺寸计算
模具的成型尺寸是指型腔、型芯上直接用来成型塑件部位的尺寸,主要有型腔和型芯的径向尺寸,型腔和型芯的深度或高度尺寸,中心距尺寸等。
在设计模具时根据制品的尺寸和精度要求来确定成型零件的相应的尺寸和精度等级,给出正确的公差值。
模具的成型尺寸的计算方法有按平均收缩率计算和按极限条件计算两大类,本设计采用平均收缩率来计算。
塑件的尺寸如图1.1所示,已知ABS的平均收缩率为0.5%,塑件未标注公差尺寸采用MT5。
(1)型腔的径向尺寸计算
型腔的径向尺寸计算的公式如下:
(4.1)
式中LM—模具型腔径向工作尺寸,mm;
LS—塑件径向尺寸,mm;
Scp—平均收缩率。
Δ—塑件尺寸公差,mm,差模塑体尺寸公差表得;
—为模具成型零件公差,差标准公差数值表得;
对于24mm的尺寸其实际尺寸Ls=24.0-0.22
模具型腔按IT10级精度制造,其制造偏差δZ=0.084
②对于25mm的尺寸其Ls=25.00-0.25
模具型腔按IT10级精度制造,其制造偏差δz=0.084
对于40mm的尺寸其Ls=40.00-0.28
LM=40+40×0.005-3/4×0.25=39.99
模具型腔按IT10级精度制造,其制造偏差δz=0.100
(2)型腔的深度尺寸计算[16]
型腔深度尺寸计算公式如下:
(4.2)
式中HM—型腔深度尺寸,mm;
HS—塑件深度尺寸,mm;
1对于15mm的尺寸其Ls=15.00-0.19
模具型腔按IT9级精度制造,其制造偏差δZ=0.070
②对于25mm的尺寸其Ls=25.00-0.25
模具型腔按IT10级精度制造,其制造偏差δZ=0.084
对于31mm的尺寸其Ls=31.00-0.28
模具型腔按IT10级精度制造,其制造偏差δZ=0.100
(3)型芯直径的计算
型芯的径向尺寸计算的公式如下:
(4.7)
对于20mm的尺寸其Ls=20+0.22
模具型腔按IT10级精度制造,其制造偏差δZ=0.084
对于25mm的尺寸其Ls=25+0.25
模具型腔按IT10级精度制造,其制造偏差δZ=0.084
(4)型芯高度尺寸的计算
型芯的高度尺寸计算的公式如下:
(4.7)
对于23mm的尺寸其Ls=23+0.22
模具型腔按IT10级精度制造,其制造偏差δZ=0.084
由于塑件为小型塑件,一些尺寸都在3mm以下,而小型塑件的尺寸主要受塑料收缩率的影响,ABS的平均收缩率为0.5%,因此那些成型部分的尺寸采用其名义尺寸。
3.4.2成型零部件的结构
〔1〕整体结构
因为型腔型芯结构简单因此本设计采用整体式,型腔型芯分别嵌入到定、动模板中镶块外形采用带轴肩的矩形台阶,然后分别从上下嵌入型腔型芯固定板中用垫板螺钉将其固定。
〔2〕型芯结构
本设计型芯结构如图3.4.2所示。
图3.4.2型芯图
型芯的材料采用优质钢材T8A,由于型芯要与推管摩擦,因此型芯要表面热处理,使其的硬度达到HRC55~60。
〔3〕型腔结构
本设计型腔如图3.4.3所示。
图3.4.3型腔示意图
3.5模具强度的校核
由于塑件其外形大体是矩形,故采用矩形组合式的计算强度公式来计算。
采用45号钢为侧壁与地板的材料。
其物理参数:
σp=200MPaE=2.1×105MPa.
3.5.1型腔侧壁厚度计算
〔1〕利用刚度公式计算
(5.1)
式中a—矩形型腔的侧壁厚度,mm;
l—矩形型腔长边尺寸,mm;
PM—型腔压力,MPa;
E—模具材料的弹性模量,碳钢为2.1×105MPa;
δ—刚度条件允许变形量,mm;
μ—模具材料泊松比,碳钢为0.25。
〔2〕利用强度公式计算
(5.2)
式中σ—模具材料的许用应力,碳钢为200MPa。
刚度和强度的比较,侧壁厚度应大于23.9mm,所以厚度选择为24mm。
3.5.2组合式型腔底板厚度计算
〔1〕利用刚度公式计算
(5.3)
式中S—型腔底板厚度,mm;
b—凹模矩形短边尺寸,MPa;
B—凹模外侧底面的宽度,mm;
〔2〕利用强度公式计算
(5.4)
式中σP—模具材料的许用应力,碳钢为200MPa。
刚度和强度的比较,满足刚度,强度要求,型腔底板厚度应大于31.76mm,取底板的厚度32mm。
3.6模架模板的选择
根据整体型腔镶块的大小及计算都得到的侧壁厚和底板厚的计算结果得:
模板的长宽分别是:
L:
107+24×2=155取标准模架参考值160mm;
B:
88+24×2=136取标准模架参考值160mm;
动模、定模底板为:
200×160.
选择模架A2型,如图3.6.1。
采用∅10×120销钉定位,用M10×120内六角螺钉进固定,其再动模底板的分布如图3.6.2所示;限位钉选择尺寸如图3.6.3所示;
3.6.1模架
3.7合模导向机构设计
3.7.1合模导向的导柱设计
导柱的直径在12mm~63mm之间,按经验其直径d和模板宽度B之比d/B在0.06~0.1之间,导柱的固定段的直径和导向段直径,其形位公差与尺寸公差之间的关系遵循包容原则,即轴的作用尺寸不得超过最大实体尺寸,而轴的局部实际尺寸必须在尺寸公差范围内。
导柱的端部做成半球形的先导部分,使其能顺利进入导向孔。
安装与模板间采用过渡配合H7/n6,导向段与导套孔间采用动配合H7/f6。
固定段表面的粗糙度为Ra1.6μm,导向段表面的粗糙度为Ra0.8μm。
材料采用优质钢材T8A,其具有硬而难磨的表面,坚韧而不易断的型芯,材料经过淬火硬度达到HRC55~60。
其结构如图3.7.1所示:
图3.7.1导柱示意图
3.7.2合模导向的导套设计
导套的主要作用是方便模板的加工和模具的维修。
导套与导柱之间的配合为动配合H7/f7,导套与模板之间的配合为过渡配合H7/m6。
其粗糙度内外表面均采用Ra1.6μm。
材料采用耐磨的优质钢材T8A,经过淬火表面硬度达到HRC50~55,比导柱的硬度低5度左右,这样工作时间久后磨损的是导套而不是导柱,导套的更换比导套容易。
其示意图如图3.7.2所示:
图3.7.2导套示意图
3.7.3导柱导套的位置分布
根据模具的大小和形状,在模具型腔的周边要设导柱和导套。
本设计采用是四根直径相同的导柱不对称的布置。
其在分型面的布置示意图如图3.7.3所示:
图3.7.3导柱、导套位置布置示意图
3.8脱模机构设计
3.8.1脱模力的计算
采用公式(7.1)进行计算
(8.1)
式中Fd—脱模力,N;
A—垂直抽芯方向型芯的投影面积,cm3。
E—塑料拉伸弹性模量,1.940;
ε—塑料收缩率,0.005;
t—塑件壁厚,mm;
α—斜度,1º;
μ—塑料泊松比,0.30;
f—摩擦因素,0.450;
L—型芯长度,mm。
=332.8
3.8.2脱模机构
本塑件是采用推杆脱模机构,其特点是推杆加工简单,安装方便,维修容易,使用寿命长。
为了方便塑件的整体脱模及不对塑件造成变形和损坏,所以推杆的分布如图3.8.1所示。
图3.8.1:
推杆分布图
3.8.3推杆尺寸的计算及机构设计
推杆受力的计算
每一推杆的平均受力
(8-2)
公式中:
Fd-脱模力;
n-推杆的数目;
推杆结构设计
推杆的直径按照公式(8.2)计算;
(8.3)
公式中;d-推杆的直径;
L-推杆长度;
=5.6
取推杆的直径为Ø6mm选用带台阶的推杆前端直径取Ø3mm。
为在推出塑件时推杆和型芯不发生干涉前端长度取40mm具体尺寸如图3.8.2。
材料选用T8A经退火处理,头部局部淬火,上段表面达到60-65HRC。
此外,拉料杆也具有推出塑件的浇道料的作用,前端尺寸直径为Ø5mm,具体尺寸如图3.8.3
图3.8.1推杆的示意图
图3.8.2拉料杆图
3.8.4复位机构设计
本设计采用复位杆复位,用4根复位根复位,具有可靠的性能用直径Ø10具体尺寸如图3.8.3所示。
图3.8.3复位杆
3.9侧抽机构设计
3.9.1抽芯距的确定与抽拔力的计算
〔1〕抽芯距的计算公式如下:
(9.1)
式中S—抽芯距,mm;
S1—取出塑件最小尺寸,mm;
〔2〕抽拔力的计算公式(8.1):
=26.57
3.9.2斜导柱分型抽芯机构的设计
斜导柱分型抽芯是应用最广的分型抽芯机构,它借助开模力完成侧向抽芯,结构简单,制造方便,动作可靠。
其结构如图3.9.1所示,滑块装在燕尾型导滑槽内,可沿着抽拔方向平稳滑移,驱动滑块的斜导柱与开模运动方向成斜角安装,斜导柱与滑块上对应的孔呈松动配合,开模时斜导柱与滑块发生相对运动,斜导柱对滑块产生一侧向分力,迫使滑块完成抽芯动作。
图中的限位挡钉和弹簧的作用是完成抽拔动作后对滑块起定位作用,使它停留在与斜导柱脱离时的位置上,以便合模时斜导柱能准确进入斜孔驱动其复位,楔紧块的作用是在闭模时压紧滑块,以免注塑时滑块受到塑料压力移位。
图3.9.1斜导柱分型抽芯机构示意图
〔1〕斜导柱
斜导柱的长度计算
当滑块抽出的方向与开模方向垂直(图3.9.1所示)斜导柱的长度计算公式如下:
(9.3)
式中L—斜导柱的总长度,mm;
D—大端的直径,mm;
S—抽拔距,mm;
d—导滑段的直径,mm;
h—固定模板厚度,mm;
α—斜导柱的倾斜度,18°。
斜导柱直径的计算:
斜导柱收受侧压力
斜导柱所受弯矩
斜导柱的直径用强度理论计算直径
--斜导柱许用弯曲应力;查表的T8A为120-160,取160。
斜导柱直径取10满足要求,斜导柱的斜角一般为15°~20°,最大不得超过25°,本设计采用18°,材料采用优质钢材T8A,淬火硬度HRC55~60。
其具体尺寸如图3.9.2
图3.9.2斜导柱
(2)滑块本设计的是组合滑块,与侧抽型芯用销钉连接,如图8.3所示,材料采用45号钢,成形部位采用局部热处理达到要求硬度。
图8.3瓣合模滑块示意图
(3)导滑槽对导滑槽与滑块的配合要求运动平稳,不宜过分松动,亦不宜过紧,因此本设计采用燕尾型导滑槽,其结构如图8.4所示。
导滑部分的表面应有足够硬度,但在本设计中,滑块成形了塑件的外形为了减少制造成本,所以导滑槽的导滑部分表面硬度应稍低滑块的硬度。
图8.4导滑槽示意图
〔4〕楔紧块当塑料熔体注射入型腔,它以很高的压力作用于侧抽型芯,迫使滑块外移。
作用力等于塑料压力和沿滑动方向塑料作用在型芯或模块上投影面积的乘积。
由于斜导柱的刚度较差,故常采用楔紧块面来承受这一侧向推力,同时斜导柱的精度不能保证滑块准确定位,而精度较高的楔紧面在合模时能确保滑块位置的精确性,其斜度一般比斜导柱大2°~3°本设计采用大2°,其示意图如图8.5所示。
图8.5楔紧块示意图
3.9.3最小开模行程的计算
最小开模行程是指抽出侧滑块所必需的开模运动距离H,其公式如下:
(9.4)
式中H—最小开模行程,mm;
S—抽拔距,mm;
α—斜导柱斜度,20°。
3.10冷却系统的设计
3.10.1冷却尺寸的确定
ABS塑料在成型时:
喷嘴温度为170-180ºC;
模具温度为50-80ºC;
成型周期50-220s
冷却回路所需的总表面积可按下式计算:
(9.1)
式中Q—单位时间内塑料传给模具的热量,kj/h;
m—每次注入模具中塑料的质量(包括浇注系统料),kg/h;
n—每小时的注塑数,n=3600/80=45;
q—单位质量的塑料在型腔内散发热量Kj/kg;
=336
冷却水带走热量计算:
塑料熔体在注射模具中稳定注塑时其热量95%由冷却水带走:
(9.2)
式中:
QW—单位时间内模具由冷却水带走的热量,KJ/h;
Q—单位时间内塑料传给模具的热量,KJ/h
KJ
热传导面积的计算:
a.冷却水对管壁的传热系数的计算:
(9.3)
公式中:
hw—冷却水的传热系数,℃;
θw—冷却水的平均温度,取平均水温为35℃;
v—冷却水的流速,m/s,1.66m/s;
dw—冷却水道的直径,m。
b.热传导面积的计算:
(9.4)
公式中:
A—热传导面积,m2
△θ—模具型腔表面的平均温度与冷却水道温度差值,取2ºC;
〔2〕冷却水路总长度的计算
其计算公式如下:
(9.5)
式中L—冷却水路总长度,mm;
A—冷却水路总面积,mm2;
dw—冷却水管的直径,mm。
模板中单条水管长度为160mm,因此开设4条冷却水路,总长度为640mm,能满足条件。
3.10.2冷却水路的分布
为了降低加工难度,水路采用直通式,其结构如下图10.1所示:
图10.1冷却水路分布示意图
3.11.
标准件
标准
4.设计说明
4.1动作原理:
本设计为两板式模具,开模过程中注塑机带动动模向下运动。
塑件紧抱型芯以及拉料杆的作用,使塑件及浇注系统凝料全部留在动模一侧。
在开模过程中斜导柱带动滑块,滑块带动侧抽型芯向左运动完成侧抽芯。
模具完全打开后,注塑机顶针推动顶出板,顶出板带动顶杆及拉料杆将塑件顶出。
合模时复位杆顶到定模上完成顶杆及拉料杆的复位,同时斜导柱带动滑块及侧型芯复位。
开始下一次的注射。
5.设计总结
这次课程设计经过我独立思考,严格按照任务书上的要求一步一步完成的。
在设计的过程中,不断地查找资料,做到设计计算和绘图同时进行,遇到问题解决问题,反复检查修改,最终完成了设计。
在本次设计中总结了以下:
各个部分设计时都不是独立的,再设计中要有整体意识,个部分设计时都要综合考虑。
设计中应多查资料。
由于本人水平有限,在设计过程中难免有许多不足之处,欢迎老师批评指正,在此先表谢意!
参考文献
[1]申开智.塑料模具设计.北京:
中国轻工业出版社,2004
[2]邹继强.塑料模具设计参考资料汇编.清华大学出版社,2005
[3]齐卫东.简明模具设计手册.北京理工大学出版社,2008
[4]张思惠.塑料材料学,西北工业大学出版社,2000