烧成系统调试及投料.docx
《烧成系统调试及投料.docx》由会员分享,可在线阅读,更多相关《烧成系统调试及投料.docx(33页珍藏版)》请在冰豆网上搜索。
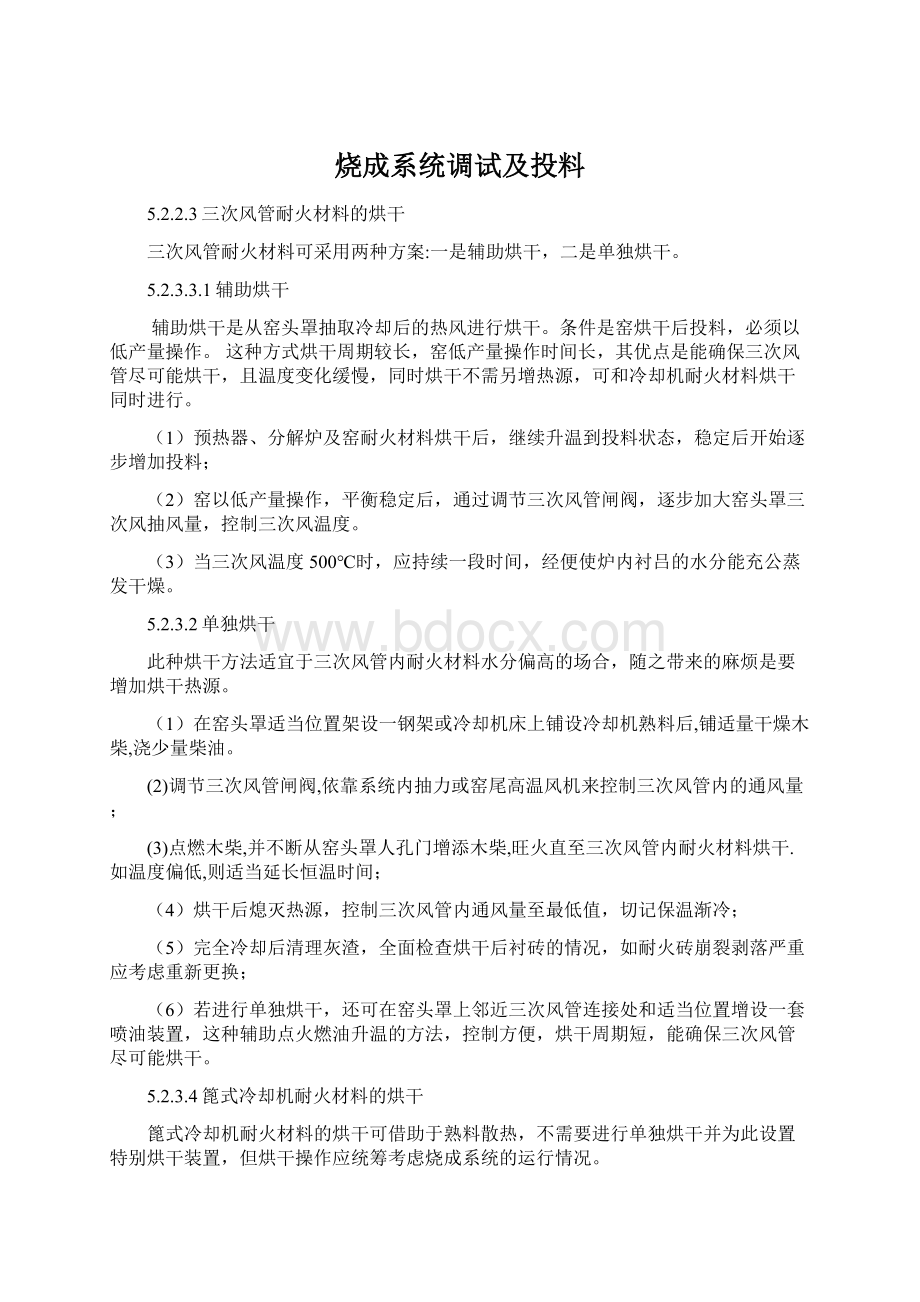
烧成系统调试及投料
5.2.2.3三次风管耐火材料的烘干
三次风管耐火材料可采用两种方案:
一是辅助烘干,二是单独烘干。
5.2.3.3.1辅助烘干
辅助烘干是从窑头罩抽取冷却后的热风进行烘干。
条件是窑烘干后投料,必须以低产量操作。
这种方式烘干周期较长,窑低产量操作时间长,其优点是能确保三次风管尽可能烘干,且温度变化缓慢,同时烘干不需另增热源,可和冷却机耐火材料烘干同时进行。
(1)预热器、分解炉及窑耐火材料烘干后,继续升温到投料状态,稳定后开始逐步增加投料;
(2)窑以低产量操作,平衡稳定后,通过调节三次风管闸阀,逐步加大窑头罩三次风抽风量,控制三次风温度。
(3)当三次风温度500℃时,应持续一段时间,经便使炉内衬吕的水分能充公蒸发干燥。
5.2.3.2单独烘干
此种烘干方法适宜于三次风管内耐火材料水分偏高的场合,随之带来的麻烦是要增加烘干热源。
(1)在窑头罩适当位置架设一钢架或冷却机床上铺设冷却机熟料后,铺适量干燥木柴,浇少量柴油。
(2)调节三次风管闸阀,依靠系统内抽力或窑尾高温风机来控制三次风管内的通风量;
(3)点燃木柴,并不断从窑头罩人孔门增添木柴,旺火直至三次风管内耐火材料烘干.如温度偏低,则适当延长恒温时间;
(4)烘干后熄灭热源,控制三次风管内通风量至最低值,切记保温渐冷;
(5)完全冷却后清理灰渣,全面检查烘干后衬砖的情况,如耐火砖崩裂剥落严重应考虑重新更换;
(6)若进行单独烘干,还可在窑头罩上邻近三次风管连接处和适当位置增设一套喷油装置,这种辅助点火燃油升温的方法,控制方便,烘干周期短,能确保三次风管尽可能烘干。
5.2.3.4篦式冷却机耐火材料的烘干
篦式冷却机耐火材料的烘干可借助于熟料散热,不需要进行单独烘干并为此设置特别烘干装置,但烘干操作应统筹考虑烧成系统的运行情况。
(1)尽可能采用长时间自然通风干燥;
(2)为防止冷却机耐火材料温度骤增,窑低产量运转应不少于48小时,操作可兼顾三次风管耐火材料的烘干同时进行;
(3)如果窑运转负荷在投料初期就较高,也可开大前几台冷却风机风量或起动冷却机喷水系统,减慢烘干速度;
(4)若操作运行前确认冷却机耐火材料有必要进行强制烘干,还可采用在
篦床上焚烧木柴的办法。
但必须事先地篦床上铺设冷熟料或耐火砖,防止局部过热造成篦板变形。
5.2.3.5衬料烘干操作的注意事项
(1)稳定喷油喷煤燃烧的火焰,不冒黑烟;
(2)防止烧成带耐火材料经受急剧的局部过热;
(3)防止由于窑筒体不均匀受热膨胀,造成对支承装置不良影响;
(4)随时注意监控窑筒体、窑尾及一级旋风筒出口的温度;
(5)密切监测窑托轮、液压挡轮、减速机等的轴承润滑状况和轴承温度;
(6)系统升温情况不得较大地偏离拟定的烘干升温曲线要求,并注意随时转窑;
(7)烘干过程中,一定要注意喷油量、喷煤量、各类风门开度的调节幅度不得过大,以免造成超温超载而损坏内衬或设备;
(8)烘窑时间,切记由于温度及二次风温较低,烯料状态不良,有爆燃回火或突然熄灭的危险。
5.3系统起动及停车操作
5.3.1第一次投料运转
烧成系统耐火材料结束后,如确证没有必要熄灭进行内部检查,一般接着进行投料运转.操作时应持稳妥、积极的态度,既要做好充分的准备,又不可过于紧张,不敢大胆操作;要力争抓住时机,较快地达到稳定燃烧,挂好窑皮,提高产量。
经验证明:
对于窑外分解窑,产量过低反而易出工艺故障,产量高时却有利于稳定制作,故应打破陈规,如无设备故障,应力争稳定地突破“操作死区,在初次点火投料后3`~5天内基本达到正常生产。
5.3.1.1投料前的进一步准备工作
1、记录烘干后耐火材料的情况;
2、确认检查门、人孔门、清扫门等全部关闭;
3、确认吹堵的压缩空气管路畅通;
4、进行系统、各部位温度的检查,投料前1小时内要拆除各级旋风筒下料翻板阀的固定铁丝,并调整妥当;
5、确信系统所有机电设备、各种计测仪表能够正常连续工作;
6、核实煤粉仓中的煤粉、均化库中生料能满足生产初期的要求储量;
7、选择好熟料输送线路并确信链斗输送机能长期正常运行;
8、若烘窑前就计划准备一次投料运转,最好预先在冷却机篦床上均匀铺设约200mm厚冷熟料或碎石灰石的料层,以确保篦板免受烧损;
9、原料粉磨与废气处理、生料均化与入窑等其它相关车间应做好随时负载运行的准通讯联络顺畅;
10、准备好各种清理、捅料、检修、安全防护等设施与设备,保证能随时取用。
5.3.1.2投料操作
1、开始喂料
(1)增加窑头喂煤量,按照点火升温曲线继续升温;
(2)起动冷却机的各台风机、熟料电收尘器引风机以及其它设备。
注意各离心风机走动前应关闭相应的调节风门;
(3)调节系统通风量及窑头煤粉燃烧的一、二次风量,监测系统各部位的温度和压力;
(4)控制窑尾温度950~1000℃,一级旋风筒出口温度360~400℃时开始投料;
(5)开始以总喂料量的15~20%喂料;
(6)系统投料后,及时将窑的辅助传动改为主传动,并采取低速转窑的方案,防止大量生料涌入烧成带。
尽可能保证首批物料的烧成,以避免物生烧引起扬尘,降低窑内的能见度,给操作观察窑内状况和进一步加料带来困难。
喂料之初,烧成热耗约为1100~1300Kal/kg.Cl;
(7)密切观察窑内状况,一级旋内筒出口温度和压力,随时调节风、煤、料使之匹配。
2、加料操作
(1)根据窑内及预热器情况,逐渐加快窑速,并相应逐渐加料至设计能力的60%左右,煤粉量随时喂料量增加,加煤操作应缓慢、稳定;
(2)加料幅度不宜大,可控制≤20t/h,每次加料5t左右;
(3)加料过程中,窑尾温度应控制在950~1100℃一级旋风筒出口温度在320~360
℃。
若窑尾温度低于950℃时应减缓或停止加料;
(4)根据加料量、加煤量及系统温度、压力的变化,及时调整风量。
在此期间,应注意系统各部位的温度、压力变化,不要破坏窑内稳定;同时还要严密注意各级下料翻板阀的动作,加强巡回检查,发现堵塞情况要及时果断处理;
(5)调整火焰活泼有力,明亮完整,不冲刷耐火砖或窑皮,从投料开始到挂窑皮结束需48小时。
3、冷却机的操作
(1)加料、加煤的同时,逐渐加大各风室风量,一般原则如下:
冷却机加风顺序:
先高温段、后低温段;
冷却杨减风顺序:
先低温段、后高温段;
在投料初期,高温段风机内门相对大些,低温段风机风门相对小些,度与熟料电收尘引风机一起按窑头罩负压-20~50Pa来调节风门;
(2)加料的同时,起动冷却机篦速慢慢运行,也可时开进停,使熟料均匀散开并能保持一定的厚度;根据篦床上熟料红亮程度、各风室内气体温度及窑的风量要求,分别调节各内室风量,从而尽可能提高二、三次风温,不至于造成风量过大吹穿料层短路;
(4)当窑的产量达到正常指标时,要检查冷却机出口熟料温并依此来调节冷却风量;当总的冷却风量超过窑和分解炉燃烧的需要时,应通过篦冷机废气引风机在控制窑头罩负压的基础是将多余废气排出;
(5)当冷却机废气温度超过280℃时,开始向冷却机内喷水,并根据温度自动控制调节喷水量。
注意雾化水不能接触到冷却机内衬。
4、分解炉喷煤
在窑稳定运行2~4小时后,一般可进行分解炉喷煤。
(1)一般分解炉内的热风温度达到600℃以上就燃烧烟煤,窑稳定运行2~4小时后,分解炉内的热风温度已达900℃以上。
(2)起动分解炉供煤系统,确认分解炉内煤粉着火,并进一步缓慢提高三次风秋热风阀的开度,增加三次风量;
(3)同时逐渐增加窑喂料量;
(4)逐渐增加窑速,最终为2.5~3.5r/min之间;
(5)加大烧成系统的排风量,最终使一级旋风筒出口负压约4000~4200Pa,CO在0.5%以下,O2在3.5~4%;
(6)增加、调整窑与分解炉的喂煤量,最终热耗为720Kal/kg.Cl左右,窑与分解炉的用煤比例大体是:
窑:
分解炉=40:
60;
(7)根据综合判断、及时加煤加煤;
(8)加料同时,增加系统排风量与冷却机各负室风量,增加冷却机篦床速度;
(9)分解炉喷煤过程中,由于总喂料量大幅度增加,窑内工况变化大,操作应密切注意系统温窑尾与分解炉有压力变化,密切观察注意窑内情况,及时调整各种参数,加煤量、喂煤量、排风量调整幅度不宜过大,处理好风、煤、料、窑速的平衡,稳定系统热工制度;
(10)烧成系统各部位的主要操作参数大体如下:
--一级旋风筒出口温度300~330℃
--一级旋风筒出口O2含量3~5%
--一级旋风筒出口CO含量<0.5%
--分解炉内温度850~900℃
-- 窑尾温度1100~1200℃
--窑尾O2含量1.0~2.0%
--烧成带温度1350~1500℃
--窑头罩负压-20~-50Pa
--二次风温度>900℃,三次风温度>700℃
--烧成带的窑筒体温度250~400℃(视筒体冷却风机的开停而定)
(11)系统热工制度稳定后,确认各类计测仪表、机电设备正常,即可投票入中控回路自控操作。
5.3.1.3投料操作原则
带分解炉的大型回转窑在操作上是比较复杂的,尤其是从点火到正常运行的投料过程中,烧成系统工况变化更为频繁,所以要保证系统投料一闪成功有必要强调和遵循以下原则:
(1)控制住窑尾温度950~1000℃,一级旋风筒出口温度340~380℃,并能平衡稳定一段时间后才开始投料;
(2)随时监测系统主要控制点的温度和压力,因为这是运转操作中调节煤、料、风的主要参数;
(3)系统投料后在生料进入烧成带之前,将采取“留火等料”的操作方工,既要保证烧成带有一定的高温,砖面发红,又要防止过高温度使耐火砖结大块跑生料,所以采取低KH值与SM值的配料方案、严格控制生料成分、稳定烧成温度在1400℃左右、调整良好在火焰形状与燃烧状态;
(4)从熟料进入冷却机开始到正常生产的整个操作过程中,应保证冷却机的冷却效率,控制合适的冷却风量和篦床速度,尽可能地提高二、三次风温,这对确保窑内燃烧气氛和烧结能力,以及分解炉顺利点火投料并较快地达到正常运行尤为重要;
(5)操作应持稳妥、积极的态度,敢于大胆操作,善于抓住时机,力争较快地突破易使系统热工制度紊乱的“操作死区”,达到正常和稳定运行;
(6)另外,具体操作中尤其需要注意以下三点:
煤料要对口,风、煤、料、窑速要平衡匹配,调节幅度不宜过大:
篦床上有热熟料时,应尽量避免停止冷却风,即使窑与篦床停止运行,也应将篦床上的熟料(至少是高温段)完全吹冷后才能停风;
加强现场巡回检查,密切注意预热器扣部位的压力监测,发现积料堵塞情况要及时果断处理。
特别严强调清料工作要安全、仔细,严防烫伤等意外事故。
5.3.2正常点火
正常点火操作,不存在耐火材料烘干及挂窑皮操作,是指短时间停机后重新起动的操作过程。
即使有时在窑内、分解炉内、三次风管内以及预热器局部更换了耐火内衬,也不需要特殊的操作,只需升温时间适当延长,开始投料时补窑皮便能顺利运转,操作方法基本相同。
1、正常点火操作前的准备
(1)确认各计测仪表、显示报警装置处于可工作状态;
(2)确认各种风机有风门、各类阀门、三次风管热风阀等操作灵活,并处于下限位置;
(3)确认操作要求、控制程序与选择设备一一对应;
(4)所以自控回路的自动、手动选择开关置于制作位置;
(5)检查所有润滑点的润滑情况,冷却用水、排水情况符合要求;
(6)检查所有检查门、清扫孔密闭;
(7)检查预热器上升烟道及废气管道,清除系统中积料;
(8)确认系统各部位下料翻板阀,活动件能活动灵活自如;
(9)确认有足够点火用燃油,点火装置可靠、齐备;
(10)检查冷却机及熟料链斗机运转可靠,尤其是篦板完好;
(11)检查窑内、预热分解炉内,冷却机、喷煤管、三次风管的耐火材料状况和窑皮状况,了解窑、三次风管、冷却机内的物料残余留量,仔细落实点火的必要条件,制定出切合实际的点火升温曲线;
(12)联系熟料入库中及进行熟料输送路线选择。
核实煤粉仓中煤粉、均化库中生料能满足生产初期的要求储量;
(13)确认熟料电收尘器及引风机、冷却风机、一次风机等关键设备能够长期连续运转;
(14)对设备巡视、工作平台楼梯、异常情况紧急处理等场合,均应充分清理,扫除杂物;同时还需检查挡板、栏杆、警告牌等劳保设施是否安全妥当;
(15)检查清扫、捅料、检修、照明、安全保护等用具准备齐全;
(16)确认综合检查结果,烧成系统所有设备可以运转,通知现场岗位工人及中控操作的人员;
2、正常点火操作
结合前述烧成系统耐火材料和烘干操作和第一次投料运转,正常点火操作方法基本上与上此类同,不再赘述。
不过以下几点需能上能下起注意:
(1)根据实际情况控制升温速率,防止温度骤变;
(2)预热器虽然都是回定的壳体,但投入使用前最好先进行通风试运转,持续时间不少于8小时。
在试运转中和试运转后,要详细检查各部位的异变情况。
5.3.3正常操作原则
带分解炉的大型回转窑需达到优质、高产、低消耗和长期、安全、稳定运转日目的,必须做到煤料对口和“五稳”(即喂料稳定、喂煤稳定、排风稳定、窑速稳定、一级旋风筒出口温度稳定),因而有必要强调和遵循以下几个操作原则:
(1)注意把握好点火关。
正确地制定不同情况下的“点火升温曲线”做好开车前的各项准备,其要点是让系统热工制度符合喂料量递增所需的热量;
(2)以炉为主,稳定窑头,稳定风、料,同步调整窑速和喂料为操作指导思想,综合判断工况条件,实现安全稳定运行;
(3)整个运转过程中,应保证冷却机的冷却效率,尽可能地提高二、三次风温,降低熟料出料温度,控制合适的冷却风量,在此期间,还应重视合理地配用一次风量的轴向风比例,控制好风煤比例及混合,从而保证其燃烧效率和理想的火焰状态;
(4)掌握也三次风量的窑内通风量的比例,掌握分解炉用煤量和窑头用煤量的比例,对于控制参数的调节,应稳宜慢,切忌大艳情大落;应综合兼顾,处理准确果断有效;
(5)在系统长期运转中有效在控制烧成带温度,窑尾温度,五级筒下料温度,四级下料温度,各旋风筒锥体负压\一级筒出口废气成份等重要参数,并密切监视本系统主机设备的安全报警;
(6)有较好技术和责任制心的操作人员,通过勤看火、勤观察、勤检查、勤联系,在各种情况发生时以迅速综合判断,采取正确的应变能力措施,使系统工作状态时时稳定在理想的操作控制范围内;
(7)具体操作中还需注意以下几点:
A、根据一级旋风筒出口废气分析来控制系统足够的通风,其风量不宜过大、过小,从而保证窑炉燃料完全燃烧,同时监测废气温度及CO的含量来保证电收尘器的正常工作;
B、煤粉没的燃烧完全的废气不能让其聚积在窑炉,预热器,风管地方,以免引起严重的爆炸事故和火灾;
C、冷窑点火或废气温度过低,均不能接通电收尘器的高压;
D、检查冷却机风室有无漏风及串风现象,提高密封效果;
E、操作中若有掉篦板现象发生,要及时停窑处理,防止篦板掉入破碎机中,造成破坏事故;
F、密切监测烧成带窑筒体温度不得超过450℃,保护窑皮和筒体;
G、进行熟料质量检验,生料与煤粉的品质检验,度根据反馈数据,实施各部分调整;
H、密切注意窗尾负压与各级旋风筒负压,以判断预热器有关部位是否积料、堵实、结皮,一旦发生应及时处理,特别注意清扫工作要安全、仔细,严防烫伤等意外事故;
I、原煤粉磨、煤粉制备系统的开停对有关风门等设备的操作,应预先和中控操作人员联系并同意后方可进行。
5.3.4正常停车
系统停车前事先把停车计划通知到原料粉磨,煤粉制备等车间,使其作好充分的准备,并随时联系,以便相互配合,原则上希望系统停车后,能做到窑空、煤粉仓空、生料库空、运输设备空,但主要还应当根据生产需要,停窑时间长短及工艺装备所限来决定生料库、煤粉仓是否要排空和库仓内生料、煤粉和剩余量。
另外,原料粉磨、煤粉制备系统需要关闭热风阀或使热风改向时,一定要与中控操作员联系并征得准许后方可进行有关设备的操作。
注意不要没有准备机而使烧成系统的气流突然变化、干扰窑的工作状况。
本系统停车时,所有自动调节回路和设备一般都应切换成手动位置,正常停车的顺序是:
炉减煤、窑减速、减料;先停煤、停料、后停窑,具体操作步骤如下:
1、分解炉的停车操作:
(1)根据热耗与温度,逐步减煤、相应减料;
(2)根据O2含量的变化,调节窑尾高温风机转速和阀门开度;
(3)适时停止一级旋风筒出口负压与系统排风量,减少冷却机各风室的风量;
(4)同时降低入窑喂料量,维持在SP窑操作状态;
(5)根据分解炉内温度变化和窑内情况,随时调节三次风管热风阀开度至合适状态;
(6)适当地降低窑速来保持正常烧结,同时调整窑头喂煤量。
2、窑的停车
(1)继续逐步降低窑转速,调整系统排风量和冷却机各室的风量;
(2)当窑尾温度偏高,一级旋风筒出口温度降低时,可以全闭三次风管热风阀;
(3)随时调节窑头喂煤量,既要保证相应的烧结温度,又不要使窑尾温度和一级旋内筒出口温度过高;
(4)当一级旋风筒出口温度下降到正常偏下且不再回升时,应立即停料。
逐级翻动下料翻板阀,清理各级旋风筒内的积料,必要时用吹堵系统清理。
若停料,一级旋风筒出口温度过高。
可打开一级筒人孔门或冷风阀;
(5)窑开始慢转。
当窑内物料基本排空时停煤,减少一次风机风量,保护喷煤管不被灼伤。
待喷煤管冷却至一定程度后,拉出窑头罩,切忌一次风量过大,使窑皮骤冷垮落;
(6)减风或停止窑尾高温风机。
注意此刻一定要使窑内温度缓慢下降,保护好窑皮和内衬。
注意一级旋风筒出口温度高于100℃时,应慢转窑尾高温风机,防止叶片变形;
(7)停窑操作过程中,窑慢转间隔要求大体如下:
0~小时,连续慢转;
1~3小时,每隔15分钟转1/4;
3~6小时,每隔30分钟转1/4;
6~12小时,每隔60分钟转1/4;
12~24小时,每隔120分钟转1/4;
24小时以后,根据窑内温度情况而定。
3、冷却机的停车操作
(1)根据窑、分解炉、预热器的风量要求,及时调整冷却风机的风门开度;
(2)窑缓慢减速、同步降低篦床速度,当窑停止向冷却机卸料后,应停止篦床推动,以保持熟料层。
若冷却机检修,则应排净篦床上物料后才停车;
(3)篦床停止运行后,应将篦床上的熟料完全次冷后方可停冷却风机,以保护篦板。
若需排净篦床上物料时,也应在冷却风机运转时进行;
(4)停熟料破碎机;
(5)待各风室内的细碎熟料全部排空后,才可停止篦下的拉链机;
(6)停冷却机的电动干油闰;
(7)各冷却风机全部停止后,停熟料电收尘器及引风机。
注意引风机停车前,一定要控制住窑头负压,以免热气体从窑头罩冒出、发生伤人事故;
(8)待熟料电收尘器回灰及设备的余料排净后相继停止熟料输送系统。
4、其它
(1)待预热器、窑、冷却机停止后,才能停止系统内的其余辅助配套设备。
才能停气、停水;
(2)关闭各种计测仪表、电气设备;
(3)记录停车时间和停机情况,报告生产调度。
5.3.5故障停车和重新启动
1、故障停车
故障停车包括设备故障停车两种。
对于设备故障停车,一般来说其停车顺序、速度均取决于设备之间的联锁关系或PC控制,不能在现场人为地加以干涉,而工艺故障停车在许多情况下其停车顺序、时间都可以人为地加以选择,也往往需要对PC控制解锁来灵活实施处理故障的手段,但不管发生哪一种故障,我们建议其操作处理原则必须遵循以下步骤:
(1)根据仪表的显示及报警,对故障原因、排除故障所需时间,对工艺生产、设备安全的影响程度及时作出准确的判断,并找出有效的处理办法;
(2)尽可能在中控室进行处理,尽可能快地恢复正常生产;
(3)设备单机停车;
(4)分系统停车;
(5)全系统停车;
此外,无论任何原因造成的停窑,都必须使窑系统的冷却过程尽可能缓解,尽量减少进入系统的冷风量,以避免窑皮的内衬受骤冷损坏。
当停窑时间估计不超过4小时,且故障很快排除,可实行“养火”保温措施,间隔或连续地在窑头喷入少时煤粉,从而为系统重新起动,尽快投入正常运转创造条件;
2、重新起动
在重新起动窑时不得将还未燃尽的煤粉及带有未燃烧的气体积存在窑内和预热器的管道内,以免引起爆炸。
为此应当遵循下列操作原则:
(1)短时停窑后,重新给窑升温时也可燃油辅助加热。
(2)风量不足时,不能喷入煤粉。
(3)若窑的温度较低或在调整火焰时,喷煤量不能突然增加。
(4)若需要调节一次风和二次曲时,要缓慢地进行,切忌猛增猛减。
(5)分解炉的喷煤应视故障停车时间的长短和重新起动时的系统工况条件酌情而定。
(6)若故障停车时进行窑慢转而造成冷却机一段篦床上堆积物料过多,重新起动时要进行篦板的检查,并在起动初期尽快送走堆积熟料。
(7)故障停车较长时间后的冷窑重新起动。
重新点火、升温、投料可参考前述有关条文并酌情调整。
5.3.6常见故障及处理
常见故障
可能的原因或现象
主要操作处理
油泵跳闸
1、电气设备故障;
2、油罐内油位过低;
3、过滤网被堵死;
4、阀门控制选择出错;
通知电工处理;
加油;
清洗;
调整;
喷头不出油
1、喷头堵塞;
2、阀门控制选择出错;
3、压力不足;
清洗;
调整;
调整;
喷头雾化不良
1、喷油嘴调整不佳;
2、压力不足;
3、过滤网有杂物;
4、喷头处有杂物;
重调;
调整;
清洗;
清洗;
喷油火焰过粗过细、冲刷窑皮
1、油压、油量波动不定;
2、喷油装置位置不佳;
调整系统稳定工作;
调整;
1、窑头点火喷油装置
2、窑头喂煤系统
常见故障
可能的原因或现象
主要操作处理
火焰分叉
1、喷煤管头部有杂物;
2、喷煤管口变形;
3、罗茨风机过滤网积灰过多,管道内有杂物造成送煤煤粉空气量不足;
清除;
更换;
清除;
火焰形状不佳
1、径、轴向风比例不佳;
2、一次风过过大或过小;
3、喷煤管出口风速低。
调节喷煤管上相应部件;
适当调节一次风机进口阀开度;减小管道及阀门的压力损失
窑尾温度偏低
1、窑炉用风配合不当;
2、窑尾负压过大;
3、系统排风量不够,窑内燃烧不充分。
4、二次风温偏低;
调总排风量或适当关小三次风阀;
清理系统结皮堵料。
调窑尾主排风机转速或阀门开度;
适当关小冷却风机阀门开度。
一次风机停车
1、风机润滑不良;
2、轴承温度超限;
3、电气故障等;
起动事故风机并打开出口阀,急停窑头喂煤系统。
现场全开喷煤管外流风阀,酌情考虑是否拉出喷煤管。
窑头喂煤系统停车
1、煤粉仓堵塞;
2、煤粉计量秤堵塞;
3、煤粉管道堵塞;
4、罗茨风机故障;
5、备用系统故障或已在运行中;
6、电气故障;
1、、停料、停分解炉喂煤、停篦床,否则会出现生烧料,还会使窑温降低过快,重新起动困难。
调整系统风量信冷却机冷却风量,慢转窑。
2、查明故障,尽快处理。
3、分解炉喂煤系统
常见故障
可能的原因或现象
主要操作处理
分解炉内温度过高
喂煤量过大
适当减小喂煤量
分解炉喂煤系统停车
(故障原因同窑头喂煤系统停车)
1、减窑喂煤量;
2、关闭三次风管热风阀开度;
3、根据煅烧情况,温度变化来控制窑头喂煤量的窑速;
4、调整窑尾主排风机转速、阀门开度及冷却机冷却风量;
5、加强监视窑尾、旋风筒、下料翻板阀的工作情况,定时吹,防止积料。
常见故障
可能的原因或现象
主要操作处理
窑尾主排风机停车
1、风机润滑不良;
2、轴承温度超限;
3、系统漏风造成坡负荷;
4、电气故障等;
停料、停分解炉煤粉,必要时也停窑头喂煤,注意保温操作。
关闭三次风;
窑筒体间隔或连续慢转,酌情拉出喷煤管,防止弯曲