锥体制作工艺.docx
《锥体制作工艺.docx》由会员分享,可在线阅读,更多相关《锥体制作工艺.docx(12页珍藏版)》请在冰豆网上搜索。
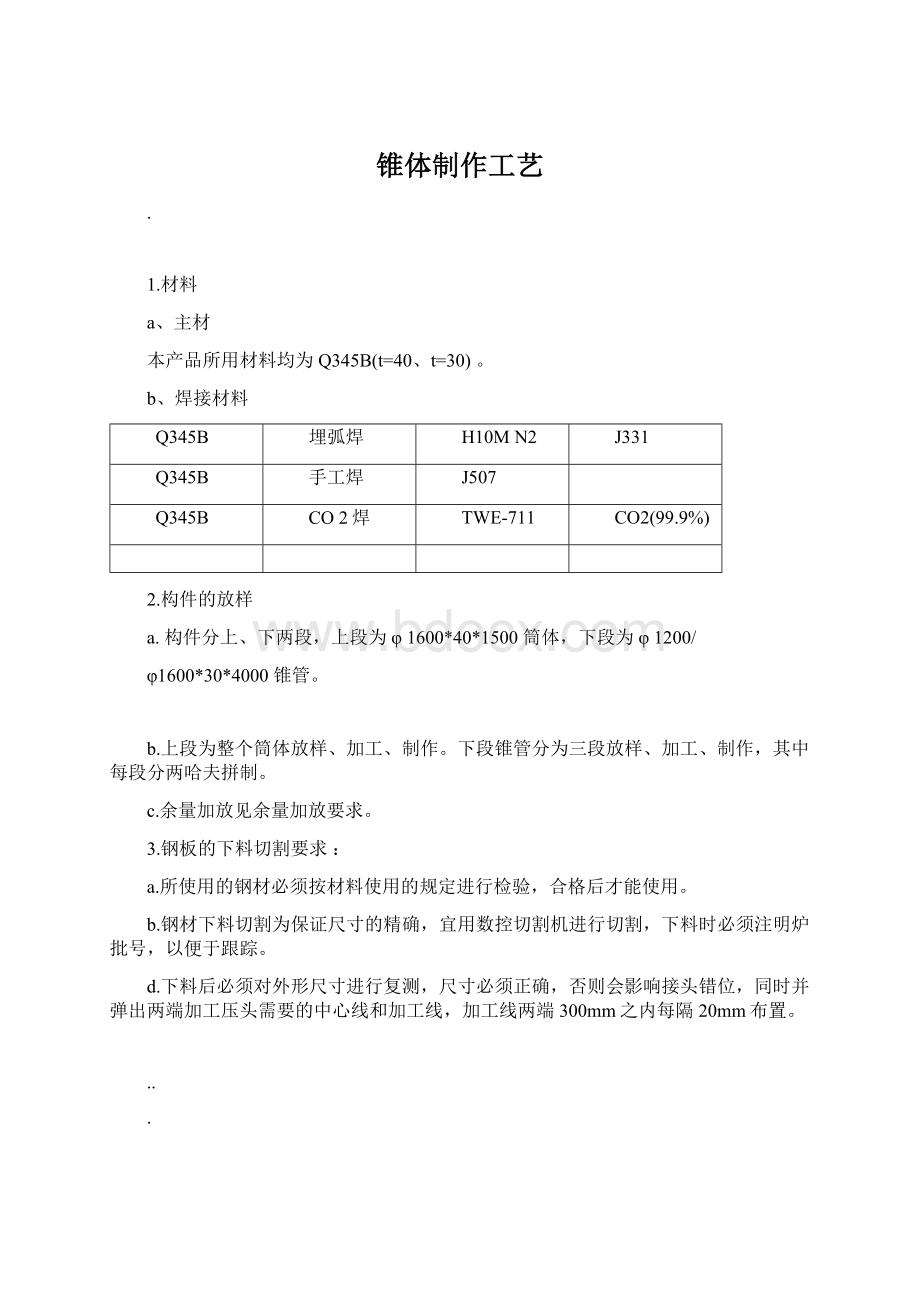
锥体制作工艺
.
1.材料
a、主材
本产品所用材料均为Q345B(t=40、t=30)。
b、焊接材料
Q345B
埋弧焊
H10MN2
J331
Q345B
手工焊
J507
Q345B
CO2焊
TWE-711
CO2(99.9%)
2.构件的放样
a.构件分上、下两段,上段为φ1600*40*1500筒体,下段为φ1200/
φ1600*30*4000锥管。
b.上段为整个筒体放样、加工、制作。
下段锥管分为三段放样、加工、制作,其中每段分两哈夫拼制。
c.余量加放见余量加放要求。
3.钢板的下料切割要求:
a.所使用的钢材必须按材料使用的规定进行检验,合格后才能使用。
b.钢材下料切割为保证尺寸的精确,宜用数控切割机进行切割,下料时必须注明炉批号,以便于跟踪。
d.下料后必须对外形尺寸进行复测,尺寸必须正确,否则会影响接头错位,同时并弹出两端加工压头需要的中心线和加工线,加工线两端300mm之内每隔20mm布置。
..
.
4.焊接坡口要求:
(t=40、t=30)
a.纵缝埋弧对接坡口b.环缝埋弧对接坡口
c.钢板厚度不一致对接坡口(厚薄处作1:
4过渡)
40
6
°
°
0
0
6
6
30
..
.
5.加工余量加放要求:
a.钢管压制直径精度的控制
在压制过程中钢板的延伸率发生变化,会直接导致加工后筒体的直径偏大,所以加工前必须采取措施进行预防,根据本公司以前曾加
工过的类似工程的实际经验,φ1200/φ1600×30/40mm钢管压制后,其圆周长将会增加约5-8mm,所以加工前应将钢管直径缩小
1.5-2.5mm展开进行下料。
b.余量及焊接收缩余量的加放要求
每条对接焊缝处需加放2mm焊接收缩余量。
钢板两端压头处各加放150mm压头余量。
6.筒体的卷制加工工艺
a.用于本工程的厚板筒体轧车选择本公司定制的数控水平下调式三棍卷板机
b.筒体的加工流程如下图示:
..
.
c.根据筒体、锥体直径制作压模并安装,采用800吨油压机进行钢板两端部压头,钢板端部的压制次数至少压三次,先在钢板端部150mm范围内压一次,然后在300mm范围内重压二次,以减小钢板的弹性,防止头部失圆,压制后用样板检验,切割两端余量后并开坡口。
d.必须注意压头质量,压头质量的好坏直接关系到筒体的轧制质量,所以为保证加工质量,尤其是椭圆度要求,压头检验用样板必须使用专用样板,样板要求用2~3mm薄钢板制作,且圆弧处必须上铣床加工,从而保证加工质量。
e.将压好头的钢板吊入三辊轧车后,必须用靠模式拉线进行调整,以保证钢板端部与轧辊成一直线,防止卷管后产生错边,然后按要求徐徐轧制,直至卷制结束,轧圆允许偏差如下:
..
.
纵缝对口错边允许偏差
≤1.5mm
管端椭圆度允许偏差
≤2mm
管端的平整度允许偏差
≤2mm
f.把卷好的筒体吊入拼装胎架上进行纵缝的拼接,拼接时应注意板边错边量和焊缝间隙,另外定位焊时不得用短弧焊进行定位,定位前
用火焰预热到120~150℃,定位焊长度不小于60mm,间距300mm左右,定位焊条用φ3.2,焊缝高度不大于8mm,且不得小于4mm。
拼接后检查管口椭圆度、错边等,合格后提交检查员验收,并作好焊
前记录。
7.多节筒体对接接长
a.焊好后单节筒体进行对接组成一个完整的构件。
b.筒体接长胎架如下图所示:
..
.
c.接管前每节小段节必须进行校正,特别是椭圆度必须校正好。
d.相邻管节拼装组装时,纵缝应相互错开120°,并必须保证两端口的椭圆度、垂直度以及直线度要求,符合要求后定位焊,定位焊要求同前。
e.拼接后在所有筒体上弹出0°、90°、180°、270°母线,并用洋冲标记,
..
.
以便检查四根中心线的直线度、水平度。
f.同样,将拼接好的筒体吊入滚轮焊接胎架上用埋弧焊进行环缝的焊接,焊接要求同纵缝要求。
g.焊后校正,冷却后探伤。
8.筒体分段测量要求
a.检查两端口的椭圆度,用钢尺在直径方向测量不少于6点。
b.检查两端的垂直度,可在两端用线锤测量。
c.检查两端口的平面度,可用粉线交叉测量,交叉处间隙不大于1mm。
d.检查整体直线度,用拉线法测量。
e.检查整体挠度,用水平仪测量。
9钢管装焊公差要求:
内
容
允许偏差(mm)
直径偏差
±1.5
钢管长度
±3
管口圆度
1.5
管面对管轴的垂直度
2
弯曲矢高
2
对口错边
1.5
10.筒体纵缝焊接
a.筒体焊接在专用筒体焊接中心滚轮胎架上进行,筒体内外侧均采用埋弧焊进行焊接。
b.焊接顺序:
先焊内侧,后焊外侧面。
内侧焊满2/3坡口深度后进行
..
.
外侧碳弧气刨清根,并焊满外侧坡口,再焊满内侧大坡口,使焊缝
成型。
c.焊前装好引熄弧板,并调整焊机机头,准备焊接。
d.焊前预热:
40mm钢板焊接前必须对焊缝两侧100mm范围内进行预热,预热采用电加热板进行预热,预热温度100~150℃,加热时需随时用测温仪和温控仪测量控制加热温度,不得太高。
e.按焊接工艺评定的参数调整焊接工艺参数,先进行内侧面的焊接,焊后用碳弧气刨进行反面清根,清除焊道内的杂物并打磨光洁,如
此时温度不够,应进行继续加热,然后再进行焊接,焊后进行校正,待48小时后完全冷却后进行焊缝无损检测。
11.焊接质量保证措施
a.材料的烘焙和储存
焊接材料在使用前应按材料说明规定的温度和时间要求进行烘焙和储存;如材料说明要求不详,则按下表要求执行:
焊条或焊剂
名称
焊条:
J507
焊剂:
HJ330
b.焊接工艺参数
焊条药皮或焊剂
使用前
使用前
类型
烘焙条件
存放条件
低氢型
330-370℃;1小时
100-150℃
熔炼型
300-350℃;2小时
100-150℃
d
工厂制作焊接参数
焊条(焊丝)焊接条件
焊接方法焊材牌号焊接位置
直径(mm)焊接电流A()焊接电压V()焊接速度cm/min()
手工焊J507平焊和Φ3.290-13022-248-12
..
.
条电弧
横焊
Φ4.0
140-180
23-25
10-18
焊
Φ5.0
180-230
24-26
12-20
Φ3.2
80-120
22-26
5-8
立焊
Φ4.0
120-150
24-26
6-10
2
平焊和
260-320
28-34
35-45
CO气体
Φ1.2
保护焊
TWE-711
横焊
570-66030-35
35-50
埋弧自H10Mn2
单层单道焊多层
平焊Φ4.8
550-660
35-50
30-35
动焊
HJ330平焊角焊单道焊角焊缝
550-660
30-35
35-50
c.预热和层间温度
焊前,母材的最小预热温度和层间温度应按下表要求执行:
母材牌号
母材厚度
20>60mm
t≤20mm
Q345B不要求
≥10℃
≥100℃
≥150℃
⑴接头的预热温度应不小于上表规定的温度,层间温度不得大于
230℃。
⑵接头预热温度的选择以较厚板为基准,应注意保证厚板侧的预热温
度,严格控制薄板侧的层间温度。
⑶预热时,焊接部位的表面用电加热均匀加热,加热区域为被焊接头
..
.
中较厚板的两倍板厚范围,但不得小于100mm区域。
加热时应尽可
能在施焊部位的背面。
⑷预热和层间温度的测量应采用测温表或测温笔进行测量。
测量时应
距焊缝两侧各75mm。
d.定位焊
⑴定位焊焊缝所采用的焊接材料及焊接工艺要求应与正式焊缝的要
求相同。
⑵定位焊焊缝的焊接应避免在焊缝的起始、结束和拐角处施焊,弧坑应填满,严禁在焊接区以外的母材上引弧和熄弧。
(3)定位焊的焊脚尺寸不应大于焊缝设计尺寸的2/3,且不大于8mm,但不应小于4mm。
对于厚板的定位焊在定位前必须用火焰进行预热,且定位焊预热温度一般要比正式施焊时高20度左右,以防止产生定位焊缝裂纹。
(4)定位焊焊缝有裂纹、气孔、夹渣等缺陷时,必须清除后重新焊接,如最后进行埋弧焊时,弧坑、气孔可不必清除。
(5)定位焊时一般采用Φ3.2mm的焊条进行,同时应采用较大的电流,以保证定位焊缝有一定的熔深。
e.引弧和熄弧板
重要的对接接头和T接头的两端应装焊引弧板和熄弧板,其材料及
接头原则上应与母材相同,其尺寸为:
手工焊、半自动—50×30×
tmm;自动焊—100×50×tmm;焊后用气割割除,磨平割口。
f.变形的控制
..
.
⑴下料、装配时,根据制造工艺要求,予留焊接收缩余量,予置焊接
反变形。
⑵装配前,矫正每一构件的变形,保证装配符合装配公差表的要求;
⑶使用必要的装配和焊接胎架、工装夹具、工艺隔板及撑杆。
⑷在同一构件上焊接时,应尽可能采用热量分散,对称分布的方式施
焊。
g.焊后处理
⑴焊缝焊接完成后,清理焊缝表面的熔碴和金属飞溅物,焊工自行检查焊缝的外观质量;如不符合要求,应焊补或打磨,修补后的焊缝
应光滑圆顺,不影响原焊缝的外观质量要求。
⑵对于重要构件或重要节点焊缝,焊工自行检查焊缝外观合格后,在
焊缝附近打上焊工的钢印。
⑶外露钢构件对接接头,根据图纸要求应磨平。
对不足360°饱满的栓钉应从不饱满的一侧进行。
(4).其他
熔焊栓钉的施工需经过专业培训的人员进行操作。
12.焊缝质量要求
a.焊缝外观质量
根据图纸要求外露部分焊缝应焊后磨平。
b.焊缝无损检测要求
⑴焊缝质量等级分类
构件纵、横向对接焊缝为一级焊缝.
..
.
⑵超声波探伤范围比例(UT)
I级焊缝100%UT检查。
c.探伤标准
⑴超声波探伤按GB11345-89要求检验,焊缝评定等级为BII级。
低合金钢的无损探伤应在焊接完成24小时后进行;对于板厚超过
40mm时,无损探伤应在焊接完成48小时后进行。
⑵局部探伤的焊缝,如发现有存在不允许的缺陷时,应在缺陷的两
端延伸探伤长度,增加的长度为该焊缝长度的10%,且不小于200mm
如仍发现有不允许的缺陷时,则应对该焊缝进行100%的探伤。
..