09835112汤志然圆槽零件加工工艺设计毕业设计.docx
《09835112汤志然圆槽零件加工工艺设计毕业设计.docx》由会员分享,可在线阅读,更多相关《09835112汤志然圆槽零件加工工艺设计毕业设计.docx(14页珍藏版)》请在冰豆网上搜索。
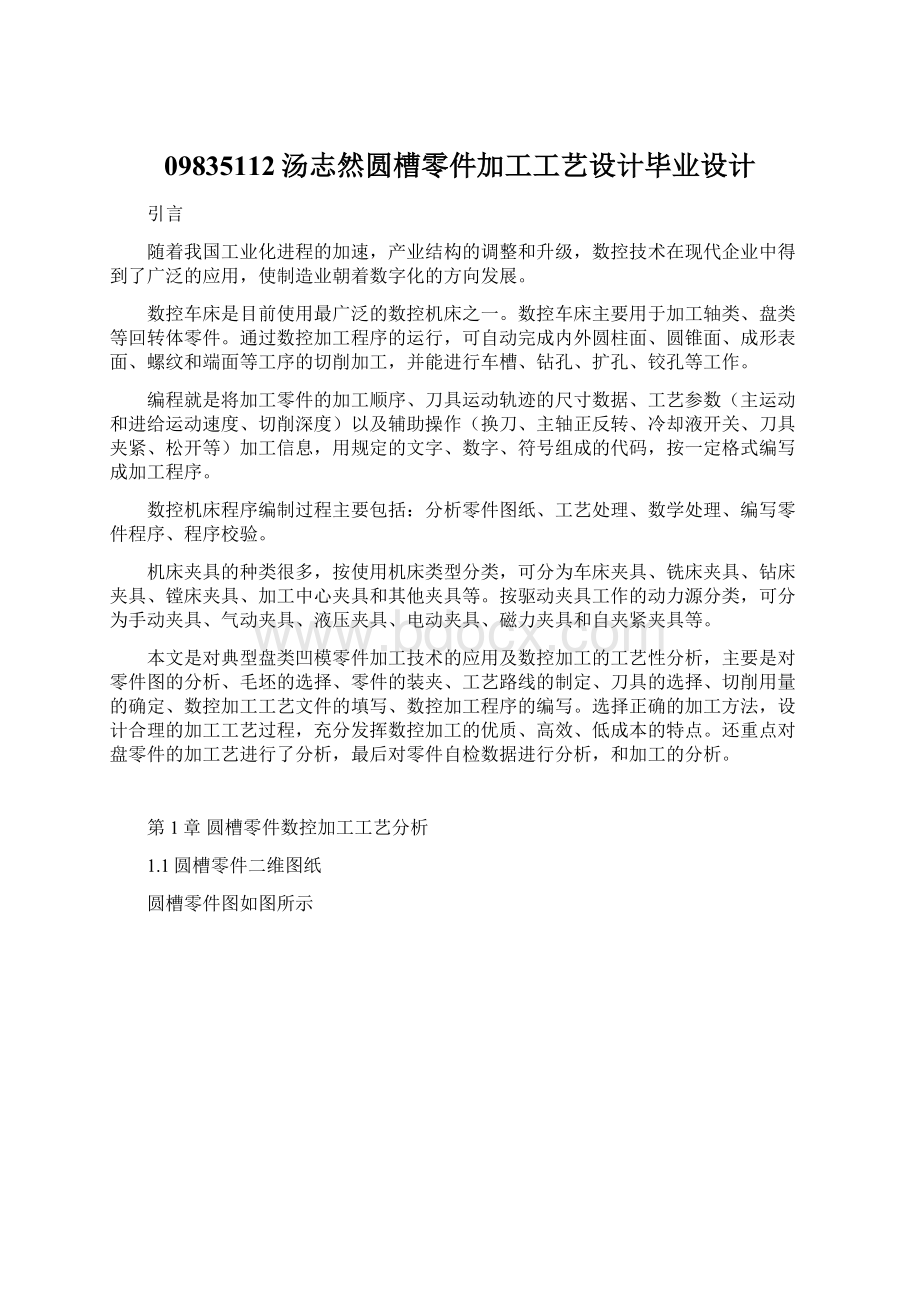
09835112汤志然圆槽零件加工工艺设计毕业设计
引言
随着我国工业化进程的加速,产业结构的调整和升级,数控技术在现代企业中得到了广泛的应用,使制造业朝着数字化的方向发展。
数控车床是目前使用最广泛的数控机床之一。
数控车床主要用于加工轴类、盘类等回转体零件。
通过数控加工程序的运行,可自动完成内外圆柱面、圆锥面、成形表面、螺纹和端面等工序的切削加工,并能进行车槽、钻孔、扩孔、铰孔等工作。
编程就是将加工零件的加工顺序、刀具运动轨迹的尺寸数据、工艺参数(主运动和进给运动速度、切削深度)以及辅助操作(换刀、主轴正反转、冷却液开关、刀具夹紧、松开等)加工信息,用规定的文字、数字、符号组成的代码,按一定格式编写成加工程序。
数控机床程序编制过程主要包括:
分析零件图纸、工艺处理、数学处理、编写零件程序、程序校验。
机床夹具的种类很多,按使用机床类型分类,可分为车床夹具、铣床夹具、钻床夹具、镗床夹具、加工中心夹具和其他夹具等。
按驱动夹具工作的动力源分类,可分为手动夹具、气动夹具、液压夹具、电动夹具、磁力夹具和自夹紧夹具等。
本文是对典型盘类凹模零件加工技术的应用及数控加工的工艺性分析,主要是对零件图的分析、毛坯的选择、零件的装夹、工艺路线的制定、刀具的选择、切削用量的确定、数控加工工艺文件的填写、数控加工程序的编写。
选择正确的加工方法,设计合理的加工工艺过程,充分发挥数控加工的优质、高效、低成本的特点。
还重点对盘零件的加工艺进行了分析,最后对零件自检数据进行分析,和加工的分析。
第1章圆槽零件数控加工工艺分析
1.1圆槽零件二维图纸
圆槽零件图如图所示
图1-1圆槽零件1图
图1-2圆槽零件2图
1.2零件图的工艺分析
工艺分析:
根据图样分析所选机床能够满足精度要求,分粗精两次加工,以保证其表面粗糙度的要求,外轮廓加工时,没有刀具直径的限制,为了提高切削效率采用较大直径铣刀加工。
48*48的槽圆角半径为R12,精加工道具的最大直径不能大于Ø24,考虑到Ø10铣刀具较常用,所以选用Ø10铣刀作为精加工刀具,槽深尺寸为自由公差,可以考虑在粗加工时直接达到尺寸要求。
具体工艺见表4.6和表4.7。
1.3分析零件图纸中的尺寸标注
图样分析:
根据图样尺寸100×100mm,外形公差为±0.03,Ø8孔深度为10±0.03mm,槽形状直径尺寸为Ø48mm,深度3.5±0.03mm,Ø32mm槽深度5±0.03mm。
表面粗糙度均为Ra3.2。
1.4零件毛坯的选择
该产品为一般性零件,对材料没太大要求,该圆槽加工案例零件为半成品,小批量生产。
该零件上下平面及四周均已按图纸技术要求加工好,要求铣削圆槽到规定尺寸,保证圆槽底平面与圆槽侧壁垂直度为0.02mm,圆槽直径分别为Ø48mm、Ø32mm。
第2章数控加工工艺方案的制定
2.1工序与工步的划分
确定加工方案
经过分析零件的尺寸精度、几何形状精度、位置精度和表面粗糙度要求,作出以下加工方案。
1.先粗铣外形,然后精铣外形。
2.先粗铣内槽,再精铣内槽。
2.2加工机床的选择
加工中心(MachiningCenter,MC)是目前世界上产量最高应用最广泛的数控机床之一。
它主要用于箱体类零件和复杂曲面零件以及体积较大零件的加工,能把铣削、镗削、钻削、攻螺纹和车螺纹等功能集中在一台设备上。
因为它具有多种换刀或选刀功能及自动工作台交换装置(APC),顾工件经一次装夹后,可自动完成或接近完成工件各面的所有加工工序,从而使生产效率和自动化程度大大提高。
1.要保证加工零件的技术要求,能加工出合格的产品。
2.有利于提高生产率。
3.尽可能降低生产成本(即生产费用)。
根据毛坯的材料和类型、零件轮廓形状复杂程度、尺寸大小、加工精度、工件数量、现有的生产条件要求。
选用日发RFMV60加工中心。
2.3刀具的选择
数控加工中的刀具选择和切削用量确定是在人机交互状态下完成的,对于铣削加工,编程人员除了考虑工件坐标系远点的位置外,还应考虑起刀点和退刀点的位置。
起刀点和退刀点必须距离加工零件上表面一定的距离的安全高度,保证在停止状态时,刀具不与加工零件和夹具发生碰撞。
下刀运动过程最好不用G00快速快速运动,而要用(G01直线插补)。
要求编程人员必须掌握刀具选择和切削用量确定的基本原则在编程时充分考虑数控加工的特点,能够正确选择刀具及切削用量。
对于铣削加工,编程人员还应充分考虑刀具的切入和切出方式。
刀具切入的方式,不仅影响加工质量,同时直接关系到加工安全。
对于二维轮廓加工,一般要求从侧向进刀或沿切线方向进刀尽量避免垂直进刀;切出方式也应从侧向或切向退刀。
刀具从安全高度下降到切削高度时,应离开工件毛坯边缘5~10mm,以免撞刀,发生危险。
对于型腔的粗铣加工,一般应用键槽洗刀先钻一个工艺孔至型腔底面(留有一定的精加工余量),然后进行扩孔,以便所使用的立铣刀能从工艺孔进刀进行型腔粗加工,型腔粗加工一般采用从中心向四周扩展的方式。
粗铣外形用Φ80mm的高速钢键槽铣刀
精铣外形用Φ16mm的高速钢键槽铣刀
粗铣Φ48槽用Φ10mm的高速钢键槽铣刀
精铣Φ32槽用Φ8mm的高速钢键槽铣刀
数控刀具有以下特点:
①刚性好(尤其是粗加工刀具)、精度高、抗振及热变形小;②互换性好,便于快速换刀;③寿命高,切削性能稳定、可靠;④刀具的尺寸便于调整,以减少换刀调整时间;⑤刀具应能可靠地断屑或卷屑,以利于切屑的排除;⑥系列化、标准化,以利于编程和刀具管理。
数控机床上用的刀具应满足安装调整方便、刚性好、精度高、耐用度好等要求。
2.4夹具的选择
装夹定位:
根据生产批量要求及零件的设计基准情况,采用平口钳装夹工件,工件上表面的中心点作为工件坐标系原点。
用寻边器找正其中心点,以工件上表面进行对刀。
2.5确定加工路线
在数控加工中,刀具刀位点相对于工件的运动轨迹和方向称为加工路线。
即刀具从对刀点开始运动起,直至结束,加工程序所经过的路径,包括切削加工的路径及刀具引入、返回等非切削空行程。
加工路线的确定原则主要有以下几点:
1.应能保证零件的加工精度和表面粗糙度的要求,且效率高。
2.应尽量缩短加工路线,既可以减少程序段,又可以减少刀具空程移动时间。
3.应使数值计算简单,以减少编程工作量。
此外,确定加工路线时,还要考虑工件的加工余量和机床、刀具的刚度等情况,确定是一次走刀,还是多次走刀完成加工。
要确定加工路线,首先要确定起始切削的加工方法。
常用方法有:
预钻削起始孔法、插铣法、坡走铣法、螺旋插补法。
本案例零件的加工采用预钻削起始孔法。
预钻削起始孔法就是在实体材料上先钻出比铣刀直径大的起始孔,铣刀先沿着起始孔下刀后,再按行切法、环切法或环切法侧向铣出内圆槽(型腔)的方法。
加工顺序安排:
基面先行原则,先粗后精原则,先主后次原则,先面后孔原则
2.6量具及辅助用具的选择
外轮廓和圆槽直径用0~200mm电子游标卡尺进行测量,自动读出数据、端面的圆跳动用百分表测量,其中圆弧用R规测量。
游标卡尺:
测量范围:
0-200mm:
分度值:
0.02mm
第3章冷却液的选择
金属切削过程中,合理选择切削液,可改善工件与刀具之间的摩擦状况,降低切削力和切削温度,减小刀具磨损和工件的热变形,从而可以提高刀具的耐用度、加工效率和加工质量。
切削液的选择应考虑下列几点因素:
1.润滑具有良好润滑能力的切屑液可减少刀具与工件或切屑间的直接接触,减轻摩擦和粘结,因此,可减少刀具磨损,延长使用寿命,提高工件表面质量。
2.冷却具有良好冷却作用的切屑液能从切削区域带走大量切削热,使切削温度降低,保护工件。
3.清洗具有良好清洗能力的切屑液可以冲走切削区域与机床上的细碎切屑和脱落的磨粒,防止划伤已加工表面和导轨。
4.防锈切削液中加入防锈剂,如亚硝酸钠、磷酸三钠和石油磺酸钡等,可在金属表面形成一层保护膜,起防锈作用。
常用切削液的种类如表2-1所示
表2-1常用冷却液
冷却液名称
主要成份
主要作用
水溶液
水,防锈剂
冷却
乳化液
水、乳化油、乳化剂
冷却、润滑、清洗
切削油
矿物油、动植物油、复合油
润滑
在加工此矩形盘类零件时根据该工件材料、刀具材料、加工方法、加工要求及冷却液的作用和价格来考虑,加工时选择乳化液比较合理。
冷却液作用:
冷却、润滑、清洗而且还有一定的防锈作用。
第4章切削用量的选择
4.1切削用量的选择原则
数控编程时,编程人员必须确定每道工序的切削用量,包括主轴转速、背吃刀量、进给速度等,并以数控系统规定的格式输入到程序中。
切削用量对于不同的加工方法,需选用不同的切削用量。
合理的选择切削用量,对零件的表面质量、精度、加工效率影响很大。
这在实际中也很难把握,要有丰富的实践经验才能够确定合适的切削用量。
在数控编程时只能凭借编程者的经验和刀具的切削用量推荐值初步确定,而最终的切削用量将根据零件数控程序的调试结果和实际加工情况来确定。
切削用量的选择原则是:
粗加工时以提高生产率为主,同时兼顾经济性和加工成本的考虑;半精加工和精加工时,应同时兼顾切削效率和加工成本的前提下,保证零件的加工质量。
值得注重的是,切削用量(主轴转速、切削深度及进给量)是一个有机的整体,只有三者相互适应,达到最合理的匹配值,才能获得最佳的切削用量。
确定切削用量时应根据加工性质、加工要求,工件材料及刀具的尺寸和材料性能等方面的具体要求,通过查阅切削手册并结合经验加以确定,确定切削用量时除了遵循一般的原则和方法外,还应考虑以下因素的影响:
1刀具差异的影响——不同的刀具厂家生产的刀具质量差异很大,所以切削用量需根据实际用刀具和现场经验加以修正。
2机床特性的影响——切削性能受数控机床的功率和机床的刚性限制,必须在机床说明书规定的范围内选择。
避免因机床功率不够发生闷车现象,或刚性不足产生大的机床振动现象,影响零件的加工质量、精度和表面粗糙度。
3数控机床生产率的影响——数控机床的工时费用较高,相对而言,刀具的损耗成本所占的比重较低,应尽量采用高的切削用量,通过适当降低刀具寿命来提高数控机床的生产率。
4.2背吃刀量的选择
确定背吃刀量ap(mm)
背吃刀量的大小主要依据机床、夹具、刀具和工件组成的工艺系统的刚度来决定,在系统刚度答应的情况下,为保证以最少的进给次数去除毛坯的加工余量,根据被加工零件的余量确定分层切削深度,选择较大的背吃刀量,以提高生产效率。
在数控加工中,为保证零件必要的加工精度和表面粗糙度,一般留少量的余量(0.2~0.5mm),在最后的精加工中沿轮廓走一刀。
粗加工时,除了留有必要的半精加工和精加工余量外,在工艺系统刚性答应的条件下,应以最少的次数完成粗加工。
留给精加工的余量应大于零件的变形量和确保零件表面完整性。
综合考虑得到:
粗加工时选取2.0mm的背吃刀量。
精加工余量取0.1~0.2mm
4.3确定主轴转速
主轴转速应根据允许的切削速度V和工件(或刀具)直径来选择。
外圆车削及其计算公式为:
n=1000v/πD式(4.1)
式中
v----切削速度,单位为m/min,由刀具的耐用度决定;
n----主轴转速,单位为r/min;
D----工件直径或刀具直径,单位为mm。
4.4进给速度的选择
进给速度F是切削时单位时间内零件与铣刀沿进给方向的相对位移量,单位为mm/r或mm/min。
进给量或进给速度在数控机床上使用进给功能字母F表示的,F是数控机床切削用量中的一个重要参数,主要依据零件的加工精度和表面粗糙度要求,以及所使用的刀具和工件材料来确定。
确定进给速度的原则是:
1当工件的质量要求能得到保证时,为提高生产效率,可选择较高的进给速度。
一般在100~200mm/min范围内选取。
2在切断、加工深孔或用高速钢刀具加工时,宜选择较低的进给速度,一般在20~50mm/min范围内选取。
3当加工精度、表面粗糙度要求较高时,进给速度应选小一些,一般在20~50mm/min范围内选取。
4当刀具空行程,特别是远距离“回零”时,可以设定该机床数控系统设定的最高进给速度。
所以,此处我们应当根据经验和粗精加工而定,粗加工选取F1.0左右。
精加工时选取较少的加工余量F0.2~F0.3。
第5章数控加工工艺过程卡片
5.1圆槽加工案例数控加工工序卡
圆槽数控加工工序卡如表4-1所示
表4-1圆槽加工案例数控加工工艺卡
工步号
加工
内容
刀
具
号
刀具
名称
刀具
规格
(mm)
补
偿
号
补偿
值(mm)
主轴
转速
(r/min)
进给
速度
(mm/min)
切削
深度
(mm)
加工
余量
(mm)
1
粗铣平面
T01
高速钢立铣刀
Φ80
D1
15
800
300
9.8
9.8
D2
10.2
2
精铣外形
T02
高速钢立铣刀
Φ16
D3
10
1000
300
0.2
0.2
3
粗铣
Φ48槽
T03
高速钢立铣刀
Φ10
D2
10.2
1000
300
4.8
19.8
4
粗铣4×Φ8孔
T04
高速刀
Φ8
D3
10
1200
300
0.2
0.2
编制
汤志然
审核
李景魁
批准
2012/3/28
共1页
第1页
5.2圆槽加工案例数控加工刀具卡
圆槽数控加工刀具卡如表4-2所示
表4-2圆槽加工案例数控加工刀具卡
序号
刀具号
刀具
加工表面
备注
规格名称
数量
刀长
1
T01
Φ80高速钢立铣刀
1
实测
铣平面
2
T02
Ø16圆柱立铣刀
1
实测
外形轮廓
3
T03
Ø10键槽铣刀
1
实测
圆槽型腔
4
T04
Ø8麻花钻头
1
实测
钻4ר8孔
编制
汤志然
审核
李景魁
2012/3/28
第6章数控加工程序
O0001
主程序名
N10G54S600M03T01
设定工件坐标系主轴正转600r/min
N20G00X-100.0Y-15.0Z10.0
快速点定位
Z0.2
进刀
N30G01X100.0F120
直线插补粗铣平面
N40G00Y60.0
快速移动点定位
N50G01X-100.0F120
直线插补粗铣平面
N60G00Z5
抬刀
X-100.0Y-15.0
快速移动点定位
Z0
N70S800M03
精铣主轴正转转速为800r/min
N80G01X100.0F80
直线插补精铣平面
N90G00Y60.0
快速移动点定位
N100G01X-100.0F80
直线插补精铣平面
N110G00Z100.0
快速移动抬刀
X0Y0
返回工件X、Y原点
N120M05
主轴停止
N130M30
程序结束
O0002
程序名(Ø16圆柱立铣刀轮廓)
N10G55G40S1000M03T01
设定工件坐标系主轴正转1000r/min
N20G00X-41.0Y-85.0Z20.0
快速移动点定位
Z-3.3
快速下降至Z-3.5mm
N30G01G41D03Y-60.0F160
建立刀具半径左补偿进行粗铣D03=24
Y21.0
直线插补切削
N40G03X-21.0Y41.0R20.0
逆时针圆弧插补顺铣圆弧R20
N50G01X21.0
直线插补切削
N60G03X41.0Y21.0R20.0
逆时针圆弧插补顺铣圆弧R20
N70G01Y-21.0
直线插补切削
N80G03X21.0Y-41.0R20.0
逆时针圆弧插补顺铣圆弧R20
N90G01X-21.0
直线插补切削
N100G03X-41.0Y-21.0R20.0
逆时针圆弧插补顺铣圆弧R20
N110G00Z20.0
快速抬刀
N120G00G40X-41.0Y-85.0
取消半径补偿
N130G01G41D02Y-60.0F200
建立刀具半径左补偿进行粗铣D02=8.2
Y21.0
N140G03X-21.0Y41.0R20.0
逆时针圆弧插补顺铣圆弧R20
N150G01X21.0
N160G03X41.0Y21.0R20.0
逆时针圆弧插补顺铣圆弧R20
N170G01Y-21.0
N180G03X21.0Y-41.0R20.0
N190G01X-21.0
N200G03X-41.0Y-21.0R20.0
N210G00Z20.0
N220G00G40X-41.0Y-85.0
Z-3.5
N230S1200M03
N240G01G41D03Y-60.0F120
Y21.0
N250G03X21.0Y41.0R20.0
N260G01X21.0
N270G03X41.0Y21.0R20.0
N280G01Y-21.0
N290G03X21.0Y-21.0R20.0
N300G01X-21.0
N310G03X-41.0Y-21.0R20.0
N320G00Z20.0
N330G00G40X-41.0Y-85.0
N340G01G41D01Y-60.0F120
建立半径左补偿D01=8
Y21.0
N350G03X-21.0Y41.0R20.0
N360G01X21.0
N370G03X41.0Y21.0R20.0
N380G01Y-21.0
N390G03X21.0Y-21.0R20.0
N400G01X-21.0
Y-60.0
N410G03X-41.0Y-21.0R20.0
N420G01X60.0
N430G00Z10.0
N440G00G40X-100.0Y-85.0
N450G28X-100.0Y-85.0Z20.0
自动返回机床原点
N460M05
N470M30
O0003
程序名(Ø10键槽铣刀铣内圆弧槽)
N10G56G40S1000M03T02
N20G00X0Y0Z10.0
N30G01Z-4.8F100
X9.0F160
N40G03I-9.0J0
N50G01X10.8
N60G03I-10.8J0
N70G01Z-3.3
X18.8
N80G03I-18.0J0
N90S1200M03
N100G01X0Y0
Z-5.0
X9.0
N120G03I-9.0J0
N130G01X11.0
N140G03I-11.0J0
N150G01X0Y0
Z-3.5
X19.0
N160G03I-19.0J0
N170G01X0Y0
N180G00Z10.0
N190G28X0Y0Z20.0
N200M05
N210M30
O0004
主程序名(Ø8麻花钻头钻4ר8孔)
N10G57G15M03S1200T04
N20G00X0Y0Z20.0
N30G16
N40G99G73X57.97Y45.0Z-15.8R3.0Q3.0F120
Y135.0
Y-135.0
G98Y45.0
N50G15G80
N60G00G0Y0Z100.0
N70M05
N80M30
程序结束,返回程序开头
结束语
首先,我学会了对相关文献资料的检索,一切科学成果的获得都是建立在前人研究的基础之上的。
因此,对于相关文献资料的检索显得尤为重要。
在现代社会中,随着计算机的普及以及网络技术的发展,对于文献资料的检索已经从图书馆的纸质资料转移到网络平台下的电子文档。
其次,对于各种工具软件的熟练使用也是做好毕业设计所必不可少的。
在这次设计中,我主要使用了AUTOCAD绘图软件、仿真软件Word和Excel编辑软件。
在这过程中我对这三个软件熟练程度又进一步加深,为以后的工作和学习打下良好的基础。
最后,最重要的是,我对自己所学的专业又有了新的认识,数控在世界的各个行业中,尤其是制造业中发挥重要的作用,那些高精密、复杂的零部件基本都是由数控来完成的,数控的发展水平也可以进一步体现国家的经济实力和工业水平。
总之,这次毕业设计不是见简简单单的完成一个课题,而是使我初步的掌握了科学研究的步骤与方法,巩固了我的专业知识,锻炼了我分析解决问题的能力,为今后的工作打下了坚实的基础。
短暂的三年大学生活很快就要结束了,我曾多么憧憬美好的学生时代,如今当自己临近毕业时,我又留恋已经流逝的三年学生生涯。
本文是在老师们的悉心指导和亲切关怀下,并且在经过不断的学习和修改完成的。
老师严谨的学风,渊博的学识,谦逊的为人,丰富的实践经验,高瞻远瞩、敏锐的科学眼光,将是我永远学习的楷模;老师的谆谆教诲,将使我终生受益。
在此,谨致以衷心的感谢和崇高的敬意。
在三年的学习、生活中,机电系的全体老师给予了诸多的指导和帮助,是你们的热心肠让我顺利的踏入工作岗位,在此唯有感谢,尽管这两个字微不足道但确实是学生的心意。
机电系的各位老师给了我很大帮助和启示,使我学到更多的知识,从而顺利的完成毕业论文。
在此一并表示衷心的感谢。
祝愿他们身体健康,工作顺利,事业上取得更大成功。
参考文献
[1]何平.数控加工中心操作与编程实训教程第二版.国防工业出版社,2010年
[2]邹新宇.数控编程[M].清华大学出版社,2006年
[3]余英良.数控加工编程及操作[M].北京:
高等教育出版社,2004年第一版
[4]黄卫.数控技术与数控编程[M].北京:
机械工业出版社,2004年
[5]眭润舟.数控编程与加工技术[M].北京:
机械工业出版社,2006年第一版
[6]华茂发.数控机床加工工艺[M].北京:
机械工业出版社,2000年
[7]黄康美.数控加工实训教程[M].北京:
电子工业出版社,2004年