实习报告.docx
《实习报告.docx》由会员分享,可在线阅读,更多相关《实习报告.docx(39页珍藏版)》请在冰豆网上搜索。
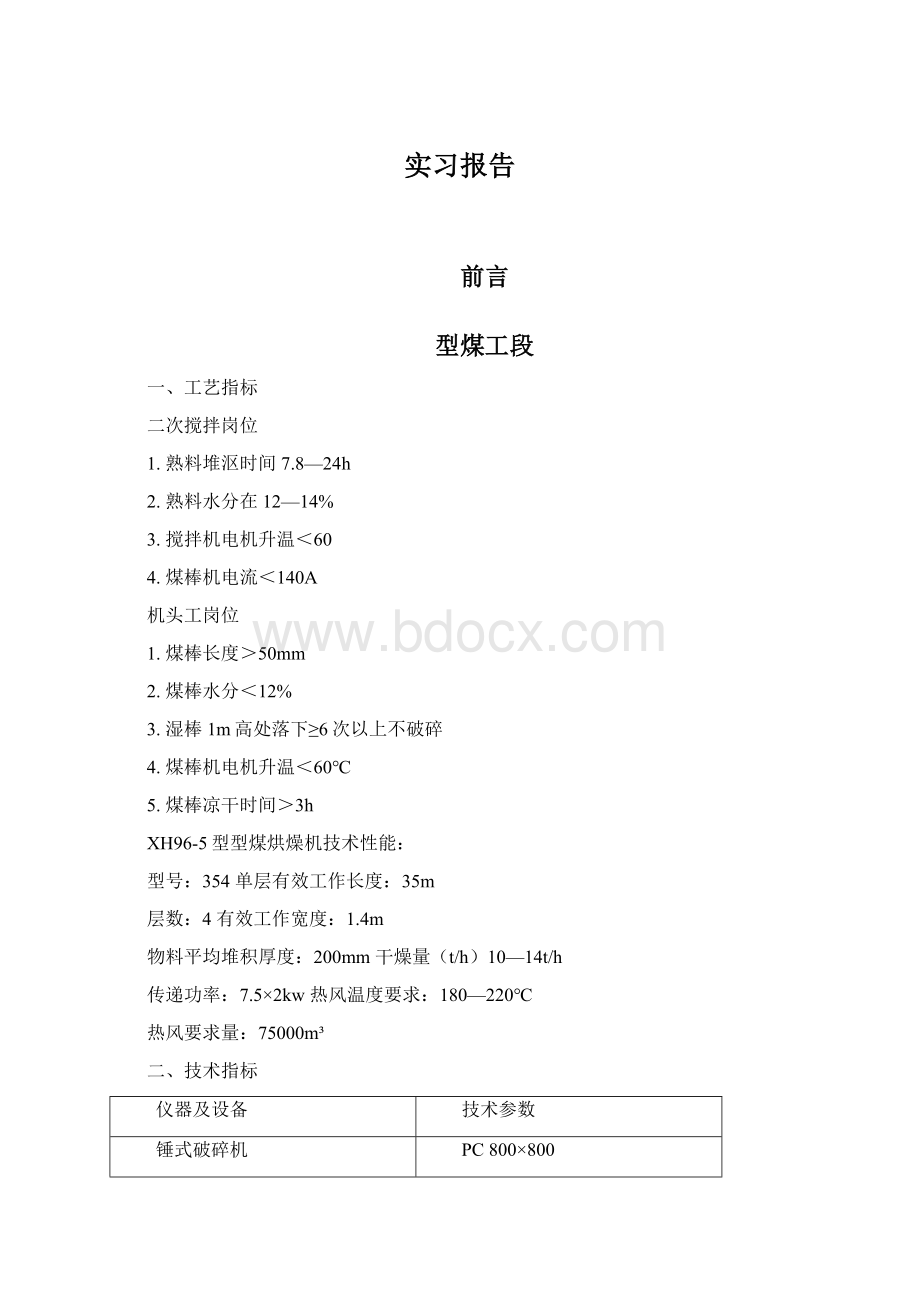
实习报告
前言
型煤工段
一、工艺指标
二次搅拌岗位
1.熟料堆沤时间7.8—24h
2.熟料水分在12—14%
3.搅拌机电机升温<60
4.煤棒机电流<140A
机头工岗位
1.煤棒长度>50mm
2.煤棒水分<12%
3.湿棒1m高处落下≥6次以上不破碎
4.煤棒机电机升温<60℃
5.煤棒凉干时间>3h
XH96-5型型煤烘燥机技术性能:
型号:
354单层有效工作长度:
35m
层数:
4有效工作宽度:
1.4m
物料平均堆积厚度:
200mm干燥量(t/h)10—14t/h
传递功率:
7.5×2kw热风温度要求:
180—220℃
热风要求量:
75000m³
二、技术指标
仪器及设备
技术参数
锤式破碎机
PC800×800
电机功率
75KW
转子直径
800mm
转子速度
1000转/min
最大进料粒度
200mm
转子宽度
800mm
分料粒度
0-10mm
重量
2-6t
抗压式煤棒机
ZMJ25-Ⅲ或ZMJ30
生产能力(t/h)
3-4或5-6
成型规格
Φ18-24或Φ18-30
主机转速(rpm)
177-143或110-135
螺旋计转数(片)
4或3
整机重量(t)
2.8-3或3.2-4
电机
Y250M-455KWY280M-490KW
Y2805-475KW
减速机
ZQ650-12.64-ⅠZZQ850-12.64-ⅠZ
ZQ650-10.35-ⅠZZLY250-12.5-ⅡZ
三角胶带
D2500、4根D2500、5根
滑柴油封
PD100×140×12
油浸石棉盘
YS250-F8
轴承
T624或22324
三、干燥机原理:
皮带传动干燥机内栅栏式叶轮,使煤棒在机内停留足够长时间。
同时,铝炉处牵引道干燥机内,吹热风,是起干燥,在外部有一压力表。
左边负、右边正。
其目的是要是干燥机内一边压力为负,一边为正。
负压力处出煤棒。
因其压力为负,其粉尘会被倒吸入机内,不会飞扬。
干燥机共有九层叶轮,煤棒干燥后,将其装车放置在一起。
因其制出后并未完全干燥,堆放在一起使其冷却、干燥,干燥后送造气处。
制煤的搅拌过程,还处于人工搅拌,可采用自动化,提高效率,减少成本。
熟材料输送过程中,有漏料,需进行回收,仍可用于制煤棒。
煤棒加工后,有碎渣,其碎渣可用于燃料,也可用来造煤棒。
传送带上方前段有磁铁,作用:
吸走矿中带铁质的物质。
锤式破碎机出来后,再用提升机,再进如笼式粉碎机。
出来后到制液罐,制液罐上有控制阀,控制两条传送量,双螺旋搅拌器出口量,粉碎机出口量控制提升机。
制液罐顶端有搅拌机(液罐直径2000mm)入料口加水,加碱以及加含煤,中部有入孔,塔外有温度表,碱助燃,含煤是合剂。
四、工艺方块图
白煤
合煤
碱
水
第一次粉碎
锤式破碎机
第二次粉碎
制液罐
离式粉碎机
煤粉
各个煤仓存放
双螺旋式搅拌机
皮带
烘干机
挤压煤棒机
皮带
熟料湿煤棒
造气工段
晒煤区
沤制
水处理工段
一、岗位任务
采用离子交换的方法,将硬水软化,除盐制得合格的除盐水,供锅炉及全厂各用软水岗位的使用。
二、工艺指标
石灰水中的氢氧根
≦0.2mg/L
石灰水温度
20~30℃
石灰水硬度
5~7mg/L
软水硬度
≦0.04mgn/L
软水氯根
≦20mg/L
软水PH
7~8
软水悬浮物
<5mg/L
盐水浓度
4~6%
盐水浊度
<20ppm
交换器前压力
0.3~0.4mpa
交换器后压力
≦0.25mpa
盐水泵出口压力
≦0.25mpa
供造气软水压力
0.6~0.8mpa
供变换碳化软水压力
≧1.2mpa
软水箱液位
80~90%
交换器出口软水分析
随时测定
软水泵出口软水分析
1次/时
石灰水分析
1次/天
石灰水池液位
70~95%
石灰水过滤器清洗
1次/月
打捞水池漂浮物
1次/班
除氧器液位
40~60%
真空除氧器内水温
55~65℃
真空除氧器内压力
≦-0.08mpa
喷射循环水池液位
80~90%
喷射循环水温
40~55℃
除氧水溶解氧
0.05mg/L
各泵加油溶解氧分析
1次/天
各泵加油
1次/班
各电机温升
<60℃
三、基本原理
由于天然水含有钠离子,镁离子,钙离子,碳酸氢根离子,硫酸根离子,氯离子和少量的氧气,二氧化碳,所以先用石灰水除去硬水中的暂时硬度,再用钠离子交换器除去永久硬度。
钠离子交换法是以离子交换剂中的钠离子交换水中的钙离子,镁离子,硬水通过钠型阳离子交换剂后,水中的钙、镁离子被交换剂中的钠离子交换而被软化,其方程式为:
2NaR+Ca2+(Mg2+)=R2Ca(Mg)+2Na+
交换剂用了一段时间后,会失去活性,干扰再生液再生,其方程式为:
Ca(HCO3)2+2NaR=CaR2+2NaHCO3
Ca(HCO3)2+2HR=CaR2+CO2↑+H2O
Mg(HCO3)2+2NaR=MgR+2NaHCO3
Mg(HCO3)+2HR=MgR2+CO2↑+H2O
CaSO4+2NaR=CaR2+Na2SO4
CaCl2+2HR=CaR2+2HCl
CaCl2+2NaR=CaR2+2NaCl
MgSO4+2HR=MgR2+H2SO4
MgSO4+2NaR=MgR2+Na2SO4
Na2SiO3+2HR=2NaR+H2SiO3
HCl+R’-OH=R’-Cl+H2O
H2CO3+R’-OH=R’-HCO3+H2O
H2SiO3+R’-OH=R’-H2SiO3+H2O
四、交换剂再生原理:
R’-SO4Na2SO4
R’-Cl+NaOH→NaCl+R’-OH
R’-SiO3Na2SiO3
CaCaCl2
Mg+HCl→MgCl2+HR
NaNaCl
Ca2+Ca2+
R+Na+→NaR+
Mg2+Mg2+
五、离子交换剂的类型
1.阳离子交换剂
(1)合成阳离子交换剂强酸交换剂带有硫酸氢磺基,其酸度接近于硫酸,弱酸交换剂带有碳酸氢根羧基,其酸度相似于草酸。
(2)磺化聚苯乙烯
(3)羧基交换剂
此类通式为碳酸氢---R的产品是弱酸型的它们能跟着相应于碳酸氢盐的钙、镁离子,氯化氢等阳离子,释放出碳酸但不能交换相应的硫酸盐,硝酸盐阴离子平衡的阳离子。
2.阴离子交换剂
合成碱基团,如叔胺,季胺官能团,有无机或有机阴离子,并能相互交换或与氢氧根交换。
六、在工作交换时的容量与下列因素有关
a)交换剂粒度:
颗粒小,容量大,但Δp大,水出口速度降低。
b)交换剂高度:
高度越高,则效率越高、容量越大。
Hmin=1.2m
c)进出口的硬度越大,含盐量中Na+浓度越小,则容量越大。
d)交换器的构造:
在h一定时,d越小容量越大。
另外,生水再生液的分配有也有影响。
e)运行条件:
水速越小,容量越大。
在工作温度范围内,可适当提高温
f)交换剂污染程度越大,容量越大,且再生过程适中。
七、水处理的工艺流程图:
1
过滤器并联
3排水
5
24
3个钠离交换并联
1.石灰水槽2.过滤器3.盐水再生槽
4.盐水再生器5.钠离子交换器
锅炉工段
一、岗位任务
主要利用烟煤做燃料,将软水加热成合格的蒸汽,供造气和变换工段使用。
二、工艺指标
DG20-2.5/400-2型锅炉项目指标值
软水压力
≥3.0MPa
连续排污
长排
锅管内蒸汽压力
≤2.5MPa
定期排污
根据炉水分析数据
送变换减压后
1.2-1.4MPa
安全阀手机排气实验
1次/天
炉堂负压
-20-40Pa
鼓风机电机电流
<200A主床
水位计压力表冲洗
2次1班
<30A引床
过热蒸汽温度
400℃
引风机电机电流
<200A
排烟温度
≤160℃
给风粒度
<8nm
锅炉液位
1/2-2/3
各电机温度
<60℃
炉水溶解固形物
≤2500mg/L
主床温度
850-950℃
相对碱度
<0.2
引床温度
750-950℃
炉水PO43-
10-30mg/L
锅炉煤料储量
60-90%
炉水SO42-
50-150mg/L
给水中溶解氧
<0.2mg/L
炉水Cl-
<150mg/L
主床风压
60×100Pa
副床风压
25×100Pa
炉堂
2×10Pa
给水流量
12.8t/h
额定蒸发量
20t/h
额定蒸汽压力
2.5MPa
额定蒸汽湿度
400℃
给水温度
104℃
主蒸汽
1.5MPa
送变换
1.2MPa
送造气
0.45MPa
给总水管
3.2MPa
主风床箱
6000Pa
副风床箱
2500Pa
蒸汽过滤器热后
328℃
主床(下段)
975℃
主床(中段)
985℃
主床(下段)
790℃
副床(中段)
824℃
总给室
855℃
排烟
176℃
省煤器出口水(一级):
103℃
出口水(软水,二级)
60℃
引风机
112℃
主床风机
150℃
副床风机
16℃
给水机
1#600r/min
2#550r/min
三、工艺流程图放安全阀
气
省煤器
上锅炉
软水
分气缺
水
测连箱
下锅炉
排污阀
造气工段
一、岗位任务
采用间歇或固定层常压汽化法,即以焦碳(或焦碳加无烟块煤)原料在高温下,交替与空气和过热蒸汽进行气化反应,制得足够数量的合格的半水煤气以供后工段连续生产的需要。
二、工艺指标
(一).造气炉微机操作指标
1.减压前蒸汽压力
造气不使用减压阀0.1~0.2mpa造气使用减压阀0.3~0.5mpa
2.减压后蒸汽压力0.05~0.08mpa
3.ZF操作工艺指标一览表
(1)循环时间的分配(每个循环25分钟)
吹风20~24%(30~36s)上吹24~28%(36~42s)
下吹42~46%(63~69s)二次上吹4~7%(6~10.5s)
空气吹净2~3%(3~4.5s)
(2)上加时间12~25S(3)回收时间1~3s
(4)总风调节2.5s(5)下吹调节3.5s
(6)回收调节3~5s(7)上加调节0~10s
(8)炉条中值50%(9)炉条调节15~35%
(10)加氮下限6~20s(11)加氮上限18.5~20s
(12)加氮中值8~16s
4.ZF目标工艺指标一揽表
空层温度350~550℃上行炉气温度350~550℃
温度系数300~380温度不均≦100℃
炉底温度180~300℃最高底温<350℃
下行炉气温度250~300℃热炭温度1.0~1.5℃
气化位置0.8~1.2℃灰渣温度0.18~0.22℃
流通系数40左右回收吹风0.75
上加吹风0.11~0.12上加回收0.2~0.25
5.气柜进口煤气温度<40℃
(二).造气主控操作指标
1.半水煤气中二氧化碳<10%
2.半水煤气中氧气≦0.5%
0.7%减量生产1.0%停车处理2.0%立即紧急停车
3.合成循环气中氢气/氮气2.0~2.8
4.加氮气设定
(1)加氮气下限5~10s
(2)加氮气上限5~20s
(3)加氮气中值8~16s
5.气柜高度
(1)高限≦2000m3低限≧700m3
6.炉条机转数
(1)炉况正常时250~400转/分
(2)炉况异常时根据实际情况调转
7.下灰次数4~6次/班.台炉
(三).造气液压油泵汽包操作指标
1.夹套汽包压力<0.2mpa2.夹套汽包液位1/2~2/3
3.夹套温度<135℃4.夹套炉水中含盐量≦3000mg/L
5.夹套汽包液位计冲洗2次/班.台炉6.夹套排污2次/班.台炉
7.夹套汽包给水压力≧0.6mpa8.液压油泵油箱油位4.0~6.0mpa
9.液压油泵油箱油位2/5~4/510.液压油泵出口总管压力4.0~6.0mpa
11.液压循环油冷却后温度30~50℃
生产气柜高度
(1)高限≦2000m3
(2)低限≧700m3
(四).造气鼓风机,加岗位操作指标
1.空气鼓风机
指标\型号AI200型D300型D400型
鼓风机出口压力(mmHg)<19<24<26.5
鼓风机电流(A)<230<337<390
鼓风机油位1/2~2/3
鼓风机电机温度<60<60<60
鼓风机加油1次/班1次/班1次/班
2.炉条机
(1)炉条机减速装置加油1次/班.台炉
(2)炉条机电流≦7A(3)炉条机电机温度≦60℃
(4)蒸汽贮能器及分离器液位无
3.加炭岗位
(1)加炭间隔时间20~30min/台炉
(2)造气炉下灰冷却4~6次/班.台炉
(3)旋风除尘器下灰吹1次/班(4)电动葫芦加油1次/班
(五).其它
1.洗气塔冷却水压力>0.15mpa2.各炉洗气塔出口温度 <50℃
3.各闸加油 1次/班 4.检查气柜加油 1次/班
三、注意事项
1.严格控制氧含量,超过0.5%时,应连续分析,防止过氧事故发生,高达1%时应立即停车.
2.炉温偏低(<500℃)应打开炉盖前点火防爆.
3.柜开车或大修后开车,应用贫气(一氧化碳和氢气<8%,氧气<1%)置换合格后才能导入煤气.
四、造气工段工艺流程
流程中包括煤气发生炉,煤气的除尘,降温,余热回收,贮存设备等.
半水煤气流程:
半水煤气发生炉——除尘过滤器——洗气塔——气柜——脱硫
——烟囱
水蒸气流程:
水蒸气——过热器——半水煤气发生炉
蒸汽缓冲器
五、兴乐化工开元化工公司制半水煤气的方法:
间歇式 即先送入空气以提高燃料层温度,生成气体大部分防空,然后送入蒸汽进行气化反应,此时引起燃料层温度下降,所得煤气配入部分吹风气即成半水煤气。
六、煤气炉燃料层的分类:
1.干燥区 即最上部燃料与煤气接触,水分蒸发
2.干馏区 燃烧下移受热,释放出烃类气体
3.气化区 当气体气化剂为空气时,在气化区的下部主要进行碳的燃烧反应,称为氧化层,其上部主要进行与二氧化碳的反应,称为还原层。
当以水蒸汽为气化剂时,在气化区进行碳——水蒸气反应,即
C+H2O=(g)CO+H2C+H2O(G)=CO2+2H2
4.灰渣区 即燃料层底部,灰渣区一方面可预热从底部进入的气化剂,保护炉底不致过热而变形。
七、间歇式制半水煤气的工作循环
1.吹风阶段 吹入空气,提高燃料层温度,吹风气放空。
2.一次上吹制气阶段 自下而上送入水蒸气进行气化反应,燃料层下部温度下降,上部升高。
3.下吹制气阶段 水蒸气自上而下进行气化反应,使燃料层温度趋于平衡。
4.二次上吹制气阶段 将炉底部下吹煤气排净,为吹入空气作准备。
5.空气吹净接 此部分吹风气加以回收,作为半水煤气中氮的主要来源。
八、间歇式制半水煤气的工艺条件
随燃料性能的不同而有很大的差异,其中燃料性能包括原料的粒度,灰熔点,机械强度,热稳定性以及反应活性。
1.温度:
(1)燃料层温度是沿着炉的轴向而变化,氧化层的温度最高,操作温度指氧化层温度,简称炉温。
(2)高温时表现为蒸汽分解率高,煤气产量高,质量好。
(3)炉温度是由吹风阶段确定的,高炉温将导致吹风气温度高,而且一氧化碳含量多,造成热损失大。
(4)为解决
(2),(3)两点之间的矛盾,在流程设计中,应对吹风哎的里热及燃烧热作充分的回收,并根据一氧化碳的反应特点,加大风速以及降低吹风气中一氧化碳的含量,因此以略低于燃料的灰溶点维持炉内不致结疤为条件,尽量在较多温度下操作。
2.吹风速度:
(1)提高炉温的主要手段是增加吹风速度和延长吹风时间,增加吹风速度对制气时间无影响,而延长吹风时间使制气时间缩短,不利提高产量。
(2)在氧化层中,碳的燃烧反应速率很快,属扩散控制,而在还原层中,二氧化碳的还原速率较慢,属动力学控制。
(3)提高吹风速度可使氧化层反应加速,切使二氧化碳在还原层停留时间减少,最终表现为吹风气中一氧化碳含量降低,从而减少热损失。
(4)风量过大将导致飞灰增加,燃料素食增大,甚至燃料层出现风洞以致被吹翻,造成气化条件严重恶化,同时也使鼓风机电耗增加。
3.蒸汽用量
蒸汽用量是改善煤气产量与质量的重要手段之一。
(1)蒸汽一次上吹制气时,炉温较高,煤气产量与质量较好,随制气的进行,气化区温度迅速下降上移,造成出口煤气温度升高,热损失加大,因而上吹时间不宜过长。
(2)蒸汽下吹时,使气化区恢复到正常位置,由于蒸汽温度较高,制气情况良好,而下吹时间比上吹时间长。
(3)蒸汽用量过大会导致分解率降低。
(4)生产中,可在制气阶段加入部分空气,称为“加氮空气”。
4.燃料层高度
对粒度较大,热稳定性较好的燃料,采用较高的燃料层;对颗粒小或热稳定性差的燃料,其高度不宜过高。
(1)较高的燃料层将使水蒸气停留时间加长,而且燃料层温度较为稳定,有利于提高蒸汽分解率。
(2)吹风阶段由于空气与燃料接触时间加长,吹风气中一氧化碳含量增加。
5.循环时间及其分配
循环时间即每一个工作循环所需时间
循环时间长,气化层温度和煤气的产量,质量波动大,反之。
6.气体成分
调节半水煤气中一氧化碳和氢气与氮气的比值方法是改变加氮空气量或改空气吹净时间。
洗气箱作用
用以防止水封以后的煤气倒回到炉口和空气混合发生爆炸并有冷却和除尘作用。
洗气塔作用
出洗气箱的气体温度约在80℃左右,必须予以冷却,而且,出洗气箱的气体中还混有制气时未分解的蒸汽和带有很多灰尘,因此,洗气塔担负着冷却、冷凝和除尘的任务。
煤气发生炉的开停车
1.开车步骤
(1)加炭,联系电机房开高压水泵和鼓风机
(2)盖好试火孔和炉盖
(3)启动自动机电动机
(4)拉出水压把
(5)拉开吹风阀操纵杆进行吹风
(6)插上制气把进行正常循环
2.停车步骤
(1)待指针教至5%吹风位置时,拔出制气把
(2)关吹风阀,推下停车把
(3)停下自动机电动机
(4)视仪表指示正常,打开试火孔点火及开炉盖
(5)发出停车讯号,联系有关岗位停车
九、造气工艺流程图:
锅炉送来的蒸汽总管
洗气塔
气柜
加热蒸汽汽包
下吹汽包蒸汽加热器
煤气发生炉烟囱
去
脱硫工段
一、主要任务
1.脱硫任务:
脱去半水煤气中的硫化氢以及其他含硫化合物,制得合格的半水煤气。
2.脱硫原理:
氨水中和法脱硫
NH4OH+H2S=NH4HS+H2ONH4OH+CO2=(NH4)2CO3+H2O
(NH4)2CO3+H2S=NH4HS+NH4HCO3
NH4OH+HCN=NH4CN+H2O
3.影响脱硫效率的主要因素:
(1)氨水浓度
提高氨水浓度对提高吸收效率有利,但过高氨损耗大,切有可能与煤气中的二氧化碳作用生成氨基钾酸铵。
(2)氨水温度
氨水很容易挥发,而且温度越高,氨挥发得越多,引起氨水浓度的下降。
(3)气液比
气液比一般控制在3~4升/m3气体。
(4)氨水中二氧化碳的含量高相对就减少了氨含量,因而氨水中的硫化氢与二氧化碳的含量越低越好。
二、工艺指标:
罗茨机进口压力
2~3kpa(210~310mmHg)
罗茨机出口压力
26~59kpa(200~375mmHg)
系统压差
<5kpa(40mmHg)
脱硫塔进口氨水温度
<35摄氏度
脱硫氨水泵出口压力
>0.3mpa
罗茨机油位
1/2~2/3
氨水再生泵出口压力
>0.4mpa
脱硫液中氨浓度
400~800mol/m3
进冷却塔水压
>0.15mpa
脱硫液中PH值
8.0~8.5
罗茨机进口煤气温度
<25摄氏度(夏)
<15摄氏度(冬)
半水煤气中氧气
≦0.5%
脱硫后半水煤气中硫化氢
≦0.07g/Nm3
罗茨机出口煤气温度
<60摄氏度
气柜高度
700~2000m3
冷却塔后煤气温度
<40摄氏度
三、脱硫工艺流程图
水管
煤气总管除焦塔冷却塔脱硫塔
半水煤气
罗茨机
除尘器
水槽
冷却罐
脱硫泵
再生泵
贫液富液再生塔
四、主要设备
1.脱硫塔:
两段式端动塔,内设海环起缓冲作用,之逆流接触的氨水和半水煤气充分接触利于脱硫。
2.再生塔:
喷射式包括喷射式组、浮选槽、液位调节器
3.综合除尘器:
内循环
五、技术指标
脱硫催化剂:
888加入捅中水溶解并混合均匀,再均匀地加入氨水中。
湿法脱硫优点:
1.脱硫剂便于输送。
2.脱硫剂可以再生产并能回收富有价值的化工原料硫磺。
任何一种化学反应吸收都是用碱性溶液吸收酸性气体硫化氢,加使脱除的硫化氢变为有用的硫,可以选择适当的氧化催化剂,将溶液中被吸收的硫化氢氧化成单体硫,因而使脱硫溶液得到再生。
载氧体(氧化态)+硫化氢=载氧体(还原态)+硫
载氧体(还原态)+1/2氧气=载氧体(氧化态)+水
脱硫剂的再生
NH4HS+1/2O2===NH4OH+SH2S+1/2O2==H2O+S
2NH4HS+2O2===(NH4)2S2O3+H2O2NH4OH+2S+O2===(NH4)2S2O3+H2O
脱硫优点:
脱硫剂无毒,脱硫效率较高,半水煤气中二氧化碳损失较少,能回收硫磺,消耗定额较低,但工艺流程较复杂,所花建设资金和所用钢材较多。
用添加少量对苯二酚的氨水溶液,吸收半水煤气中的硫化氢,吸收液在再生塔中与空气接触,硫化氢即被氧化或元素硫。
氨水溶液再生后,循环使用,再生过程中消耗的氨及损耗的对苯二酚,定期补充。
影响脱硫效率的主要因素:
1.溶液循环量
循环量愈大,对吸收硫化氢愈有利,但循环量过大,则动力消耗增高,不经济。
循环量过小,不能满足吸收硫化氢的要求,因此溶液循环量应该控制在一定范围。
2.再生不完全
再生后溶液中硫化氢含量较高时,脱硫效率下降。
3.溶液温度
溶液温度越低,脱硫效率越高,反之脱硫效率降低。
4.填料表面积和溶液喷淋情况
喷料表面积大,可以增加气液接触时间,对提高脱硫效率有利。
5.进脱硫塔半水煤气中硫化氢含量高,则脱硫塔气体中硫化氢含量也相应增高。
影响再生效率的因素:
1.溶液中对苯二酚的加入量:
对苯二酚加入过多,可能造成溶液提前进行再生反应,析出固体硫磺而发生堵塞泵和管道的现象。
2.再生空气量:
空气过多,动力消耗高,反之对再生反应不利。
3.溶液在再生槽内停留时间的长短决定于液气比对芬二酚量,空气量和溶液中硫化氢的高低来确定。
工艺指标中的分析频率
半水煤气中硫化氢(脱硫前)
1次/小时
半水煤气中硫化氢(脱硫后)