最新版北京科技大学毕业课程设计连铸车间设计.docx
《最新版北京科技大学毕业课程设计连铸车间设计.docx》由会员分享,可在线阅读,更多相关《最新版北京科技大学毕业课程设计连铸车间设计.docx(19页珍藏版)》请在冰豆网上搜索。
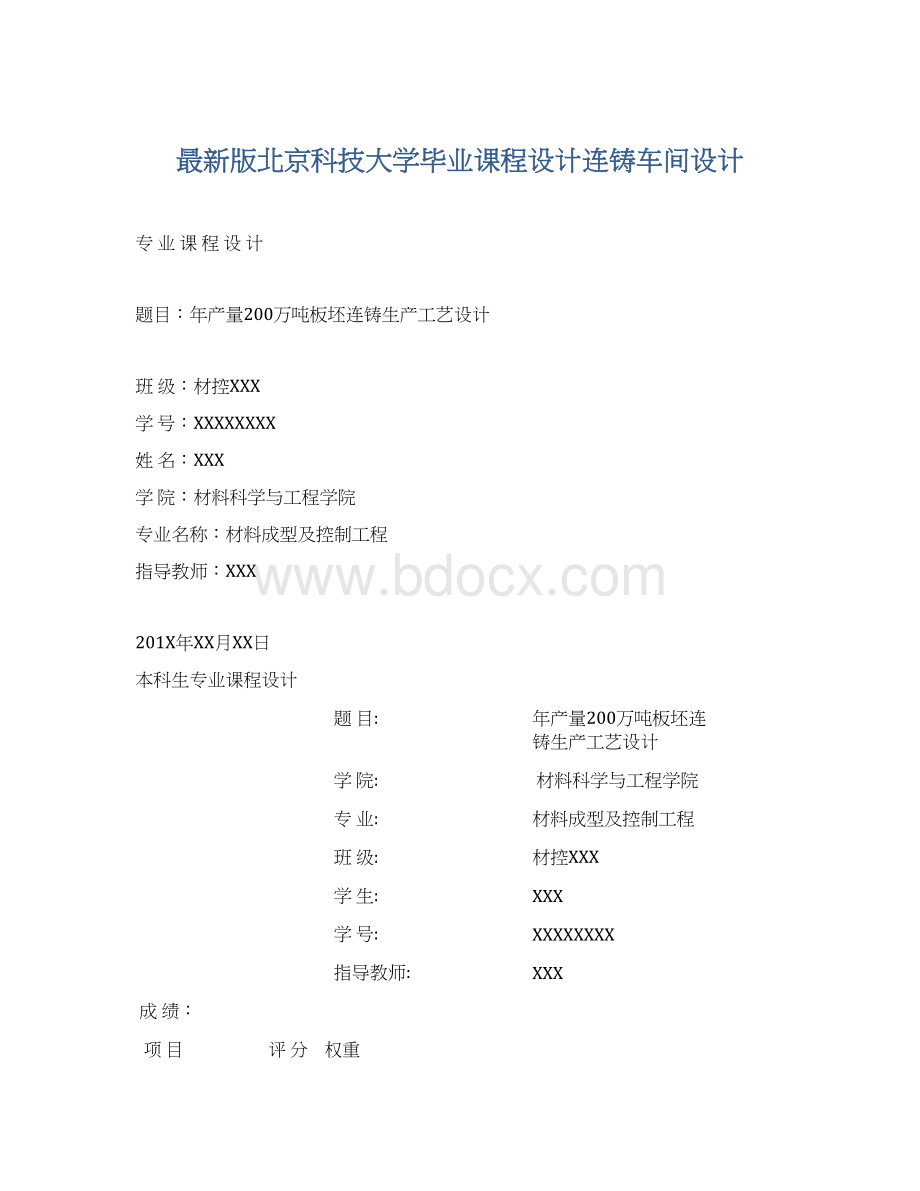
最新版北京科技大学毕业课程设计连铸车间设计
专业课程设计
题目:
年产量200万吨板坯连铸生产工艺设计
班级:
材控XXX
学号:
XXXXXXXX
姓名:
XXX
学院:
材料科学与工程学院
专业名称:
材料成型及控制工程
指导教师:
XXX
201X年XX月XX日
本科生专业课程设计
题目:
年产量200万吨板坯连铸生产工艺设计
学院:
材料科学与工程学院
专业:
材料成型及控制工程
班级:
材控XXX
学生:
XXX
学号:
XXXXXXXX
指导教师:
XXX
成绩:
项目
评分
权重
平时成绩
0.2
说明书及图纸
0.4
答辩评分
0.4
综合成绩
目录
一、绪论2
二、产品大纲及生产工艺流程4
1.产品大纲4
2.生产工艺流程4
三、连铸机设备参数的计算5
1.连铸机类型选择5
2.连铸机流数6
3.中间包容量6
4.设备清单7
四、连铸主要工艺参数11
1.浇注温度11
2.浇注时间11
3.拉速12
4.连铸机冶金长度12
5.结晶器长度13
6.铸机的弧形半径13
7.匹配系数计算13
五、金属平衡图15
六、连铸机主要性能参数16
1.连浇炉数16
2.浇注周期16
3.连铸机的作业率αp16
4.金属收得率17
5.连铸机生产能力17
6.生产能力校核18
七、参考文献19
工艺设计任务书
一、学生姓名:
XXX学号:
XXXXXXXX
二、题目:
年产量200万吨板坯连铸生产工艺设计
已知:
1.某钢铁厂拟新建一板坯连铸车间,生产的典型钢种为压力容器用钢板16MnR、碳素结构钢板Q195,化学成分是:
16MnR钢:
C:
≤0.20,Si:
0.20~0.55,Mn:
1.20~1.60,P:
≤0.035,S:
≤0.030,Cr:
≤0.,30,Ni:
≤0.,30,Cu:
≤0.30;Cr+Ni+Cu≤0.60;Q195钢:
C:
≤:
0.06~0.12,Si:
≤0.30,Mn:
0.25~0.50,P:
≤0.045,S:
≤0.05,Cr:
≤0.30,Ni:
≤0.30,Cu:
≤0.30。
2.铸坯规格为:
mm×mm(厚度×宽度)。
3.计划采用的转炉容量为100吨,冶炼时间为40分钟。
三、设计任务
1.编写产品大纲,制定典型产品的生产工艺流程。
2.确定连铸设备参数,如连铸机的类型、数量、流数、中间包容量等;提出生产需要的有关设备清单。
3.确定连铸主要工艺参数,如钢水的浇注温度、浇注时间、拉坯速度、板坯尺寸以及冶炼与连铸机的配合。
4.编制金属平衡图。
5.连铸浇注周期、连铸机作业率、连铸坯收得率、连铸机生产能力计算。
6.撰写设计说明书。
四、日程安排
1.2011.12.30~2011.12.31查阅国内外技术资料,制定总体工艺方案;
2.2012.01.01~2012.01.10连铸工艺设计;
3.2012.01.11~2012.01.12编写设计说明书;
4.2012.01.13答辩。
五、参考书目
[1]陈家祥主编.连续铸钢手册.冶金工业出版社.1991.12.
[2]李传薪主编.钢铁厂设计原理(下).冶金工业出版社.1995.5.
[3]《中国冶金报》社编.连续铸钢500问.冶金工业出版社.2002.6.
[4]李慧主编.钢铁冶金概论.冶金工业出版社.1993.11.
[5]陈雷.连续铸钢.冶金工业出版社.1994.5.
一、绪论
连铸即为连续铸钢(ContinuousSteelCasting)的简称。
在钢铁厂生产各类钢铁产品过程中,使用钢水凝固成型有两种方法:
传统的模铸法和连续铸钢法。
而在二十世纪五十年代在欧美国家出现的连铸技术是一项把钢水直接浇注成形的先进技术。
与传统方法相比,连铸技术具有大幅提高金属收得率和铸坯质量,节约能源等显著优势。
使钢水不断地通过水冷结晶器,凝成硬壳后从结晶器下方出口连续拉出,经喷水冷却,全部凝固后切成坯料的铸造工艺。
同通常钢锭浇铸相比,具有增加金属收得率,节约能源,提高铸坯质量,改善劳动条件,便于实现机械化、自动化等优点。
连铸镇静钢的钢材综合收得率比模铸的约高10%。
沸腾钢连铸比较困难,至今尚未成功。
近年对沸腾钢成分的钢液进行真空“轻处理”,可以顺利地进行连铸。
有色金属的连铸发展比钢铁连铸为早。
如在辊式连铸机上,兼有凝固和塑性变形,则称连续铸轧。
由于连铸简化了炼钢铸锭及轧钢开坯加工工序,每吨钢可节约能量(0.15~0.25)×10千卡,如进一步解决铸坯和成材轧机的合理配合问题,热送直接成材,还可进一步节约能源。
连铸坯在结晶结构上的主要特点是:
连铸工艺使钢水迅速而均匀地冷却,因而迅速形成较厚微晶细粒的表面凝固层,没有充分时间形成柱状晶区;连铸坯断面较小,整罐钢水的连铸从开始到终了的冷却凝固时间接近,连铸坯纵向成分偏析差别可在10%以内,这是模铸钢锭无法与之比拟的;连铸坯不像模铸钢锭那样分单根浇铸,所以可避免形成缩孔或空洞,使金属收得率提高;在塑性加工中,为消除铸态组织所需的压缩比也可较小。
当然,连铸技术也有其缺陷。
在浇铸生产过程中,由于钢水成分、温度、浇铸速度、冷却水强度等控制不当,以及铸机设备安装不合规格等原因,可造成与模铸相似的各种缺陷。
与模铸钢锭的差别是裂纹缺陷比较多见。
近年连铸生产自动化技术迅速发展。
在技术先进的钢厂已经开始实现对钢水成分、温度、结晶器钢液面、铸速、二次水冷却、铸坯质量热检查、定尺切割等用计算机进行全面自动控制;生产过程中有质量不合格铸坯时,实行自动切除;然后热送连轧生产。
中国于50年代开始进行半连铸的工业试验。
1959和1960年间建成直立式方扁坯连铸机。
60年代中期建成弧形板坯连铸机。
同时还建有立弯式小方坯连铸机。
截至1981年,中国投产的连铸机有26台,1981年生产连铸坯254万吨,占全国钢产量的7.65%。
浇铸的钢种有普通碳钢、低合金结构钢、弹簧钢、电工钢等。
连铸坯的品种有120~200毫米方坯,700~2300毫米宽板坯。
80年代在工业发达国家已有不少电炉车间实现了全连铸化,新建大型转炉车间也有全连铸的。
浇铸的钢种在1970年以前大多是普通碳素钢。
目前除极少数高碳、高合金钢和易产生裂纹的钢种,如含铅易切削钢、高速工具钢和某些轴承钢及阀门钢,连铸尚有困难外,约有85%钢种都能连续浇铸。
70年代采用了电磁搅拌,可提高连铸坯质量。
连铸生产的钢种包括有深冲的薄板钢,高强度的中厚板钢、钢轨钢、弹簧钢、线材钢、不锈耐酸钢等。
特别是不锈耐酸钢,目前全世界约有50%以上是用连铸法生产的。
生产的板坯最大尺寸为宽2640毫米,厚350毫米;方坯最大为560×400毫米,最小为50×50毫米,实际生产中常控制在100×100毫米以上;圆坯最大为φ450毫米,最小为φ40毫米。
由于连铸的种种优势,它是最近几十年来钢铁行业的重点和热点问题。
作为钢铁行业的本科生,对连铸技术有一定的了解也显得十分必要。
因此,借助此次课程设计的机会,我全面地学习了连铸的基本知识,并在老师的指导下完成了这篇车间设计论文。
以上。
二、产品大纲及生产工艺流程
1.产品大纲
1)生产规模
计划年产合格铸坯:
200万吨年
2)产品分类(见表1)
表1产品规格及分类
铸坯断面mm×mm
钢号
钢种
年产量wt
比例%
200×1600
16MnR
压力容器用钢
50
25
200×2100
16MnR
压力容器用钢
50
25
270×1600
Q195
优质碳素结构钢
50
25
270×2100
Q195
优质碳素结构钢
50
25
2.生产工艺流程
本连铸车间的生产工艺流程为:
将原料送入100吨转炉冶炼后,再由精炼炉精炼,制得的钢水装入钢包,经天车运至钢水包回转台。
回转台转动到浇注位置吼,将钢水注入中间包,中间包再经水口将钢水分配到各个结晶器中。
钢水在结晶器中迅速凝固成形,得到带液心的铸坯,铸坯经由二次冷却装置冷却,拉坯矫直装置矫直后,送交切割机切成符合用户要求的板坯长度,再由打印机打印注明生产批次及相关数据。
得到的板坯经垛板台垛板后,一部分经热送辊道送入轧钢车间,余下部分未充分冷却的送入冷床冷却,之后一并清理检查,再次交友冷床冷却,之后作为车间成品外运。
生产工艺流程如下图:
三、连铸机设备参数的计算
3.连铸机类型选择
现在世界各国使用的连铸坯有立式、立弯式、弧形、椭圆形和水平式5种。
据不完全统计,目前世界上所建的连铸机中,立式占17%,立弯式占21%,弧形占55%,其他形式占7%。
目前新建的连铸机是弧形的最多。
立式连铸机从中间包到切割站等主要设备都排在一条垂直绳上。
整个机身矗立在车间地平面上或者布置在地下的深坑内。
这种连铸机占地面积小,设备紧凑,高温铸坯无需弯曲变形,铸坯表面和内部裂纹少,铸坯内凝固液体中夹杂物容易上浮,钢水比较“干净”,二次冷却装置和夹辊等结构简单,便于维护。
立式连铸机的缺点是机身高达20~46m,必须加高厂房或深挖地坑,基建费用昂贵;因不能把连铸机高度增加过高,故只能低速浇注,生产率低。
适用于优质钢、合金钢和对裂纹敏感小断面钢种铸坯的浇注。
立弯式连铸机与立式相比,机身高度降低,节省投资;水平方向出坯,加长机身比较容易,可实现高速浇注;铸坯内未凝固钢液中得夹杂物易上浮,夹杂物分布均匀。
缺点是因铸坯要经过一次弯曲一次矫直,故容易产生内部裂纹;铸机高度虽然降低,但基建费用依然较高。
结晶器和立式连铸机一样都是直的,属于过渡机型。
弧形连铸机采用的是具有某一曲率半径的弧形结晶器。
其结晶器,二次冷却装置和拉矫设备都布置在某一半径的一个圆的四分之一弧度上。
铸坯在结晶器内凝固时就已经弯曲,带液心的铸坯从结晶器拉出来,沿着弧形轨道运行,继续喷水冷却,在四分之一圆弧处完成凝固,然后矫直并拉出送至切割站。
弧形连铸机的高度仅为立式的三分之一,建设费用低,钢水静压力小,铸坯在辊间的鼓肚小,铸坯质量好;加长机身也比较容易,故可高速浇注,生产率高。
弧形连铸机的缺点是:
因铸坯弯曲矫直,容易引起内部裂纹;铸坯内夹杂物分布不均,内弧侧存在夹杂物的聚集;设备较为复杂,维修也较困难。
弧形连铸机虽然有缺点,但由于在设备和工艺上的技术进步,仍然是世界各国钢厂采用最多的一种机型。
垂直弯曲型连铸机也就是带直结器的弧形连铸机,这种连铸机成为垂直弯曲型连铸机。
该种铸机的垂直段较短,一般仅为2~3m,铸坯带液相弯曲和矫直。
它保持了立式连铸机的夹杂物易上浮的特点,但由于铸坯带液相弯曲和矫直,因而设计中应尽量降低弯曲和矫直点铸坯两相界面处的变形率以保障内部质量。
椭圆形连铸机又称为超低头连铸机,它的结晶器、二次冷却段、夹辊和拉坯矫直机均布置在14椭圆弧上,椭圆形圆弧是由多个半径的圆弧线所组成,其基本特点与弧形连铸机相图。
水平连铸机的结晶器、二次冷却区、拉坯矫直机、切割装置等设备安装在水平位置上。
水平连铸机的中间罐与结晶器是紧密相连的。
中间罐水口与结晶器相连接处装有分离环。
拉坯时,结晶器不振动,而是通过拉坯机带动铸坯做拉——反推——停不同组合的周期性运动来实现的。
水平连铸机是高度最低的连铸机,其设备简单,投资省,维护方便。
水平连铸机结晶器内钢液静压力小,避免了铸坯的鼓肚变形,中间罐与结晶器之间是密封连接,有效防止了钢液流动过程中的二次氧化;铸坯的清洁度高,夹杂物含量少,一般仅为弧形连铸坯的18~116、另外,铸坯无需矫直,也就不存在由于矫直弯曲而产生裂纹的可能性