模具设计与制造毕业设计论文.docx
《模具设计与制造毕业设计论文.docx》由会员分享,可在线阅读,更多相关《模具设计与制造毕业设计论文.docx(24页珍藏版)》请在冰豆网上搜索。
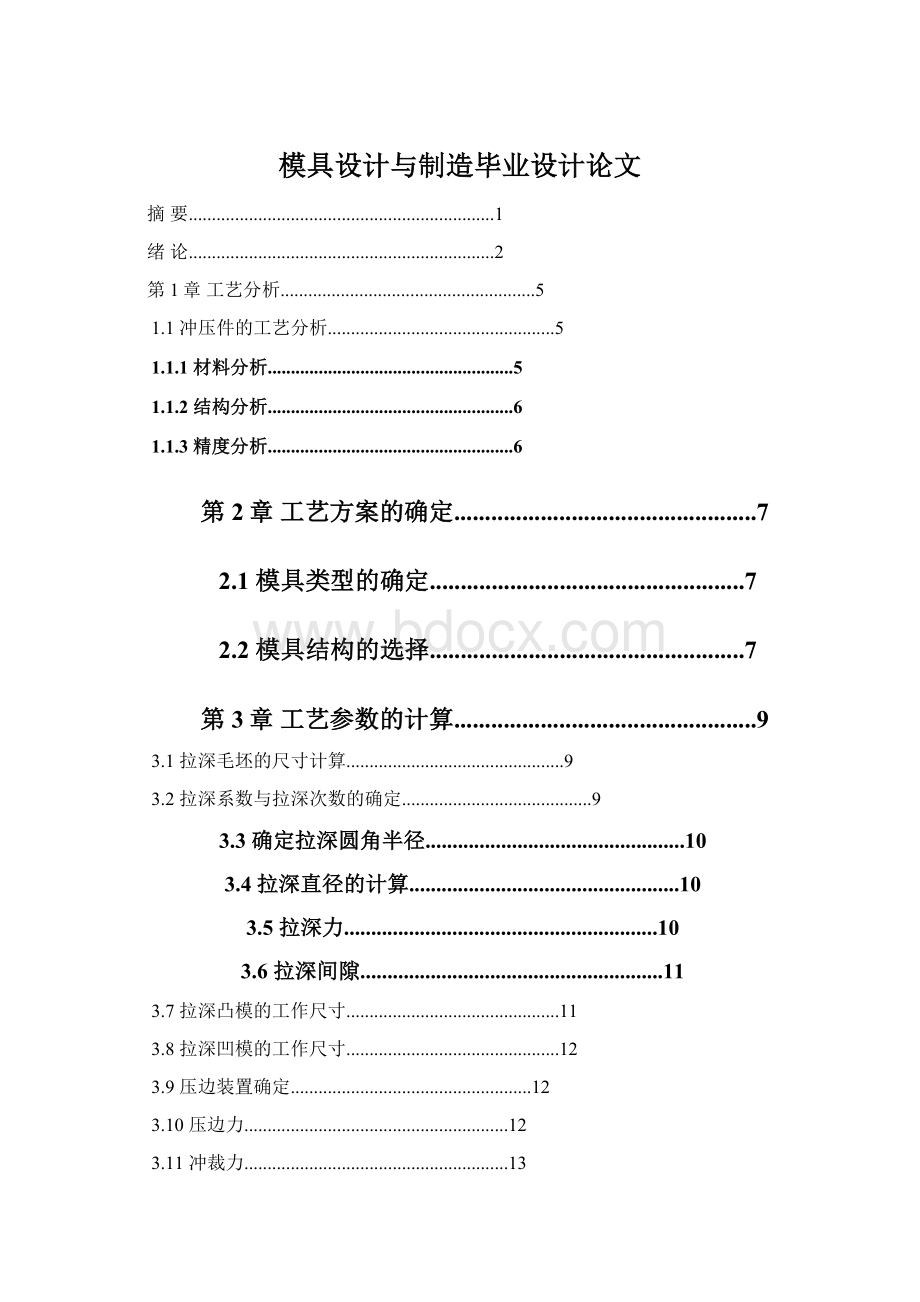
模具设计与制造毕业设计论文
摘要..................................................................1
绪论..................................................................2
第1章工艺分析.......................................................5
1.1冲压件的工艺分析.................................................5
1.1.1材料分析.....................................................5
1.1.2结构分析.....................................................6
1.1.3精度分析.....................................................6
第2章工艺方案的确定.................................................7
2.1模具类型的确定...................................................7
2.2模具结构的选择...................................................7
第3章工艺参数的计算.................................................9
3.1拉深毛坯的尺寸计算...............................................9
3.2拉深系数与拉深次数的确定.........................................9
3.3确定拉深圆角半径................................................10
3.4拉深直径的计算..................................................10
3.5拉深力..........................................................10
3.6拉深间隙........................................................11
3.7拉深凸模的工作尺寸..............................................11
3.8拉深凹模的工作尺寸..............................................12
3.9压边装置确定....................................................12
3.10压边力.........................................................12
3.11冲裁力.........................................................13
3.12冲裁凹模的工作尺寸.............................................13
3.13冲裁凸模的工作尺寸.............................................14
3.14相关计算.......................................................15
3.14.1排样设计...................................................15
3.14.2压力机的公称压力...........................................15
第4章模具主要零件的设计............................................16
4.1冲裁凹模的结构设计..............................................16
4.2压边圈..........................................................17
4.2.1压边圈内径尺寸计算...........................................17
4.2.2压边圈外径尺寸计算...........................................17
4.3拉深凸模的结构计算..............................................18
4.4凸凹模的结构设计................................................19
第5章模架的选择....................................................20
第6章压力机的选择..................................................22
6.1压力机的选择....................................................22
6.1.1冲裁拉深模的闭合高度的计算...................................22
6.2压力机的校核...................................................23
设计总结..............................................................24
设计图纸
制造的模具装配图
加工零件图
加工工艺卡
模具加工、装配、调试总结...............................................25
模具实物图
参考文献..............................................................26
致谢词................................................................27
摘要
简短介绍了我国模具行业发展状况,以及在当下模具行业情况,并且对国内外模具行业发展现状加以分析,从而对我国模具行业与国外模具行业进行了综合比较提出差距所在。
同时介绍了模具的类型和主要功能。
综合阐述对焊片落料拉深模具进行设计,首先对工件进行工艺分析,对拉深特点拉深变形过程进行技术分析。
在设计之前先确定修边余量和毛坯尺寸是否需要使用压边圈。
其次对拉深模具进行总体设计,了解拉深模具结构、分类,选择压边装置。
然后确定工作部分结构参数,确定拉深系数及工序尺寸。
计算凸模圆角半径、凹模圆角半径、间隙、凸、凹模尺寸公差、压边力、压边圈尺寸、拉深力、卸料力、拍样计算,并计算压力中心对压力机进行选择。
最后选择模具主要零部件及结构,对模具材料、模架进行选择,计算凸模长度、凹模高度和壁厚、凸模固定板尺寸以及校核凸、凹模强度。
同时设计选择其他零部件,确定模具闭合高度,对拉深模具进行安装调试。
关键词模具;落料;拉深
绪论
1.1模具在加工工业中的地位
目前,随着汽车及轻工业的迅速发展,模具设计制造日益受到人们的广泛关注,将高新技术应用于模具设计与制造,已成为快速制造优质模具的有力保证:
CAD/CAM的广泛应用,显示了用信息技术带动和提升模具工业的优越性。
在CAD的应用方面,已经超越了图板、二维绘图的初级阶段,目前3D设计如PRO/E、UG等软件的应用很普遍。
现代生产中,合理的加工工艺、高效的设备、先进的模具是必不可少是三项重要因素,尤其是模具对实现材料加工工艺要求、塑料制件的使用要求和造型设计起着重要的作用。
高效的全自动设备也只有装上能自动化生产的模具才有可能发挥其作用,产品的生产和更新都是以模具的制造和更新为前提的。
由于制件品种和产量需求很大,对模具也提出了越来越高的要求。
因此促进模具的不断向前发展
1.2冲压技术的现状及发展方向
随着科学技术的不断进步和工业生产的迅速发展,许多新技术、新工艺、新设备、新材料不断涌现,因而促进了冲压技术的不断革新和发展。
其主要表现和发展方向如下。
1.2.1冲压技术的现状
目前,国内外对冲压成形理论的研究非常重视,在材料冲压性能研究、冲压成形过程应力应变分析、板料变形规律研究及坯料与模具之间的相互作用研究等方面均取得了较大的进展。
特别是随着计算机技术的飞跃发展和塑性变形理论的进一步完善,近年来国内外已开始应用塑性成形过程的计算机模拟技术,模拟金属的塑性成形过程,根据分析结果,设计人员可预测某一工艺方案成形的可行性及可能出现的质量问题,并通过在计算机上选择修改相关参数,可实现工艺及模具的优化设计。
这样既节省了昂贵的试模费用,也缩短了制模具周期。
研究推广能提高生产率及产品质量、降低成本和扩大冲压工艺应用范围的各种压新工艺,也是冲压技术的发展方向之一。
目前,国内外相继涌现出精密冲压工艺、软模成形工艺、高能高速成形工艺及无模多点成形工艺等精密、高效、经济的冲压新工艺。
其中,精密冲裁是提高冲裁件质量的有效方法,它扩大了冲压加工范围,目前精密冲裁加工零件的厚度可达25mm,精度可达IT16~17级;我国已自主设计制造了具有国际领先水平的无模多点成形设备,解决了多点压机成形法,从而可随意改变变形路径与受力状态,提高了材料的成形极限,同时利用反复成形技术可消除材料内残余应力,实现无回弹成形。
无模多点成形系统以CAD/CAM/CAE技术为主要手段,能快速经济地实现三维曲面的自动化成形。
精密、高效的多工位及多功能级进模和大型复杂的汽车覆盖件冲模代表了现代冲模的技术水平。
目前,50个工位以上的级进模进距精度可达到2微米,多功能级进模不仅可以完成冲压全过程,还可完成焊接、装配等工序。
我国已能自行设计制造出达到国际水平的精度达2
~5微米,进距精度2~3微米,总寿命达1亿次。
我国主要汽车模具企业,已能生产成套轿车覆盖件模具,在设计制造方法、手段方面已基本达到了国际水平,但在制造方法手段方面已基本达到了国际水平,模具结构、功能方面也接近国际水平,但在制造质量、精度、制造周期和成本方面与国外相比还存在一定差距。
1.2.2冲模具的发展
在冲模的设计制造上,目前正朝着以下两方面发展:
一方面,为了适应高速、自动、精密、安全等大批量现代生产的需要,冲模正向高效率、高精度、高寿命及多工位、多功能方向发展,与此相比适应的新型模具材料及其热处理技术,各种高效、精密、数控自动化的模具加工机床和检测设备以及模具CAD/CAM技术也在迅速发展;另一方面,为了适应产品更新换代和试制或小批量生产的需要,锌基合金冲模、聚氨酯橡胶冲模、薄板冲模、钢带冲模、组合冲模等各种简易冲模及其制造技术也得到了迅速发展。
1.3冲压模的工艺与冲压模具
冲压是利用安装在冲压设备(主要是压力机)上的模具对材料施加压力,
使其产生分离或塑性变形,从而获得所需零件(俗称冲压或冲压件)的一种压力加工方法。
冲压通常是在常温下对材料进行冷变形加工,且主要采用板料来加工成所需零件,所以也叫冷冲压或板料冲压。
冲压所使用的模具称为冲压模具,简称冲模。
冲模是将材料(金属或非金属)批量加工成所需冲件的专用工具,是冲压加工的三要素之一。
与机械加工及塑性加工的其它方法相比,冲压加工无论在技术方面还是经济
方面都具有许多独特的优点。
主要表现如下。
(1)冲压加工的生产效率高,且操作方便,易于实现机械化与自动化。
这是因为冲压是依靠冲模和冲压设备来完成加工,普通压力机的行程次数为每分钟可达几十次,高速压力要每分钟可达数百次甚至千次以上,而且每次冲压行程就可能得到一个冲件。
(2)冲压时由于模具保证了冲压件的尺寸与形状精度,且一般不破坏冲压件的表面质量,而模具的寿命一般较长,所以冲压的质量稳定,互换性好,具有“一模一样”的特征。
(3)冲压可加工出尺寸范围较大、形状较复杂的零件,如小到钟表的秒表,大到汽车纵梁、覆盖件等,加上冲压时材料的冷变形硬化效应,冲压的强度和刚度均较高。
(4)冲压一般没有切屑碎料生成,材料的消耗较少,且不需其它加热设备,因而是一种省料,节能的加工方法,冲压件的成本较低。
1.4本课题研究的意义
本课题借助绘图软件进行模具设计,内容包括:
工艺分析及工艺方案的确定,压力机的选用等。
并对模具中的有关零件进行强度核算。
设计内容涵盖了整个大学所的课程,是对大学三年学习的一个很好的检验,而且很多方面要靠在设计过程中的自学完成,既能拓展知识面又能锻炼自学能力。
一套设计合理的模具不仅可以生产出高质量的零件,既可以提高材料的利用率又方便操作者操作,大大提高了生产率,为公司创造更大的利益。
第1章工艺分析
1.1冲压件的工艺分析
图1-1工件图
图1-1为拉深件的零件图。
这是焊片,材料为08AL,料厚为2mm,大批量生产。
1.1.1材料分析
08AL钢为优质碳素结构钢,属于深拉深级别钢,具有良好的拉深成形性能。
牌号:
08AL
标准:
GB/T699-1988
特性及适用范围:
为极软的碳素钢,强度、硬度很低,而韧性和塑性极高,具有良好的深冲、拉延、弯曲和镦粗等冷加工性能、焊接性能。
但存在时效敏感性,淬硬性及淬透性极低。
大多轧制成高精度的薄板或冷轧钢带用以制造易加工成形,强度低的深冲压或深拉延的覆盖零件和焊接构件。
化学成份:
碳C:
≤0.12
硅Si:
≤0.03
锰Mn:
≤0.65
硫S:
≤0.035
磷P:
≤0.035
铬Cr:
≤0.10
镍Ni:
≤0.25
铜Cu:
≤0.25
力学性能:
抗拉强度σb(MPa):
≥325(33)
屈服强度σs(MPa):
≥195(20)
伸长率δ5(%):
≥33
断面收缩率ψ(%):
≥60
硬度:
未热处理,≤131HB
试样尺寸:
试样尺寸为25mm
抗剪强度:
280MPa
热处理规范及金相组织:
热处理规范:
正火930℃,45min,空冷。
金相组织:
铁素体+极少量珠光体。
1.1.2结构分析
此零件是轴对称的旋转体,结构简单,零件的最大尺寸为凸缘方向上的尺寸,为d=44mm,属于小型零件,零件的尺寸全部为自由公差,可看作IT14级,尺寸精度较低,该零件的形状和结构表明它为拉深件,所以拉深为基本工序。
通过对零件结构分析可知,该零件主要通过拉深模具成型,并可获得尺寸精度。
通过初步计算可知该拉深件的拉深次数为1,可考虑通过正拉深完成。
因此可知该零件的基本冲压工序为:
落料、正拉深完成。
1.1.3精度分析
零件上尺寸均为未注公差尺寸,普通拉深即可达到零件的精度要求。
第二章工艺方案的确定
2.1模具类型的确定
根据制件的工艺性分析:
因为该模具能在压力机一次行程内,完成落料拉深两道工序,在完成这些工序过程中无需进给移动。
方案可分为以下三种:
方案一:
采用单工序模逐步加工
(1)落料→拉深单工序模
(2)拉深→落料单工序模
方案优缺点:
单工序模(俗称简单模),即在一副模具中只能完成一种工序。
由于采用单工序模,模具制造简单,制造周期短,价格低,维修方便,生产率低,工件精度低,不适合大批量生产,单生产通用性好,适用于中小批量生产。
方案二:
采用级进模加工
方案的优缺点:
级进模具有操作安全的显著特点,模具强度较高,寿命较长。
使用级进模便于冲压生产自动化,可以采用高速压力机生产。
级进模较难保证内、外形性对位置一定。
单级进模轮廓尺寸较大,制造复杂,生产成本较高,一般适用于大批量生产小型零件。
方案三:
采用复合模加工成形
方案的优缺点:
生产效率高,工件内孔与外缘的相对位置精度高,板料的定位精度要求比级进模低,冲模的轮廓尺寸较小。
但模具制造较复杂,制造精度要求高,成本高,调整维修较麻烦,使用寿命低。
主要用于生产批量大、精度要求高的冲裁件。
根据零件的设计要求,以及上述的三种方案的特点来看,决定采用方案三加工比较合理。
2.2模具结构的选择
为了适应大批量生产,采用导柱导向复合模,而且模具安装在压力机上安装比较简单。
操作方便,可降低成本。
落料部分应采用顺装方式设计,拉深部分应采用倒装方式设计。
为节约材料,不采用侧刃定位,用固定定位销定距。
为方便操作和取件,选用单柱式可倾压力机,横向送料。
并且本工件为大批量生产,为降低人力成本,所以采用自动送料装置所以在模具设计过程中不考虑落料后废料的卸料装置。
综上所述:
该模具应选自动送料固定定位销定距倒装复合模。
第3章工艺参数的计算
3.1拉深毛坯的尺寸计算(查参考文献[1]表4-17)
在计算拉深件毛坯尺寸时,应先确定修边余量。
并把修边余量加到拉深件高度上,这时拉伸件的高度(H)为原拉深件高度(h)与修边余量(△h)之和,即d=
+2△h。
1)确定修边余量△h
该拉深件d=27,
=44,
所以
/d=44/27=1.629,
查得△h=2即d=44+4=48。
2)计算毛坯直径D
因为板料厚度为2mm,故需要用零件中线尺寸计算。
D=
式中D——拉深件毛坯尺寸,mm;
r——拉深件底部圆角半径,mm;
H——拉深件高度,mm;
d——拉深件直径,mm。
D=
=53.7527674mm
所以拉深件毛培尺寸为53.7527674mm。
3.2拉深系数与拉深次数的确定(查参考文献[1]表4-18)
1)计算相对高度得:
2)计算毛培相对厚度得:
3)计算凸缘相对直径:
查得要求尺寸的带凸缘件首次拉深最大相对高度
为0.48~0.58。
小于
0.48~0.58所以能一次拉深。
3.3确定拉深圆角半径
因为只需拉深一次所以拉深凸凹模圆角半径为零件圆角半径,均为R2。
3.4拉深直径的计算
由于此工件可一次拉深成形,故拉深直径根据拉深件的零件图进行计算即可。
若是需要多次拉深成形,那么对每次拉深都需要重新计算拉深直径,以满足拉深次数的需求。
3.5拉深力(查参考文献[1]式4-20)
根据拉深力计算公式
式中d1——首次拉深件直径;
t——板料厚度;
——材料抗剪强度;
K1——修正系数。
查表得08AL在常温下抗剪强度280MPa。
考虑到刃口磨损、间隙的波动、材料力学性能的变化、板料厚度的偏差等因素的影响,可取修正系数为K=1。
F=π×27×2×275×1
F=25645.95N
所以拉深件的拉深力为F=25645.95N。
3.6拉深间隙(查参考文献[1]式4-29,表4-8)
根据拉深间隙计算公式
式中
——板料最大厚度;
K——拉深间隙系数,查得为0.07~0.09。
Z=2+2×0.09
=2.18mm
所以拉深间隙为2.18mm。
3.7拉深凸模的工作尺寸(查参考文献[1]式4-31;查参考文献[3]表4-17)
由于产品要求的是内形尺寸所以在计算时以凸模为计算基准。
根据凸模尺寸计算公式
式中d——拉深内形尺寸;
△——拉深件公差。
查得拉深件公差为+0.52。
=
=
mm
所以拉深凸模的工作尺寸为
mm。
3.8拉深凹模的工作尺寸(查参考文献[1]式4-32;查参考文献[3]表4-17)
根据凹模尺寸计算公式
式中d——拉深内形尺寸;
Z——单面拉深间隙;
△——拉深件公差。
查得拉深件公差为+0.52。
=
=
mm
所以拉深凹模的工作尺寸为
mm。
3.9压边装置确定(查参考文献[1]表4-2)
查得:
>2.0
并求
实际等于0.5小于0.6所以需要采用压边装置。
3.10压边力(查参考文献[1]式4-18,表4-3)
根据压边力计算公式
式中A——初始有效压边面积;
——单位压边力。
查得单位压边力为3.0~4.5。
=2993.545215N
所以拉深件拉深是所需压边力为2993.545215N。
3.11冲裁力(查参考文献[1]式2-13)
根据冲裁力计算公式
式中K——定值系数;
ι——冲裁轮廓的总长度(mm);
t——板料厚度(mm);
τ——材料抗拉强度(Mpa)。
F
=122936.6956N
所以冲裁部分冲裁力为122936.6956N。
3.12冲裁凹模的工作尺寸(查参考文献[1]式2-32;参考文献[3]表4-17)
根据凹模刃口尺寸计算公式
式中
——落料凹模刃口设计尺寸(mm);
——落料件最大极限尺寸(mm);
——凹模尺寸上偏差,下偏差为零(mm);
X——磨损补偿系数,工件精度在IT10以上、IT11至IT13、IT14以下,x分别为1、0.75、0.5。
外形尺寸为自由公差按IT14级公差处理,查得公差为-0.74。
mm
所以冲裁凹模的工作尺寸为
mm。
3.13冲裁凸模的工作尺寸(查参考文献[1]表1-3,式2-33;文献[2]表4-17)
根据凸模刃口尺寸计算公式
式中
——落料凸模刃口设计尺寸(mm);
——凸模尺寸下偏差,上偏差为零(mm)。
查得冲裁间隙为Zmin=0.160Zmax=0.200。
外形尺寸为自由公差按IT14级公差处理,查得公差为-0.74。
mm
所以冲裁凸模的工作尺寸为
mm。
3.14相关计算
3.14.1排样设计(查参考文献[1]表2-10)
查得最小工艺搭边值a=1.2
=1.5;
为使定位但方便所以我们将a选区为5mm。
最终排样图如图3-1所示:
图3-1排样图
3.14.2压力机的公称压力(查参考文献[1]式4-23)
根据公称压力计算公式
F=25645+2993
=28638N
由于拉深公称压力小于冲裁力122936N,考虑冲裁是必须工序,所以压力机的公称压力选取冲裁力,公称压力为122936N即压力机公称压力不小于12KN。
第4章模具主要零件的设计
4.1冲裁凹模的结构设计(查参考文献[1]表2-18;参考文献[2]表5-4)
根据[3.12]已计算的凹模刃口尺寸和条料宽度查得凹模周界的L最小为115.38mm,所以根据这一点选择最接近的凹模板大小L×B为125×100。
由于冲裁件是圆形,所以压力中心是在模板的中心,并且考虑到冲裁后需要马上进行拉深的工序,而且拉深时需要压边圈,所以刃口和落料孔设计为直通台阶式。
且根据已设计好的排样图,得到最终设计结果如图4-1所示:
图4-1冲裁凹模
4.2压边圈尺寸计算(查参考文献[1]P191)
4.2