煤气吹脱解析法处理一百万吨焦化厂剩余氨水工艺设计.docx
《煤气吹脱解析法处理一百万吨焦化厂剩余氨水工艺设计.docx》由会员分享,可在线阅读,更多相关《煤气吹脱解析法处理一百万吨焦化厂剩余氨水工艺设计.docx(48页珍藏版)》请在冰豆网上搜索。
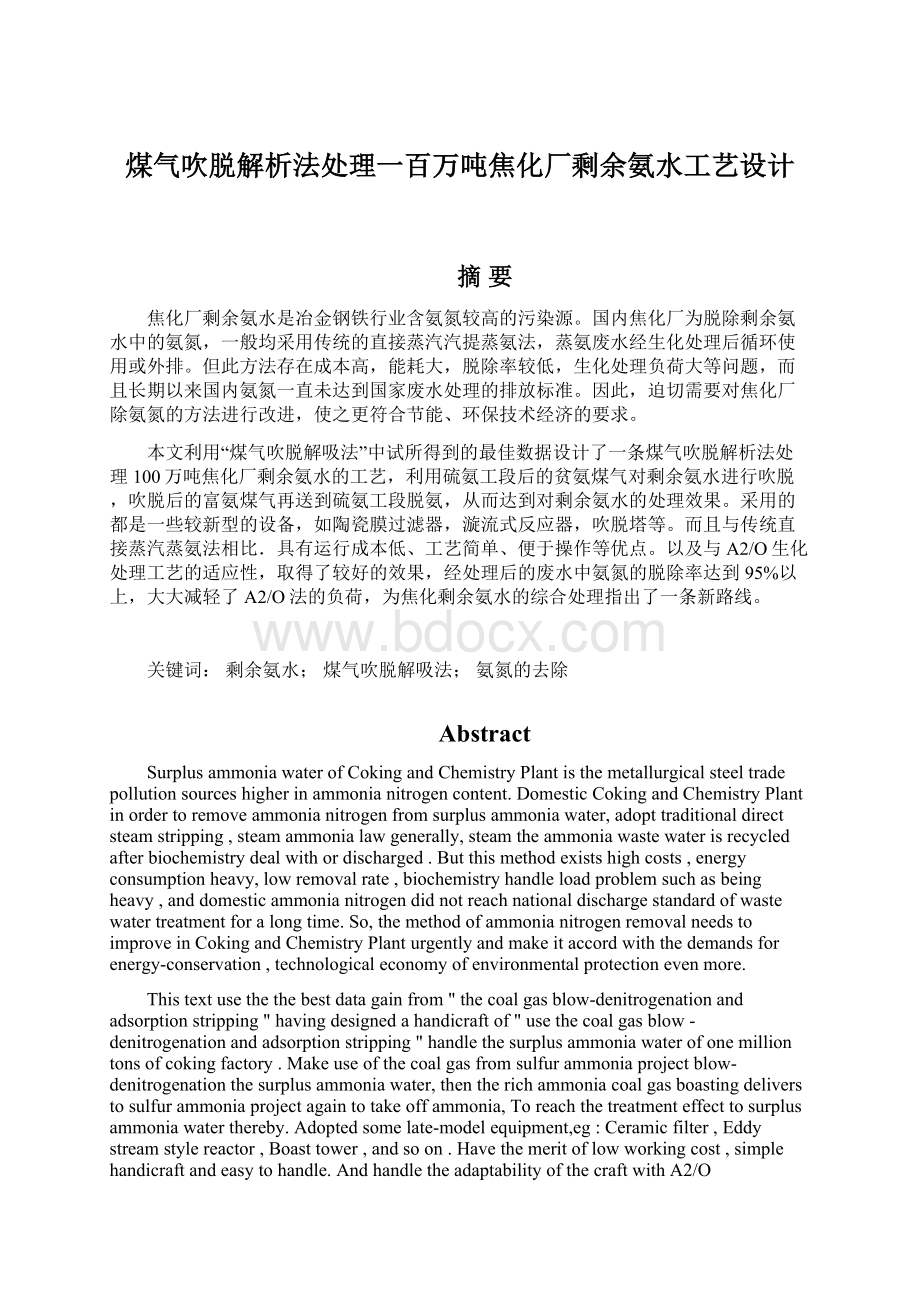
煤气吹脱解析法处理一百万吨焦化厂剩余氨水工艺设计
摘要
焦化厂剩余氨水是冶金钢铁行业含氨氮较高的污染源。
国内焦化厂为脱除剩余氨水中的氨氮,一般均采用传统的直接蒸汽汽提蒸氨法,蒸氨废水经生化处理后循环使用或外排。
但此方法存在成本高,能耗大,脱除率较低,生化处理负荷大等问题,而且长期以来国内氨氮一直未达到国家废水处理的排放标准。
因此,迫切需要对焦化厂除氨氮的方法进行改进,使之更符合节能、环保技术经济的要求。
本文利用“煤气吹脱解吸法”中试所得到的最佳数据设计了一条煤气吹脱解析法处理100万吨焦化厂剩余氨水的工艺,利用硫氨工段后的贫氨煤气对剩余氨水进行吹脱,吹脱后的富氨煤气再送到硫氨工段脱氨,从而达到对剩余氨水的处理效果。
采用的都是一些较新型的设备,如陶瓷膜过滤器,漩流式反应器,吹脱塔等。
而且与传统直接蒸汽蒸氨法相比.具有运行成本低、工艺简单、便于操作等优点。
以及与A2/O生化处理工艺的适应性,取得了较好的效果,经处理后的废水中氨氮的脱除率达到95%以上,大大减轻了A2/O法的负荷,为焦化剩余氨水的综合处理指出了一条新路线。
关键词:
剩余氨水;煤气吹脱解吸法;氨氮的去除
Abstract
SurplusammoniawaterofCokingandChemistryPlantisthemetallurgicalsteeltradepollutionsourceshigherinammonianitrogencontent.DomesticCokingandChemistryPlantinordertoremoveammonianitrogenfromsurplusammoniawater,adopttraditionaldirectsteamstripping,steamammonialawgenerally,steamtheammoniawastewaterisrecycledafterbiochemistrydealwithordischarged.Butthismethodexistshighcosts,energyconsumptionheavy,lowremovalrate,biochemistryhandleloadproblemsuchasbeingheavy,anddomesticammonianitrogendidnotreachnationaldischargestandardofwastewatertreatmentforalongtime.So,themethodofammonianitrogenremovalneedstoimproveinCokingandChemistryPlanturgentlyandmakeitaccordwiththedemandsforenergy-conservation,technologicaleconomyofenvironmentalprotectionevenmore.
Thistextusethethebestdatagainfrom"thecoalgasblow-denitrogenationandadsorptionstripping"havingdesignedahandicraftof"usethecoalgasblow-denitrogenationandadsorptionstripping"handlethesurplusammoniawaterofonemilliontonsofcokingfactory.Makeuseofthecoalgasfromsulfurammoniaprojectblow-denitrogenationthesurplusammoniawater,thentherichammoniacoalgasboastingdeliverstosulfurammoniaprojectagaintotakeoffammonia,Toreachthetreatmenteffecttosurplusammoniawaterthereby.Adoptedsomelate-modelequipment,eg:
Ceramicfilter,Eddystreamstylereactor,Boasttower,andsoon.Havethemeritoflowworkingcost,simplehandicraftandeasytohandle.AndhandletheadaptabilityofthecraftwithA2/Obiochemistry,makebetterresult.Theremovalrateoftheammonianitrogenismorethan95percentinthewastewaterafteritisdealtwiththat"thecoalgaslow-denitrogenationandadsorptionstripping",greatloadoflighteningA2/Olaw,tofoundanewrouteforthecomprehensivetreatmentofsurplusammoniawaterofcoking.
Keyword:
surplusammoniawater;coalgasblow-denitrogenationandadsorptionstripping;ammonianitrogenremoval
前言
最近几年,科技日新月异,经济迅速发展,特别是我国,基础建设规模日益庞大,钢铁用量则空前增长,用于炼钢炼铁原料的焦碳自然用量剧增。
随之而来的是一系列环境问题,如温室效应、光化学烟雾、江河湖水污染变臭、噪音污染等问题正威胁着人类和社会的健康发展。
因此,优化工厂生产工艺流程,减少污染物排放量,积极治理环境污染已经是刻不容缓。
在这些环境污染中,水污染是一个重要的因素。
而含氮废水的量一般较大,而且含氮废水中的氮容易造成水体富营养化,导致水质恶化,大量水生生物死亡。
焦化废水的来源主要有3部分:
煤干馏煤气冷却过程中产生的剩余氨水;煤气净化过程中产生的煤气终冷水及粗苯分离水;焦油、粗苯等精制过程中产生的污水。
其中剩余氨水的污染量占总污染量的一半以上,它既是焦化污水的主要来源,同时又是冶金钢铁行业含氨氮较高的污染源。
剩余氨水中主要含有煤焦油、酚、氰化物、挥发氨和固定氨、硫化氢以及少量的含锗化合物,在排放到自然界之前,这些物质都必须进行回收处理,以免造成环境污染。
焦化厂废水中的氨和铵盐,对金属设备和管道有腐蚀作用,并影响生物脱酚的正常操作,直接排放又严重污染环境。
如何寻找一条脱除氨氮,并配合切实可行的生化方法,是各企业急于探求的目标。
1总论
1.1概述
国内焦化厂中,为脱除剩余氨水中的氨,一般都采用传统的直接蒸汽汽提法蒸氨,蒸氨废水经生化处理后循环使用或外排。
但是此法存在蒸汽耗量大,设备腐蚀严重和操作费用高等问题。
许多焦化厂也都建有蒸氨装置,但由于存在蒸汽不足,设备腐蚀和堵塞等问题而长期未开工。
剩余氨水不经任何处理,直接送生化装置处理后外排。
致使生化装置因进水的污染物含量高,而难以达到理想的处理效果,造成外排水多项指标长年超标排放。
焦化废水的来源主要有3部分:
煤干馏煤气冷却过程中产生的剩余氨水;煤气净化过程中产生的煤气终冷水及粗苯分离水;焦油、粗苯等精制过程中产生的污水。
其中剩余氨水的污染量占总污染量的一半以上,它既是焦化污水的主要来源,同时又是冶金钢铁行业含氨氮较高的污染源。
废水中氨氮的处理技术一直是各国学者研究的热门课题。
脱氨方法有很多,目前在工业上应用的主要有蒸氨法、吹脱法、生物脱氮法、折点加氯法、离子交换法、烟道气治理法等等。
生物脱氮法适用于处理含有机物的低氨氮浓度废水,该法技术可靠,处理效果好,主要应用于化工废水和生活污水的处理。
对于高浓度无机氨氮废水,如化肥废水、催化剂废水,目前工业应用较多采用吹脱法。
国内焦化厂为脱除剩余氨水中的氨氮,一般均采用蒸氨法。
考虑到本设计在技术和经济上的合理性,有必要进行设计之前的技术资料准备工作,以蒸氨工艺为参考,考虑预处理后的生化处理的联运,从工艺,设备及相关资料普查入手,经计算整理,设计一条利用煤气吹脱解析法处理100万吨焦化厂剩余氨水的工艺道路。
由中试“煤气吹脱解析法处理剩余氨水”的试验结果可知,吹脱法处理的剩余氨水明显减轻了生化处理装置的负担,生化出水的水质也得到了明显的改善,外排水水质全部达标。
而且大大降低了蒸汽耗量,降低工艺生产费用。
1.2剩余氨水的来源,特点及质量组成[1]
在焦炉煤气初冷过程中形成了大量氨水,其中大部分用做循环氨水喷洒冷却集气管的煤气,多余部分称剩余氨水。
剩余氨水组成与焦炉操作制度、煤气初冷方式、初冷后煤气温度和初冷冷凝液的分离方法有关。
其一般组成范围见表1.1。
表1.1剩余氨水组成表[1]
初冷工艺
组成,克/升
初冷后煤气温度℃
全氨
挥发氨
CO2
H2S
HCN
酚
吡啶
煤气的初冷
初冷冷凝液单独分离
30~40
7~9
6~8
2~4
1~3
0.1~0.2
1~2
0.2~0.4
初冷冷凝液与集气管循环氨水混合分离
硫铵流程
30~40
2~5
1~2
1~2
0.2~2
0.04~0.14
氨水流程
20~25
2~3
1.5~3
0.5~2.5
0.1~0.2
煤气直接初冷
初冷循环氨水与洗氨氨水混合分离
25~30
4~6
0.4~1.4
0.1~0.24
1.3车间规模组成及主要装备水平
本工艺适用于硫铵车间,用来取代蒸氨工艺,装备水平为100万吨焦化厂硫铵工段装备水平。
1.4节能技术与环保
煤气吹脱解析法脱氨氮比蒸氨法脱氨成本要低,蒸氨法的直接气耗量为160~200公斤/米3原料氨水,按市场平均价格算,每吨蒸气的价格约为90元人民币,也就是说每处理一吨氨水,光消耗蒸汽就要花费18元。
按60万吨焦化厂计,仅耗蒸汽约300万元。
采用煤气吹脱法,通入的是焦化厂本身就产生的焦炉煤气,利用焦炉煤气本身的热量和余压对剩余氨水进行吹脱。
节约了能源,保护了环境,降低了成本。
另外,蒸氨法工艺流程较复杂,设备较大。
而煤气吹脱解吸法工艺流程简单,与整个水处理工艺能联运循环。
总之,煤气吹脱法比蒸氨法成本明显要低,工艺要更为合理优化。
1.5主要技术方案综述
1.5.1主要技术的叙述[8]
当废水中含有可挥发性物质(如硫化氢、氨气等)时,可以用向废水中通入蒸汽的方法将之提取出来,这就是“吹脱”,带出来的挥发性物质可以通过适当的方法加以回收利用。
氨氮的去除率是指通过处理,从废水中除掉的氨氮的量占原废水中氨氮总量的百分比。
废水中的氨氮多数是以铵离子(NH4+)和游离氨(NH3)的状态存在,并且它们之间存在如下的平衡关系:
显然,游离氨的浓度与废水的pH值有关系,pH值越高,游离氨的浓度越高。
常温时,当PH值为7左右时氨氮大多数以铵离子状态存在,而PH为11左右时,游离氨大致占90%。
当水的PH值升高,呈游离状态的氨易于逸出。
若加以搅拌,曝气等物理作用更可促使氨从水中溢出。
在实际工程中,大多采用吹脱塔。
吹脱塔的构造一般采用气液接触装置,通常以石灰作为碱剂处理,经石灰调节PH值后的水从塔的上部淋撒到填料上而形成水滴,而下部的煤气鼓泡而出与水逆流接触,完成传质过程,使氨由液相转变为气相,随煤气而出,完成吹脱过程。
吹脱是一种对流传质过程,根据有效膜理论,其推动力是溶质组分的液相浓度与气相浓度差,根据资料,常温下氨水系统的平衡方程式为:
Y=1.2X(1.1)式中:
Y――氨在空气中的摩尔分率;
X――氨在水中的摩尔分率
由上式可以计算出,当氨氮去除率达到95%时的最小气液比为0.79,即气液比为980:
1,由于氨吹脱属气相阻力控制,因此通常情况其实际生产过程的气液比可能还要大。
1.5.2吹脱工艺流程,设备及其特点
本工艺流程大致为:
于剩余氨水中投入碳酸钠,调节耗PH值后流经漩流式反应器,经反应后进入吹脱塔与煤气进行逆流接触,脱氨后用鼓风机抽至硫氨工段。
本工艺流程中煤气的走向大体上可以说是一个循环的过程,即利用硫氨工段后的贫氨煤气对剩余氨水进行吹脱,吹脱后的富氨煤气再送到硫氨工段脱氨,从而达到对剩余氨水的处理效果。
采用的都是一些较新型的设备,如陶瓷膜过滤器,漩流式反应器,吹脱塔等。
而且与传统直接蒸汽蒸氨法相比.具有运行成本低、工艺简单、便于操作等优点。
吹脱塔的形式有填料塔,筛板塔等。
废水自塔顶喷下,煤气自塔底通入,在塔内废水与煤气进行逆流接触,废水吹脱后从塔底经水封管排出,自塔顶排出的气体进入到下一工段。
单位时间吹脱的气体量,正比于气液两相的浓度差(或分压差)和两相的接触面积。
即G=K·A·△C(1.2)式中:
G――为单位时间内由水中吹脱的气体量;
A――为气液两相的接触面积;
K――为吹脱系数
1.6设计的依据
1.6.1数据依据[1]
本设计题目为煤气吹脱法处理100万吨焦化厂剩余氨水的工艺设计。
由文献[1]可知,标准状态下煤气处理量Q如下。
Q=W×1.07Mg(1.3)式中:
W――装炉干煤量,吨/时;
1.07――焦炉紧张操作系数;
Mg――煤气发生量,标米3/吨干煤
煤气发生量系指1吨干装炉煤产生的标准状况下的干煤气体积。
通常在洗苯塔后测出,故实际上不包括焦炉损失的煤气量。
煤气发生量波动于285~420标米3/吨干煤,约相当于装炉干煤重量的15~19%。
它随煤料的挥发分而变。
本设计中Mg取340标米3/吨干煤。
则可得W=100÷0.75=133万吨/年=0.36万吨/天=151吨/时.
Q=151×340×104
=5.1×108标米3/时
而剩余氨水量W为10~11%的干煤量。
W=133×0.1
=13.3万吨/年
1.6.2试验依据
设计之前我们在武钢燃气厂气柜车间进行了煤气吹脱解析法处理剩余氨水的中试试验,由正交试验取得的最佳试验数据,以及出于对工业环保,经济等诸多因数的考虑选取设计依据为下表1.2。
表1.2试验所得最佳数据
气液比
吹脱时间
PH值
温度
600:
1
120min
10.2
80℃
1.7设计存在的主要问题(或遗留问题)及处理
由于设计者能力和设计时间的有限,至使设计过程中出现的一些问题,具体如下:
1、由于设计的主要依据为“煤气吹托解析法”的中试试验。
中试所用的煤气吹托盘设计比较粗糙,所用的孔径,开孔大小等,可能还没有达到最佳设计,应此试验所得的最佳气液比可能还会减小。
也就是说,凡是和煤气有关的设计部分,设计的大小可能都有偏大。
2、反应器的保温采用的是夹套加热,应此,由设计参考资料塔径不能过大,导致吹托塔体过高,从而吹托煤气的动力要求也较大。
以后的研究可以尝试选用其他的保温方法,增大塔径,降低塔高,减小煤气动力要求。
3、经过吹脱的煤气,本来温度可以不用要求到45℃,因为如果直接送往硫铵饱和器的话,温度降到60℃就足够了,但是如果这样的话,对于整个硫胺工段又涉及到了一个水平衡的问题,而使整个硫铵车间的反应条件都要依其作出一定的调整。
整个工程调节过大,所以把吹脱后的煤气送往鼓风机前。
以后的设计可以考虑在本设计的基础上向这个方向设计。
3、煤气吹脱解析法处理剩余氨水的中试试验中,为了和后面的A2/O相匹配,我们选用的助脱除剂为碳酸钠,但是试验中我们发现如果选用碳酸钠,投碱量会比较大,于经济和简便方面都不是很合适,因此,本设计中选用氢氧化钠。
4、中试装置的冷凝部分,我们设计的是蛇管形式,但是实际的试验中发现蛇管固然可以达到一定的冷凝效果,但是应此所需要的塔体部分高度过高,因此在本设计中,设计的是列管式,许多部分都可以按照标准件来设计,冷凝塔体部分高度减少了不少。
5、中试试验中发现煤气带雾现象比较严重,因此在设计中,加入了抽雾层,确保吹脱效果。
6、本设计开始时冷凝部分使用的冷凝水是16℃的冷却水,换热后温度达到35℃。
后来注意到采用16℃的冷却水,消耗比较大,因此设计过程中又改为32℃的冷却水。
但是经计算当采用32℃冷却水时所需要的还热面积又会增大,而且煤气吹托的动力要求也会增大,所以最终确定冷凝水为16℃的冷却水。
考虑到处理后的剩余氨水到生化前也需要冷却,但要求并不高,因此设计用这里的35℃的出水来冷却处理后的剩余氨水。
2吹脱法处理剩余氨水工艺论述
2.1目前国内外吹脱法的现状[8]
2.1.1吹脱技术净化石油污染地下水
在石油污染水中,大多数污染水为石油裂解产物或带有各种官能团的烃类衍生物,和NH4+-N等污染物质,采用吹脱技术,可以较容易实现以下效果:
(1)有效降低出水中油含量,随着气水比的增加,吹脱出水中油含量逐渐降低,可去除石油类有机物中绝大部分挥发性组分。
(2)吹脱时,非离子氨(NH3)从液相进入气相,从而使水中NH4+-N浓度降低。
(3)吹脱对高锰酸钾指数的去除率较低,说明在吹脱掉的石油类污染物中,绝大部分是不可被高锰酸钾氧化的有机物质。
吹脱还能增加水中的溶解氧,为后续的生物处理提供充足的溶解氧。
2.1.2吹脱法处理中低浓度氨氮废水
废水中的氨氮大多以氨离子(NH4+)和游离氨(NH3)的形式存在。
当水的pH值升高时,游离态氨易于逸出。
采用搅拌、曝气等方法可加快氨的逸出。
采用吹脱塔和气液接触装置,经石灰调节pH值后的水从塔的上部淋洒到填料上而形成水滴,顺着填料的间隙次第落下,与由风机从塔底向上或水平方向吹送的空气逆流接触,完成传质过程;氨由液相转为气相,随空气排放,完成吹脱过程。
2.1.3氧化吹脱-离子交换处理2-萘酚生产废水
2-萘酚生产废水是高盐、高COD、高色的化工废水,传统物化与生化法无法处理,可采用氧化吹脱-离子交换组合工艺方法,首先氧化吹脱废水中的亚硫酸盐,然后分离富集废水中萘磺酸盐并加以回收利用,处理后的废水可回用为洗涤液和回收硫酸钠。
显著降低处理费用,力求做到废水资源化,是治理此类废水的关键。
工艺流程如图2.1。
废水氧化吹脱结果表明,在弱酸性条件下,亚硫酸以氧化为主,当PH小于3时,SO32一转化成SO2而被吹脱去除,此时COD氧化去除速率明显高于弱酸PH条件下的氧化速率。
但在经过5h氧化吹脱反应后,弱酸与酸性PH条件下的氧化吹脱速率基本重合,废水COD去除率达到最大值。
因此该处理212艺方案适宜对高含盐量,尤其对采用磺化反应而产生的高色度、高含盐量、高COD值的染料中间体化工废水的治理。
图2.1氧化吹脱-离子交换处理2-萘酚生产废水工艺流程
2.1.4超声波吹脱技术处理高浓度氨氮废水
超声波吹脱技术可以克服一般方法中吹脱效果低,NH4+-N的去除率只有40%~50%,不能达标排放的缺点。
其原理是利用超声波辐射被处理废水,使水分子承受交替压缩和扩张,产生空化气泡,加强NH3的挥发和传质效果,使其更容易由液相转为气相。
因产生超声波的动力是压缩空气,空气进入废水中能及时将NH3带出水面,以保持气液二相中NH3的分压差,从而获得吹脱NH3的高效率。
工艺流程如图2.2。
图2.2超声波吹脱法处理高浓度氨氮废水工艺流程
本方法大大提高吹脱效率,降低供气量,节省动力消耗,缩短了吹脱时间,从而缩小了吹脱塔的体积,降低投资;吹脱效率比传统吹脱技术的脱氮率高17%~164%;其对废水中的COD也有明显的去除效果;吹脱后的尾气可以通过盐酸溶液吸收,制成高浓度的NH4Cl溶液,作为原料返回生产系统。
2.1.5超重力法吹脱氨氮废水技术
利用旋转填料床产生强大离心力场一超重力场,可使气液流速与填料的比表面积提高而不产生液泛,氨氮废水在高分散、高湍动、强混合以及界面急速更新的情况下与气体以极大的相对速度在弯曲孔道中逆向接触,强化了传质过程。
这种特殊强化传质作用,大幅度提高吹脱能力和吹脱效率,有效地实现氨氮废水的吹脱,在PH值为10.8,气液比1200m3/m3的操作条件下,氨的单程吹脱率达到95%。
该技术特点:
(a)传质系数大幅度提高,在气液比为传统吹脱法l/4左右时即可达到同样的吹脱效果,降低了运行费用,吹脱后空气中氨的浓度高,易于回收利用。
(b)气液在床层中的流速加快,湍流加剧,污垢及好氧生物和藻类不易沉积在填料层中,保证设备的长期正常运行。
(c)由于传质过程的强化,使得设备体积缩小,重量减轻,设备及基建费用减少。
(d)过程放大容易,开车、停车时间短,在数分钟内就能达到稳定运行状态,更适合间断氨氮废水排放的处理。
2.1.6吹脱法脱除炼油厂含硫化氢废水
炼油厂从冷凝器排出的废水中,含有大量石油及硫化氢,具有很强的腐蚀性,其中硫化氢的存在形式因pH值不同而异,处理时一般先酸化至DH<5以后,再用吹脱法除去。
工艺流程图如图2.3。
图2.3吹脱法脱除炼油厂含硫化氢废水工艺流程
吹脱技术还可脱除其它一些气体和物质。
1)由于二氧化碳不会引起大气污染,故可在吹脱池内进行。
2)在选矿废水中,氰化物主要以氰化钠形式存在,它是一种强碱弱酸盐,在水溶液中易水解为氰化氢,加酸可促进水解反应的进行。
生成的氰化钠用吹脱法脱除后,再用NaOH碱液吸收,可回收氰化钠,重新用于生产。
如采用真空闭路循环系统,可使输送氰化氢气体的管路处于负压下,可防止漏气中毒,还可避免新鲜空气中所含CO2,对碱液的消耗。
3)利用空气吹脱的方法对水中的三氯乙烯、氯苯、l,3一二氯苯都有好的去除效果,去除率为30%~85%,去除效果随温度的升高而增加。
2.2目前国内外剩余氨水的生化处理方法[9]
2.2.1传统工艺脱氮法
该工艺以氨化、硝化、反硝化三项反应为基础,流程如图2.4。
图2.4 传统工艺脱氮流程
从图上可看出,I、Ⅱ、Ⅲ分别完成氨化、硝化和反硝化作用,加碱是为了保持硝化所需的偏碱环境,加甲醉是为了提供反硝化所需的碳源。
此系统有下列优点:
氨化、硝化、反硝化分开进行,氧化速度高,污泥负荷率可达1.4mgN/gMLSS·h;不同性质污泥在不同沉淀他分离和回流,运行方便,灵活性大,效果较好。
缺点:
处理设备多,造价高;由于投加甲酵而带来的BOD5(生化需氧量)需在系统后设曝气池和沉淀池除去。
在实践中,也常采用单级脱氯系统,此系统仅有一个沉淀池,流程简单,设备少,稳定性和效果可能有不足之处,但由于该系统可达到脱氯处理要求,且经济实用,管理方便,故常采用。
流程如图2.5。