钢结构油漆涂装施工工艺.docx
《钢结构油漆涂装施工工艺.docx》由会员分享,可在线阅读,更多相关《钢结构油漆涂装施工工艺.docx(9页珍藏版)》请在冰豆网上搜索。
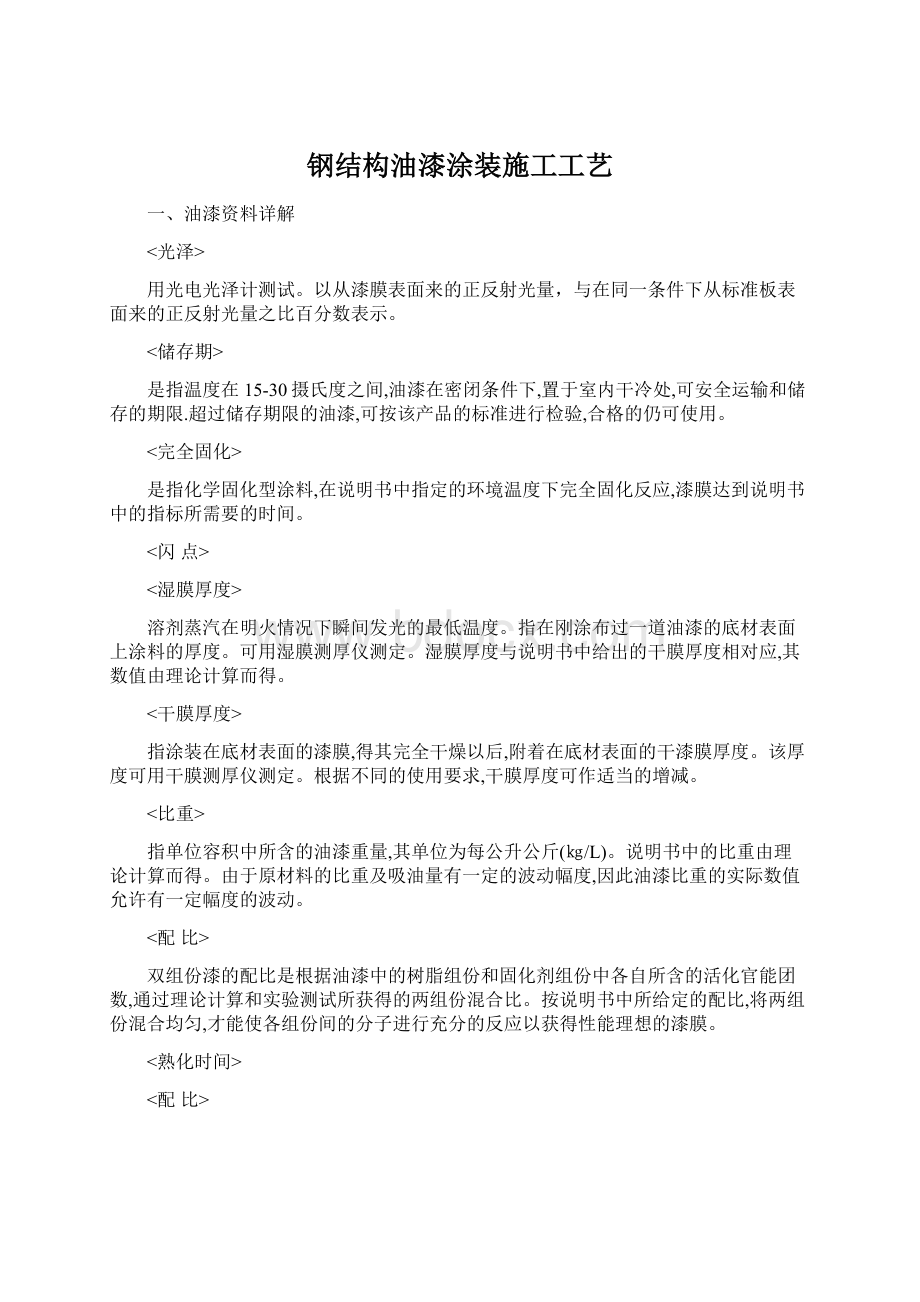
钢结构油漆涂装施工工艺
一、油漆资料详解
<光泽>
用光电光泽计测试。
以从漆膜表面来的正反射光量,与在同一条件下从标准板表面来的正反射光量之比百分数表示。
<储存期>
是指温度在15-30摄氏度之间,油漆在密闭条件下,置于室内干冷处,可安全运输和储存的期限.超过储存期限的油漆,可按该产品的标准进行检验,合格的仍可使用。
<完全固化>
是指化学固化型涂料,在说明书中指定的环境温度下完全固化反应,漆膜达到说明书中的指标所需要的时间。
<闪点>
<湿膜厚度>
溶剂蒸汽在明火情况下瞬间发光的最低温度。
指在刚涂布过一道油漆的底材表面上涂料的厚度。
可用湿膜测厚仪测定。
湿膜厚度与说明书中给出的干膜厚度相对应,其数值由理论计算而得。
<干膜厚度>
指涂装在底材表面的漆膜,得其完全干燥以后,附着在底材表面的干漆膜厚度。
该厚度可用干膜测厚仪测定。
根据不同的使用要求,干膜厚度可作适当的增减。
<比重>
指单位容积中所含的油漆重量,其单位为每公升公斤(㎏/L)。
说明书中的比重由理论计算而得。
由于原材料的比重及吸油量有一定的波动幅度,因此油漆比重的实际数值允许有一定幅度的波动。
<配比>
双组份漆的配比是根据油漆中的树脂组份和固化剂组份中各自所含的活化官能团数,通过理论计算和实验测试所获得的两组份混合比。
按说明书中所给定的配比,将两组份混合均匀,才能使各组份间的分子进行充分的反应以获得性能理想的漆膜。
<熟化时间>
<配比>
双组份漆的配比是根据油漆中的树脂组份和固化剂组份中各自所含的活化官能团数,通过理计算和实验测试所获得的两组份混合比。
按说明书中所给定的配比,将两组份混合均匀,才能使各组份间的分子进行充分的反应以获得性能理想的漆膜。
<熟化时间>
指油漆的树脂组份和固化剂组份混合均匀后,在使用前所须放置的一段时间。
使油漆里树脂和固化剂在这段时间里进行一定程度的化学反应,以利涂装并形成较好的漆膜。
<适用期>
是指多组份的化学固化型涂料,相互混合均匀后,到不再适合于施工的最长时间。
超过这一时间后,即使加入稀释剂也无法使用。
<涂装间隔>
涂装间隔即为两道涂层在涂装的过程中,对间隔时间的要求。
不同类型的涂料,其间隔要求也不同。
施工时,应按各自的要求进行施工,不能小于或超出各自规定的间隔时间,否则会影响漆膜层与层之间的结合力而造成漆膜剥离等弊病。
各别超出最长涂装间隔期的钢材表面必须仔细打磨,才能进行后道涂装。
<理论用量>
指面积在一平方米光洁、平整的理想底材表面上制得其说明书中给出的漆膜厚度相同的干膜厚度时所需要的油漆用量。
该数值为理论计算值。
<实际用量>
与理论用量不同,实际用量要视漆膜的实际厚度、涂装时的损耗、涂装方法、被涂物面的粗糙度等不同的情况而定。
其数值差别较大,就一般情况而言,油漆的实际耗用量为理论用量的1.5-1.8倍。
较为详细的耗用量计算公式及估算方法如下:
计算公式:
P=(1+Ex)QS
实际耗用量为理论用量的1.5-1.8倍。
较为详细的耗用量计算公式及估算方法如下:
计算公式:
P=(1+Ex)QS
x的参数值如下:
x1:
由环境风速确定。
风速在3m/s时,约为0.2,当风速大于3m/s时,则不宜施工。
X2:
由被涂物面的形状确定,型钢一般为0.2,钢管则视直径不同而异,直径在2.5-13cm范围内,约为0.5-1.0。
X3:
由涂料种类确定,一般单组份涂料为0.07,双组份涂料为0.15。
X4:
由漆膜分布要求而定,分布要求为两个80%时,约为0.1,分布要求为两个90%时,约为0.15。
X5:
由局部修补而定,一般单组份涂料为0.1,双组份涂料为0.15。
X6:
由表面粗糙度而定,如表面粗糙度为70-100um时,薄涂层的x为0.2,厚涂层的x为0.1。
*以上为高压无气喷涂时与涂料损耗的有关因素。
因此,通常在平整表面上施工,Ex约为0.6-0.8,在复杂表面上施工,Ex为0.8-1.0;手工涂刷的损耗则小得多,约为无气喷涂的一半左右。
环氧富锌底漆、无机锌底漆及环氧铁红车间底漆,因规定的漆膜厚度分别为15-20um和20-25um,漆膜很薄,而比重又大于一般油漆,其损耗系数Ex约在2.0左右。
因此在计算实际用量时,不能以理论用量进行计算,必须按以上公式计算油漆的
实际用量。
<稀释剂>
为0.8-1.0;手工涂刷的损耗则小得多,约为无气喷涂的一半左右。
环氧富锌底漆、无机锌底漆及环氧铁红车间底漆,因规定的漆膜厚度分别为15-20um和20-25um,漆膜很薄,而比重又大于一般油漆,其损耗系数Ex约在2.0左右。
因此在计算实际用量时,不能以理论用量进行计算,必须按以上公式计算油漆的实际用量。
<稀释剂>
是用来调节油漆粘度,以符合不同场合施工之需。
但若使用不当,漆膜易产生弊病,导致油漆早期失效,甚至发生火灾等事故,为正确使用稀释剂,请仔细阅读施工指南及参考表1-1,并注意防火安全问题。
涂装前钢铁表面处理
为了防止钢铁的腐蚀并由此造成的经济损失,采用涂料保护是当今防止钢铁腐蚀的主要手段之一。
防腐蚀涂层的有效寿命与涂装之前钢铁表面的除锈质量、漆膜厚度、油漆品种、涂装的工艺条件等因素有关。
表2-1列出上述各种因素对漆膜寿命影响的分析结果。
由表可见,涂装前钢铁表面的除锈质量是确保漆膜防腐蚀效果和保护寿命的关键因素。
因此钢铁表面处理的质量控制是防腐涂层的最关键环节。
防腐蚀效果和保护寿命的关键因素。
因此钢铁表面处理的质量控制是防腐涂层的最关键环节。
称除锈。
它不仅是指除去钢铁表面的污垢、油脂、铁锈、氧化皮、焊渣或已失效的旧漆膜的清除程度,即清洁度;还包括除锈后钢铁表面所形成合适的“粗糙度”。
钢铁表面的除锈可按不同的方法分类。
按除锈顺序可分为一次除锈和二次除锈;按工艺阶段可分为车间原材料预处理、分段除锈、整体除锈;按除锈方式可分为喷射除锈、动力工具除锈、手工敲铲除锈和酸洗等方法。
预处理
钢铁表面的预处理,就是在涂装车间底漆或底漆之前,经钢材预处理流水线,以抛丸除锈法清除钢材表面的氧化皮、锈蚀物以及由外部因素造成的处理后的表面灰尘等。
其次,表面预处理还包括在涂装防腐涂料或装饰涂料之前,将已涂过底漆或车间底漆的钢铁表面的浮锈和焊渣、污垢及灰尘等清除干净。
钢丝刷清理
钢丝刷除锈清理时,一般用风动或电动旋转钢丝刷。
这种方法不适用于清除氧化皮等,但适用于浮锈的预处理,处理后的表面若有以下情况,即:
表面的锈蚀物没有完全清除;处理后的表面太光滑,以及表面尚有油脂、污垢等,都不利于涂装。
若在这种情况下进行涂装,会降低漆膜的附着力,并影响整个油漆涂装体系的效果。
砂轮除锈是利用风动或电动旋转的弹性砂轮片打磨钢铁表面来进行除锈的方法,适用局部除锈和焊缝的处理。
这是一种较为有效的除锈方法,可以获得比钢丝刷除锈更为满意的效果。
喷射除锈
喷射除锈方法是将高速运动的磨料喷射到钢铁表面,使其强烈地撞击和摩擦钢铁表面,从而达到除锈目的的一种除锈工艺方法。
喷射除锈是一种除锈最彻底、效率最高且能实现自动流水线作业的先进除锈方法。
喷射除锈常用的有抛丸、喷丸、喷砂和真空喷射等方法。
*喷射磨料应符合密度大、韧性好、颗粒均匀、不易破碎、散释粉尘少、喷射后的表面不应有残留物及表面粉尘易清洁的要求,因此喷射磨料通常采用颗粒直径为0.5-1.5mm的铸铁丸、铸钢丸、棱角钢砂、钢丝段和铜矿渣等,或将其中的两种磨料以一定的比例参合成混合磨料。
*以及控制喷射的能量和角度,可以得到理想的,符合要求的清洁度(即除锈质量等级),和涂装油漆所需要的30-75um的粗糙度。
*喷射除锈处理后,表面粉尘必须全部清理干净。
被涂件的外部可用喷枪喷出经干燥处理的压缩空气,将粉尘吹干净。
内部则用真空吸尘器彻底除去所有的磨料和粉尘。
*喷射除锈会产生大量的粉尘飞扬,必须做好安全工作。
操作人员必须戴好通气面罩,并防止对周围环境的污染,最好设立喷砂车间,并进行一定的通风换气。
锈蚀等级
钢材表面的四个锈蚀等级分别以A.B.C.D表示,文字表述如下:
A.金属覆盖着氧化皮而几乎没有铁锈的钢材表面。
B.已发生锈蚀,并且部份氧化皮已经剥落的钢材表面。
C.氧化皮已因锈蚀而剥落或可以刮除,并且有少量点蚀的钢材。
D.氧化皮已因锈蚀而全面剥离,并且已普遍发生点蚀的钢材。
除锈等级
钢材表面的除锈等级,是以英文字母加阿拉伯数字表示的,
如Sa2.5。
前面的英文字母表示除锈方法,St和Sa分别表示手工
除锈及喷射除锈方法。
后面的阿拉伯数字表示除锈等级,即清除
氧化皮、铁锈和旧油漆等附着程度的等级。
Sa---表示喷射或抛丸除锈法
St---表示手动工具和动力工具除锈法。
Sa喷射或抛丸除锈等级又分为四个等级,文字表示如下:
等级分类钢材表面状态
Sa1表示轻度的喷射或抛丸除锈。
钢材表面应无可见的油脂及
污垢,且没有附着氧化皮、铁锈。
Sa2彻底的喷射或抛丸除锈。
钢材表面应无可见的油脂及污
垢,且附着的氧化皮、铁锈已基本清除。
Sa2.5彻底的喷射或抛丸除锈。
钢材表面应无可见的油脂及污
垢,且附着的氧化皮、铁锈已完全清除,无任何残留痕迹。
Sa3表示钢材表面洁净的喷射或抛丸除锈。
钢材表面应无可见
的油脂及污垢,且附着的氧化皮、铁锈已完全清除,显示均
匀金属光泽。
(*除锈等级可参照国家标准GB8923-88《钢材表面锈蚀等级和
除锈等级》彩色照片加以比较)
手动工具和动力工具除锈也应首先除去较厚的锈蚀层并清
除油脂及污垢,再清除浮灰和碎片。
其除锈等级也分St2和St3。
不同类型的涂料由于其基料的组成不同,被不同类型的涂料由于其基料的组成不同,被除
锈质量适应性涂物体所处的环境不同,以及对涂料保护性能和保护寿命的不同要求。
因此对钢铁表面的除锈质量有不同的要求和不同的适应性。
一般情况下,像醇酸、酚醛、油性和沥青、环氧、氯化橡胶等高性能涂料或重防腐涂料,则对钢铁表面处理的质量要求很高,对除锈质量有一定的适用关系,如表2-2所示,以供涂装要求参考。
二、涂装前准备工作
开桶首先将桶外的灰尘、杂物除尽以免混入漆桶内。
开通后若发现有结皮现象,则应将漆皮整块或分若干块取出,以免影响质量。
搅拌由于漆中各成份比重的差异,可能有沉淀出现。
所以在油漆使用前,须将桶内的油漆及沉淀物全部搅拌均匀后才可使用。
搅拌均匀后,按指定比例混合。
双组份涂料是由基料和固化剂组成的,通过化学反应来实现固化。
熟化
·对于双组份的涂料,油漆产品规定了熟化时间,甲、乙两组份混合均匀后,使漆内的树脂与固化剂完全化学反应,以保证施工和漆膜的性能。
稀释涂料在出厂时已将粘度调节到适宜于施工要求的粘度范围,但由于储存条件、施工方法、作业环境、气温变化的情况影响,在使用时需用稀释剂来调整粘度。
各种涂料使用的稀释剂及最大用量都有明确规定,使用时必须严格执行,否则会造成涂料的报废及性能下降的后果。
过滤涂料在使用前,需将涂料中可能产生的或混入的固体颗粒、漆皮杂质过滤去,以避免这些杂质堵塞喷嘴及影响施工进度和漆膜的性能、外观。
一般可使用80-120目的金属网或尼龙丝筛进行过滤。
涂装环境
钢材表面涂装前要注意钢材表面状况和大气环境,施工须在表面温度高于露点温度以上3摄氏度,相对温度在85%以下的条件中进行。
当钢材表面受雨水或冰雪的影响时,则不能进行涂装施工。
施工温度
*在平均气温低于
5摄氏度的低温条件下,环氧型、聚氨酯等化学固化型涂料的固化反应已经停止,因此不能施工,但可在设有升温装置的涂装车间内进行分段涂装。
*当平均气温高于35摄氏度的高温天气时,涂料中的溶剂挥发很快。
在无气喷涂时,涂料中的溶剂在喷嘴与被涂物面之间大量挥发而发生干喷现象,致使油漆凝结、流挂,从而影
响施工质量。
环境湿度
涂装施工的环境湿度一般控制在不大于80%方允许施工。
涂装施工方法
刷涂方法涂刷是以人工用刷子涂油漆的一种施工方法。
这种方法使用的最早也最简便。
该法优点是:
可涂各种形状的物体,工具简单,施工不受场地限制,省漆料和稀释剂,涂刷时由于刷子的机械作用,可增加漆膜的附着力。
所以主要用于油性漆和初期干燥较慢的涂料的涂装。
其缺点为:
劳动强度大,施工效率低,涂刷挥发性涂料时较困难。
滚涂方法
滚涂方法是用羊毛或合成纤维做成多孔吸附材料附在空心的圆筒上制成的滚子,进行涂料施工的一种方法。
该法施工用具简单,操作方便,施工效率比涂刷法高1-2倍,用漆料量与涂刷法基本相同。
其缺点是:
劳动强度大,施工效率比喷吐法低,且该法只适用于较宽的平面物体。
主要用于油性、合成树脂漆的涂装。
空气喷涂法
空气喷涂法是利用压缩空气(压力为0.3-0.5MPA)把气带到喷枪的喷嘴处,并吹成雾状,喷于物体表面,喷咀与物面距离保持30厘米左右。
该法的优点是:
漆膜均匀、光滑平整,施工效率比刷涂法高5-10倍。
其缺点:
漆料和稀释剂损耗大,漆雾飞散多,涂料的利用率一般只有75%;漆膜较薄,需喷涂多次才能达到一定厚度;喷涂时产生的漆雾,飞散在空气中对人体有害。
空气喷涂法适用性也较强,大部份涂料都可以采用喷涂;对小件物品,考虑到漆料的浪费,所以不宜采用此方法。
涂装过程控制涂装间隔时间控制涂漆间隔时间,对保证涂层质量有很大作用,否则将影响整体效果,甚至漆膜大片脱落或咬底。
每种涂料由于性能各异,要求的涂漆间隔时间也不同。
如油基漆类涂料,一般要求前道漆干燥后,方可涂下道漆,否则前道漆在很长时间内不会干燥,即使以后干燥了,也容易产生起皱现象;挥发性涂料,过早涂下道漆会发生咬底,过晚时又会产生附着力不好的现象,如环氧漆的施工,如果两道漆涂漆间隔过长,由于环氧树脂易老化和颜料的粉化,将严重影响各涂层间的附着力。
漆膜的干燥
(一)涂料施工后的干燥过程,即成膜过程。
涂料成膜后才具有防护性能,成膜过程质量的好坏,直接影响涂层的防护效果和寿命。
因此,漆膜的干燥也是施工中重要的一道工序。
漆膜的干燥分自然干燥、加热干燥、照射干燥(即红外线照射)。
防腐涂装施工通常采用在常温自然大气状态(温度8摄氏度以上)的自然干燥方法。
漆膜的干燥标准
1表干:
用手指轻轻按漆膜,感到发粘,但漆膜不粘附在手指上的状态。
2半干:
用手指轻按漆膜,在漆膜上不留指纹的状态。
3实干(完全干燥):
用手指重压或急速捅碰漆膜,在漆膜上不残留指纹或伤痕的状态。
燥分自然干燥、加热干燥、照射干燥(即红外线照射)。
防腐涂装施工通常采用在常温自然大气状态(温度8摄氏度以上)的自然干燥方法。
漆膜的干燥标准
1表干:
用手指轻轻按漆膜,感到发粘,但漆膜不粘附在手指上的状态。
2半干:
用手指轻按漆膜,在漆膜上不留指纹的状态。
3实干(完全干燥):
用手指重压或急速捅碰漆膜,在漆膜上不残留指纹或伤痕的状态。
(二)漆膜在干燥过程中,应保持周围环境清洁,防止灰尘、雨水、雪等污染。
漆膜厚度的控制
为了使涂料能够发挥其最佳性能,足够的漆膜厚度是极其重要的,因此必须严格控制漆膜的厚度。
施工时应按使用量进行涂装,并经常用干、湿漆膜测厚仪测定漆膜厚度,以保证干膜厚度和各涂层的均匀。
对于边、角、焊缝、切痕等部位,在喷涂之前应先涂刷一道,然后进行大面积的涂装,以保证凸出部位的漆膜厚度。
一般情况下,漆膜厚度分布应控制在两个80%以上。
即要求90%以上的测点测得的膜厚值,必须达到或超过规定的膜厚值,余下的不到10%的测点测得的膜厚值不得低于规定膜厚值
的90%。
在恶劣的腐蚀环境中及防腐要求较高的领域,应控制在两个95%以上。
选择测点要有代表性的地方,检测频数应根据被涂物表面的具体情况而定。
原则上,平整表面每平方米检测10点,复杂表面可每平方米检测20点。
狭小区域部位每一自由面测试8个以上测点。
二次涂装
二次涂装一般是指由于作业分工在两地或分二次进行施工的涂装。
但由于各种原因,前道漆涂完后,超过一个月以上再涂下道油漆,也应算作二次涂装,并应按二次涂装的规定进行表面处理。
进行二次涂装的目的主要是为了增强下道涂层与前道涂层的附着力。
所以在进行前,先将灰尘清除干净,如有局部返锈,应从表面处理重新除锈开始,然后修补前道漆种,直至与完好部位一样。
修补涂装
在涂装施工过程中或施工后,涂层产生缺陷是很难避免的,因此修补漆是正常的工作。
但这项工作常被轻视而影响整个涂装工程质量,这是造成以往涂装工程防护效果差、寿命短的主要原因之一。
修补漆时,所使用的涂料品种、涂层层次与厚度、涂层颜色应与原设计要求一致;表面处理可采用手工机械除锈方法,但要注意油脂及灰尘的污染。
在修补部位与不修补部位的边缘处,要有过渡段,以保证搭接处的平整和附着牢固。
对补涂部位的要求也应与上述相同。
三、安全技术
燃烧与防火涂装施工,所用的材料主要是易燃、易爆和有毒化学品。
这些材料在施工过程中形成漆雾、有机溶剂蒸气、粉尘,它们与空气混合积聚到一定浓度时,一旦接触明火,就很容易引起火灾和爆炸事故;有些油漆材料被操作人员长期接触或吸入体内可能引起慢性中毒,损害健康。
因此,施工技术人员和涂装操作者首先应掌握各种涂料的安全知识,并组织安全措施的落实和实施,在施工的过程中经常进行安全检查。
例如说:
如果大气温度接近或
在涂料产品闪点温度以上时,必须提供充分的通风以降低溶剂蒸气浓度,使之在燃烧极限下限的10%以下。
这样,即使大气温度高于闪点温度,施工仍可以进行。
爆炸与防爆
当溶剂蒸气与空气混合达到一定比例时,一遇到火源(明火)即发生爆炸。
为了确保涂装施工的安全,千万不要在狭小且密闭的空间内进行操作,一定要保持施工环境的通风、换气。
同时在涂料堆放和施工现场严禁使用明火及敲击油漆桶,将涂料远离电源装置存放。
毒害与防毒
涂料中的大部份溶剂和施工用的稀释剂都是有毒的化学品,它们不仅对人体皮肤有侵蚀作用,而且对人体中枢神经系统、呼吸系统也有刺激破坏作用。
这些都是通过呼吸道吸入及人体皮肤直接接触而造成的。
为了防止中毒,首先必须严格控制挥发性的有机溶剂蒸气在空气中的浓度,浓度标准按国家卫生部颁布的《工业企业设计卫生标准》规定执行。
对空气中的有害气体防止办法除限制浓度外,施工人员进入涂装现场必须戴防毒口罩或佩戴具有吸附作用的面罩(一般选用活性炭作为吸附剂),以便有效的阻止粉尘和漆雾被人体吸入;对于涂料接触性侵害,施工人员应穿好工作服、戴手套和防护眼镜,尽量不要和油漆溶剂接触,经常用肥皂或消毒液洗手。
四涂料配套方案涂料品种繁多,按其性能及使用用途的不同,配套使用方案也各有不同。
本技术方案主要介绍五类用途广泛的涂料配套方案,分别为耐高温漆配套体系、建筑重防腐漆配套方案、桥梁漆配套方案、发电厂油漆配套方案、港口机械钢铁结构油漆建议配套方案。
1.耐高温漆配套体系
大多数耐高温漆在高温下的保护作用主要依赖于铝粉。
醇酸铝粉耐高温漆保护钢铁的最高温度约为175摄氏度,高于这温度醇酸树脂会遭破坏,但漆膜中的铝粉将继续保护钢铁表面直至350摄氏度。
聚酯型铝粉耐高温漆具有较好的耐热性能,保护钢铁表面的温度在200-400摄氏度;二苯醚树脂为基料的FZ-15耐高温漆保护钢材的温度约为400-500摄氏度。
在耐高温漆的涂装过程中,表面处理非常重要。
表面有氧化铁的钢铁必须使用喷砂处理,达到国际GB8923的Sa2.5级。